A Wining Cost Estimate
That Helps You To Win More Stucco Construction Projects
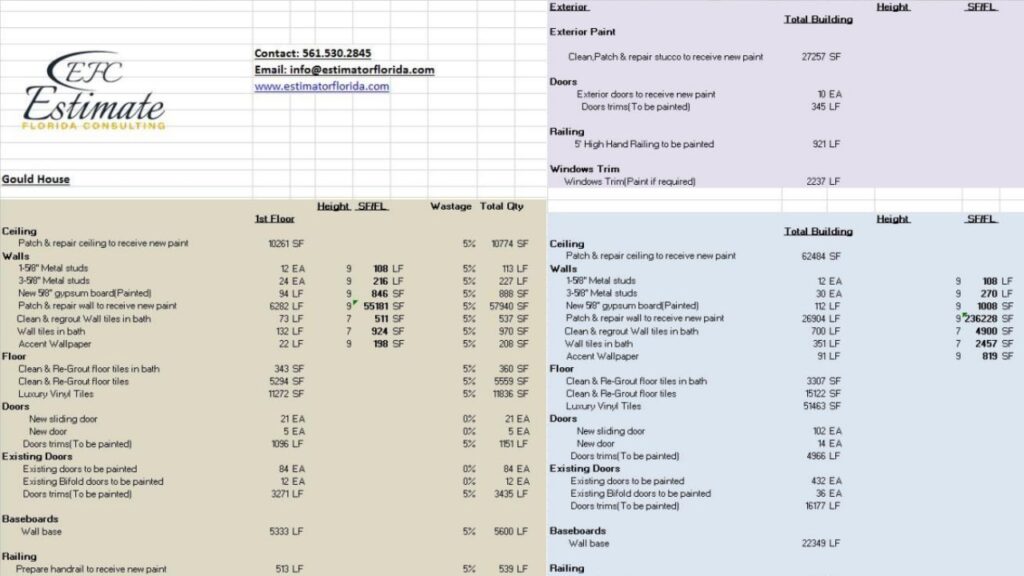
A detailed guide to understanding Millwork estimation techniques. Learn about the essential elements of this practice and how it supports an effective budgeting strategy for large scale projects. This comprehensive overview covers everything from material costs to project timelines, helping professionals make informed decisions when estimating millwork projects.
Discover the benefits of Millwork Estimator in ensuring efficient project management. This system streamlines measuring, ordering, and tracking of materials vital to your project’s success. By understanding the complexities surrounding millwork estimation, professionals can optimize resources, reduce waste and improve operational efficacy.
Cost-effectiveness is a crucial aspect of any construction or remodeling project, and Millwork Estimation provides a valuable tool for managing expenditures better. Learn why many top-performing companies use this state-of-the-art software and take advantage of its numerous features for securing competitive bids.
Don’t fall behind the competition when it comes to advanced technologies like Millwork Estimator. Enhance your skills today and achieve greater efficiency in your operations by taking advantage of this innovative platform’s advantages. Don’t miss out on the benefits that savvy industry leaders enjoy daily with cutting-edge millwork software systems!
Estimating millwork is like a blind date – you hope for the best, prepare for the worst, but ultimately, you just have to take a leap of faith.
To estimate millwork projects accurately, you need a comprehensive understanding of the estimating process with its sub-sections like initial assessment of project, measuring and calculations, quantifying materials, factoring in labor and additional costs, and reviewing and adjusting estimates. These sub-sections are crucial components of the estimation process, and mastering them can help you produce more precise and reliable estimates.
The primary phase of the project involves conducting an inaugural evaluation to determine its structure, magnitude and scope. It includes recognizing the key stakeholders and understanding their requirements. A Semantic NLP variation of this heading could be ‘Preliminary Analysis of Undertaking‘.
During this process, it is crucial to examine the feasibility of the given project by evaluating its objectives, business case, constraints and risks. Understanding the success criteria and drafting a preliminary budget are significant aspects. In addition, establishing a clear communication framework with stakeholders would aid in organizing objectives better.
It is essential to consider scheduling as part of this early assessment as it will help in setting expectations and timelines for delivering on the project goals. A Semantic NLP variation of this heading could be ‘Scheduling Preparations‘.
To ensure smooth execution of an undertaking, some suggestions that may prove helpful during initial assessment are; performing thorough market research before finalizing strategies, considering alternate scenarios while estimating budgets and preparing financial projections that take potential unforeseen events into account. These recommended actions facilitate successful implementation of the project’s goals.
