Rebar takeoff is the process of quantifying the amount of reinforcing steel required for a construction project. This includes determining the lengths, sizes, and weights of rebar based on structural drawings and project specifications. Accurate takeoffs are critical for budget estimation, procurement, and ensuring the structural integrity of the final build. At Estimate Florida Consulting, we specialize in providing detailed rebar takeoffs tailored to the needs of contractors and developers, helping projects stay on budget and on schedule.
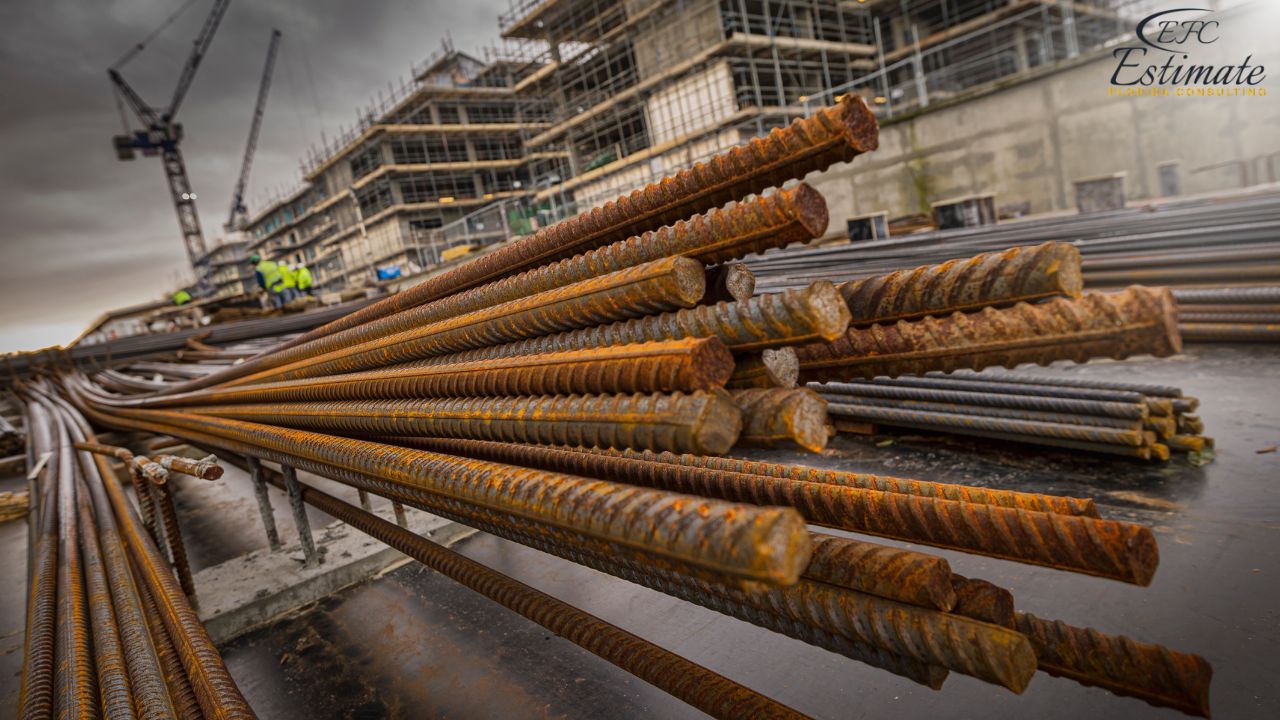
What Is Rebar Takeoff?
Rebar takeoff involves analyzing blueprints and construction plans to calculate the exact quantities of rebar needed for a project. This process requires attention to detail, as errors can lead to material shortages, project delays, or unnecessary expenses. The takeoff process typically includes the following steps:
- Reviewing project specifications and design drawings.
- Calculating linear footage, weight, and type of rebar.
- Accounting for overlaps, bends, and cuts.
