90% More Chances to Win Projects With Our Estimate!
- Multi-Family Building
- Hotel Building
- Hospital Building
- Warehouse Building
- School & University Building
- High-Rise Building
- Shopping Complex
- Data Center Building
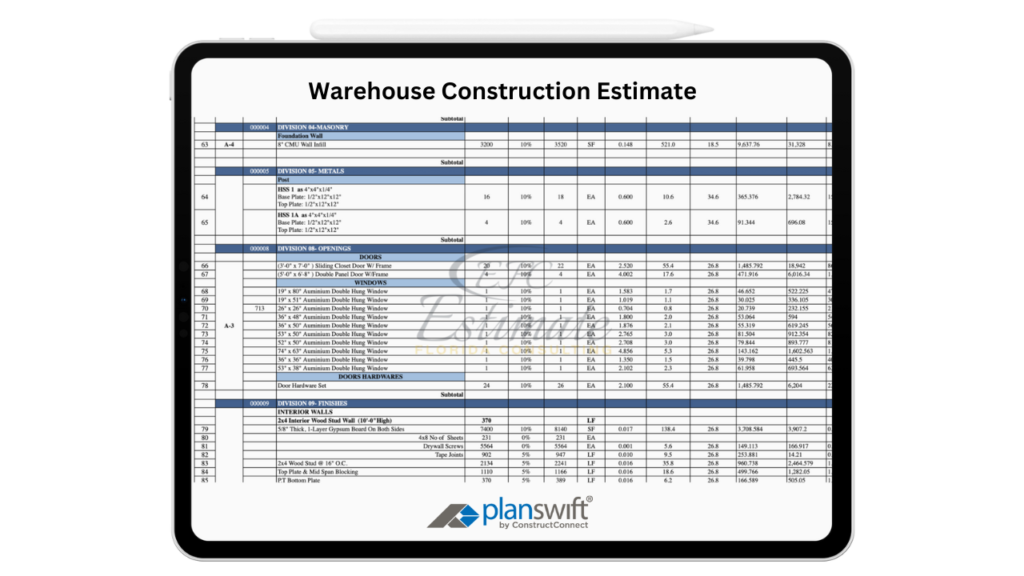
The average turnkey cost to build a warehouse typically ranges from $24 to $72 per square foot. Costs can vary depending on the warehouse size and specifications, with a smaller 30×40 warehouse now costing around $42,000, while a 50,000-square-foot distribution center can exceed $1.2 million.
The average cost of building a warehouse starts at $24 per square foot for a shell building. For smaller warehouses, like a 40×60 ft structure, costs are estimated at $180,000, while larger warehouses of around 50,000 square feet can reach approximately $3,750,000. Costs are influenced by warehouse size, materials used, delivery fees, and construction methods.
Below is an updated estimate of warehouse costs by size and price, sourced from Strong Building Systems.
DIMENSIONS | SQUARE FEET | TURNKEY ESTIMATE |
40×60 | 2,400 | $180,000 |
50×60 | 3,000 | $225,000 |
50×80 | 4,000 | $63,360 |
50×100 | 5,000 | $375,000 |
60×100 | 6,000 | $450,000 |
80×80 | 6,400 | $480,000 |
80×100 | 8,000 | $600,000 |
100×100 | 10,000 | $750,000 |
100×150 | 15,000 | $1,125,000 |
100×200 | 20,000 | $1,500,000 |
100×300 | 30,000 | $2,250,000 |
100×400 | 40,000 | $3,000,000 |
100×500 | 50,000 | $3,750,000 |
100×1,000 | 100,000 | $7,500,000 |
For the shell structure, which includes a concrete slab base, the cost is approximately $24 per square foot, while the steel building framework ranges from $8.40 to $14.40 per square foot, depending on the steel gauge. These estimates also include land and grading, which can help reduce total construction costs if lower-priced land and grading services are secured.
Constructing a warehouse involves various cost categories: hard, soft, financing, and long-term operational costs.
