- Homepage
- Blogs
Steel Structure Cost Estimation Services
Leading provider of steel structure estimating.
The cost of constructing a steel structure varies significantly depending on the type of building and its specifications. On average, steel structure costs range from $20 to $50 per square foot, excluding foundation and finishing. When these additional costs are included, the price can rise to $70 to $120 per square foot.
Type of Steel Structure | Cost per Square Foot |
Pre-Engineered Steel Building | $20 – $40 |
Custom Steel Framed Building | $30 – $60 |
Steel Residential Homes | $70 – $120 |
Steel Commercial Warehouses | $40 – $100 |
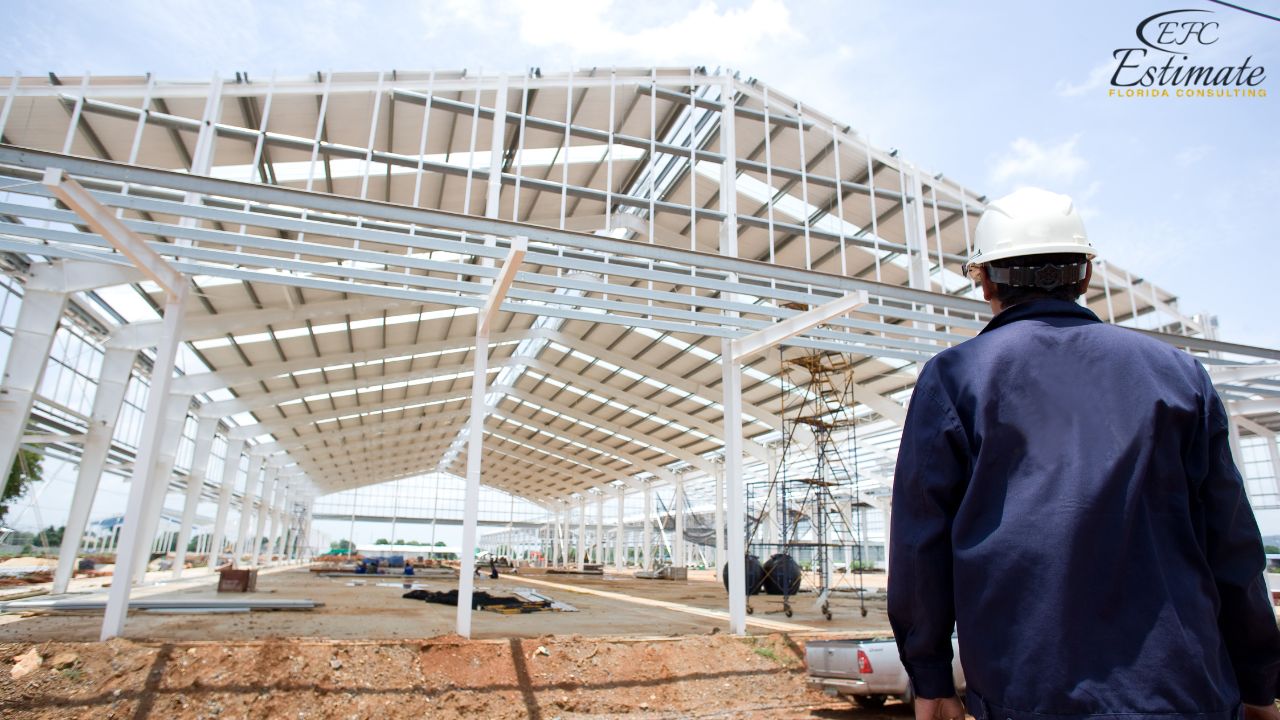
Steel Structure Cost by Building Size
The size of a steel structure is one of the most significant factors affecting its cost. Larger buildings generally benefit from economies of scale, reducing the cost per square foot. Here’s a breakdown of costs based on building size:
Building Size (Sq. Ft.) | Estimated Cost |
1,000 Sq. Ft. | $70,000 – $120,000 |
5,000 Sq. Ft. | $200,000 – $400,000 |
10,000 Sq. Ft. | $500,000 – $1,000,000 |
20,000 Sq. Ft. | $1,000,000 – $2,000,000 |
Types of Steel Structures
Pre-Engineered Steel Buildings
Pre-engineered steel buildings are an affordable and efficient option for projects with standard needs. They’re commonly used for warehouses, barns, and workshops. These structures come with pre-assembled components, which speed up construction and reduce labor costs, making them a go-to choice for projects on a tight budget.
