A Wining Cost Estimate
That Helps You To Win More Drywall Construction Projects
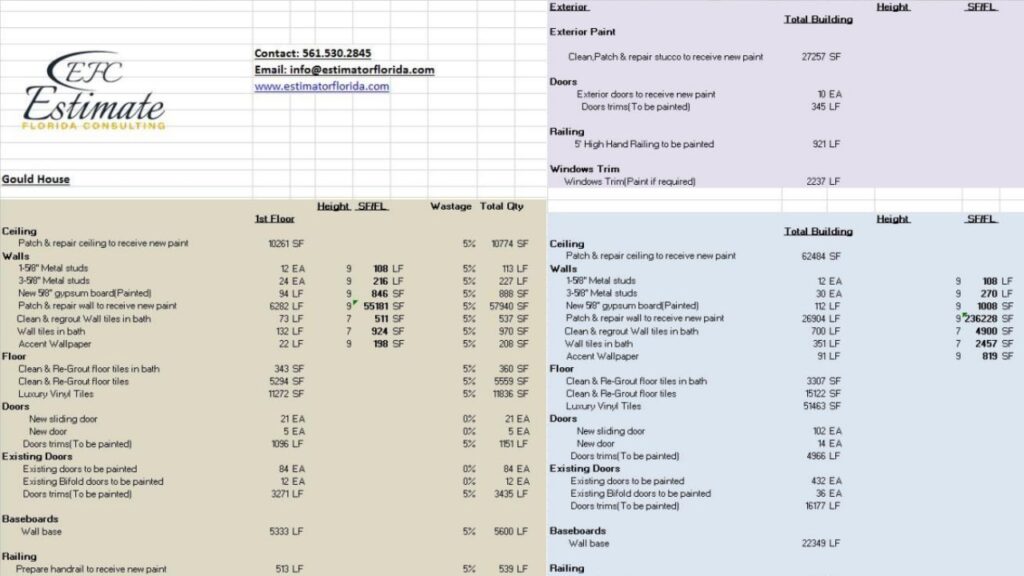
To understand the basics of drywall estimation with the help of The Complete Guide to Drywall estimator, you need to know what it is and why it’s important in construction projects. Along with that, key factors to be considered and common drywall estimation formulas and equations are also crucial in accurate estimation of materials and cost.
Drywall estimation is the process of calculating the amount of materials required to construct or repair a drywall structure. It involves assessing the space that requires drywall installation, calculating the quantity of materials required, and estimating the total cost for acquiring them.
Aside from taking measurements, several factors such as design complexity, drywall thickness and type, labor costs may impact your budget. Analysis of these factors helps ensure that you obtain precisely what’s required while also spotting any prospective issues in advance.
It is advisable to gather information from experts and vendors regarding current pricing trends and material availability at different locations. This way, you can adjust prices accordingly to improve your bidding strategies for new jobs without overpricing or losing profit margins.
Pro Tip: It’s essential to consider unexpected expenses such as underdeveloped textured ceiling surfaces and any extra work arising while on-site. You may increase costs while keeping them practical by including a contingency fee in your budget.
Without drywall estimation, you’re just blindly throwing up walls and hoping for the best – don’t be that guy.
Drywall estimation plays a crucial role in the successful completion of construction projects. The process involves calculating the required amount of drywall materials and labor costs, ensuring the project stays within budget and is completed on time. Accurately estimating drywall is essential for preventing unexpected expenses, delays, or mistakes during construction.
Drywall estimation ensures that accurate cost calculations are made for every step involved in the installation process, from measuring and cutting to hanging it in place and finishing it off with joint compound. One wrong estimate can result in significant financial losses to contractors or project owners. Hence, correct analysis and planning are imperative when estimating drywall quantities.
It is not just about getting an accurate quote; it also helps construction professionals mitigate risks such as material shortage or wastage-related issues that might arise during the project’s execution. With accurate drywall estimation techniques, one can prevent unnecessary wastage by ordering appropriate material amounts while mitigating all kinds of risk factors.
