- Homepage
- Tilt-Up Concrete Construction Cost Estimator
Tilt-Up Concrete Construction Cost Estimator
Leading provider of tilt-up concrete estimating.
Tilt-up concrete construction is a highly efficient and cost-effective method for building large commercial structures, including warehouses, retail stores, and office buildings. The cost of tilt-up concrete construction typically ranges from $156 to $234 per square foot. This cost range includes materials, labor, and equipment, but the total cost can vary significantly depending on factors such as building size, design complexity, panel thickness, site conditions, and the level of customization required. Understanding these factors is crucial for budgeting effectively and ensuring the success of your project. By considering each aspect in detail, you can achieve a balance between cost-efficiency and high-quality construction, ensuring that your investment delivers long-term value.
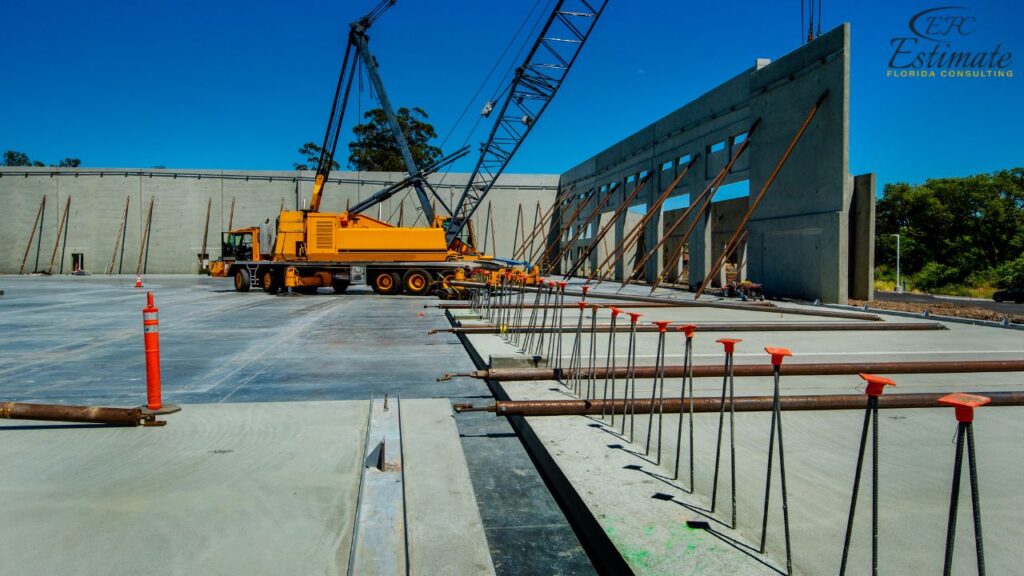
Cost Breakdown for Tilt-Up Concrete Construction by Building Size
The cost of tilt-up concrete construction varies depending on the size of the building. Larger buildings may benefit from economies of scale, which can reduce the cost per square foot, but the overall cost increases with the size of the project. Here is a detailed cost breakdown based on different building sizes:
Building Size (Square Feet) | Cost per Square Foot | Total Cost Range |
10,000 sq ft | $156 – $234 | $1,560,000 – $2,340,000 |
20,000 sq ft | $149.50 – $227.50 | $2,990,000 – $4,550,000 |
50,000 sq ft | $143 – $221 | $7,150,000 – $11,050,000 |
100,000 sq ft | $136.50 – $214.50 | $13,650,000 – $21,450,000 |
200,000 sq ft | $130 – $208 | $26,000,000 – $41,600,000 |
How Much Does Tilt-Up Concrete Construction Cost per Square Foot?
Tilt-up concrete construction costs are generally calculated on a per-square-foot basis, providing a more accurate estimate tailored to the specific needs of the project. The cost per square foot can range from $156 to $234, depending on various factors, including the quality of materials used, the complexity of the project, and the labor required. Here’s a breakdown of the per-square-foot costs:
Cost Component | Cost per Square Foot |
Concrete Materials | $65 – $110.50 |
Labor Costs | $39 – $84.50 |
Equipment Rental | $13 – $39 |
Site Preparation and Foundation | $26 – $52 |
Panel Finishes and Customization | $13 – $32.50 |
Concrete Materials
Concrete materials form the foundation of any commercial painting project. This cost covers the price of concrete, reinforcement, and any necessary admixtures used during the panel casting process. The wide range in pricing reflects fluctuations in the market for essential materials like cement, aggregates, and steel, which can significantly impact the overall project cost.
Labor Costs
Labor costs are a crucial component, encompassing the skilled labor required for casting, lifting, and securing panels. These tasks are vital to ensure the structural integrity and long-term durability of the building. The increase in labor costs over time can be attributed to rising wages and shortages in the construction industry, making labor one of the most variable factors in your painting project budget.
