- Homepage
- Construction in Bal Harbour
Warehouse Construction in Bal Harbour
Leading provider of warehouse construction services.
Bal Harbour, typically known for its luxury apartments and beachfront condos, is now also drawing attention from industrial developers seeking high-performance warehouses for logistics, storage, and distribution. With the rise of e-commerce, increasing port activity, and the growing demand for same-day delivery infrastructure, the need for strategically placed warehouse spaces has become critical. This makes Bal Harbour a valuable location despite its premium land values and coastal construction regulations. This comprehensive blog by Estimate Florida Consulting dives into the construction costs, phases, and planning involved in building a warehouse in Bal Harbour, Florida.
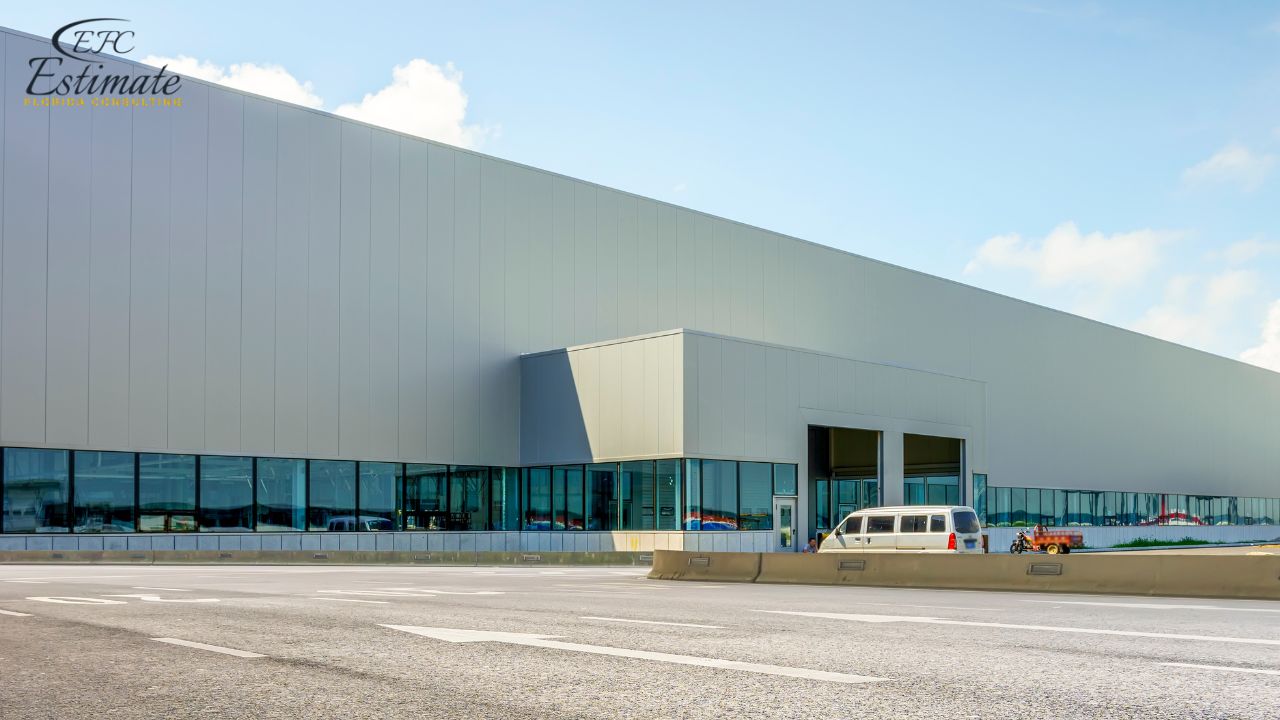
Warehouse Construction Overview in Bal Harbour
Bal Harbour offers a unique mix of commercial opportunity and coastal beauty, but it comes with construction challenges that demand expertise. Developers considering warehouse construction must address flood zones, zoning restrictions, and building codes designed to withstand hurricane-force winds. Still, the city’s closeness to major distribution channels like the Port of Miami, Miami International Airport, and I-95 corridor adds immense value to industrial real estate projects. Many investors and logistics firms are exploring warehouse construction in the area to serve last-mile delivery networks and refrigerated supply chains.
Average Warehouse Construction Costs
Warehouse construction costs in Bal Harbour are higher than inland areas due to coastal regulations, labor rates, and material sourcing. Costs will also depend on the level of automation and the warehouse’s intended use. Cold storage, for instance, requires specialized insulation and cooling systems, while light industrial warehouses focus more on space and storage without sophisticated internal systems.
