Cost estimation is the process of predicting the expenses required to complete a construction project. It involves detailed analysis and forecasting, considering materials, labor, equipment, permits, and unforeseen challenges. For general contractors in Florida, accurate cost estimation is crucial due to the state’s specific climate considerations, building codes, and fluctuating market conditions.
At Estimate Florida Consulting, we specialize in providing detailed cost estimates tailored to Florida’s construction landscape, helping contractors and developers make informed decisions and avoid costly overruns.
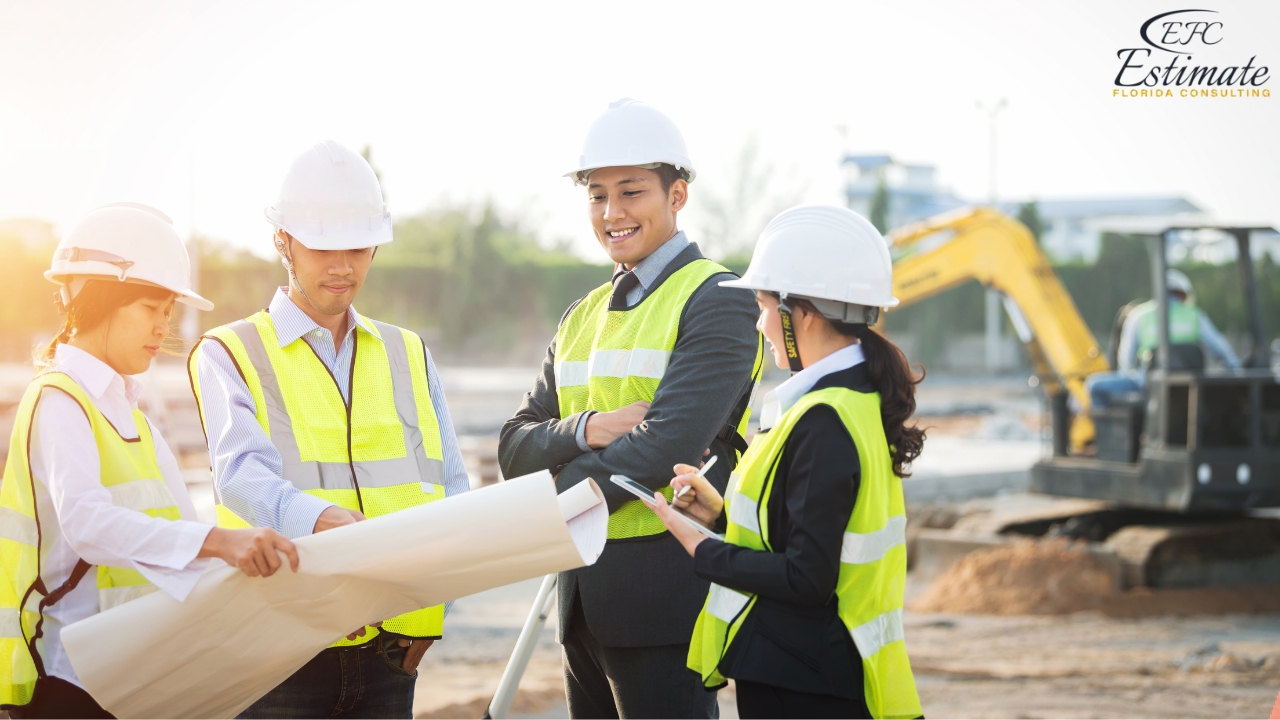
Key Elements of Cost Estimation
Labor Costs
Labor costs form a substantial part of any construction budget and can vary based on several factors, including the number of workers needed, their expertise, and regional wage rates. Skilled trades, such as electricians and plumbers in Florida, typically charge between $60 and $144 per hour, while general labor costs range from $30 to $60 per hour. The type of work required and the project timeline can further influence these expenses.