Soft costs are among the most challenging to estimate since they are not directly related to physical construction but are essential for project completion. They include permits, taxes, insurance, engineering and architectural design, and movable equipment. Due to their variability and uniqueness in each project, soft costs can be difficult to estimate accurately and may delay progress if unplanned.
Hard costs cover all expenses directly linked to the physical construction process. These predictable costs include labor, materials, site development, grading, and landscaping. Although these costs are more straightforward to estimate, they can fluctuate with market conditions.
Financing is a significant consideration in construction, as many clients use loans to fund their projects. Owners should carefully assess financing options to ensure good value. Warehouse financing usually involves three types:
These are ongoing costs such as maintenance, utilities, and upkeep, which can vary over a warehouse’s life. For instance, investing in energy-efficient upgrades and insulation can reduce long-term electricity bills, even though initial costs are higher. Other long-term expenses include property management, taxes, and insurance.
Warehouses rely on reinforced concrete foundations, anchored with rebar to withstand wind and seismic forces. The average cost of a concrete foundation is around $7.20 per square foot, higher than standard residential slabs due to added structural requirements.
Building a warehouse is a major infrastructure investment with multiple cost-driving factors. Key considerations include the type, location, and design of the warehouse, as well as initial planning and project scope.
Several initial factors immediately impact warehouse costs, such as the volume of goods to be stored, access to market outlets, employee accessibility, and potential for future expansion. The warehouse location plays a critical role, affecting both transportation costs and land acquisition expenses.
The project’s scope is one of the largest cost drivers, as larger construction projects naturally incur higher expenses. Expansion potential within an existing warehouse also raises costs. Project complexity further amplifies costs due to increased labor and material requirements.
Warehouse design varies significantly based on intended use, impacting overall costs. For instance, warehouses with cold storage for perishable items involve additional design elements and facilities. These adjustments increase both the architectural and material costs needed to accommodate specialized needs.
Designing a functional warehouse to support a productive work environment incurs varying costs based on the warehouse type. Options like humidity-controlled or refrigerated warehouses demand additional architectural and engineering input, raising both material and labor expenses.
Complex architectural designs, especially for warehouses storing diverse goods with specific storage needs, can drive up costs. A warehouse designed to accommodate multiple storage types may require extra rooms and specialized features, increasing both design and labor expenses.
Material costs are a significant factor, varying widely depending on warehouse type. For example, a cold storage warehouse might cost between $180 and $204 per square foot, whereas a standard warehouse typically costs between $60 and $78 per square foot. Additionally, the height and construction quality affect material costs—higher warehouses necessitate additional structural support, raising material expenses.
Building and maintaining a warehouse can be costly, but several strategies can help control expenses while ensuring efficiency.
Utilizing natural light reduces energy bills by lowering electricity consumption. This approach not only cuts power costs but also enhances employee productivity and workplace satisfaction, contributing to greater operational efficiency.
Efficient control of temperature and humidity can protect stored goods and reduce overall costs. Positioning thermostats strategically, installing humidifiers, and applying insulation on ceilings, windows, walls, and doors can help maintain stable interior conditions, reducing reliance on costly climate control systems.
Voice-enabling technology supports inventory control, reduces labor costs, and prevents loss from misplacement or theft, optimizing ROI. This technology streamlines operations by enabling real-time inventory management and reducing the likelihood of inventory-related errors.
Eliminate intermediaries by implementing cross-docking, which involves direct interaction with clients and minimizes handling time. Cross-docking reduces warehouse storage needs, speeding up distribution and cutting down on storage and management costs.
Routine pest inspections and control prevent damage from rodents and other pests, protecting both goods and infrastructure. Preventive pest management helps avoid costly repairs and losses associated with pest infestations, safeguarding your investment.
Assessing the appropriate size and functional needs of a warehouse involves several key factors:
The materials used in warehouse construction impact both its size and functionality. For example, materials suited for chemical processing, refrigeration, or general storage each require specific design features that affect the overall warehouse dimensions.
The size of a warehouse is directly related to the volume of goods it will store. Volume is calculated by the formula Volume=Length×Width×Height, allowing you to estimate the necessary space to accommodate the storage volume effectively.
