Warehouse Construction Cost
The average turnkey cost to build a warehouse now ranges from $26 to $78 per square foot. Depending on the size and specifics, costs can vary widely. For example, a smaller 30×40 warehouse might cost around $45,500, while a larger 50,000-square-foot distribution center could easily exceed $1.3 million.
Key Factors Impacting Warehouse Construction Costs
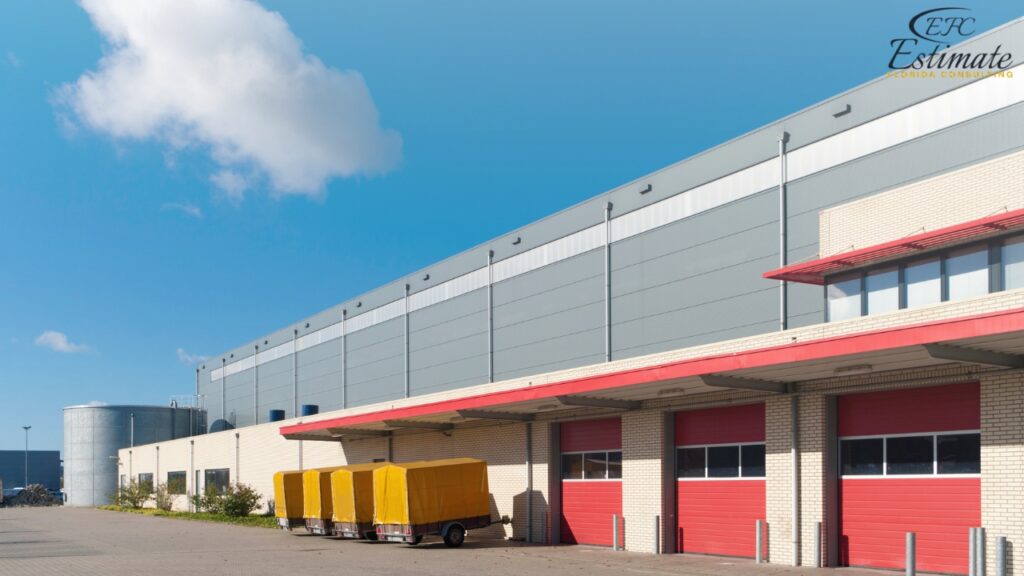
Understanding the various factors that influence the cost of building a warehouse can help you make informed decisions and manage your budget more effectively. Here’s a closer look at what affects the overall cost:
Size
The size of your warehouse is one of the biggest factors that will determine the cost. Larger warehouses naturally require more building materials, more hours of labor, and possibly more advanced construction equipment. The bigger the project, the more resources are needed. For instance, a small warehouse for basic storage might have lower costs, while a large distribution center could require a significant investment. As the square footage increases, so does the need for specialized services, making it crucial to plan your budget according to the scale of your project.
Location
The location where you plan to build your warehouse can have a significant impact on your budget. Construction costs can vary widely depending on the region. In some areas, the cost of materials and labor is higher due to factors like local demand, transportation costs, and regional economic conditions. For example, building in a metropolitan area might be more expensive than in a rural location. Additionally, local building codes and regulations can influence costs, so it’s important to factor in any location-specific requirements that might affect the overall price.
Materials
The materials you choose for your warehouse construction play a crucial role in determining the final cost. Different materials come with different price tags and levels of durability. High-quality materials like concrete, glass, and insulated metal panels (IMPs) are more expensive but offer long-term benefits, including energy efficiency and durability. On the other hand, standard metal wall and roof panels are more affordable upfront but may require more maintenance over time. When selecting materials, consider both the initial costs and the long-term savings they might provide, especially in terms of energy efficiency and durability.
Design
The design of your warehouse is another factor that can influence costs significantly. A simple, straightforward design will generally be more affordable, while a complex design with unique features can increase expenses. For instance, warehouses with specialized roof styles, multiple levels, or intricate layouts require more detailed engineering and longer construction time. This not only increases the amount of materials and labor needed but also requires more time from architects and engineers, which can add to the overall cost. Custom designs that cater to specific business needs can be a worthwhile investment, but they come at a higher price.
Intended Use
How you plan to use the warehouse will also impact construction costs. Warehouses that are intended for basic storage might have simpler requirements and, therefore, lower costs. However, if your warehouse needs to support manufacturing operations, or if it’s designed for high-traffic distribution activities, it will require more robust infrastructure. This might include reinforced flooring, specialized loading docks, or heavy-duty shelving systems. The intended use of the warehouse can dictate the level of customization required, influencing both construction costs and long-term operational efficiency.
