The cost of structural steel per square foot varies depending on the type of project and the complexity of the design. On average, the cost ranges from $30 to $60 per square foot, which includes materials, fabrication, and installation.
Project Type | Cost per Sq. Ft. |
Residential Buildings | $30 – $45 |
Commercial Buildings | $40 – $60 |
Industrial Facilities | $50 – $70 |
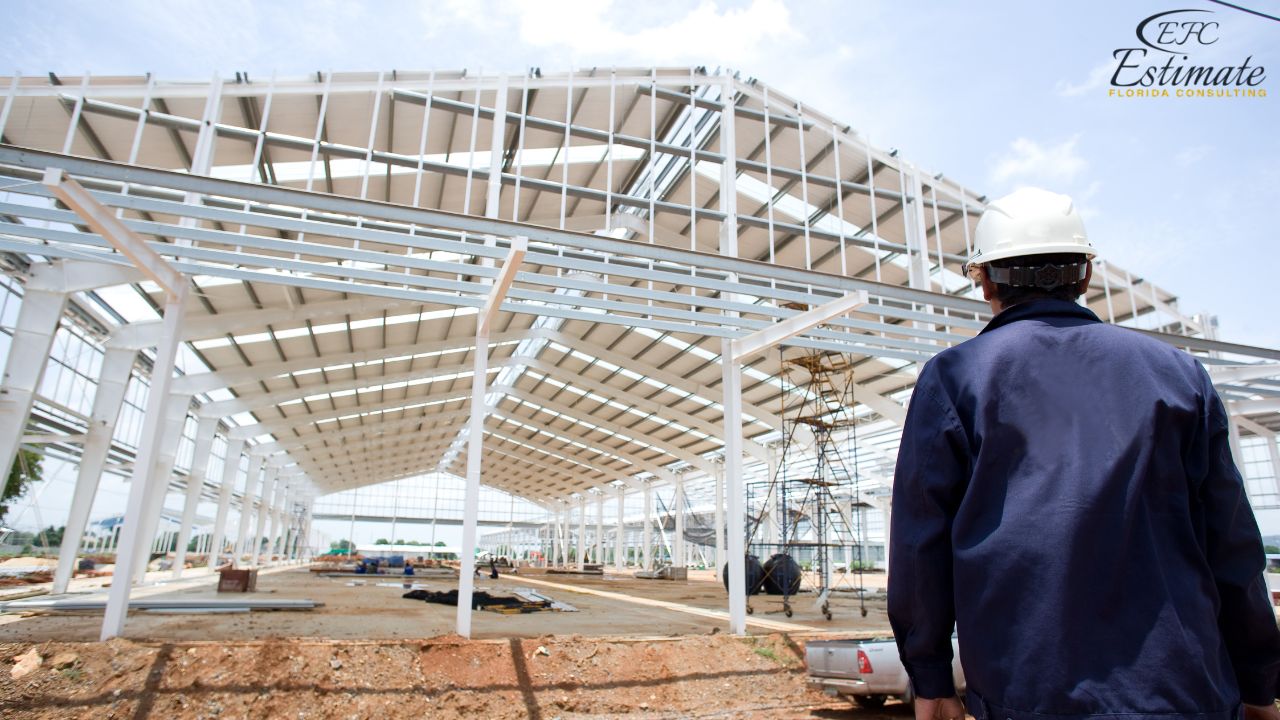
Structural Steel Framing Costs
Steel framing is a popular choice for its strength and efficiency in both residential and commercial construction. The cost of steel framing typically ranges from $10 to $20 per square foot, including materials and labor.
Building Type | Framing Cost per Sq. Ft. |
Residential Homes | $10 – $15 |
Commercial Buildings | $15 – $20 |
Residential Structural Steel Takeoff
Structural steel is increasingly used in residential construction due to its durability, flexibility, and ability to support modern architectural designs. Residential steel takeoffs typically include beams, columns, and steel frames for open floor plans, large windows, and multi-story layouts.
