Steam Systems Cost Estimator
Steam systems are essential in various industrial, commercial, and even some residential applications, providing heat, power, and energy efficiency. Whether you’re installing a new steam system or upgrading an existing one, understanding the costs involved is crucial for effective budgeting and planning. Estimate Florida Consulting provides expert cost estimator services to help you plan and execute your steam system installation or replacement project with precision, ensuring that your project stays within budget while meeting all performance and safety requirements.
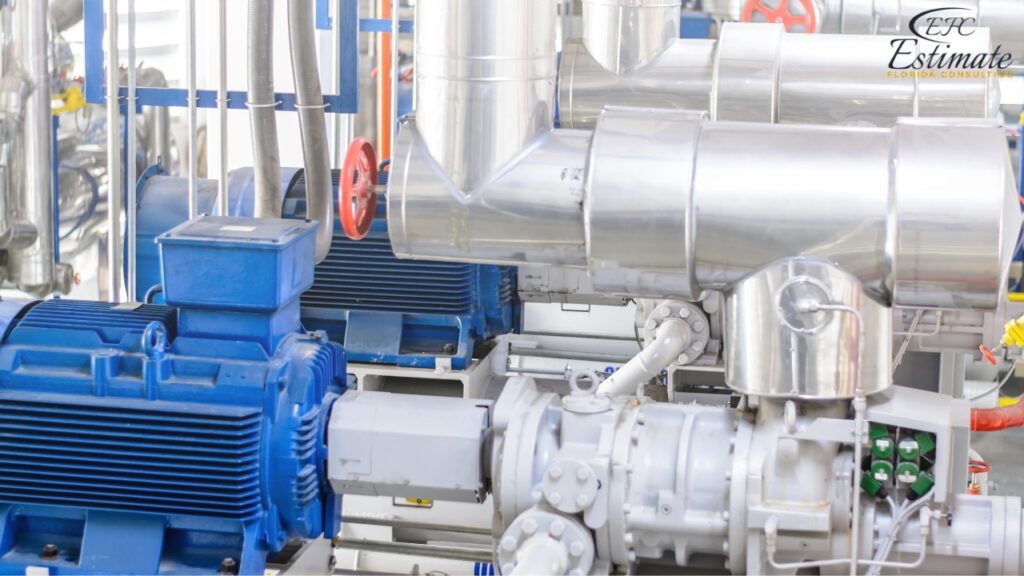
Steam System Components and Their Costs
A steam system comprises several components, each with its own cost considerations. The overall cost of a steam system depends on the size, complexity, and specific requirements of the installation. Below is a breakdown of the primary components and their associated costs.
Steam System Component | Price per Unit (Material Only) | Price per Unit (Installed) |
Boiler | $3,900 – $39,000 | $7,800 – $58,500 |
Piping (Steel or Copper) | $5 – $15 per Linear Foot | $15 – $39 per Linear Foot |
Steam Traps | $150 – $600 | $300 – $780 |
Pressure-Reducing Valves | $250 – $1,500 | $500 – $2,250 |
Control Systems | $1,500 – $9,000 | $3,000 – $13,500 |
Condensate Return Pumps | $900 – $3,600 | $1,800 – $5,400 |
Heat Exchangers | $2,500 – $10,500 | $5,000 – $15,750 |
Insulation (for Pipes) | $1.30 – $6.50 per Linear Foot | $3.90 – $13 per Linear Foot |
Boiler
The boiler is the heart of the steam system, responsible for generating steam by heating water. The cost of a boiler varies significantly based on its size, type, and capacity. For industrial or commercial applications, the cost of a boiler typically ranges from $3,900 to $39,000 for the material, with installation costs ranging from $7,800 to $58,500. High-capacity boilers designed for large-scale operations may cost even more. Factors such as fuel type (natural gas, oil, electric), efficiency ratings, and additional features like automation or monitoring systems will also affect the overall cost.
Piping (Steel or Copper)
Piping is essential for transporting steam from the boiler to various points of use within the system. The choice of material, whether steel or copper, and the length of the piping required significantly impact the cost. Piping costs typically range from $5 to $15 per linear foot for the material, with installation costs ranging from $15 to $39 per linear foot. Steel is commonly used for high-pressure steam systems due to its strength and durability, while copper may be used in lower-pressure applications. The cost also depends on the complexity of the piping layout, including the need for bends, joints, and supports.
Steam Traps
Steam traps are critical components that remove condensate (water) from the steam system without letting steam escape. The cost of steam traps typically ranges from $150 to $600 per unit, with installation costs ranging from $300 to $780 per unit. The type of steam trap (thermodynamic, thermostatic, or mechanical) and its application within the system will influence the cost. Properly functioning steam traps are essential for maintaining efficiency and preventing water hammer, a potentially damaging condition caused by condensate buildup.
Pressure-Reducing Valves
Pressure-reducing valves (PRVs) are used to lower steam pressure to safe and usable levels in various parts of the system. The cost of PRVs typically ranges from $250 to $1,500 per unit, with installation costs ranging from $500 to $2,250 per unit. These valves are vital for ensuring that the steam pressure is appropriate for different applications, such as heating or process operations. The size and specifications of the PRV, as well as the pressure reduction required, will affect the overall cost.
Control Systems
Control systems manage the operation of the steam system, including temperature, pressure, and flow rate. The cost of control systems typically ranges from $1,500 to $9,000 for the material, with installation costs ranging from $3,000 to $13,500. Modern control systems often include digital interfaces, remote monitoring, and automated adjustments to optimize efficiency and safety. The complexity of the control system, the level of automation, and the integration with other building management systems will influence the cost.
