90% More Chances to Win Projects With Our Estimate!
- Multi-Family Building
- Hotel Building
- Hospital Building
- Warehouse Building
- School & University Building
- High-Rise Building
- Shopping Complex
- Data Center Building
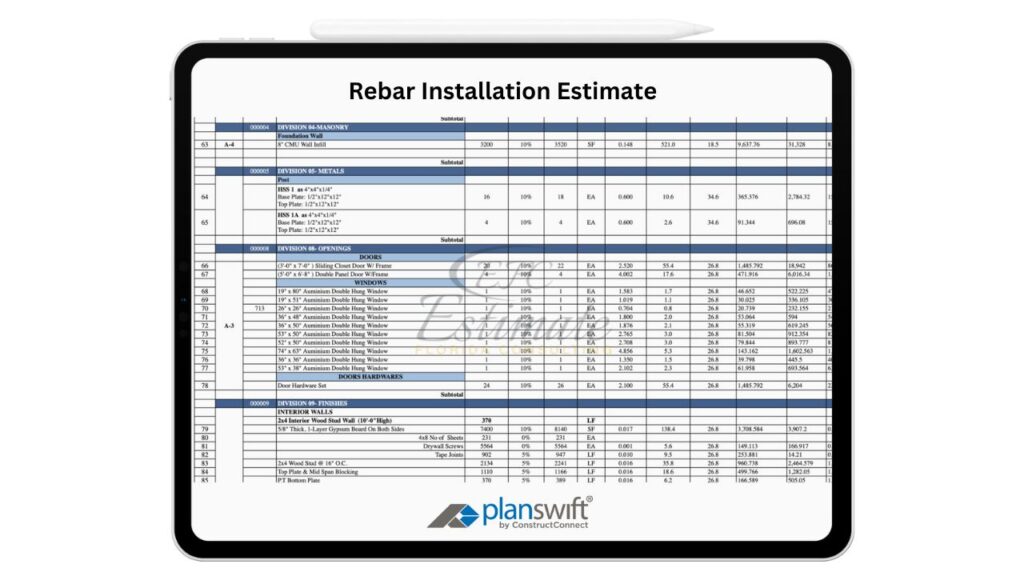
Rebar material prices typically range from $55 to $400 for a patio and $165 to $1,100 for a driveway. On average, rebar costs between $0.44 to $2.48 per linear foot for standard sizes like 3/8” to 5/8”. If you’re buying in bulk, rebar prices range from $1,430 to $2,200 per ton, or $0.55 to $1.10 per pound.
Size (mm) | Diameter (inches) | Price per foot | Price per ton | Usage |
#3 (10) | 3/8″ | $0.44 – $1.38 | $1,595 – $2,200 | Patio, Sidewalk, Walkway, Basic driveway, Pool deck border, Pool walls |
#4 (13) | 1/2″ | $0.55 – $1.93 | $1,485 – $1,870 | Concrete retaining wall, Small footings, Driveway for large vehicles, Small columns |
#5 (16) | 5/8″ | $0.77 – $2.48 | $1,430 – $1,980 | Foundations, Footings, Extra-large walls & columns, Small beams, Large swimming pool base |
#6 (19) | 3/4″ | $0.99 – $3.03 | $1,320 – $1,870 | Retaining walls, Roads & highways, Long ceiling beams |
#7 (22) | 7/8″ | $1.10 – $3.30 | $1,100 – $1,540 | Multi-story parking garages, Bridges |
#8 (25) | 1″ | $1.38 – $4.95 | $1,100 – $1,540 | Heavy commercial applications, Seawalls |
Here is the information you provided in a table format:
Project Size | Total Linear Feet of Rebar* | Rebar Material Prices |
10′ x 10′ Patio (100 SF) | 132 – 165 | $55 – $220 |
10′ x 20′ Patio (200 SF) | 275 – 319 | $110 – $396 |
20′ x 20′ Patio (400 SF) | 550 – 605 | $220 – $770 |
4′ x 50′ Sidewalk or Walkway (200 SF) | 253 – 352 | $99 – $440 |
4′ Pool Deck Border (360 SF) | 462 – 627 | $187 – $770 |
25′ x 3′ Concrete Retaining Wall (75 SF) | 88 – 132 | $44 – $220 |
25′ x 6′ Concrete Retaining Wall (150 SF) | 198 – 242 | $99 – $418 |
12′ x 24′ Size 1-car Driveway (288 SF) | 396 – 440 | $165 – $550 |
24′ x 24′ Size 2-car Driveway (576 SF) | 814 – 880 | $330 – $1,100 |
24′ x 36′ Size 3-car Driveway (864 SF) | 1,210 – 1,320 | $484 – $1,650 |
30′ x 40′ Foundation (1,200 SF) | 1,705 – 1,815 | $1,210 – $4,070 |
30′ x 60′ Foundation (1,800 SF) | 2,585 – 2,805 | $1,815 – $6,270 |
40′ x 60′ Foundation (2,400 SF) | 3,410 – 3,630 | $2,420 – $8,140 |
Plain and untreated steel rebar typically costs between $0.44 and $1.38 per linear foot, while stainless steel rebar can range from $0.44 to $9.90 per linear foot. The specific type of rebar required will depend on the intended design and the installation location.
