A Wining Cost Estimate
That Helps You To Win More Concrete Construction Projects
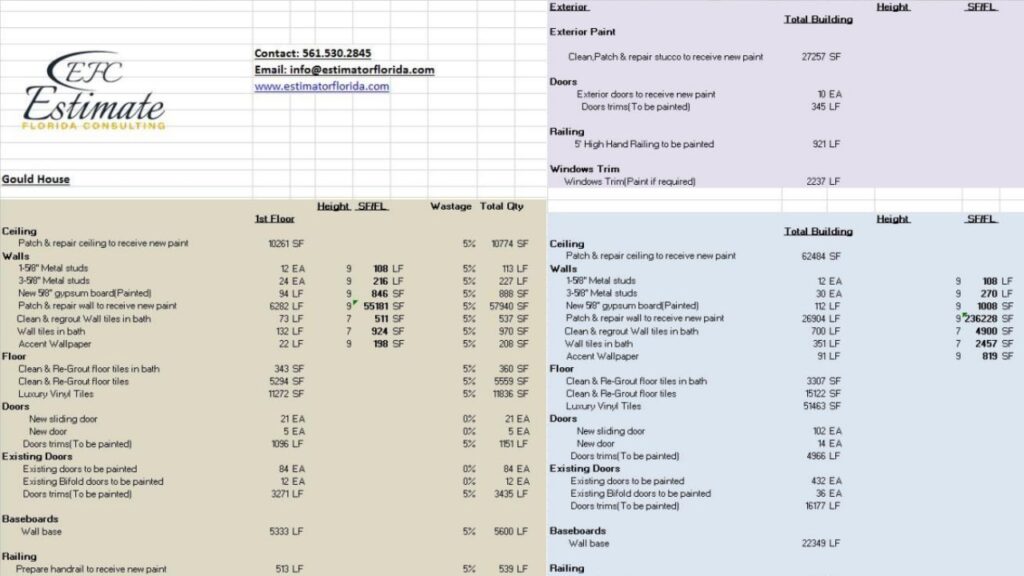
Factors that affect the pricing of commercial concrete projects include:
It’s essential to remember that other details should also be taken into account when estimating commercial concrete expenses. Equipment for site access or material delivery can cause expenses to rise.
Pro Tip: When making an estimate, do your research to avoid any external factors that can affect the final price. Make sure you don’t end up with unexpected expenses when executing your project.
This section focuses on the costs associated with the essential materials and equipment required for commercial concrete projects.
Below is a comprehensive table of the costs of required materials and equipment for commercial concrete projects.
Material/Equipment | Unit | Average Cost ($) |
---|---|---|
Concrete | Cubic Yard | $135 – $175 |
Rebar | Ton | $700 – $800 |
Forms | Square Foot | $10 – $25 |
Excavation | Hourly | $100 – $150 |
Finishing Tools | Set | $500 – $700 |
It is important to note that additional costs such as transportation and delivery fees may be included in the final price of materials and equipment.
The history of commercial concrete dates back to ancient civilizations such as the Romans who used concrete to build significant structures such as the Colosseum and the Pantheon. Today, concrete remains a critical building material with a variety of applications in both commercial and residential construction industries.
Concrete mixes, because apparently ‘just add water’ doesn’t apply to everything in life.
Building needs the right materials and equipment. Concrete is an important element for solid structure. Knowing the costs of different Concrete Variants can help with budgeting.
We made a table with ratios and costs for Regular Mix, High-Strength Mix, Lightweight Mix, etc. Components such as cement, sand, coarse aggregate, and water are listed with estimated price each.
Remember mix designs can vary because of temperature and availability. Also, costs might change due to economic reasons.
Pro Tip: Ask local material providers or contractors about current prices in your area before budgeting.
Reinforcements? Oh yeah, my bank account needs some serious help!
Reinforcing materials are essential for construction projects’ strength and stability. They serve as a supporting system to improve structures’ performance and durability..
Depending on the region and structure needs, unique combinations of material types can be used for reinforcement.
It’s interesting to note that reinforcing materials have been utilized since ancient times. For example, the Romans used iron rebar to reinforce their buildings. As technology advanced, new alternatives better suited for specific applications emerged.
Materials and equipment costs are key when completing a project. These can include paints, tiles, wood panels, and much more. It all depends on the desired outcome and budget.