Additional Features
Finally, any extra features you want to include in your warehouse can add to the overall cost. For example, if your warehouse needs refrigeration units for cold storage, advanced security systems for sensitive materials, or even eco-friendly features like solar panels, these will increase the initial investment. While these features can provide significant benefits, such as improved security, better energy efficiency, and compliance with industry regulations, they also add to the overall cost of construction. It’s important to weigh these benefits against the additional costs to determine what’s essential for your operation.
How Much Does It Cost to Build a Commercial Warehouse?
Building a commercial warehouse involves various costs, and understanding how much does it cost to build a commercial warehouse requires considering several factors. The average turnkey cost now ranges from $26 to $78 per square foot, depending on size, materials, and specific design elements. For instance, a smaller 30×40 warehouse might cost around $45,500, while a larger 50,000-square-foot distribution center could easily exceed $1.3 million. These costs can also vary based on location, site preparation, permits, and specialized features like climate control or heavy-duty flooring. Consulting with construction experts is crucial to get a tailored and accurate estimate for your project.
Steel Warehouse Construction Costs by Building System
When it comes to building a modern warehouse, you have a few different construction methods to choose from, each with its own cost implications. Let’s break down the options:
Pre-Engineered Metal Building (PEMB) Construction
PEMB construction is a popular choice for warehouses because it involves using prefabricated components that are assembled on-site. This approach is often quicker and more cost-effective than other construction methods, with typical build costs ranging from $26 to $45.50 per square foot. This makes it ideal for projects with tight timelines. However, while PEMB is efficient, it might not offer as much design flexibility as other methods, which could be a consideration if you need a highly customized layout.
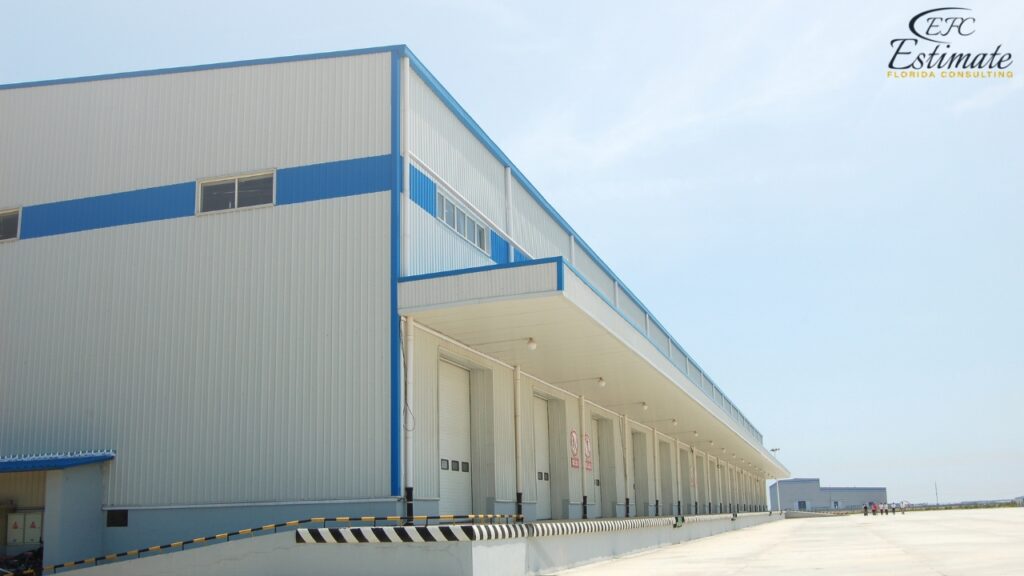
Tilt-Up Construction
Tilt-up construction is another efficient method where concrete panels are poured on a flat surface and then tilted up to form the warehouse walls. This method is relatively fast and offers a good balance between cost and durability, with typical build costs falling between $52 to $71.50 per square foot. However, it may not be the best choice for very large warehouses or those with intricate designs, as it’s somewhat limited in terms of scalability and complexity.
Structural Steel-Frame (Weld-Up) Construction
For those looking to build a larger or more complex warehouse, structural steel-frame construction is a solid option. This method uses steel beams and columns to create the warehouse’s frame, which is then completed with materials like concrete or masonry for the walls and roof. While this method offers the greatest flexibility in design and can accommodate larger structures, it’s also more labor-intensive and generally comes with higher costs, typically ranging from $58.50 to $78 per square foot.
Sample Warehouse Costs by Size
If you’re planning to build a warehouse using Pre-Engineered Metal Building (PEMB) construction, here are some rough cost estimates based on popular warehouse sizes:
Square Feet | Estimated Cost | Cost per Sq Ft |
1,200 sq ft | $43,680 | $36.40/sq ft |
2,400 sq ft | $80,860 | $33.80/sq ft |
5,000 sq ft | $156,000 | $31.20/sq ft |
10,000 sq ft | $299,000 | $29.90/sq ft |
20,000 sq ft | $585,000 | $29.90/sq ft |
50,000 sq ft | $1,495,000 | $29.90/sq ft |
These estimates give you a ballpark figure, but keep in mind that various factors, such as site preparation, foundation work, and local building codes, can influence the final cost. For the most accurate pricing:
- Consult a Local Structural Engineer: They can provide detailed estimates for site preparation, foundation work, and any unique requirements your site may have.
