90% More Chances to Win Projects With Our Estimate!
- Multi-Family Building
- Hotel Building
- Hospital Building
- Warehouse Building
- School & University Building
- High-Rise Building
- Shopping Complex
- Data Center Building
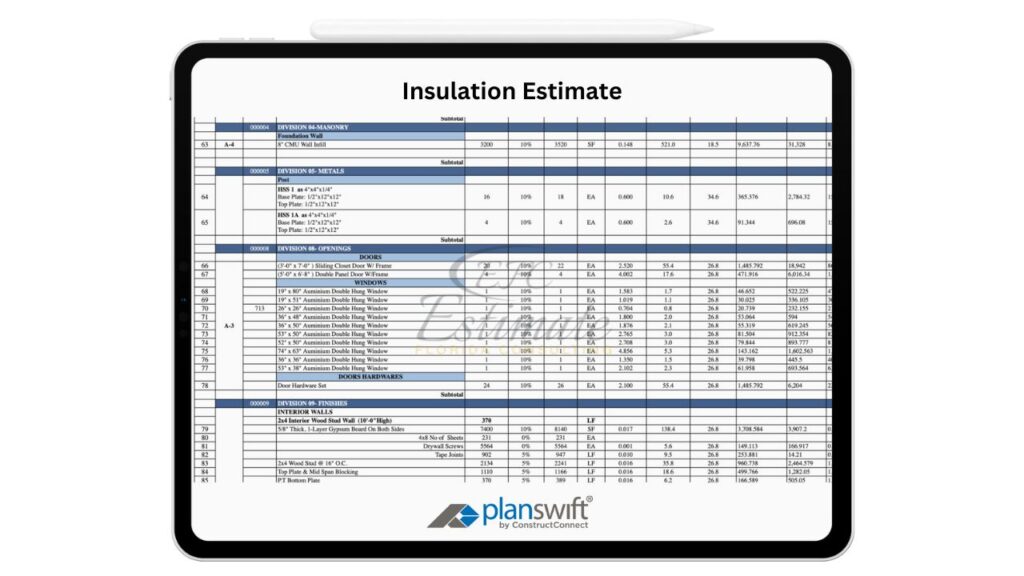
Wall insulation is essential for improving energy efficiency and maintaining a comfortable indoor environment. It acts as a barrier that prevents heat from escaping during the winter and entering during the summer, significantly reducing heating and cooling costs. Whether you’re building a new home, retrofitting an existing structure, or working on a large commercial project, understanding the costs of wall insulation is crucial for budget planning. This guide breaks down wall insulation costs, helping contractors, developers, and homeowners make informed decisions.
The cost of wall insulation varies by the type of material used. Generally, prices range from $1.80 to $4.20 per square foot for installation. Fiberglass batts remain the most affordable option, costing between $1.80 and $3.60 per square foot. Spray foam insulation, while more expensive, ranges from $3.00 to $4.20 per square foot, providing excellent thermal efficiency.
Insulation Type | Material Cost (per sq ft) | Installed Cost (per sq ft) |
Fiberglass Batts | $0.60 – $1.20 | $1.80 – $3.60 |
Spray Foam | $1.20 – $1.80 | $3.00 – $4.20 |
Rigid Foam Panels | $0.84 – $1.20 | $1.80 – $3.00 |
For large-scale insulation projects, such as insulating entire homes, the total cost depends on the area. Insulating a 1,000-square-foot area using fiberglass batts typically costs between $1,800 and $3,600. However, for a 1,500-square-foot area, the cost ranges from $2,700 to $5,400, depending on the type of insulation and labor charges.
Square Footage | Fiberglass Batts Cost | Spray Foam Cost |
1,000 sq ft | $1,800 – $3,600 | $3,000 – $4,200 |
1,500 sq ft | $2,700 – $5,400 | $4,500 – $6,300 |
2,000 sq ft | $3,600 – $7,200 | $6,000 – $8,400 |
Commercial buildings usually require a larger budget for insulation due to their size and more stringent energy-efficiency codes. On average, commercial insulation costs range between $1.80 to $6.00 per square foot. For a medium-sized commercial space of 5,000 square feet, the cost can range from $9,000 to $30,000, depending on the insulation material used and the labor required.
