Boost Your Warehouse Construction Bids – Request a Precision Estimate!
- Accurancy
- Efficiency
- Transparency
- Customization
- Time Saving
- Professionalism
- Cost Control
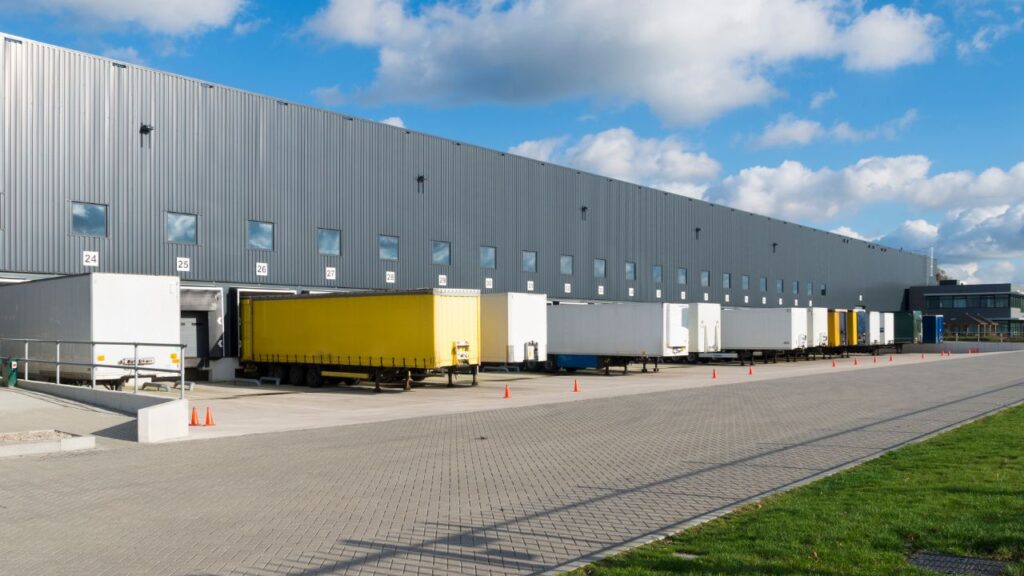
Calculating the cost per square foot for a steel warehouse involves considering various components. The overall expense for a 5,000 square foot warehouse, encompassing the building structure, concrete slab, and erection, typically amounts to approximately $140,000. This translates to an estimated cost of $25 per square foot. When dissecting this figure further, the steel building alone contributes a significant portion. The steel structure’s cost falls within the range of $9 to $15 per square foot, resulting in a total steel building expense ranging from $55,000 to $92,000.
The cornerstone of any steel warehouse is, undoubtedly, the steel itself. However, this seemingly straightforward component is subject to the capricious nature of global markets, economic shifts, and fluctuating demand. The intricacies of steel pricing, influenced by an array of external factors, necessitate a nuanced approach during project planning. Beyond steel, the choice of foundation materials introduces another layer of complexity. Whether opting for the solidity of concrete or the resilience of steel piers, the implications on cost per square foot reverberate through the entirety of the project, underscoring the significance of strategic material decisions.
Fully Insured Licensed
Hire Contractor For Warehouse Construction
Make Informed Design Decisions Showcase Your Design Ideas
Get RenderingThe visual allure of a steel warehouse often belies the intricate engineering and design processes underpinning its creation. Architectural complexity, a defining characteristic of many modern warehouses, contributes not only to the aesthetic appeal but also to the financial intricacies of the project. The more elaborate the design, the greater the demands on engineering expertise, translating into elevated costs per square foot. Customization, a hallmark of contemporary construction, introduces yet another dimension, as tailored features, mezzanines, specialized doors, and unique layouts all weave into the narrative of design-driven expenditures.
Assembling the structural framework of a steel warehouse necessitates a skilled labor force adept in the nuances of steel construction. The expertise of welders, steel erectors, and other specialized professionals directly influences the cost per square foot. Skilled labor, with its inherent value and expertise, commands wages that impact the overall financial landscape of the project, prompting stakeholders to weigh the benefits of proficiency against the associated costs.
The geographical context within which a steel warehouse takes shape introduces a myriad of considerations, each carrying potential financial implications. Local building codes, unique to each region, demand compliance efforts that may incur additional costs. The topography and condition of the construction site, including soil quality and accessibility, add further layers of complexity. Navigating these geographical nuances is essential for mitigating unexpected expenses and ensuring seamless adherence to local regulations.
Beyond the structural skeleton, the functionality and comfort of a steel warehouse hinge on the integration of essential systems. Heating, ventilation, air conditioning (HVAC), electrical wiring, and plumbing are critical components that enhance operational efficiency and occupant comfort. However, the inclusion of these systems introduces an additional layer of costs that must be factored into the overall square footage calculation, highlighting the delicate balance between functionality and financial prudence.
