Steel Frame Building Cost Estimator
Estimating the cost of a steel frame building can be achieved through a reliable steel frame building cost estimator. The cost of constructing such a building can vary widely depending on several factors such as size, design complexity, location, and materials used. On average, you can expect to pay between $50 to $150 per square foot for a basic steel frame building. This cost typically includes the structural steel framework, but it does not cover additional expenses like foundation work, interior finishes, or exterior cladding.
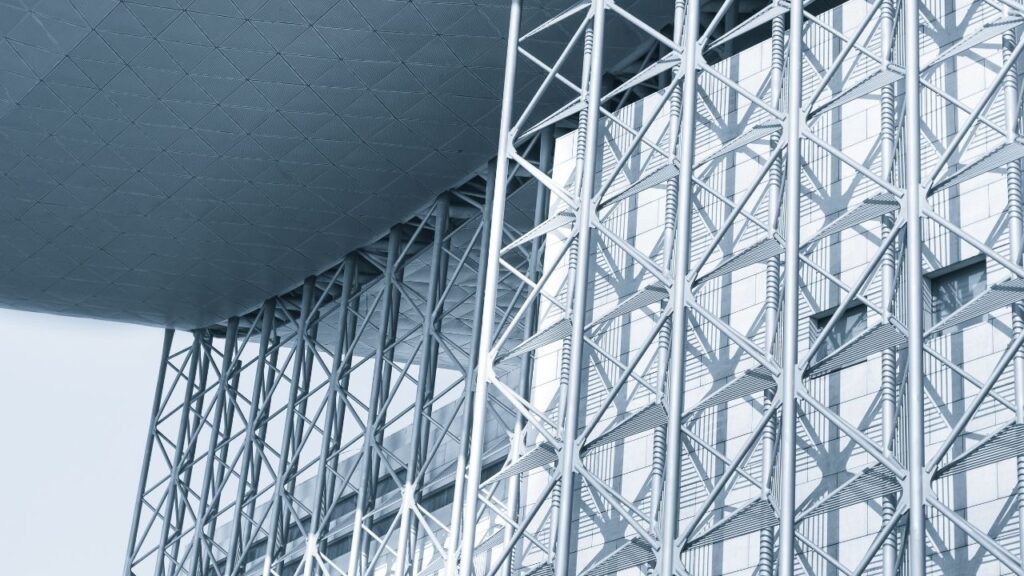
More intricate designs and specialized features may drive costs higher, while the overall cost may also be influenced by fluctuations in steel prices and labor rates in your specific area. To get an accurate estimate for your project, it’s advisable to consult with a local contractor or use a reputable steel frame building cost estimator. At Estimate Florida Consulting, we provide estimates for your project, ensuring you have the information you need to make informed decisions.
Are You Looking For?
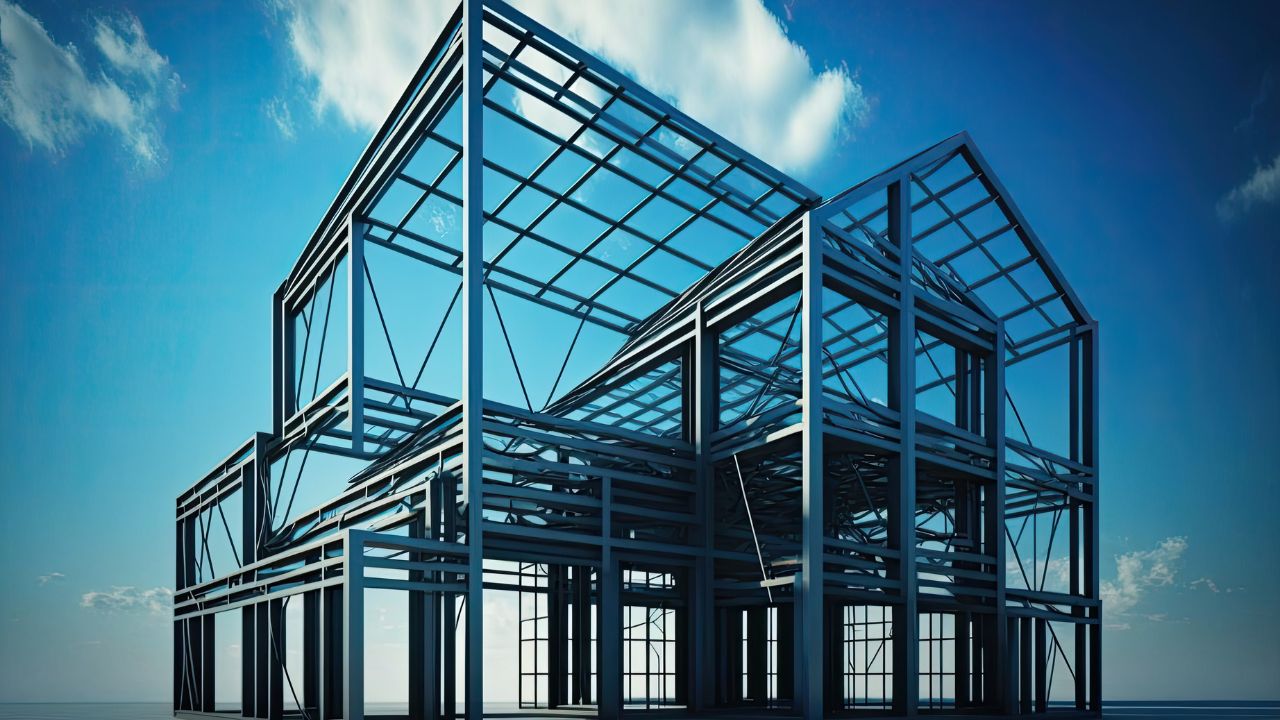
Make Informed Design Decisions Showcase Your Design Ideas