Commercial Building Size | Fiberglass Batts Cost | Spray Foam Cost |
2,500 sq ft | $4,500 – $9,000 | $7,500 – $10,500 |
5,000 sq ft | $9,000 – $18,000 | $15,000 – $21,000 |
10,000 sq ft | $18,000 – $36,000 | $30,000 – $42,000 |
For residential homes, the average cost of wall insulation varies based on size and insulation type. The cost of insulating a 2,000-square-foot home using fiberglass batts typically ranges between $3,600 and $7,200, while spray foam insulation can cost between $6,000 and $8,400.
Home Size | Fiberglass Batts Cost | Spray Foam Cost |
1,000 sq ft | $1,800 – $3,600 | $3,000 – $4,200 |
1,500 sq ft | $2,700 – $5,400 | $4,500 – $6,300 |
2,000 sq ft | $3,600 – $7,200 | $6,000 – $8,400 |
For a 1,500-square-foot home, the cost of insulation depends on the material used. Fiberglass batts typically range from $2,700 to $5,400, while spray foam costs range from $4,500 to $6,300. These costs include both materials and installation.
Insulation Type | Material Cost (per sq ft) | Total Cost for 1,500 sq ft |
Fiberglass Batts | $0.60 – $1.20 | $2,700 – $5,400 |
Spray Foam | $1.20 – $1.80 | $4,500 – $6,300 |
Exterior walls typically require more insulation than interior walls due to their exposure to the elements. Insulating exterior walls generally costs between $1.80 to $4.20 per square foot, while interior walls are slightly cheaper, ranging from $1.20 to $3.00 per square foot.
Wall Type | Material Cost (per sq ft) | Installed Cost (per sq ft) |
Interior Walls | $0.60 – $1.20 | $1.20 – $3.00 |
Exterior Walls | $0.90 – $2.40 | $1.80 – $4.20 |
Spray foam insulation, both open and closed-cell, is one of the most effective but expensive options. Open-cell spray foam costs around $1.80 to $3.00 per square foot, while closed-cell spray foam is more expensive, costing between $3.00 and $4.20 per square foot. While the upfront cost is higher, spray foam offers long-term savings by reducing energy bills up to 50%.
Spray Foam Type | R-Value per Inch | Material Cost (per sq ft) | Installed Cost (per sq ft) |
Open-Cell | R-3.7 | $0.72 – $1.08 | $1.80 – $3.00 |
Closed-Cell | R-6.5 | $1.20 – $1.80 | $3.00 – $4.20 |
Blown-in insulation, especially in retrofitting projects, offers flexibility and excellent coverage. The cost for blown-in fiberglass insulation has increased to $1.20 to $2.40 per square foot. Cellulose insulation, a popular eco-friendly option, ranges from $1.80 to $3.00 per square foot.
Insulation Type | Material Cost per Square Foot | Installed Cost Range (per sq ft) |
Blown-in Fiberglass | $0.72 – $0.96 | $1.20 – $2.40 |
Blown-in Cellulose | $0.84 – $1.08 | $1.80 – $3.00 |
The cost to insulate walls can vary depending on whether you’re dealing with exterior walls, interior walls, or specific types such as basement or partition walls. Exterior walls generally require more insulation to protect against outdoor temperature changes, now costing between $1.80 to $4.20 per square foot. Interior walls, mainly used for soundproofing or temperature regulation, now cost between $1.20 to $3.00 per square foot. Basement walls often need moisture-resistant insulation, like rigid foam panels, which range from $3.00 to $4.80 per square foot.
Wall Type | Insulation Material Cost (per sq ft) | Installed Cost (per sq ft) |
Interior Partition | $0.60 – $1.20 | $1.20 – $3.00 |
Exterior Wall | $1.20 – $2.40 | $1.80 – $4.20 |
Basement Wall | $1.80 – $3.00 | $3.00 – $4.80 |
Attics typically require thicker insulation, which can increase costs compared to wall insulation. Now, attic insulation costs between $2.40 to $4.80 per square foot, depending on the material used. While wall insulation is generally less expensive, it still plays an equally important role in ensuring a well-insulated home. If you’re insulating both walls and the attic, budgeting for the higher cost of attic insulation is essential.
