A Wining Cost Estimate
That Helps You To Win More Construction Projects
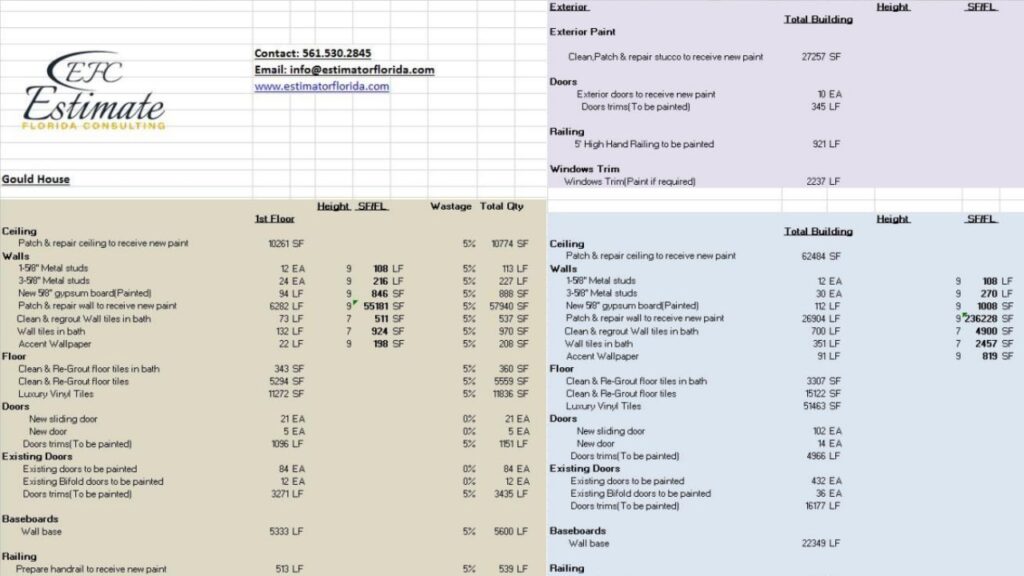
A Construction Material Takeoff is a calculation process. It helps contractors figure out the cost of a project and make sure they have the right amount of materials. Specialists use blueprints and other documents. They look at dimensions, weight, and measurements to find out how much of each material they need.
It’s important for those conducting the takeoff to know the details in the design documents. Don’t risk not having enough materials! Get professional help with your material takeoff. It’s like cooking without knowing the ingredients. Avoid disaster – get a Construction Material Takeoff
In construction projects, determining the amount and type of materials needed is crucial for the success and profitability of the project. The process of identifying and quantifying the materials required for construction is referred to as material takeoff.
To understand the importance of material takeoff, let us look at the following table, which highlights the benefits of a thorough material takeoff process.
A well-executed material takeoff is essential for reducing waste and excess costs associated with over-ordering materials. It also allows contractors to obtain accurate estimates of project costs and timelines, as well as effectively schedule and allocate resources. Moreover, it helps promote effective communication between project stakeholders, such as contractors, architects, and suppliers.
Pro Tip: Implementing a digital software solution for material takeoff can simplify the process and improve accuracy.
In summary, material takeoff is a critical component of construction projects, and implementing a thorough and accurate process can positively impact project success and profitability.
Money talks, but an accurate budget and cost estimation screams.
Accurate budget and cost estimation is key for a successful construction project. This can be achieved through proper methods of material takeoff.
The table below explains some factors that influence these aspects:
Factor | Description |
---|---|
Project Type | Bigger projects need more resources, people and machines. |
Material Cost | Market demand and supply affects raw material prices. |
Labor Costs | Skilled labor availability and workload affects costs. |
Timeframe | Longer timeframes typically raise costs due to inflation and resource scarcity. |
Analyzing these factors during material takeoff can provide a realistic expense estimation. It also helps find areas where costs can be cut with no compromise on quality.
Accurate budget and cost estimation during material takeoff also allows for better planning and scheduling, reducing the chances of delays or interruptions caused by lack of resources or incorrect estimates. This leads to timely project delivery.
Pro Tip: Tech such as software tools for material takeoff can streamline the process, and reduce human errors that may occur during manual calculations.
Material planning is like trying to fit a puzzle together while blindfolded and wearing mittens!
A table below shows the importance of Material Planning and Resource Allocation for construction projects. It displays different stages of a project and the materials required for each stage, with the allocated resources for each task.
