90% More Chances to Win Projects With Our Estimate!
- Multi-Family Building
- Hotel Building
- Hospital Building
- Warehouse Building
- School & University Building
- High-Rise Building
- Shopping Complex
- Data Center Building
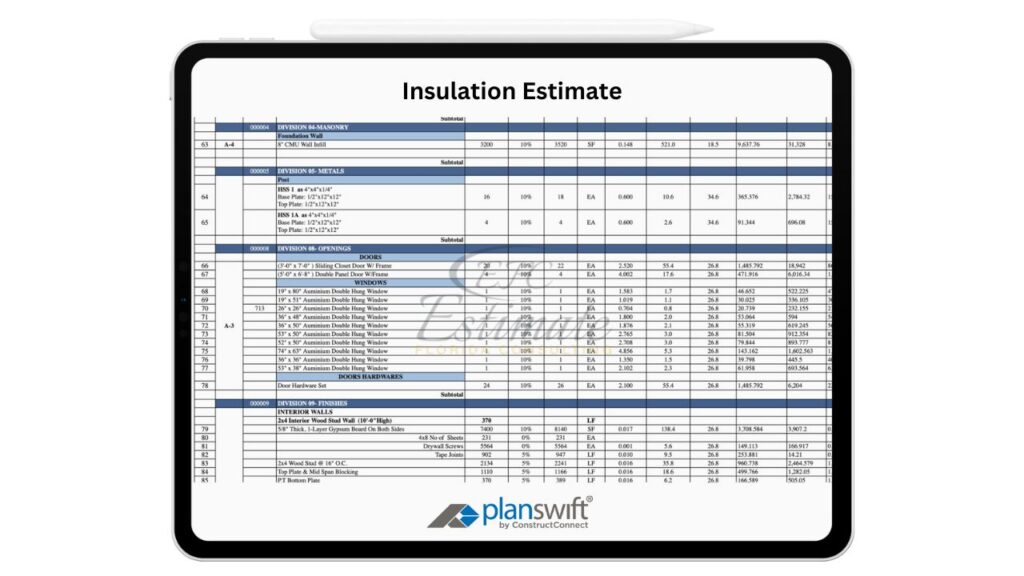
Blown-in cellulose insulation is one of the most sustainable insulation options available today, offering excellent thermal performance for both residential and commercial buildings. It’s primarily made from recycled paper products, with newsprint being a significant component. After being treated with non-toxic fire retardants, the cellulose is blown into attics, walls, and other spaces using specialized equipment. This process ensures an even distribution of the insulation material, filling all nooks and gaps to create an energy-efficient barrier that reduces heat transfer and improves indoor comfort.
Choosing blown-in cellulose insulation means opting for an environmentally friendly product with a low carbon footprint. In comparison to traditional insulation materials, it requires less energy to produce, and its use of recycled materials helps reduce landfill waste. Understanding the cost factors is critical for accurately planning your budget and making the most out of this eco-friendly solution.
When considering blown-in insulation for your home, it’s essential to understand the costs involved. On average, you can expect to pay between $1.00 and $2.80 per square foot for installation. However, various factors can influence these prices, including the insulation material type (cellulose, fiberglass, or Rockwool), the installation location, the desired R-value, and the size of the project.
Location | Average Cost |
Attic Floor | $900 – $3,600 |
Exterior Walls | $1,900 – $7,800 |
Two-Car Garage | $1,400 – $4,600 |
Garage Walls | $950 – $3,200 |
Garage Attic Floor | $520 – $1,400 |
Entire House (New Construction) | $3,500 – $11,600 |
Entire House (Existing Construction) | $4,500 – $16,000 |
Note: Costs are based on a home size of 2,000 to 2,500 square feet with a two-car detached garage.
When looking at blown-in insulation costs on a per-square-foot basis, here’s what you can expect:
This range reflects the various types of insulation materials, their R-values, and the specifics of the installation site.
Square Feet | Average Cost to Install |
100 | $100 – $280 |
300 | $300 – $840 |
500 | $500 – $1,400 |
700 | $700 – $2,000 |
1,000 | $1,000 – $2,800 |
1,200 | $1,200 – $3,400 |
1,500 | $1,500 – $4,200 |
2,000 | $2,000 – $5,600 |
2,500 | $2,500 – $7,000 |
3,000 | $3,000 – $8,400 |
The overall cost of blown-in cellulose insulation is influenced by several key factors, each of which must be carefully considered during the estimation process:
The following table outlines the revised cost breakdown for blown-in cellulose insulation. This updated cost estimate provides a realistic view of what homeowners, contractors, and developers can expect to pay:
Component | Cost Range (Per Square Foot) |
Material | $0.55 – $2.20 |
Labor | $0.66 – $1.65 |
Equipment Rental | $55 – $220 (Daily) |
Total Installed Cost | $1.21 – $3.85 |
These costs are subject to further adjustments depending on the specific characteristics of the project, such as insulation thickness and the complexity of the installation.