The type of goods stored influences the design and size of the warehouse. It’s essential to categorize perishable and non-perishable goods and identify any items that require specialized storage conditions. Inventory planning helps in designing a warehouse that meets storage requirements safely and efficiently.
While a larger warehouse involves higher costs, it offers more storage flexibility, which is beneficial for adapting to fluctuations in inventory. This adaptability ensures that the warehouse can handle sudden surges or drops in stored materials without compromising functionality.
The rate of distribution also impacts warehouse size requirements. Higher distribution rates typically necessitate larger storage spaces, whereas warehouses with lower distribution demands can remain smaller and operate with fewer requirements.
Building an efficient warehouse is a multifaceted process that follows a four-stage approach: Initiation, Preconstruction, Procurement, and Construction. Below is an overview of each stage to guide the process.
In this inception phase, the client and project team make foundational decisions that impact the project’s success. The client provides input on project needs, while the team conducts feasibility studies to align the project with budget goals. If a location isn’t selected, the team performs zoning analysis and site selection. Key stakeholders, including a structural engineer, architect, client representative, and contractor, join the team. Contractor selection typically occurs through competitive bidding.
The preconstruction phase is crucial for planning and design. Here, the project team initiates the design process, which includes preliminary, schematic, detailed, and final construction designs. During the preliminary design, proposals and cost estimations are developed, followed by a schematic design phase where spatial layouts, materials, and appearances are approved. Detailed designs refine all specifications and finalize the cost estimate, allowing contract renegotiation if necessary.
This stage also involves extensive feasibility studies, assessing factors such as building type, cost-saving options like prefabrication, potential incentives (tax reductions, land donations, or employee training programs), and regulatory requirements, including zoning and environmental impact assessments.
With a roadmap in place, the procurement stage begins, where the project team sources necessary materials and equipment. The ease of procurement varies based on project size, resource availability, and schedule. Some contractors have in-house procurement capabilities, which can streamline the process and offer cost savings.
The construction phase is when visible progress occurs, starting with a preconstruction meeting to ensure everyone aligns on quality control, job site access, material storage, and working hours. Effective planning here reduces the risk of cost overruns and delays.
The construction sequence includes:
Once construction concludes, post-construction activities prepare the warehouse for handover. This stage is subdivided into Warehouse Commissioning, Owner Occupancy, and Project Closeout.
Consider the following strategies to help your organization cut costs when building a new warehouse. While these may not apply to every project, they are valuable cost-saving tips.
Detailed planning from the outset helps prevent costly change orders and reduces the risk of budget overruns. Adhering to a well-defined timeline can also minimize the need for extended construction financing, saving on loan interest costs.
A straightforward design generally requires less material, engineering, and design time than more complex layouts, directly reducing overall costs. Simplifying design features can help streamline the construction process.
A single-sloped roof with a 1:12 pitch is typically the most cost-effective option. More complex roof styles, like gable and hip roofs, demand additional materials, engineering, and labor, driving up expenses. A gable roof with a 2:12 pitch can also be a cost-effective alternative.
Keep height requirements realistic to reduce building costs. Taller warehouses need more steel, increasing both material costs and energy expenses for heating and cooling.
Design with future growth in mind by ordering ‘expandable end walls.’ This setup allows for more cost-effective expansion if needed, as retrofitting additional space later without this planning is typically far more expensive.
The cost of a pre-engineered metal building can vary based on the supplier and location. To find the best price, obtain at least four quotes from different suppliers. Platforms like BuildingsGuide can assist in connecting you with vetted suppliers to ensure you receive competitive rates for your warehouse project.
Beyond basic construction costs, several additional factors can impact your budget. These costs vary depending on the warehouse’s purpose and operational needs:
Determine if insulation is necessary and, if so, what type is best suited for your application. Insulation type and specifications can be guided by your general contractor or HVAC specialist to optimize energy efficiency and temperature control.
Climate control is essential for certain warehouse uses. An engineer can help specify the right HVAC systems based on your warehouse’s intended use, ensuring efficient heating, cooling, and ventilation.