- Collaborate with Your Building Supplier: Work closely with your supplier to finalize design requirements and ensure the building meets your specific needs.
- Check with Local Building Authorities: Speak with your local building department to understand the building permit process, fees, and any additional regulations that might apply to your project.
Additional Cost Considerations for Warehouse Construction
When planning your warehouse project, it’s important to account for several additional costs that can significantly impact your overall budget. These costs will vary depending on your warehouse’s intended use, location, and specific needs.
Insulation
When considering the Metal Warehouse Insulation Cost, insulation is a major factor that can impact both initial and long-term expenses. Depending on your warehouse’s location and purpose, insulation may be essential for maintaining a stable internal temperature. The type of insulation required will depend on factors like climate, energy efficiency goals, and the materials used in your building. Consulting with your general contractor (GC) or an HVAC specialist can help you determine the best insulation solution for your warehouse. While quality insulation might increase the upfront costs, it can lead to significant energy savings over time.
Climate and Environmental Control
If your warehouse will store temperature-sensitive goods or requires specific climate conditions, you’ll need to install an HVAC system designed to meet those needs. Engineers can help specify the right heating, ventilation, and air conditioning systems to ensure optimal environmental control. While this can add to your upfront expenses, it’s crucial for protecting your inventory and ensuring a comfortable working environment for employees.
Doors
The number, type, and size of doors are other important considerations. Whether you need large bay doors for trucks or standard-sized entry doors, each type will come with its own set of costs. The choice of material, automation features, and security measures will also influence the overall price. Properly planning the door layout and specifications is essential for ensuring smooth operations and efficient workflow in your warehouse.
Loading Docks
Loading docks are critical for warehouses involved in logistics and distribution. The number of docks, their size, and the type of equipment required (like dock levelers and shelters) will depend on your warehouse’s operational needs. Properly designed loading docks can streamline your shipping and receiving processes, but they do come with additional costs that should be factored into your budget.
Interior Finishing and Build-Out
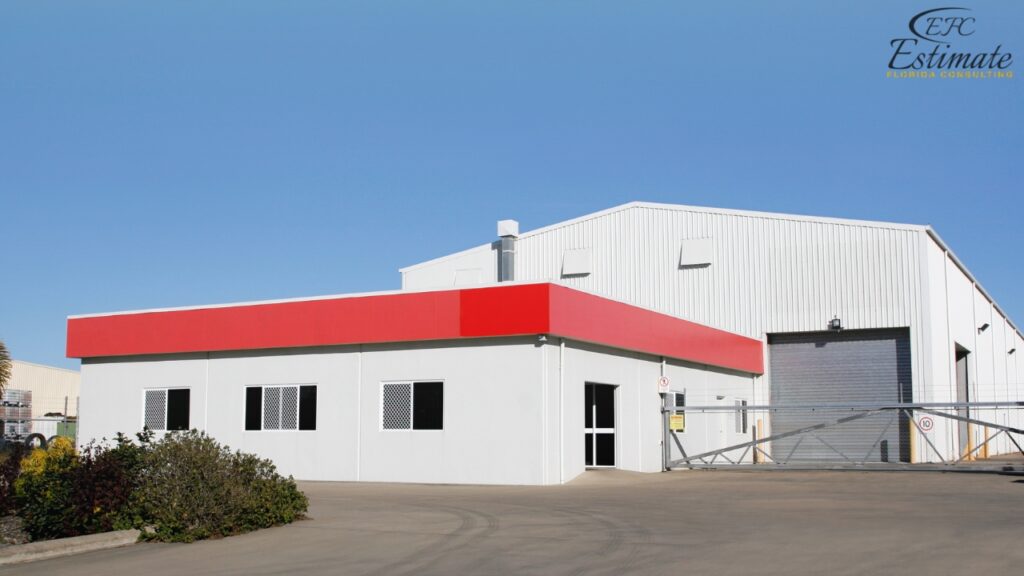
Finally, consider the interior finishing and build-out of your warehouse. This could include office spaces, break rooms, restrooms, and other amenities. The cost of these additions will vary depending on the level of finish and the specific requirements of your operation. Well-designed interior spaces can enhance the functionality and comfort of your warehouse, but they also add to the overall construction cost.
Planning and Construction of a Prefabricated Steel Warehouse
Planning and constructing a prefabricated steel warehouse is a significant investment that requires careful consideration and thorough preparation. With the advancement of modern warehouse designs, you now have access to a variety of options that can be tailored to your specific needs. Partnering with a pre-engineered building manufacturer can streamline the process, providing you with sample plans and designs that align with your warehousing requirements. However, there are several key factors you need to consider to ensure the project’s success.