Here’s a breakdown of some typical finishing materials for construction:
Material | Description | Price Range ($) |
---|---|---|
Tiles | Ceramic or Porcelain pieces for walls or floors | 5 – 50 per square foot |
Paints | Pigmented liquid or paste coating applied to surfaces for color or protection. | 20 – 100 per gallon |
Carpets or Rugs | Soft floor covering made of fibers or textiles that are used to cover floors in various settings such as homes or offices. | 2-20 per square foot |
Bear in mind that prices may vary due to location and other factors. Consider durability, maintenance requirements, and safety implications of each material. It is best to consult professionals in the field for guidance. They can recommend reliable suppliers and provide trend insight. Also, getting quotes from multiple vendors is recommended for competitive pricing.
Informed decisions about finishing materials can enhance a project’s quality while controlling costs. Researching machine and equipment costs may make manual labor more appealing.
We help contractors find new customers with high-converting websites and locally targeted niche-specific lead-generation programs. You’ll never need to worry about running out of work again! We focus on quality over quantity with our leads for contractors.
When deciding project expenses, essential costs related to obtaining required machines and equipment are key to consider. Thus, analyzing Machine and Equipment Costs in detail is a must.
Take a look at the table below. It highlights ‘Required Machine and Equipment Costs’, and the standard Columns- Maintenance, Upgrade & Installation Cost and Total Cost in US Dollars.
Machine & Equipment | Maintenance Cost | Upgrade & Installation Cost | Total Cost |
---|---|---|---|
Machines A | $1000 | $3500 | $4500 |
Machines B | $2000 | $5500 | $7500 |
Machines C | $2500 | $5000 | $7500 |
Other [Equipment items] | Varies according to demand & model |
Bear in mind that all machines and tools require maintenance. Therefore, make sure you have a budget for regular check-ups.
Did you know that, according to a survey conducted by “The Statistics Portal,” machinery needs to be upgraded every 5 years? Skip the gym and lift those hefty labor cost invoices instead!
In this section, we will discuss the expenses related to Human Resources involved in the commercial concrete project.
We present a table that includes details of workers, their wages, and the total cost per hour for each worker. The table includes columns such as Job
Job | Hourly Wage | Hours Worked | Total Cost |
---|---|---|---|
Concrete Finisher | $25-$40 | 40 | $1000-$1600 |
Concrete Laborer | $15-$25 | 40 | $600-$1000 |
Concrete Foreman | $30-$50 | 40 | $1200-$2000 |
It is crucial to have a detailed project plan that includes a breakdown of the workforce needed for the project. Careful
consideration of the qualifications and expertise of each worker is necessary to effectively manage labor costs.
It is crucial to have a detailed project plan that includes a breakdown of the workforce needed for the project. Careful consideration of the qualifications and expertise of each worker is necessary to effectively manage labor costs.
Additionally, engaging in ongoing training and upskilling opportunities for the workforce can lead to efficiency and cost savings with a better quality of work. This investment in employees can lead to reduced labor costs in the long run as they acquire more knowledge and skills.
Proper management of Human Resources is critical to ensuring that the project stays within budget and is completed on time with the desired quality standards.
Site preparation is the concrete jungle’s version of a spa day – cleaning, exfoliating, and getting everything ready for the foundation to shine.
Earthworks is a crucial step before any construction work. It involves excavation, site clearance and leveling the land. Also, site preparation is necessary. This includes installing access roads, job office trailers, toilets and generators. Plus, inspection of land for toxic materials.
In addition, unwanted or existing structures like trees and shrubs are removed with earth moving equipment or manually by workers.
An unexpected challenge happened during a school construction project in rural Zambia. Heavy rain caused standing water and made it impossible to start. The project manager arranged for extra equipment for proper drainage management to save the project from delay.
Think concrete pouring is hard? Just wait to see the price tag for finishing it!
Discover the transformative power of hiring professional contractors for your project. Unlock a wealth of expertise and experience to ensure success. Get started today and see the difference!
Pouring and Finishing Concrete – a 3-Step Guide!
Costs can increase with colorants or stampings for aesthetics.
Pro Tip: Gather an experienced team to ensure quality control for excellent results!
Plus! Wrecking balls and garbage trucks rejoice – the demolition and cleanup industry is thriving due to high labor costs.
Demolition and Removal Expenses – 6 Pointers.
Local regulations may mandate paperwork to show recycling was done.
Pro Tip: Check with a local expert beforehand.
Permits and inspection costs won’t make your money vanish like magic!
Costs Associated with Permits and Inspections. Underestimating the costs associated with permits and inspections can affect the overall budget for a commercial concrete project.
To give an idea of the costs involved, the following table outlines what may be required for permits and inspections based on location and project type.
