Boost Your Roof Bids – Request a Precision Estimate!
- Accurancy
- Efficiency
- Transparency
- Customization
- Time Saving
- Professionalism
- Cost Control
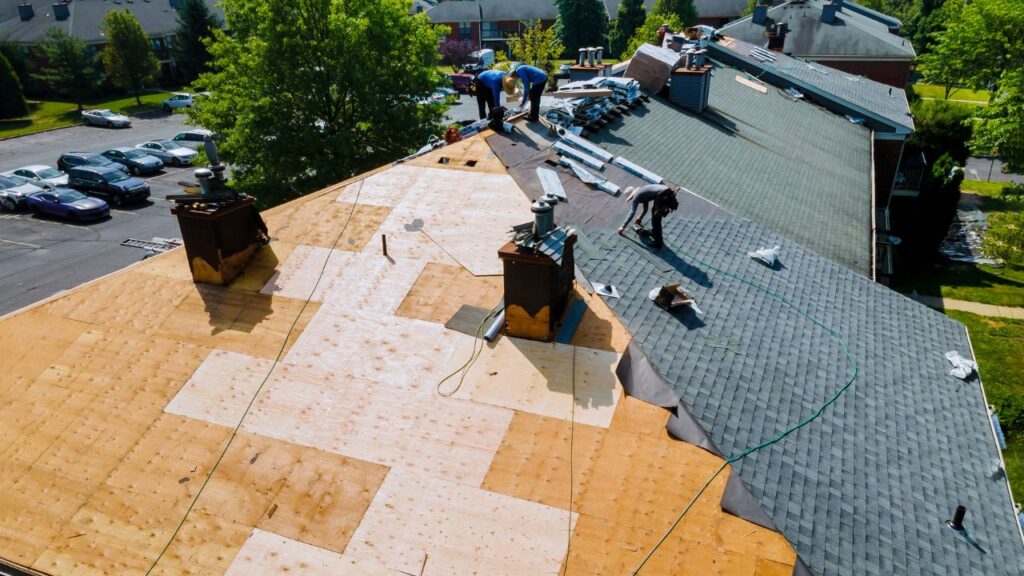
Maintaining the structural integrity of an industrial facility is paramount, and the roof plays a critical role in safeguarding assets. This guide delves into the intricate aspects of estimating and managing the cost of roof replacement for industrial facilities. From material selection to labor considerations, explore the key factors influencing expenses and strategic approaches for a successful project.
The selection of roofing materials stands as a critical decision in the roof replacement process for industrial facilities. The options, including metal, TPO, EPDM, and built-up roofing, each come with distinct advantages. Metal roofs offer durability and longevity, while TPO and EPDM provide excellent insulation. Understanding these nuances is crucial as it directly influences costs and contributes to the overall performance and resilience of the industrial roof.
Industrial roofs, characterized by their vast expanse and intricate designs, introduce variations in replacement costs. Larger roofs and complex configurations may necessitate additional labor and materials. The sheer scale of these roofs amplifies the intricacies of the replacement process. Factorizing these elements into cost considerations is essential for an accurate estimate, ensuring that the project aligns with budgetary constraints while meeting structural requirements.
The potential for underlying structural issues during roof replacement underscores the importance of a thorough initial assessment. Discovering and addressing these issues can introduce unforeseen expenses to the project. A comprehensive inspection of the existing structure is crucial, as it sets the foundation for defining the scope of work and accurately estimating the overall cost. Identifying and rectifying structural concerns early in the process mitigates risks and prevents cost escalations.
Skilled labor and specialized equipment play pivotal roles in the roof replacement process for industrial facilities. The complexity of the project, accessibility challenges, and stringent safety requirements directly influence labor costs. Moreover, the need for specialized equipment adds another dimension to the overall expenses. Understanding the intricacies of labor and equipment requirements is essential for accurate cost estimation and successful project execution.
Incorporating energy-efficient roofing solutions is a strategic consideration in roof replacement projects for industrial facilities. While these upgrades may incur additional upfront costs, the long-term savings in energy consumption make them a prudent investment. Enhanced insulation, reflective materials, and sustainable roofing solutions contribute not only to energy efficiency but also to environmental stewardship, aligning with modern industrial practices.
