- Homepage
- Construction in Miami Beach
Warehouse Construction in Miami Beach
Leading provider of warehouse construction services.
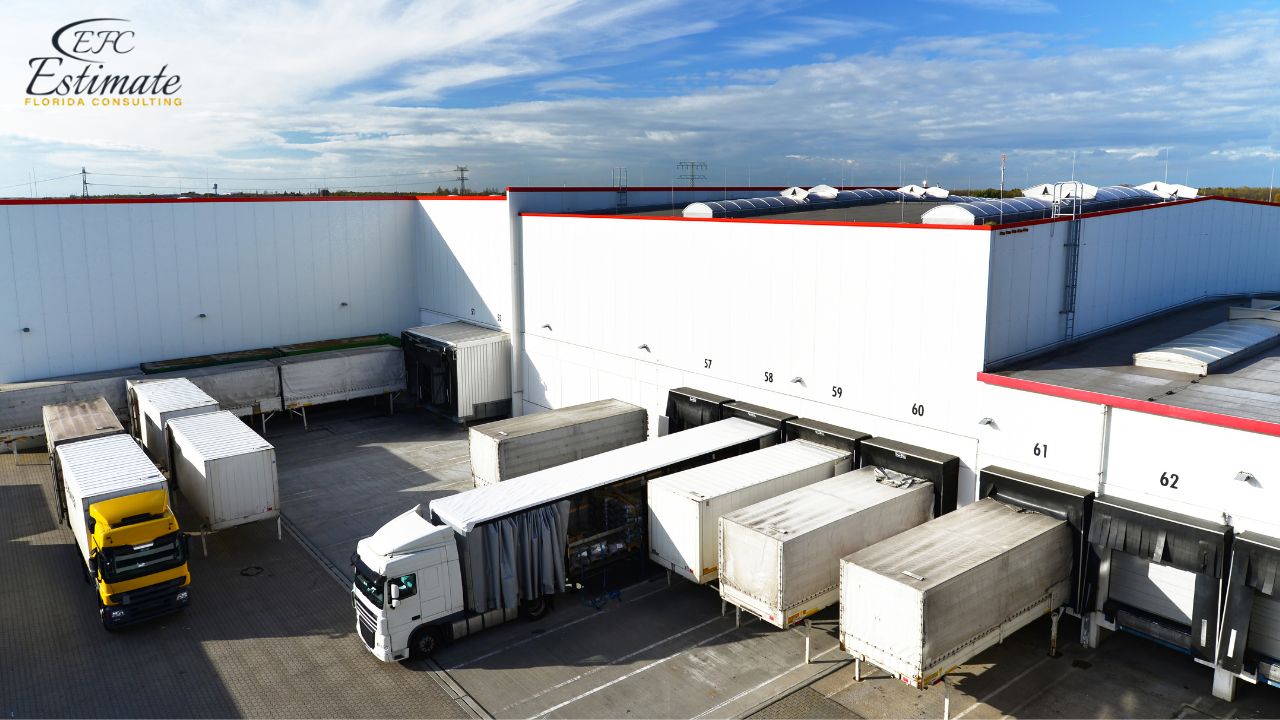
Estimated Warehouse Cost Breakdown
On average, the cost of constructing a warehouse in Miami Beach ranges from $60 to $200 per square foot, depending on project specifications.
- Basic warehouse (minimal features): $600,000 – $2,000,000 for a 10,000 sq. ft. facility
- Mid-range warehouse (with office & utilities): $1,500,000 – $4,000,000
- High-end warehouse (cold storage, automation, etc.): $3,000,000 – $10,000,000+
Primary Factors Influencing Warehouse Construction Costs
Several key elements play a critical role in determining the overall cost of constructing a warehouse. These factors vary widely depending on the specifics of the project, and understanding them can help in planning and budgeting effectively. Below, we explore the most significant contributors to warehouse costs, including size, location, materials, design, intended use, and additional features, each of which can significantly shift the financial investment required.
Size of the Warehouse
The physical dimensions of a warehouse are one of the most influential factors affecting its construction cost. A larger warehouse naturally demands a greater quantity of raw materials, such as steel, concrete, and roofing components, which directly increases expenses. Additionally, bigger projects often require more labor hours to complete, pushing up the overall budget.
- Material Demand: Larger sizes mean more steel, concrete, and roofing, raising material costs significantly.
- Labor and Equipment: Increased scale requires additional workforce and possibly heavy machinery or specialized tools.
