Boost Your Warehouse Bids – Request a Precision Estimate!
- Accurancy
- Efficiency
- Transparency
- Customization
- Time Saving
- Professionalism
- Cost Control
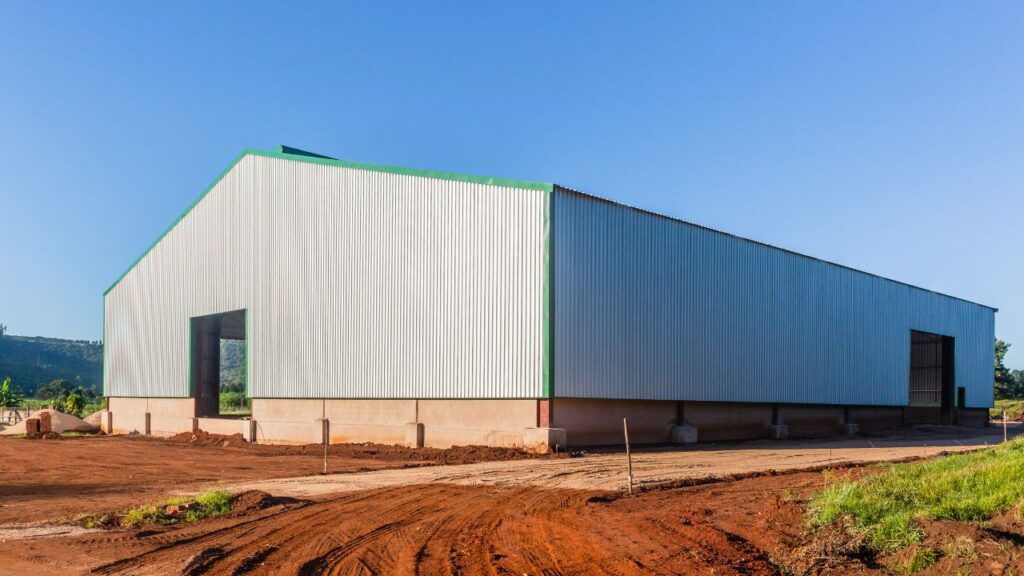
The cost of warehouse racking is a significant consideration for businesses optimizing their storage space. The price can vary based on the type of racking system and its specifications. On average, warehouse racking costs fall within the range of $50 to $200 per pallet position. Single-deep pallet racks, which are more straightforward in design, generally come at a lower cost, ranging from $50 to $80 per pallet position. These racks are suitable for efficient access to individual pallets. In contrast, double-deep pallet racks, which allow for higher storage density but limit immediate accessibility, typically have a higher price range of $75 to $105 per pallet position.
The total expense of warehouse racking also depends on factors such as rack height, load capacity, and any additional features like adjustable shelving or specialized rack configurations. It is advisable for businesses to assess their specific storage needs, consult with professional rack suppliers, and obtain detailed quotes to make informed decisions about the most cost-effective and efficient warehouse racking solution for their operations.
Fully Insured Licensed Hire a Contractor For Warehouse
Hire ContractorMake Informed Design Decisions Showcase Your Design Ideas
Get RenderingSeveral factors influence the cost of warehouse racking, making it crucial to consider these elements before making any investment. The type of pallet racks, storage capacity requirements, material quality, customization options, and specialized features all contribute to the overall cost. Understanding the interplay of these factors is essential for making informed decisions that align with your business needs and budget constraints.
Single-deep pallet racks, as the name suggests, allow for the storage of pallets in a single row. These racks are known for their simplicity and accessibility. The design allows for easy access to each pallet position, making them suitable for businesses with a high inventory turnover.
The cost of single-deep pallet racks typically ranges from $50 to $80 per pallet position. However, this estimate can vary based on several factors. Material quality is a significant cost influencer, with high-strength steel racks costing more than standard options. Additionally, the size of the racks, adjustable beam features, and the inclusion of safety features such as mesh decking or rack guards can contribute to variations in cost.