Equipment Rental
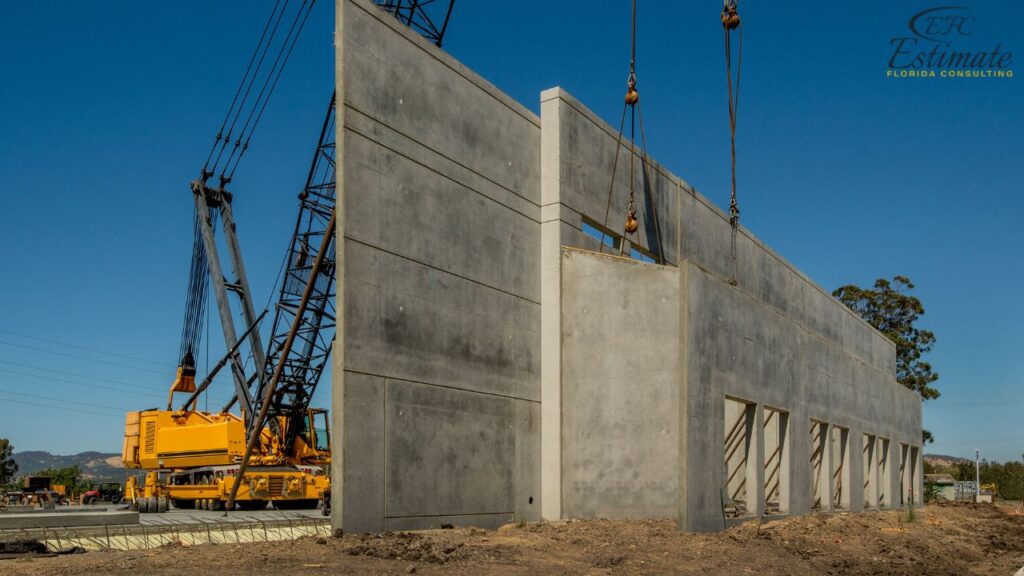
Specialized equipment is necessary for handling and positioning the panels, and these costs cover the rental of cranes, lifting devices, and other machinery. Equipment rental rates can vary based on demand, with higher costs often seen during peak construction periods.
Site Preparation and Foundation
Before painting can begin, proper site preparation and foundation work must be completed. This involves grading, excavation, and other foundation tasks essential for creating a stable base. The costs in this category have been rising due to increased fuel prices and the high demand for heavy machinery.
Panel Finishes and Customization
To enhance the aesthetic appeal of the building, additional costs may be incurred for panel finishes and customization. This includes adding textures, colors, patterns, and other features that can significantly improve the visual impact of the structure. The growing demand for premium finishes and materials has contributed to the rise in these costs, making it a key consideration for those looking to achieve a specific look or design.
Skilled Concrete Experts?
- Concrete Foundation and Slab Installation for Office Buildings
- Structural Concrete Services for Commercial Projects
- Concrete Paving and Hardscaping Solutions
- Warehouse Concrete Flooring and Structural Design
- Commercial Building Concrete Renovations and Upgrades
- Concrete Repair, Resurfacing, and Restoration Services
Advantages of Tilt-Up Concrete Construction for Commercial Buildings
Tilt-up concrete construction offers numerous advantages for commercial buildings, making it a preferred choice for many developers and contractors. These benefits have become even more pronounced in today’s market, where efficiency and cost-effectiveness are paramount.
- Cost Efficiency: Tilt-up construction is often more economical than traditional building methods due to reduced labor and material handling requirements. The panels are cast on-site, which eliminates the need for transporting large precast panels, thus reducing overall costs. Additionally, by minimizing the need for extensive formwork and scaffolding, tilt-up construction can save both time and money.
- Speed of Construction: The process of casting and lifting panels allows for rapid construction timelines, enabling faster project completion compared to other construction methods. This speed is particularly beneficial for commercial projects where time-to-market is critical. Faster construction not only reduces labor costs but also allows businesses to start operations sooner, leading to quicker returns on investment.
- Durability and Strength: Tilt-up concrete buildings are known for their durability and strength. The concrete panels provide excellent resistance to natural disasters, such as hurricanes, earthquakes, and fires, making them ideal for regions prone to extreme weather. The inherent strength of concrete also enhances the building’s longevity, reducing maintenance costs over time.
- Energy Efficiency: Concrete’s high thermal mass helps regulate indoor temperatures by absorbing and slowly releasing heat, which can lead to lower energy costs for heating and cooling. This energy efficiency contributes to the overall sustainability of the building, making tilt-up construction an environmentally friendly option that meets modern energy standards.
- Design Flexibility: Tilt-up construction offers a variety of aesthetic options, including different textures, colors, and finishes. Panels can be customized to achieve the desired look, allowing for creative and visually appealing designs. This flexibility makes it possible to create unique, architecturally interesting commercial buildings that stand out while still benefiting from the durability and cost-effectiveness of concrete.
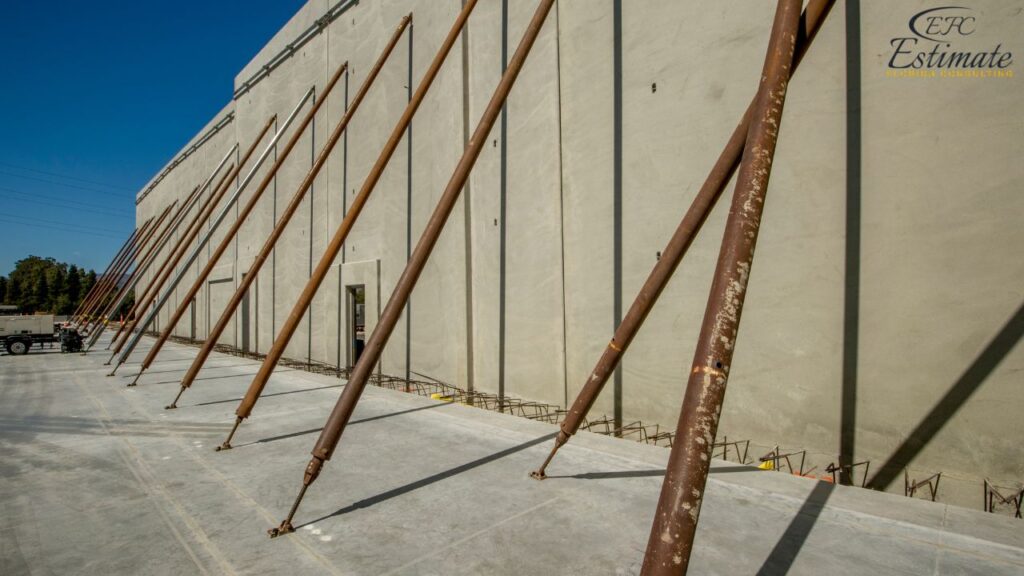
Tilt-Up Construction Process: Step-by-Step Guide
The tilt-up construction process involves several key steps, each critical to the successful completion of the project. Understanding these steps is essential for ensuring that the project is executed efficiently and meets all structural and aesthetic requirements.
