Warehouse Electrical Installation Cost Estimator
When it comes to estimating the cost of an electrical installation for a warehouse, there are a number of factors to consider.
The size of the warehouse will play a major role in determining the cost of the electrical installation. A larger warehouse will require more wiring, fixtures, and other electrical components, which will increase the cost.
The amount of power needed to run the warehouse’s equipment and machinery will also impact the cost of the electrical installation. Be sure to factor in the power requirements of any large equipment or machinery when estimating the cost.
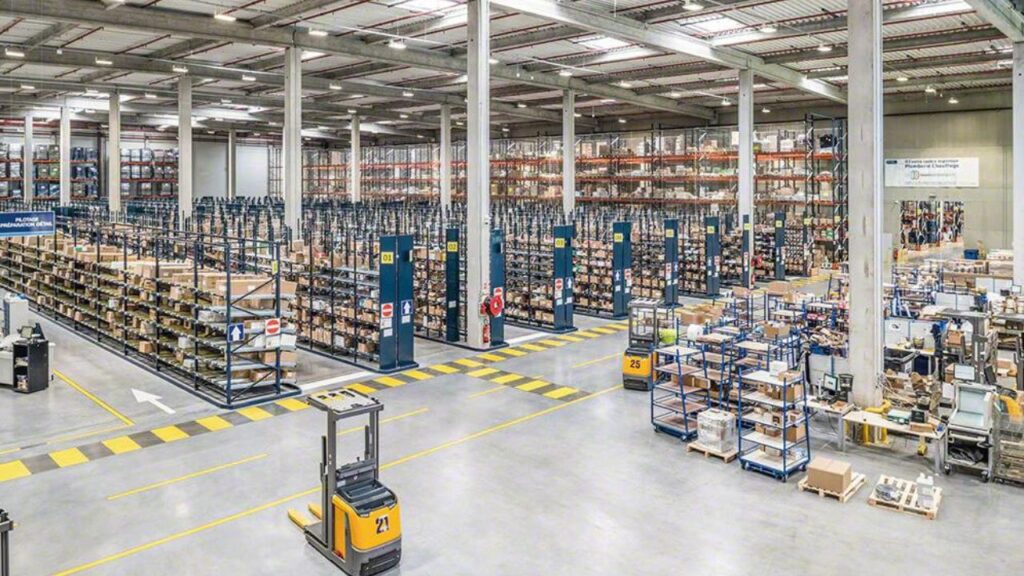
For a small warehouse (less than 10,000 square feet), you can expect to pay anywhere from $12,000 to $24,000 for the electrical installation. For a medium-sized warehouse (between 10,000 and 50,000 square feet), the cost will likely range from $24,000 to $55,000. For a large warehouse (over 50,000 square feet), the cost could exceed $120,000 or more, depending on the specific requirements of the installation.
Need Estimate & Materials For Warehouse Electrical Installation?
We help Residential & Commercial Contractors to win more projects with higher accuracy.
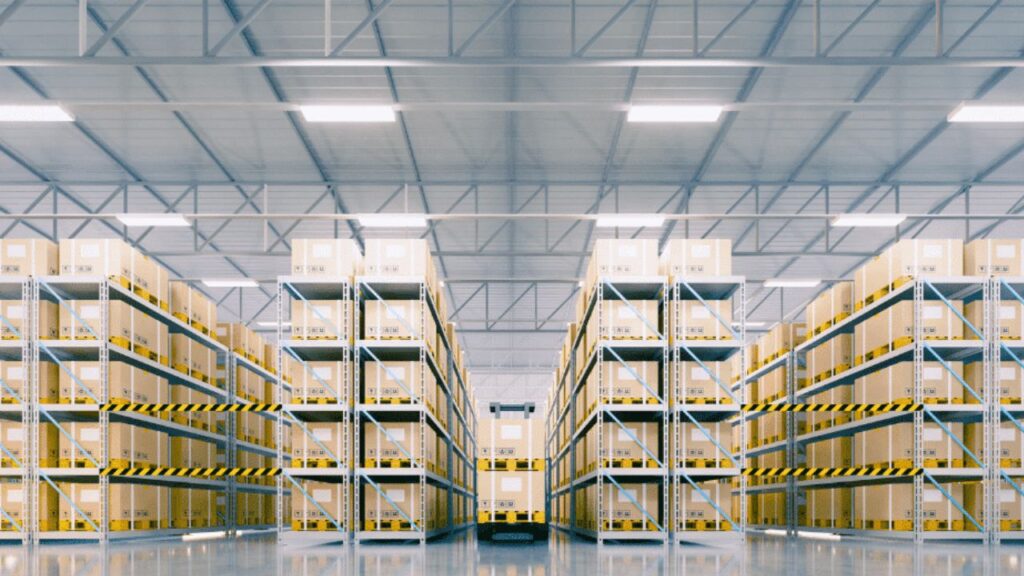
Warehouse Electrical Wiring Cost Estimator
The size of the warehouse will play a significant role in determining the cost of wiring installation. A larger warehouse will require more wiring, which will increase the cost. The type of wiring you choose for the warehouse will also impact the cost. Copper wiring is generally more expensive than aluminum wiring, but it is also more durable and has a longer lifespan.