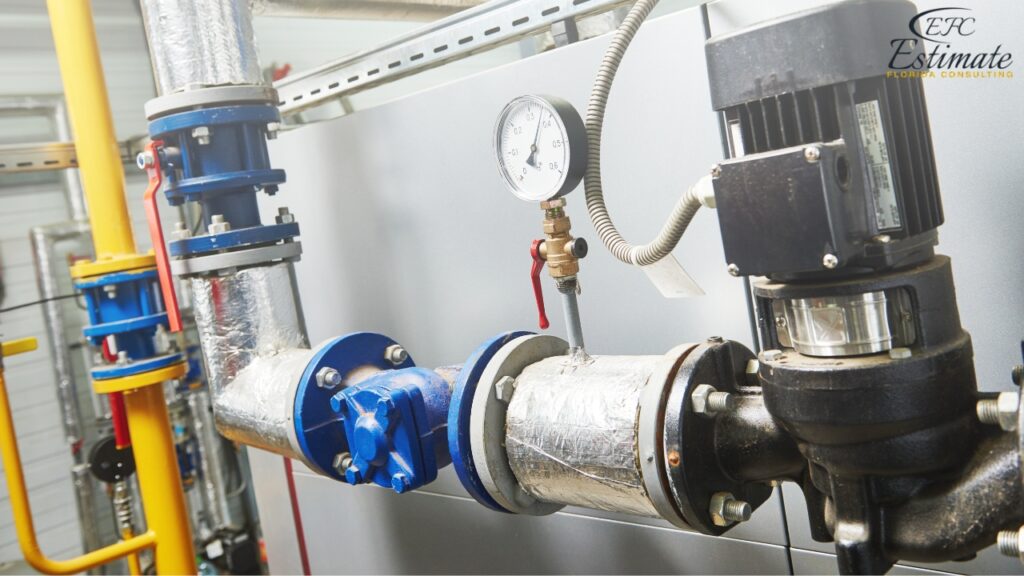
Condensate Return Pumps
Condensate return pumps are used to collect and return condensate back to the boiler for reheating, improving system efficiency and reducing water and energy waste. The cost of condensate return pumps typically ranges from $900 to $3,600 per unit, with installation costs ranging from $1,800 to $5,400 per unit. The capacity and design of the pump, as well as the distance between the point of condensate collection and the boiler, will affect the cost. A well-designed condensate return system can significantly lower operating costs by recycling water and heat energy.
Heat Exchangers
Heat exchangers transfer heat from the steam to another fluid, such as water or air, for various heating or process applications. The cost of heat exchangers typically ranges from $2,500 to $10,500 for the material, with installation costs ranging from $5,000 to $15,750. The type of heat exchanger (shell and tube, plate, or finned tube), its size, and its efficiency will influence the overall cost. Heat exchangers are crucial for applications such as space heating, domestic hot water generation, and industrial processes.
Insulation (for Pipes)
Insulating steam pipes is essential to minimize heat loss, improve system efficiency, and protect personnel from high surface temperatures. The cost of insulation typically ranges from $1.30 to $6.50 per linear foot for the material, with installation costs ranging from $3.90 to $13 per linear foot. The type of insulation material (fiberglass, foam, or mineral wool), the thickness required, and the operating temperature of the system will determine the cost. Proper insulation not only conserves energy but also reduces the risk of pipe corrosion and extends the lifespan of the steam system.
Steam System Cost by Project Type
The overall cost of a steam system is influenced by the specific project type, such as whether you’re installing a new system, upgrading existing components, or performing routine maintenance. Each project type presents unique challenges and cost considerations that must be taken into account.
Project Type | Cost Range |
New Steam System Installation | $50,000 – $300,000 |
System Upgrade (Partial) | $10,000 – $75,000 |
System Retrofit (Full) | $30,000 – $150,000 |
Routine Maintenance and Repairs | $2,000 – $15,000 per year |
Energy Efficiency Improvements | $15,000 – $100,000 |
New Steam System Installation
Installing a new steam system is a significant investment, with costs typically ranging from $50,000 to $300,000 depending on the size, complexity, and specific requirements of the system. New installations involve the design, procurement, and installation of all components, including boilers, piping, steam traps, control systems, and insulation. The choice of materials, the level of automation, and the integration with existing infrastructure will also influence the overall cost. New installations are often required in industrial facilities, commercial buildings, or large residential properties where steam is used for heating or process operations.
Steam System Installation Video
Steam Boiler Installation
Boiler System Installation
Full Boiler Installation
System Upgrade (Partial)
Upgrading specific components of an existing steam system, such as replacing old steam traps, installing new control systems, or adding insulation, typically costs between $10,000 and $75,000. Partial upgrades are often undertaken to improve system efficiency, extend the life of the system, or comply with new regulations. The cost will depend on the scope of the upgrade, the number of components involved, and the complexity of the installation. Partial upgrades can be a cost-effective way to enhance system performance without the need for a complete system overhaul.
System Retrofit (Full)
Retrofitting an existing steam system to improve efficiency, reduce emissions, or modernize outdated components typically costs between $30,000 and $150,000. A full retrofit may involve replacing the boiler, upgrading the control system, and installing new piping, steam traps, and heat exchangers. Retrofitting is often done in older buildings or industrial facilities where the existing system is still operational but requires significant updates to meet modern standards or achieve desired energy savings. The cost will vary depending on the extent of the retrofit, the condition of the existing system, and the desired improvements.
Routine Maintenance and Repairs
Regular maintenance and repairs are essential to ensure the safe and efficient operation of a steam system. The cost of routine maintenance typically ranges from $2,000 to $15,000 per year, depending on the size of the system, the frequency of maintenance, and the condition of the components. Maintenance activities may include inspecting and cleaning the boiler, checking and replacing steam traps, testing safety valves, and monitoring control systems. Preventive maintenance helps to identify and address potential issues before they lead to costly breakdowns or system failures.