The adaptation of roofing materials to withstand local weather conditions and environmental factors is crucial for the durability and performance of industrial roofs. Extreme temperatures, heavy rainfall, or high winds can impact the longevity of the roof. Selecting materials that can withstand these local challenges ensures a resilient roofing system, minimizing the need for frequent replacements and associated costs.
Navigating local building codes and obtaining necessary permits are integral components contributing to the overall cost of roof replacement for industrial facilities. Compliance with specific regulations ensures a seamless and legal process. Failing to adhere to these requirements can lead to delays, fines, and potential legal issues, emphasizing the importance of including permit-related costs in the overall estimation.
Conducting a meticulous initial assessment is the cornerstone of any successful industrial roof replacement endeavor. This phase involves a detailed inspection aimed at identifying existing issues and gauging the overall health of the current roof. Through scrutinizing the condition of roofing materials, uncovering potential leaks, and assessing structural integrity, this assessment lays the foundation for defining the project’s scope and provides essential insights for accurate cost estimation. It acts as a proactive measure, allowing for the identification and mitigation of challenges before the project commences, thereby minimizing surprises during execution.
The choice of roofing materials is a pivotal decision in the roof replacement process for industrial facilities. This selection is influenced by the specific needs of the facility, prevailing climate conditions, and budget constraints. Each material, whether it be metal, TPO, EPDM, or built-up roofing, comes with unique characteristics. Considering long-term benefits and potential energy efficiency gains is crucial. Striking the right balance ensures that the selected materials align with the facility’s requirements while remaining within the predefined budget for the project.
Accurate measurements of the roof’s size and square footage are fundamental elements in the cost estimation process. The precision in these measurements is paramount to determining material and labor requirements with precision. Utilizing advanced measurement techniques, such as drone surveys or digital mapping tools, ensures a comprehensive understanding of the roof’s dimensions. This meticulous approach contributes significantly to the overall accuracy of the cost estimation process, preventing both overestimation and underestimation of necessary resources.
Defining the scope of work is a critical aspect of the roof replacement cost estimation process. This involves clearly outlining the specific tasks and activities that will be part of the industrial roof replacement project. Structural repairs, insulation installations, ventilation enhancements, and safety measures should all be part of this comprehensive scope definition. Ensuring clarity in this phase prevents surprises during the execution of the project, facilitating a smooth and well-managed replacement process.
Labor costs constitute a significant portion of industrial roof replacement expenses. Analyzing these costs involves a detailed assessment of various factors. The complexity of the project, accessibility challenges, and the need for specialized skills or equipment all contribute to the labor cost calculation. Obtaining detailed quotes from reputable contractors becomes crucial in this stage, as it allows for an accurate assessment of labor costs and ensures that the chosen contractor possesses the expertise required for the project’s successful execution.
Considering energy-efficient upgrades during industrial roof replacement is a forward-thinking approach. While these upgrades may incur additional initial costs, the long-term savings in energy consumption make them a strategic consideration. Evaluating the potential for enhanced insulation, reflective materials, and sustainable roofing solutions not only contributes to energy efficiency but also aligns with contemporary industrial practices, making the facility more environmentally responsible.
Incorporating a contingency factor into the cost estimate is a prudent strategy to address unforeseen challenges. This contingency planning adds flexibility to the budget, ensuring the project remains resilient in the face of unexpected developments. Whether dealing with hidden structural issues or unforeseen weather-related delays, a contingency factor allows for adaptation, preventing potential setbacks and cost escalations.
The expense associated with replacing an industrial roof is influenced by various elements, encompassing material selection, roof size, pitch, number of stories, location specifics, and necessary permits and inspections. Commercial roof replacement costs typically span from $6,000 to $60,000. Depending on the materials chosen, the cost range for a commercial roof replacement might fall between $18,000 and $72,000. For a metal roof replacement, the average cost per square foot ranges from $8.40 to $18.00.
Implementing an efficient material use strategy is crucial in minimizing waste and reducing overall costs associated with industrial roof replacement projects. This involves meticulous planning and optimization of material quantities to ensure that resources are utilized effectively without compromising on durability or structural integrity. By adopting innovative approaches and modern construction practices, such as precision cutting and modular designs, waste can be significantly minimized, contributing to cost-efficiency and sustainability.