Type of Warehouse | Cost per Sq. Ft. |
Light Industrial Warehouse | $160 – $220 |
Cold Storage Facility | $260 – $350 |
High-Clearance Distribution | $200 – $280 |
Tilt-Up Concrete Warehouse | $190 – $250 |
90% More Chances to Win Warehouse Bids with Our Estimate
Cost by Warehouse Type
Each warehouse type presents unique construction challenges and budget expectations:
- Cold Storage: These facilities are tailored for perishable goods and pharmaceuticals. They require vapor barriers, insulation systems, glycol floors, and industrial freezers. The need for constant temperature regulation raises both construction and operational costs.
- Distribution Centers: These are typically large-scale facilities with high ceilings, reinforced slabs, and numerous truck loading bays. Developers should budget for extensive paving, dock levelers, racking systems, and automated conveyor infrastructure.
- Light Industrial: These facilities are ideal for small-scale manufacturing, storage, or mixed-use applications. With fewer mechanical systems and less automation, the construction costs remain lower, but they still require fire suppression, efficient lighting, and proper ventilation.
Cost Per Square Foot Estimator
Warehouses vary widely in design and use, so square footage plays a major role in determining total project costs. Land preparation, accessibility, and level of customization also affect these estimates.
Size (Sq. Ft.) | Estimated Cost Range (Total) |
10,000 sq. ft. | $1.7M – $2.5M |
25,000 sq. ft. | $4.2M – $6.5M |
50,000 sq. ft. | $8.8M – $13.5M |
100,000 sq. ft. | $17M – $27M |
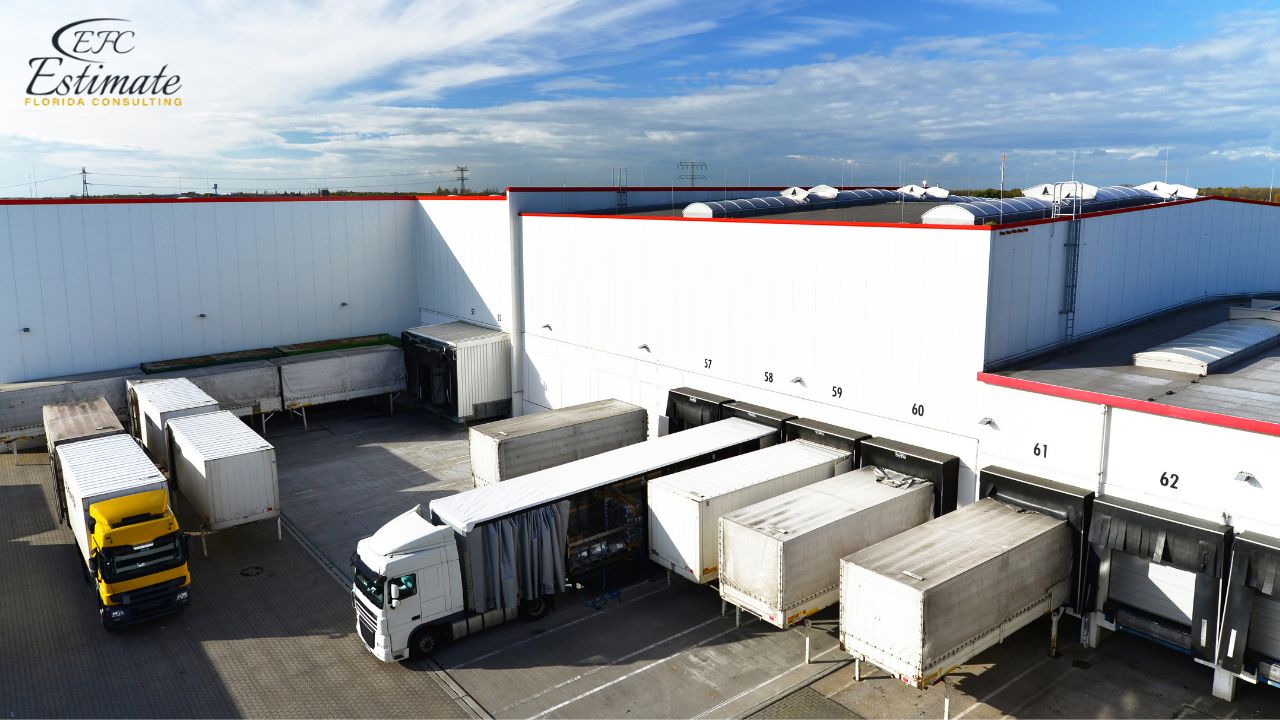
Foundation, Structural, and Roofing Costs
The foundation and structural components are the backbone of a warehouse. Depending on soil conditions and flood risk, you may need to invest in deep footings, slab reinforcement, or even pile foundations.