Costs for Residential Steel Takeoff
Home Size | Steel Cost Estimate |
2,000 sq. ft. Home | $60,000 – $90,000 |
3,500 sq. ft. Home | $105,000 – $150,000 |
5,000 sq. ft. Home | $150,000 – $225,000 |
Structural Steel Takeoff
Beams
Beams are critical horizontal structural elements that support and distribute loads to columns, ensuring structural stability and integrity. Common types of steel beams include I-beams, H-beams, and wide flange beams, each suited to different applications based on load requirements and span lengths. I-beams, for instance, are often used in smaller-scale construction, while wide flange beams are preferred for large-scale projects due to their enhanced strength and versatility. The cost of beams, typically ranging from $800 to $1,200 per ton, is influenced by factors such as size, weight, and the material grade of steel used. Additional costs may include fabrication for specific dimensions, coating for corrosion resistance, and transportation to the construction site.
Columns
Columns are vertical structural elements designed to bear axial loads and transfer them to the foundation. They are a fundamental component in structural steel frameworks, particularly in high-rise buildings, industrial facilities, and large commercial projects. The design and material of steel columns depend on the load they need to support and the height of the structure. Tapered or square hollow steel columns are commonly used to provide robust support. Costs for columns range from $900 to $1,400 per ton, with price variations depending on the column’s size, length, and the steel grade required. Installation and additional treatments, such as fireproofing or corrosion protection, may also add to the total expense.
Get Acquainted with Estimation
Mastering Bids: 12 Pro-Level Bidding Tips for Construction Managers
Maximize Profits: Budgeting Hacks for Big Construction Projects
Braces
Braces play a crucial role in maintaining lateral stability in structures by resisting forces such as wind loads or seismic activity. They are especially vital in earthquake-prone regions or areas subject to high winds. Common types include cross-braces, chevron braces, and knee braces, chosen based on the building’s architectural design and structural needs. Braces are often fabricated using steel tubes or angles, which provide high tensile strength and durability. The cost of braces typically ranges from $600 to $1,000 per ton, depending on the complexity of the design, material used, and the length required for the application. Additional considerations include labor costs for installation and any reinforcement needed for specific conditions.
Braces
Braces play a crucial role in maintaining lateral stability in structures by resisting forces such as wind loads or seismic activity. They are especially vital in earthquake-prone regions or areas subject to high winds. Common types include cross-braces, chevron braces, and knee braces, chosen based on the building’s architectural design and structural needs. Braces are often fabricated using steel tubes or angles, which provide high tensile strength and durability. The cost of braces typically ranges from $600 to $1,000 per ton, depending on the complexity of the design, material used, and the length required for the application. Additional considerations include labor costs for installation and any reinforcement needed for specific conditions.
Plates and Connectors
Plates and connectors are essential for joining various steel components together, ensuring a secure and stable framework. These include base plates, gusset plates, splice plates, and connectors such as bolts, rivets, and welds. Base plates distribute column loads to the foundation, while gusset plates provide support and stability at joints. The cost of plates and connectors ranges from $300 to $700 per ton, with variations based on the type, thickness, and steel grade. Complex connection designs or high-load requirements may necessitate specialized plates and high-strength bolts, increasing the overall cost. Additionally, labor for installation and welding, as well as any protective coatings, can significantly influence the final expense.