Stage | Materials Needed | Resources Allocated |
---|---|---|
Excavation | Tools, Trucks, Fuel | Excavators, Dumpers, Operators |
Foundation | Mixers, Cement, Bars | Masons, Carpenters, Crane Operator |
Framework | Bricks/Blocks/Panels, Mortar | Bricklayers, Scaffolders |
Finishing | Paints/Coatings/Varnish/Flooring | Painters/Flooring Workers |
Material Planning involves figuring out what raw materials are needed for each stage. Resource Allocation is about assigning workers with skills suited to the task.
Good material planning starts by inspecting plans closely and deciding what needs to be bought or ordered. Plus, when those items need to be delivered. If access to the site is limited, alternate logistics will have to be used or third-party delivery services.
A study showed how bad Material Planning and Resource Allocation led to extra costs and late completion times (one year behind). This proves how essential Material Planning and Resources allocation are for construction projects.
Material utilization is key to successful construction projects. Optimizing materials consumption leads to less waste and more productivity. This boosts efficiency throughout the project.
Material takeoff is the process of estimating the amount and type of material needed. This helps avoid waste and improve productivity. Calculating the right quantity of materials also helps plan better and carry out tasks efficiently.
Material takeoff can reveal potential wastage spots. Teams can then re-examine specs or find alternative solutions. This helps them stay responsible and manage rising costs due to mismanagement.
Recently, an automated material takeoff system cut down costly errors from manual processes. O.C.R technology can capture data from PDF plans, too. This digital tech controls hazards and provides a paperless, ethical approach.
Construction is politely telling you to hurry up with material takeoff – delay is just another way of saying it.
The importance of a comprehensive material takeoff is essential for successful construction projects. Ignoring this process can lead to project delays and interruptions. Analyzing and estimating correctly help professionals to determine the exact amount of materials needed, in order to finish the project on time.
Errors and omissions in the project scope can result in costly modifications or even work stoppages. To avoid this, contractors should prioritize a thorough material takeoff. This includes recognizing the materials necessary for the job, as well as predicting potential changes that occur during the project.
Technology has changed how companies approach material takeoffs for construction. By using various software solutions, personnel can accurately estimate prices and improve labor allocation with real-time data. A strategic and efficient builder will add value to the field.
Not giving importance to material takeoff planning can cause major problems in the future. Many have experienced delays due to incorrect calculations or bad material planning. Adopting the best practices and using innovative technology will help ensure clarity between the teams involved in building projects. Flip a coin and pray it doesn’t land on its edge when trying to decide between manual or digital material takeoff!
Construction projects require accurate material takeoff estimates in preparation for procurement. Types of Material Takeoff Methods include counting and calculating material quantity, measuring footage, and estimating by weight, volume, or area.
Types of Material Takeoff Methods:
Method | Description | Pros | Cons |
Counting and Calculating Material Quantity | Count and calculate each material unit for accurate estimates | Accuracy, precision, and consistency of estimates | Time-consuming and prone to errors |
Measuring Footage | Measure the length, width, and height of a structure | Quick and easy to measure multiple dimensions | May miss small details or variations |
Estimating by Weight, Volume or Area | Estimate material quantity based on standardized weights, volumes, or areas | Quick and easy method for standard materials | May not consider site-specific requirements or customization |
In addition to the above methods, material takeoff can also be performed using Building Information Modeling (BIM) software. This method provides an accurate 3D model of a building, allowing for accurate estimates of building materials and quantities.
Pro Tip: Always use the same material takeoff method consistently throughout the project to ensure accuracy and consistency.
Forget high-tech tools, manual material takeoff is the original workout for your brain and biceps.
Hands-on Material Takeoff is a tedious manual process that requires calculations and estimations to find out the exact amount of materials needed for construction projects. It’s different from digital methods and takes more effort, but gives professionals more control and accuracy.
The International Journal of Engineering Development and Research claims that manual material takeoff is popular in developing countries, due to limited access to digital tools and a lack of technology infrastructure.
Calculators and spreadsheets can make material takeoff easier. You’ll soon feel like a mathlete!
The ways and instruments used to generate material takeoff differ based on the scope and size of the project.