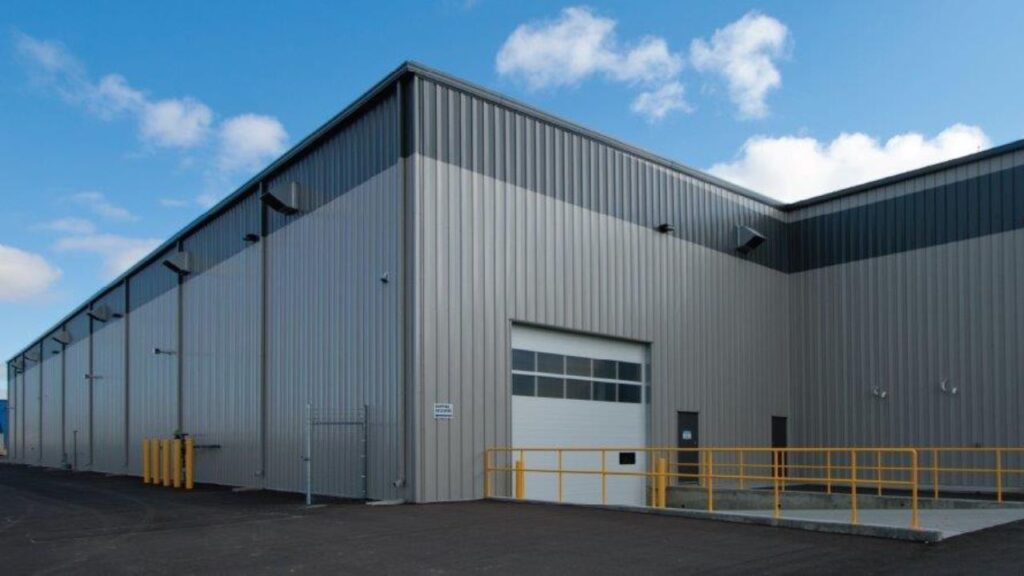
The size of the warehouse will play a significant role in determining the cost of wiring installation. A larger warehouse will require more wiring, which will increase the cost. The type of wiring you choose for the warehouse will also impact the cost. Copper wiring is generally more expensive than aluminum wiring, but it is also more durable and has a longer lifespan.
We Help Electrical Contractors To Get More Leads
We help Residential & Commercial Contractors to grow your business online
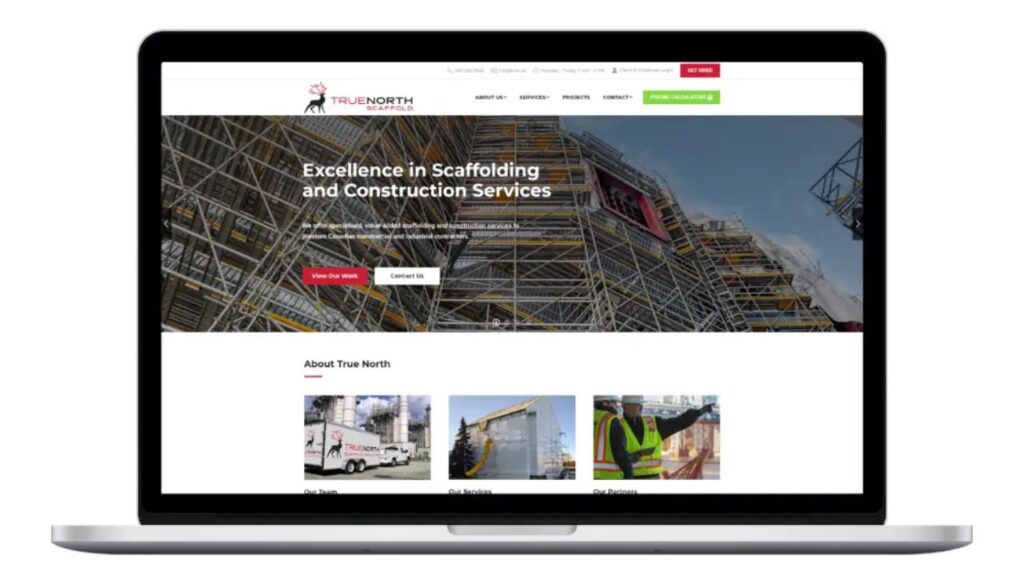
Warehouse Electrical Wiring Takeoffs
Warehouse electrical installation takeoffs service is a service offered by electrical contractors or construction estimators. It involves creating a detailed list of materials and labor required for the electrical installation of a warehouse project.
The takeoff process involves reviewing the project plans and specifications, identifying all electrical components and materials required, and quantifying the amount of each item needed. This includes wiring, outlets, lighting fixtures, switches, panels, conduits, and other electrical components.
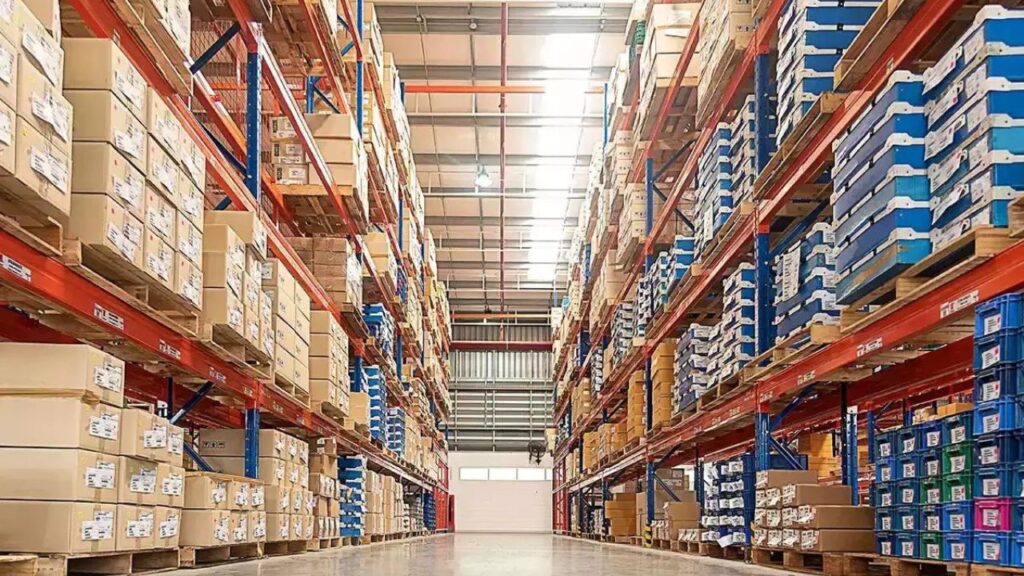
By providing a comprehensive electrical takeoff, the contractor or estimator can provide the client with an accurate estimate of the cost of the electrical installation. This allows the client to make informed decisions regarding the project and helps to avoid unexpected costs or delays down the line.