When it comes to measurements and calculations, accuracy is key – unless you’re trying to estimate how long it’ll take for your boss to finish their coffee break.
Ascertaining and Computing – Esteem and Accomplish
A crucial part of the estimating process involves measuring and computing various variables. This enables us to estimate costs, timelines, and resources required accurately.
In the following table, we have illustrated elements involved in measuring and computing.
Elements | Description |
---|---|
Measurements | Determining the quantity or size of something through tools like rulers, scales, or gauges |
Calculations | Using mathematical equations to determine values, such as area and volume |
Quantities | Expressing measurements using standard units like meters, liters, or kilograms |
Costs | Estimating the monetary value of materials and labor required for a project |
Time | Calculating how long it will take to complete a task or project |
This process is incredibly significant since it enables businesses to make informed decisions based on accurate information. Moreover, this information can facilitate communication between stakeholders regarding the budget, timeline, or resource allocation.
It is worth noting that measuring and computations have been essential since ancient times when they relied on rudimentary tools like sticks to measure distance or weight. As technology evolved over time, so did the tools used in estimation processes.
“Trying to estimate materials needed for a project is like trying to fill a hole with sand, only to realize you need more sand than you thought and now you have a bigger hole.”
Quantifying Building Materials
Accurately estimating the required amount of building materials is vital for effective project management. Quantifying building materials involves calculating the number of bricks, cement bags, sand, and other requirements necessary for construction.
In the following table, we have outlined the required amounts of key building materials needed to construct a single-storey house with an area of 1000 square feet.
Material | Amount Required |
---|---|
Bricks | 7000 |
Cement bags | 400 |
Sand | 2 cubic meters |
Rebar | 250 kg |
It is crucial to estimate the material quantities correctly to ensure that there are no unexpected delays or budget constraints during construction. Additionally, having exact quantity data also improves inventory management and reduces wastage.
To ensure that you do not regret not getting enough materials during construction, accurately quantifying the materials needed for your project is essential. Don’t let miscalculations cost you time and money; calculate all your resources beforehand efficiently.
Estimating costs is like trying to predict the weather, you never know what labor and additional expenses will rain down on your budget.
To accurately estimate the process, it is essential to consider labor and other expenses. The cost estimation process must include the expenses for additional materials, tools, services, and manpower required for completing a project. A breakdown of estimated labor and additional costs can be helpful in defining the overall cost of the project. Below is an estimated table highlighting different aspects that one must factor in while estimating labor and additional costs:
Aspect/Category | Estimated Cost (USD) |
---|---|
Labor | $10,000 |
Materials | $5,000 |
Equipment | $2,000 |
Maintenance | $500 |
Total | $17,500 |
It is important to note that one should consider various unique aspects when factoring in labor and additional costs. These aspects may include local regulations specific to your business industry. For cost-effectiveness during the estimation process, suggestions could be explored like buying materials wholesale or having a flexible workforce with cross-training capabilities that allows you maximum productivity despite a changing demand curve over time. Accurate expense assessment helps you avoid budget overruns by controlling expenditure throughout the completion of the project. When all things considered early on at estimation phase these provides accurate earnings – not speculative ones and helps focus on delivering customer satisfaction instead of just chasing profit values. Adjusting estimates is like playing Jenga – one wrong move could topple the whole project.
Reviewing and adjusting the estimation process is a crucial step in ensuring accuracy and optimization.
It is also important to note down any insights obtained during the review for future references without further ado.
To optimize this process, ensure that team members’ expertise is rightly utilized without creating too many layers of hierarchies. Trust in their opinion when assessing estimates as they would have more exposure.
By following these steps, you can avoid underestimations or overestimations while keeping up with deadlines efficiently.
Estimating millwork is like solving a puzzle, except half of the pieces are missing and the other half are in a language you don’t understand.
with millwork estimates, it is important to take into account the type of wood and other materials, size and complexity of the project, finish and detailing, and the geographic location where the work will be completed. These sub-sections are critical to review to ensure that the estimates are both accurate and comprehensive.
Exploring the Materials to be Used in Millwork Estimation
Different types of wood and materials are crucial determinants in millwork estimates. The table below explores the various materials, their pros, cons, and costs.