Understanding Local Building Codes
One of the first steps in planning your steel warehouse is understanding and complying with local building codes. This involves contacting your local building department to discuss your intended use of the warehouse and the specifics of the building you plan to construct. You’ll need to provide engineered building plans, foundation plans, and a detailed site plan that indicates access routes and the exact location of your building on the plot. As the project owner, it’s your responsibility to ensure that the metal building supplier has the correct and final code information. Additionally, it’s wise to research setbacks and other local regulations that may affect the feasibility of using a steel building on your chosen lot. Navigating these requirements early on can help you avoid costly delays and ensure a smooth construction process.
Choosing the Right Warehouse Size
Selecting the appropriate size for your warehouse is crucial and should be based on several factors. Consider the amount and type of inventory you plan to store, the number of employees who will work in the warehouse, and the space required for equipment and other facilities. It’s also important to think about future growth and expansion. If you anticipate needing more space down the road, be sure to specify ‘expandable end walls’ when ordering your steel building. This foresight can save you money and hassle in the long term by making future expansions more manageable.
The size of the warehouse should also accommodate the vehicles used for transporting goods in and out of the facility, as well as the layout of the surrounding area. Striking a balance is key—you want a warehouse large enough to meet your current and future needs without being so oversized that it becomes inefficient or costly to maintain. If you’re unsure about how much space you’ll need, consider using a space calculator designed to help determine the square footage required for pallet racking and other storage solutions.
Key Considerations for Warehouse Height and Roof Design
When planning your steel warehouse, two critical aspects of height must be considered: the overall height, known as eave height, and the interior clearance height. Zoning laws typically regulate the eave height, but it’s the interior clearance height that will have a more significant impact on your design decisions. For most small to medium-sized warehouse applications, a clearance height of 16 to 20 feet is sufficient. However, it’s essential to note that most Pre-Engineered Metal Buildings (PEMB) are generally limited to a maximum height of 30 feet unless you opt for specialized and more expensive engineering solutions.
Roof Profile and Pitch
The roof design is another vital element in warehouse construction. Most warehouses feature a single-slope roof profile with a 1:12 or 2:12 pitch, which is generally the most cost-effective option. However, it’s crucial to consider both the roof’s shape and pitch, as rigid frame metal buildings offer several roofing options. Selecting the right roof for your needs while ensuring compliance with local regulations is essential for the longevity and functionality of your warehouse. For more in-depth information, you can explore our metal building roofs page, which details various roofing systems and their benefits.
Download Template For Warehouse Project Breakdown
- Materials list updated to the zip code
- Fast delivery
- Data base of general contractors and sub-contractors
- Local estimators
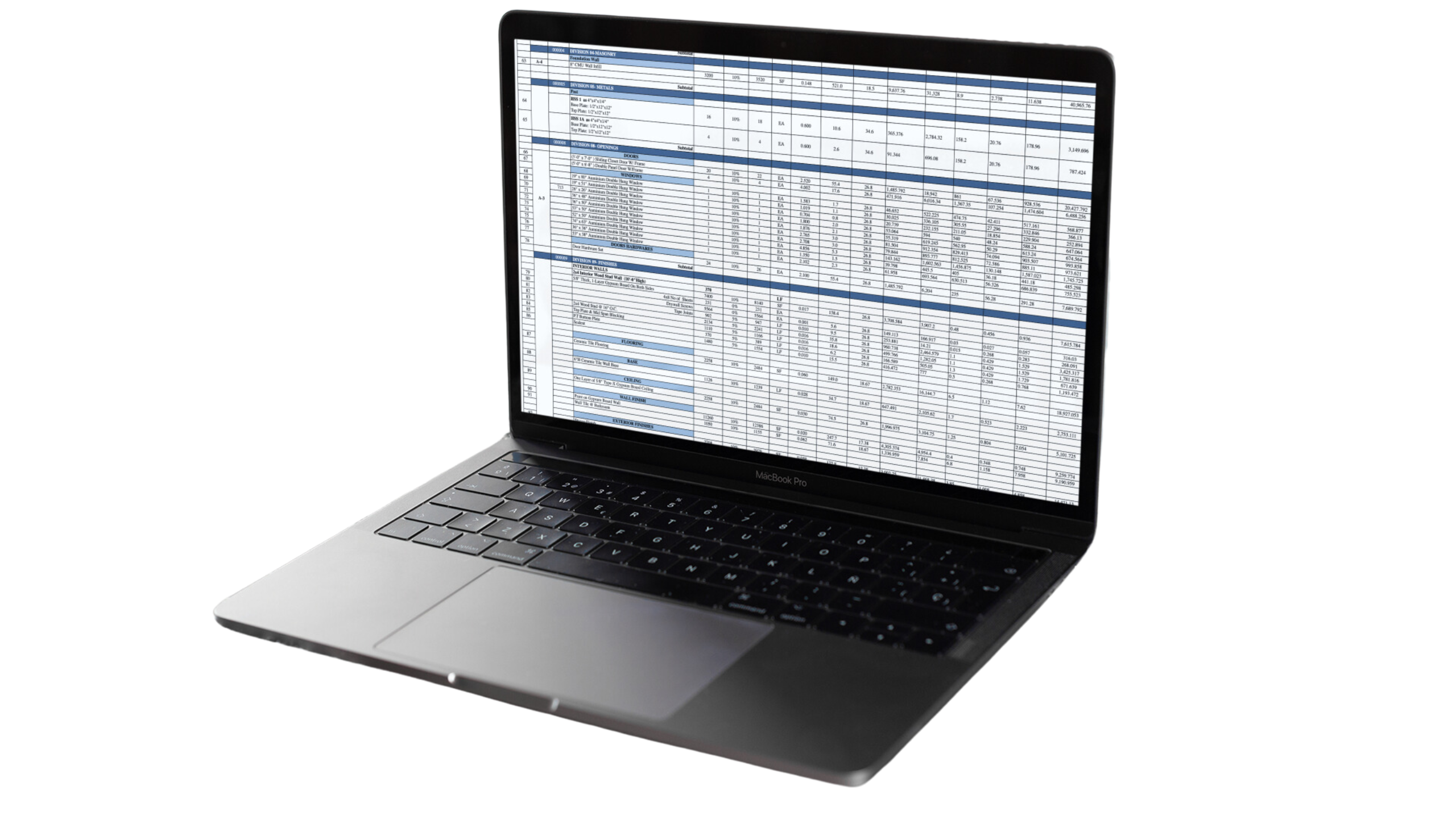
Moving from Design to Construction: Key Steps