Structural Steel Framed Buildings
Structural steel framed buildings are designed for projects that require unique designs or complex layouts. These are often used in multi-story buildings because of their strength and flexibility. While they offer a high level of customization, they tend to be more expensive than pre-engineered buildings due to the added design and construction work.
Get Acquainted with Estimation
Commercial Construction Estimator | Commercial Construction Estimating
Dominate the Competition: Tips to Secure More Construction Bids
Residential Steel Structures
Residential steel structures, like steel-framed homes and garages, are becoming more popular for their sleek designs, fire resistance, and low maintenance. These homes often feature open layouts and a modern aesthetic, making them a great option for people who want something stylish and durable.
Commercial Steel Structures
Steel is a top choice for commercial buildings because it can support wide spans without needing many columns, which increases usable space. From office buildings to retail stores, steel structures are perfect for creating versatile, scalable spaces that can adapt to changing business needs.
Cost Breakdown for Steel Structure Construction
Steel Frame
The steel frame is the backbone of any steel structure, providing the necessary support and durability. It forms the skeleton of the building, ensuring stability and strength to withstand various environmental factors. The cost of the steel frame generally ranges between $10 and $30 per square foot, depending on several factors such as the type of steel used, the complexity of the design, and the overall size of the structure. High-grade steel and more intricate architectural designs will typically drive up the costs. For larger industrial projects, additional expenses may arise from the need for heavier-duty steel and specialized fabrication techniques.
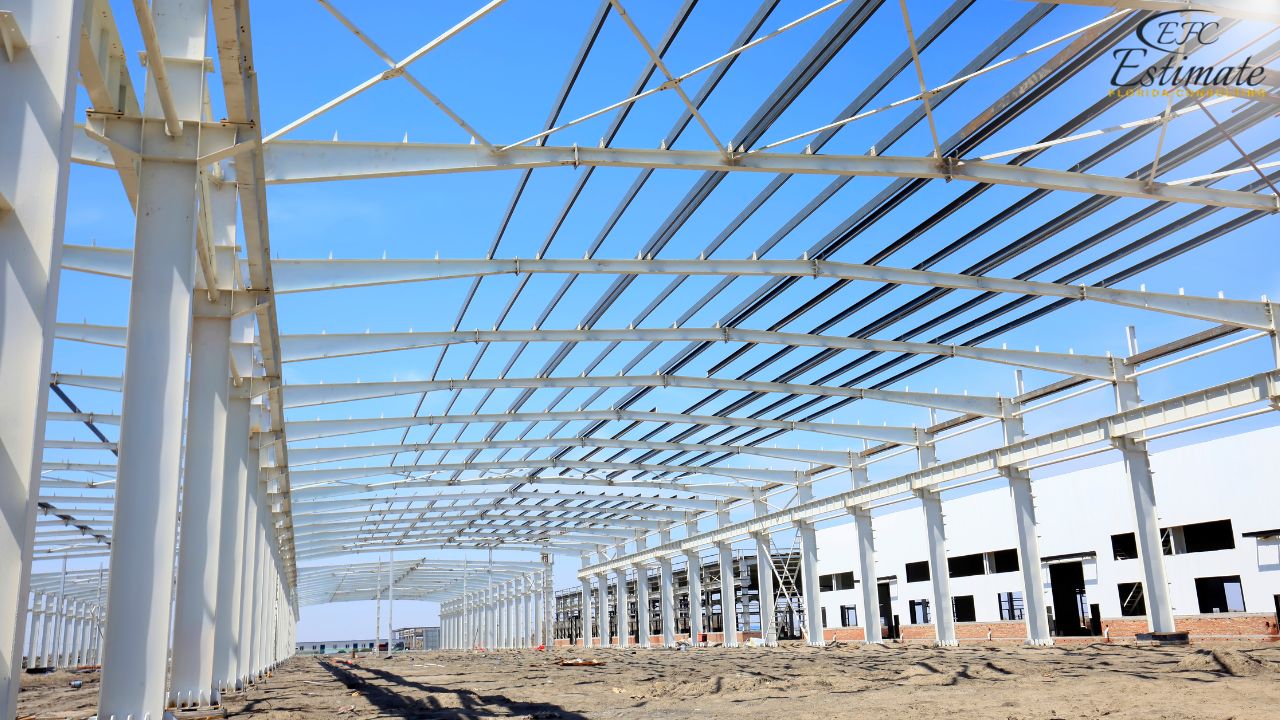
Roofing and Cladding
Roofing and cladding are essential components that not only protect the steel structure from the elements but also contribute to its visual appeal. These materials form the outer shell of the building, safeguarding it from rain, wind, and temperature fluctuations. The cost of roofing and cladding typically falls between $5 and $15 per square foot, depending on the material chosen. Options like standard metal panels are often more affordable, while insulated panels or custom designs can significantly increase costs. Factors such as weather resistance, energy efficiency, and aesthetic preferences often play a role in material selection, influencing the overall budget.