Get RenderingCall Us To Discuss More at 561-530-2845
Understanding Steel Frame Buildings
Steel frame buildings have gained widespread popularity for their exceptional attributes, making them a top choice in construction. These structures are crafted using steel columns, beams, and various components, serving diverse purposes such as industrial facilities, warehouses, and even residential homes.
The advantages of steel frame buildings are numerous and compelling:
Durability: Steel’s innate robustness and resilience make it an ideal material for structures that must endure harsh environmental conditions, providing long-term reliability and structural integrity.
Cost-Effectiveness: While the initial investment in steel frame construction may surpass that of traditional methods, the enduring cost savings, reduced maintenance, and extended lifespan of these buildings ultimately make them a financially savvy choice.
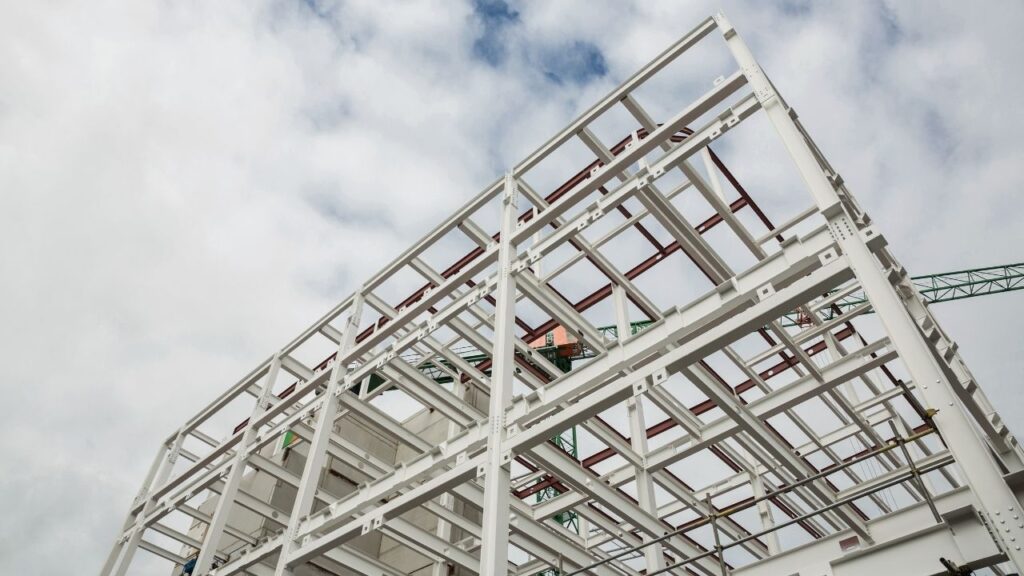
Quick Construction: The efficient assembly of steel structures significantly reduces construction timelines. This not only minimizes labor costs but also allows you to start using the facility sooner, enhancing your return on investment.