- Site Preparation: The site is cleared, graded, and the foundation is poured to provide a stable base for the tilt-up panels. Proper site preparation is essential to ensure that the foundation is level and strong enough to support the weight of the concrete panels. This phase has become more costly due to increased prices for site preparation services and materials, but it remains a crucial step in the construction process.
- Panel Design and Formwork: Concrete panels are designed according to the building’s specifications. Formwork is set up on the foundation slab where the panels will be cast. This step involves detailed planning and precision to ensure that the panels meet the required dimensions and specifications. The cost of formwork materials has risen, reflecting higher material costs and the need for more intricate designs in modern commercial buildings.
- Reinforcement Installation: Steel reinforcement bars are placed within the formwork to strengthen the panels, ensuring they can withstand the loads they will bear once erected. The reinforcement is crucial for maintaining the structural integrity of the building, particularly in areas prone to seismic activity. With steel prices increasing, the cost of reinforcement has also risen, making this an important consideration in the overall budget.
- Concrete Pouring: Concrete is poured into the formwork and allowed to cure, forming the solid panels that will become the building’s walls. The curing process is carefully monitored to ensure that the concrete reaches the required strength before lifting. The cost of high-quality concrete and the necessary admixtures has increased, contributing to the overall rise in construction costs.
- Panel Lifting: Once cured, the panels are lifted (or tilted) into place using cranes. The panels are secured to the foundation and connected to each other to form the building’s structure. This step requires precise coordination and skilled labor to ensure that the panels are correctly aligned and securely fastened. The rising costs of skilled labor and equipment rental are reflected in this phase of the construction process.
- Finishing Touches: After the panels are in place, finishing touches such as sealing, painting, and installing windows and doors are completed. These final steps enhance the building’s appearance and ensure that it meets all functional and aesthetic requirements. The increased demand for high-quality finishes and materials has led to higher costs in this phase, but these
90% More Chances to Win Concrete Bids with Our Estimate
Comparing Tilt-Up Concrete to Other Construction Methods
Tilt-up concrete construction offers unique advantages compared to other construction methods, such as precast concrete, steel framing, and masonry.
- Tilt-Up vs. Precast Concrete: Tilt-up panels are cast on-site, reducing transportation costs and allowing for greater customization. In contrast, precast concrete panels must be manufactured off-site and transported to the construction site, which can add to the overall cost. Additionally, tilt-up construction allows for faster project timelines, as panels can be cast and erected on the same site without delays caused by transportation or scheduling conflicts. The on-site casting process also allows for last-minute adjustments, offering greater flexibility compared to precast methods.
- Tilt-Up vs. Steel Framing: While steel framing is lightweight and quick to erect, it may not offer the same level of durability and resistance to natural disasters as tilt-up concrete. Concrete panels provide superior thermal mass and sound insulation, making them a better choice for buildings that require high energy efficiency and noise control. Furthermore, tilt-up construction can be more cost-effective for large-scale projects, where the benefits of concrete’s durability and low maintenance requirements outweigh the initial investment.
- Tilt-Up vs. Masonry: Masonry construction, although durable and aesthetically pleasing, often requires more labor and time to complete, making it more expensive for large buildings compared to tilt-up construction. Tilt-up concrete offers a faster and more efficient construction process, with fewer workers needed to achieve similar structural strength and aesthetic appeal. Additionally, the larger, uninterrupted panels used in tilt-up construction can reduce the number of joints and potential weak points in the building’s envelope, enhancing its overall performance and longevity.
Get Acquainted with For Concrete Work
Concrete Work
Concrete
HUGE Concrete Pour
Factors Influencing the Cost of Tilt-Up Concrete Construction
Several factors can influence the overall cost of tilt-up concrete construction, each contributing to the final budget of the project. Understanding these factors is essential for effective planning and budgeting, especially in a market where costs are increasing.
- Building Size and Complexity: Larger buildings and those with more complex designs will generally have higher costs due to the increased materials, labor, and engineering required. Complex buildings may also require more detailed planning and coordination, which can add to the overall cost. The need for specialized engineering solutions to address structural challenges can also drive up costs, particularly in large-scale projects.
- Panel Thickness and Reinforcement: Thicker panels and greater reinforcement provide better structural integrity but also increase material costs. The specific requirements for panel thickness and reinforcement depend on factors such as the building’s intended use, local building codes, and environmental conditions. With the rising cost of steel and other reinforcement materials, these considerations have become even more critical in determining the overall budget.