Energy Efficiency Improvements
Implementing energy efficiency improvements in a steam system can lead to significant cost savings over time. These improvements may include upgrading insulation, installing variable frequency drives (VFDs) on pumps, optimizing control systems, or retrofitting the boiler with advanced combustion controls. The cost of energy efficiency improvements typically ranges from $15,000 to $100,000, depending on the scope of the project and the expected energy savings. While the initial investment may be substantial, the long-term benefits in terms of reduced energy consumption, lower operating costs, and improved system performance can be considerable.
Steam System Costs by Project Scope and Application
Here’s a breakdown of estimated steam system costs by application, providing you with a clear understanding of how different project types impact overall costs:
Application | Estimated Steam System Cost Range | Total Cost Range |
Industrial Steam System | $50,000 – $500,000 | $50,000 – $1,000,000+ (depending on size and complexity) |
Commercial Steam System | $20,000 – $150,000 | $20,000 – $300,000+ (depending on size and complexity) |
Residential Steam System | $10,000 – $30,000 | $10,000 – $50,000+ (depending on size and complexity) |
Steam System Upgrades | $5,000 – $100,000 | $5,000 – $200,000+ (depending on scope and complexity) |
Industrial Steam System Costs
Industrial steam systems are often large-scale and highly complex, designed to meet the demands of manufacturing processes, power generation, and other industrial operations. The estimated cost range for an industrial steam system is between $50,000 and $500,000. However, depending on the size and complexity of the system, the total cost can exceed $1,000,000. This includes the cost of specialized equipment, extensive piping networks, and high-capacity boilers, as well as the labor required for installation and testing.
Commercial Steam System Costs
Commercial steam systems are typically used in facilities such as hospitals, hotels, and office buildings. These systems are smaller than industrial systems but still require significant investment. The estimated cost range for a commercial steam system is between $20,000 and $150,000, with the total cost potentially reaching $300,000 or more, depending on the system’s size and complexity. Costs in this range account for the necessary steam generation and distribution equipment, installation, and any necessary compliance with local regulations.
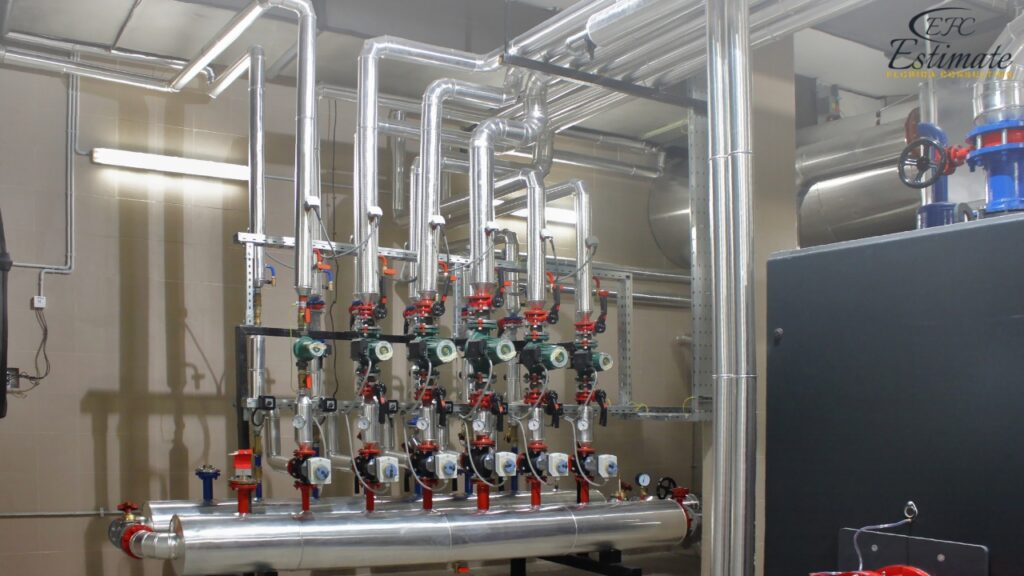
Residential Steam System Costs
Residential steam systems are much smaller and simpler compared to industrial and commercial systems, often used for heating purposes in homes. The estimated cost for a residential steam system ranges from $10,000 to $30,000. Depending on the home’s size and the complexity of the system, total costs can go up to $50,000 or more. These costs include the boiler, radiators, and installation work, as well as any necessary modifications to existing home infrastructure.
Steam System Upgrades
Upgrading an existing steam system, whether in an industrial, commercial, or residential setting, involves modernizing outdated components, improving efficiency, or expanding the system’s capacity. The estimated cost for steam system upgrades ranges from $5,000 to $100,000. Depending on the scope and complexity of the upgrade, total costs can exceed $200,000. This may include replacing old boilers, installing advanced control systems, or adding new steam lines to accommodate increased demand.
Factors Influencing Steam System Costs
The cost of a steam system can vary widely depending on several critical factors, including the type of boiler selected, the capacity of the system, the complexity of the installation, and additional expenses such as maintenance, compliance with regulations, and potential system upgrades. Understanding these factors is essential for accurately estimating the total cost of your project and making informed decisions that align with your budget. Each of these elements plays a significant role in determining the overall expense, and careful consideration of these factors can help optimize your investment in a steam system.
Type of Steam Boiler
The type of steam boiler you choose is one of the most significant factors affecting the overall cost of your steam system. Different types of boilers offer varying levels of efficiency, capacity, and suitability for specific applications, all of which contribute to the cost structure of the system. Choosing the right boiler type for your needs is crucial for achieving optimal performance and cost-effectiveness.