- Site Preparation: Bigger warehouses may need extensive grading or foundational work, adding to expenses.
- Permits and Utilities: Larger projects can incur higher permitting fees and utility connection costs.
90% More Chances to Win Projects With Our Estimate!
- Multi-Family Building
- Hotel Building
- Hospital Building
- Warehouse Building
- School & University Building
- High-Rise Building
- Shopping Complex
- Data Center Building
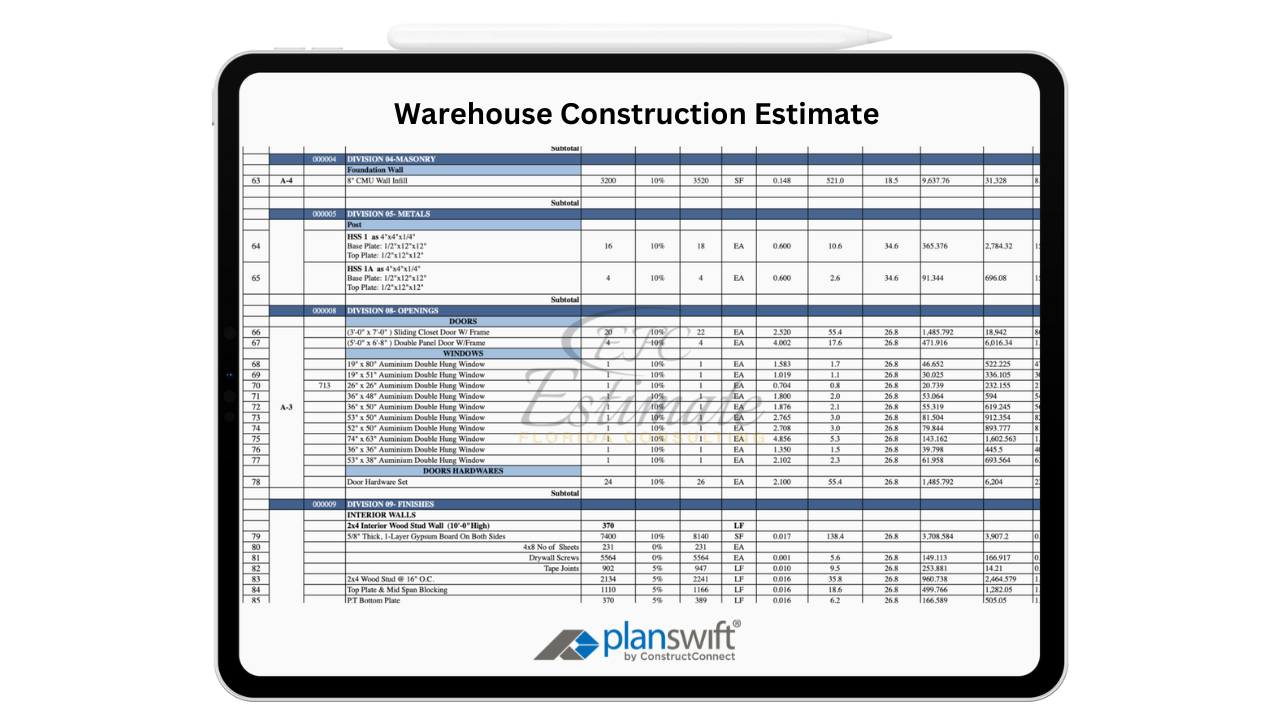
Cost to Build 20000 sq. ft. Warehouse
Warehouse Size | Cost Range | Influencing Factors |
20,000 sq ft | $288,000 – $456,000+ | Location, steel prices, building design, inventory type; urban areas, rising material costs, and custom features increase costs |
This table reflects the typical cost range for a 20,000 square foot metal warehouse and the key factors that affect the pricing.
Location of the Warehouse
Where a warehouse is built can have a substantial effect on its total cost due to regional differences in economic and environmental factors.
- Land Cost: Urban locations often have pricier land compared to rural areas.
- Labor Rates: Higher wages in cities or unionized regions increase construction costs.
- Transportation: Rural sites may face elevated costs for delivering materials.
- Environmental Factors: Areas with extreme weather or seismic risks require costly structural reinforcements.