Once you’ve nailed down the design of your steel building, several crucial steps remain before construction can commence:
Engineering and Blueprint Creation
After finalizing the basic design and paying a deposit, a certified engineer will create the building’s specifications and blueprints. These blueprints detail the materials to be used and the loads the building must withstand to meet local building codes. This step ensures that your building is structurally sound and compliant with all relevant regulations, which is essential for avoiding costly modifications or delays later in the project.
Fabrication and Delivery of Components
Once the blueprints are approved, the real production begins. The steel framing components, siding, and roofing panels are fabricated at the factory. These parts are pre-cut, pre-drilled, and ready to be bolted together by your construction crew. The fabrication process can take anywhere from four to sixteen weeks, depending on the complexity of your structure. It’s important to factor this time into your overall construction timeline to avoid any scheduling conflicts.
Preparing the Building Site
While your building components are being manufactured, you can prepare the construction site. Steel buildings typically require poured concrete foundations, which need to be ready before the structure arrives. Proper site preparation is crucial for ensuring a smooth and efficient construction process, as it sets the stage for the successful assembly of your steel warehouse.
6 Smart Strategies to Reduce Warehouse Construction Costs
Building a warehouse is a significant investment, but there are ways to keep costs down without compromising on quality. Here are six practical strategies to help you save money on your new build. Keep in mind that not all of these tips may apply to your specific needs, but they offer valuable insights into cost-saving opportunities.
1. Thorough Planning
A well-thought-out plan is crucial for any major construction project. By meticulously planning every detail, you can avoid costly change orders and minimize the risk of budget overruns. Sticking to a strict timeline can also help reduce expenses related to construction financing loans, which can quickly add up if your project faces delays.
2. Simplify the Design
Opting for a simpler design can significantly cut costs. A straightforward design requires less material, design time, and engineering effort compared to more elaborate structures. Streamlining the design process not only saves money but also speeds up construction, getting your warehouse operational faster.
3. Choose a Basic Roof Profile and Low Pitch
When it comes to roofing, a single-sloped roof with a 1:12 pitch is the most cost-effective option. More complex roof designs, like gable or hip roofs, involve additional materials, engineering, and construction time, which can drive up costs. If you need an alternative, a gable roof with a 2:12 pitch offers a balance between functionality and affordability.
4. Optimize Warehouse Height
Be realistic about your height requirements. Taller buildings require more steel, which increases both construction and long-term operational costs, such as heating and cooling. By reducing the height to what is truly necessary, you can save a substantial amount on both the initial build and ongoing expenses.
5. Plan for Future Expansion
If you anticipate needing more space in the future, plan for it now. Steel buildings can be easily expanded later if you include ‘expandable end walls’ in your initial design. Without this foresight, adding additional bays in the future will be much more expensive, as it will involve extra engineering and construction work.