Flexibility: Steel’s strength and versatility enable the creation of open and adaptable floor plans. This adaptability makes steel frame buildings suitable for a wide range of applications, from vast industrial spaces to modern residential designs.
Sustainability: Steel is a recyclable material, and its reuse in construction contributes to sustainability. Steel frame buildings can be designed with energy-efficient features, further reducing their environmental impact.
Factors Influencing the Cost
The cost of building a steel frame structure can vary significantly based on several key factors. Let’s explore these factors in detail to gain a comprehensive understanding of how they impact the overall budget.
Size and Design:
The size and design of your steel frame building play a pivotal role in determining the total cost. Larger buildings with intricate or unique designs will naturally incur higher expenses. The complexity of the architectural design and the intended use of the building can significantly influence the budget. Customized features and specialized layouts can also add to the overall cost.
Location:
The geographical location of your construction site is another critical factor affecting costs. Building in areas with higher construction and labor costs, such as metropolitan regions, will naturally increase the overall expenses. Furthermore, local building codes and regulations can have a substantial impact on the cost and may necessitate specific features like seismic reinforcements, which can add to the project’s complexity and budget.
Material Quality:
The quality of steel and other construction materials used in your project can have a notable influence on the cost. While high-quality steel may have a higher upfront cost, it provides greater durability and longevity, reducing the need for frequent maintenance and repairs in the long run. Opting for top-grade materials can lead to substantial cost savings over the life of the building.
Labor Costs:
Labor costs represent a significant portion of any construction project. The availability of skilled labor in your area and the complexity of the project can impact labor expenses. Efficient project management, streamlined construction processes, and skilled labor can help control labor costs and enhance project efficiency.
Site-Specific Conditions:
Site-specific conditions, such as soil quality and topography, can also affect the cost of a steel frame building. Sites with challenging terrain or soil conditions may require additional foundation work or site preparation, leading to increased project costs.
Market Conditions:
Fluctuations in the construction industry and steel prices can impact the overall cost of your project. Economic conditions, supply and demand dynamics, and market trends may influence the prices of materials and labor during the construction process.
Project Timeline:
The duration of the construction project can affect costs as well. Delays in construction can lead to increased labor and material expenses. Efficient project scheduling and management are essential to control these costs.
Estimated Cost Breakdown for a Typical Steel Frame Building Project
Cost Category | Estimated Cost Range |
Site Preparation | $5,000 – $15,000 |
Foundation | $10,000 – $30,000 |
Structural Steel | $20,000 – $60,000 |
Roofing and Cladding | $15,000 – $45,000 |
Interior Finishes | $10,000 – $30,000 |
Plumbing and Electrical | $5,000 – $20,000 |
HVAC System | $7,000 – $25,000 |
Windows and Doors | $5,000 – $15,000 |
Miscellaneous Costs | $5,000 – $20,000 |
Contingency (10%) | $7,000 – $20,000 |
Total Estimated Cost | $89,000 – $265,000 |
Cost Estimation Methods
Accurately estimating the cost of a steel frame building is a crucial aspect of the construction planning process. Various methods can be employed, but two common approaches are:
Square Foot Cost:
This method involves calculating the cost per square foot of the building’s total area. While it provides a quick and straightforward estimate, it may not fully account for variations in design complexity and other specific project factors. Therefore, it’s often used as a preliminary estimate to gauge overall project feasibility.
Detailed Cost Estimation:
A more comprehensive approach involves conducting a detailed cost estimation. This method takes into account various aspects, including the specific design, materials, labor, and site conditions. Detailed cost estimation provides a more accurate assessment of project expenses, making it invaluable for precise budgeting and financial planning.