Material Costs
Material costs depend largely on the type and quality of materials used, along with regional availability and market conditions. Essential materials like lumber, steel, concrete, and fixtures can see price fluctuations. For example, lumber prices in Florida range from $600 to $1,200 per 1,000 board feet, varying by grade and market demand. Higher-quality materials and specialized components naturally incur higher costs.
Equipment Costs
Equipment costs encompass rental fees, purchase prices, and ongoing maintenance. Renting heavy machinery like a backhoe in Florida typically costs between $240 and $600 per day, while purchasing the same equipment may cost over $60,000. Choosing between renting and buying often depends on project size, duration, and equipment needs.
Overhead and Profit Margins
Overhead costs include administrative expenses, insurance, permits, and marketing efforts. To ensure profitability, contractors generally apply a profit margin of 12% to 24% to their estimates. This margin helps cover indirect costs and maintain sustainable operations.
Contingency Costs
Contingency costs are crucial for handling unforeseen expenses, such as weather-related delays, design modifications, or material price increases. Most contractors allocate 6% to 18% of the total project budget as a contingency fund. This ensures financial flexibility to manage unexpected challenges effectively.
Factors Influencing Construction Costs
Project Scope and Complexity
The scope and complexity of a construction project play a major role in determining costs. For example, building a single-family home involves fewer resources and simpler planning compared to a high-rise apartment complex or a commercial shopping mall. Larger and more intricate projects demand specialized skills, additional materials, and more time, which can significantly drive up expenses.
Location and Market Conditions
Construction costs vary widely based on location and market conditions. Regional differences in labor wages, material availability, and overall demand can cause significant fluctuations in project budgets. Urban areas like Miami or Orlando often have higher construction costs compared to smaller towns or rural areas due to greater competition and demand for skilled labor and materials.
Design and Architectural Features
Custom designs and unique architectural features can add significant costs to a project. Incorporating high-end finishes, intricate layouts, or modern design elements often requires the use of premium materials and skilled labor, increasing the overall expense. Tailored designs also tend to extend project timelines, further influencing costs.
Cost Estimation by Project Type
Residential Construction Costs
Residential construction costs in Florida generally fall between $180 and $360 per square foot, depending on the type of home and the finishes involved. Basic homes with standard materials are on the lower end, while custom-built homes and those featuring high-end or luxury finishes can significantly increase the overall cost.
Commercial Construction Costs
Commercial construction, including office buildings, retail spaces, and warehouses, typically costs $240 to $480 per square foot. The final cost depends heavily on the complexity of the design, the level of amenities included, and any specific requirements for the space, such as energy-efficient systems or high-end materials.
Infrastructure Projects
Infrastructure construction, such as roads, bridges, and utilities, involves specialized materials, equipment, and labor. Costs for these projects can start around $600,000 and reach several million dollars, depending on the size, complexity, and location of the project. These large-scale projects often require meticulous planning and advanced engineering solutions to meet local regulations and safety standards.