It could range from manual counting to digital tools and software; a combination of these may also be applied. For an efficient understanding of the various methods used in material takeoff, a table showing strengths and weaknesses of each approach is required. See below:
Method | Description |
Manual Counting | Physically counting materials |
Excel Spreadsheet | Manual data entry in an Excel worksheet |
2D Takeoff Software | Digital measuring tool for 2D surfaces |
BIM-Based Takeoff | Utilizing BIM models for quantity estimation |
It’s noteworthy that 2D takeoff software offers speedy results and cuts down errors related to manual counting, while BIM-based takeoff is most suitable for bigger projects with complex designs.
To get the best out of the material takeoff process, it is suggested to use software tools that provide automation features such as precise measurements, easy customization, and real-time updates. It’s also essential to keep records updated during the construction phase, as modifications may occur or extra materials may be needed.
Material takeoff methods offer both pros and cons. For instance, the quantity survey method is accurate but slow. Whereas, the assembly method is fast but may lead to errors.
Each project has its own unique needs, so understanding these requirements is vital. With accurate info at the pre-tender stage, decision-making is easier.
Comprehending material takeoff methods helps ensure a successful project from start to finish. Who needs a measuring tape? Get digital with digital material takeoff.
Digital takeoff estimation is a great way for construction professionals to quickly and accurately measure the materials needed for a project. It uses user-friendly tools to extract data from digital project drawings.
Benefits of this process include:
Tools used in the process include:
Additionally, digital takeoffs generate accurate cost estimates, minimize errors and provide detailed records of previous projects. It also enables stakeholders to collaborate in real-time.
A report from Allied Market Research estimates that the global construction estimating software market will reach $4.6 billion by 2027, with a CAGR of 10.2%. Let’s explore the tools and processes used for material takeoff – math and spreadsheets can be exciting!
The way and tools used for material takeoff varies based on a project’s specific needs. Here are three methods:
Cloud-based tools enable teams to collaborate in real time from any place. They can also offer features such as updates when design changes.
Prioritise accuracy over speed when doing the material takeoff. Even minor mistakes can cause expensive rework. Knowledge is key here – not ignorance.
Maximize your construction business’s potential with our competitive financing options
Material takeoff has many advantages and drawbacks. It’s important to be aware of these before deciding which method to use for a construction project. Here is what to keep in mind:
Selecting a method might depend on project size or budget. Each has its place in certain contexts. Remember, a successful material takeoff is essential. People have been using various techniques for construction since ancient times. Guessing and hoping for the best is part of material takeoff, but accuracy is still key.
The Accuracy of Construction Material Calculations
Construction material takeoff accuracy is heavily dependent on several factors. These factors include the complexity of the project, the quantity and extent of material variations, and the experience of the estimator. Other important factors include the accuracy of the blueprints and specifications, the quality of the design drawings, the availability of updated material prices, and the quality of the software or tools used for calculations.
Factors Column 1 | Factors Column 2 |
Project Complexity | The quantity and extent of material variations |
Estimator Experience | The accuracy of the blueprints and specifications |
Accuracy of Blueprints and Specifications | The quality of the design drawings |
Quality of Design Drawings | Availability of updated material prices |
In addition to these factors, the location of the project, the type and size of the material to be used, and the expected time frame for completion can also impact the accuracy of calculations. Estimators need to use accurate data, keep track of changes in project design, and update material prices regularly to ensure reliable calculations. They must also have a good understanding of building codes, safety protocols, and material requirements to minimize errors.
It is also important to ensure that the estimator is using the latest tools and software to perform material takeoffs. These tools can help automate calculations, identify inconsistencies, and improve overall accuracy. Regular training and education can keep estimators up-to-date with the latest trends and technologies.
“Designing a project may sound glamorous, but it’s really just a fancy way of saying ‘figuring out how many bricks you need’.”
Project scope impacts material takeoff accuracy. The more comprehensive and defined the scope, the simpler it is to work out how much material is needed. A well-defined scope specifies materials, budget and timeline.
Inaccurate or unclear scope leads to material takeoff errors. It’s important to have open communication between parties involved in the project. This way, scope changes are documented and communicated.
Good communication of project scope means accurate material takeoff and reduced risk of shortages or overages. If changes are necessary during the project, project managers must adjust calculations but stay within the budget.
Before starting the project, design and scope should be analyzed. This helps planners to anticipate problems and plan for them. Reliable software tools like BIM can help reduce human error.