Embracing technological advancements plays a pivotal role in enhancing project management efficiency and potentially realizing cost savings in industrial roof replacement endeavors. The integration of cutting-edge tools, such as project management software, drones for roof inspections, and digital mapping technologies, can streamline workflows, improve accuracy in measurements, and provide real-time data. This not only enhances the overall efficiency of the project but also contributes to informed decision-making, potentially reducing unforeseen costs.
Prioritizing regular preventive maintenance is a proactive approach to extend the lifespan of an industrial roof, ultimately reducing the frequency of replacements. A well-executed maintenance plan includes routine inspections, timely repairs, and addressing minor issues before they escalate. Investing in preventive measures can result in long-term cost savings by avoiding major structural problems and prolonging the overall durability of the roofing system.
Negotiating bulk material prices is a strategic approach to securing discounts and cost advantages in industrial roof replacement projects. Purchasing roofing materials in large quantities often allows for more favorable pricing terms from suppliers. This cost-saving measure requires effective planning and coordination with suppliers to ensure a steady and timely supply of materials throughout the project. Bulk material purchase not only reduces costs but also contributes to better project budget management.
Exploring local suppliers for roofing materials is a sustainable practice that can reduce transportation costs and support the regional economy. Local sourcing minimizes the environmental impact associated with long-distance transportation, contributing to a more eco-friendly project. Additionally, working with local suppliers fosters community engagement and promotes economic growth within the region, aligning with responsible and cost-effective procurement practices.
From small to large projects, residential to commercial, we’re here to help you win. Fast results guaranteed.
Collaborating with roofing professionals and industry experts is essential for gaining insights into cost-effective solutions and ensuring adherence to industry standards. Seeking expert consultation at various stages of the project, from initial planning to execution, can provide valuable guidance on material selection, project timelines, and potential cost-saving measures. Engaging with experienced professionals helps avoid common pitfalls, ensures regulatory compliance, and contributes to the overall success and cost-effectiveness of the industrial roof replacement project.
Managing the cost of roof replacement for industrial facilities is a multifaceted process influenced by factors such as roofing materials, roof size, structural repairs, labor, energy efficiency upgrades, environmental considerations, permitting, and regulations. A meticulous initial assessment lays the foundation for precise cost estimation, emphasizing the importance of material selection, accurate measurement, and defining the scope of work. Considering energy-efficient upgrades and incorporating contingency planning adds strategic value. The cost range for industrial roof replacement varies based on diverse elements, spanning from $6,000 to $60,000. To enhance cost-effectiveness, strategies such as efficient material use, technology adoption, preventive maintenance, bulk material purchase, local sourcing, and expert consultation are recommended. These approaches contribute to sustainability, resilience, and successful execution of industrial roof replacement projects.
The cost is influenced by roofing materials, roof size, complexity, structural repairs, labor, energy efficiency upgrades, environmental considerations, and compliance with permitting and regulations.
Each material (metal, TPO, EPDM, built-up roofing) has distinct advantages affecting durability, longevity, insulation, and overall performance, directly influencing costs in the industrial roof replacement process.
The initial assessment identifies existing issues, gauges the roof’s health, and sets the foundation for accurate cost estimation. It allows proactive identification and mitigation of challenges, minimizing surprises during execution.
Strategies include efficient material use, technology adoption, preventive maintenance, bulk material purchase, local sourcing, and expert consultation. These approaches contribute to cost-efficiency, sustainability, and successful project execution.
Commercial roof replacement costs typically range from $6,000 to $60,000. For metal roofs, the average cost per square foot falls between $8.40 and $18.00, depending on factors like materials chosen, roof size, and location specifics.
Here I am going to share some steps to get an industrial facility roof replacement cost estimate report.
You can send us your plan on info@estimatorflorida.com
Before starting your project, we send you a quote for your service. That quote will have detailed information about your project. Here you will get information about the size, difficulty, complexity and bid date when determining pricing.
Our team will takeoff and estimate your project. When we deliver you’ll receive a PDF and an Excel file of your estimate. We can also offer construction lead generation services for the jobs you’d like to pursue further.
561-530-2845
info@estimatorflorida.com
Address
5245 Wiles Rd Apt 3-102 St. Pete Beach, FL 33073 United States
561-530-2845
info@estimatorflorida.com
Address
5245 Wiles Rd Apt 3-102 St. Pete Beach, FL 33073 United States
All copyright © Reserved | Designed By V Marketing Media | Disclaimer