Boost Your Machanical Bids – Request a Precision Estimate!
- Accurancy
- Efficiency
- Transparency
- Customization
- Time Saving
- Professionalism
- Cost Control
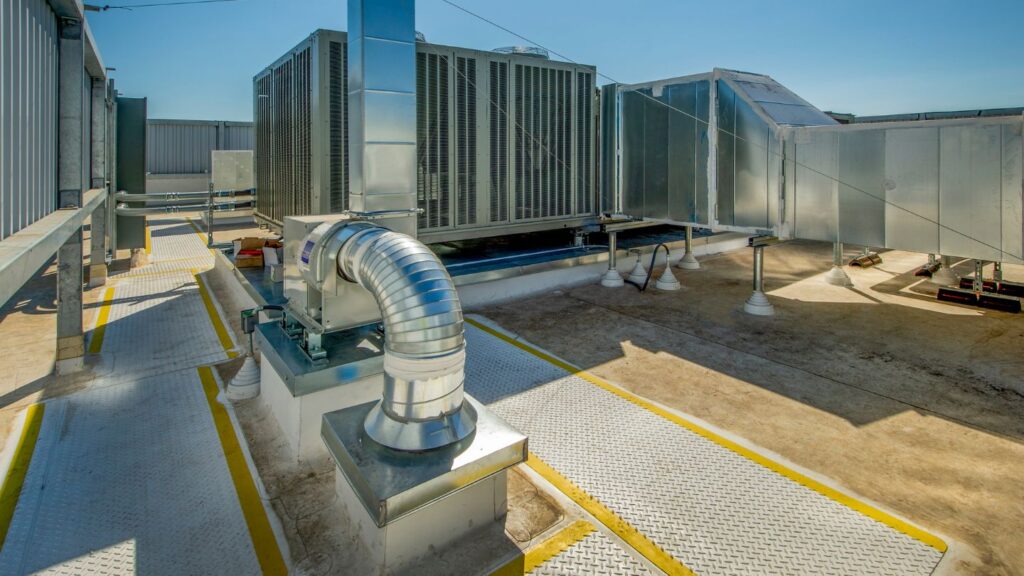
Effective climate control within a warehouse is crucial for maintaining the integrity of stored goods and ensuring a comfortable working environment for employees. Heating, ventilation, and air conditioning (HVAC) systems play a pivotal role in achieving these objectives. Determining the cost of warehouse HVAC on a per-square-foot basis involves considering various factors, each influencing the overall expenses. In this article, we’ll explore the key components that contribute to the cost of warehouse HVAC systems.
The size of a warehouse is a fundamental factor influencing HVAC costs. Larger warehouses necessitate more extensive heating, ventilation, and air conditioning (HVAC) systems to achieve and maintain uniform temperature and ventilation throughout the facility. The sheer volume of air that needs conditioning in a larger space requires powerful HVAC systems, contributing to higher upfront and operational costs. Efficient system design becomes crucial to ensure optimal performance while managing costs, as larger spaces often present more complex challenges in maintaining consistent environmental conditions.
Fully Insured Licensed Hire A Contractor For Mechanical Contractor
Hire ContractorMake Informed Design Decisions Showcase Your Design Ideas
Get RenderingThe level of insulation and the efficiency of the building envelope are critical considerations in determining HVAC costs. Well-insulated warehouses equipped with energy-efficient windows and doors create a more stable internal environment. This not only enhances the comfort of the workspace but also significantly reduces the workload on the HVAC system. By minimizing heat transfer through walls and ceilings, a well-insulated building can lower operational costs, as the HVAC system doesn’t need to work as hard to regulate temperatures. Investing in quality insulation and airtight building envelopes can lead to substantial long-term energy savings.
The climate and geographical location of a warehouse play a pivotal role in HVAC requirements and costs. Warehouses located in extreme climates, characterized by either very high or very low temperatures, demand more robust HVAC systems to cope with temperature variations. In colder climates, efficient heating systems are crucial, while in hotter regions, powerful cooling systems are essential. Additionally, local energy prices and the availability of renewable energy sources can influence operating costs. Adaptations to climate considerations should be factored into the selection and design of HVAC systems for optimal efficiency and cost-effectiveness.