Pro Tip: When estimating drywall, taking note of the smallest details can yield great results in terms of accuracy. Accurate measurements should be taken and double-checked before determining how much material is required for a specific job.
Drywall estimation can be summed up in just two words: measure twice, cry once.
In drywall estimation, there are several essential factors that need to be considered. These elements can significantly affect the cost and time required to complete a project. Here are some crucial points to keep in mind for accurate drywall estimation:
It’s also essential to factor in other expenses such as tools, taxes, insurance fees, permit fees that accrue during project execution.
Pro Tip – Make sure you calculate all aspects of a project accurately before providing an estimate as this helps in avoiding discrepancies further down the line. Get your calculator ready, because we’re about to do some math that even your high school math teacher would find impressive.
When it comes to estimating drywall requirements, there are several essential formulas and equations that professionals utilize to make informed decisions quickly. These estimates help individuals determine the number of materials required and the amount of money they’ll need for a project.
The following table showcases some of the most commonly used drywall estimation formulas and equations, along with their corresponding variables and descriptions:
Formula/Equation | Variables | Description |
---|---|---|
Area Calculation | A = LW or A = LH | Calculates the surface area of a wall or ceiling by multiplying its length (L) by its width (W) or height (H). |
Volume Calculation | V = AL | Calculates the volume of drywall needed by multiplying the area (A) by the desired thickness level (L). |
Waste Factor Calculation | W = AG x 0.1 | Determines how much extra material will be required due to cutting errors and other waste factors by multiplying the gross surface area (AG) by 10%. |
Drywall Sheet Calculation | S = V/SF or S = A/SF x T/DST x WSR | Estimates the number of drywall sheets required based on total square footage (SF), desired thickness level per sheet (T/DST), and waste factor (%) while considering weight support requirements of framing members either 16-inches or 24 inches apart. |
It’s important to note that each project will include unique requirements, such as ceiling heights, curved walls, windows & doors which can affect these estimations. Therefore, it is always advisable to consult with an expert before planning your project.
While working on a particularly large commercial project, one estimator misjudged their calculations, resulting in a shortage of materials during construction. The mistake was costly not only regarding finances but also delayed progress significantly. It highlights how crucial accurate estimations are in any construction project.
Get your measuring tape ready, because estimating drywall is more precise than a surgeon’s scalpel.
Maximize your drywall construction business’s potential with our competitive financing options
To prepare for an accurate drywall estimation with this section on ‘Preparing for Drywall Estimation – The Complete Guide to Drywall estimator’, you need to gather project information, prepare cost estimation sheets and templates, evaluate materials and labor costs and identify possible cost savings measures.
To attain an accurate estimate for drywall installation, it is essential to gather comprehensive project information. Understanding the nature of the project, wall dimensions, ceiling height, and other details can help the estimator determine the appropriate materials required and costs. Moreover, they can also analyze factors like complexity, accessibility and time duration to assess labor costs accurately.
Additionally, gathering these project details can enable estimators to make informed decisions about how many people will be needed on-site each day and what tools are necessary to complete the job. Knowing any pre-existing electrical or plumbing installations could help prevent surprise delays in progress.
Pro Tip: Always double-check with clients before commencing a project to ensure all project details have been obtained.
Get ready to crunch some numbers and make your calculator cry with these cost estimation sheets and templates.
To prepare for estimating drywall costs, it’s important to create comprehensive sheets and templates. These can be used to track various expenses and ensure accurate cost calculations.
In the following table, we have illustrated how to prepare cost estimation sheets and templates for drywall:
Category | Estimated Cost | Actual Cost |
---|---|---|
Drywall | $X | $X |
Tape | $X | $X |
Joint compound | $X | $X |
It is also essential to include additional factors in the estimation sheets such as labor costs, material quantity, overheads, taxes and profit margin. Uniformity makes it easy for anyone reading the sheet to understand the entire process.
When planning for estimating drywall costs, ensure that all previous estimations on projects are analyzed because getting as much detail as possible will improve your future estimates. Use project management tools like Trello or Basecamp to track worker progressions and implementations in real-time.