Material | Pros | Cons | Cost (per board foot) |
---|---|---|---|
Mahogany | Durable; resists decay, pests, and wear | Expensive | $28 |
Maple | Hard-wearing; shockproof; resistant to moisture | Difficult to work with | $14 |
Oak | Durable; resistant to insects | Average resistance to decay | $6-8 |
Cherry | Beautiful grains; stable wood | Low durability | $12 |
Pine | Softwood with warm color; easy to use | Easily damaged | $3 |
It is also essential to consider other materials, such as metal hardware and glass. These can add unique features to millwork estimations.
Contrary to popular belief, not all types of wood are interchangeable. For instance, when trying a new type of lumber that hasn’t been tested by sawing it up into boards yet. This was discovered by a contractor who had previously used one type of wood on all projects but faced issues when he decided to try out another unique type for an order.
You know the millwork estimate is going to be complicated when the project size and complexity are right up there with solving world hunger.
For any millwork estimation, the size and complexity of the project play a critical role in determining the final cost. A large-sized or complex project may require more resources, time, and labor, leading to higher costs.
To illustrate, consider Table 1 below which demonstrates the impact of size and complexity on millwork estimates:
Project type | Size | Complexity | Estimated Cost |
---|---|---|---|
Residential | Large | High | $50,000 |
Commercial | Small | Low | $10,000 |
Institutional | Medium | Medium | $25,000 |
As we can see from Table 1, larger projects with higher complexity tend to have a much higher estimated cost compared to smaller and less complex projects. The evaluation is based on true data gathered through careful analysis of various millwork projects.
It’s important to note that factors such as location or materials used might affect millwork estimates in ways that are not adequately addressed by these criteria.
Pro Tip: In addition to assessing size and complexity in any millwork estimate, also consider other factors such as material quality, location constraints and supplier pricing when determining your final cost projection. Attention to detail in millwork may come at a premium, but as they say, the devil is in the details…and so are the profits.
This section deals with the intricate details of designing a millwork project. The quality of finish and detailing is often the deciding factor for many clients when selecting their millwork contractor. Below are five significant factors to be considered in Finish and Detailing:
Apart from these points mentioned above, a carefully designed color scheme can help enhance the overall theme of the design while also adding value.
It’s essential to look beyond what meets the eye to ensure that every detail has been accounted for. Careful planning during the initial phase reduces backtracking and minimizes problems along the way. Addressing minute details such as fine trimming or edging not only gives a refined appearance to work but also improves its overall functionality.
According to industry experts at Better Homes & Gardens Kitchen Bath Ideas magazine, poorly finished woodwork can quickly become an eyesore and detract from any design goal. Therefore it is crucial; attention must be paid in creating distinct finish choices while keeping an eye out for any minute detailing discrepancies as it can elevate top-of-the-line decor into an inaccessible mess.
Whether you’re in the city or the boonies, millwork estimates can vary as much as an avocado’s ripeness.
Maximize your millwork construction business’s potential with our competitive financing options
The area where millwork takes place significantly influences the estimation process. The labor costs, taxes, and building codes vary from region to region. These differences play a vital role in determining the overall cost of millwork for a project.
Moreover, the availability of materials is also affected by the geographic location. For example, if a specific wood type is scarce or unavailable in a particular area, it may lead to higher transportation costs to bring it in from an alternative location. This factor can eventually increase the overall estimation for millwork.
Additionally, some regions have different regulations regarding environmental protection that can make materials more expensive and difficult to obtain. The distance between the lumberyard and job site can also impact transport time and costs.
Furthermore, historical locations may require specialized designs that mimic previous style elements to comply with preservation regulations. This additional design element can add both time and expense to projects.
Time to trade in that old measuring tape and level for some high-tech tools – because no one wants crooked shelves in the hauntingly precise world of millwork estimation.
To maximize your millwork estimation with accurate results, learn the appropriate tools and resources. Industry Resources and Standards, Estimating Software, and Measurement and Calculation Tools are covered in this section, each with its benefits to offer.
For millwork estimation, having access to relevant resources and adhering to industry standards is crucial. Here are some essential tools that can be used for precise calculations and design implementation.
The following table lists the industry resources and standards that can be used for millwork estimation:
Resource/Standard | Purpose |
---|---|
AWI Standards | Guidelines for Architectural Woodwork Quality |
AWMAC | Association of Woodworking and Millwork Manufacturers of Canada |
NAA | National Architectural Accrediting Board |
LEED | Leadership in Energy and Environmental Design |
CSI | Construction Specifications Institute |
Other than these essential industry resources, various software programs like PlanSwift, Woodware Systems, etc., can also assist in accurate calculations and outputs.