Insulation
Proper insulation is a key element in making steel buildings energy-efficient and comfortable for occupants. Insulation helps regulate indoor temperatures, reducing energy consumption and utility bills. Costs for insulation typically range from $2 to $6 per square foot, varying by the type of material used, such as fiberglass, spray foam, or rigid panels. High-performance insulation materials may cost more but offer better energy savings in the long run. Additionally, the climate of the building’s location can influence the choice and thickness of the insulation, with colder regions requiring more robust solutions.
Foundation
A solid foundation is crucial for supporting the weight of a steel structure and ensuring its stability over time. Foundations for steel buildings are usually made from concrete, with common types being slabs or piers. Costs can range from $5,000 to $50,000, depending on factors such as the size and weight of the structure, the soil conditions at the site, and the design of the foundation. For larger buildings or areas with challenging soil conditions, more advanced foundation systems may be required, which can increase costs. Additional considerations, such as excavation and drainage systems, may also affect the final price.
Utilities
The installation of utilities like electrical systems, plumbing, and HVAC is a significant part of the overall construction budget, ensuring the building is functional and meets modern standards. These installations typically cost between $15,000 and $100,000, depending on the complexity and size of the project. Electrical systems may include basic wiring or advanced setups for heavy machinery, while plumbing can range from simple bathroom fixtures to complex networks for industrial use. HVAC systems are another major component, with costs influenced by the size of the building and the desired level of climate control. Custom features, such as smart systems or high-capacity installations, can further add to the expenses.
Residential Steel Structure Costs
Steel Homes
Steel homes have become increasingly popular due to their modern aesthetic, strength, and energy efficiency. These homes are constructed using prefabricated steel frames, which not only offer durability but also resist pests, mold, and extreme weather conditions. Many steel homes come with advanced insulation options, ensuring lower energy bills and greater comfort year-round. The cost to build a steel home typically falls between $70 and $120 per square foot, which includes the structure, insulation, and interior finishes. Factors such as design complexity, the quality of finishes, and additional customizations can affect the total price.
Win More Projects With Us
Steel Garages and Workshops
Steel garages and workshops provide a cost-effective and long-lasting solution for residential properties. Whether used for vehicle storage, as a workshop, or even a hobby space, these structures are known for their versatility and resistance to rust and wear. Prefabricated options can be easily customized with roll-up doors, windows, and shelving. Costs typically range from $30 to $60 per square foot, with price variations depending on the size, insulation needs, and additional features such as electrical wiring or ventilation systems.
Steel Barns
Steel barns are widely used in agricultural settings for storing equipment, housing livestock, or sheltering crops. Their low-maintenance requirements and resistance to fire, pests, and rot make them a popular choice among farmers and landowners. Unlike traditional wood barns, steel barns require less upkeep over time, saving money in the long run. Costs typically range from $20 to $50 per square foot, depending on factors like size, roofing materials, and any interior modifications, such as stalls, lofts, or climate control systems.
Commercial Steel Structure Costs
Steel Warehouses
Steel warehouses are an excellent choice for businesses needing large, open spaces to store goods, machinery, or inventory. These buildings are highly customizable, allowing for add-ons like mezzanine levels, loading docks, and specialized climate control systems. The straightforward design of steel warehouses also makes them faster to construct compared to traditional materials, reducing labor costs. Costs typically range from $40 to $100 per square foot, depending on the size, level of customization, and location-specific labor expenses.