Adjustable beams offer flexibility in accommodating varying pallet sizes. The inclusion of safety features, such as mesh decking to prevent items from falling through, adds to the overall cost. Additional accessories like rack guards protect against forklift damage but also impact the budget. Businesses must carefully evaluate these options to strike a balance between cost and functionality.
While single-deep racks are cost-effective and easy to navigate, they may not be the most space-efficient option. The advantages lie in their simplicity and quick access to inventory. However, for larger warehouses with space constraints, the cost-effectiveness may be outweighed by the need for increased storage density. Businesses with a high inventory turnover rate may find the accessibility of single-deep racks advantageous, but careful consideration is necessary to determine if the benefits align with operational needs.
Double-deep pallet racks allow for two pallets to be stored in a row, doubling storage density compared to single-deep racks. This design optimizes available space and is suitable for businesses with a higher volume of products but less frequent inventory turnover.
The cost for double-deep pallet racks can range from $75 to $105 per pallet position. The primary factor influencing this cost is customization. Tailoring the racks to specific needs, such as specialized beam configurations or corrosion-resistant materials, can contribute to higher costs. A crucial consideration is the impact of aisle width on accessibility. Narrower aisles may require specialized forklifts, affecting maneuverability and potentially increasing labor costs.
The distance between racks, or aisle width, is a critical consideration. Narrow aisles maximize storage density but require specialized forklifts with extended reach capabilities, impacting both upfront and operational costs. Wider aisles, while reducing the need for specialized equipment, sacrifice some storage density. Businesses must carefully assess their inventory characteristics and operational needs to determine the most cost-effective aisle width.
While double-deep racks offer increased storage density, they may pose accessibility challenges. Forklifts with extended reach are often required, impacting maneuverability and potentially increasing labor costs. The advantages lie in the efficient use of available space, making them suitable for businesses with high-volume, low-frequency inventory turnover. Careful consideration of the specific needs of the operation is crucial in deciding between single and double-deep options.
Customization adds a layer of flexibility to warehouse racking systems. Businesses can tailor the racks to accommodate specific product dimensions, weight requirements, or unique storage needs. However, customization comes at an additional cost. Specialized features, such as seismic bracing for earthquake-prone regions or temperature-resistant coatings for cold storage, can increase the overall expense. While customization adds to the upfront cost, businesses must assess the long-term benefits and operational efficiency gained through tailored solutions.
Investing in professional installation services is paramount for ensuring the stability and safety of your racking system. Installation costs can vary based on factors such as rack complexity, site preparation requirements, and local labor rates. While some businesses may consider DIY installation to cut costs, professional installation ensures compliance with safety standards and reduces the risk of structural issues. Site preparation costs, including leveling the floor and addressing any structural deficiencies, are additional considerations impacting the overall installation budget.
Regular maintenance is essential for the longevity and efficiency of warehouse racking. Maintenance expenses include routine inspections, repairs, and replacements of damaged components. On average, businesses can expect to allocate 1-2% of the initial racking investment for annual maintenance costs. Neglecting maintenance can lead to safety hazards, reduced efficiency, and increased long-term expenses. It’s crucial to factor in these ongoing costs when estimating the total cost of ownership for a warehouse racking system.
Analyzing the long-term benefits of warehouse racking is essential for making informed investment decisions. Improved efficiency, reduced labor costs, and optimized space utilization contribute to a positive ROI. Calculating potential ROI based on different scenarios, such as increased inventory turnover or operational expansion, provides a clearer picture of the investment’s financial impact over time. Businesses must consider the lifespan of the chosen racking system and how it aligns with future growth and changes in operational requirements.