To conclude: Defining design and goals early is essential. Clear communication among stakeholders lets you manage uncertainties instead of making last-minute decisions that can affect budgets or timeframes. Quality counts when it comes to material takeoff data. Unless you’re using a bathroom scale.
In construction estimation, data quality and availability have a big impact on material takeoff accuracy. Here is how:
Data Factor | Effect on Accuracy |
Availability | The more data there is, the more accurate the result. |
Relevance | Data that meets project requirements gives better accuracy than irrelevant or outdated information. |
Consistency | Inconsistencies in data sources reduce confidence in results and accuracy. |
We had one experience where a specification was missed, leading to erroneous measurements. We had to start all over and be careful to follow project requirements. It was a hard lesson in paying attention to detail.
Accurate material takeoff seems to be as hard to find as unlimited resources and time in construction.
Material takeoff accuracy is impacted by resource and time availability. When resources are scarce, essential tools like updated software and reference docs might not be accessible. Plus, when time is limited, wrong estimates can reduce quality and affect success.
For some companies or clients, unrealistic deadlines are set without considering project size or complexity. This timeline forces professionals into a rush, leading to inaccurate quantity estimates. Also, without safety protocols or training, work takes longer.
To improve material takeoff accuracy, asset management systems need robust software and electronic communication platforms. Also, project timelines should be based on project details. Further, certifications and education help protect worker safety and better the company’s bottom line. Upgrade to software for smoother material takeoffs!
Software Solutions and Tools for Material Takeoff
An essential part of construction, material takeoff is a detailed process of identifying and estimating the required materials for a construction project. In today’s technological era, several software solutions and tools can save time and improve accuracy. Here are some of the most widely used software tools and solutions for material takeoff:
Software Tool | Description |
AutoCAD | Advanced software for 2D and 3D modeling and design. Bluebeam Revu Specialized software tool for estimators, designers and contractors for creating electronic charts, documents, catalogs, and more. |
PlanSwift | Easy and efficient takeoff software for construction companies of all sizes. |
Stack | Preconstruction and bidding software that helps you save time and prepare accurate estimates. |
Other software tools and solutions include BuildingConnected, On Center Software, Sigma Estimates, and more.
Pro Tip: To choose the best software solution for material takeoff, prioritize software with advanced features that perfectly match your business needs. Conduct proper research, read software reviews, and consult with experts or professionals before making any decision.
Managing construction materials just got a digital upgrade – say goodbye to sticky note chaos and hello to streamlined organization with material management software.
Construction Material Management Software is a must-have for the construction industry. It helps professionals keep an eye on their raw materials. It offers accuracy and convenience.
Features like estimating and purchasing help teams collaborate. It also tracks inventory levels and spending. So, contractors, architects, and engineers like it.
The software makes databases, tracks costs, and keeps suppliers in line. It provides info on production schedules, availability, and market visibility.
This software has been around for a while. Now, with tech advancements, construction managers have better results from them. Get accurate material takeoffs without any trouble. Enjoy features and benefits of modern software – no degree needed!
Material Takeoff Software: Enhancing Accuracy and Efficiency in Construction Projects.
Construction projects require careful management of material estimation. But fear not, Material Takeoff Software is here with its amazing features and benefits! These include:
Plus, it has unique functionalities like the ability to export results into different file formats such as CSV, Excel or PDF. And, it integrates with popular design/CAD programs to make the process even smoother.
To make the most of Material Takeoff Software, here’s what to do:
It’s like choosing your favorite child – you’ll love Material Takeoff Software too!
Glimpse into the Unique Features and Functionalities of Material Takeoff Software!
Compare various software options available in the market with their prices, features and functionalities.
Software Name | Price | Features | Functionality |
Bluebeam Revu | $399/user (standard edition) | Collab | Tools, Estimation Tools, Markup tools Cross-platform, Cloud-hosted collaboration |
PlanSwift | $1595 (perpetual license) | Digital takeoff templates, Calibration tools, Annotation tools | All-in-one solution for bidding to management |
eTakeoff Dimension | Starting at $495/user/year (full version) | Highly specialized measurement capabilities with second-mouse tech… | On-screen takeoff integration across multiple software |
RoadEng Civil Engineer SE | $2,495/year or $4,495/perpetual licence(standalone version) | Pavement design capability along with incorporation of advanced designing tools. Includes customization on site settings and overviews of products data | Offers widest range of measuring units for accurate calculations |
Furthermore, you can integrate BIM & CAD for planning and costing. Select the software that best fits your organisation’s needs and budget.