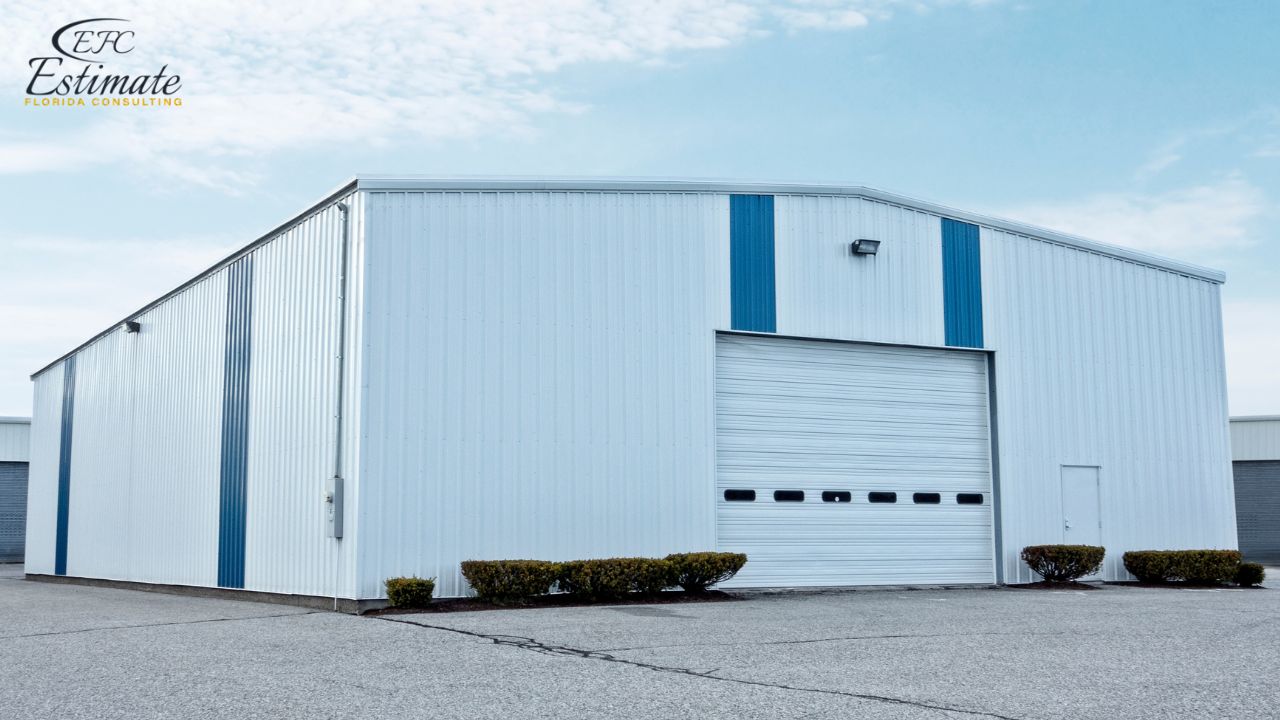
Materials Used in Construction
The choice of construction materials is another critical determinant of warehouse costs, as different options come with varying price tags and long-term implications. For instance, high-quality materials like concrete, glass, or insulated metal panels (IMPs) can significantly raise upfront costs compared to more economical standard metal panels.
- Material Cost: Concrete, glass, and IMPs are pricier than basic metal panels.
- Installation Needs: Premium materials may require specialized skills or equipment, increasing labor expenses.
- Durability Benefits: Higher-end options often offer better insulation or longevity.
- Maintenance Trade-Off: Cheaper materials might save upfront but lead to higher long-term repair costs.
Best Materials for Building a Warehouse
Choosing the right material for a warehouse affects both cost and durability. Steel is favored for its strength, longevity, and lower cost, though alternatives like insulated concrete offer benefits such as durability and insulation. Knowing material costs helps estimate your budget. Below are key options with updated costs per square foot, increased due to market trends.
Material | Average Cost per Square Foot | Key Benefits |
Stud Frames | $25 – $50 | Versatile, widely available |
Tilt-Up Construction | $30 – $50 | Fast assembly, good insulation |
Steel Frames | $15 – $25 | Durable, cost-effective, long-lasting |
Design and Architectural Complexity
The architectural design of a warehouse, including its layout, roof style, and structural intricacies, heavily influences construction expenses. Simple, rectangular designs with flat roofs are typically the most cost-effective, requiring fewer materials and less labor. However, more elaborate designs—such as those with sloped roofs, multiple levels, or customized interiors—demand additional engineering expertise, more complex framing, and increased construction time. Unique aesthetic features or layouts tailored to specific operational needs can also necessitate advanced planning and design work, driving up professional service fees and material requirements. Thus, the complexity of the design directly correlates with the overall budget.