Steel Office Buildings
Steel office buildings provide businesses with the flexibility to scale their operations while ensuring a durable and energy-efficient workspace. These buildings can be customized with various layouts, high-quality finishes, and advanced HVAC systems to meet the specific needs of a business. Steel office buildings also offer superior fire resistance and reduced maintenance costs compared to traditional wood or concrete structures. Construction costs generally range from $50 to $120 per square foot, with variations based on the interior design, size, and additional amenities such as elevators, lighting, and soundproofing.
Steel Retail Spaces
Steel retail spaces are designed to offer both durability and a customer-friendly environment. These structures are highly versatile, allowing businesses to tailor the interior and exterior designs to attract customers and suit their branding needs. Features such as large windows, energy-efficient lighting, and open floor plans can be easily incorporated into steel retail spaces. The cost of constructing steel retail spaces typically ranges from $50 to $100 per square foot, depending on the project’s size, location, and design complexity. Additional features like partition walls, display areas, and custom facades can further influence the price.
Steel Frame Construction Costs by Story Height
Single-Story Steel Structures
Single-story steel buildings are a popular choice due to their cost-effectiveness and speed of construction. They are often used for warehouses, retail stores, and small industrial facilities. These structures are relatively straightforward to design and build, requiring minimal structural reinforcements compared to multi-story buildings. The cost typically ranges from $100 to $220 per square foot, influenced by the building’s size, function, and the materials chosen. Additional costs may include features like insulation, HVAC systems, or custom exterior finishes.
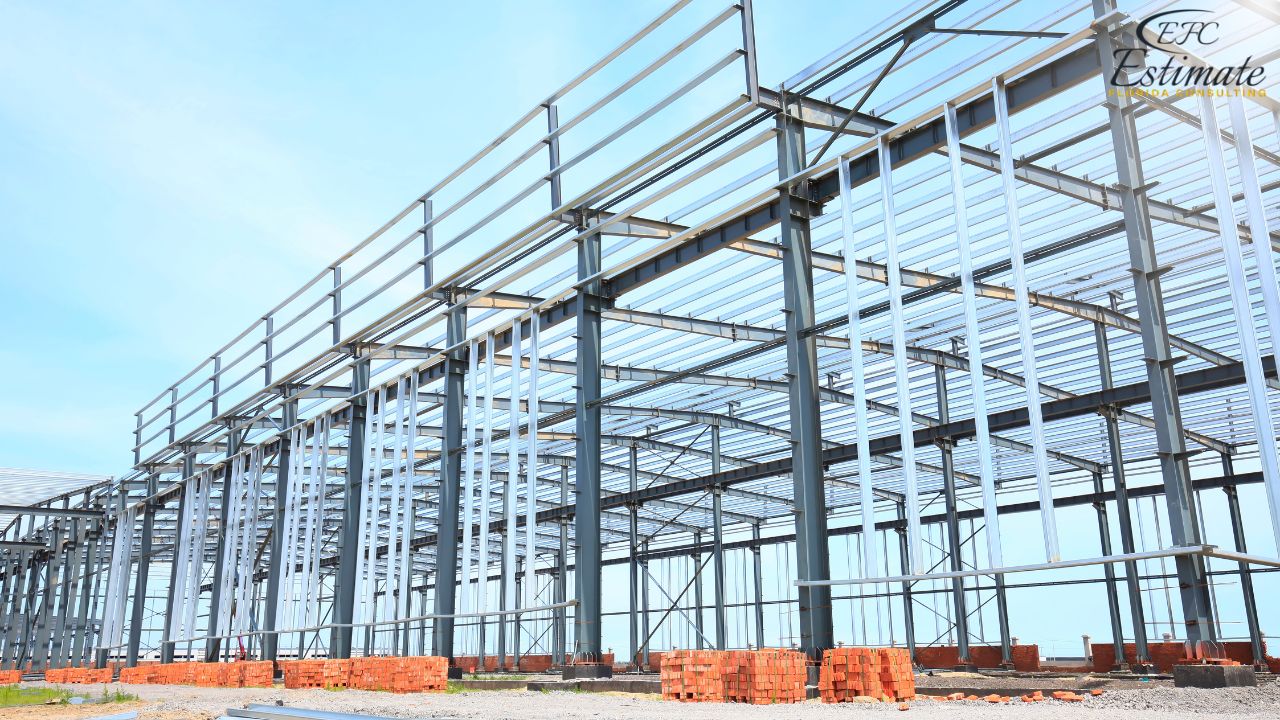
Despite their simplicity, single-story buildings can be customized to meet specific functional and aesthetic requirements, making them a versatile option for various industries.
