Why Shop Drawings Are the Backbone of Efficient Design-Build Projects?
Have you thought about how large construction projects stay on schedule and avoid expensive errors? The answer is frequent shop drawings. These are a type of drawing that provides details on how specific components will be manufactured and assembled in a building. Unlike general design plans, shop drawings pay attention to the details that ensure every part functions and fits together appropriately. They do not allow any gaps in communication between builders, fabricators, and engineers.
In design-build projects where speed and coordination are vital, shop drawings enhance the effectiveness of the streamlined processes. In this blog, we’ll explain why shop drawings are essential and how they translate designs into sturdy, fully completed structures.
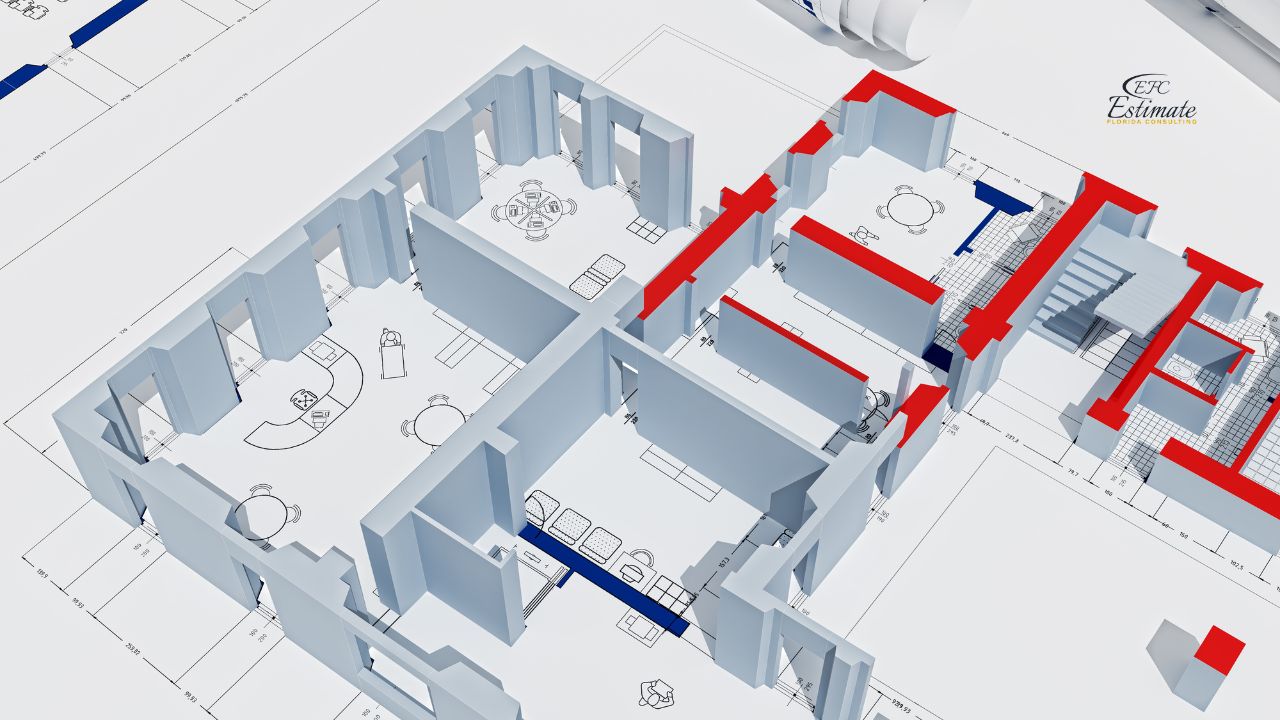
What Are Shop Drawings?
Shop drawings are defined as comprehensive illustrations of architectural or engineering designs that include precise measurements, materials, fabrication methods, and assembly instructions. Shop drawings can provide more detailed and accurate information than construction drawings or 3D construction rendering services.