- Site Conditions: Challenging site conditions, such as poor soil or difficult topography, may require additional site preparation, raising the overall cost. Sites with uneven terrain or difficult access may necessitate more extensive grading, excavation, or foundation work, which can significantly impact the project’s budget. The cost of addressing site-specific challenges has increased due to higher fuel prices and the demand for specialized equipment.
- Customization and Design Features: Custom finishes, intricate designs, and additional openings for windows and doors can significantly increase costs. Buildings that require a high level of aesthetic detail or specialized architectural features will generally see higher costs due to the additional labor and materials needed to achieve the desired result. The growing trend toward personalized, high-end designs has further driven up the costs associated with customization in tilt-up construction.
- Labor and Equipment Availability: The availability and cost of skilled labor and necessary equipment in the project’s location can also impact costs. In areas with high demand for construction services, labor and equipment costs may be higher, affecting the overall budget. Ensuring that the construction team is experienced in tilt-up construction can help optimize efficiency and reduce potential delays, further influencing costs. The scarcity of skilled labor and specialized equipment has become a significant factor in the rising costs of construction projects.
Design Flexibility and Aesthetic Options in Tilt-Up Concrete
Tilt-up concrete construction offers significant design flexibility, allowing for a wide range of aesthetic options that can enhance the visual appeal of commercial buildings. This flexibility is particularly valuable in today’s market, where customized, high-quality designs are in high demand.
- Panel Textures and Finishes: Panels can be customized with various textures, such as smooth, ribbed, or patterned surfaces, to achieve the desired look. These textures can be created during the casting process using different form liners, which imprint patterns into the concrete as it cures. The choice of texture can significantly impact the building’s appearance, from a modern, sleek look to a more traditional, textured finish. The increased cost of high-quality form liners and the demand for unique textures have driven up the prices in this category.
- Color Options: Colors can be added to the concrete mix or applied as a finish, offering a broad palette for achieving the desired aesthetic. Integral colorants can be mixed directly into the concrete before casting, ensuring consistent color throughout the panel. Alternatively, surface-applied stains or paints can provide a more vibrant or customized color scheme, allowing for greater design flexibility. The growing preference for custom color schemes and high-quality finishes has contributed to the overall increase in costs.
- Architectural Features: Panels can be designed to incorporate architectural features such as reveals, insets, and decorative elements. These features can be cast into the panels during the initial pour or added later as architectural enhancements. The ability to customize panels with unique architectural details allows for creative and visually striking designs that enhance the building’s overall appeal. The demand for intricate architectural features and the rising costs of materials have made this a more expensive aspect of tilt-up construction.
- Integration of Windows and Doors: Tilt-up panels can be designed with openings for windows, doors, and other elements, providing seamless integration with the building’s design. These openings can be pre-cast during the panel’s construction or cut out afterward, depending on the design requirements. The flexibility to incorporate various openings allows for greater design freedom and the ability to create buildings that meet specific functional and aesthetic needs. The cost of integrating these elements has increased due to the higher prices of materials and the complexity of custom designs.
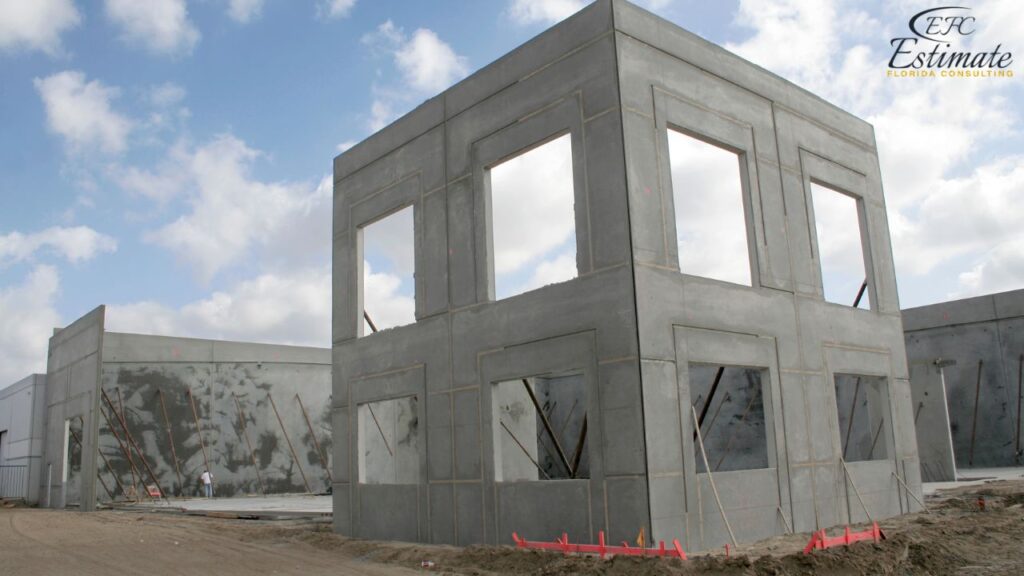
What is Tilt-Up Concrete Construction?
Tilt-up concrete construction is a method where concrete panels are cast on-site horizontally and then lifted into place to form the walls of a building. This method is widely used for large commercial structures due to its efficiency, cost-effectiveness, and speed of construction. Unlike traditional masonry or steel frame construction, tilt-up allows for the rapid erection of large, durable buildings with reduced labor and material costs. The method’s versatility makes it suitable for a wide range of applications, from industrial warehouses to retail centers and office buildings.