Get Warehouse Electrical Wiring Cost Estimate
We help Residential & Commercial Contractors to win more projects with higher accuracy.
Warehouse Electrical Panel Installation Estimator
To provide an accurate cost estimate for a warehouse electrical panel, We would need some more information such as:
- Size of the warehouse
- Number of electrical panels required
- Type and capacity of the panels needed
- Location of the warehouse
- Labor costs for installation
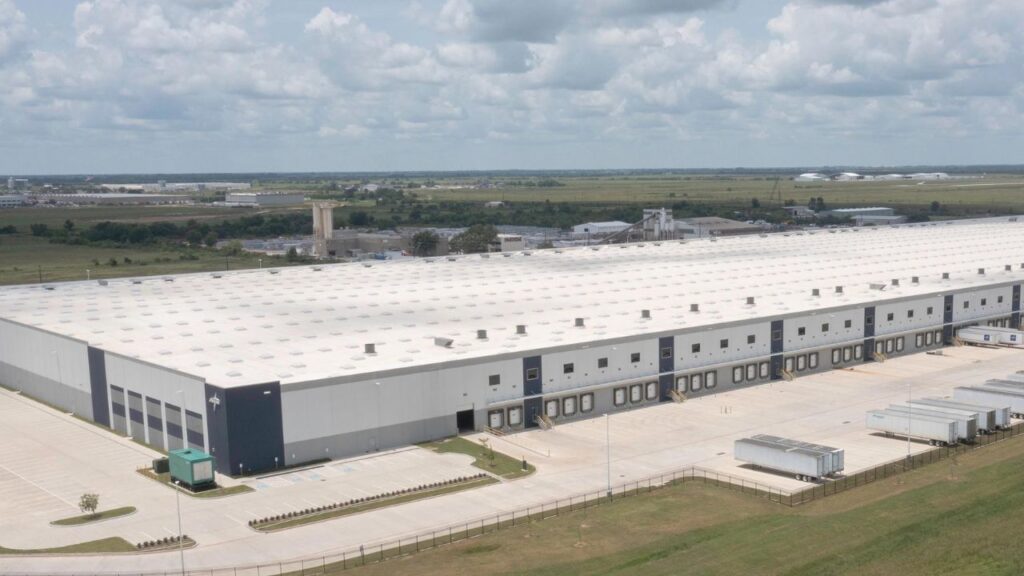
Without this information, it is difficult to provide an accurate estimate. However, as a rough estimate, the cost of a single electrical panel can range from $550 to $13,000 or more depending on the size and capacity required. The labor cost for installation can also vary depending on the complexity of the installation and the location.
Get Warehouse Electrical Panel Cost Estimate
We help Residential & Commercial Contractors to win more projects with higher accuracy.
Warehouse Thermostate Installation Estimator
The cost of warehouse thermostats can vary widely. However, a rough estimate for a basic, non-smart thermostat with a single-zone control system for a small to medium-sized warehouse can range from $200 to $500. For larger warehouses or thermostats with more advanced features, the cost can range from $550 to $1200 or more.
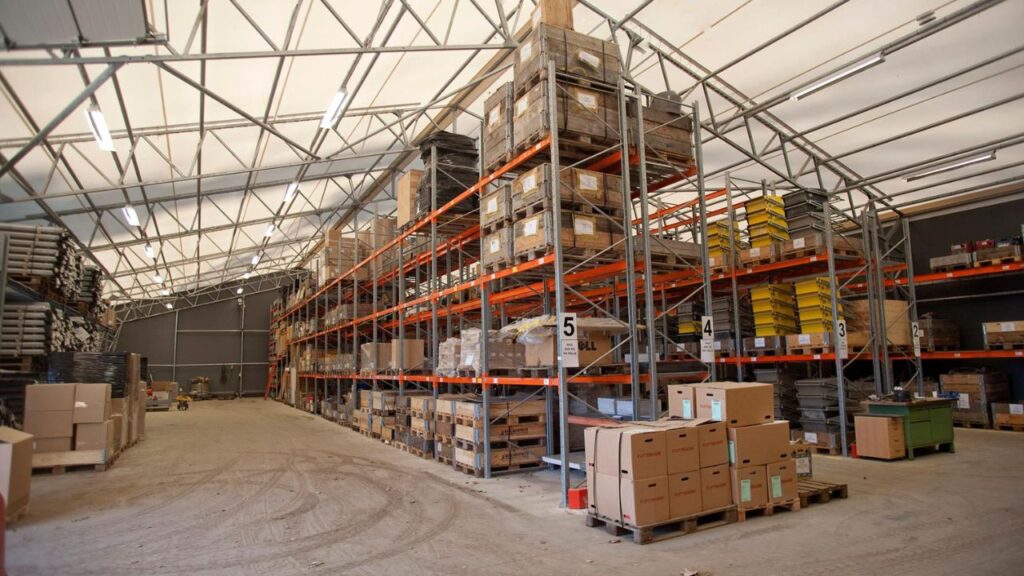
Warehouse Fire Alarm System Cost Estimator
Warehouses are one of the most integral parts of a company. It’s where all the valuable stock and inventory are stored, which is why any disruptions to the operations there can have severe consequences to you and your company’s reputation.