They also show the subsequent stages of the prefabrication process after creating the design requirements and drawings. Another way to think of shop drawings is as the development of building drawings. From trusses, concrete panes, and stainless steel beams to electrical layouts, ducts, cabinets, lifts, and equipment, these designs include a variety of prepared components.
The most typical specifications included in shop drawings are as follows:
- Any important work site measurements that need to be confirmed and examined prior to component installation and manufacturing
- Any changes or departures from the original construction and design blueprints
- Physical dimensions, detailed instructions, production procedures, and material specifications are examples of component manufacturing data.
- Experienced architectural drafting professionals created thorough and detailed drawings of the prefabricated components from various perspectives.
- Comprehensive references that demonstrate how the prefabrication design satisfies the original construction and design documents’ requirements and specifications
- A connection diagram, detailed instructions, and a list of all the necessary supplies that will be purchased in order for a successful installation are examples of information necessary for component installation and assembly.
- The dates of the initial drawing and the subsequent changes
- The project’s number and title
Why Should We Call It the Backbone of the Project?
It is believed that shop drawings form the backbone of the entire manufacturing process. They participate in every step of the building and restoration project. Shop drawing services in Florida, which include measurements, production standards, and manufacturing specifications, are typically required for prefabricated components. For the AEC to accomplish error-free, cost-effective, and timely work in the rapidly evolving construction sector, shop drawings are also essential.
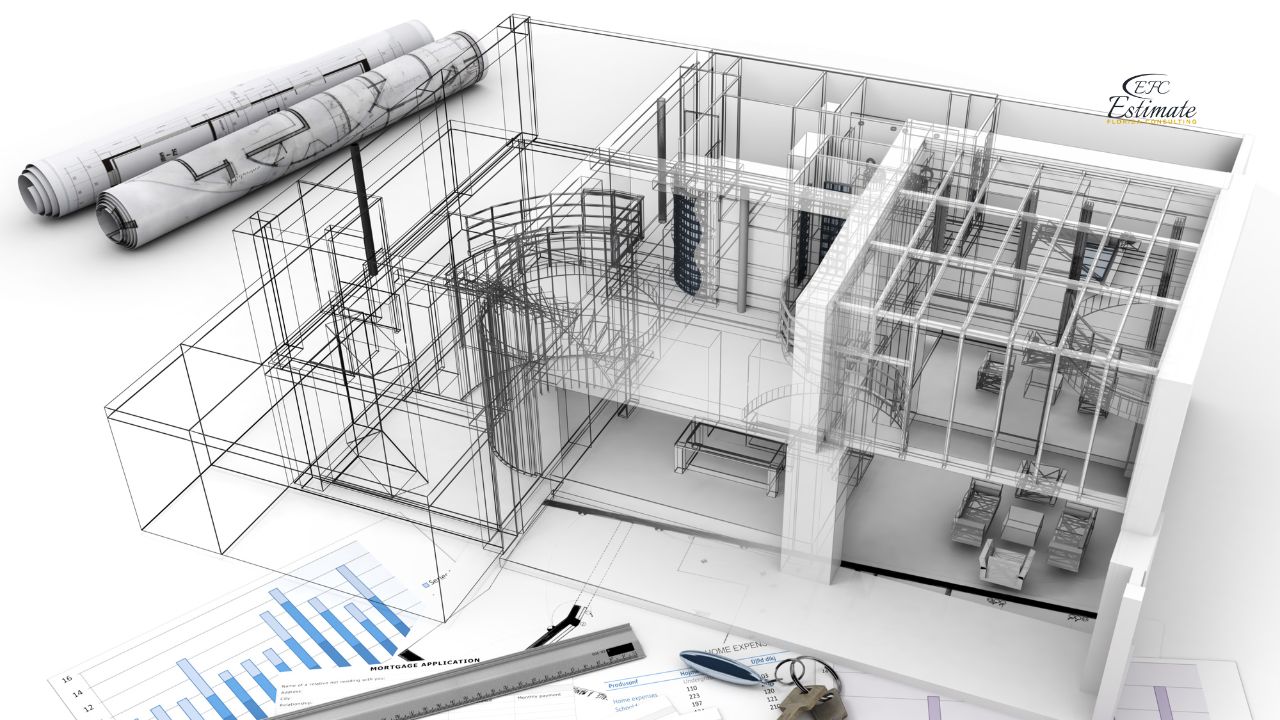
The Key Role of Shop Drawings
Reducing Errors and Misunderstandings
Accurate shop drawings greatly reduce construction errors, which can ruin projects. Without appropriate shop drawings, accurate dimensions, materials, and assembly processes can lead to erroneous assumptions that can be a blunder. Inaccurate shop drawings can lead to huge monetary and resource-related waste.