Tilt-Up Cost Estimator Services
For those planning a tilt-up concrete construction project, using a cost estimator service can provide accurate budgeting and financial planning. Estimate Florida Consulting offers comprehensive cost estimation services tailored to tilt-up construction projects. Their team assesses all relevant factors, including site conditions, design specifications, and current market trends, to provide a detailed estimate that reflects the true cost of your project. This service ensures that you can plan your project with confidence, avoiding unexpected expenses and ensuring that your budget aligns with your construction goals. By utilizing professional cost estimator services, you can make informed decisions that optimize your investment and help ensure the success of your tilt-up construction project.
We Provide 3D Rendering Services!
For Telt-Up Concrete and Other Projects
Turnaround time is 1-2 days.
Win More Projects With Us
How Much Does it Cost to Build a Tilt-Up Concrete Warehouse?
Building a tilt-up concrete warehouse is a cost-effective option for large storage or distribution facilities. The cost to build a tilt-up concrete warehouse typically ranges from $143 to $234 per square foot, depending on factors such as building size, panel thickness, and customization options. Below is a detailed cost breakdown based on different warehouse sizes:
Warehouse Size (Square Feet) | Cost per Square Foot | Total Cost Range |
20,000 sq ft | $149.50 – $227.50 | $2,990,000 – $4,550,000 |
50,000 sq ft | $143 – $221 | $7,150,000 – $11,050,000 |
100,000 sq ft | $136.50 – $214.50 | $13,650,000 – $21,450,000 |
200,000 sq ft | $130 – $208 | $26,000,000 – $41,600,000 |
These warehouses are not only cost-effective but also offer the durability and flexibility needed to accommodate various industrial and commercial needs. The ability to customize the design and layout of the warehouse ensures that it meets the specific operational requirements of the business, making it a practical and versatile solution for large-scale storage and distribution.
Common Challenges and Solutions in Tilt-Up Concrete Construction
While tilt-up concrete construction offers many benefits, it also presents some challenges that must be addressed to ensure the project’s success. Understanding these challenges and implementing effective solutions is crucial in today’s construction environment, where costs and risks are higher than ever.
Weather Dependence
Since panels are cast on-site, adverse weather conditions can delay the construction process. Rain, extreme temperatures, or high humidity can affect the curing of the concrete, potentially leading to delays or quality issues. To mitigate these risks, careful scheduling and weather monitoring are essential. Implementing protective measures, such as temporary enclosures or heated curing tents, can help maintain construction timelines and ensure that the panels achieve the required strength. The cost of these protective measures has increased, but they are essential for avoiding costly delays and ensuring the quality of the finished product.
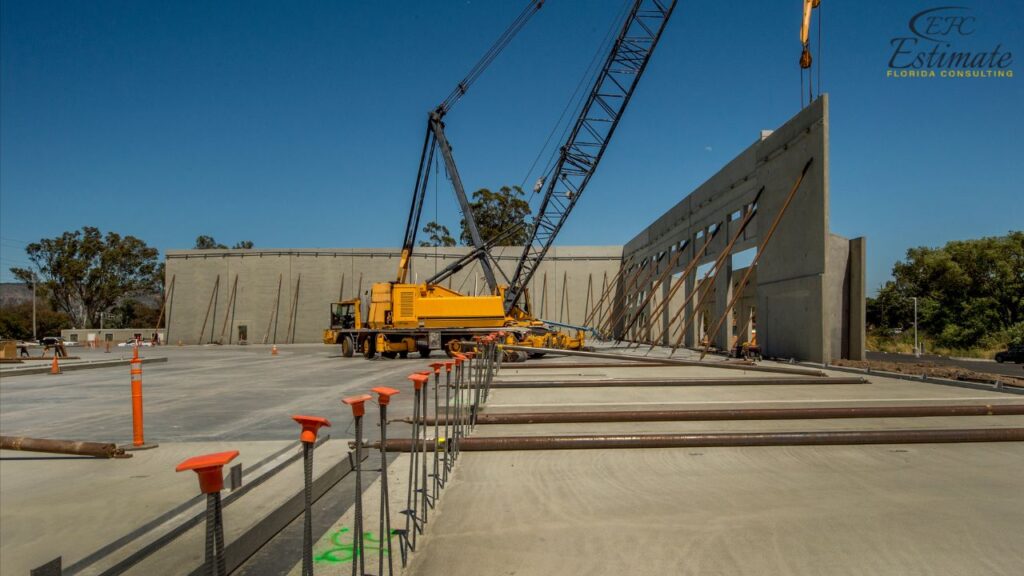
Site Constraints
Limited space on the construction site can make it challenging to cast and lift panels. In urban areas or tight job sites, there may not be enough room to lay out and tilt up large panels. In such cases, strategic site planning and the use of mobile cranes can help overcome these challenges. Additionally, modular construction techniques or phased panel casting may be employed to optimize the use of available space. The cost of specialized equipment and additional planning has increased, but these solutions are necessary for successfully executing projects in constrained environments.
Panel Cracking
Improper curing or handling of panels can lead to cracks, compromising the structural integrity of the building. To reduce the risk of cracking, it’s crucial to use proper curing methods, such as controlling the rate of moisture loss and maintaining consistent temperatures during the curing process. Ensuring that the construction team is experienced in handling and lifting heavy concrete panels is also vital to prevent damage during erection. The cost of high-quality curing agents and the demand for experienced labor have risen, but these investments are essential for ensuring the long-term durability of the building.
Coordination and Logistics
Tilt-up construction requires precise coordination among various trades, including concrete suppliers, crane operators, and general contractors. Poor coordination can lead to delays, increased costs, and potential safety hazards. Effective project management, clear communication, and detailed scheduling are essential to ensure that all aspects of the construction process are well-coordinated and executed efficiently. The rising cost of project management and logistics reflects the increased complexity of modern construction projects, where successful coordination is more important than ever.