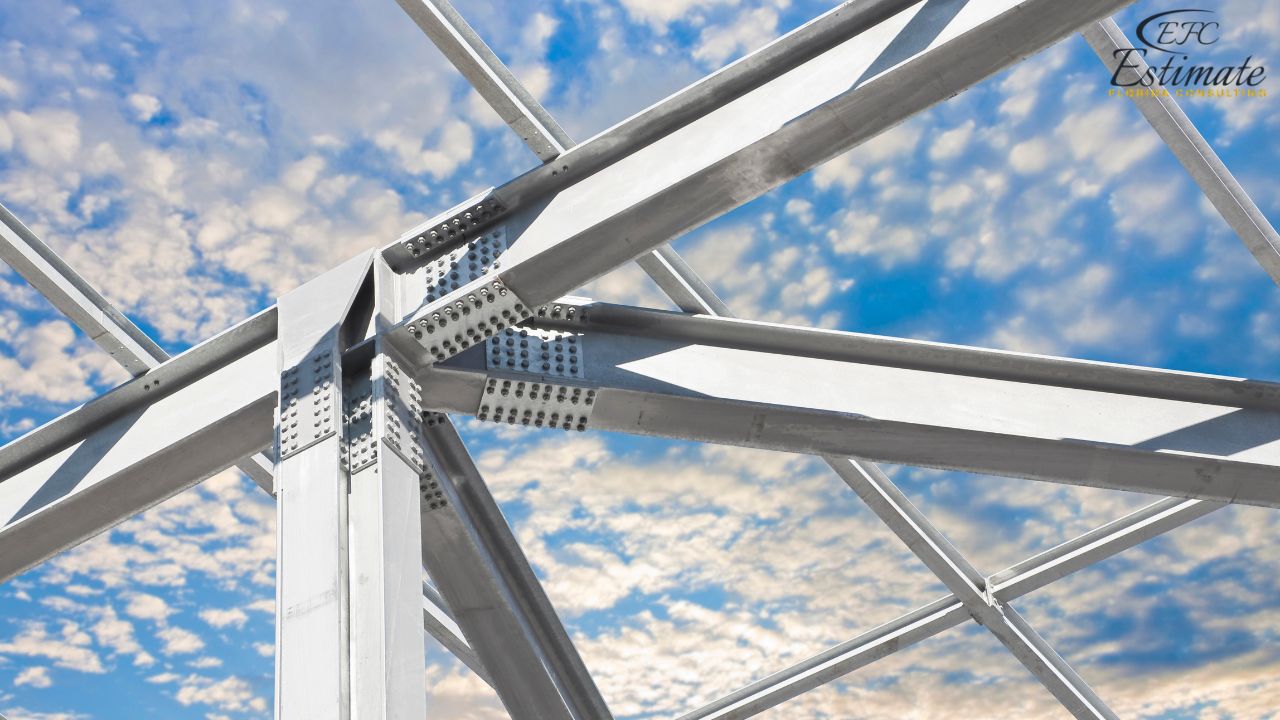
Component | Average Cost per Ton |
Beams | $800 – $1,200 |
Columns | $900 – $1,400 |
Braces | $600 – $1,000 |
Plates & Connectors | $300 – $700 |
Structural Steel Takeoff by Project Size
Small-Scale Projects
Small-scale projects, such as single-family homes or small commercial buildings, require comparatively less structural steel, but the cost per unit can be higher due to fabrication and transportation expenses. These projects typically involve basic structural elements like beams, columns, and framing components. The average cost for small-scale projects ranges from $20,000 to $100,000, depending on the building’s complexity and location. Additional costs may arise for custom steel designs, on-site adjustments, or specialized coatings to improve durability against environmental factors. For homes incorporating modern architectural features, such as large open spaces or cantilevered sections, the required steel could further increase both material and labor costs.
Medium-Scale Projects
Medium-scale projects, including mid-rise residential or commercial buildings, require more steel, specialized components, and careful planning to ensure structural integrity. These projects typically use a combination of standard and customized steel components, such as joists, trusses, and reinforcements for larger spans. Costs for medium-scale projects generally range from $100,000 to $500,000, with variations based on design complexity, steel grade, and local market conditions. The need for specialized equipment, such as cranes for lifting heavy steel sections, and the coordination between multiple contractors can further increase expenses. Additionally, medium-scale projects often require compliance with stricter building codes and safety regulations, adding to the overall cost.
Large-Scale Projects
Large-scale projects, such as high-rise buildings, industrial facilities, and expansive commercial complexes, involve significant quantities of steel, advanced engineering, and complex logistics. These projects often require custom-fabricated steel components, such as heavy girders, advanced connection systems, and pre-engineered modules, to handle immense structural loads. Costs for large-scale projects can exceed $1 million, depending on the size, scope, and geographical location of the project. Logistics, including transporting large steel sections to the construction site and managing their assembly, significantly impact the budget. Advanced project management, the involvement of structural engineers, and cutting-edge technology, such as Building Information Modeling (BIM), are often essential for these massive undertakings, further increasing overall costs.