By nature, warehouses are built as large, open spaces with high ceilings and many rows of racking. The cause for concern here is that they are probably packed from floor to ceiling with flammable materials.
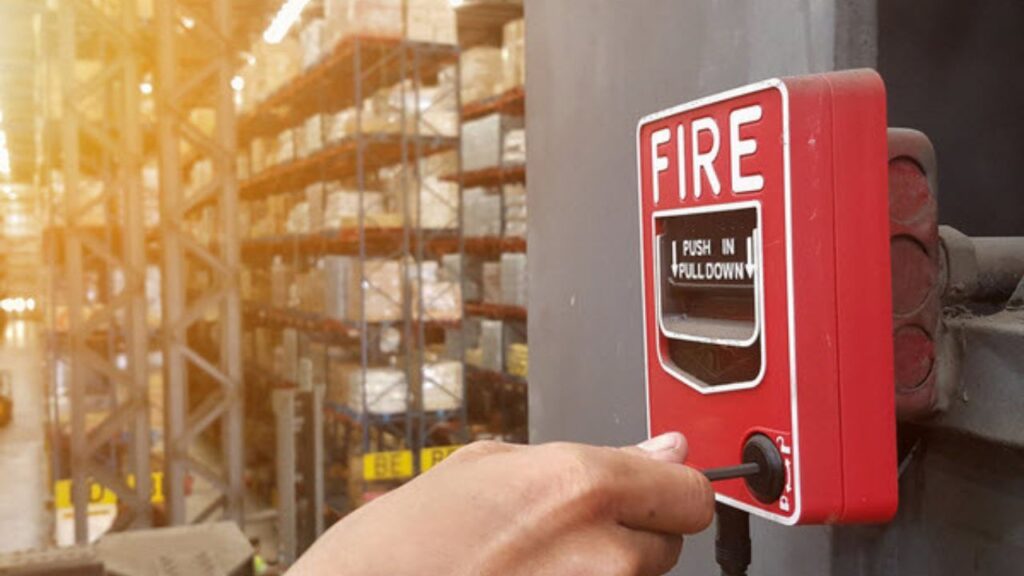
It doesn’t matter whether the goods themselves are flammable or not because the cardboard or plastic packaging that they are most likely in is. Additionally, if the goods are mounted on wooden shelves, that’s another flammable thing to worry about.
A fire breaking out in a warehouse is a real nightmare for businesses since it puts both human life and property at risk, resulting in huge financial losses and, of course, a tarnished image for the business.
Count on an average cost of $2 to $4 per square foot for a simple installation. For a complex installation, such as in a multi-floor building, the price may increase to $5 to $7 per square foot or higher. Because older buildings often present unique challenges, retrofitting an older structure may cost between $6 per square foot up to $15 per square foot. This is due to the cost of additional labor for a more difficult installation. New construction installation is usually easier and cheaper.
Need Estimate & Materials For Warehouse Fire Alarm System?
We help Residential & Commercial Contractors to win more projects with higher accuracy.
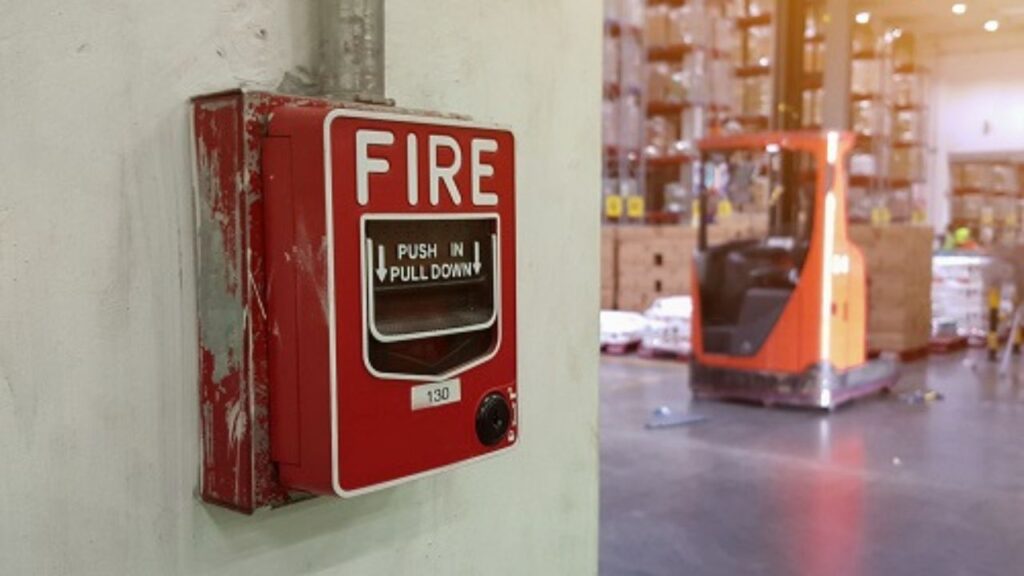
2D Plan & 3D Rendering For Warehouse?
Ready to take your warehouse design to the next level? Our team of 3D rendering experts can bring your vision to life with stunning and realistic 3D renderings.