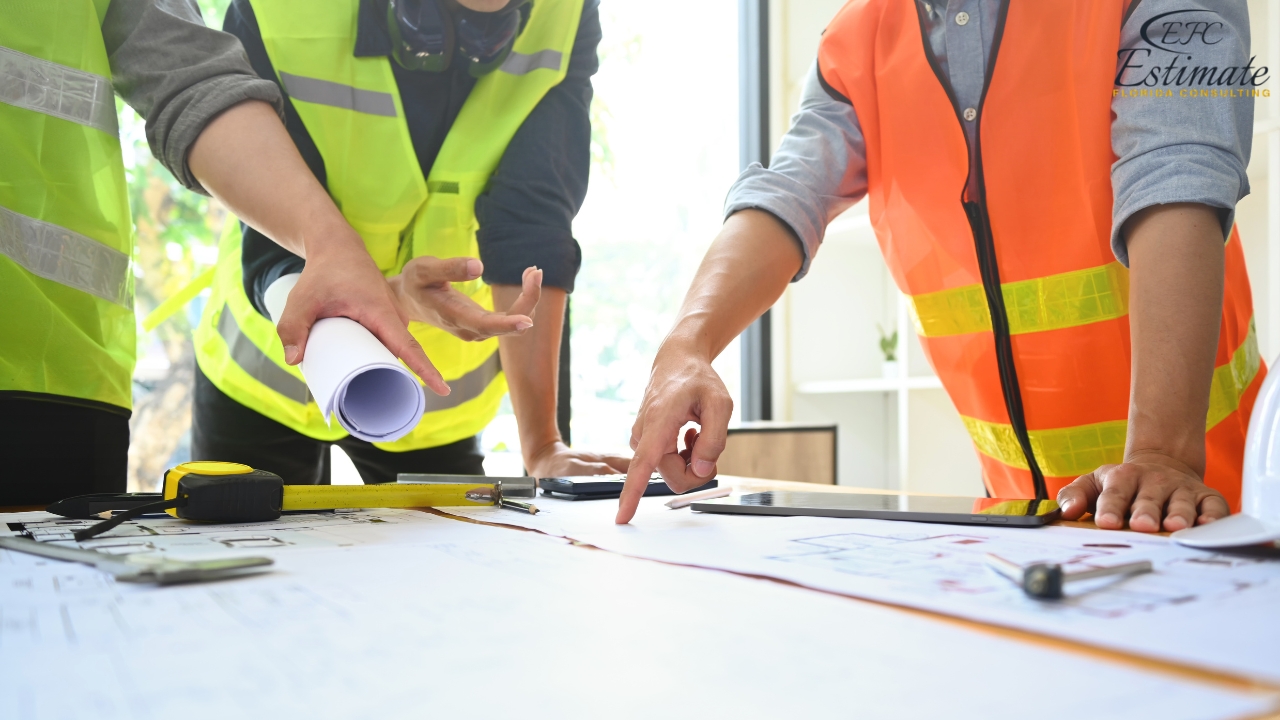
Step-by-Step Cost Estimation Process
Initial Assessment
Start by thoroughly analyzing the project’s overall scope, design specifications, and client expectations. This phase involves an in-depth review of architectural and engineering plans, which helps identify the project’s unique requirements. Site visits are essential to assess the terrain, existing infrastructure, and any potential obstacles that could affect construction timelines or costs. For instance, challenges like poor soil conditions, difficult access routes, or local zoning restrictions should be noted. Additionally, understanding client priorities, such as preferences for sustainable materials or luxury finishes, ensures the estimate aligns with their vision and goals.
Quantity Takeoff
The quantity takeoff process requires a detailed inventory of all materials, labor, and equipment necessary for the project. This step includes calculating precise amounts, such as cubic yards of concrete for foundations, square footage of drywall for walls and ceilings, or the number of fixtures for electrical and plumbing systems. Modern tools, like construction estimating software or Building Information Modeling (BIM), can streamline this process for greater accuracy. A thorough quantity takeoff reduces the risk of material shortages or overordering, which can lead to delays or increased costs. It also allows for adjustments if design changes occur during construction.
Price Sourcing
Price sourcing involves gathering current pricing information for all required materials, labor, and equipment from trusted suppliers and subcontractors. This step is critical because market conditions, such as inflation, material shortages, or labor demand, can significantly affect costs. Building relationships with reliable vendors can help secure competitive pricing or bulk discounts. Additionally, factoring in regional variations, such as higher costs for urban projects compared to suburban ones, ensures your estimate remains realistic. Including an allowance for potential price fluctuations can safeguard against unexpected increases during the project’s duration.
Budget Development
Once all costs are compiled, create a comprehensive budget that accounts for every aspect of the project, including direct expenses, contingency funds, and profit margins. The budget should include allowances for unforeseen issues, such as weather delays or material price hikes, to ensure financial stability throughout the project. Present the estimate in a clear and transparent format, breaking down costs by categories like materials, labor, equipment, and overhead. This not only helps the client understand where their money is allocated but also builds trust. An accurately developed budget serves as a roadmap for the project, ensuring all parties remain aligned on financial expectations.