Win More Projects With Us
Structural Steel Takeoff Process
The structural steel takeoff process is a critical part of estimating and planning in construction projects. It ensures accurate cost forecasting and efficient resource allocation. Below are the detailed steps involved in this process:
Reviewing Blueprints
The process begins with a thorough analysis of the project’s blueprints and construction drawings. This involves identifying all structural steel components, including beams, columns, trusses, braces, and connections. Engineers and estimators pay close attention to design specifications, material grades, and dimensions outlined in the plans. Additionally, special requirements such as load-bearing capacity or fire resistance coatings are noted to ensure no detail is overlooked. Accurate blueprint analysis is essential for avoiding errors that could lead to material shortages or project delays.
Quantifying Materials
Once the blueprints are reviewed, the next step is to measure and calculate the quantities of steel required. This involves determining the lengths, weights, and numbers of each steel component. Advanced software or manual calculations may be used to account for factors like cutting losses, wastage, and overlaps in material usage. For projects with complex designs, such as curved or tapered sections, additional calculations are performed to ensure precision. The goal is to create a detailed list or Bill of Materials (BOM) that includes every piece of steel required for the project.
Pricing Materials
After quantifying the materials, current market prices for structural steel are researched. Pricing includes the cost of raw steel, fabrication services (such as cutting, welding, or bending), and coatings (like galvanizing or painting). Transportation costs are also factored in, considering the delivery location and volume of materials. Additionally, labor costs for handling and installing the steel components are estimated. Adjustments may be made for potential fluctuations in steel prices or for bulk purchase discounts, ensuring the estimate is both accurate and competitive.
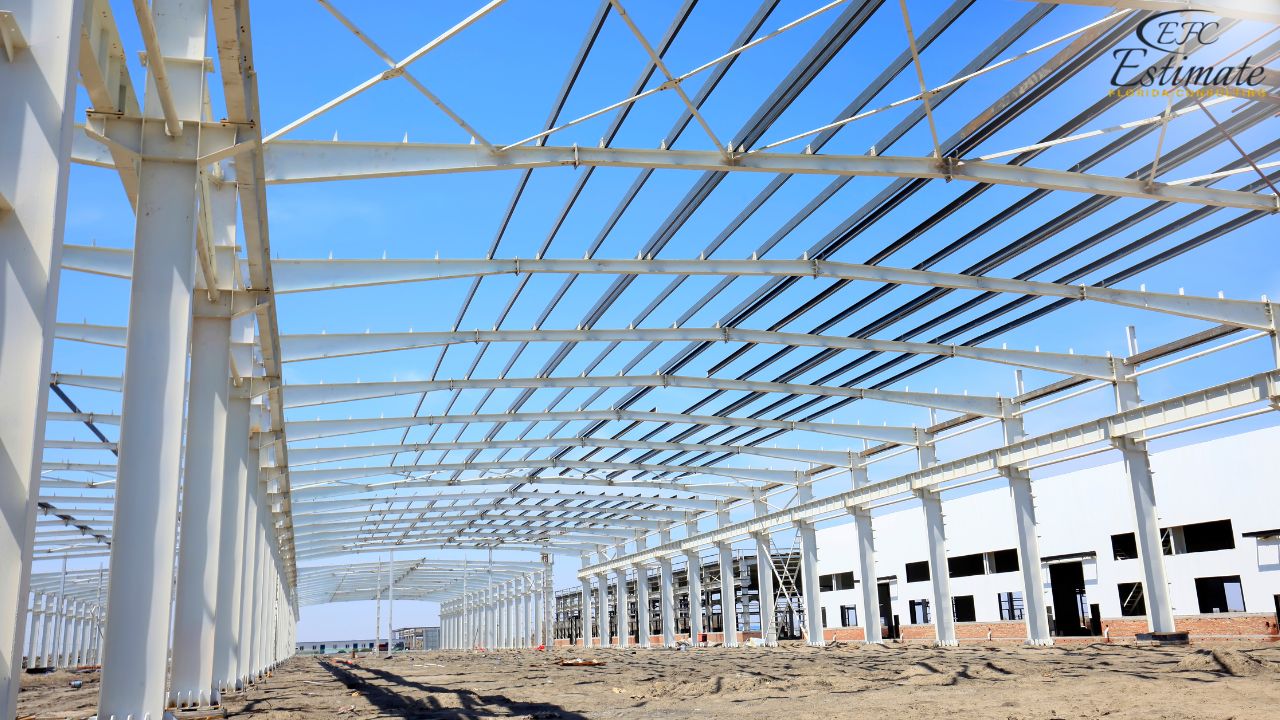
Finalizing the Estimate
The final step is compiling all data into a comprehensive estimate report. This document includes detailed quantities, material costs, labor expenses, and project timelines. Estimators also account for contingencies, such as unforeseen design changes or material price volatility. A well-prepared estimate not only guides procurement and budgeting but also provides a clear roadmap for project execution. By presenting this information in a clear and organized format, stakeholders can make informed decisions and align resources effectively to meet project goals.