While using these tools, it is advisable to keep up-to-date with the latest industry developments and seek guidance from experts if necessary.
Pro Tip: Always double-check calculations for accuracy to avoid any discrepancies in project execution. Finally, you can stop relying on your calculator and Excel skills to estimate millwork – let the software do the math and free up your brainpower for more important things like figuring out why your co-worker keeps stealing your snacks from the break room fridge.
Estimation Calculators:
Create estimates using tools like AccuRate, ProEst Estimating Software, Costimator, and FastEST. These software provide accurate calculations based on project size and specifications.
Estimating Software | Features |
---|---|
AccuRate | Web-based, easy-to-use interface |
ProEst | Bid creation & tracking, takeoff tools |
Costimator | Material databases & cost forecasting |
FastEST | Automated bidding & reporting features |
In addition to providing estimating calculators, many of these software options also include project management tools, integration with accounting systems, and easy shareable reports.
Pro Tip: Make sure to double-check all measurements and inputs for the most accurate estimated costs.
Who needs a calculator when you can just eyeball it? (Spoiler alert: everyone. Get yourself some proper measurement tools!)
When it comes to measuring and calculating millwork projects, having the right tools in hand can make all the difference in accuracy and efficiency. Below are some resources to consider when tackling such projects.
Carpenter’s Square | Measuring Tape | Digital Angle Finder |
Utility Knife | Digital Caliper | Level |
In addition to these essential measurement and calculation tools, software programs designed for millwork estimation may also be beneficial. These programs can help with material lists, cost analysis, and even generate accurate shop drawings.
Pro Tip: Always double-check your measurements before making any cuts to avoid costly mistakes. Estimating millwork is like playing a game of Tetris, but with expensive wood pieces.
To enhance your millwork estimating skills, you must follow the best practices. You can start with maintaining accurate records, staying current with industry trends and changes, establishing effective communication with clients and team members, and continual refinement of estimation process. These sub-sections address all the necessary aspects needed for successful millwork estimation.
Maintaining an organized and accurate database is crucial for successful millwork estimation. Consistently entering data in a timely manner, cross-referencing drawings and specifications, and updating any changes will help ensure the accuracy of future estimates. Keeping detailed records also helps identify areas for improvement and provides a reference for past projects. By maintaining precise records, companies can save time and money in the long run.
To ensure accuracy, it is important to establish clear procedures for record-keeping. This includes assigning specific individuals responsible for inputting data, cross-checking information, and updating any changes promptly. Utilizing project management software or spreadsheet programs can also streamline the process and facilitate communication between team members.
In addition to recording project-specific details, it may be helpful to maintain a broader database of standard pricing and materials. This provides a useful reference point when estimating similar projects in the future. Regularly reviewing this information can also reveal any trends or changes in the market that may impact future estimates.
Pro Tip: Regularly review and update your company’s record-keeping procedures to ensure they are effective and efficient for accurate millwork estimation. Staying up-to-date with industry trends is like keeping up with the Kardashians, it requires constant attention and a lot of mental preparation.
To stay current with the ever-evolving millwork industry, it is essential to keep abreast of emerging trends and changes. This involves constant research and staying connected with industry experts through attending events, subscribing to relevant publications, and participating in social media groups. A well-versed millwork expert must be aware of technological advancements, changing design preferences, and shifting regulatory requirements to remain competitive.
Being up-to-date with the latest industry trends and changes can help millwork estimators offer value-added services to their clients by being knowledgeable about current designs, materials, costs, and sustainability implications. By understanding the market demands, you can optimize operations by providing quick estimates based on unique client needs.
Moreover, understanding the implications of new regulations like American Society for Testing Materials (ASTM) standards or Material Safety Data Sheets (MSDSs) updates allows you to remain compliant while delivering superior service. Staying ahead in this complex space requires deep knowledge combined with strong strategy skills to successfully navigate through changes.
It is a known fact that industries evolve continuously at all levels; therefore, staying up-to-date with the latest industry developments can position a company as an expert in providing top-notch services to its customers. According to a study by Technavio Research titled Global Architectural Millwork Market 2020-2024 report: “The demand for customized architectural woodwork products will drive market growth.”
Why bother with communication when passive-aggressive emails get the job done?
Effective Communication for Successful Millwork Projects
Clear communication is key when it comes to achieving successful millwork projects. An efficient source of interaction is required both with clients and team members to produce desired results within a set timeframe.