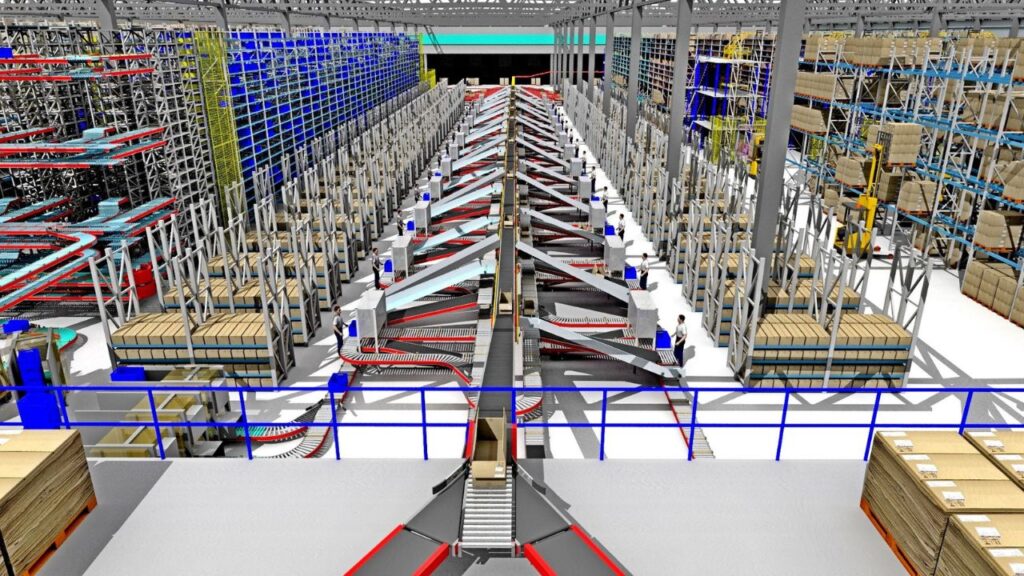
Warehouse Solar Panel Installation Cost Estimator
Solar panels for warehouses can be a highly effective measure for boosting the energy efficiency of these large commercial buildings, which can result in big savings for business owners due to the higher operating costs involved.
And with sustainability an ever-more pressing item on the agenda for business owners, solar panels for warehouses can be an excellent way to make a sizeable impact on your carbon footprint, demonstrating tangible Corporate Social Responsibility (CSR) to ever more environmentally-conscious customers and business investors.
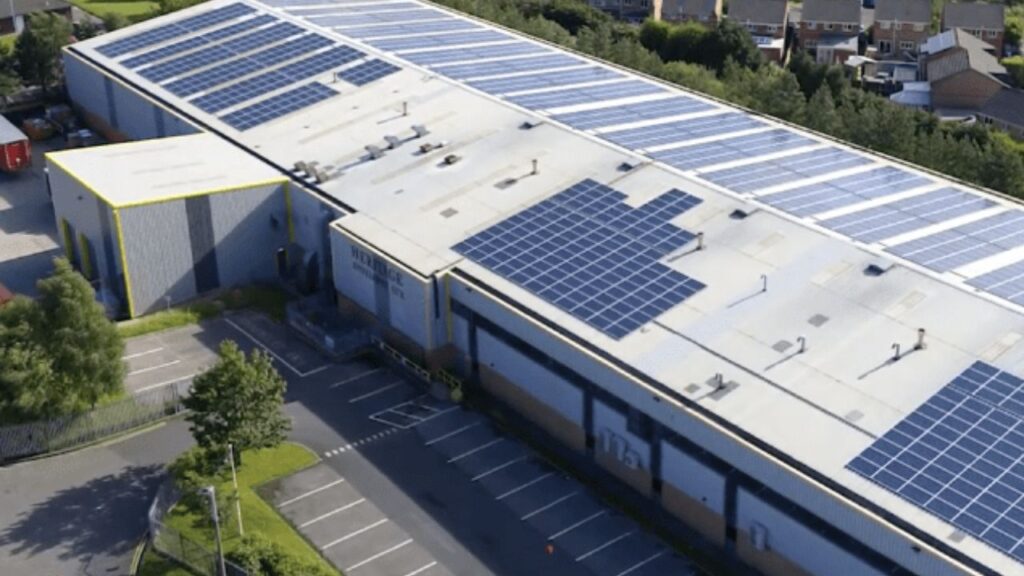
Solar panels are perfectly suited to warehouses and other large industrial premises. Not only are they instrumental for offsetting the notably higher operating costs for these types of buildings, but they also make excellent use of the considerable roof space available, which otherwise goes largely unused.
Significant financial savings are the first and perhaps most obvious advantage, as commercial solar panels for warehouses and factories provide the perfect way to monetise the large amount of roof space these premises typically have available. This space is often otherwise of very little use to most businesses and organisations, making it the ideal place to install a bespoke solar panel system, with minimal disruption to your operations.
The sheer amount of space that’s generally available on warehouses and factories means that they can accommodate particularly large-scale solar PV installations. What’s more, these panels produce most of their energy in the day, when the warehouses and factories themselves are usually at their most active. This makes solar panels great for effectively offsetting the notably higher running costs from these buildings, which are normally home to some of the most energy-intensive industrial operations.
Need Estimate & Materials For Warehouse Fire Solar Panel?
We help Residential & Commercial Contractors to win more projects with higher accuracy.
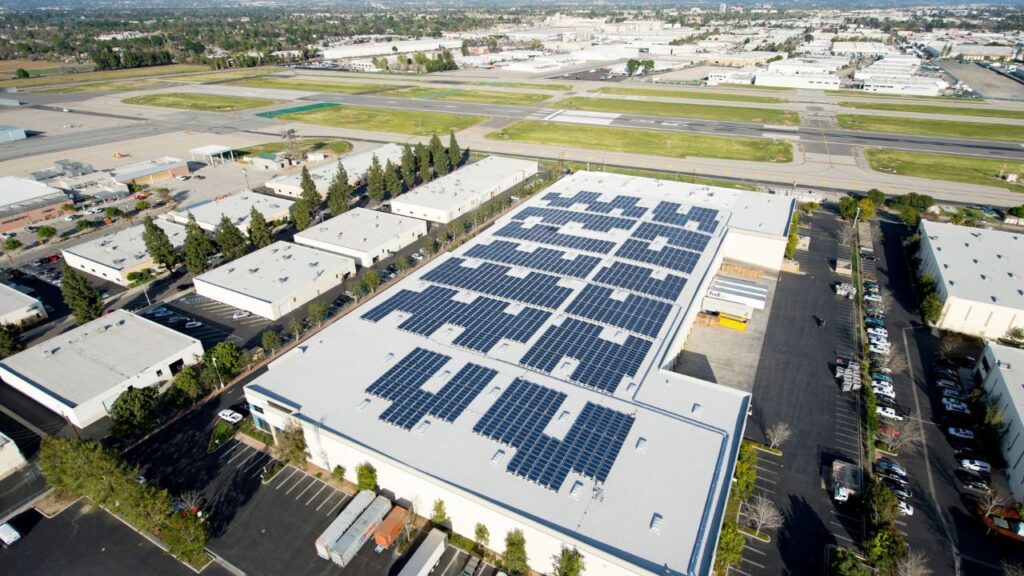
Lead Generation: For Warehouse Solar Panel Installation
Contractors can grow their business with our lead generation services.