Additional Features and Amenities
Adding specialized features to a warehouse, like refrigeration units, advanced security systems (e.g., cameras, biometric access), or extras such as break rooms, offices, or solar panels, can significantly raise costs. These enhancements improve functionality and safety but must be balanced against budget limits, as they can quickly increase the total investment.
Category | Cost Range |
Security Systems (CCTV, Access Control, etc.) | $10,000 – $100,000 |
IT Infrastructure & Smart Warehouse Technology | $20,000 – $500,000 |
Solar Panels & Energy Efficiency Upgrades | $50,000 – $500,000 |
Insurance & Contingencies | 5% – 15% of total project cost |
3D Rendering Cost for a Warehouse
The cost of 3D rendering for warehouse construction varies based on project complexity, detail, quality, and timeline. Basic static images range from $300 to $600+, mid-tier renders with elements like shelving cost $700 to $1,600+, and photorealistic visuals for marketing or bids run $1,500 to $3,000+ per image. Animations showcasing workflows are priced at $2,000 to $8,000+ per minute, while 360-degree virtual tours fall between $800 and $2,000+. Full packages for large warehouses, including multiple views and animations, can exceed $5,000 to $15,000+. Hiring skilled 3D artists or agencies ensures precise, high-quality visuals and efficient project delivery.
We Provide 3D Rendering Services!
For Warehouse Buildings and Other Projects
Turnaround time is 1-2 days.
Win More Projects With Us
Warehouse Construction Cost Breakdown in Miami Beach
Category | Cost Range |
---|---|
Land Acquisition & Preparation | $500,000 – $5,000,000+ |
Site Preparation & Foundation | $6 – $50 per sq. ft. |
Structural Construction | $10 – $60 per sq. ft. |
Roofing | $5 – $15 per sq. ft. |
Interior Build-Out | $3 – $150 per sq. ft. |
Permitting & Legal | $5,000 – $150,000 |
Additional Costs | Varies (5% – 15% of total) |
Miami Beach-Specific Considerations for Warehouse Construction
Miami Beach’s unique environment adds layers to planning and costs.
- Hurricane Preparedness: Reinforced structures and elevated foundations are often required, adding 10-20% to costs.
- Flood Zones: Many areas need flood mitigation, like raised slabs or drainage systems.
- Permitting Delays: Miami Beach’s rigorous permitting process can extend timelines and budgets.
- Labor Shortages: High demand for skilled workers in South Florida may increase rates.
Sustainable Warehouse Construction Trends
Sustainability is gaining traction in Miami Beach’s warehouse sector.
- Energy Efficiency: LED lighting and solar panels reduce operational costs.
- Green Materials: Recycled steel or insulated concrete lowers environmental impact.
- Water Management: Rainwater harvesting systems address Miami Beach’s wet climate.
These features may raise initial costs by 5-15% but offer long-term savings and tax incentives.
90% More Chances to Win Warehouse Bids with Our Estimate
Does Buying or Renting a Warehouse Save More Money?
Whether buying or renting a warehouse is more cost-effective hinges on your business’s unique needs, financial position, and future plans. Below are key considerations to guide your decision:
- Upfront vs. Ongoing Costs
Buying a warehouse involves a higher initial investment, but it eliminates recurring rent payments, potentially saving money over time. Renting, however, offers lower short-term costs, though it lacks the long-term financial advantages of ownership. - Property as an Investment
Purchasing land or a warehouse at the right time could pay off if property values rise, allowing you to profit from a future sale or lease. Renting offers no such equity-building opportunity. - Operational Flexibility
Renting provides the freedom to relocate or scale operations quickly without long-term ties. Owning a warehouse demands more commitment and planning, locking you into a fixed location. - Location Considerations
If you’re set on a specific area for the long haul, buying can be a smart investment. Renting suits shorter-term needs or uncertainty about future location requirements. - Financing Factors
Buying often involves loans, so you’ll need to evaluate interest rates, repayment terms, and additional costs like fees. Ensure any financing aligns with your budget and goals.
Ultimately, the choice between buying and renting depends on your priorities. Consulting a financial advisor or real estate expert can help clarify which path best fits your situation.
4 Key Ways to Reduce Warehouse Build Costs
Invest in Detailed Planning
Thorough planning is a cornerstone of cost control in warehouse construction, as it helps avoid the financial pitfalls that often arise during a project. By dedicating time upfront to map out every detail—such as material needs, labor schedules, and site logistics—you can significantly reduce the likelihood of expensive change orders that disrupt budgets. Furthermore, a well-structured plan ensures that unexpected overruns, which can stem from miscalculations or delays, are kept to a minimum. Adhering to a strict timeline is equally critical; it not only keeps the project on track but also limits the duration of construction loans, which can accrue substantial interest over time.