Here’s a table outlining approximate Steel Frame Building Costs per square foot in the United States:
Building Type | Cost per Square Foot ($) |
Warehouse | $80 – $120 |
Office Building | $150 – $250 |
Retail Store | $100 – $150 |
Industrial Facility | $80 – $120 |
Apartment Building | $150 – $250 |
Gymnasium | $100 – $150 |
School Building | $120 – $200 |
Healthcare Facility | $200 – $300 |
Hotel | $150 – $250 |
Parking Garage | $30 – $50 |
These costs are approximate and can vary significantly based on location, building size, design complexity, materials used, labor costs, and other factors.
The Cost Estimation Process
Estimating the cost of a steel frame building in Florida is a systematic and multifaceted procedure, critical for effective project planning and budgeting. Here’s a detailed breakdown of the steps involved:
Preliminary Cost Assessment:
The process commences with a preliminary cost assessment. This initial step involves creating a rough estimate based on the key parameters of your project, including the size, design, and location. This provides a foundational figure for further, more detailed cost analysis.
Detailed Quantity Takeoff:
A crucial phase in the estimation process, the detailed quantity takeoff, involves calculating the precise quantities of materials, labor, and other resources required for the project. This meticulous approach ensures that the costs are pinpointed accurately, leaving little room for unexpected surprises during the construction process.
Material and Labor Costs Research:
Staying informed about current market prices for key materials like steel, cladding, insulation, and labor is essential. Construction costs can be subject to fluctuations, so regular updates are crucial to ensure your estimates remain current and reliable.
Overhead and Contingency:
Estimating the cost of a steel frame building also requires factoring in overhead expenses. This includes costs associated with equipment rental, insurance, and any administrative expenses. Equally important is the establishment of a contingency fund to account for unexpected or unforeseen expenses that may arise during the construction process. An adequate contingency fund ensures that the project remains on track, even in the face of unforeseen challenges.
Professional Estimation Software:
In the modern construction industry, the use of specialized construction estimation software has become indispensable. These tools are designed to streamline the estimation process, minimize errors, and enhance accuracy. Professional estimation software can also provide valuable insights and cost breakdowns to support effective decision-making throughout the project.
Steel Frame Building Types
Steel frame buildings offer a diverse range of types, each characterized by unique features and cost considerations. Understanding these categories is essential for selecting the right building type to meet your specific needs. Here are a few common steel frame building categories:
Residential Steel Homes:
Residential steel homes are gaining popularity for their exceptional energy efficiency and modern aesthetics. The cost of such homes can vary significantly based on factors like size, design complexity, and interior finishes. While initial costs may be higher, long-term energy savings and durability make them a compelling investment.
Commercial Buildings:
Steel frame construction is a prevalent choice for commercial spaces. The cost of commercial steel buildings is influenced by various factors, including the building’s intended purpose, size, and interior requirements. Customizations for office spaces, retail establishments, or mixed-use developments can impact the overall project budget.
Industrial Facilities:
Large industrial structures often utilize steel frames for their exceptional durability and ability to withstand heavy loads. The cost of industrial steel buildings is shaped by factors such as size, specialized equipment needs, safety regulations compliance, and site-specific requirements. These buildings are designed to provide efficient, safe, and robust spaces for manufacturing, warehousing, and other industrial operations.
Agricultural Steel Structures:
Steel frames are a popular choice for agricultural buildings like barns and storage facilities. Cost considerations include size, the need for specialized features like ventilation or insulation, and any unique requirements for the storage or handling of agricultural products and equipment.
Institutional Buildings:
Schools, healthcare facilities, and other institutional buildings often employ steel frame construction for its strength and flexibility. Costs can vary based on the building’s size, design features, and the specific needs of the institution.
Recreational and Sports Facilities:
Steel frame construction is well-suited for indoor sports complexes, gymnasiums, and recreational facilities. The cost may be influenced by the building’s size, specialized features, and the need for open, column-free spaces.
Aviation Hangars:
Steel is a favored material for constructing aviation hangars due to its ability to span large, open areas. The cost of aviation hangars can fluctuate based on size, design specifications, and any additional requirements for aircraft maintenance or storage.