Win More Projects With Us
Tips for Reducing Costs Without Compromising Quality
- Bulk Purchasing Materials: Ordering construction materials in large quantities can lead to significant cost savings. Bulk discounts from suppliers help lower per-unit costs, especially for commonly used items like drywall, flooring, and fixtures.
- Streamlined Scheduling: Coordinating construction timelines efficiently can minimize labor downtime and avoid unnecessary delays. Proper planning ensures workers and resources are used effectively, reducing overall labor costs.
- Using Alternative Materials: Opt for affordable yet durable alternatives to traditional materials. For example, engineered wood can replace hardwood, and composite materials can serve as cost-effective substitutes for natural stone.
- Incorporating Energy-Efficient Designs: Invest in energy-efficient solutions like LED lighting, high-performance windows, and modern insulation. These upgrades may have a slightly higher upfront cost but can significantly reduce long-term operational expenses for the building.
Common Construction Cost Categories
Site Preparation Costs
Site preparation involves essential tasks like land clearing, excavation, and grading to ensure the land is ready for construction. These costs typically range from $6,000 to $60,000, depending on factors such as the size of the property and site conditions, including soil quality and accessibility.
Material Costs
Material costs often make up a significant portion of the overall construction budget, accounting for 40% to 60% of the total expenses. The selection of high-quality or specialized materials, such as eco-friendly or custom finishes, can substantially impact the overall cost. Material sourcing and availability can also influence the budget.
Get Acquainted with Estimation
Maximize Profits: Budgeting Hacks for Big Construction Projects
Estimating Construction Costs in Bad Weather: What You Need to Know?
Labor Costs
Labor costs vary widely based on the complexity of the project and the skill level required. Highly skilled tradespeople, such as electricians, plumbers, and masons, typically command higher wages, particularly in regions with strong demand for construction services. Labor is a critical component that can fluctuate based on project timelines and local labor markets.