Warehouse CCTV Camera Installation Cost Estimator
For estimating the cost of installing a CCTV system in a warehouse, you will need to determine the amount of work that will need to be done to run the cable. The cost of setting up a system is very minimal — usually it’s no more complicated than plugging in a few video wires and connecting the power with a few screws. The real cost is setting up a CCTV system running the cable through the ceiling, wall, or other area. Setting up a CCTV system involves a comfort level with electronics, but the majority of the work is very similar to that of an electrician or computer networking company.
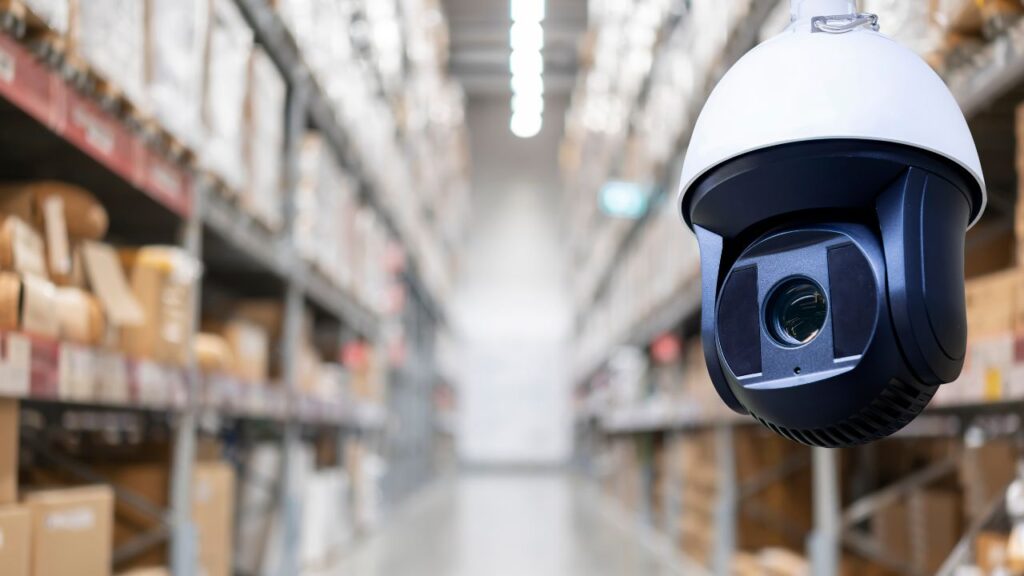
CCTV cameras can be used to monitor employee movement and activities within the warehouse and to make sure whether basic operating procedures are being adhered to or not. This helps in more ways than one. It makes sure that employees utilize their time efficiently, follow safety protocols, and are dissuaded from stealing. This also reduces the time and effort spent by floor managers in monitoring their employees, and they can focus more on the core part of their jobs.
Need Estimate & Materials For Warehouse CCTV Camera?
We help Residential & Commercial Contractors to win more projects with higher accuracy.
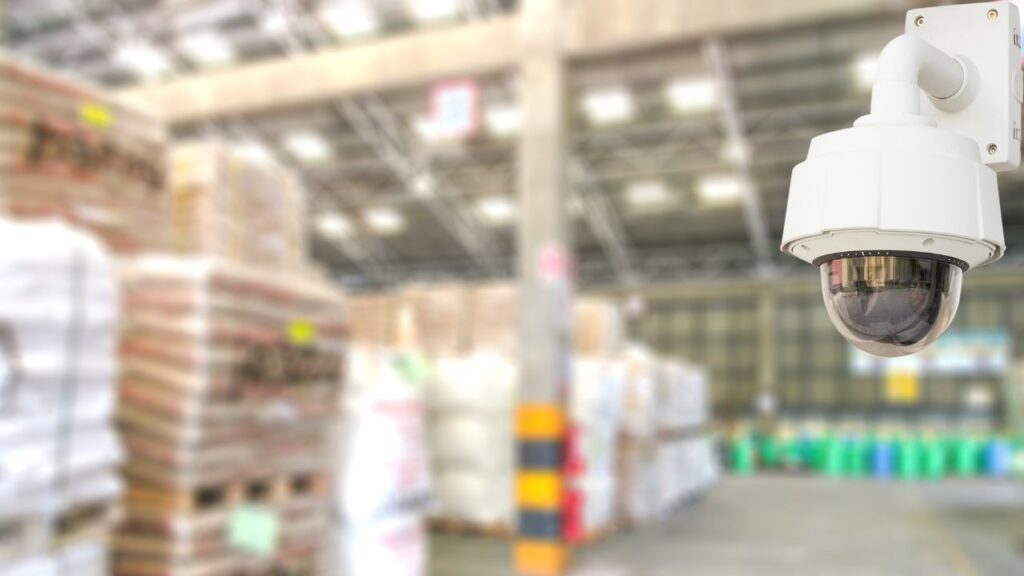
Lead Generation: For Warehouse CCTV Installation
Contractors can grow their business with our lead generation services.