Quantifying Materials
Once the blueprints are reviewed, the next step is to measure and calculate the quantities of steel required. This involves determining the lengths, weights, and numbers of each steel component. Advanced software or manual calculations may be used to account for factors like cutting losses, wastage, and overlaps in material usage. For projects with complex designs, such as curved or tapered sections, additional calculations are performed to ensure precision. The goal is to create a detailed list or Bill of Materials (BOM) that includes every piece of steel required for the project.
Factors Affecting Structural Steel Costs
Market Fluctuations
Global demand and supply disruptions significantly impact structural steel costs. Economic factors, such as trade tariffs, geopolitical tensions, or raw material shortages, can cause sharp price fluctuations. For instance, an increase in global construction activity often drives up demand, leading to higher prices. Conversely, surplus steel production or declining demand in major markets may reduce costs. Staying informed about market trends is crucial for accurately budgeting a project involving structural steel.
Design Complexity
Intricate designs require additional fabrication and skilled labor, which can increase costs. Projects involving custom shapes, curved steel components, or specialized coatings demand more time and expertise in the fabrication process. Complex designs may also necessitate advanced welding techniques, precision cutting, and additional quality checks to ensure the structural integrity of the steel components, all of which contribute to higher expenses.
Project Location
Transportation costs play a significant role in determining structural steel prices. The farther the project site is from the steel supplier or fabrication facility, the higher the logistics expenses. Additionally, regions with limited access to steel suppliers or challenging transportation routes may face elevated delivery costs. Urban areas with heavy traffic congestion or rural locations with underdeveloped infrastructure can further complicate and increase transportation expenditures.
Fabrication Requirements
Transportation costs play a significant role in determining structural steel prices. The farther the project site is from the steel supplier or fabrication facility, the higher the logistics expenses. Additionally, regions with limited access to steel suppliers or challenging transportation routes may face elevated delivery costs. Urban areas with heavy traffic congestion or rural locations with underdeveloped infrastructure can further complicate and increase transportation expenditures.