Type of Permit | Cost |
---|---|
Building Permit | $500 – $3,000 |
Demolition Permit | $200 – $2,000 |
Electrical Permit | $100 – $500 |
Plumbing Permit | $200 – $500 |
Excavation Permit | $100 – $300 |
Inspection Fees | $50 – $500 per visit |
It is important to note that these costs may vary depending on the location and size of the project, as well as the type of permits required. Additionally, specific permits may be needed for certain aspects of the project, such as environmental permits or special use permits.
One example of the necessity of permits and inspections can be seen in the history of the Hyatt Regency walkway collapse in 1981. The disaster occurred due to a change in the original design, which did not receive proper permitting and inspection, leading to a catastrophic failure and resulting in 114 deaths. This highlights the importance of following proper permitting and inspection procedures to ensure the safety and success of a commercial concrete project. Permit fees are like taxes, but at least with taxes you get a road – all you get with permit fees is a headache.
Permit costs are an important part of any construction project. These fees are used to pay for local government regulations, and ensure compliance with building codes, zoning laws, and safety standards. Fees can differ depending on the project and region.
Here is a breakdown of permit fees for different projects:
Project Type | Permit Fee Range |
---|---|
New Construction | $500-$5,000+ |
Renovation/Remodeling | $200-$2,500+ |
Electrical Work | $50-$500+ |
Plumbing Work | $75-$750+ |
It’s important to remember that permit fees aren’t the only expenses related to inspections. Extra costs may apply if your project needs multiple visits or more work.
Knowing permit and inspection costs will help you plan for unexpected expenses and have a successful outcome with no delays. Don’t forget to be aware of permit and inspection costs for a successful project. It’s best to use qualified experts to help and guide you through the process.
“Nobody likes to think of inspection fees with glee – said no one ever!”
The charges for inspecting buildings or sites are known as ‘Assessment Expenses’. They are connected to permit fees, and the amount varies depending on the type of permit, size of the project, scope, and complexity.
A table of ‘Assessment Expenses’ includes columns such as Permit Type, Site Inspection Fee, Re-inspection Fee, Expedited Service Fee (if necessary), and other relevant fees. In a city like New York, a site inspection fee for a construction project may range from $150 to $280, depending on the size.
In addition to size and location, there could be other charges during specific inspections. These are unique requirements such as elevator inspections ($500 per unit), sprinkler inspections ($40 per riser), and others.
A Pro Tip: Before starting any project requiring permits or assessments, it is important to find out all the requirements in advance, to avoid unexpected fees during construction. Transportation costs may be pricey, but at least you’re getting closer to your daily Fitbit target!
Transporting materials from suppliers to construction sites is essential when calculating commercial concrete costs. This cost can really influence the total budget and should be considered before deciding on prices.
Check out the table below for estimates of transportation costs for various concrete types and quantities. These rates may change based on distance, accessibility, and delivery times.
Type of Concrete | Quantity | Transportation Cost (approx.) |
---|---|---|
Ready-Mix Concrete | 1-3 cubic yards | $110 – $150 |
Ready-Mix Concrete | 4-8 cubic yards | $180 – $220 |
Ready-Mix Concrete | 9-10 cubic yards | $250 – $300 |
Pre-Cast Concrete | per piece/foot | $30 – $50 |
Beware of extra fees associated with handling, unloading, or waiting times during delivery. Communicating well with your supplier is key to avoiding these charges.
Failing to include transportation costs in your estimates can lead to inaccurate budgets and construction delays. Be sure to take these expenses into account from the start so that you can plan appropriately.
Including every detail matters when calculating your project expenses – don’t forget to factor in the cost of therapy for stress relief too!
Maximize your concrete construction business’s potential with our competitive financing options
The Complete Guide to Commercial Concrete Cost Estimation covers multiple aspects of estimating costs of building with concrete. In addition to the direct expenses are other expenses that must be accounted for.
There are several costs apart from the primary expenses that need to be considered when estimating commercial concrete costs. These include permit fees, potential project delays, drainage systems, curing requirements, reinforcement, and finishing touches.
It is vital to note that permits and other legal compliance requirements may vary depending on the jurisdiction. Therefore, it is essential to do comprehensive research or consult with regulatory bodies to avoid unnecessary penalties.
According to the National Ready Mixed Concrete Association, “Concrete is the second most consumed substance in the world, second to water“. Architectural and engineering fees: because paying for a building that won’t collapse is priceless.