6. Compare Quotes
Prices for pre-engineered metal building packages can vary widely depending on the manufacturer and location. It’s wise to get at least four written quotes from different suppliers to compare costs. This approach ensures you’re getting the best deal for your project. Tools like BuildingsGuide can assist by matching you with vetted suppliers who meet your specific needs and deliver to your job site.
Is It Cheaper to Buy or Rent a Warehouse?
Deciding whether to buy or rent a warehouse depends on your business’s unique needs, financial situation, and long-term objectives. Let’s break down the factors to help you make an informed decision:
1. Cost to Build or Rent
Purchasing a warehouse might seem more expensive initially, but it can save you money over time by eliminating ongoing rental payments. Owning the property can be a wise investment, especially as property values rise. On the other hand, renting might be more budget-friendly in the short term but may not offer the same long-term financial benefits as owning.
2. Investment Potential
Buying a warehouse can be a valuable investment, particularly if property values in the area increase. Owning the property allows you to capitalize on its appreciation, potentially selling or leasing it at a profit later. Renting doesn’t offer the same opportunity to benefit from rising land values, so consider your long-term financial goals when making this decision.
3. Flexibility
Renting a warehouse provides greater flexibility to move or expand your operations as your business grows or changes. If you anticipate the need to relocate or scale up quickly, renting might be the better option. However, buying a warehouse requires more planning and a stronger commitment to the location, making it ideal for businesses with stable, long-term plans.
4. Location Considerations
The warehouse’s location plays a crucial role in your decision. If you’re confident about operating in a specific area for an extended period, buying could be a smart investment. However, if your business needs to be in a particular location for only a short time, renting might be more practical and less risky.
5. Financing Options
If you’re considering purchasing a warehouse, it’s essential to review the financing terms carefully. Look at the interest rates, repayment periods, and any associated fees or closing costs. Ensure the loan terms align with your business’s financial capabilities and long-term goals. Renting, on the other hand, typically involves fewer financial complexities, making it a more straightforward option for some businesses.
Conclusion
When planning to build a warehouse, costs can quickly add up depending on various factors like size, location, and design complexity. The average turnkey cost to construct a warehouse now ranges between $26 and $78 per square foot, with smaller warehouses costing around $45,500 and larger distribution centers exceeding $1.3 million. To manage these costs effectively, consider thorough planning, simplifying designs, opting for basic roof profiles, and planning for future expansion. Comparing quotes from different suppliers can also help you secure the best deal. Ultimately, balancing these factors with your business needs will ensure a cost-effective warehouse construction project.
FAQs
The average turnkey cost to build a warehouse ranges from $26 to $78 per square foot. For instance, a smaller 30×40 warehouse might cost around $45,500, while a larger 50,000-square-foot distribution center could exceed $1.3 million. The cost varies based on size, location, materials, and design complexity.
Several factors influence warehouse construction costs:
- Size: Larger warehouses require more materials, labor, and potentially specialized equipment, increasing the overall cost.
- Location: Costs can vary by region due to differences in labor, materials, and local building codes.
- Materials: High-quality materials like concrete and insulated metal panels cost more but offer long-term benefits.
- Design: Complex designs with specialized features increase expenses due to more detailed engineering and longer construction times.
- Intended Use: Warehouses designed for manufacturing or high-traffic distribution need more robust infrastructure, raising costs.
- Additional Features: Extras like refrigeration units, security systems, or eco-friendly additions can further increase costs.
There are three main construction methods, each with different cost implications:
- Pre-Engineered Metal Building (PEMB): This method is cost-effective and quick, with costs ranging from $26 to $45.50 per square foot. It’s ideal for simpler designs and tight timelines but offers less design flexibility.
- Tilt-Up Construction: Involves pouring concrete panels on-site and tilting them up to form walls. Costs range from $52 to $71.50 per square foot, offering a balance between cost and durability but limited scalability.
- Structural Steel-Frame (Weld-Up): This method is used for larger, complex warehouses. It offers the most design flexibility but is more labor-intensive and costly, ranging from $58.50 to $78 per square foot.
Here are rough estimates for PEMB construction based on popular warehouse sizes:
- 1,200 sq ft: $43,680 ($36.40/sq ft)
- 2,400 sq ft: $80,860 ($33.80/sq ft)
- 5,000 sq ft: $156,000 ($31.20/sq ft)
- 10,000 sq ft: $299,000 ($29.90/sq ft)
- 20,000 sq ft: $585,000 ($29.90/sq ft)
- 50,000 sq ft: $1,495,000 ($29.90/sq ft)
In addition to basic construction costs, consider:
- Insulation: Essential for temperature control, especially in climate-sensitive environments. Costs vary based on type and efficiency.
- Climate Control: HVAC systems tailored to your warehouse’s needs can add to upfront costs but are necessary for protecting inventory and ensuring a comfortable workspace.
- Doors: The type, size, and number of doors impact overall cost, especially if specialized doors like large bay or security doors are needed.