Benefits of Steel Frame Buildings
Now that we’ve delved into the factors influencing steel frame building costs and various estimation methods, it’s essential to recognize the myriad benefits that make steel frame construction an attractive choice for a wide range of applications:
Sustainability: Steel is renowned for its sustainability. It is a highly recyclable material, making it an eco-friendly choice for environmentally conscious projects. The ability to reuse steel reduces the overall environmental impact of construction, contributing to a greener future.
Energy Efficiency: Steel frame buildings can be designed to incorporate advanced insulation materials and energy-efficient systems. This not only enhances comfort for occupants but also leads to substantial long-term savings on operational costs, making them a wise financial investment.
Minimal Maintenance: Steel structures require significantly less maintenance compared to traditional building materials like wood. Steel is resistant to issues such as rot and warping, ensuring that the structure remains durable and appealing over time. Reduced maintenance demands translate to lower ongoing costs.
Fire Resistance: Steel is inherently fire-resistant, providing an added layer of safety for building occupants. In the event of a fire, steel maintains its structural integrity for a longer period, offering more time for evacuation and firefighting efforts.
Customization: Steel frame construction offers endless design possibilities. Its inherent strength and flexibility allow for diverse architectural designs and versatile floor plans. This enables you to create a structure tailored to your specific needs and preferences, whether it’s a cutting-edge modern office space or a unique residential home.
Longevity: Steel structures have a notably longer lifespan compared to many other building materials. Their resistance to weathering, corrosion, and other environmental factors ensures that your investment endures for decades. This longevity is not only a testament to their durability but also a testament to their value for the long term.
Quick Construction: Steel frame buildings can be erected faster than traditional buildings. The efficient construction process reduces labor costs and project timelines, allowing you to start utilizing the facility sooner and realizing the benefits of your investment.
Conclusion
Estimating the cost of a steel frame building is a multifaceted process that involves considering numerous factors, including size, design, location, materials, labor, and market conditions. Steel frame buildings offer a wide range of advantages, such as durability, cost-effectiveness, quick construction, flexibility, and sustainability. The cost breakdown for a typical steel frame building project shows the various expense categories, and using accurate cost estimation methods is essential for effective budgeting. Steel frame construction is versatile, suitable for various building types, and offers long-term benefits such as sustainability, energy efficiency, minimal maintenance, fire resistance, customization, and longevity. When considering a steel frame building project, a reliable cost estimator and thorough research can help you make informed decisions and ensure a successful construction endeavor. Whether for residential, commercial, industrial, or institutional purposes, steel frame buildings continue to be a smart and sustainable choice in the world of construction.
FAQs
The cost of a steel frame building is influenced by factors such as size, design complexity, location, material quality, labor costs, site-specific conditions, and market conditions. These variables can significantly impact the overall project budget.
The cost estimation process involves several steps, including preliminary cost assessment, detailed quantity takeoff, research on material and labor costs, factoring in overhead and contingency, and using professional estimation software. This systematic approach ensures a more accurate cost estimate.
On average, you can expect to pay between $50 to $150 per square foot for a basic steel frame building. This estimate typically covers the structural steel framework but does not include additional expenses like foundation work, interior finishes, or exterior cladding.
Steel frame buildings offer numerous benefits, including sustainability due to steel’s recyclability, energy efficiency, minimal maintenance requirements, fire resistance, customization options, longevity, and quick construction. These advantages make steel frame construction a compelling choice for a wide range of building projects.
Steel frame buildings come in various types, including residential steel homes, commercial buildings, industrial facilities, agricultural steel structures, institutional buildings, recreational and sports facilities, and aviation hangars. Each type has its unique features and cost considerations.
To ensure an accurate cost estimate, it’s advisable to consult with a local contractor who has experience in steel frame construction. Additionally, utilizing specialized construction estimation software and conducting detailed quantity takeoffs can enhance the accuracy of your estimate.
Yes, steel frame construction is considered eco-friendly due to the recyclability of steel. It can be reused, reducing the environmental impact of construction. Additionally, steel frame buildings can be designed with energy-efficient features to further reduce their environmental footprint.