Insulation Area | Material Cost per sq ft | Installed Cost per sq ft |
Walls | $1.08 – $3.00 | $1.80 – $4.20 |
Attic | $1.20 – $2.40 | $2.40 – $4.80 |
Insulation costs can vary significantly between commercial and residential buildings. Commercial buildings often need more extensive insulation, now costing from $1.80 to $6.00 per square foot, whereas residential insulation now ranges between $1.20 to $4.20 per square foot. Commercial projects often involve more complex insulation types, which also affect costs.
Building Type | Insulation Cost per Square Foot | Total Installed Cost Range |
Residential | $1.20 – $4.20 | $1,800 – $14,400 |
Commercial | $1.80 – $6.00 | $9,000 – $150,000 |
Soundproofing walls with insulation materials like rock wool or fiberglass batts now ranges from $1.20 to $3.00 per square foot. Spray foam, while more effective, is more expensive, now costing between $3.00 and $4.20 per square foot.
Soundproofing Material | Material Cost (per sq ft) | Installed Cost (per sq ft) |
Fiberglass Batts | $0.60 – $1.08 | $1.20 – $1.80 |
Rock Wool | $0.84 – $1.20 | $1.80 – $3.00 |
Spray Foam | $1.80 – $2.40 | $3.00 – $4.20 |
For DIY insulation, costs for fiberglass batts have increased to around $0.60 to $1.80 per square foot, whereas hiring a professional would now increase the total cost to $1.80 to $3.60 per square foot. For spray foam, professional installation costs have risen to between $3.00 to $4.20 per square foot.
Insulation Type | DIY Cost (per sq ft) | Professional Cost (per sq ft) |
Fiberglass Batts | $0.60 – $1.80 | $1.80 – $3.60 |
Spray Foam | N/A | $3.00 – $4.20 |
Insulating a 1,500 square foot home can now reduce energy costs by 15% to 30%, but with the increase in material and installation costs, the payback period has adjusted. While spray foam still offers up to a 50% reduction in heating and cooling costs, the upfront cost is now higher.
Insulation Material | Average Energy Savings | Estimated Payback Period |
Fiberglass Batts | 15% – 20% | 3.6 – 6 years |
Blown-in Cellulose | 20% – 25% | 4.8 – 7.2 years |
Spray Foam | 30% – 50% | 6 – 8.4 years |
Closed-cell spray foam, now costing between $3.00 to $4.20 per square foot, remains the best for moisture control. Rigid foam panels, which have increased to $1.80 to $3.00 per square foot, are also highly effective in preventing moisture damage.
Moisture-Resistant Insulation | Installed Cost (per sq ft) | Best Use Case |
Closed-Cell Spray Foam | $3.00 – $4.20 | Exterior/Basement Walls |
Rigid Foam Panels | $1.80 – $3.00 | Basement/Attic |
Mineral wool and fiberglass remain cost-effective choices for fire-resistant insulation. Mineral wool now costs around $1.20 to $1.80 per square foot, and fiberglass costs $0.60 to $1.20 per square foot.
Fire-Resistant Material | Material Cost (per sq ft) | Installed Cost (per sq ft) |
Mineral Wool | $1.20 – $1.80 | $2.40 – $3.60 |
Fiberglass | $0.60 – $1.20 | $1.20 – $3.00 |
Choosing the right insulation for your project is a multifaceted decision that significantly impacts energy efficiency, comfort, and overall construction costs. Insulation not only helps regulate indoor temperatures but also plays a vital role in reducing energy consumption and associated costs over time. To make an informed choice, it’s essential to consider various factors, including your specific needs, budget, and the building’s location. Below are some comprehensive tips to help you select the best insulation option for your project:
The climate in your area is one of the most critical factors in determining the appropriate insulation for your project. Insulation is rated by its R-value, which measures its thermal resistance. Colder climates, such as those found in northern regions, typically require higher R-values to maintain warmth and reduce heating costs. Conversely, warmer climates may need insulation that helps keep buildings cool, thus necessitating different R-value considerations. It’s essential to consult local building codes and climate data to determine the recommended R-values for your specific area. Understanding your local climate patterns—such as temperature extremes, humidity levels, and seasonal changes—can also help you choose insulation that performs optimally year-round.