Overhead and Indirect Costs
Overhead expenses, including administrative costs, insurance premiums, permits, and equipment maintenance, often account for about 10% to 20% of the total budget. These costs ensure the smooth operation of the project and include items that are not directly tied to physical construction but are vital for project management.
Contingency Costs
A contingency fund is crucial to address unexpected expenses such as project delays, design modifications, or adverse weather conditions. This financial buffer helps mitigate risks and ensures the project stays on track without compromising quality or deadlines.
Download Template For Construction Project Breakdown
- Materials list updated to the zip code
- Fast delivery
- Data base of general contractors and sub-contractors
- Local estimators
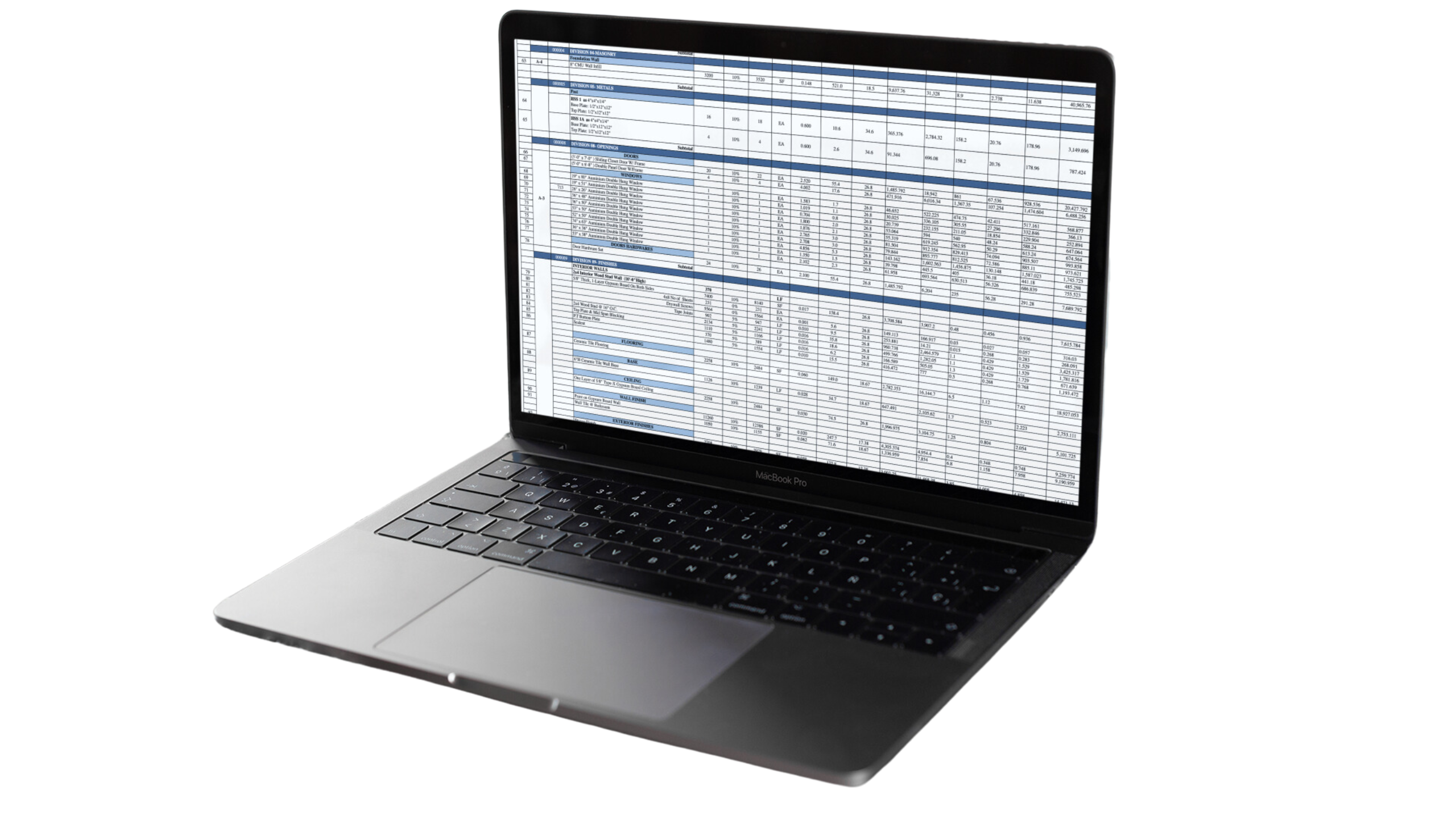
Conclusion
Accurate cost estimation is the cornerstone of successful construction projects, particularly in Florida’s unique market. It ensures that general contractors can navigate regional challenges, adhere to budgets, and meet client expectations effectively. By factoring in key elements such as labor, materials, equipment, and contingency costs, contractors can make informed decisions and mitigate risks. At Estimate Florida Consulting, we are committed to delivering detailed, reliable estimates tailored to Florida’s construction landscape. Our expertise helps contractors and developers optimize resources, reduce costs, and achieve project success with confidence. Partner with us for precise estimates that drive results.
Question Answer
Frequently Asked Question
Cost estimation is the process of predicting the total expenses required to complete a construction project. It involves analyzing and forecasting costs related to materials, labor, equipment, permits, and potential unforeseen challenges.
Accurate cost estimation is crucial in Florida due to the state’s unique climate, building codes, and fluctuating market conditions. It helps contractors avoid cost overruns and make informed decisions, ensuring project profitability and compliance with regulations.
- Labor Costs: Vary based on worker expertise and regional wage rates, with skilled trades in Florida charging $60–$144/hour and general labor $30–$60/hour.