Get 5 New Projects in the Next 7 Days With Our System
Selecting the Right Contractor for Tilt-Up Concrete Projects
Choosing the right contractor is crucial for the success of a tilt-up concrete project. When selecting a contractor, consider the following factors, especially in today’s market where costs and risks are higher:
- Experience and Expertise: Ensure the contractor has extensive experience with tilt-up construction and a proven track record of completed projects similar to yours. Experience is key to navigating the unique challenges of tilt-up construction, such as precise panel placement and integration of architectural features.
- Reputation and References: Check the contractor’s reputation by reviewing online reviews, asking for references, and visiting completed projects. Positive feedback from previous clients is a good indicator of the contractor’s reliability and quality of work. Speaking directly with past clients can provide valuable insights into the contractor’s ability to meet deadlines, stay within budget, and deliver high-quality results.
- Resources and Equipment: Verify that the contractor has access to the necessary equipment and skilled labor to complete the project efficiently. This includes cranes, lifting devices, and specialized tools required for tilt-up construction. Contractors with the right resources are more likely to complete the project on time and to the highest standards.
- Transparency and Communication: A reputable contractor will provide a detailed quote, clear contract terms, and open communication throughout the project. Transparency in pricing, scheduling, and scope of work helps prevent misunderstandings and ensures that both parties are aligned on the project’s goals. Regular updates and clear communication channels are essential for addressing any issues that arise during construction.
- Understanding of Local Conditions: In addition to technical expertise, the contractor should have a strong understanding of local building codes, weather conditions, and permitting processes. Local knowledge can streamline the project by ensuring compliance with regulations and minimizing delays caused by permit approvals or weather-related disruptions.
How Much Does Concrete Cost Per Yard?
The cost of concrete per yard has increased and typically ranges from $150 to $200. Several factors affect the price, such as your location, the type of concrete, and any additives like fiber or color. Standard concrete mix will be closer to $150 per yard, while specialty or high-strength mixes could push costs to $200 or more.
If you’re ordering less than 10 yards, expect additional delivery fees. For larger projects, you might find bulk discounts to help offset some of the higher prices.
Download Template For Tilt-Up Concrete Construction Project Breakdown
- Materials list updated to the zip code
- Fast delivery
- Data base of general contractors and sub-contractors
- Local estimators
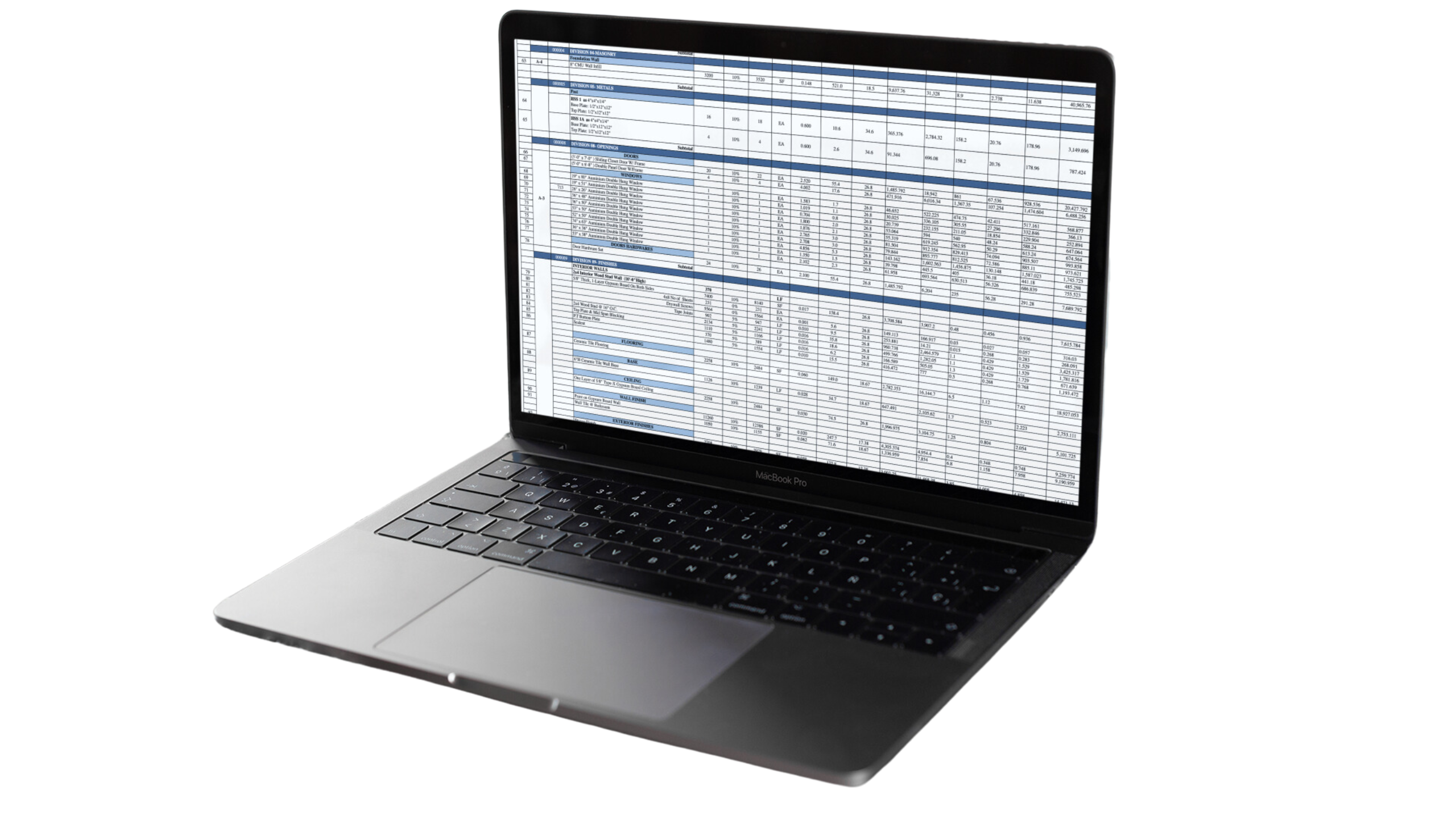
How Estimate Florida Consulting Can Assist with Your Tilt-Up Concrete Project
Estimate Florida Consulting offers a range of services to support your tilt-up concrete construction project, from providing accurate cost estimates to connecting you with reputable contractors. Their expert team understands the unique challenges of tilt-up construction and can offer valuable insights and recommendations to ensure the success of your project. By leveraging their experience and industry connections, Estimate Florida Consulting helps you navigate the complexities of tilt-up construction, from initial budgeting to final completion.