- Preparing a detailed materials list for procurement.
Why Is Accurate Rebar Takeoff Important?
Accurate rebar takeoffs ensure that construction projects remain within budget while meeting structural requirements. Overestimating rebar can lead to excess material costs, while underestimating can cause delays and increased labor expenses. A precise takeoff streamlines the procurement process, reduces waste, and supports efficient project management.
Types of Rebar Takeoff
Rebar takeoff is a critical component in construction estimating, involving the precise calculation of reinforcement bar requirements for various structural elements. The scope of rebar takeoff varies depending on the type of project, as each category has distinct requirements.
Residential Rebar Takeoff
Residential projects, such as single-family homes or small multi-family dwellings, typically require rebar for foundations, driveways, patios, and retaining walls. A residential rebar takeoff includes calculations for slab-on-grade construction, which involves reinforcing the concrete slab with rebar to prevent cracking and improve durability. It also includes footing reinforcements, such as in perimeter footings or piers, and additional elements like retaining walls for landscaping. Residential takeoffs often prioritize cost-efficiency and practicality, as they cater to smaller-scale projects with less demanding structural loads.
Commercial Rebar Takeoff
Commercial projects, such as office buildings, retail spaces, or hotels, involve more extensive rebar requirements to support larger structures. These projects often include elements like parking structures, expansive slabs, and reinforced walls to accommodate heavy loads and dynamic forces. For instance, parking garages require rebar designed to handle the weight of vehicles, while reinforced walls in high-rise buildings must account for wind loads and seismic activity. Commercial rebar takeoffs also incorporate specialized reinforcements, such as shear walls and core structures, to ensure the stability and longevity of the building.
Industrial Rebar Takeoff
Industrial construction projects, including warehouses, factories, and manufacturing facilities, demand robust rebar solutions. These structures often feature thicker concrete slabs, reinforced beams, and columns to support heavy machinery, equipment, and dynamic loads from industrial operations. Rebar takeoffs for industrial projects must account for the increased scale and complexity of the structure, including load-bearing elements like mezzanine floors and crane supports. Durability and resilience are key priorities, as industrial facilities are often subjected to significant wear and tear.
Get Acquainted with Estimation
Mastering Bids: 12 Pro-Level Bidding Tips for Construction Managers
Construction Cost Estimator | Call: 561-530-2845
Custom Rebar Projects
Custom rebar projects, such as decorative concrete structures, unique architectural designs, or high-end residential features, require a tailored approach to takeoff. These projects often involve intricate patterns, non-standard sizes, and additional reinforcements to achieve both aesthetic and functional goals. For example, curved rebar may be needed for architectural arches, or decorative panels may require complex rebar grids for stability. Custom takeoffs must also consider the fabrication and installation challenges associated with non-standard designs, ensuring that the reinforcement meets the project’s specific requirements.
Types of Rebar and Their Applications
Rebar comes in various types, each suited for specific structural and environmental conditions. Understanding the properties and applications of each type ensures optimal performance and cost-effectiveness for construction projects.
Mild Steel Rebar
Mild steel rebar is the most commonly used type due to its affordability and versatility. It is easy to cut, bend, and weld, making it ideal for standard construction projects. Applications typically include residential buildings, low-load-bearing structures, and lightweight construction elements such as patios or small retaining walls. While cost-effective, mild steel rebar is prone to corrosion, so it is best used in environments with minimal exposure to moisture or aggressive chemicals.