- Material Costs: Depend on material type, quality, and market conditions; for example, lumber ranges from $600 to $1,200 per 1,000 board feet.
- Equipment Costs: Include rentals ($240–$600/day for heavy machinery) and purchases (e.g., $60,000+ for a backhoe).
- Overhead and Profit Margins: Typically, contractors add 12–24% for overhead and profit.
- Contingency Costs: 6–18% of the total budget is reserved for unforeseen expenses.
- Project Scope and Complexity: Larger or intricate projects, like high-rises, demand more resources and skilled labor.
- Location and Market Conditions: Costs differ between urban (e.g., Miami) and rural areas due to labor and material availability.
- Design and Architectural Features: Custom designs with unique finishes or layouts increase expenses.
- Residential Construction: $180–$360/sq ft for homes, depending on finishes.
- Commercial Construction: $240–$480/sq ft, influenced by design complexity and amenities.
- Infrastructure Projects: Costs start around $600,000 and vary widely based on scale and engineering needs.
- Initial Assessment: Analyze project scope, design, and site conditions.
- Quantity Takeoff: Calculate exact material, labor, and equipment needs.
- Price Sourcing: Gather real-time pricing from suppliers and subcontractors.
- Budget Development: Create a comprehensive budget, including contingencies and profit margins.
- Bulk Purchasing: Saves costs on frequently used materials like drywall or flooring.
- Streamlined Scheduling: Reduces labor downtime with efficient planning.
- Alternative Materials: Opt for durable, cost-effective materials like engineered wood.
- Energy-Efficient Designs: Invest in upgrades like LED lighting to reduce long-term costs.
- Site Preparation Costs: $6,000–$60,000, depending on size and conditions.
- Material Costs: Make up 40–60% of total costs, with specialized materials costing more.
- Labor Costs: Depend on trade complexity, timelines, and market demand.
- Overhead and Indirect Costs: Include permits, insurance, and administration, typically 10–20% of the budget.
- Contingency Costs: Set aside funds for unexpected challenges, typically 6–18% of the total budget.
Comprehensive Trade-Specific Estimates
At Estimate Florida Consulting, we offer detailed cost estimates across all major trades, ensuring no part of your project is overlooked. From the foundation to the finishing touches, our trade-specific estimates provide you with a complete and accurate breakdown of costs for any type of construction project.
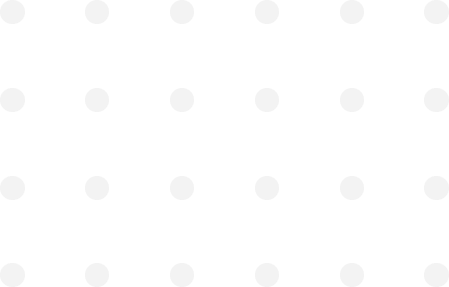
Testimonials
What Our Clients Say
We take pride in delivering accurate, timely, and reliable estimates that help contractors and builders win more projects. Our clients consistently praise our attention to detail, fast turnaround times, and the positive impact our estimates have on their businesses.
Estimate Florida Consulting has helped us win more bids with their fast and accurate estimates. We trust them for every project!