Multi-Story Steel Structures
Multi-story steel buildings are essential for urban areas where space is limited and vertical construction is necessary. These structures are common for office buildings, hotels, and residential complexes. Unlike single-story buildings, multi-story projects involve advanced engineering to ensure stability, safety, and compliance with local building codes. For a 2-story steel building, costs range from $150 to $300 per square foot, but taller buildings can exceed $350 per square foot due to the need for stronger foundations, elevators, fireproofing, and advanced structural elements. The complexity of multi-story construction also extends the timeline, requiring skilled labor and precise coordination, which contributes to higher costs.
Factors Affecting Steel Structure Construction Costs
Location
The location of a construction project significantly impacts costs. In Florida, cities like Miami, Tampa, and Orlando tend to have higher material and labor costs due to greater demand and higher living expenses in urban areas. In contrast, rural regions or smaller cities may offer lower construction costs but could have limited access to specialized contractors or materials, which might cause delays or increased transportation costs. Additionally, local building codes and regulations can also affect the final price. For example, areas prone to hurricanes may require reinforced steel structures, which increase costs.
Design Complexity
The complexity of the building’s design plays a crucial role in determining costs. Buildings with intricate architectural elements, such as curved facades, custom steel framing, or unique layouts, demand more detailed engineering and construction work. This can increase overall costs by 10% to 30%, as these designs often require specialized labor and custom materials. Even small changes, like the addition of large windows, skylights, or decorative steel elements, can add to the project’s price due to additional structural considerations. Complex designs also extend project timelines, further increasing labor costs.
Material Choices
The quality and type of materials used in construction directly impact costs. Opting for high-grade steel can increase initial expenses but may provide better durability, corrosion resistance, and lower maintenance costs over time. Sustainable materials, such as recycled steel, are often preferred for eco-friendly projects, although they come at a premium. Beyond steel, additional materials like insulation, fireproof coatings, and exterior cladding also affect the overall budget. Choosing the right materials is a balancing act between upfront costs and long-term savings, as higher-quality materials can improve the building’s lifespan and reduce future repair needs.
Labor Costs
Labor costs for steel construction vary based on location, project size, and complexity. In Florida, rates range from $50 to $150 per hour, with urban areas generally having higher labor rates due to increased demand for skilled workers. The type of work also influences costs—basic assembly may require general laborers, while tasks like welding, fireproofing, or installing HVAC systems require specialized professionals. Labor shortages in some areas can further drive up costs, particularly for large or complex projects. Proper project planning and hiring experienced contractors can help manage labor expenses effectively.
How Steel Structure Cost Estimation Works?
Getting an accurate estimate for a steel structure involves multiple detailed steps, each critical for budgeting and planning:
- Project Consultation
The first step involves understanding the project’s purpose, size, and design preferences. This includes discussing the intended use of the building, such as a warehouse, office, or residential complex, and identifying any specific requirements like energy efficiency or advanced safety features. Clear communication during this stage ensures that the client’s vision aligns with the proposed design and budget. - Site Assessment
Evaluating the construction site is vital to identify potential challenges that could impact costs. Factors like soil conditions, accessibility, and proximity to suppliers play a significant role. For example, a site with poor soil may require additional foundation work, while a remote location might increase transportation costs for materials and labor. Proper site assessment helps avoid unexpected expenses during construction. - Detailed Cost Breakdown
This step involves creating an itemized list of all project costs, including materials, labor, equipment, permits, and utilities. Each component is carefully evaluated to ensure accuracy. For instance, the cost of high-grade steel, fireproof coatings, and HVAC systems are calculated separately. This level of detail helps clients understand where their money is being spent and allows for adjustments if needed. - Final Estimate
A comprehensive estimate is provided, which includes contingencies for unforeseen expenses such as weather delays or material shortages. This final figure gives clients a clear picture of the total project cost, helping them make informed decisions and plan their budget effectively.