Epoxy-Coated Rebar
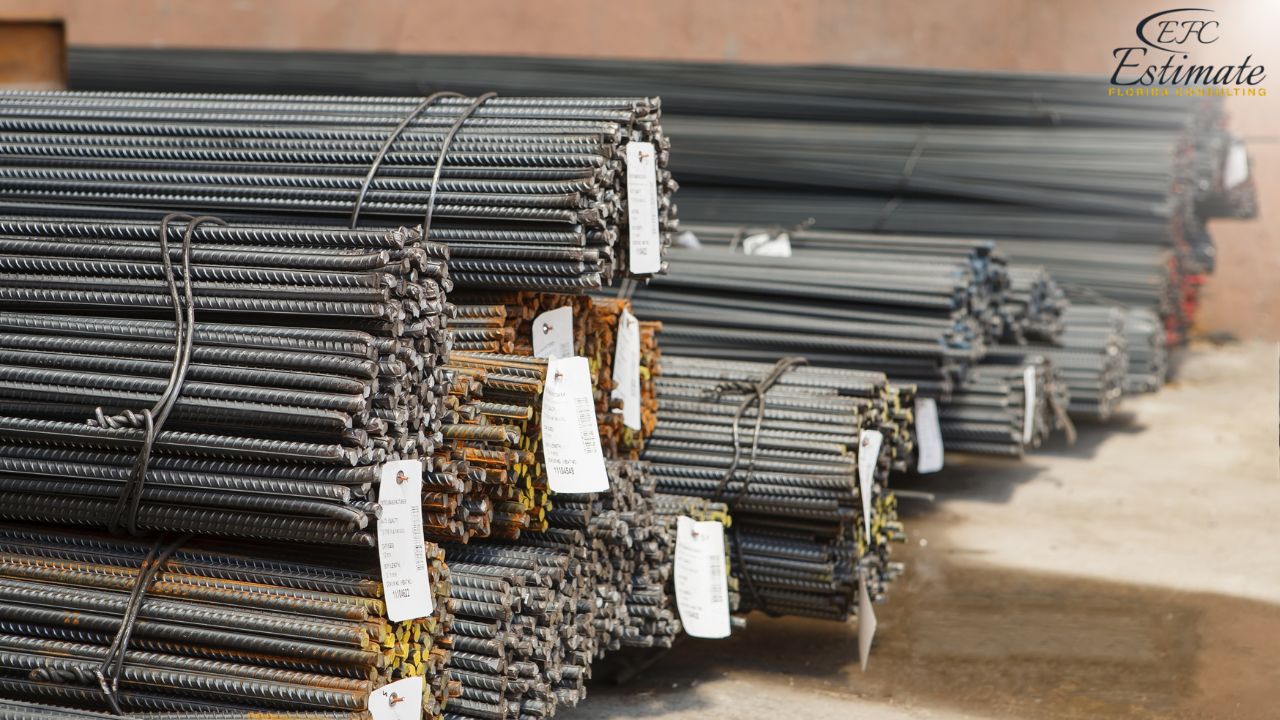
Epoxy-coated rebar is designed to resist corrosion, thanks to its protective epoxy layer. This makes it highly suitable for projects in coastal regions or high-humidity environments, such as those found in Florida. Common applications include marine structures, parking garages, and highway bridges, where exposure to saltwater or de-icing chemicals can degrade standard rebar. While more expensive than mild steel, epoxy-coated rebar offers long-term durability, reducing maintenance costs over the structure’s lifespan. However, the coating must be handled carefully to avoid damage during installation.
Stainless Steel Rebar
Stainless steel rebar provides superior strength and excellent resistance to corrosion, even in extreme conditions. It is commonly used in large infrastructure projects, such as bridges, tunnels, and wastewater treatment plants, where durability is paramount. While significantly more expensive than other rebar types, stainless steel rebar offers unmatched longevity, making it a cost-effective choice for critical structures with long service lives. Additionally, it is resistant to thermal and chemical stresses, making it ideal for specialized industrial applications.
Galvanized Rebar
Galvanized rebar is coated with zinc to enhance its resistance to rust and corrosion. It is an excellent choice for structures exposed to water, chemicals, or moisture, such as water treatment plants, marine environments, and sewage systems. Galvanized rebar is more durable than epoxy-coated rebar and less prone to damage during transportation and installation. While it offers a middle ground in terms of cost and performance, its zinc coating can degrade over time in highly aggressive environments, so proper evaluation of site conditions is essential.