Component | Cost per Sq. Ft. |
Slab on Grade | $12 – $18 |
Tilt-Up Concrete Panels | $38 – $55 |
Pre-Engineered Steel | $30 – $45 |
Flat TPO Roofing System | $14 – $22 |
3D Rendering Cost for a Warehouse
The cost of 3D rendering for warehouse construction varies based on project complexity, detail, quality, and timeline. Basic static images range from $300 to $600+, mid-tier renders with elements like shelving cost $700 to $1,600+, and photorealistic visuals for marketing or bids run $1,500 to $3,000+ per image. Animations showcasing workflows are priced at $2,000 to $8,000+ per minute, while 360-degree virtual tours fall between $800 and $2,000+. Full packages for large warehouses, including multiple views and animations, can exceed $5,000 to $15,000+. Hiring skilled 3D artists or agencies ensures precise, high-quality visuals and efficient project delivery.
We Provide 3D Rendering Services!
For Warehouse and Other Projects
Turnaround time is 1-2 days.
Win More Projects With Us
MEP Systems (Mechanical, Electrical, Plumbing)
Efficient mechanical, electrical, and plumbing (MEP) systems ensure the building’s functionality and safety. For larger warehouses or those with climate control, these costs can account for up to 30% of the total project.
System | Cost per Sq. Ft. |
HVAC (Warehouse Grade) | $5 – $9 |
Electrical Distribution | $6 – $10 |
Plumbing Installations | $3 – $6 |
Fire Suppression | $4 – $7 |
Site Preparation and Permitting
Before breaking ground, site prep and permitting can take weeks to months. This includes grading, soil testing, environmental assessments, and drainage planning. Permitting delays are common in coastal zones.
- Land Clearing & Grading: $4 – $8 per sq. ft.
- Soil & Drainage Engineering: $0.50 – $1.50 per sq. ft.