The number of employees, equipment, and machinery within a warehouse directly contribute to the overall heat load. High occupancy or the presence of energy-intensive equipment increases the demand on the HVAC system to maintain a comfortable indoor environment. The type of equipment and its usage patterns also influence the size and specifications of the HVAC system. Proper assessment and consideration of occupancy and equipment factors are essential to ensure that the HVAC system meets the specific needs of the warehouse without unnecessary oversizing, which could lead to higher installation and operational costs.
The choice of HVAC system has a substantial impact on overall costs. Various systems, such as Variable Refrigerant Flow (VRF), rooftop units, and centralized systems, come with different installation and maintenance expenses. While energy-efficient systems may have higher upfront costs, they often result in long-term savings through reduced energy consumption. The selection of the most suitable HVAC system should align with the specific requirements of the warehouse, considering factors like space layout, usage patterns, and energy efficiency goals.
Compliance with building codes and environmental regulations is a crucial aspect of warehouse HVAC systems, and it may contribute to additional costs. Meeting specific standards, such as energy efficiency requirements or air quality standards, can impact the selection, installation, and ongoing operation of HVAC equipment. Failure to comply with regulations may result in penalties and fines. Therefore, careful consideration of regulatory requirements is necessary to ensure that the HVAC system not only meets operational needs but also aligns with legal and environmental standards. Thorough planning and consultation with experts can help navigate compliance challenges while managing associated costs effectively.
The building’s size stands as a pivotal determinant in assessing HVAC installation costs, with larger structures demanding increased heating and cooling capacity, often requiring more intricate systems, thus leading to higher installation and maintenance expenses.
For residential homes, which typically feature smaller dimensions, the average HVAC installation cost for a single-family dwelling ranges from $6,000 to $14,400. In contrast, commercial buildings incur considerably greater costs, often falling within the range of $18,000 to $60,000 or more, contingent upon both size and installation complexity.
Here is an adjusted guideline for HVAC installation costs based on square footage:
1,000 – 2,000 square feet: $6,000 – $10,800
2,000 – 3,000 square feet: $10,800 – $14,400
3,000 – 4,000 square feet: $14,400 – $19,200
4,000 – 5,000 square feet: $19,200 – $24,000
These estimates are subject to variation based on specific building needs, encompassing factors such as insulation levels, window efficiency, and other elements that influence overall energy efficiency.
Beyond the fundamental HVAC installation expenses, there typically arise supplementary costs associated with upgrades and personalized enhancements. Homeowners or business proprietors might opt for additional features, including:
When approximating the overall cost of HVAC installation, it becomes crucial to factor in considerations such as building size, equipment efficiency and features, as well as any supplementary upgrades or customization. Collaborating with a reputable HVAC contractor is essential for a comprehensive estimate that considers these factors, allowing for effective project planning:
Choosing HVAC systems with high energy efficiency ratings, such as Seasonal Energy Efficiency Ratio (SEER) for air conditioners and Annual Fuel Utilization Efficiency (AFUE) for furnaces, is a strategic investment in long-term savings. While these systems may entail slightly higher upfront costs, their reduced energy consumption leads to substantial operational efficiencies over time. High SEER-rated air conditioners, for instance, optimize cooling performance while minimizing electricity usage, making them environmentally conscious and cost-effective choices.
Ensuring accurate sizing of HVAC systems is paramount to avoiding inefficiencies, excessive energy consumption, and potential operational issues. Professional assessments by HVAC experts are invaluable in determining the optimal system size tailored to the specific needs of the space. An undersized system may struggle to meet demand, leading to increased wear and higher utility bills, while an oversized system may cycle on and off frequently, diminishing overall efficiency. Proper sizing, guided by expert evaluation, ensures optimal performance and long-term cost savings.