Finally, keep in mind that accurate data is necessary for any reliable estimations. To achieve this, talk with suppliers and other professionals who are familiar with drywall material attributes so you can obtain precise figures.
Follow these steps when preparing cost estimation sheets and templates for drywall to ensure success during your analyses. Improved accuracy means better decision-making abilities!
Forget the crystal ball, when it comes to estimating drywall costs, a calculator and a sprinkle of gut feeling should do the trick.
The cost evaluation of materials and labor is a critical step in preparing for drywall estimation. It requires a detailed analysis of the right materials to be used and the labor required to put them together seamlessly.
A table below outlines a comprehensive overview of evaluating material and labor costs that could be useful in creating estimates.
Cost Item | Description | Unit | Quantity | Rate | Total Cost |
---|---|---|---|---|---|
Drywall Board | Material cost | Per board | 200 | $15.00 | $3,000 |
Joint Compound | Material cost | Per bag | 50 | $20.00 | $1,000 |
Sandpaper | Material cost | Per sheet | 150 | $0.25 | $37.50 |
Labor | *Estimated based on individual rates | ||||
Board Hanging & Taping | -Prices can range from $0.75-$2 per sq ft depending on skill level | Per sq ft | 5000 sq ft | Avg rate of $1/sq foot | – |
When dealing with cost evaluations, it’s essential to keep in mind the quality of materials and experience of laborers can affect the overall calculation tremendously.
An important aspect to remember when evaluating material and labor costs is reputation; reputable companies typically charge more due to higher quality materials and experienced laborers.
Saving money on your drywall project? Don’t be a wallflower, let’s dive into some cost-cutting measures.
Possible Strategies for Cost Reduction during Drywall Estimation
It is essential to identify potential areas of cost savings when estimating drywall projects, and there are several strategies you can employ.
Moreover, estimate preparation should also incorporate contingency plans for unexpected expenses adequately. By identifying these potential cost savings measures early on, you can minimize costs throughout the entire drywall project lifecycle.
Pro Tip – Consider leveraging technology-based solutions such as BIM (Building Information Modelling) or 3D modelling software that allows detailed visualization of a building structure before construction, making planning more manageable.
Get ready to crunch some numbers, because drywall estimation is where math meets masochism.
To perform drywall estimation with accuracy, you need to calculate framing and sheathing requirements, determine drywall panel requirements, estimate joint compound, fasteners, and other materials, as well as estimate the labor costs and timeframe. These sub-sections will provide you with comprehensive insights to perform all the necessary estimations for any drywall project.
When it comes to estimating drywall, calculating framing and sheathing requirements is a crucial task. It involves determining the amount of materials needed for wall framing and sheathing, which will ultimately impact the overall cost of the project.
To better understand this process, refer to the following table:
Material | Dimension | Quantity Needed |
---|---|---|
Framing lumber | 2x4x8ft or 2x6x8ft | Based on wall height and layout |
Exterior sheathing | 4ft x 8ft x 1/2in sheets of OSB or plywood | Based on square footage of walls |
Interior gypsum board (drywall) | 4ft x 8ft x 1/2in sheets | Based on square footage of walls |
Note that while these are general guidelines, specific projects may require additional materials or unique dimensions.
It’s important to keep in mind that both overestimating and underestimating can have negative consequences. Overestimating can lead to wasted materials and increased costs, while underestimating can result in delays, additional trips to the store, and ultimately higher expenses.
To avoid these issues, always double-check measurements before ordering materials and consider consulting with a professional estimator for larger projects. By taking the time to accurately calculate framing and sheathing requirements, you’ll be well on your way to a successful drywall installation.
Brace yourselves, we’re gonna need to start counting those drywall panels like we’re counting our blessings – carefully and with lots of patience.
To determine the number of drywall panels required for a project, you need to understand the area that needs coverage.
Here’s a 4-Step guide on how to Determine Drywall Panel Requirements:
It’s important to remember that many factors could affect your final estimate, such as cutting around fixtures or taking into account possible waste.