The number, type, and size of doors impact both functionality and costs. Consider what is needed to support daily operations and any specific loading requirements.
Depending on your distribution needs, plan for the number and size of loading docks required. Loading docks impact the efficiency of deliveries and dispatch, influencing both design and material costs.
Determine if additional interior spaces are needed, such as offices, lunchrooms, break areas, or restrooms. These areas add to the project’s finishing costs and may require specific fixtures, materials, and design considerations.
Estimating warehouse construction costs involves careful analysis of various factors, from the building’s size and intended use to material selection and long-term operational expenses. Key costs include hard, soft, financing, and ongoing maintenance, all of which are influenced by the warehouse’s complexity and functional needs. Strategic planning, simple design choices, and energy-efficient upgrades can help optimize costs while meeting project goals. Considering additional needs, like climate control or specialized storage, is crucial for achieving a cost-effective and functional warehouse. With careful management and informed decision-making, a warehouse project can meet budget requirements while providing lasting value.
The average cost to build a warehouse ranges from $24 to $72 per square foot, depending on size, materials, and design specifications.
A 30x40 warehouse, approximately 1,200 square feet, typically costs around $42,000 for a turnkey construction.
Key cost factors include warehouse size, material selection, delivery fees, labor, site preparation, and any specialized storage requirements like climate control.
A 50,000-square-foot warehouse may cost around $3,750,000, depending on location, design, and construction materials.
Hard costs cover the physical aspects of construction, such as labor, materials, grading, site development, and landscaping, which tend to vary with market conditions.
Soft costs include non-physical project expenses like permits, insurance, taxes, engineering, and design fees, which are essential for completion but can vary widely.
Many projects involve financing, which may include construction loans, bridge financing, and long-term funding, impacting the overall budget with associated interest and fees.
Yes, strategies include simplifying the design, using natural light, selecting efficient materials, and planning for future expansion to avoid costly retrofitting.
Insulation helps control interior temperatures, which is crucial for energy efficiency, especially in warehouses with climate control needs. Adding insulation increases initial costs but reduces long-term utility expenses.
Taller warehouses require more structural support, increasing steel and material costs as well as long-term heating and cooling expenses.
Cross-docking involves direct client interaction to reduce handling time, storage needs, and management costs by speeding up the distribution process.
Planning for future growth with expandable walls is more cost-effective than retrofitting, saving on construction and material expenses if expansion is needed later.
Material costs vary by warehouse type; for example, cold storage warehouses typically cost more per square foot than standard warehouses due to additional insulation and structural requirements.
A concrete foundation for a warehouse costs around $7.20 per square foot, higher than residential foundations due to the reinforced structural demands.
Warehouse construction includes initiation, preconstruction (planning/design), procurement (materials/equipment sourcing), and construction, each phase involving specific steps to ensure project success.
A turnkey warehouse is a fully completed project ready for immediate use, typically covering everything from foundations and structures to electrical and HVAC installations.
At Estimate Florida Consulting, we offer detailed cost estimates across all major trades, ensuring no part of your project is overlooked. From the foundation to the finishing touches, our trade-specific estimates provide you with a complete and accurate breakdown of costs for any type of construction project.
We take pride in delivering accurate, timely, and reliable estimates that help contractors and builders win more projects. Our clients consistently praise our attention to detail, fast turnaround times, and the positive impact our estimates have on their businesses.
Estimate Florida Consulting has helped us win more bids with their fast and accurate estimates. We trust them for every project!
Submit your project plans, blueprints, or relevant documents through our online form or via email.
We’ll review your project details and send you a quote based on your scope and requirements.
Confirm the details and finalize any adjustments to ensure the estimate meets your project needs.
Receive your detailed, trade-specific estimate within 1-2 business days, ready for your project execution.
561-530-2845
info@estimatorflorida.com
Address
5245 Wiles Rd Apt 3-102 St. Pete Beach, FL 33073 United States
561-530-2845
info@estimatorflorida.com
Address
5245 Wiles Rd Apt 3-102 St. Pete Beach, FL 33073 United States
All copyright © Reserved | Designed By V Marketing Media | Disclaimer