Download Template For Structural Steel Project Breakdown
- Materials list updated to the zip code
- Fast delivery
- Data base of general contractors and sub-contractors
- Local estimators
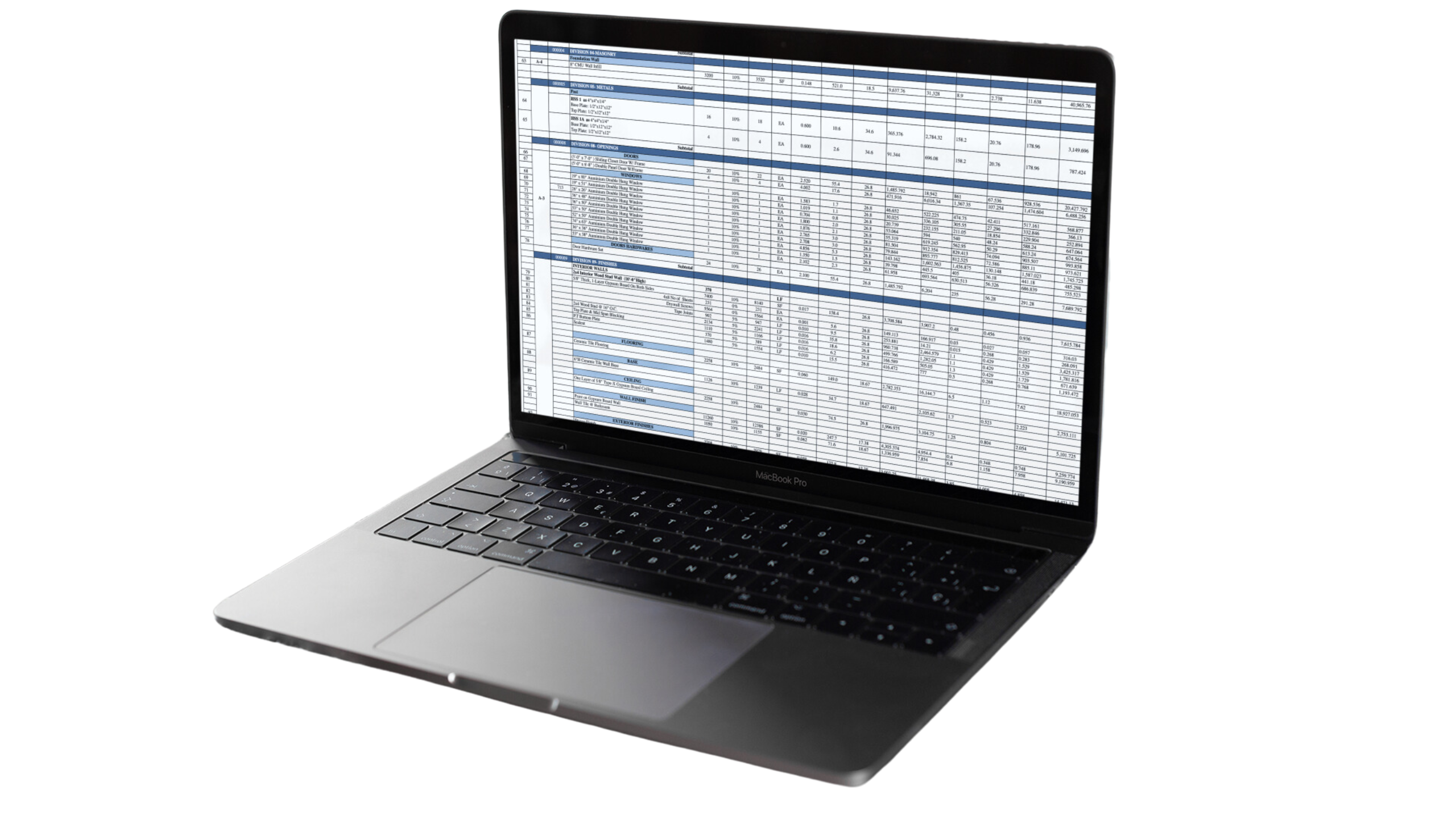
Tips for Accurate Structural Steel Takeoff
- Use Advanced Software: Tools like Tekla, PlanSwift, and Bluebeam can enhance accuracy and efficiency.
- Review Plans Thoroughly: Ensure all steel components are accounted for in the initial review.
- Consult Professionals: Work with experienced estimators to avoid costly mistakes.
- Consider Waste Factors: Account for potential waste when calculating material quantities.
Conclusion
Structural steel takeoff is a critical aspect of any construction project, ensuring that all steel components are accurately quantified and costs are effectively managed. From residential homes to large-scale commercial developments, understanding the intricacies of steel takeoff can help stakeholders make informed decisions and stay within budget. At Estimate Florida Consulting, we provide expert takeoff services tailored to your project’s specific needs, ensuring precision and transparency at every stage.