When comparing blown-in cellulose to other popular insulation materials like fiberglass or spray foam, it’s essential to consider not only the upfront costs but also the long-term benefits. Blown-in cellulose offers a competitive balance of cost, performance, and environmental impact:
Insulation Type | Cost (Per Square Foot) | R-Value Per Inch |
Blown-In Cellulose | $1.21 – $3.85 | 3.2 – 3.8 |
Fiberglass Batts | $0.66 – $1.98 | 2.2 – 2.7 |
Spray Foam | $1.10 – $4.95 | 6.0 – 7.0 |
Blown-in cellulose stands out for its affordability, particularly when compared to spray foam. It offers a solid R-value, providing excellent thermal insulation while being made from recycled materials, which is a significant advantage in terms of sustainability.
Labor costs are a critical part of the overall budget for insulation projects. Professional labor fees for blown-in cellulose insulation typically range between $0.66 and $1.65 per square foot. This range can fluctuate depending on several factors, including the size of the space, the difficulty of installation, and regional labor rates.
The R-value of insulation measures its effectiveness in resisting heat transfer, with a higher R-value offering better insulation. Blown-in cellulose insulation typically provides an R-value of 3.2 to 3.8 per inch. The thickness of the insulation directly impacts the cost; thicker insulation requires more material and labor, increasing overall expenses.
The cost of blown-in cellulose insulation will rise as the required R-value increases, particularly in colder regions where higher R-values are necessary to meet building code standards.
For homeowners considering a DIY approach, the primary savings come from reduced labor costs. However, a DIY project often requires equipment rentals and can be time-consuming. Professional installation, while more expensive, ensures that the insulation is properly installed, minimizing the risk of under-insulated areas, air leaks, or inefficient energy performance.
Installation Type | Cost (Per Square Foot) |
DIY | $0.55 – $2.20 |
Professional | $1.21 – $3.85 |
DIY installations may seem attractive, but they often come with hidden costs, such as the time required to learn proper techniques and the risk of mistakes. On the other hand, professional installers have the expertise to complete the job efficiently and effectively, ensuring optimal performance and long-term savings.
Installation costs for blown-in cellulose insulation vary across regions due to differences in labor costs, material availability, and local building codes. Urban areas, particularly those with a higher cost of living, tend to have more expensive labor rates. Rural areas, while potentially offering lower labor costs, may have higher material prices due to transportation and supply challenges.
These regional differences should be taken into account when estimating project costs, as they can significantly impact the final budget.
While the upfront costs of blown-in cellulose insulation may be higher than some other options, the long-term energy savings are substantial. Homeowners can expect to save up to 20% on heating and cooling costs annually, thanks to the insulation’s ability to minimize heat loss in the winter and keep cool air inside during the summer. Over the lifespan of the insulation, these savings can quickly offset the initial investment.
Additionally, cellulose insulation helps to reduce drafts, maintain more consistent indoor temperatures, and improve overall home comfort. In many regions, blown-in cellulose insulation also qualifies for government rebates and tax incentives, further increasing the financial return on investment.
To accurately estimate the cost of blown-in cellulose insulation, start by measuring the square footage of the area you wish to insulate. Consider both walls and ceilings, as insulation requirements may differ. Use a tape measure or laser measuring tool to get precise measurements. Don’t forget to account for any architectural features such as vaulted ceilings, staircases, or complex roof lines, as these can affect the total area that needs insulation. It may be helpful to create a simple diagram of the area to visualize the project and ensure that all spaces are accounted for.
Different applications may require different thicknesses of insulation. Consult local building codes and energy efficiency recommendations to determine the appropriate thickness for your project. Standard thicknesses typically range from 4 to 12 inches, but factors like climate, building design, and energy efficiency goals can influence the best choice. Working with an insulation professional can provide valuable insights into the optimal thickness for your specific situation, ensuring that you achieve maximum energy efficiency and comfort.