Download Template For Steel Structure Project Breakdown
- Materials list updated to the zip code
- Fast delivery
- Data base of general contractors and sub-contractors
- Local estimators
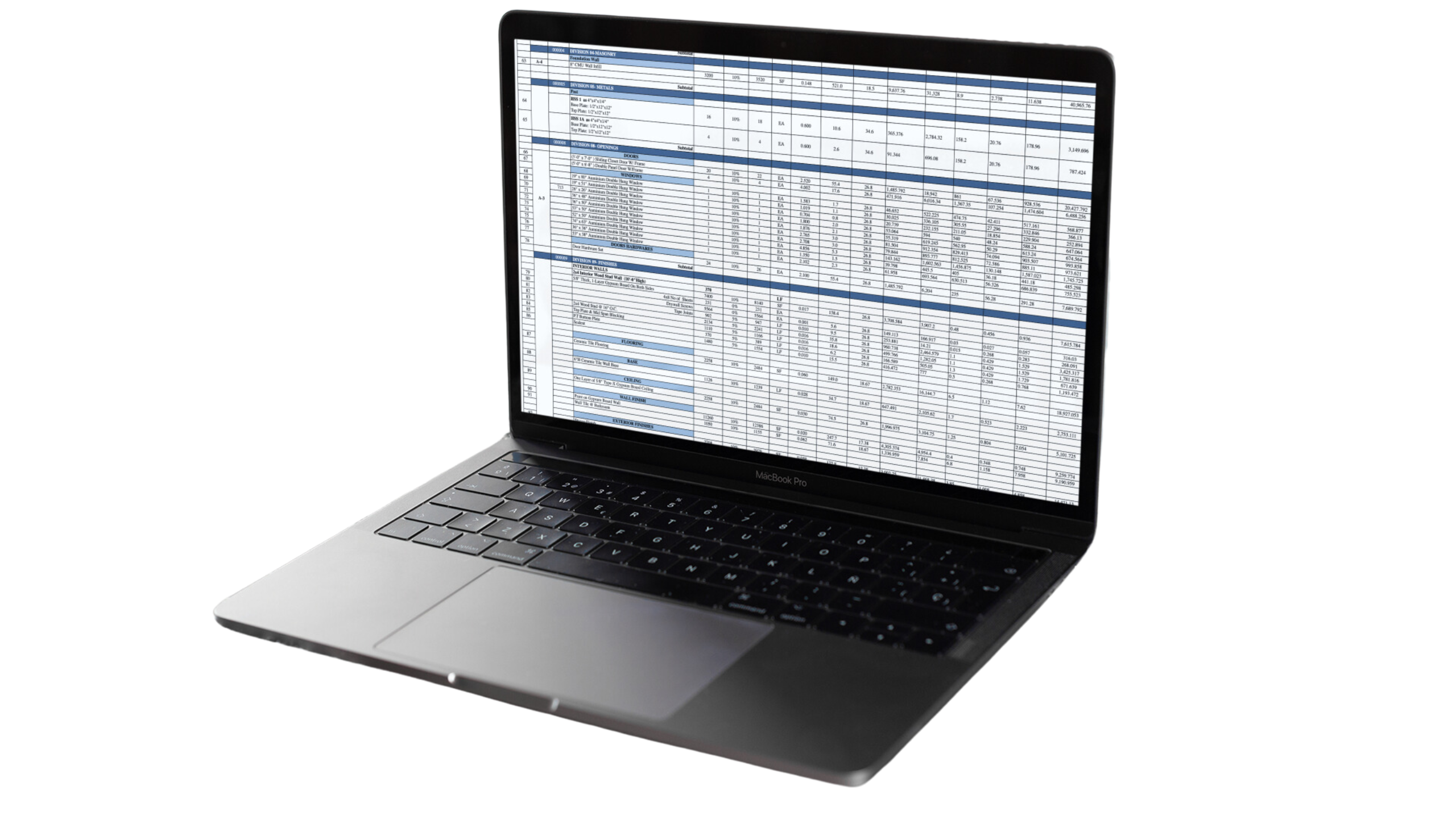
Why Accurate Steel Structure Cost Estimation Matters?