- Permits and Impact Fees: $50,000 – $150,000
- Zoning and Coastal Code Approvals: $20,000+
Parking, Loading Bays & Access Infrastructure
Accessibility features ensure smooth truck and trailer operations. Concrete loading zones, dock pits, and turning radii must be incorporated in the design.
Feature | Cost Estimate |
Truck Dock & Ramps | $18,000 – $45,000 each |
Heavy Duty Paved Parking | $8 – $16 per sq. ft. |
Security Gates & Cameras | $15,000 – $35,000+ |
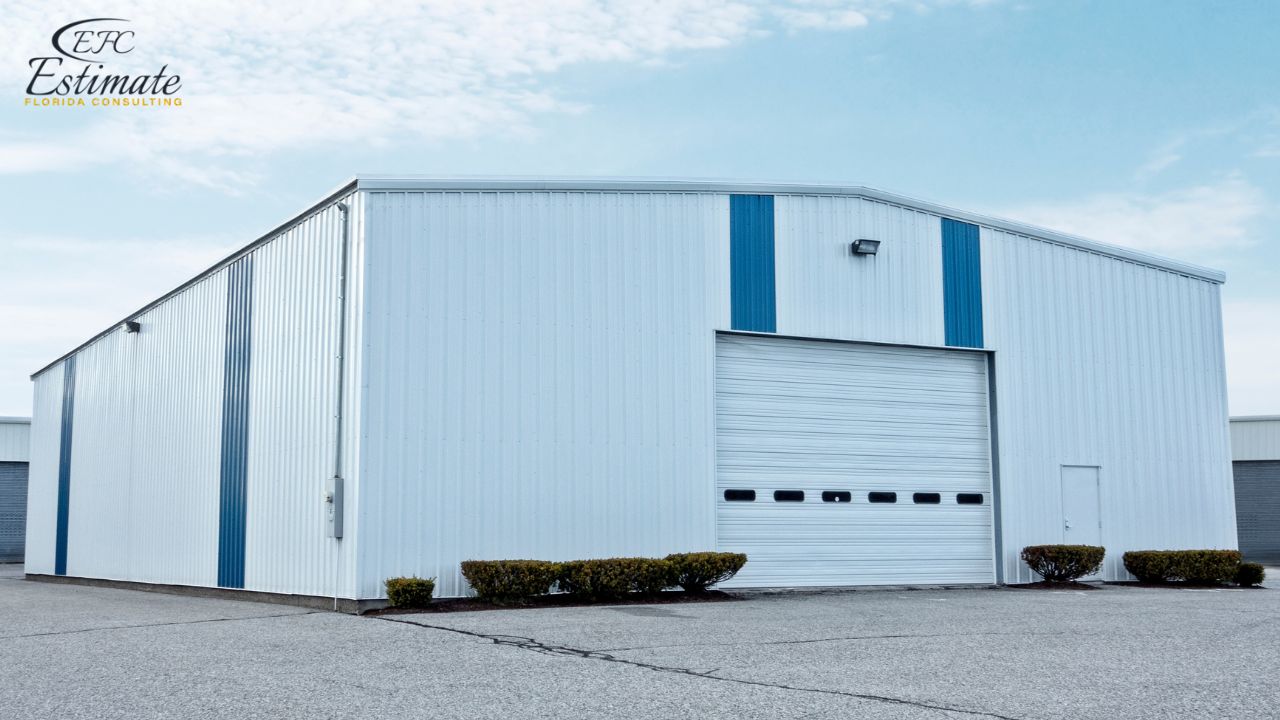
Coastal Construction & Hurricane Compliance
Warehouses in Sunny Isles must comply with Miami-Dade’s HVHZ codes. Buildings must be hurricane-resilient with impact-rated doors, wind-rated roll-up systems, stormwater mitigation, and elevated floor heights if in flood zones. Reinforced roofing systems and tie-down anchorages are also standard.
Smart Warehouse & Green Energy Features
Today’s warehouses are moving toward automation and sustainability. Smart sensors, lighting controls, solar panels, and energy-efficient HVAC can reduce long-term operational costs.
- LED Lighting Systems: $1.50 – $3 per sq. ft.
- Solar Panels Install: $2.25 – $4.50 per watt
- Battery Backup Systems: $30,000+
- Automation & IoT Systems: $5 – $9 per sq. ft.
90% More Chances to Win Projects With Our Estimate!
- Multi-Family Building
- Hotel Building
- Hospital Building
- Warehouse Building
- School & University Building
- High-Rise Building
- Shopping Complex
- Data Center Building
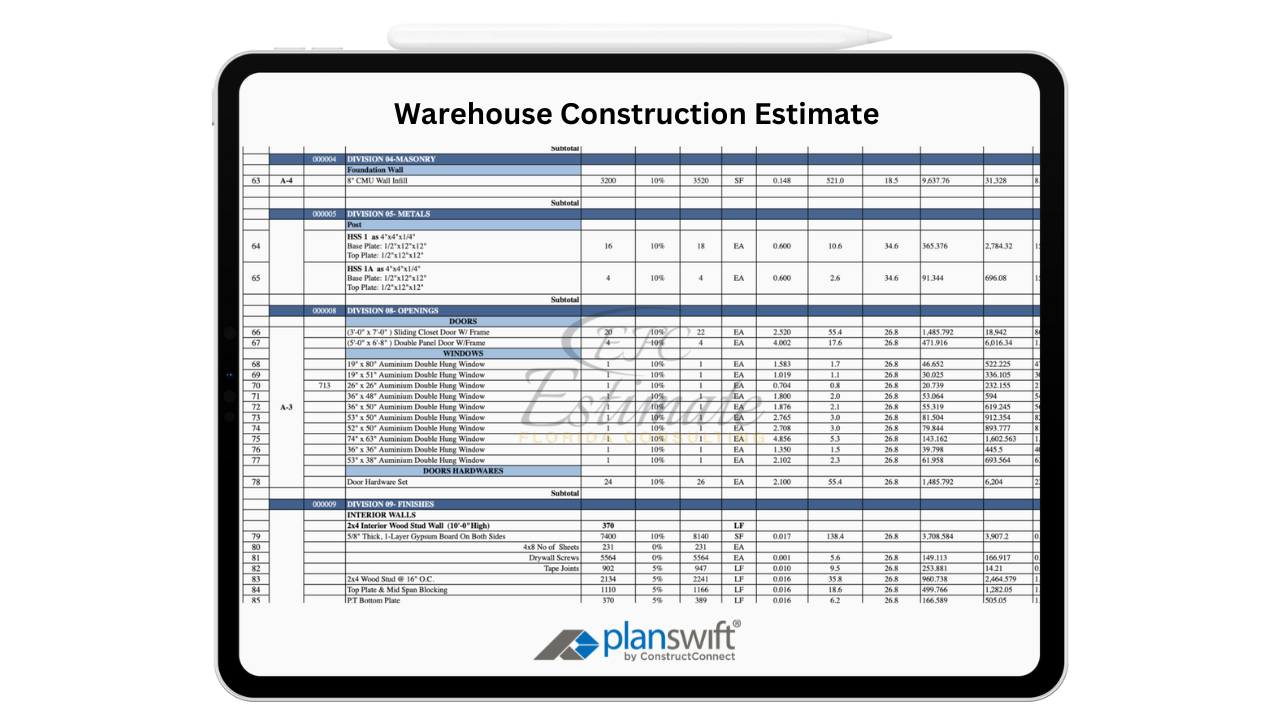
Annual Maintenance & Repair Estimates
Proper maintenance is critical to protecting warehouse assets and reducing life cycle costs. Annual inspections of roofing, lighting, and mechanical systems help prevent costly downtimes.