Implementing a proactive maintenance schedule is crucial for the prevention of breakdowns, the enhancement of system performance, and the extension of equipment lifespan. Regular tune-ups, including thorough filter cleaning and refrigerant level checks, contribute to optimal efficiency by addressing potential issues before they escalate. This not only ensures the system operates at peak performance but also reduces the risk of costly repairs and premature replacements, thus optimizing long-term cost-effectiveness.
The integration of smart thermostats represents a forward-thinking approach to precise control over heating and cooling schedules. These intelligent devices adapt to occupancy patterns, optimizing temperature settings based on real-time needs. Additionally, smart thermostats enable remote monitoring and control, fostering energy savings and lower utility bills. Their adaptive capabilities ensure that heating and cooling systems operate efficiently only when necessary, contributing to both comfort and economic sustainability.
Zoning systems offer a sophisticated solution to building climate control by dividing a space into different temperature zones. This approach allows for granular control over heating and cooling, enhancing comfort and reducing energy consumption by conditioning only occupied areas. By directing conditioned air precisely where needed, zoning systems contribute significantly to energy efficiency and operational cost savings, particularly in larger or multi-use buildings.
Obtaining detailed estimates from multiple reputable HVAC contractors and comparing bids is a crucial step in ensuring a cost-effective installation without compromising quality. These bids should encompass equipment costs, labor, and additional expenses. By evaluating bids based on value and expertise, property owners can make informed decisions, selecting a contractor who not only meets budgetary constraints but also demonstrates the competence required for a successful and efficient HVAC installation. This careful selection process contributes to long-term satisfaction and optimized cost efficiency.
cost-efficient warehouse HVAC installation hinges on key considerations. Warehouse size impacts costs, emphasizing the need for strategic system design. Prioritizing insulation, efficient building envelopes, and energy-efficient systems minimizes operational expenses.
Factors like climate, occupancy, and equipment influence HVAC efficiency. Choosing the right system type is critical for long-term savings. Regulatory compliance ensures standards are met but may incur additional costs.
Average installation costs based on building size, adjusted by 20%, provide useful estimates. Strategies for cost efficiency stress energy-efficient systems, proper sizing, and modern technologies. Meticulous planning and collaboration with reputable contractors are vital for success and economic viability, ensuring a comfortable indoor environment while optimizing costs.
Effective climate control in warehouses is essential to maintain the integrity of stored goods and provide a comfortable working environment for employees.
Larger warehouses require more extensive HVAC systems, leading to higher upfront and operational costs due to the increased volume of air that needs conditioning.
Well-insulated warehouses with energy-efficient windows and doors create a stable internal environment, reducing HVAC workload and operational costs.
Warehouses in extreme climates may require more robust HVAC systems to cope with temperature variations. Local energy prices and renewable energy availability also influence operating costs.
The number of employees, equipment, and machinery contribute to the overall heat load, impacting the size and specifications of the HVAC system.
The choice of HVAC system, such as Variable Refrigerant Flow (VRF) or rooftop units, influences installation and maintenance costs. Energy-efficient systems may have higher upfront costs but lead to long-term savings.
Compliance with building codes and environmental regulations may result in additional costs, but it ensures the HVAC system aligns with legal and environmental standards.
For residential homes, costs range from $6,000 to $14,400, while commercial buildings may incur expenses between $18,000 to $60,000, depending on size and complexity. Adjusted guidelines based on square footage are provided in the article.
Here I am going to share some steps to get your warehouse HVAC cost estimate report.
You can send us your plan on info@estimatorflorida.com
Before starting your project, we send you a quote for your service. That quote will have detailed information about your project. Here you will get information about the size, difficulty, complexity and bid date when determining pricing.
Our team will takeoff and estimate your project. When we deliver you’ll receive a PDF and an Excel file of your estimate. We can also offer construction lead generation services for the jobs you’d like to pursue further.
561-530-2845
info@estimatorflorida.com
Address
5245 Wiles Rd Apt 3-102 St. Pete Beach, FL 33073 United States
561-530-2845
info@estimatorflorida.com
Address
5245 Wiles Rd Apt 3-102 St. Pete Beach, FL 33073 United States
All copyright © Reserved | Designed By V Marketing Media | Disclaimer