Frequently Asked Question
A structural steel takeoff is a detailed estimation process used to determine the quantity and cost of steel components required for a construction project. It includes calculating materials like beams, columns, braces, plates, and connectors based on project blueprints and specifications.
Key factors that affect structural steel costs include:
- Market fluctuations in steel prices due to supply-demand dynamics.
- Design complexity, which may require custom fabrication or intricate shapes.
- Project location, influencing transportation and logistics costs.
- Fabrication requirements, such as galvanizing, fireproofing, or specialized treatments.
The cost of structural steel per square foot varies based on the project type:
- Residential buildings: $30 - $45
- Commercial buildings: $40 - $60
- Industrial facilities: $50 - $70
Steel framing costs range from $10 to $20 per square foot, depending on the building type:
- Residential homes: $10 - $15
- Commercial buildings: $15 - $20
The amount of structural steel required depends on the home size:
- 2,000 sq. ft. home: $60,000 - $90,000
- 3,500 sq. ft. home: $105,000 - $150,000
- 5,000 sq. ft. home: $150,000 - $225,000
The average cost per ton of key structural steel components includes:
- Beams: $800 - $1,200
- Columns: $900 - $1,400
- Braces: $600 - $1,000
- Plates and connectors: $300 - $700
Steel framing offers several benefits, including:
- High strength and durability.
- Resistance to pests, fire, and weather damage.
- Flexibility for modern architectural designs.
- Efficient installation with minimal waste.
The takeoff process involves:
- Reviewing blueprints to identify all steel components.
- Quantifying materials like beams, columns, and braces.
- Pricing materials based on current market rates, fabrication, and transportation.
- Finalizing the estimate by compiling data into a comprehensive report.
Advanced software like Tekla, PlanSwift, and Bluebeam are commonly used for precise calculations and efficient planning during the takeoff process.
To ensure accuracy:
- Use advanced estimating software.
- Thoroughly review construction plans and blueprints.
- Account for potential waste in material calculations.
- Consult with professional estimators for expert insights.
Comprehensive Trade-Specific Estimates
At Estimate Florida Consulting, we offer detailed cost estimates across all major trades, ensuring no part of your project is overlooked. From the foundation to the finishing touches, our trade-specific estimates provide you with a complete and accurate breakdown of costs for any type of construction project.
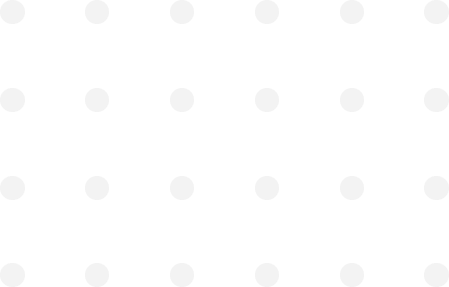
Testimonials
What Our Clients Say
We take pride in delivering accurate, timely, and reliable estimates that help contractors and builders win more projects. Our clients consistently praise our attention to detail, fast turnaround times, and the positive impact our estimates have on their businesses.
Estimate Florida Consulting has helped us win more bids with their fast and accurate estimates. We trust them for every project!