Consider a custom display fixture in a retail space; if the shop drawing is missing some details or is inaccurate, the fixture won’t fit as it’s supposed to, leading to redesign and reconstruction costs. To mitigate these problems, accurate shop drawings enable precise detailing, ensuring that all necessary and accurate parts are available, thus eliminating the need for material assembly.
Encouraging Compliance with Regulations
Shop drawings are created to match particular local building codes, safety standards, and other checklists for compliance. Inspection prerequisites also incorporate certain markups on fire rating, structural bonding, and material ratings that are passed off within the blueprints provided.
Shop drawings, when complemented with compliance documentation, provide a greater value that permits project teams to reduce burdens associated with last-minute scope changes. A greater deal of oversight works to ensure all design aspects of the components are tailored to the specified laws and regulations. Compliance aspects lessen the chances that the work delivered will serve to be the basis for non-compliance litigation.
Improving Communication
Enhancing communication in relation to retail projects is one of the main functions of shop drawings, which assist in preparing effective construction documents. Everyone from the architects to the contractors receives the shop drawing, which assists them in understanding, fulfilling, and handing over the requirements. This alignment helps in fulfilling the objectives of the entire pre- and post-construction retail project and minimizes the chances of delays and misunderstandings.
Improve the Construction Project’s Efficiency
One can make the construction project seamless with accurate and detailed shop drawings. They provide clear details, which, in turn, makes the installation of components such as fixtures less problematic from a time perspective. This can improve the completion timelines of construction projects, which would allow retailers to open their stores earlier.
Moreover, accurate shop drawings can enable contractors to guess what materials and tools will be required for each phase of work in advance. If project teams have accurate, detailed prerequisites, then planning for labor and materials will be much more efficient.
Strategies to Ensure Precision in Drawings for Shops
In order to reap the maximum rewards of shop drawings in retail developments, it is necessary to adhere to certain guidelines while crafting them. Here are a few guiding points that one should keep in mind:
Communicate During the Entire Design Process
Architects, contractors, and fabricators must work together as a team from the very beginning of a project and throughout all phases of construction in order to create precise shop drawings. Including stakeholders in the design phase lets potential roadblocks be resolved well in advance. It can be achieved through dialogue, coordination, and formal communication structures.