- Loading Docks: Crucial for logistics, the number, size, and equipment (like dock levelers) required will depend on operational needs.
- Interior Finishing: Includes office spaces, break rooms, and restrooms, which add to construction costs based on the level of finish and specific requirements.
When planning a prefabricated steel warehouse:
- Building Codes: Understand and comply with local building codes by consulting your local building department.
- Warehouse Size: Choose a size that meets current and future needs, considering inventory, employees, and equipment.
- Height and Roof Design: Ensure the height and roof design meet your needs and comply with local regulations.
- Engineering and Site Preparation: Work with certified engineers to finalize blueprints and prepare the site, including concrete foundations.
To manage and reduce construction costs:
- Thorough Planning: Avoid costly change orders and overruns by meticulously planning your project.
- Simplified Design: Opt for simpler designs to reduce material and labor costs.
- Basic Roof Profile: Choose a single-sloped roof with a low pitch to minimize roofing expenses.
- Optimize Height: Be realistic about height requirements to save on materials and long-term operational costs.
- Plan for Expansion: Include expandable end walls to facilitate future growth without significant additional expense.
- Compare Quotes: Obtain multiple quotes to ensure competitive pricing and the best value for your project.
The decision to buy or rent depends on:
- Cost: Buying may have higher upfront costs but offers long-term savings by eliminating rent. Renting is more affordable initially but doesn’t offer the same long-term financial benefits.