Here is the information in a table format:
Rebar Type | Average Cost per Linear Foot* | Details |
Steel | $0.44 – $1.38 | Basic untreated steel, weldable, corrodible |
Stainless Steel | $4.95 – $9.90 | Corrosion-resistant surface, maintenance-free, suitable for saltwater areas, difficult to weld, not recommended for pool foundations near chlorinated water |
Galvanized | $1.32 – $1.76 | Zinc-coated surface, resists corrosion and abrasion, not ideal for saltwater areas |
Fiberglass | $0.72 – $2.75 | Lighter than steel, corrosion-resistant, some types stronger than steel, thermally non-conductive |
The cost of rebar increases with its thickness and length. For residential or commercial construction, thicker rebar (like 5/8″ or larger) is often required for heavy-duty areas such as driveways, parking lots, or multi-story buildings. This directly impacts the overall cost, especially when scaling up for larger projects like hotels or multi-story apartments. If your project involves long spans of rebar, such as a foundation or retaining wall, expect a significant rise in material expenses.
Buying rebar in bulk typically lowers the per-foot cost, but the savings grow more evident for large-scale projects. For contractors or material suppliers dealing with high-demand projects, like those in Florida, where construction is booming, purchasing larger quantities can unlock valuable bulk discounts. Whether you’re working on a small residential driveway or a multi-story office building, quantity impacts pricing, so planning ahead can help mitigate some costs.
Galvanized and stainless steel rebar can be significantly more expensive than regular steel. Galvanized rebar is great for resisting corrosion, which is essential for long-term durability, particularly in coastal areas like Florida, where saltwater exposure is common. Stainless steel is even more durable, though it comes at a much higher price. In scenarios where cost is a major concern, sticking with standard steel rebar may help manage the budget, but the material type is something to weigh carefully, especially for high-exposure environments.
Coating rebar with corrosion-resistant paint offers extra protection, which is a valuable feature in projects where the rebar might be exposed to harsh elements or moisture. This can be particularly useful for projects near coastal regions or where long-term durability is key. However, opting for this corrosion-resistant coating will increase the cost compared to standard black rebar, though it can potentially save on maintenance and repair in the long run.
Steel prices fluctuate based on market conditions, availability, and even geographic location. For estimators and contractors working in Florida or other construction-heavy states, staying on top of steel price trends is crucial for budgeting accurately. A sudden spike in steel prices can impact projects like hotels, apartment buildings, or large commercial complexes, making it essential to factor in some flexibility when estimating costs.
Not all rebar is created equal. Premium brands offer rebar that has higher strength and durability, often with fewer alloys, but they come at a higher price point. For high-quality construction projects, using better-grade rebar from reputable brands can provide long-term benefits, such as improved structural integrity and reduced maintenance. This is especially relevant for multi-story buildings or commercial spaces where safety and durability are top priorities.
Delivery costs depend not only on the size of your rebar order but also on the distance to your construction site. Large-scale projects like hotels or multi-story buildings may require substantial amounts of rebar, leading to higher transportation costs. Contractors should factor in these logistical expenses early in the planning stage to avoid unexpected cost increases, particularly when ordering materials from suppliers located far from the site.
When considering rebar for construction projects, understanding the differences in grades is essential for selecting the right material for your specific needs. Grade 60 rebar generally costs up to 40% more on average than Grade 40 rebar, with prices varying based on market availability. The grade of rebar indicates its strength, measured in pounds per square inch (PSI) that the steel can withstand.