Warehouse Electricity Generator Installation Cost Estimator
In today’s business landscape, having a reliable source of electricity is critical for smooth operations. However, power outages can happen unexpectedly, leading to production downtime and revenue loss. This is where warehouse electricity generators come in handy. They provide a backup power source to keep your operations running smoothly in the event of an outage.
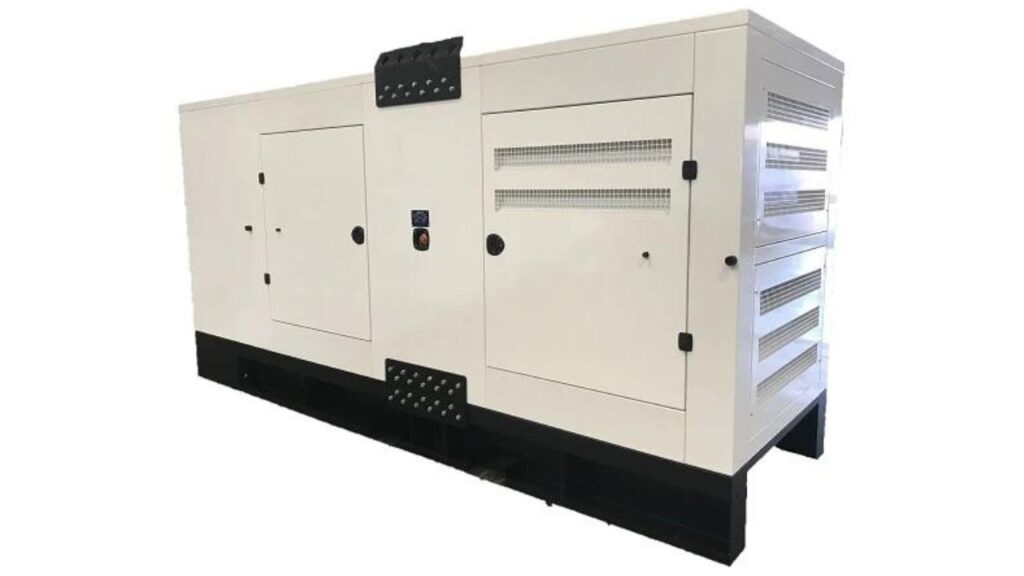
Before you can estimate the cost of a generator, you need to know how much power your warehouse requires. This will depend on the size of your facility and the equipment you use. For example, a warehouse that relies on heavy machinery will require more power than a warehouse that uses only light equipment. Once you know your power needs, you can determine the size and capacity of the generator you need. There are different types of generators available, each with its own advantages and disadvantages. The most common types are diesel, natural gas, and propane generators. Diesel generators are known for their reliability and durability, while natural gas generators are more eco-friendly and cost-effective in the long run. Propane generators are the quietest option and require less maintenance. Your choice will depend on your specific needs and budget.
The installation cost of a generator can vary depending on several factors, such as the location of the generator, the type of fuel it uses, and the complexity of the installation. For example, if your generator requires a concrete foundation or a fuel storage tank, the installation cost will be higher. It’s important to get a detailed quote from your installer to ensure you have an accurate estimate of the total cost.
Need Estimate & Materials For Warehouse Electricity Generator?
We help Residential & Commercial Contractors to win more projects with higher accuracy.
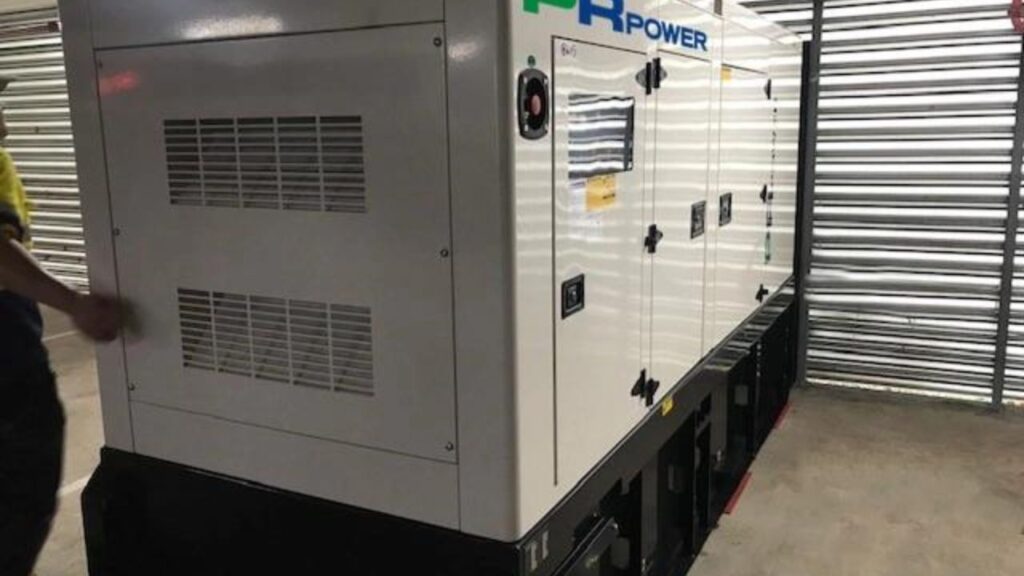
Lead Generation: For Warehouse Electricity Generator
Contractors can grow their business with our lead generation services.