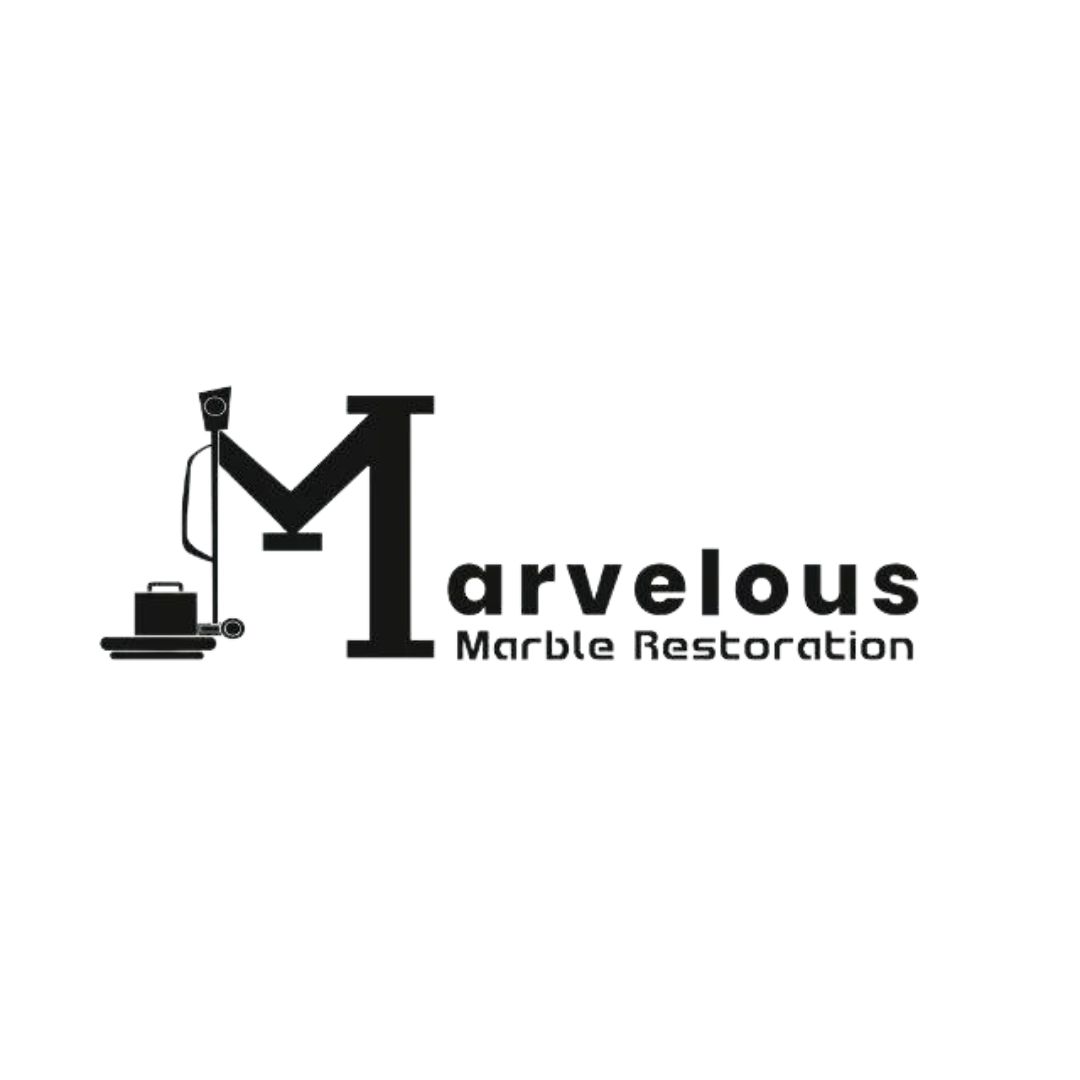
Steps to Follow
Our Simple Process to Get Your Estimate
01
Upload Plans
Submit your project plans, blueprints, or relevant documents through our online form or via email.
02
Receive Quotation
We’ll review your project details and send you a quote based on your scope and requirements.
03
Confirmation
Confirm the details and finalize any adjustments to ensure the estimate meets your project needs.
04
Get Estimate
Receive your detailed, trade-specific estimate within 1-2 business days, ready for your project execution.
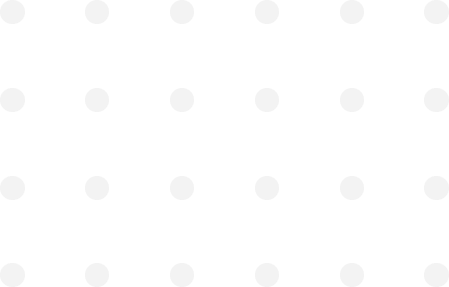