Rebar Takeoff Process
The rebar takeoff process involves a systematic approach to accurately calculate the reinforcement requirements for a construction project. By following these steps, contractors can ensure precise estimates and efficient project execution.
Reviewing Blueprints
The first step in the rebar takeoff process is thoroughly reviewing blueprints, structural drawings, and any relevant design documents. This review helps identify all structural elements that require rebar reinforcement, such as foundations, columns, beams, slabs, and retaining walls. Special attention is given to design notes specifying rebar grades, sizes, and spacing, as these details are crucial for accurate takeoff calculations. Identifying any unique project requirements, such as curved or custom rebar, ensures that no critical elements are overlooked.
Win More Projects With Us
Calculating Quantities
Once the structural elements are identified, the next step is to calculate the quantities of rebar needed. This involves measuring the lengths, diameters, and spacing of the rebar based on project specifications. Advanced software tools or manual calculations are used to determine the total footage required for each type of rebar. Since rebar is typically sold by weight, these measurements are converted into weight estimates using standard weight-per-foot charts for different rebar sizes. For example, #4 rebar (1/2 inch) weighs approximately 0.668 pounds per foot, which helps translate linear footage into total weight.
Accounting for Waste
To ensure the estimate covers real-world conditions, a waste factor of 5% to 10% is added to the total quantities. This accounts for cutting losses, overlaps at joints, and on-site adjustments during installation. For instance, rebar overlaps in lap splices or additional reinforcements in high-stress areas can consume more material than initially calculated. Including this margin reduces the risk of shortages, which could cause delays or additional procurement costs.
Finalizing the Estimate
The final step involves combining all components into a comprehensive rebar takeoff estimate. This includes:
- Material Costs: Calculated based on the total weight of rebar and the current market price per pound or ton.
- Labor Costs: Estimated based on the time and skill required for rebar installation, influenced by project complexity and local wage rates.
- Additional Expenses: Includes transportation, storage, and waste disposal costs.
A detailed summary is prepared, itemizing rebar requirements by structural element and cost component. This finalized estimate provides a clear breakdown for project budgeting, procurement, and bidding.
Rebar Cost Breakdown by Major Components
Accurately estimating rebar costs involves considering several key components, including material, labor, and logistics. Here’s a detailed breakdown:
Rebar Material Costs
Rebar material costs are a significant portion of the overall expense and vary depending on the type and grade of steel. Prices typically range from $0.30 to $0.90 per pound, translating to $600 to $1,800 per ton. The variation is influenced by factors such as market demand, regional availability, and the specific properties of the rebar, such as epoxy coating for corrosion resistance or higher grades for greater strength. For large-scale projects, bulk purchasing can sometimes reduce material costs, though fluctuations in steel prices may still impact overall expenses.