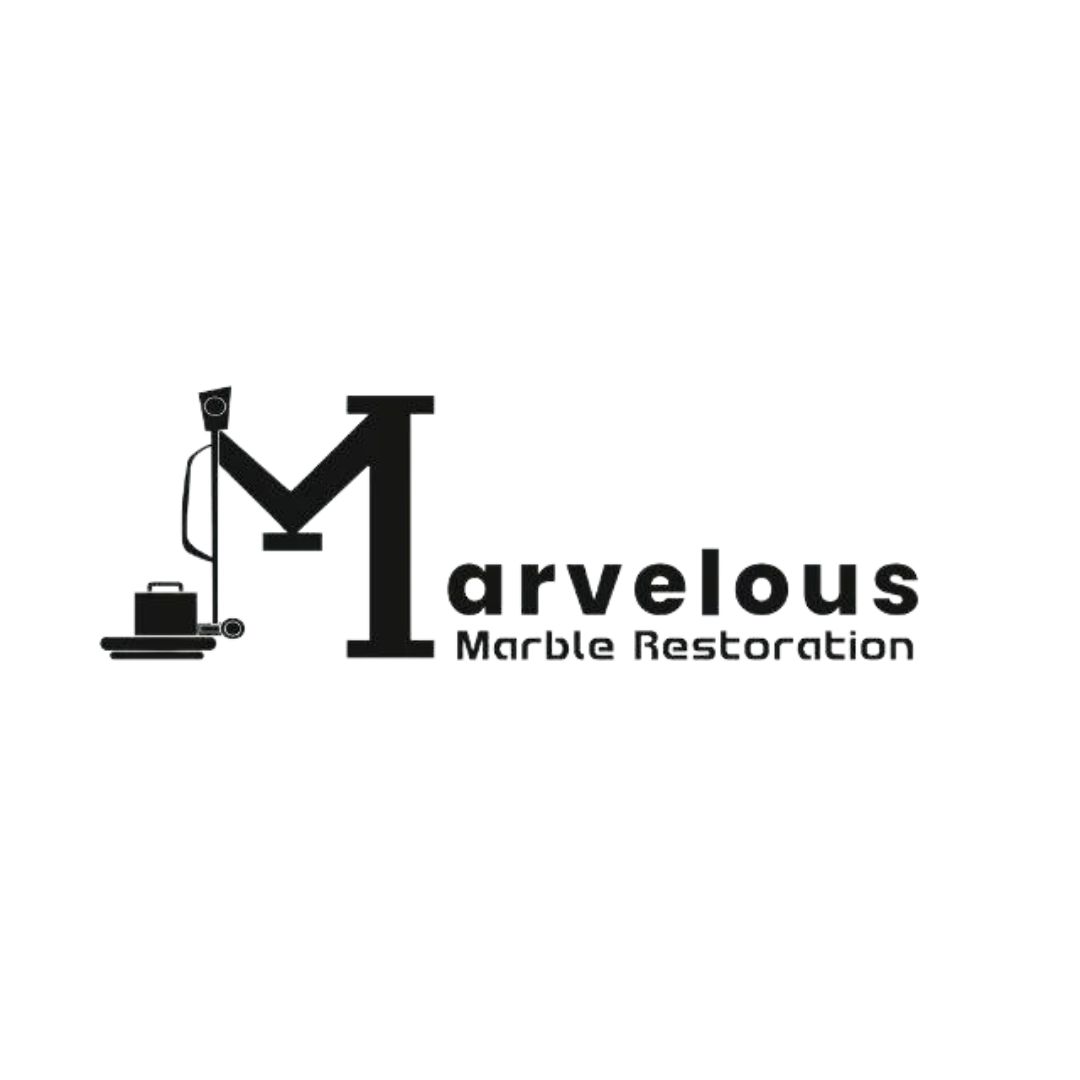
Steps to Follow
Our Simple Process to Get Your Estimate
01
Upload Plans
Submit your project plans, blueprints, or relevant documents through our online form or via email.
02
Receive Quotation
We’ll review your project details and send you a quote based on your scope and requirements.
03
Confirmation
Confirm the details and finalize any adjustments to ensure the estimate meets your project needs.
04
Get Estimate
Receive your detailed, trade-specific estimate within 1-2 business days, ready for your project execution.
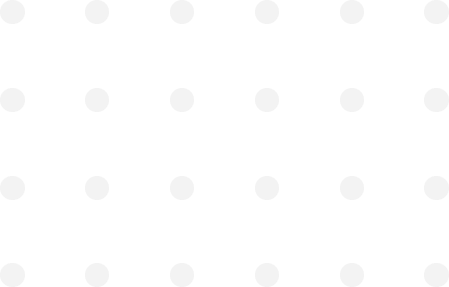