Choose Your Trade & Get a Sample Project
Google Reviews
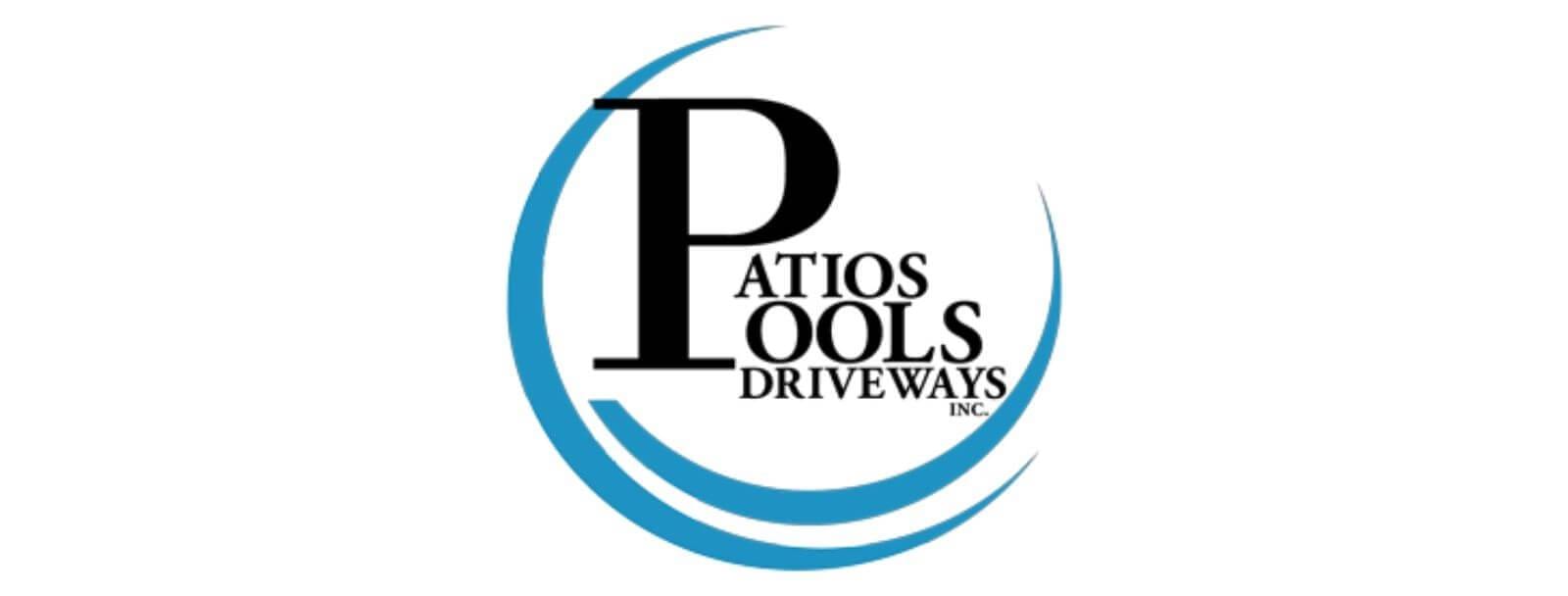
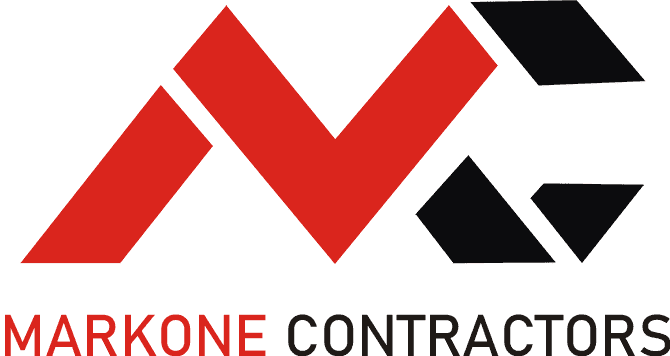
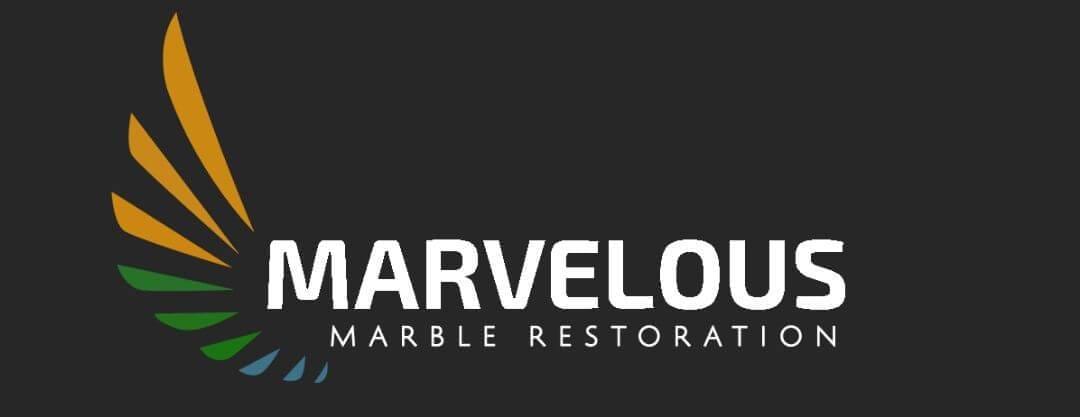
Process To Get Warehouse Electrical Installation Cost Estimate Report
Here I am going to share some steps to get your warehouse electrical installation cost estimate report.
-
You need to send your plan to us.
You can send us your plan on info@estimatorflorida.com
-
You receive a quote for your project.
Before starting your project, we send you a quote for your service. That quote will have detailed information about your project. Here you will get information about the size, difficulty, complexity and bid date when determining pricing.
-
Get Estimate Report
We do warehouse electrical installation cost estimate and prepare a detailed report for your project. At last you finalize the report and finish the project.