Stronger Grade 60 rebar is commonly used for large structures, such as high-rise buildings and bridges, where durability and load-bearing capacity are critical. On the other hand, Grade 40 rebar is more prevalent in residential projects, where the structural demands are typically lower. The choice between these two grades can significantly impact both the cost and structural integrity of the project.
Rebar Rating Type | Minimum Yield Strength | Minimum Tensile Strength |
Grade 40 | 40,000 PSI (40 KSI) | 60,000 PSI (60 KSI) |
Grade 60 | 60,000 PSI (60 KSI) | 90,000 PSI (90 KSI) |
This grade has a minimum yield strength of 40,000 PSI and a minimum tensile strength of 60,000 PSI. It is suitable for most residential applications, such as foundations, slabs, and small retaining walls. Its lower cost makes it an attractive option for homeowners and small-scale contractors.
With a minimum yield strength of 60,000 PSI and a minimum tensile strength of 90,000 PSI, Grade 60 rebar is engineered for heavy-duty applications. Its higher strength makes it ideal for large commercial buildings, bridges, and other structures that require superior durability and resistance to heavy loads. Although it comes with a higher price tag, the investment pays off in terms of long-term structural integrity and safety.
The labor cost to install rebar typically ranges from $1.10 to $1.93 per square foot, excluding the cost of materials. This price can vary based on several factors, including the complexity of the project, local labor rates, and the specific requirements of the installation. For example, projects that involve intricate designs or large areas may require more skilled labor, leading to higher costs.
When considering a concrete driveway, the total installation cost generally falls between $4.40 and $8.80 per square foot. This pricing includes not just the labor for rebar installation but also the pouring and finishing of the concrete. Therefore, for a complete understanding of the total expense, both the labor costs for installing rebar and the costs associated with pouring the concrete should be factored in.
In terms of concrete pricing, expect to pay between $132 and $165 per cubic yard for delivered concrete alone. This cost reflects just the material and does not include any labor or other necessary materials for rebar installation. Understanding the separate costs associated with both labor and materials is crucial for effective budgeting and planning.
Here’s a breakdown of the estimated costs associated with installing rebar:
Factor | Cost per Square Foot |
Rebar Materials | $0.44 – $2.48 |
Installation Labor | $1.10 – $1.93 |
Total Cost to Install | $1.54 – $4.41 |
When considering rebar installation, it’s essential to weigh the pros and cons of doing it yourself versus hiring a professional. Installing rebar is not just about placing steel bars in the correct position; it requires a solid understanding of concrete properties and the use of specialized tools designed for cutting, bending, and tying rebar. Additionally, you’ll need the ability to read and interpret engineering plans, which outline the structural requirements for the project.
Improper installation of rebar can lead to serious consequences, such as structural weaknesses that might result in cracking, sagging, or even catastrophic failure of the concrete over time. Such safety risks make it crucial to have the right skills and knowledge, particularly for larger projects or critical structures.
For these reasons, rebar installation is often best left to professionals. Experienced concrete foundation or floor installers have the training and expertise needed to ensure that rebar is installed correctly and adheres to safety standards. By hiring a qualified local installer, you can save yourself the stress of potentially making costly mistakes and ensure that the job is done right the first time.
Rebar material prices typically range from $55 to $400 for a patio and $165 to $1,100 for a driveway. On average, rebar costs between $0.44 and $2.48 per linear foot for standard sizes (3/8” to 5/8”). If purchasing in bulk, prices range from $1,430 to $2,200 per ton or $0.55 to $1.10 per pound.