Labor Costs for Rebar Installation
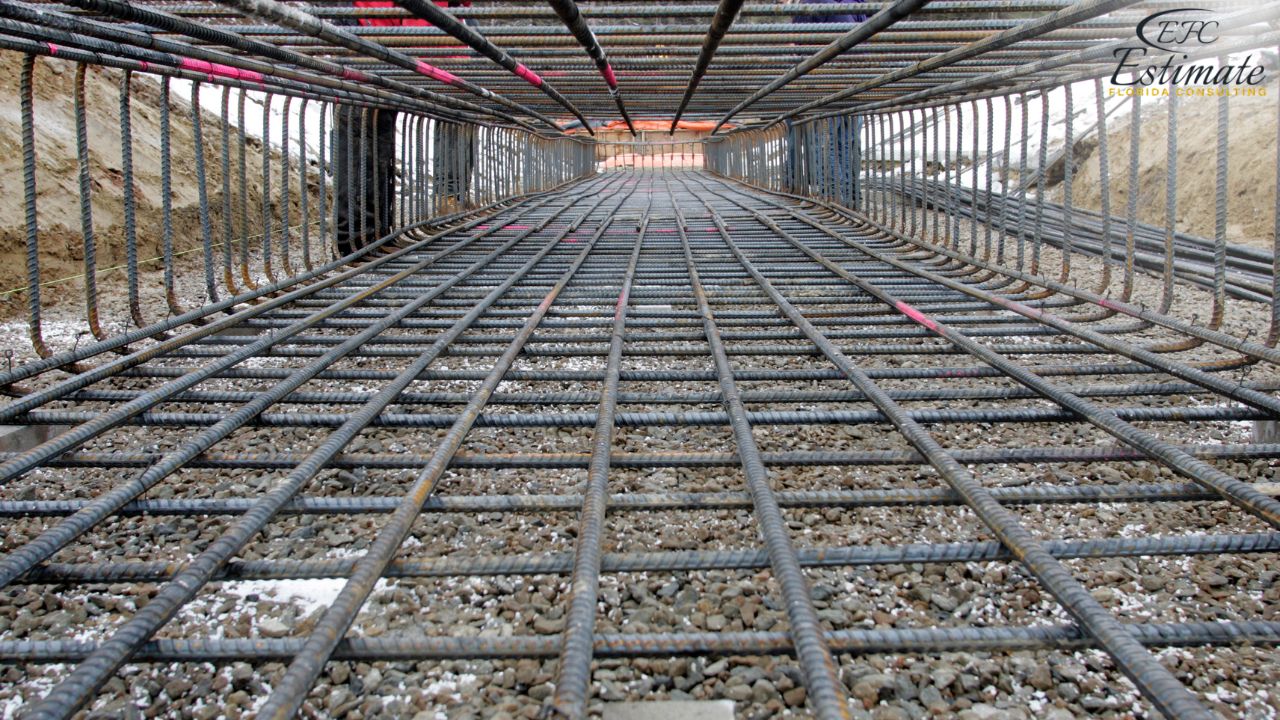
Labor costs for rebar installation are influenced by the project’s complexity, site conditions, and local wage rates. On average, labor expenses range from $2,500 to $5,000 per ton of rebar. Projects requiring intricate rebar layouts, such as curved or tightly spaced reinforcement, will demand more time and skill, increasing labor costs. Additionally, the use of specialized techniques, such as post-tensioning or on-site bending, can further elevate installation expenses. Labor efficiency is critical in controlling costs, with experienced crews often able to complete work faster and more accurately.
Transportation and Storage Costs
Transportation and storage add another layer of cost, typically ranging from $500 to $1,500 per ton of rebar. These costs depend on the distance from the supplier to the site, the size of the order, and the site’s accessibility. Remote locations or urban areas with restricted access can increase transportation expenses due to logistical challenges. Storage requirements, such as maintaining rebar in a secure and dry location to prevent rust or damage, may also add to the cost. Efficient planning and scheduling can help minimize these expenses by reducing the need for prolonged on-site storage.