Process To Get Steel Frame Building Cost Estimate Report
Here I am going to share some steps to get your steel frame building cost estimate report.
-
You need to send your plan to us.
You can send us your plan on info@estimatorflorida.com
-
You receive a quote for your project.
Before starting your project, we send you a quote for your service. That quote will have detailed information about your project. Here you will get information about the size, difficulty, complexity and bid date when determining pricing.
-
Get Estimate Report
Our team will takeoff and estimate your project. When we deliver you’ll receive a PDF and an Excel file of your estimate. We can also offer construction lead generation services for the jobs you’d like to pursue further.
Google Reviews
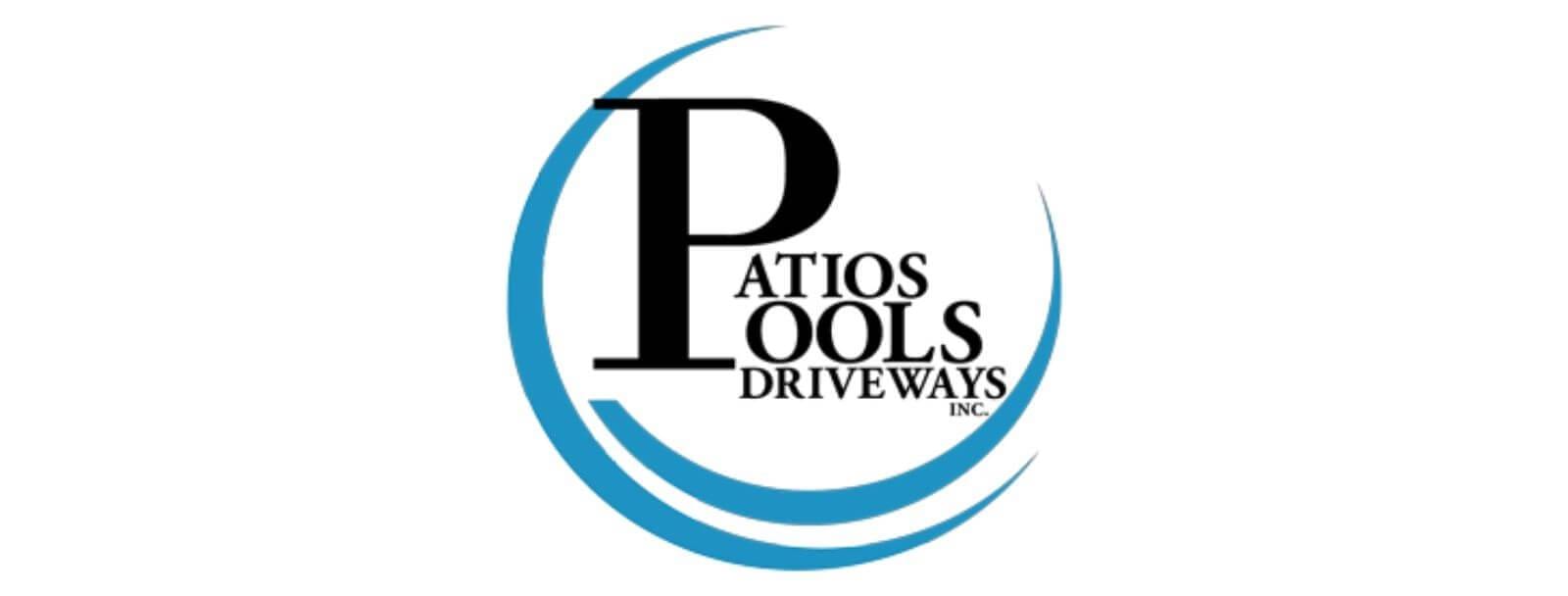
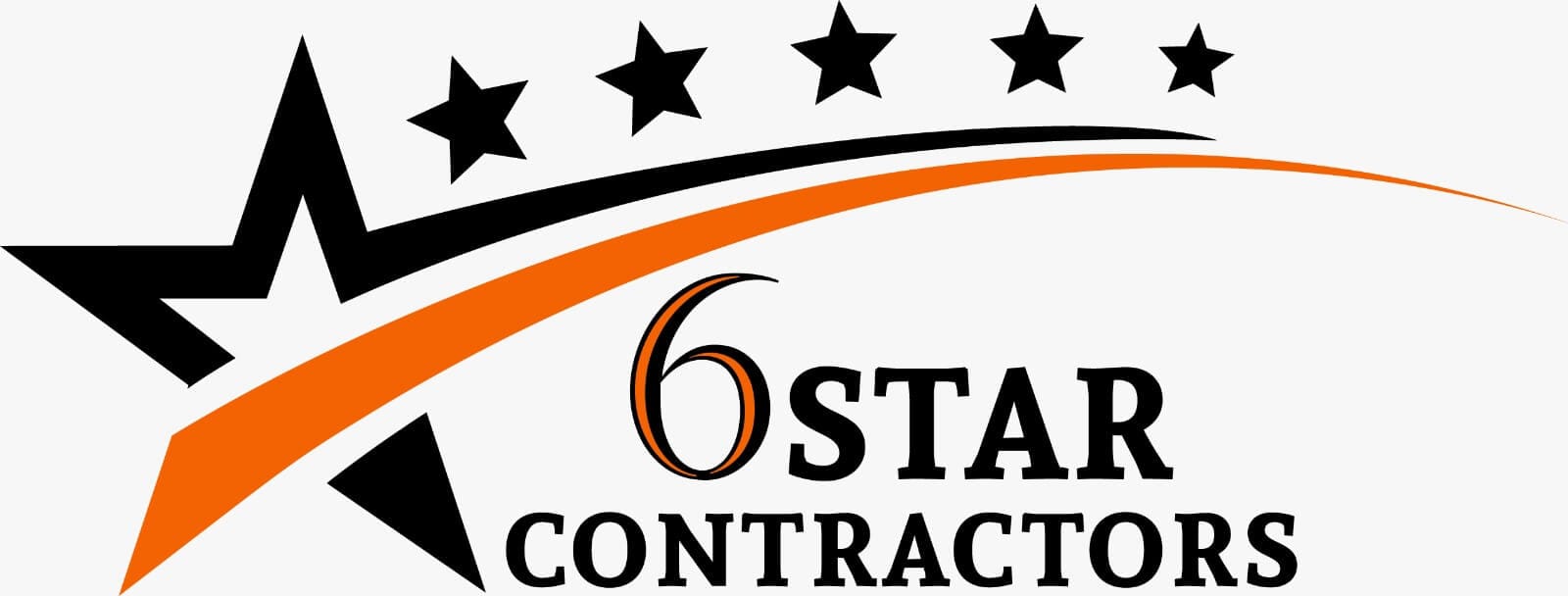
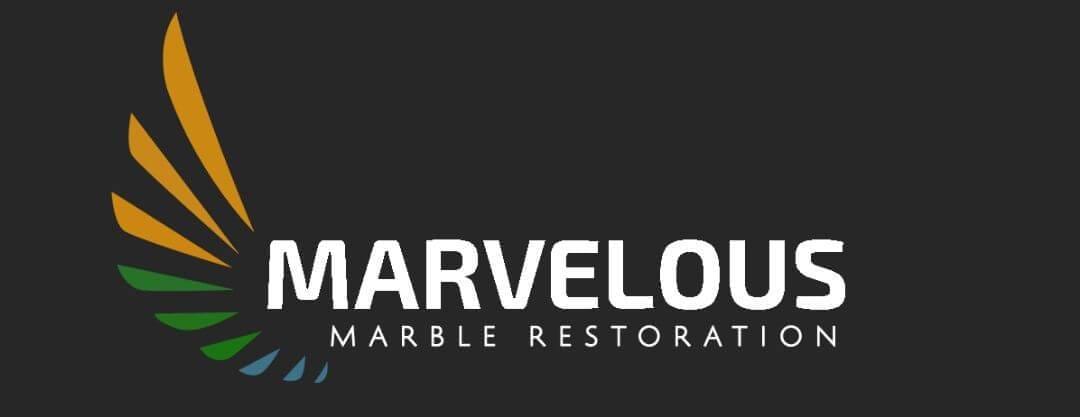