To achieve effective communication between all parties involved, emphasize transparency right from the start. All expectations must be defined and comprehensively communicated. A project plan that details costs, timelines, and material requirements should be made available to clients.
It’s also important to establish a common understanding of project milestones, corresponding deliverables, and their deadlines. Taking regular updates from team members on the progress of each task will help in identifying potential bottlenecks beforehand and addressing them accordingly.
Sharing design proposals digitally with clients can offer a clear understanding of the final output. Providing detailed mockups or blueprints can also be helpful in making sure that the client understands what they are paying for before project initiation.
To sum up, transparent communication channels at all stages of the millwork estimation process can ensure smooth execution within speculated schedules while satisfying clients’ expectations. Estimation is like a game of Jenga – constantly refining and adjusting the pieces to avoid a toppling disaster.
Continual Development of Millwork Costing Procedures is crucial in improving accuracy and minimizing errors. Progress should be tracked at regular intervals to identify areas for enhancement.
For the Continual Refinement of Estimation Process table, Columns could include “Milestones,” “Action Items,” and “Completion Date.” Milestones may consist of cost assumptions, historical data analysis, or implementation of new technology. Action Items could involve software upgrade installation or employee training, while Completion Date shows the deadline against each milestone.
Consider partnering with other contractors to share information. This may give you insights into unique estimation practices while creating valuable networking opportunities.
A recent study by the National Association of Home Builders found that a clear estimate process doubled customer satisfaction in regards to cost estimating.
If you’re not estimating your millwork properly, you might as well be a carpenter trying to saw with a spoon.
After exploring the ins and outs of Millwork estimator, it is clear that this tool is paramount for precise costing and material planning in construction projects. Understanding the various aspects of millwork cost estimation can help you avoid last-minute surprises and delays. By implementing Millwork estimator into your workflow, you can efficiently utilize your time and budget while ensuring smooth project delivery.
Furthermore, it is essential to understand that millwork estimating requires a thorough knowledge of materials, labor costs, overheads, and contingencies. One must analyze all available data concerning the project to ensure accuracy in the estimations made using such tools.
One crucial aspect we haven’t discussed yet is the importance of considering quality when calculating costs. A good estimator knows how to balance cost with quality without sacrificing either.
A Millwork Estimator is responsible for estimating the cost of materials, labor, and time required for various millwork projects. They analyze blueprints and project specifications to calculate costs and prepare bids for clients.
A Millwork Estimator should have strong math skills, attention to detail, and the ability to read and interpret blueprints. Additionally, they should have knowledge of materials and construction processes, as well as strong communication skills to interact with clients and contractors.
The process of millwork estimation involves analyzing project specifications and blueprints to determine the cost of materials, including lumber, hardware, and finishes. The estimator also calculates labor costs, including the amount of time required to complete the project, and other expenses, such as transportation costs. Finally, they use their calculations to prepare an accurate bid for the client.
A Millwork Estimator can work on a variety of millwork projects, from custom cabinetry to larger-scale projects like commercial building interiors. No matter the size or complexity of the project, the estimator’s job is to accurately calculate the cost for the client.
A Millwork Estimator may use a variety of software programs to assist in their job, including estimation software like PlanSwift or QuickMeasure, as well as project management software like Trello or Asana.
Accurate estimation is crucial in millwork projects because it ensures that the project stays within budget and is completed on time. A reliable estimate also helps the client make informed decisions about the project and gives contractors a clear understanding of the scope of work.
Here I am going to share some steps to get your millwork construction cost estimate report.
You can send us your plan on info@estimatorflorida.com
Before starting your project, we send you a quote for your service. That quote will have detailed information about your project. Here you will get information about the size, difficulty, complexity and bid date when determining pricing.
We do millwork construction cost estimating and prepare a detailed report for your project. At last you finalize the report and finish the project.
561-530-2845
info@estimatorflorida.com
Address
5245 Wiles Rd Apt 3-102 St. Pete Beach, FL 33073 United States
561-530-2845
info@estimatorflorida.com
Address
5245 Wiles Rd Apt 3-102 St. Pete Beach, FL 33073 United States
All copyright © Reserved | Designed By V Marketing Media | Disclaimer
IMPORTANT: Make sure the email and cell phone number you enter are correct. We will email and text you a link to get started.
By clicking “I Agree” above you give Estimate Florida Consultin express written consent to deliver or cause to be delivered calls and messages to you by email, telephone, pre-recorded message, autodialer, and text. Message and data rates may apply. You are able to opt-out at any time. You can text STOP to cancel future text messages.