For best results, consider using online drywall calculators or consulting with an experienced contractor. By considering all aspects beforehand, you can come up with an effective estimation.
One suggestion would be to add an extra ten percent of materials on hand when placing an order. This will give you leeway in case any unexpected costs or mistakes occur. To avoid generating excess waste during installation, plan accordingly with measurements before cutting your sheets.
It’s a good thing joint compound doesn’t have feelings, because we put it through a lot of abuse during the drywall process.
When estimating the required joint compound, fasteners, and other materials for drywall installation, one needs to consider the size of the area to be covered and the number of layers required for a smooth finish. Here are some estimates for the necessary materials as per industry standards:
Materials | Units | Quantity Required |
Joint Compound | Pails | 1 pail every 450 sq. ft. |
Screws or Nails | Pounds/boxes | 5 lbs. or 1 box every 500 sq. ft. |
It’s worth noting that additional materials may be needed, such as corner bead and tape for joint treatment, self-adhesive mesh tape to reinforce joints in high-stress areas, and insulation for soundproofing purposes. It’s important to factor in these estimates while planning your drywall project to avoid any delays or shortages mid-way through installation. According to HomeAdvisor’s Drywall Installation Cost Guide, on average, it can cost between $1.50 – $3 per square foot for materials alone in North America. Remember that proper estimation is key when undertaking a new construction project! Estimating labor costs and timeframe is like playing a game of ‘guess how long this will take’ with a brick wall.
Estimating the total hours and costs needed for the drywall project is a crucial task, requiring a comprehensive understanding of various factors that impact the outcome. To achieve reliable results, it is essential to consider labor costs and timeframe requirements.
Four key steps towards determining an accurate estimate are as follows:
It’s worth noting that weekend installer rates could be higher than weekdays charges. Depending on their specialization and qualifications, renowned contractors may charge higher per hour wages.
Pro Tip: It would be ideal to provide extra walls space measurements calculated according to industry standards. Having clear dimensions would allow contractors to eliminate guesswork during estimation.
Estimating drywall is like trying to solve a puzzle where the pieces keep changing size and shape, but with advanced techniques, you can finally put the pieces together.
To master advanced drywall estimation techniques with the help of digital tools and software, building information modeling (BIM), and parametric estimation, you need to understand the different benefits each technique has to offer. The following sub-sections will delve deeper into how to utilize them in order to optimize and improve your drywall estimation skills.
As the construction industry evolves, advanced methods for estimating drywall requirements emerge. One of these is the use of digital tools and software to streamline estimation processes and increase accuracy. Here is an example table showcasing some of these digital tools and their features:
Tool | Features |
---|---|
PlanSwift | Calculates material quantities, provides a digitized takeoff, integrates with other software |
STACK | Offers pre-built templates, allows for customizations, calculates labor costs |
On Center Software | Provides automated takeoffs, allows for real-time collaboration, generates reports |
These tools not only save time but also improve overall estimation accuracy. Another advantage is that they allow for multiple team members to work on the project simultaneously. It’s important to note that there are also cloud-based options available, which enable remote access and collaboration from anywhere with an internet connection. Don’t let outdated estimation methods hold your business back. Utilizing these modern tools can result in significant cost savings and more efficient project completion. Upgrade your techniques today and see the benefits firsthand. Don’t miss out on this opportunity to stay ahead of the competition. Who says estimating drywall can’t be exciting? With BIM incorporated in the mix, it’s like playing a game of Tetris with building blocks.
Incorporating Building Information Modeling (BIM) in Drywall Estimation enables contractors to visualize the project and make sensitive decisions. The 3D models assist in material quantity takeoffs and estimating costs.
Benefits of BIM in Estimation | Real-life Examples of BIM |
---|---|
Accuracy of Material Takeoffs | BIM Used in The Construction of Burj Khalifa, UAE |
Cross-checking with Drawings and Schedules | Austrian National Library Renovation, Austria |
Detecting clashes during construction. | Houston Astrodome Remodel, USA |
The utilization of BIM boosts project efficiency by creating a clear communication pathway between the design team, builders, estimators and clients.