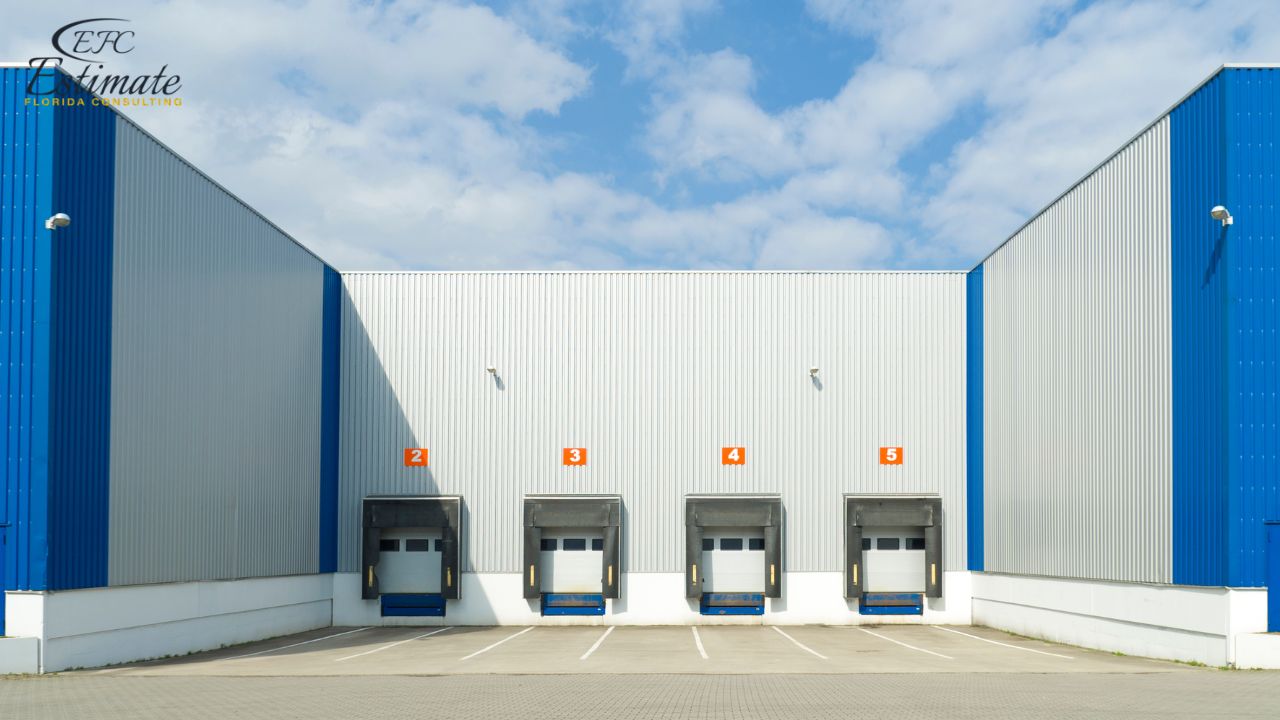
Simplify the Design
Choosing a straightforward design is one of the most effective ways to keep warehouse construction costs in check, as it directly impacts multiple expense categories. Complex layouts with intricate features or irregular shapes demand more materials, which can quickly inflate the budget, especially when specialty items are required. Beyond materials, elaborate designs increase the time spent on architectural planning and engineering, adding professional fees that a simpler blueprint avoids. A basic, functional design—think rectangular footprints and minimal embellishments—streamlines the construction process, reducing labor hours and the need for advanced equipment. This approach doesn’t just save money upfront; it also makes future maintenance easier and less costly, ensuring long-term savings without sacrificing utility.
Choose a Simple Roof with Low Pitch
Opting for a simple roof profile with a low pitch is a smart strategy to minimize construction expenses, as the roof is a major cost driver in any warehouse project. A single-sloped roof with a 1:12 pitch stands out as the most economical choice, requiring fewer materials like steel or roofing panels compared to more intricate designs such as gable or hip roofs. These complex alternatives not only demand additional resources but also increase labor time due to their assembly challenges, pushing costs higher. Engineering for a low-pitch roof is also simpler, avoiding the extra design work needed for steeper or multi-faceted styles. For those wanting a slight upgrade, a gable roof with a 2:12 pitch strikes a balance between affordability and aesthetics, still keeping expenses lower than more elaborate options.