Type of Steam Boiler | Average Cost Range |
Fire-Tube Boiler | $26,000 – $260,000 |
Water-Tube Boiler | $65,000 – $650,000 |
Electric Boiler | $13,000 – $195,000 |
Fire-Tube Boiler
Fire-tube boilers are among the most common types of steam boilers, particularly in smaller industrial and commercial applications. These boilers are generally more affordable, with costs ranging from $26,000 to $260,000 depending on the capacity and specifications. Fire-tube boilers are known for their straightforward operation and relatively simple maintenance requirements, making them a popular choice for facilities that need reliable steam generation without the complexity of larger systems. Their compact design and ease of installation also make them suitable for smaller spaces and less demanding applications.
Water-Tube Boiler
Water-tube boilers are typically used in larger industrial applications where higher pressure and capacity are required. These boilers are more complex and can cost between $65,000 and $650,000, depending on the size and configuration. Water-tube boilers offer higher efficiency and can handle more demanding operations, such as high-pressure steam generation for power plants or large manufacturing facilities. However, they also require more specialized maintenance and operation, which can contribute to higher long-term costs. The increased efficiency and capacity of water-tube boilers make them an excellent choice for large-scale operations where performance and reliability are paramount.
Electric Boiler
Electric boilers are often used in smaller applications or in situations where fuel combustion is not feasible or desired. These boilers are generally more compact and have lower upfront costs, ranging from $13,000 to $195,000. However, operating costs can be higher due to electricity prices, and they may not be suitable for large-scale industrial applications where high steam capacity is required. Despite these limitations, electric boilers offer several advantages, including zero emissions, quiet operation, and the ability to operate in environments where traditional boilers might be restricted due to regulatory or environmental concerns.
System Capacity
The capacity of your steam system, typically measured in pounds per hour (PPH) or British Thermal Units (BTUs), will have a significant impact on the overall cost. Larger systems capable of producing more steam require bigger boilers, more extensive piping, and larger auxiliary equipment, all of which contribute to higher costs. Accurately sizing your steam system is essential to ensure that it meets both current and future operational demands without incurring unnecessary expenses.
System Capacity | Cost Range |
Up to 10,000 PPH | $26,000 – $130,000 |
10,000 – 50,000 PPH | $130,000 – $390,000 |
50,000 – 100,000 PPH | $390,000 – $780,000 |
Over 100,000 PPH | $780,000 – $1,300,000+ |
When sizing your steam system, it’s crucial to consider both your current needs and potential future expansion. Installing a system with adequate capacity ensures that your facility can meet its steam demands without overloading the system, which can lead to inefficiencies and increased wear and tear. Additionally, a well-sized system can help avoid the need for costly upgrades or replacements as your operational needs evolve, providing long-term value and reliability.
Download Template For Machanical Project Breakdown
- Materials list updated to the zip code
- Fast delivery
- Data base of general contractors and sub-contractors
- Local estimators
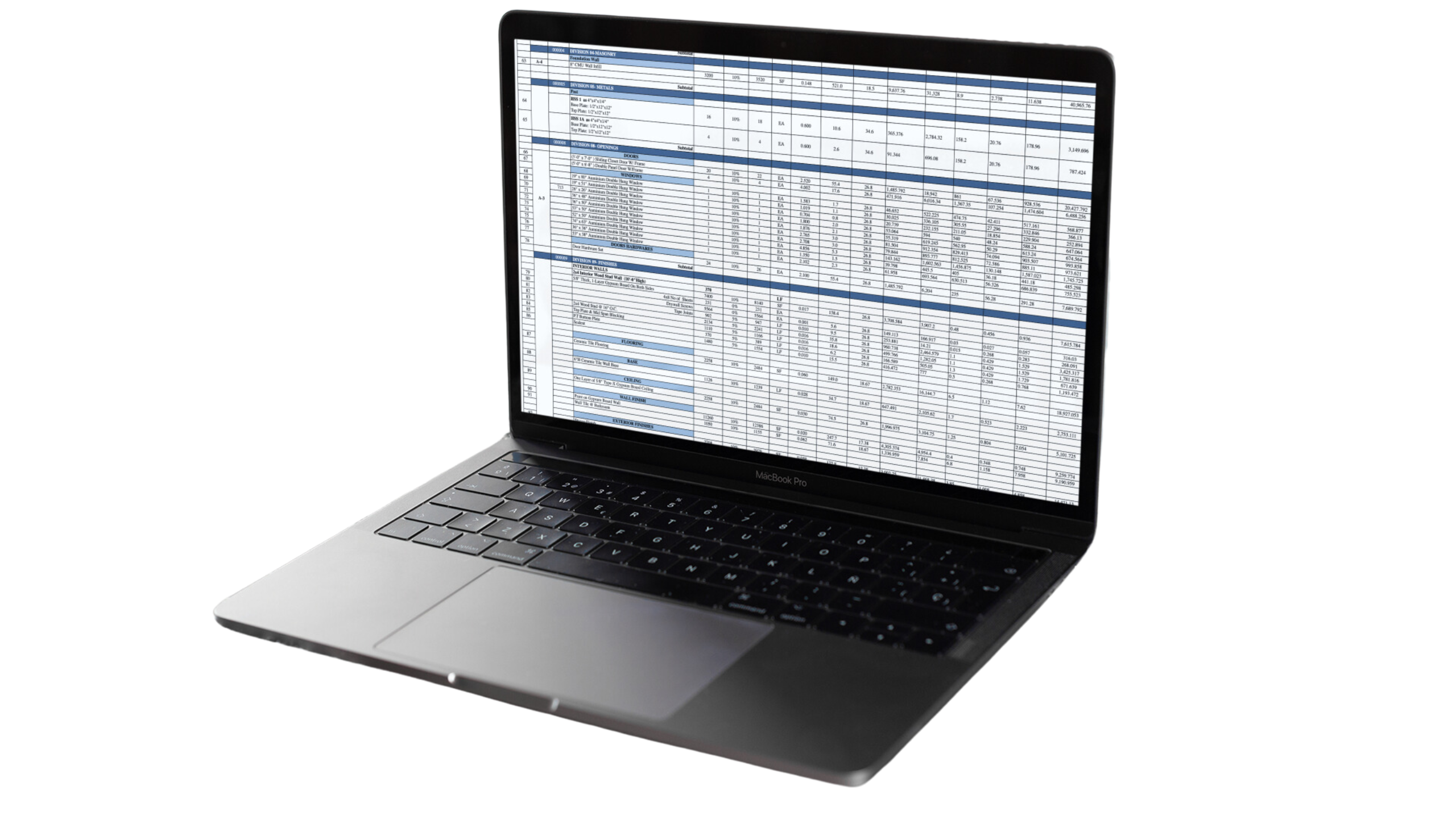
Installation Complexity
The complexity of the steam system installation can also have a significant impact on the total cost. Factors such as the layout of the facility, the need for custom piping, and the integration with existing systems can all influence labor costs. Complex installations often require specialized skills and equipment, which can increase both the time and cost required to complete the project.