When selecting insulation, it’s vital to evaluate the costs of various materials. Different types of insulation materials—like fiberglass, foam board, spray foam, and cellulose—vary significantly in price. Setting a budget that balances initial costs with potential long-term savings on energy bills can be beneficial. While some insulation materials might have a higher upfront cost, they may offer better energy efficiency, leading to significant savings over time. For example, spray foam insulation tends to be more expensive initially but provides superior air sealing and insulation efficiency, potentially lowering heating and cooling costs. It’s wise to analyze the overall cost of installation, including labor and materials, to get a clearer picture of your investment. Additionally, consider potential rebates or incentives for energy-efficient insulation options offered by local governments or utility companies.
The complexity of installation is another important factor to consider when selecting insulation. Some insulation types, such as spray foam, require professional installation due to their specialized application methods and safety considerations. This can add to the overall cost of the project. In contrast, insulation materials like fiberglass batts or rigid foam boards are often more DIY-friendly, making them an appealing option for homeowners looking to save on labor costs. However, it’s crucial to understand that improper installation can lead to air leaks and reduced efficiency, negating any savings. Therefore, if you choose a more complex insulation type, ensure you have the necessary skills and tools or hire a qualified professional to guarantee optimal performance. Assessing your comfort level with installation and the availability of professional help in your area can significantly influence your choice.
In today’s environmentally conscious market, sustainability is an increasingly important consideration when choosing insulation. Many consumers are looking for eco-friendly options that minimize environmental impact and improve indoor air quality. Materials like cellulose insulation, made from recycled paper products, or sheep’s wool, offer sustainable alternatives that can also provide excellent thermal performance. Additionally, some manufacturers produce insulation using sustainable practices or renewable resources, which can appeal to environmentally-minded builders and homeowners. Consider researching the lifecycle impacts of various insulation materials, including their energy efficiency during production, installation, and disposal phases. Opting for sustainable insulation not only contributes to a healthier planet but can also enhance your building’s marketability and appeal to eco-conscious buyers.
The first step in calculating your insulation costs is to accurately measure the height and length of each wall that requires insulation. This will give you the total square footage of the area. For irregularly shaped rooms or spaces with many doors and windows, be sure to deduct their dimensions to avoid overestimating the square footage. If you’re unsure about your measurements, it’s advisable to consult a professional who can help with precise calculations.
Once you have the total square footage, you can begin estimating material and labor costs. Knowing the exact size of the area allows you to make informed decisions about the type of insulation material and installation methods that will work best for your project.
Next, select the insulation material that best suits your needs and budget. Each material has different R-values (a measure of thermal resistance), costs, and environmental impacts. For example, if you’re focused on sustainability, blown-in cellulose made from recycled materials may be the best choice. Alternatively, if you need superior air sealing, spray foam may be more appropriate despite its higher cost.
When choosing insulation, consider not only the upfront costs but also the long-term benefits. A more expensive material with a higher R-value may save you money in energy bills over time. Additionally, some insulation materials are eligible for government incentives or rebates, which can help offset the initial investment.
Multiply the total square footage by the cost per square foot for your chosen insulation material to estimate material costs. Be sure to account for any bulk discounts if you’re purchasing large quantities of insulation. Many suppliers offer reduced rates for bulk orders, which can help lower overall costs. Don’t forget to include any additional features, such as vapor barriers or air sealing, in your material cost calculations.
If you’re unsure about how much material to purchase, most manufacturers and suppliers offer online calculators or estimators to help you determine the amount of insulation needed for your specific project.
Labor costs vary depending on the complexity of the project and the location. To get an accurate estimate, obtain quotes from several insulation contractors in your area. Request itemized quotes that detail labor costs, materials, and any additional expenses to avoid unexpected charges later. Comparing quotes will also give you a better sense of what a fair price is for your project, ensuring that you choose a contractor who offers quality service at a reasonable cost.