- Investment Potential: Owning allows you to capitalize on property value increases, while renting doesn’t offer this benefit.
- Flexibility: Renting offers more flexibility to relocate or expand, whereas buying requires more commitment.
- Location: Consider if the warehouse’s location aligns with your long-term business goals.
- Financing: Review financing options carefully if buying, ensuring the terms fit your business’s financial situation. Renting is typically less complex financially.
To get the most accurate quotes:
- Consult a Local Structural Engineer: They can provide detailed estimates for site preparation and foundation work.
- Collaborate with Your Building Supplier: Ensure the building design meets your specific needs and budget.
- Check with Local Building Authorities: Understand permit processes, fees, and regulations that might affect your project.
Google Reviews
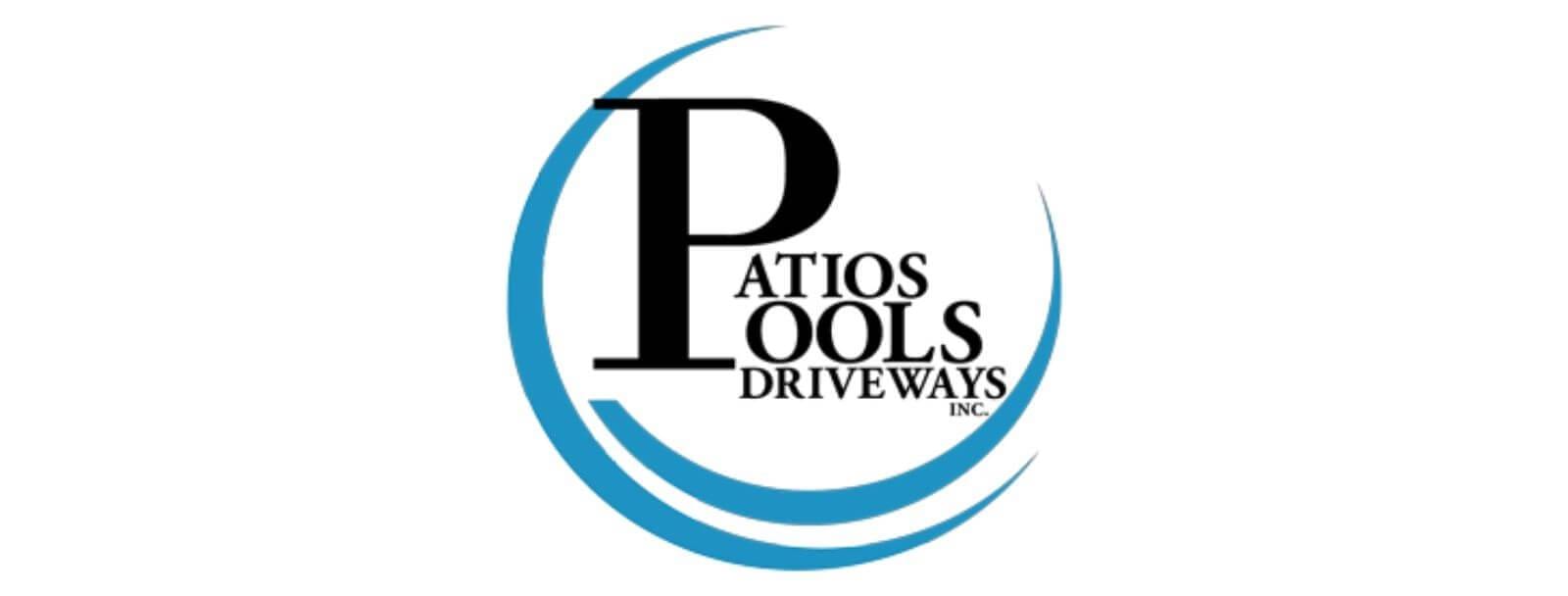
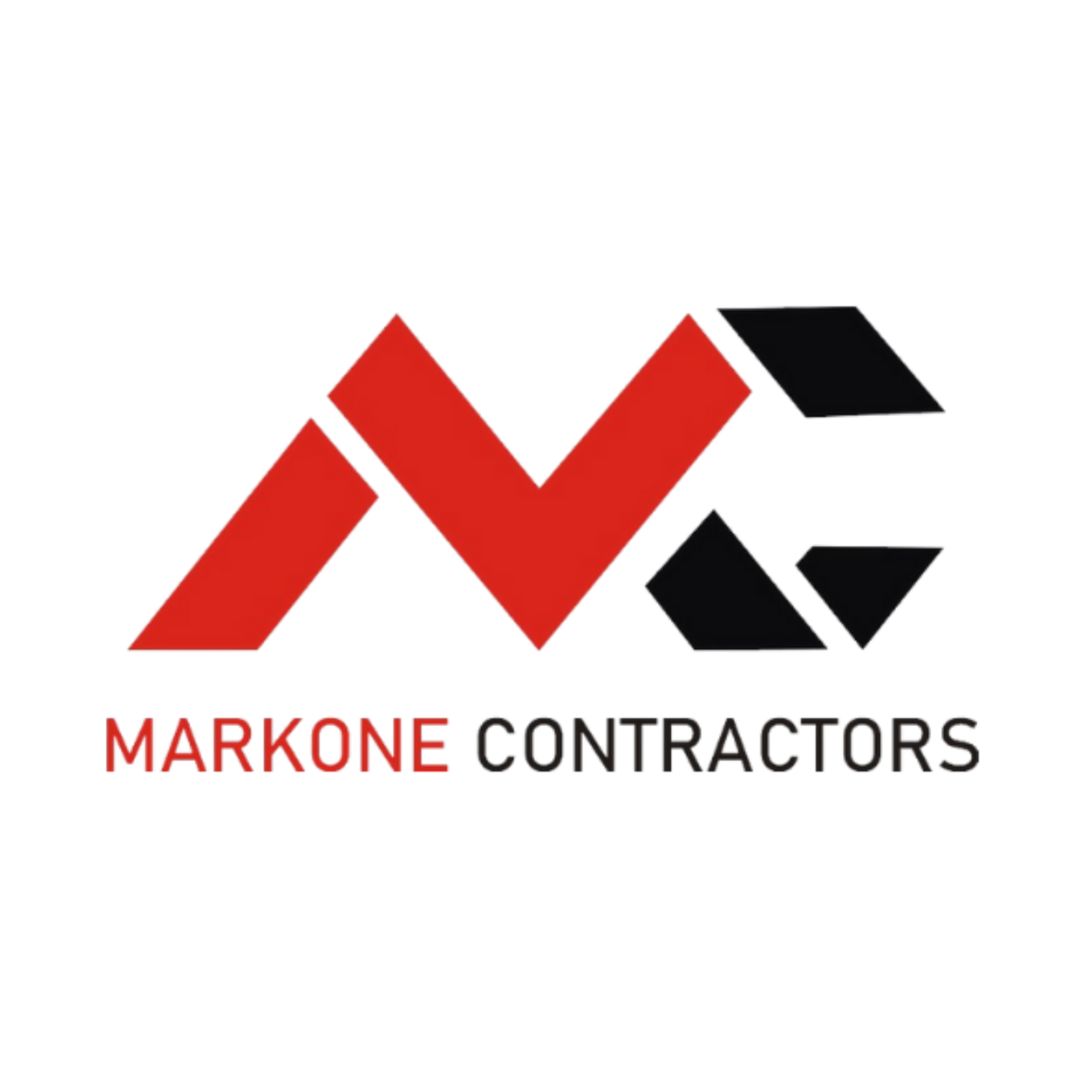

Process To Get The Warehouse Construction Estimate Report
Here I am going to share some steps to get the warehouse construction estimate report.
-
You need to send your plan to us.
You can send us your plan on info@estimatorflorida.com
-
You receive a quote for your project.
Before starting your project, we send you a quote for your service. That quote will have detailed information about your project. Here you will get information about the size, difficulty, complexity and bid date when determining pricing.
-
Get Estimate Report
Our team will takeoff and estimate your project. When we deliver you’ll receive a PDF and an Excel file of your estimate. We can also offer construction lead generation services for the jobs you’d like to pursue further.