Installation Complexity | Average Labor Cost |
Simple Installation | $26,000 – $65,000 |
Moderate Installation | $65,000 – $130,000 |
Complex Installation | $130,000 – $390,000+ |
Simple Installation
Involves straightforward setups with minimal customization, typically in facilities that are designed with steam systems in mind. Costs for simple installations can range from $26,000 to $65,000 depending on the scope of work. Simple installations are often completed quickly and with minimal disruption to existing operations, making them an attractive option for businesses looking to minimize downtime and costs.
Moderate Installation
Requires some customization, integration with existing systems, or installation in facilities with more complex layouts. Labor costs for moderate installations can range from $65,000 to $130,000. These installations may involve additional challenges, such as working around existing infrastructure or retrofitting older systems, which can add to the overall cost and complexity of the project.
Complex Installation
Involves highly customized solutions, integration with multiple existing systems, or installation in challenging environments. These installations can be significantly more expensive, with labor costs ranging from $130,000 to $390,000 or more. Complex installations often require extensive planning, coordination with multiple stakeholders, and the use of specialized equipment, all of which contribute to higher costs. However, the investment in a well-executed complex installation can yield significant long-term benefits in terms of system performance, efficiency, and reliability.

Additional Costs
In addition to the costs of the boiler and installation, there are several additional expenses to consider when budgeting for a steam system, including maintenance, compliance with regulations, and potential upgrades to existing infrastructure. These ongoing costs are critical for ensuring the long-term efficiency and reliability of your steam system, and they should be factored into your overall budget to avoid unexpected expenses.
Maintenance Costs
Regular maintenance is essential for ensuring the longevity and efficiency of your steam system. Annual maintenance costs can range from $6,500 to $26,000, depending on the size and complexity of the system. Maintenance tasks include inspections, cleaning, and replacing worn parts. Proper maintenance not only helps prevent costly breakdowns but also ensures that the system operates at peak efficiency, reducing fuel consumption and operating costs. Additionally, regular maintenance can extend the lifespan of the system, protecting your investment and reducing the need for expensive repairs or replacements.
Compliance Costs
Steam systems must comply with various safety and environmental regulations, which can add to the overall cost. Compliance may involve additional inspections, safety equipment, and modifications to meet local codes. The cost of compliance can vary widely depending on the location and the specific requirements, typically ranging from $13,000 to $65,000. Ensuring compliance is critical to avoiding fines and ensuring the safe operation of the system. Compliance costs should be viewed as an investment in the safety and sustainability of your operations, as non-compliance can result in significant legal and financial penalties.
Upgrades
If you are upgrading an existing steam system, additional costs may include retrofitting old equipment, upgrading controls, or improving system efficiency. These upgrades can range from $26,000 to $260,000 or more, depending on the scope of the work. Upgrades can improve the performance and efficiency of your steam system, potentially leading to significant cost savings over time. Whether it’s upgrading to more efficient boilers, installing advanced control systems, or retrofitting existing infrastructure, investing in upgrades can enhance the overall value of your steam system and ensure that it meets the evolving needs of your business.
Estimating the Total Cost
To provide a clearer understanding of what to expect, here’s an example of estimating the cost for a medium-scale industrial steam system with a capacity of 50,000 PPH, including the boiler, installation, and additional costs. This example takes into account the most common variables that affect steam system costs and provides a realistic estimate for a typical project.
- Water-Tube Boiler: $390,000 – $650,000
- Installation (Moderate Complexity): $65,000 – $130,000
- Maintenance (Annual): $6,500 – $26,000
- Compliance Costs: $13,000 – $65,000
- Upgrades: $26,000 – $130,000
Cost Component | Low Estimate | High Estimate |
Water-Tube Boiler | $390,000 | $650,000 |
Installation | $65,000 | $130,000 |
Maintenance (Annual) | $6,500 | $26,000 |
Compliance | $13,000 | $65,000 |
Upgrades | $26,000 | $130,000 |
Total Estimated Cost | $500,500 | $1,001,000 |
This example demonstrates how various components contribute to the overall cost of your steam system project. By understanding these costs, you can better plan your budget and ensure that all aspects of the project are covered, leading to a successful and efficient steam system. Proper planning also helps you avoid unexpected expenses, ensuring that your project stays within budget. The detailed breakdown provides transparency and allows you to see exactly where your money is being spent, helping you make informed decisions throughout the process. Additionally, considering the potential for energy savings, improved efficiency, and enhanced system reliability, the investment in a well-designed steam system can offer substantial long-term benefits.
Why Choose a Steam System? Benefits for Efficiency and Reliability
High Efficiency
Steam systems are known for their high efficiency in converting energy into heat or power, making them a cost-effective choice for many applications. Properly designed and installed steam systems minimize energy loss and reduce operational costs, providing long-term savings. Estimate Florida Consulting provides estimate services that help you select and install a steam system that maximizes efficiency and minimizes costs.