- Comprehensive Cost Estimation: Their cost estimation services take into account all relevant factors, including site conditions, design specifications, and market trends, providing you with a detailed and accurate estimate that reflects the true cost of your project.
- Contractor Selection: Estimate Florida Consulting can connect you with experienced contractors who specialize in tilt-up construction, ensuring that your project is completed to the highest standards. Their network of trusted professionals ensures that you have access to the resources and expertise needed to achieve your construction goals.
- Project Planning and Management: From initial planning to project execution, Estimate Florida Consulting provides ongoing support to help you manage your project efficiently. Their services include scheduling, budgeting, and coordination with contractors, ensuring that your project stays on track and within budget.
- Customized Solutions: Whether you’re building a warehouse, office building, or retail space, Estimate Florida Consulting tailors their services to meet your specific needs, ensuring that your tilt-up construction project aligns with your vision and financial goals.
Frequently Asked Question
Tilt-up concrete construction is a cost-effective and efficient method used for building large commercial structures such as warehouses, retail stores, and office buildings. In this process, concrete panels are cast horizontally on-site and then lifted into place to form the building’s walls. This technique offers several advantages, including reduced labor costs, faster construction times, and enhanced durability.
The cost of tilt-up concrete construction generally ranges from $156 to $234 per square foot. This price includes materials, labor, and equipment. However, the total cost can vary based on factors like the quality of materials, the complexity of the project, and the level of customization required. The wide range in costs allows for flexibility depending on the specific needs and goals of the project.
The cost of tilt-up concrete construction varies depending on the size of the building. Larger buildings often benefit from economies of scale, reducing the cost per square foot. Here’s a detailed breakdown:
- 10,000 sq ft: $156 – $234 per sq ft | Total Cost: $1,560,000 – $2,340,000
- 20,000 sq ft: $149.50 – $227.50 per sq ft | Total Cost: $2,990,000 – $4,550,000
- 50,000 sq ft: $143 – $221 per sq ft | Total Cost: $7,150,000 – $11,050,000
- 100,000 sq ft: $136.50 – $214.50 per sq ft | Total Cost: $13,650,000 – $21,450,000
- 200,000 sq ft: $130 – $208 per sq ft | Total Cost: $26,000,000 – $41,600,000
Several factors can significantly influence the cost of tilt-up concrete construction:
- Building Size and Complexity: Larger or more complex buildings will have higher costs due to increased materials, labor, and engineering requirements.
- Panel Thickness and Reinforcement: Thicker panels and greater reinforcement add to material costs but provide better structural integrity.
- Site Conditions: Challenging site conditions, such as poor soil or difficult topography, may require additional site preparation, increasing overall costs.
- Customization and Design Features: Custom finishes, intricate designs, and additional openings for windows and doors can significantly raise costs.
- Labor and Equipment Availability: Costs can vary depending on the availability and cost of skilled labor and necessary equipment in the project’s location.
Here’s a breakdown of costs by component:
- Concrete Materials: $65 – $110.50 per sq ft
- Labor Costs: $39 – $84.50 per sq ft
- Equipment Rental: $13 – $39 per sq ft
- Site Preparation and Foundation: $26 – $52 per sq ft
- Panel Finishes and Customization: $13 – $32.50 per sq ft
Tilt-up concrete construction offers several advantages for commercial buildings:
- Cost Efficiency: It is often more economical than traditional building methods due to reduced labor and material handling requirements.
- Speed of Construction: The process allows for rapid construction timelines, enabling faster project completion and quicker returns on investment.
- Durability and Strength: Tilt-up buildings are known for their resistance to natural disasters, making them ideal for regions prone to extreme weather.
- Energy Efficiency: The high thermal mass of concrete helps regulate indoor temperatures, leading to lower energy costs.
- Design Flexibility: Tilt-up construction offers a variety of aesthetic options, including different textures, colors, and finishes.
Comprehensive Trade-Specific Estimates
At Estimate Florida Consulting, we offer detailed cost estimates across all major trades, ensuring no part of your project is overlooked. From the foundation to the finishing touches, our trade-specific estimates provide you with a complete and accurate breakdown of costs for any type of construction project.