Accurate cost estimation is a cornerstone of successful construction projects. It provides several benefits that ensure efficiency and client satisfaction:
- Better Budget Management
A precise estimate helps avoid unexpected costs, ensuring that the project stays within financial limits. This is especially important for large-scale projects where even small deviations can lead to significant budget overruns. - Improved Project Planning
With a clear cost estimate, contractors can plan every aspect of the project, from material procurement to labor scheduling. This reduces delays and ensures that all necessary resources are available when needed. - Enhanced Communication
Detailed cost estimates build trust between contractors and clients by fostering transparency. Clients feel confident knowing exactly where their money is going and can make informed decisions about upgrades or changes to the project.
Conclusion
Steel structure cost estimation is a critical step in planning a successful construction project. From pre-engineered buildings to custom designs, understanding cost factors such as materials, labor, and location ensures informed decision-making and budget control. With prices ranging from $20 to $120 per square foot depending on the building type and complexity, a detailed estimate helps avoid surprises and optimize resource allocation. Accurate estimation not only streamlines planning but also fosters trust and transparency between contractors and clients, ensuring the project is completed on time and within budget while meeting all design and functionality requirements.
Frequently Asked Question
The cost of constructing a steel structure ranges from $20 to $50 per square foot for basic structures. With foundation and finishing, the cost typically increases to $70 to $120 per square foot, depending on the building type and specifications.
Larger buildings generally benefit from economies of scale, reducing the cost per square foot. For instance, a 1,000 sq. ft. building may cost $70,000–$120,000, while a 20,000 sq. ft. building may range from $1,000,000–$2,000,000.
Pre-engineered steel buildings cost between $20 and $40 per square foot, offering affordability and quick assembly. Custom steel-framed buildings cost $30 to $60 per square foot due to additional design and construction requirements.
Residential steel structures, including homes, cost between $70 and $120 per square foot. This price includes the frame, insulation, and basic finishes but may vary based on design complexity and customization.
Costs for commercial steel structures, like warehouses or retail spaces, range from $40 to $120 per square foot, influenced by customization, location, utilities, and additional features such as mezzanines or climate control systems.
- Steel frames: $10–$30 per square foot
- Roofing and cladding: $5–$15 per square foot
- Insulation: $2–$6 per square foot
- Utilities: $15,000–$100,000, depending on complexity
Insulation improves energy efficiency and occupant comfort by regulating indoor temperatures. Costs range from $2 to $6 per square foot, with options like fiberglass, spray foam, and rigid panels.
Labor costs in Florida range from $50 to $150 per hour, varying based on location and project complexity. Specialized tasks, like welding or installing HVAC systems, may cost more than basic assembly work.
Foundation costs range from $5,000 to $50,000, depending on soil conditions, structure size, and foundation type (slabs or piers). Complex foundations for larger structures may increase costs.
The process includes:
- Project Consultation: Understanding building needs and preferences.
- Site Assessment: Evaluating site conditions and accessibility.
- Detailed Cost Breakdown: Itemizing materials, labor, and other expenses.
- Final Estimate: Providing a comprehensive budget with contingencies.
Comprehensive Trade-Specific Estimates
At Estimate Florida Consulting, we offer detailed cost estimates across all major trades, ensuring no part of your project is overlooked. From the foundation to the finishing touches, our trade-specific estimates provide you with a complete and accurate breakdown of costs for any type of construction project.
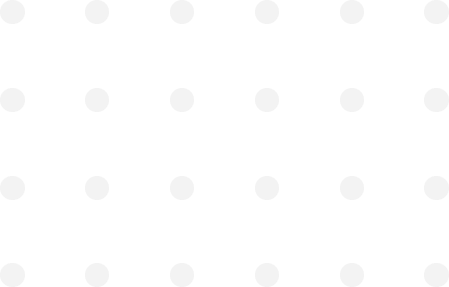
Testimonials
What Our Clients Say
We take pride in delivering accurate, timely, and reliable estimates that help contractors and builders win more projects. Our clients consistently praise our attention to detail, fast turnaround times, and the positive impact our estimates have on their businesses.
Estimate Florida Consulting has helped us win more bids with their fast and accurate estimates. We trust them for every project!