Reliability and Durability
In addition to their efficiency, steam systems are highly reliable and durable, often lasting for decades with proper maintenance. This longevity makes them an attractive investment for industries and buildings that require consistent and dependable heating or power generation. Estimate Florida Consulting provides estimate services that help you choose a steam system that offers long-term performance and reliability, ensuring peace of mind and value for your investment.
Long-Term Benefits of Investing in a Steam System
Investing in a steam system offers numerous long-term benefits that can significantly impact the efficiency, performance, and reliability of your operations. By choosing high-quality equipment and ensuring proper installation and maintenance, you can enjoy a reliable and cost-effective system that meets your heating, power generation, and process steam needs for years to come. These benefits extend beyond immediate cost savings, contributing to the overall success and sustainability of your business.
Energy Savings
One of the most significant benefits of investing in a steam system is the potential for energy savings. Steam systems are highly efficient, and by optimizing fuel use and reducing energy waste, they can help lower operating costs significantly. Over time, the energy savings achieved through efficient steam system operation can offset the initial investment and provide a substantial return on investment. Additionally, efficient steam systems can help businesses meet sustainability goals, reduce their carbon footprint, and comply with environmental regulations, further enhancing their value.
Improved System Performance
A well-designed steam system provides consistent and reliable performance, ensuring that your operations run smoothly and without interruption. This reliability is particularly important in industries where continuous operation is critical, such as manufacturing, power generation, and food processing. By investing in a high-quality steam system, you can reduce the risk of unexpected downtime, minimize maintenance costs, and ensure that your system delivers the performance needed to meet your operational demands. The consistent performance of a steam system also contributes to better product quality, improved process efficiency, and enhanced overall productivity.
Extended System Lifespan
Proper installation and regular maintenance of your steam system can significantly extend its lifespan, protecting your investment and reducing the need for costly repairs or replacements. A steam system that is well-maintained can last for decades, providing reliable service and reducing the total cost of ownership over time. By investing in regular inspections, timely repairs, and system upgrades, you can ensure that your steam system remains efficient, safe, and effective throughout its operational life. This long-term durability makes steam systems a valuable asset for businesses looking to maximize the return on their investment and ensure the sustainability of their operations.
Get 5 New Leads Next 7Days With Our System
- Multi-Family Building
- Hotel Building
- Hospital Building
- Warehouse Building
- High-Rise Building
- Shopping Complex
Conclusion
Accurate cost estimation is the foundation of a successful steam system installation or replacement project. Estimate Florida Consulting provides comprehensive and precise estimate services that help you plan and execute your project with confidence. By understanding the cost components and potential variables, you can make informed decisions that align with your budget and project goals. Contact us today to get started with your steam system cost estimator services, and take the first step toward creating an efficient, reliable, and cost-effective steam system. With our expert guidance and detailed cost breakdowns, you can be assured that your project will be completed on time, within budget, and to the highest standards of quality and performance. Our commitment to excellence ensures that every aspect of your project is handled with the utmost care and professionalism, resulting in a steam system that not only meets your needs but also enhances the overall efficiency and reliability of your operations.
FAQs for Steam Systems Cost Estimator
A steam system consists of several components, including boilers, piping, steam traps, pressure-reducing valves, control systems, condensate return pumps, heat exchangers, and insulation. Each component has its own cost, influenced by factors like size, material, and complexity of installation. For example, a boiler’s cost ranges from $3,900 to $39,000, with installation potentially increasing the total to $58,500. Understanding these components helps in estimating the overall cost of the steam system.
The cost of installing a new steam system varies significantly based on factors such as the system’s size, complexity, and specific requirements. Typically, the cost ranges from $50,000 to $300,000. This includes the design, procurement, and installation of all components. The choice of materials, level of automation, and integration with existing infrastructure can further influence the total cost.
Upgrading an existing steam system, such as replacing steam traps or installing new control systems, typically costs between $10,000 and $75,000. The scope of the upgrade, the number of components involved, and the complexity of the installation will impact the final cost. Partial upgrades can improve system efficiency and extend its life without requiring a full system replacement.
The type of steam boiler—whether fire-tube, water-tube, or electric—significantly impacts the cost. Fire-tube boilers are generally more affordable, with costs ranging from $26,000 to $260,000. Water-tube boilers, used for larger industrial applications, cost between $65,000 and $650,000. Electric boilers, often used in smaller applications, range from $13,000 to $195,000. The choice of boiler depends on the specific needs of the application, with each type offering different levels of efficiency and capacity.
Several factors influence the cost of steam system installation, including the layout of the facility, the need for custom piping, integration with existing systems, and the overall complexity of the installation. Simple installations may cost between $26,000 and $65,000, while more complex installations can exceed $390,000 due to the need for specialized skills and equipment.
In addition to the costs of the boiler and installation, you should consider ongoing maintenance, compliance with safety and environmental regulations, and potential upgrades. Maintenance costs can range from $6,500 to $26,000 annually, while compliance costs may add another $13,000 to $65,000. Upgrades, such as retrofitting old equipment or installing advanced controls, can range from $26,000 to $260,000 or more.
System capacity, measured in pounds per hour (PPH) or British Thermal Units (BTUs), directly impacts the cost of a steam system. Larger systems capable of producing more steam require bigger boilers, more extensive piping, and larger auxiliary equipment, leading to higher costs. For example, a system with a capacity of up to 10,000 PPH may cost between $26,000 and $130,000, while systems over 100,000 PPH can exceed $1,300,000.
Investing in a steam system offers long-term benefits such as energy savings, improved system performance, and extended lifespan. Efficient steam systems reduce operational costs, enhance reliability, and minimize downtime. Proper installation and regular maintenance can ensure the system’s durability, making it a valuable asset that offers substantial returns over time.