A holistic approach to drywall projects is necessary to maintain professionalism and productivity. Incorporating value engineering analysis while utilizing BIM technology enhances project reliability and overall performance.
For instance, professionals who used these techniques provided estimates for a $10 million hotel renovation project between 6 -12 days; however, with advanced planning using BIM software tools alongside value-engineering techniques, an estimate was delivered within 48 hours.
Why estimate drywall with outdated techniques when you can implement parametric estimation and save yourself a headache (and a sore thumb from all that counting)?
Starting with an advanced technique, you may consider utilizing a parametric estimation method to estimate drywall expenses. This method involves calculating material and labor costs based on specific parameters that affect the project’s scope.
To showcase this technique effectively, we have created a comprehensive table that breaks down the essential details of implementing parametric estimation.
Parameter | Description | Example Value |
---|---|---|
Square Footage | Total square footage of wall space | 1000 sq ft |
Wall Height | Height of walls in feet | 10ft |
Type of Drywall | Different types of drywall available | Standard Gypsum Board |
Finish Level | Varying degrees of finishing quality | Level 3 Finish |
Location | Geographical location affecting price per unit | New York City |
By filling in these parameters appropriately, it is possible to estimate the cost accurately. Nevertheless, it is essential to note that each parameter involves numerous complex interrelated factors. Hence while applying this technique, one should take care to limit themselves from oversimplifying or overcomplicating the formula used for parametric estimation.
A word of advice for effective implementation – Always review and update your estimations periodically (especially when working with larger projects) by examining past projects and adjusting formulas accordingly to get the most accurate predictions based on historical data.
Pro Tip: A thorough understanding of industry standards and prices is crucial while determining parametric values. Hence it helps broaden your knowledge base by keeping yourself updated about current pricing trends and industry standards.
Estimating drywall quantities is a science, but using a Ouija board to call on the spirits of past contractors is not considered a best practice.
To master the art of drywall estimation with accurate results and satisfied clients, learn the Best Practices in Drywall Estimation. Being accurate and consistent in estimation, updating estimates as project progresses, communicating effectively with clients and team members, learning from previous projects and improving estimation methods are topics we’ll cover in this section.
Achieving Precision and Consistency in Drywall Estimation
Drywall estimation requires accuracy and consistency to ensure that the project is within budget and avoid any financial losses. To achieve this, one must first assess the scope of work, including the type of drywall material, the dimension of surfaces, and special requirements. This information will guide the estimator in calculating costs accurately.
To maintain consistency, a standardized approach must be adopted for each project. For instance, preparing an estimate checklist can help create uniformity in factors such as measurements, scrap allowance, hourly rate for labor, taxes and permits. Estimators may use software programs to automate measurements,cost estimates while being consistent with rates used in previous projects.
It is also essential to get regular updates on market prices for materials such as screws or joint compounds. Regular communication channels with suppliers can ensure estimators are updated on any price changes affecting specific products; this makes it possible to suggest alternative materials if prices become prohibitively high.
In addition to improving accuracy and consistency, creativity can be applied by getting multiple bids from different suppliers to compare prices and confirm that costs are accurately captured. While developing an estimate may not entirely eliminate errors or unforeseen circumstances that require reevaluation of costs or change orders; having proper monitoring of costs during construction before final payment diminishes likelihoods of disputes between contractor-owners or subcontractors – so always stay vigilant.
You might as well estimate your sanity while you’re at it, because updating drywall estimates as the project progresses is just as mind-numbing.
Updating Estimates as the Project Progresses:
The key to effective drywall estimation lies in regular updating of project estimates as work progresses. This holds especially true for drywall projects that are prone to complexity due to multiple factors such as location, design and materials.
Here are some key points on how to update estimates as a project progresses:
To ensure optimal success rates, contractors must take all necessary steps towards informing their clients about how frequently they plan on revising their project estimates. By doing this effectively, they can establish credibility with their clients while ensuring customer satisfaction throughout the duration of the project.