Here’s a breakdown of rebar costs based on size:
Size (mm) | Diameter (inches) | Price per foot | Price per ton | Usage |
#3 (10) | 3/8" | $0.44 – $1.38 | $1,595 – $2,200 | Patio, sidewalk, walkway, basic driveway, pool deck border, pool walls |
#4 (13) | 1/2" | $0.55 – $1.93 | $1,485 – $1,870 | Concrete retaining wall, small footings, driveway for large vehicles, small columns |
#5 (16) | 5/8" | $0.77 – $2.48 | $1,430 – $1,980 | Foundations, footings, extra-large walls & columns, small beams, large swimming pool base |
#6 (19) | 3/4" | $0.99 – $3.03 | $1,320 – $1,870 | Retaining walls, roads & highways, long ceiling beams |
#7 (22) | 7/8" | $1.10 – $3.30 | $1,100 – $1,540 | Multi-story parking garages, bridges |
#8 (25) | 1" | $1.38 – $4.95 | $1,100 – $1,540 | Heavy commercial applications, seawalls |
The following chart shows the estimated total linear feet of rebar required for various residential projects along with their corresponding material prices:
Project Size | Total Linear Feet of Rebar | Rebar Material Prices |
10' x 10' Patio (100 SF) | 132 – 165 | $55 – $220 |
10' x 20' Patio (200 SF) | 275 – 319 | $110 – $396 |
20' x 20' Patio (400 SF) | 550 – 605 | $220 – $770 |
4' x 50' Sidewalk (200 SF) | 253 – 352 | $99 – $440 |
4' Pool Deck Border (360 SF) | 462 – 627 | $187 – $770 |
25' x 3' Retaining Wall (75 SF) | 88 – 132 | $44 – $220 |
25' x 6' Retaining Wall (150 SF) | 198 – 242 | $99 – $418 |
12' x 24' Driveway (288 SF) | 396 – 440 | $165 – $550 |
24' x 24' Driveway (576 SF) | 814 – 880 | $330 – $1,100 |
24' x 36' Driveway (864 SF) | 1,210 – 1,320 | $484 – $1,650 |
30' x 40' Foundation (1,200 SF) | 1,705 – 1,815 | $1,210 – $4,070 |
30' x 60' Foundation (1,800 SF) | 2,585 – 2,805 | $1,815 – $6,270 |
40' x 60' Foundation (2,400 SF) | 3,410 – 3,630 | $2,420 – $8,140 |
Most residential projects utilize rebar that ranges from 3/8" to 5/8" in thickness. For concrete slabs less than 4 inches thick, rebar typically isn't necessary, while slabs thicker than 4 inches, especially those supporting heavy vehicles, generally require rebar.
Several factors can impact rebar pricing, including:
Rebar types and their average costs per linear foot include:
Rebar Type | Average Cost per Linear Foot | Details |
Steel | $0.44 – $1.38 | Basic untreated steel, weldable, corrodible |
Stainless Steel | $4.95 – $9.90 | Corrosion-resistant, suitable for saltwater areas, maintenance-free |
Galvanized | $1.32 – $1.76 | Zinc-coated, resists corrosion and abrasion |
Fiberglass | $0.72 – $2.75 | Corrosion-resistant, lighter than steel |
Labor costs for rebar installation typically range from $1.10 to $1.93 per square foot, excluding material costs. For a concrete driveway, the total installation cost falls between $4.40 and $8.80 per square foot, which includes pouring and finishing the concrete.
Here’s a breakdown of estimated costs for installing rebar:
Factor | Cost per Square Foot |
Rebar Materials | $0.44 – $2.48 |
Installation Labor | $1.10 – $1.93 |
Total Cost to Install | $1.54 – $4.41 |
While DIY installation can save costs, rebar installation requires expertise in concrete properties and the use of specialized tools. Improper installation can lead to structural weaknesses and safety risks. Hiring a professional ensures that rebar is installed correctly, adhering to safety standards, especially for larger or critical structures.
At Estimate Florida Consulting, we offer detailed cost estimates across all major trades, ensuring no part of your project is overlooked. From the foundation to the finishing touches, our trade-specific estimates provide you with a complete and accurate breakdown of costs for any type of construction project.
We take pride in delivering accurate, timely, and reliable estimates that help contractors and builders win more projects. Our clients consistently praise our attention to detail, fast turnaround times, and the positive impact our estimates have on their businesses.
Estimate Florida Consulting has helped us win more bids with their fast and accurate estimates. We trust them for every project!
Submit your project plans, blueprints, or relevant documents through our online form or via email.
We’ll review your project details and send you a quote based on your scope and requirements.
Confirm the details and finalize any adjustments to ensure the estimate meets your project needs.
Receive your detailed, trade-specific estimate within 1-2 business days, ready for your project execution.
561-530-2845
info@estimatorflorida.com
Address
5245 Wiles Rd Apt 3-102 St. Pete Beach, FL 33073 United States
561-530-2845
info@estimatorflorida.com
Address
5245 Wiles Rd Apt 3-102 St. Pete Beach, FL 33073 United States
All copyright © Reserved | Designed By V Marketing Media | Disclaimer