Architectural and Engineering Services are essential for any construction project. These include design and planning, structural elements, sustainability aspects and more. Here is an overview of the fees you may expect for these professional services:
Service | Average Cost |
---|---|
Architecture Consultation | $150-$400/hr |
Structural Engineering | $5000-$10,000+ (depending on complexity) |
Geotechnical Engineering | $3,000-$5,000+ (depending on site requirements) |
Bear in mind that these prices may vary based on factors such as the project scope and location. Other costs may include permits and approvals from local authorities.
For maximum return on investment, it’s important to match building resources with architectural expectations. Investing in architectural services can save you from costly design modifications down the line.
Don’t risk compromising your vision or budget. Get expert advice to comply with regulations and ensure your building is flawless
– hire architects and engineers today! Prepare for the worst and budget for contingency costs.
It’s crucial to consider ‘Emergency Costs’ for unanticipated expenses. Emergencies can happen at any moment and are usually not accounted for in budgets. Below is a table displaying possible emergency costs:
Emergency Cost | Amount |
---|---|
Equipment repairs/replacements | $1,000-$10,000 |
Weather-related disruptions | $5,000-$20,000+ |
Regulatory Changes/Legal Expenses | $500-$5,000+ |
Personnel/Staff changes | $2,500-$10,000 |
It’s noteworthy that the figures vary depending on the size and type of the project. Natural disasters can cause costs beyond the estimated range.
Project managers must be proactive to get ready for emergency costs. A proper risk assessment plan should be created to foresee emergency circumstances. This allows for better preparation.
Two strategies can be adopted to limit exposure to financial losses from unexpected expenses during projects or tasks: a contingency fund or insurance policies. The former includes setting aside money in savings accounts and the latter requires obtaining suitable insurance coverage depending on one’s needs.
To sum up, taking into account emergency costs is essential when planning projects or tasks. By proactively mitigating risks and using best practices like contingency funds and insurance policies, we can avoid significant financial losses.
Accurately estimating the cost of commercial concrete is critical to ensure successful completion of construction projects within budget and on time. This requires careful planning, knowledge of industry standards, and a detailed understanding of project requirements.
Factors Affecting Commercial Concrete Costs
To accurately estimate commercial concrete costs, it is important to consider the factors that contribute to cost variations. The following table provides an overview of factors that conventional concrete contractors consider while estimating costs:
Factors | Actual Data |
---|---|
Concrete mix design | $3-$12 per square foot |
Labor costs | $25-$75 per hour |
Concrete thickness | $4-$6 per square foot |
Location access | $50-$200 per hour |
Equipment usage | $250-$500 per day |
Finishing and curing methods | $2-$6 per square foot |
While the above factors are important, it is also vital to consider environmental conditions, project timelines, and specific project requirements. For example, an unusual site terrain or complex design may require additional labor, equipment, and materials, contributing to an increased cost of production.
According to the National Ready Mixed Concrete Association, the US concrete industry generates over $35 billion in annual revenue.
Working with experienced contractors is like hiring a bodyguard for your concrete project – they’ll protect it from any crackheads.
Construction projects take multiple steps to save money and time. To ensure success, contracting teams should collaborate with skilled technicians. Here are tips for getting the best results:
Collaborating with expert contractors helps reduce unexpected
setbacks. Plus, it increases the chance that the project will stay within budget. To accurately estimate cost, defining project requirements is key.
To get a precise cost estimate for commercial concrete, you must make a clear and straightforward project brief. This should include the type of building project, the size of the concrete-covered area, and the design specs for the concrete structure.
Being aware of the project’s scope is important for an accurate cost estimation. Check blueprints, site plans, and any needed permits. Knowing these details will help you foresee and prevent surprises during the building project.
When defining the project requirements, make sure everyone is on the same page to keep communication smooth. Leave nothing to chance or interpretation about the project info.
Seek advice from pros experienced with similar projects. They can give you useful advice about resource planning and material use based on their past work.
Document all aspects of the requirements list so it serves as a reference point during the construction project. This way, everyone knows what needs to be done at every step.
Don’t forget to check the local market conditions too – you don’t want to pay too much for concrete!
Comprehending regional business dynamics is key to calculating commercial concrete costs. Being aware of the economic, political, and social state in a particular area is essential in estimating the cost of concrete-related projects. This comprehension will help in setting prices that fit with market realities and competitors.
Local market conditions are extremely important in deciding how much to bill for concrete works. For instance, places with high demand for construction activities may allow higher pricing levels. Similarly, lack of resources such as cement or delays in importing them may result in higher project expenses. Knowing past trends can also give an idea of future industry developments and inform pricing decisions.