One noteworthy factor in estimating drywall jobs is having realistic expectations when it comes to deadlines. Perhaps even more pertinent though is maintaining an accurate record of work which can be used later for reference purposes thereby establishing better working practices amongst construction workers.
A contractor once reported a case where he had decided not to update his client’s estimated costs during a significant renovation project due to recurrent material supply delays from suppliers. While this saved him time, it created problems later when he was forced to rush through the remainder of the project leaving behind dissatisfied customers.
Remember: Clear communication is key…unless you’re a magician, in which case misdirection works just as well.
Effective Communication with Clients and Colleagues
Clear communication is an essential aspect of conducting successful drywall estimation projects. A project manager must communicate effectively with both the clients and team members to ensure that everyone is on the same page. Open communication helps in minimizing misunderstandings and avoiding costly errors.
To communicate effectively, one must listen actively, ask relevant questions, and be respectful. A clear understanding of client requirements is necessary for providing accurate estimates. Creating a detailed scope of work document can help bridge any confusion gap between the two parties.
Using modern communication tools such as video conferencing or messaging apps can also improve communication flow. Visual aids like images or 3D models can provide a better understanding of complex concepts for clients without a background in construction.
Lastly, providing regular updates about the project’s progress ensures transparency and keeps stakeholders informed about any changes or delays.
A survey conducted by the Construction Specification Institute revealed that poor communication contributes to 70% of construction disputes. Effective dialogue can prevent most conflicts and create better outcomes for all involved parties.
Learn from your mistakes, but also learn from your successes – that way you can estimate your drywall needs like a boss.
Learning from past project endeavors has been an essential aspect of ensuring improvements and refining estimation methods. In doing so, understanding the mistakes made in previous projects can help to avoid such errors in future ones. With further learning, a better estimation technique can be established as well as gaining more knowledge of the job requirements and site conditions.
Using improved estimation methods, cost-effective solutions are more achievable through accurate estimates of material quantities for each job. This is beneficial for contractors and clients alike, allowing work to be completed quicker without any additional expenses being added later.
Moreover, accurate estimations allow for better planning and scheduling, resulting in a much smoother workflow for the construction project.
Pro Tip: Utilize software tools that enhance precision and efficiency in drywall estimation, producing error-free results that save time and costs.
A drywall estimator is a tool used to determine the amount of drywall needed for a specific project. It takes into account the size of the space, the number of doors and windows, and other details to give an accurate estimate.
Drywall estimating is important to ensure you have the correct amount of materials for your project. It can also help save money by avoiding overbuying materials you don’t need.
Yes, drywall estimators can be used for any project that requires drywall. They can be used for both residential and commercial projects.
Many drywall estimators are available online and can be used for free without any special software. Some may require a download or purchase of a specific software program.
While a drywall estimator can provide an accurate estimate, it’s important to double-check the amount of materials needed with a professional or experienced contractor to ensure you have everything you need.
Here I am going to share some steps to get your drywall construction cost estimate report.
You can send us your plan on info@estimatorflorida.com
Before starting your project, we send you a quote for your service. That quote will have detailed information about your project. Here you will get information about the size, difficulty, complexity and bid date when determining pricing.
We do drywall construction cost estimating and prepare a detailed report for your project. At last you finalize the report and finish the project.
561-530-2845
info@estimatorflorida.com
Address
5245 Wiles Rd Apt 3-102 St. Pete Beach, FL 33073 United States
561-530-2845
info@estimatorflorida.com
Address
5245 Wiles Rd Apt 3-102 St. Pete Beach, FL 33073 United States
All copyright © Reserved | Designed By V Marketing Media | Disclaimer
IMPORTANT: Make sure the email and cell phone number you enter are correct. We will email and text you a link to get started.
By clicking “I Agree” above you give Estimate Florida Consultin express written consent to deliver or cause to be delivered calls and messages to you by email, telephone, pre-recorded message, autodialer, and text. Message and data rates may apply. You are able to opt-out at any time. You can text STOP to cancel future text messages.