In some cases, DIY installation may be an option, particularly for less complex insulation projects. However, for more intricate jobs or those involving spray foam or blown-in insulation, it’s best to hire a professional to ensure proper installation and maximize energy efficiency.
Finally, be sure to factor in any additional costs, such as repairs to the existing structure or the installation of vapor barriers. These extras are often overlooked during initial budgeting, but they can significantly impact the overall cost of the project. A thorough assessment of your insulation needs, as well as a complete understanding of any additional work required, will help you create a more accurate budget and avoid unpleasant surprises during the installation process.
One of the most common mistakes homeowners and contractors make is underestimating the total cost of materials and labor. It’s crucial to gather accurate quotes and account for all necessary components to ensure a realistic budget. This includes factoring in the costs of any additional materials, such as vapor barriers or air sealing products, as well as labor for any structural modifications or repairs. Failing to account for these extra expenses can lead to financial strain and delays in completing the project.
Additionally, some may underestimate the value of professional installation, thinking they can save by doing the work themselves. However, improper installation can lead to gaps, moisture issues, and other problems that compromise the insulation’s effectiveness, ultimately costing more in repairs or rework.
Another common mistake is focusing solely on the initial installation costs without considering the long-term energy savings that quality insulation can provide. While some insulation materials may be more expensive upfront, they can significantly reduce heating and cooling costs, leading to substantial savings over time. An energy audit can help you estimate the potential savings and better understand the return on investment (ROI) for different insulation types. Insulation is an investment that can pay off in reduced energy bills and increased property value, so it’s essential to consider the long-term benefits.
Ignoring local building codes and regulations related to insulation can result in costly fines or the need for rework. Different areas have specific requirements for insulation materials, R-values, and installation techniques, especially in regions with extreme climates. Before starting your insulation project, consult local codes or hire a professional who is familiar with these regulations to ensure your project complies. Failure to do so may not only lead to additional expenses but also affect the overall performance of your insulation system.
Understanding wall insulation costs is vital for making informed decisions in any construction or renovation project. By evaluating material options and installation methods, contractors and homeowners can effectively budget for insulation, ensuring both energy efficiency and comfort in their spaces. From the cost variations among different insulation types to the long-term savings they offer, this guide serves as a comprehensive resource for assessing wall insulation needs. Ultimately, investing in quality insulation is an essential step toward enhancing energy efficiency, reducing utility bills, and improving overall indoor air quality for residential and commercial buildings alike.
The cost of wall insulation is influenced by several factors, including the type of insulation material chosen, the size of the area to be insulated, labor costs, and any additional features such as vapor barriers. Local building codes and the complexity of installation also play significant roles in determining overall costs.
Wall insulation costs typically range from $1.80 to $4.20 per square foot for installation. The specific cost depends on the insulation material used. For instance, fiberglass batts cost between $1.80 and $3.60 per square foot, while spray foam insulation ranges from $3.00 to $4.20 per square foot.
The most common types of insulation materials include:
Larger projects, such as insulating an entire home, generally see economies of scale. For example, insulating a 1,000-square-foot area with fiberglass batts costs between $1,800 and $3,600. In contrast, a 1,500-square-foot area may range from $2,700 to $5,400, depending on the insulation type and labor costs.
Commercial insulation projects often require larger budgets due to their size and stricter energy-efficiency codes. Typically, commercial insulation costs range from $1.80 to $6.00 per square foot, while residential insulation ranges from $1.20 to $4.20 per square foot.
Spray foam insulation is one of the most effective insulation types due to its superior air sealing and energy efficiency. While it has a higher upfront cost, it can reduce heating and cooling costs by up to 50%, making it a cost-effective option in the long run.
At Estimate Florida Consulting, we offer detailed cost estimates across all major trades, ensuring no part of your project is overlooked. From the foundation to the finishing touches, our trade-specific estimates provide you with a complete and accurate breakdown of costs for any type of construction project.
561-530-2845
info@estimatorflorida.com
Address
5245 Wiles Rd Apt 3-102 St. Pete Beach, FL 33073 United States
561-530-2845
info@estimatorflorida.com
Address
5245 Wiles Rd Apt 3-102 St. Pete Beach, FL 33073 United States
All copyright © Reserved | Designed By V Marketing Media | Disclaimer