While warehouse racking is a popular storage solution, comparing costs with alternative options is crucial. Traditional shelving, mezzanine systems, and automated storage and retrieval systems (AS/RS) are among the alternatives. Real-world cost examples, considering factors like installation, maintenance, and space utilization, provide insights into the cost-efficiency of racking systems. Businesses should weigh the benefits and drawbacks of each option to determine the most cost-effective solution based on their unique needs and budget constraints.
Future-proofing your warehouse racking investments involves considering scalability and adaptability. Investing in modular racking systems that can be easily reconfigured to accommodate changing storage needs minimizes the need for costly replacements. While upfront costs for scalable systems may be slightly higher, the long-term savings from avoiding complete system overhauls justify the investment. Evaluating the expected lifespan of the racking system and its compatibility with future technology and industry trends ensures a wise investment that withstands the test of time.
Different industries may have unique warehouse requirements, influencing the choice and cost of racking systems. For example, the pharmaceutical industry may require climate-controlled storage, impacting material choices and costs. Tailoring the racking system to specific industry needs ensures optimal functionality and cost-effectiveness. Compliance with industry regulations and standards may also affect costs, making it imperative for businesses to understand the unique requirements of their sector.
As sustainability becomes a growing concern, exploring eco-friendly options in warehouse racking can positively impact both costs and environmental responsibility. Recyclable materials, energy-efficient design, and sustainable manufacturing practices contribute to a greener warehouse. While initial costs for sustainable options may be slightly higher, businesses benefit from reduced energy expenses and potential tax incentives. It’s essential to consider the long-term environmental and financial benefits when evaluating sustainable warehouse racking options.
Identifying common pitfalls in estimating and investing in warehouse racking helps businesses avoid unnecessary expenses and make informed decisions. Overlooking future expansion needs, neglecting regular maintenance, and underestimating customization requirements are common mistakes that can lead to cost overruns. Real-world examples of businesses facing challenges due to these mistakes serve as cautionary tales for prospective investors. Learning from the experiences of others is a valuable strategy in ensuring a smooth and cost-effective implementation of a warehouse racking system.
Understanding the costs associated with warehouse racking is crucial for businesses aiming to optimize their storage systems. By considering factors such as rack type, customization, installation, ongoing maintenance, and future-proofing, businesses can make informed decisions that contribute to long-term efficiency and cost savings. Conducting a thorough cost analysis and exploring the diverse options available ensure that your investment aligns with both your immediate needs and future goals. Warehouse racking is not just a storage solution; it’s a strategic investment in the overall success of your business.
The type of pallet racks, storage capacity requirements, material quality, customization options, and specialized features all contribute to the overall cost.
Customization options can influence both the cost and efficiency of the racking system. Specialized features may incur additional expenses, but they can cater to unique storage needs.
Yes, professional installation is crucial for ensuring stability and safety. DIY installation may compromise structural integrity, leading to safety hazards.
Factors such as improved efficiency, reduced labor costs, and optimized space utilization contribute to a positive ROI. Calculating potential ROI based on specific business scenarios provides clarity on the investment’s financial impact.
The estimate generated by the tool is a rough approximation based on the provided input and standard cost parameters. Actual costs may vary due to unforeseen circumstances or changes in project specifications.
Here I am going to share some steps to get a warehouse racking cost estimate report.
You can send us your plan on info@estimatorflorida.com
Before starting your project, we send you a quote for your service. That quote will have detailed information about your project. Here you will get information about the size, difficulty, complexity and bid date when determining pricing.
Our team will takeoff and estimate your project. When we deliver you’ll receive a PDF and an Excel file of your estimate. We can also offer construction lead generation services for the jobs you’d like to pursue further.
561-530-2845
info@estimatorflorida.com
Address
5245 Wiles Rd Apt 3-102 St. Pete Beach, FL 33073 United States
561-530-2845
info@estimatorflorida.com
Address
5245 Wiles Rd Apt 3-102 St. Pete Beach, FL 33073 United States
All copyright © Reserved | Designed By V Marketing Media | Disclaimer