Pro Tip: Before you choose a takeoff software, look into the customer support quality. It is essential to clear up any confusion regarding usage or implementation in your workflow.
Now, let’s get ready to start measuring and taking off!
A construction material takeoff involves estimating the quantities and costs of all materials required for a construction project. Here’s how to create one:
Gather resources for construction by obtaining a clear description of all materials needed. Look at both construction drawings and specs to get comprehensive info. Review every detail of the drawings and specs collected and check for accuracy in material, quantity, dimension, and other details. To be extra sure, ask a professional to check for missing or wrong items.
Now calculate material quantity and tools needed – time to get creative!
It’s critical to do an exact takeoff and accurate estimates to determine the necessary tools and calculate material quantity. Various considerations and approaches might be needed.
Steps to follow:
For construction materials and costs, it’s essential to do a cost calculation and make a Bill of Materials (BOM). This helps with budgeting and avoiding shortages or overages.
Create a table with columns like Material Name, Quantity Required, Unit Cost, Total Cost and Supplier. Fill it with true and accurate data to avoid confusion or wrong estimates.
Material Name | Quantity Required | Unit Cost | Total Cost | Supplier |
Cement 100 bags | 100 bags | $10 | $1000 | ABC Industries |
Gravel 10 tons | 10 tons | $50 | $500 | XYZ Construction |
Concrete blocks 500 blocks | 500 blocks | $2.5 | $1250 | DEF Builders |
Enter material details and cost per unit in the table. Calculate the total cost by multiplying the quantity and unit cost, then add supplier information if you need more.
Recording BOM details accurately is critical to avoid problems during construction. An organized BOM helps track material inventory.
A friend recently shared how they forgot to calculate costs for a project. This caused them to run out of funds midway through construction. Preparing an accurate BOM helps to predict potential problems and plan ahead.
Make sure you don’t order ten tons of gravel instead of ten bags, unless you’re trying to build a mini Mount Everest in your backyard!
Getting organized and executing effectively is key to carrying out a successful plan for procurement and distribution of construction materials. Here’s how:
Material takeoff is vital in the construction industry. It guarantees the right materials are requested and project estimates are precise. Technology has progressed, suggesting future trends will include automated material takeoff solutions such as AI software and predictive analytics. Professionals in the industry working together can enhance accuracy and speed of material takeoff processes. This will lead to more successful construction projects.
A construction material takeoff is the process of calculating the quantity of materials needed for a construction project.
A material takeoff is important because it gives the contractor an accurate estimate of the cost and quantity of materials needed for the project.
A construction estimator or a quantity surveyor typically performs a material takeoff.
The steps involved in a material takeoff typically include reading the plans and specifications, identifying the items to be counted and measured, taking off quantities, and recording the information in a format that can be used for estimating.
tools required for a construction material takeoff may include a calculator, a scale ruler, a measuring tape, a digital plan reader, and software programs for estimating and takeoff.
A construction material takeoff can be very accurate if it is done by a skilled estimator who is familiar with the project, the materials used and the methods of construction. However, unforeseen changes in the project scope or unforeseen circumstances can affect the accuracy of a material takeoff.
Here I am going to share some steps to get your construction cost estimate report.
You can send us your plan on info@estimatorflorida.com
Before starting your project, we send you a quote for your service. That quote will have detailed information about your project. Here you will get information about the size, difficulty, complexity and bid date when determining pricing.
We do construction cost estimating and prepare a detailed report for your project. At last you finalize the report and finish the project.
561-530-2845
info@estimatorflorida.com
Address
5245 Wiles Rd Apt 3-102 St. Pete Beach, FL 33073 United States
561-530-2845
info@estimatorflorida.com
Address
5245 Wiles Rd Apt 3-102 St. Pete Beach, FL 33073 United States
All copyright © Reserved | Designed By V Marketing Media | Disclaimer
IMPORTANT: Make sure the email and cell phone number you enter are correct. We will email and text you a link to get started.
By clicking “I Agree” above you give Estimate Florida Consultin express written consent to deliver or cause to be delivered calls and messages to you by email, telephone, pre-recorded message, autodialer, and text. Message and data rates may apply. You are able to opt-out at any time. You can text STOP to cancel future text messages.