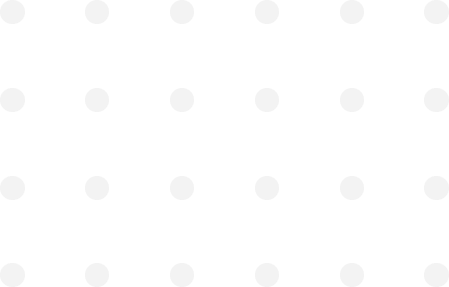
Testimonials
What Our Clients Say
We take pride in delivering accurate, timely, and reliable estimates that help contractors and builders win more projects. Our clients consistently praise our attention to detail, fast turnaround times, and the positive impact our estimates have on their businesses.
Estimate Florida Consulting has helped us win more bids with their fast and accurate estimates. We trust them for every project!
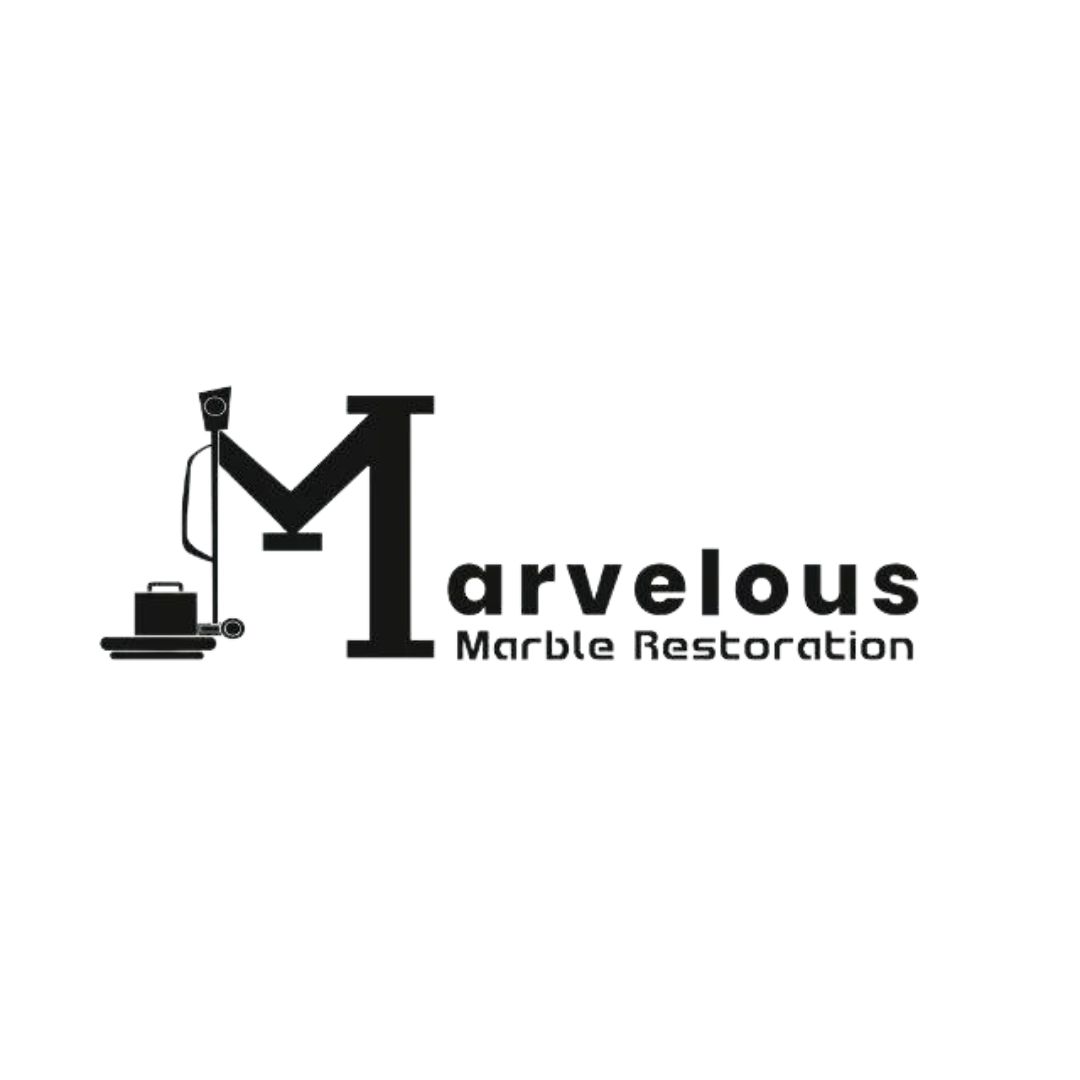
Steps to Follow
Our Simple Process to Get Your Estimate
01
Upload Plans
Submit your project plans, blueprints, or relevant documents through our online form or via email.
02
Receive Quotation
We’ll review your project details and send you a quote based on your scope and requirements.
03
Confirmation
Confirm the details and finalize any adjustments to ensure the estimate meets your project needs.
04
Get Estimate
Receive your detailed, trade-specific estimate within 1-2 business days, ready for your project execution.
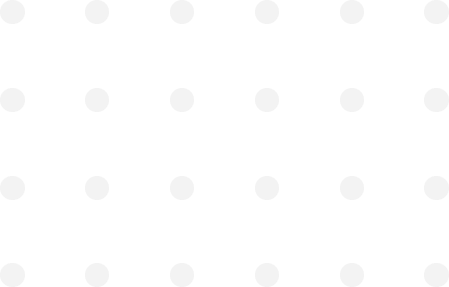