Estimate Florida Consulting provides expert cost estimator services to help plan and execute your steam system project with precision. By offering detailed cost breakdowns, our services ensure your project stays within budget while meeting all performance and safety requirements. Our expertise in steam system costs allows you to make informed decisions that align with your project goals.
Steam systems are known for their high efficiency, reliability, and durability, making them a cost-effective choice for various applications. They offer long-term benefits, including reduced operating costs and extended system lifespan. Steam systems are particularly suited for industries and buildings requiring consistent heating or power generation. Estimate Florida Consulting can help you select and install a steam system that maximizes these benefits while ensuring cost-effectiveness.
We Provide Steam Systems Cost Estimator
Florida’s Cities
- Alachua
- Altamonte Springs
- Anna Maria
- Apalachicola
- Apopka
- Atlantic Beach
- Auburndale
- Aventura
- Avon Park
- Bal Harbour
- Bartow
- Bay Harbor Islands
- Boca Raton
- Bonita Springs
- Boynton Beach
- Bradenton
- Brooksville
- Cape Canaveral
- Cape Coral
- Casselberry
- Celebration
- Chipley
- Cinco Bayou
- Clearwater
- Clermont
- Clewiston
- Cocoa
- Cocoa Beach
- Coconut Creek
- Coral Gables
- Coral Springs
- Crystal River
- Dania Beach
- Davie
- Daytona Beach
- Deerfield Beach
- DeFuniak Springs
- DeLand
- Delray Beach
- Deltona
- Destin
- Dunedin
- Eagle Lake
- Edgewater
- Edgewood
- Eustis
- Fort Lauderdale
- Fort Meade
- Fort Myers
- Fort Myers Beach
- Fort Pierce
- Fort Walton Beach
- Fruitland Park
- Gainesville
- Greenacres
- Green Cove Springs
- Gulf Breeze
- Gulfport
- Haines City
- Hallandale Beach
- Hawthorne
- Hialeah
- Hialeah Gardens
- Highland Beach
- Hollywood
- Holly Hill
- Holmes Beach
- Homestead
- Hypoluxo
- Indialantic
- Jacksonville
- Juno Beach
- Jupiter
- Key Biscayne
- Key West
- Kissimmee
- LaBelle
- Lady Lake
- Lake Alfred
- Lakeland
- Lake Mary
- Lake Park
- Lake Wales
- Lake Worth
- Lantana
- Largo