Rebar Takeoff Cost by Project Size
Project Size | Rebar Required (Tons) | Estimated Cost |
Small Residential (1,500 sq. ft.) | 1 – 2 | $3,500 – $7,500 |
Medium Residential (2,500 sq. ft.) | 2 – 4 | $7,500 – $15,000 |
Large Commercial (10,000 sq. ft.) | 10 – 20 | $35,000 – $75,000 |
Download Template For Rebar Takeoff Project Breakdown
- Materials list updated to the zip code
- Fast delivery
- Data base of general contractors and sub-contractors
- Local estimators
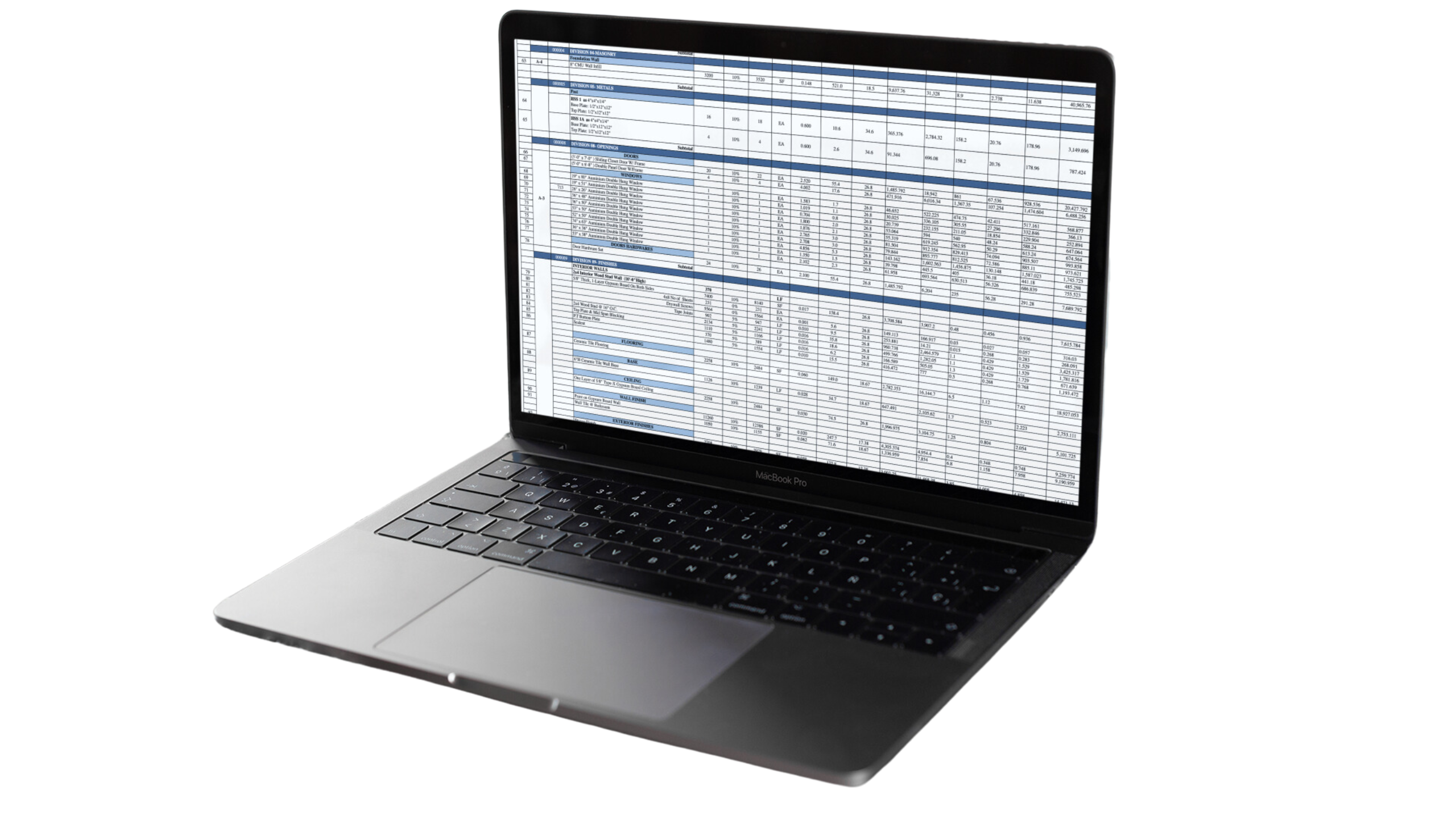
Conclusion
Rebar takeoff is a vital step in the construction process, ensuring accurate budgeting, efficient material use, and structural integrity. From understanding rebar types and applications to calculating quantities for specific structural elements, this guide provides the knowledge and tools needed for successful project execution. At Estimate Florida Consulting, we offer expert rebar takeoff and cost estimation services, tailored to meet the unique needs of Florida’s construction industry. Contact us today to streamline your next project.