Review and Revisions
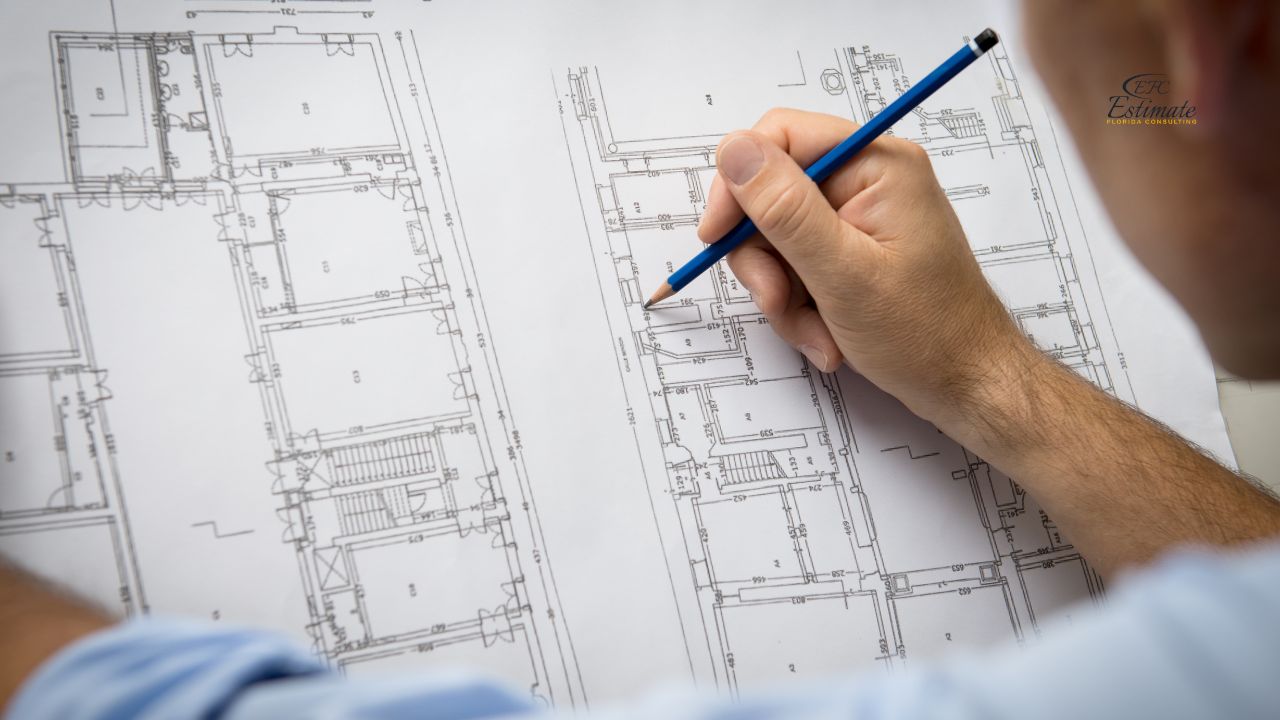
After shop drawings are created, they should be accompanied by a thorough review, which must be the last step in the process. This review should involve a multitude of different stakeholders so that all opinions are taken into consideration. Address anything that must be altered before fabrication is started.
Apply State-of-the-Art Technology
In order to further polish the accuracy of shop drawings, using them alongside other advanced tools such as Building Information Modeling (BIM) and other Computer Aided Designing (CAD) technologies greatly aids in detecting problems contractually and other complex schemata representations, leading to conflict resolution prior to the start of the work procedures.
Add All Relevant Details
In terms of specifications, a shop drawing must include all relevant details, including the measurements, type of materials, finishing, and assembly instructions. The greater the detail, the smoother the process will be for the contractors and fabricators.
Organize Records
All drawings, changes made, and even approvals given concerning the correctly completed construction shop drawings must be cataloged appropriately throughout the project. There are bound to be construction issues that will require some form of constructive conflict resolution, and retaining these documents ensures that such differences can be solved while still being held accountable.
Final Thought
Precision in shop drawings significantly impacts the success of construction projects. It improves communication, error reduction, legal compliance, and overall construction flow. Retailers and project teams stand to lose a lot of money because, without detailed shop drawings, they can never ensure that their designs are executed as intended.
The best practices of collaboration, implementation of technology, detailed specification writing, and documentation all work towards improving drawings’ preciseness, interdisciplinary coordination, and shop drawings that capture pictorial representation of construction details. In the fast-paced retail sector, having the ability to construct sophisticated and appealing shopping spaces that satisfy client needs hinges on the accuracy and importance of these documents.
Question Answer
Frequently Asked Question
Construction drawings are the base factor for any building project. They convert the architect's idea into a thorough blueprint that engineers, builders, and contractors can adhere to. It is essential to comprehend these designs in order to ensure that a project is carried out precisely and effectively.
Yes, they must be reviewed and approved by architects or engineers before construction begins. It ensures that everything meets the design and safety standards.