Keep Height Practical
Maintaining a realistic warehouse height is essential for controlling costs, as vertical scale directly influences both construction and operational budgets. Taller buildings require significantly more steel for structural support, driving up material costs, especially when bracing or thicker beams are needed to ensure stability. The construction process itself becomes more expensive too, as higher walls may necessitate cranes or additional safety measures, increasing labor and equipment expenses. Beyond the build, excessive height impacts long-term costs—think higher heating and cooling bills due to increased air volume, or even pricier lighting setups. By assessing actual storage needs and avoiding unnecessary vertical space, you can trim both the initial investment and ongoing operational overhead, making practicality a key to cost efficiency.
Role Of Professionals for Warehouse Construction
- Contractors: Oversee the entire warehouse construction project, ensuring quality work, managing materials, labor, and timelines while adhering to safety regulations. Hire experienced contractors to keep your project on track and meet operational needs.
- Subcontractors: Specialize in critical tasks such as electrical systems, plumbing, HVAC installation, and structural work to ensure durability and efficiency. Hire skilled subcontractors for high-quality execution tailored to warehouse functionality.
- Architects: Design practical, efficient, and adaptable warehouse layouts that optimize space, meet safety codes, and support operational workflows. Hire professional architects to create the ideal warehouse design.
- Engineers: Ensure the structural integrity, safety, and efficiency of the warehouse by planning and overseeing mechanical, electrical, and civil aspects. Hire expert engineers to guarantee a robust and sustainable structure built for long-term use.
- Construction Estimators – Provide accurate cost assessments for materials, labor, and project timelines to help optimize budget planning and prevent cost overruns. Hire professional estimators to ensure financial efficiency and project feasibility.
Get 5 New Projects in the Next 7 Days With Our System
Construction Timeline Expectations
Understanding timelines is critical for planning and financing:
- Small Warehouse (10,000 sq. ft.): 4-8 months, depending on complexity.
- Mid-Size (20,000-50,000 sq. ft.): 8-12 months, factoring in permitting delays.
- Large/High-End (>50,000 sq. ft.): 12-18+ months, especially with custom features.
- Miami Beach Factors: Weather disruptions (e.g., hurricane season) and permitting can extend schedules by 1-3 months.
Early coordination with contractors and local authorities mitigates delays.
Conclusion
Warehouse construction in Miami Beach offers immense opportunities for businesses looking to capitalize on the city’s strategic location and growing logistics landscape. However, success hinges on navigating a complex web of factors—ranging from size and material choices to Miami Beach-specific challenges like hurricane preparedness and permitting delays. Costs can span from modest investments for basic facilities to multimillion-dollar budgets for high-end, tech-integrated warehouses, making accurate planning and budgeting essential. By leveraging strategies such as simplified designs, practical height considerations, and sustainable features, businesses can optimize their investment while meeting operational needs. At Estimate Florida Consulting, we’re committed to providing detailed cost analyses and expert guidance to turn your warehouse vision into a cost-effective reality. Contact us today to ensure your project thrives in Miami Beach’s dynamic market, balancing immediate expenses with long-term value.
Question Answer
Frequently Asked Question
The cost ranges from $60 to $200 per square foot, depending on the project specifications. A basic 10,000 sq. ft. warehouse costs $600,000 – $2,000,000, while a high-end facility with automation or cold storage can exceed $10 million.
Key cost factors include warehouse size, location, materials, design complexity, and additional features like refrigeration, security systems, and automation. Labor rates and permitting fees also play a role.
Construction timelines vary, but a small 10,000 sq. ft. warehouse takes 4-8 months, while larger or more complex projects can take a year or more due to permitting, design, and material sourcing.
Common materials include steel frames ($15-$25/sq. ft.), tilt-up concrete ($30-$50/sq. ft.), and stud frames ($25-$50/sq. ft.), each offering different benefits in durability, cost, and insulation.
Yes. Hurricane-proofing, flood zone requirements, and high land costs increase expenses. Additionally, Miami Beach has rigorous permitting regulations and skilled labor shortages, which can extend timelines and budgets.
Buying offers long-term financial benefits and property appreciation, while renting provides lower upfront costs and flexibility. The best choice depends on business stability, budget, and future expansion plans.
Construction Professionals For Your Project?
- Electrical
- Plumbing
- Masonry
- Roofing
- Painting
- More