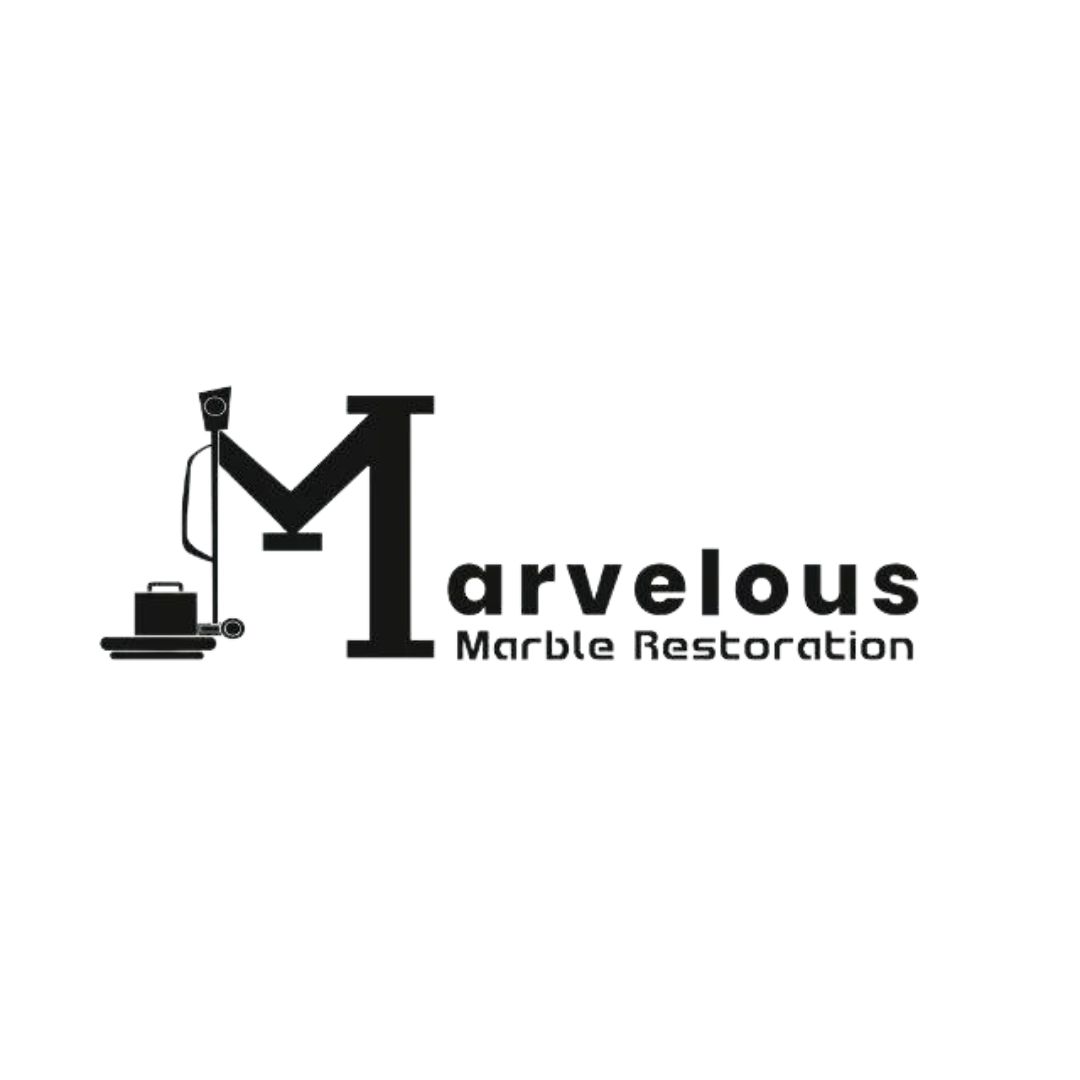
Steps to Follow
Our Simple Process to Get Your Estimate
01
Upload Plans
Submit your project plans, blueprints, or relevant documents through our online form or via email.
02
Receive Quotation
We’ll review your project details and send you a quote based on your scope and requirements.
03
Confirmation
Confirm the details and finalize any adjustments to ensure the estimate meets your project needs.
04
Get Estimate
Receive your detailed, trade-specific estimate within 1-2 business days, ready for your project execution.
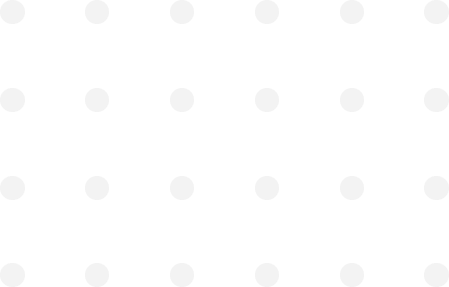