Analyze competitive models when looking into local market conditions to estimate commercial concrete costs. Examining competitor pricing structures would assist in comprehending what rates are suitable for the local space. Examining their previous quotes will help understand which elements lead them to choose the rate sheets’ expenditures.
According to a recent report by IndustryArc, the worldwide construction aggregate market is projected to grow at a CAGR of 6% from 2021-2026.
Remember, gauging concrete costs is like playing a game of Jenga – one wrong move can topple the whole project, so always be prepared to re-evaluate and adjust.
It’s vital to have an efficient commercial concrete cost estimation for complex construction projects. Updating estimations throughout the project can help plan any potential changes in cost factors and progress.
Periodically reviewing estimates and managing timelines is key for accuracy. Inaccurate estimations can bring delays, budget constraints, and even affect the quality of workmanship.
Being mindful of hidden charges, weather changes, and unforeseen events is beneficial. Regularly updating construction plans and equipment requirements is essential.
Overlooking regular reviews is a common mistake that can disrupt precise expenses forecasts. This can cause unpredicted delays and may put the whole plan at risk. Therefore, regular reviews ensure you stay on track and help minimize delays.
Remember, it’s always better to overestimate your commercial concrete project cost, unless you’re willing to risk bankruptcy.
Estimate Costs for Unexpected Situations.
When planning commercial concrete construction projects, set aside a budget for unforeseen costs. These could include bad weather, extra excavation, design changes, material availability, or labor. To ensure you have enough funds, add an extra 10-15% to the total project cost. Break it down item-wise too, for easier tracking.
Include these estimates in your proposal and earn your clients’ trust. This way, you won’t have to worry about unexpected expenses. Bidding too low can create tension, delays, and stress on resources – so make sure to plan ahead! And if your concrete costs end up being inaccurate: mistakes make great garden ornaments!
Exploring commercial concrete cost estimation reveals several factors that affect the total cost. One is understanding the project’s needs and choosing the right materials. Hiring skilled contractors who offer competitive costs is also very important. Additionally, inspecting regularly and guaranteeing quality work prevents costly repairs later.
Accurately estimating costs helps to stop underestimation which may lead to extra costs during construction. It’s wise to take action to guarantee all expenses are considered beforehand, for any concrete repair or building job.
Fascinatingly, a report from FMI, a construction consulting business, states that 70% of construction companies view proper estimating as vital for successful business management.
Factors such as location, project size, and the type and quality of materials used can all impact the cost of commercial concrete projects.
Cost estimates for commercial concrete projects can vary in accuracy depending on the amount of detail provided and the experience of the estimator. For the most accurate estimates, it is recommended to work with a professional estimator.
While it may seem appealing to cut costs by using lower quality materials, this can actually end up costing more in the long run due to the need for repairs or replacements. It is best to use high-quality materials that can withstand the demands of commercial use.
The timeline for a commercial concrete project can vary depending on factors such as project size, weather conditions, and site accessibility. A professional contractor can provide a more accurate timeline based on the specifics of the project.
While it is possible to estimate the cost of a commercial concrete project on your own, it is recommended to work with a professional estimator to ensure accuracy and to account for all necessary factors.
It is important to consider factors such as building codes and regulations, project design and specifications, and site accessibility before starting a commercial concrete project. Working with a professional contractor can ensure that all of these factors are taken into account.
Here I am going to share some steps to get your concrete construction cost estimate report.
You can send us your plan on info@estimatorflorida.com
Before starting your project, we send you a quote for your service. That quote will have detailed information about your project. Here you will get information about the size, difficulty, complexity and bid date when determining pricing.
We do concrete construction cost estimating and prepare a detailed report for your project. At last, you finalize the report and finish the project.
561-530-2845
info@estimatorflorida.com
Address
5245 Wiles Rd Apt 3-102 St. Pete Beach, FL 33073 United States
561-530-2845
info@estimatorflorida.com
Address
5245 Wiles Rd Apt 3-102 St. Pete Beach, FL 33073 United States
All copyright © Reserved | Designed By V Marketing Media | Disclaimer
IMPORTANT: Make sure the email and cell phone number you enter are correct. We will email and text you a link to get started.
By clicking “I Agree” above you give Estimate Florida Consultin express written consent to deliver or cause to be delivered calls and messages to you by email, telephone, pre-recorded message, autodialer, and text. Message and data rates may apply. You are able to opt-out at any time. You can text STOP to cancel future text messages.