Using the average price range for cellulose insulation material, multiply the cost per square foot by the total square footage of the area to get a preliminary estimate. Keep in mind that this estimate may vary based on the specific product chosen and any discounts available for bulk purchases. Additionally, consider the costs of any necessary equipment for installation, such as blowing machines or protective gear, which may be rented or purchased separately. Having a detailed breakdown of these costs will help you create a more accurate overall budget.
Based on your local labor rates and the complexity of the installation, estimate the installation costs using the ranges provided above. It’s essential to obtain quotes from multiple contractors to ensure you are getting competitive pricing. Ask for detailed estimates that break down labor and any additional costs, such as disposal of old insulation or preparation of the site. Keep in mind that the lowest bid may not always represent the best value; quality of work and reputation are also critical factors to consider when selecting an installer.
Consider any additional features or services required for your project. This may include air sealing, vapor barriers, or other enhancements that can contribute to energy efficiency. If you’re working on a renovation project, you might also need to budget for the removal of existing insulation or repairs to walls or ceilings, which can increase costs. By proactively addressing these potential expenses, you can avoid surprises and ensure your project stays on track and within budget.
Reducing insulation costs doesn’t have to mean compromising on quality. Here are some practical strategies to help lower the cost of blown-in cellulose insulation:
One of the most significant advantages of blown-in cellulose insulation is its positive impact on the environment. As a product made from up to 85% recycled materials, cellulose insulation helps reduce the demand for new raw materials and minimizes landfill waste. The production process for cellulose insulation also requires less energy compared to other types of insulation, such as fiberglass or spray foam.
Additionally, because blown-in cellulose fills every nook and cranny in a space, it helps eliminate air leaks and improves energy efficiency. This translates to lower energy consumption and reduced greenhouse gas emissions, making it an environmentally responsible choice for any construction project.
Below is an updated cost table, reflecting the 10% price increase. This table can serve as a reference for estimating the total cost of insulation for different building sizes:
Area | Square Footage | Material Cost | Labor Cost | Total Cost |
Small Home (1,500 sq ft) | 1,500 sq ft | $825 – $3,300 | $990 – $2,475 | $1,815 – $5,775 |
Medium Home (2,500 sq ft) | 2,500 sq ft | $1,375 – $5,500 | $1,650 – $4,125 | $3,025 – $9,625 |
Large Home (3,500 sq ft) | 3,500 sq ft | $1,925 – $7,700 | $2,310 – $5,775 | $4,235 – $13,475 |
Cost estimation for blown-in cellulose insulation can be tricky. Here are some common mistakes and tips for avoiding them:
On average, blown-in cellulose insulation costs between $1.21 and $3.85 per square foot, depending on the location, the thickness of the insulation, and whether it's a DIY or professional installation.
Blown-in cellulose insulation can last 20 to 30 years, or even longer, if installed correctly. It’s resistant to settling, and its effectiveness remains stable over time.
Yes, blown-in cellulose insulation is one of the most eco-friendly options available. It’s made from up to 85% recycled materials and requires less energy to produce than many other insulation types.
Yes, blown-in cellulose insulation can be installed as a DIY project. However, it requires specific equipment, such as an insulation blower, and a good understanding of proper installation techniques. For larger or more complex areas, it’s often better to hire a professional.
On average, blown-in cellulose insulation can reduce energy bills by up to 20%, depending on the thickness and quality of the installation. This can lead to significant savings over time, making it a wise investment for energy efficiency.
At Estimate Florida Consulting, we offer detailed cost estimates across all major trades, ensuring no part of your project is overlooked. From the foundation to the finishing touches, our trade-specific estimates provide you with a complete and accurate breakdown of costs for any type of construction project.
We take pride in delivering accurate, timely, and reliable estimates that help contractors and builders win more projects. Our clients consistently praise our attention to detail, fast turnaround times, and the positive impact our estimates have on their businesses.
Estimate Florida Consulting has helped us win more bids with their fast and accurate estimates. We trust them for every project!
Submit your project plans, blueprints, or relevant documents through our online form or via email.
We’ll review your project details and send you a quote based on your scope and requirements.
Confirm the details and finalize any adjustments to ensure the estimate meets your project needs.
Receive your detailed, trade-specific estimate within 1-2 business days, ready for your project execution.
561-530-2845
info@estimatorflorida.com
Address
5245 Wiles Rd Apt 3-102 St. Pete Beach, FL 33073 United States
561-530-2845
info@estimatorflorida.com
Address
5245 Wiles Rd Apt 3-102 St. Pete Beach, FL 33073 United States
All copyright © Reserved | Designed By V Marketing Media | Disclaimer