The regulatory landscape governing construction projects is as diverse as the geographical regions in which they unfold. Securing permits and approvals from local authorities involves a complex and often bureaucratic process, entailing administrative expenses that contribute to the overall project costs. Delays in the permitting process can have cascading effects, impacting not only the timeline but also the financial equilibrium of the project.
In the unpredictable realm of construction, unforeseen challenges are an inherent reality. Ranging from unexpected weather events to unanticipated site conditions, these variables necessitate the inclusion of a contingency budget. Safeguarding against the unforeseen is a strategic imperative, and stakeholders must carefully allocate resources to address unexpected contingencies. Additionally, miscellaneous costs such as insurance, project management fees, and legal expenses add further layers to the financial mosaic, emphasizing the need for a comprehensive approach to budgeting.
The construction of a steel warehouse, while inherently robust and efficient, often comes with associated costs that demand careful consideration. Cost-saving strategies play a pivotal role in optimizing financial investments, ensuring that the project aligns with budgetary constraints without compromising on quality or functionality. In this article, we explore proactive approaches and effective cost-saving strategies for steel warehouse construction.
Steel warehouses stand as formidable structures, playing a pivotal role in various industries worldwide. Their importance extends beyond mere physical presence; these structures are the backbone of industrial efficiency, providing crucial storage, logistics, and operational solutions. In this article, we explore the multifaceted and indispensable role that steel warehouses play in fostering economic growth, enhancing logistical operations, and supporting diverse industries.
The cost of constructing a steel warehouse per square foot can vary widely depending on several factors, including location, design complexity, materials used, and specific project requirements.
It’s crucial to note that these estimates are general guidelines, and the actual cost for a specific project may vary based on the factors mentioned earlier. Additionally, costs may include not only the construction of the steel structure but also expenses related to site preparation, permits, utilities, and interior finishes.
Fully Insured Licensed
Hire Contractor For Warehouse Construction
Make Informed Design Decisions Showcase Your Design Ideas
Get RenderingThe construction of steel warehouses involves careful consideration of factors influencing the cost per square foot. Material costs, design intricacies, labor considerations, geographic factors, utility integration, and regulatory compliance all impact the economic landscape of the project. Employing cost-saving strategies and proactive approaches, such as optimized design and streamlined construction techniques, can mitigate expenses.
Steel warehouses play a crucial role in industrial efficiency, providing strategic storage, logistical optimization, and support for various industries. While the cost per square foot can vary, estimates range from $50 to $200 or more, depending on location and project specifics. Stakeholders are advised to consult local professionals for precise cost estimates tailored to their unique needs. Despite challenges, the resilience, adaptability, and long-term cost-effectiveness of steel warehouses make them essential contributors to modern industrial ecosystems.
The cost per square foot is a fundamental metric in steel warehouse construction, serving as the cornerstone for budgeting and strategic decision-making. It reflects the intricate interplay of various factors and influences stakeholders’ ability to optimize financial investments while realizing their structural vision.
Material costs, particularly steel, are crucial contributors to the overall cost per square foot. The capricious nature of global markets and economic shifts introduces complexities, making strategic material decisions paramount. Additionally, the choice of foundation materials, such as concrete or steel piers, adds another layer of cost implications.
Design complexity significantly influences the cost per square foot in steel warehouse construction. The more elaborate the design, the greater the demands on engineering expertise, translating into elevated costs. Tailored features, mezzanines, specialized doors, and unique layouts contribute to design-driven expenditures, underscoring the financial intricacies of architectural elegance.
The geographical context introduces diverse considerations, including compliance with local building codes and addressing site-specific conditions such as soil quality and accessibility. These factors may lead to additional costs, emphasizing the need to navigate local nuances for seamless adherence to regulations and mitigation of unexpected expenses.
The integration of essential systems, such as HVAC, electrical wiring, and plumbing, introduces additional costs that must be factored into the overall square footage calculation. Balancing functionality and financial prudence becomes crucial in maintaining the delicate equilibrium between operational efficiency and costs.
Cost-saving strategies are pivotal in aligning projects with budgetary constraints without compromising on quality or functionality. These include bulk purchases, value engineering, standardized designs, efficient space utilization, prefabrication, sustainable design principles, and proactive risk mitigation. Implementing these approaches can contribute to long-term cost-effectiveness in steel warehouse construction.
Here I am going to share some steps to get your steel warehouse per square foot cost estimate report.
You can send us your plan on info@estimatorflorida.com
Before starting your project, we send you a quote for your service. That quote will have detailed information about your project. Here you will get information about the size, difficulty, complexity and bid date when determining pricing.
Our team will takeoff and estimate your project. When we deliver you’ll receive a PDF and an Excel file of your estimate. We can also offer construction lead generation services for the jobs you’d like to pursue further.
561-530-2845
info@estimatorflorida.com
Address
5245 Wiles Rd Apt 3-102 St. Pete Beach, FL 33073 United States
561-530-2845
info@estimatorflorida.com
Address
5245 Wiles Rd Apt 3-102 St. Pete Beach, FL 33073 United States
All copyright © Reserved | Designed By V Marketing Media | Disclaimer