- Lauderdale By The Sea
- Lauderhill
- Leesburg
- Lighthouse Point
- Longboat Key
- Longwood
- Maitland
- Marco Island
- Margate
- Melbourne
- Melbourne Beach
- Miami
- Miami Beach
- Milton
- Minneola
- Miramar
- Mount Dora
- Naples
- Neptune Beach
- New Port Richey
- New Smyrna Beach
- Niceville
- North Miami
- North Miami Beach
- North Port
- Oakland Park
- Ocala
- Ocean Ridge
- Ocoee
- Okeechobee
- Oldsmar
- Orange Park
- Orlando
- Ormond Beach
- Oviedo
- Palatka
- Palm Bay
- Palm Beach
- Palm Beach Gardens
- Palm Coast
- Palmetto
- Panama City
- Panama City Beach
- Pembroke Pines
- Pensacola
- Pinecrest
- Pinellas Park
- Plant City
- Plantation
- Pompano Beach
- Ponce Inlet
- Port Orange
- Port St. Lucie
- Punta Gorda
- Rockledge
- Royal Palm Beach
- St. Augustine
- St. Augustine Beach
- St. Cloud
- St. Pete Beach
- St. Petersburg
- Safety Harbor
- Sanford
- Sanibel
- Sarasota
- Satellite Beach
- Seaside
- Sebastian
- Sewall's Point
- Shalimar
- Stuart
- Surfside
- Tallahassee
- Tamarac
- Tampa
- Tarpon Springs
- Tavares
- Temple Terrace
- Titusville
- Treasure Island
- Valparaiso
- Venice
- Vero Beach
- Wellington
- West Melbourne
- West Palm Beach
- Weston
- Wilton Manors
- Winter Garden
- Winter Haven
- Winter Park
- Winter Springs
Google Reviews
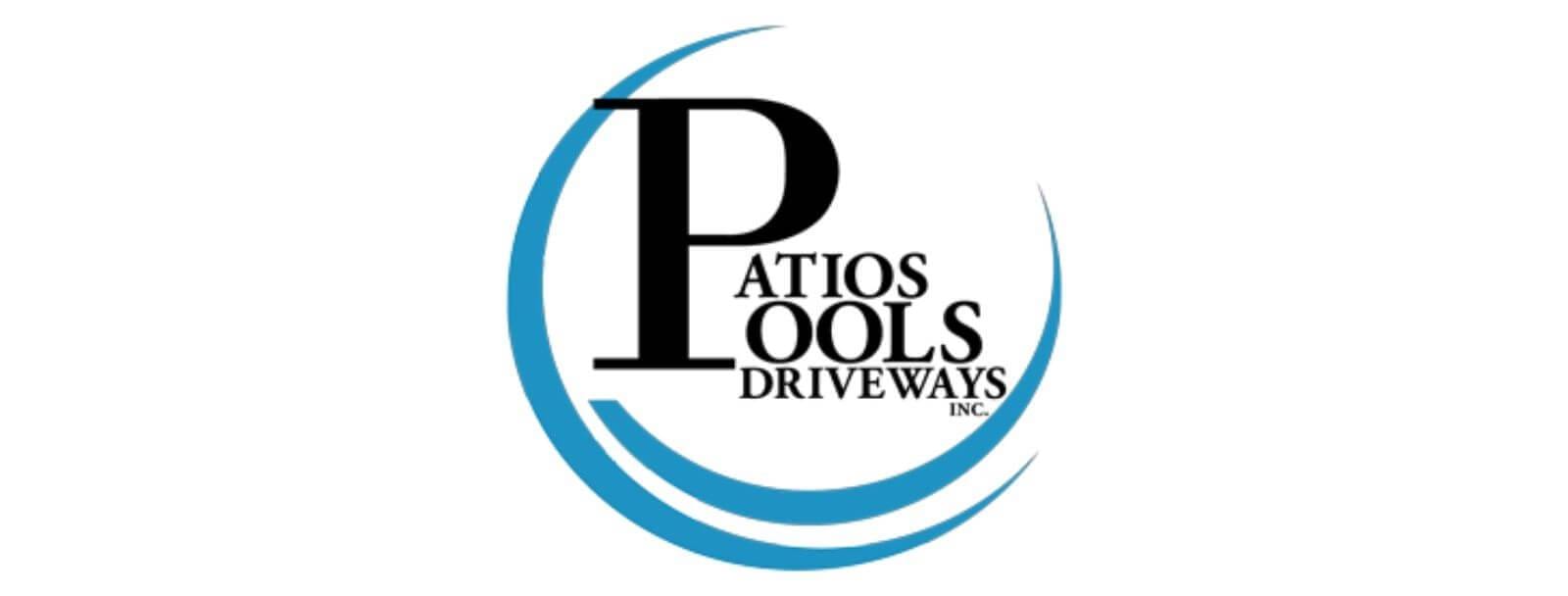
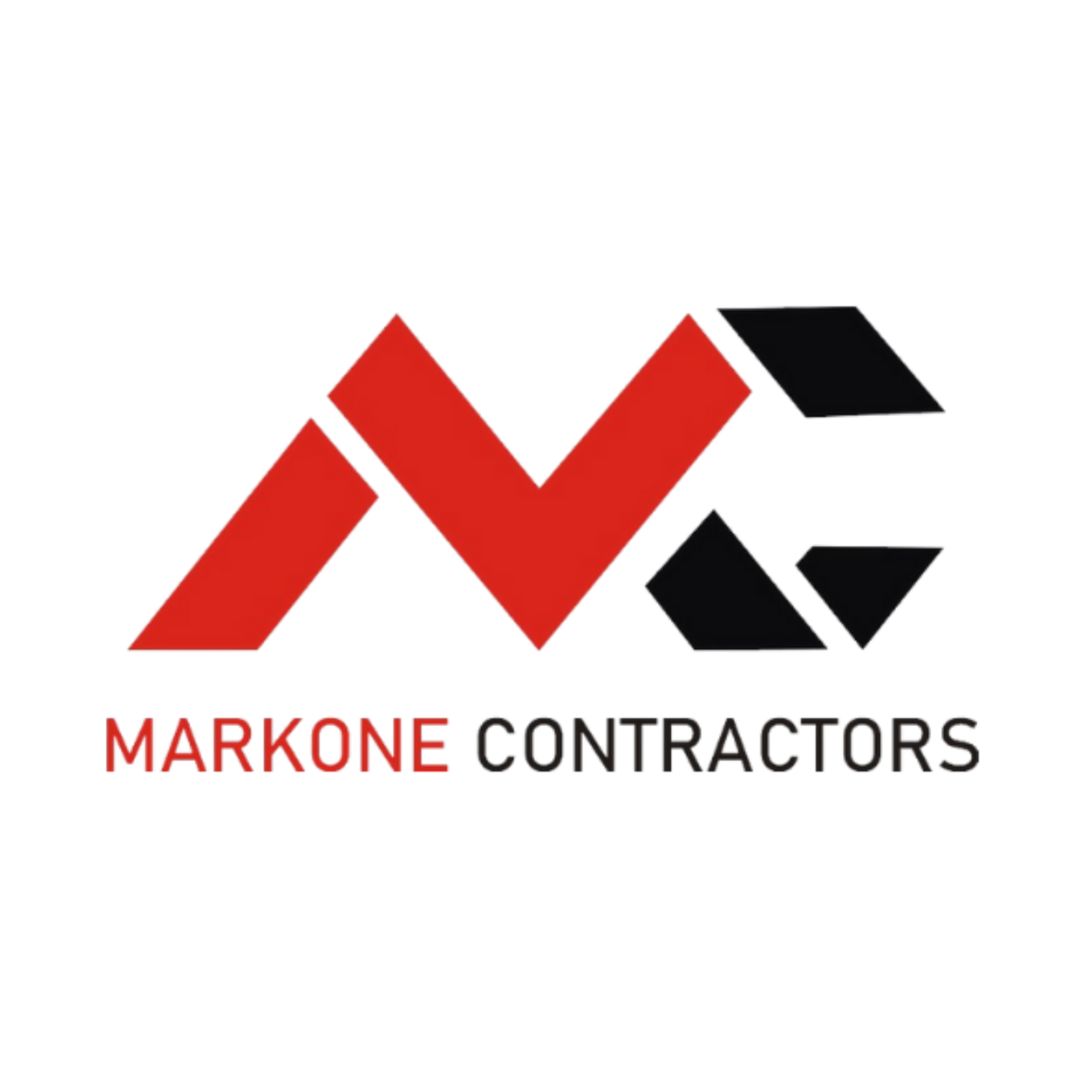

Process To Get The Steam Systems Cost Estimate Report
Here I am going to share some steps to get the steam systems cost estimate report.
-
You need to send your plan to us.
You can send us your plan on info@estimatorflorida.com
-
You receive a quote for your project.
Before starting your project, we send you a quote for your service. That quote will have detailed information about your project. Here you will get information about the size, difficulty, complexity and bid date when determining pricing.
-
Get Estimate Report
Our team will takeoff and estimate your project. When we deliver you’ll receive a PDF and an Excel file of your estimate. We can also offer construction lead generation services for the jobs you’d like to pursue further.