Category | Annual Cost Estimate |
Roof Maintenance | $0.50 – $1.25 per sq. ft. |
HVAC Servicing | $0.75 – $1.50 per sq. ft. |
Electrical & Lighting | $0.30 – $0.60 per sq. ft. |
Floor Resurfacing (as needed) | $15,000 – $40,000 every 10 yrs |
Role Of Professionals in Warehouse Construction Bal Harbour
- Contractors: Oversee the entire warehouse construction project, ensuring quality work, managing materials, labor, and timelines while adhering to safety regulations. Hire experienced contractors to keep your project on track and meet operational needs.
- Subcontractors: Specialize in critical tasks such as electrical systems, plumbing, HVAC installation, and structural work to ensure durability and efficiency. Hire skilled subcontractors for high-quality execution tailored to warehouse functionality.
- Architects: Design practical, efficient, and adaptable warehouse layouts that optimize space, meet safety codes, and support operational workflows. Hire professional architects to create the ideal warehouse design.
- Engineers: Ensure the structural integrity, safety, and efficiency of the warehouse by planning and overseeing mechanical, electrical, and civil aspects. Hire expert engineers to guarantee a robust and sustainable structure built for long-term use.
- Construction Estimators – Provide accurate cost assessments for materials, labor, and project timelines to help optimize budget planning and prevent cost overruns. Hire professional estimators to ensure financial efficiency and project feasibility.
Get 5 New Projects in the Next 7 Days With Our System
Conclusion
Constructing a warehouse in Bal Harbour offers a rare combination of commercial potential and strategic location. The region’s proximity to ports and infrastructure makes it ideal for supply chain operations. However, developers must prepare for elevated construction costs, rigorous coastal codes, and detailed planning processes. Whether you’re planning a cold storage unit, light industrial facility, or smart logistics hub, Estimate Florida Consulting provides tailored cost estimations, zoning consultations, and expert construction guidance to ensure your project is both efficient and compliant.
Question Answer
Frequently Asked Question
This is based on your operational workflow, racking system, inventory turnover, equipment clearances, and future scalability. We conduct space utilization analysis and simulate traffic flow before finalizing the layout.
Warehouse construction typically requires site development permits, environmental clearance, fire and life safety permits, utility approvals, and structural plan reviews. In Florida, additional hurricane compliance documentation may be needed.
Yes, tilt-up construction remains a leading choice due to its speed, cost-efficiency, and durability—especially for large-footprint warehouses over 10,000 sq. ft. It's ideal for flat sites and is often paired with steel roof systems.
Builders now pre-wire for IoT sensors, automated material handling systems, advanced fire suppression systems, and smart lighting/HVAC systems. These upgrades enhance safety, efficiency, and long-term cost savings.
Poor soil quality, flood zones, restricted access, or off-grid utilities can significantly raise costs. Site prep, grading, and utility hook-ups can account for 10–20% of the total budget in complex areas.
Durability depends on proper material selection (e.g., galvanized steel, reinforced concrete), routine maintenance planning, corrosion-resistant coatings, and ensuring the roof and envelope are properly sealed from day one.
Construction Professionals For Your Project?
- Electrical
- Plumbing
- Masonry
- Roofing
- Painting
- More