Frequently Asked Question
A rebar takeoff is the process of determining the exact quantity, size, and type of reinforcing steel (rebar) required for a construction project. This includes analyzing blueprints, structural drawings, and project specifications to calculate lengths, weights, and overlaps for procurement and budgeting purposes.
Accurate rebar takeoff ensures:
- Adequate material supply, preventing delays or shortages.
- Budget efficiency by avoiding overestimation or underestimation of materials.
- Structural integrity by adhering to project specifications and design requirements.
- Blueprint Review: Analyze structural drawings to identify reinforcement needs.
- Quantity Calculation: Measure rebar lengths, weights, and diameters based on project specifications.
- Waste Factor: Add 5-10% to account for cutting losses and overlaps.
- Final Estimate: Combine material, labor, and logistics costs into a detailed report.
- Mild Steel Rebar: Cost-effective and versatile but prone to corrosion.
- Epoxy-Coated Rebar: Corrosion-resistant, ideal for marine or humid environments.
- Stainless Steel Rebar: High durability and corrosion resistance, suitable for critical structures.
- Galvanized Rebar: Zinc-coated for medium corrosion resistance, often used in water-related projects.
- Residential Projects: Foundations, patios, and retaining walls for homes.
- Commercial Projects: Office buildings, hotels, and parking structures.
- Industrial Projects: Factories, warehouses, and heavy equipment facilities.
- Custom Projects: Decorative structures and unique architectural designs.
- Material Costs: $0.30 to $0.90 per pound or $600 to $1,800 per ton.
- Labor Costs: $2,500 to $5,000 per ton, depending on complexity.
- Transportation and Storage: $500 to $1,500 per ton based on distance and site conditions.
- Accurate interpretation of structural drawings.
- Adjusting for project-specific factors like curved or custom rebar.
- Managing waste and overlap requirements.
- Ensuring timely procurement within fluctuating steel markets.
A waste factor of 5-10% is added to account for:
- Overlaps in lap splices.
- Cutting losses during installation.
- On-site adjustments for design changes or high-stress areas.
Project Size | Rebar Required (Tons) | Estimated Cost |
Small Residential (1,500 sq. ft.) | 1 - 2 | $3,500 - $7,500 |
Medium Residential (2,500 sq. ft.) | 2 - 4 | $7,500 - $15,000 |
Large Commercial (10,000 sq. ft.) | 10 - 20 | $35,000 - $75,000 |
We provide:
- Detailed rebar takeoff services for all project types.
- Accurate budgeting and material estimates tailored to Florida’s construction market.
- Expert consultation to streamline procurement and project timelines.
Comprehensive Trade-Specific Estimates
At Estimate Florida Consulting, we offer detailed cost estimates across all major trades, ensuring no part of your project is overlooked. From the foundation to the finishing touches, our trade-specific estimates provide you with a complete and accurate breakdown of costs for any type of construction project.
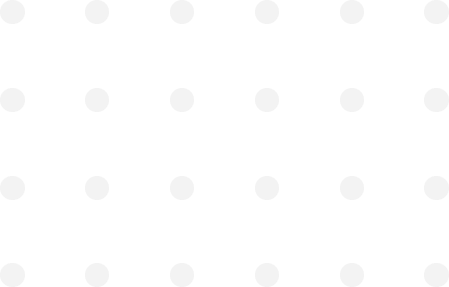
Testimonials
What Our Clients Say
We take pride in delivering accurate, timely, and reliable estimates that help contractors and builders win more projects. Our clients consistently praise our attention to detail, fast turnaround times, and the positive impact our estimates have on their businesses.
Estimate Florida Consulting has helped us win more bids with their fast and accurate estimates. We trust them for every project!
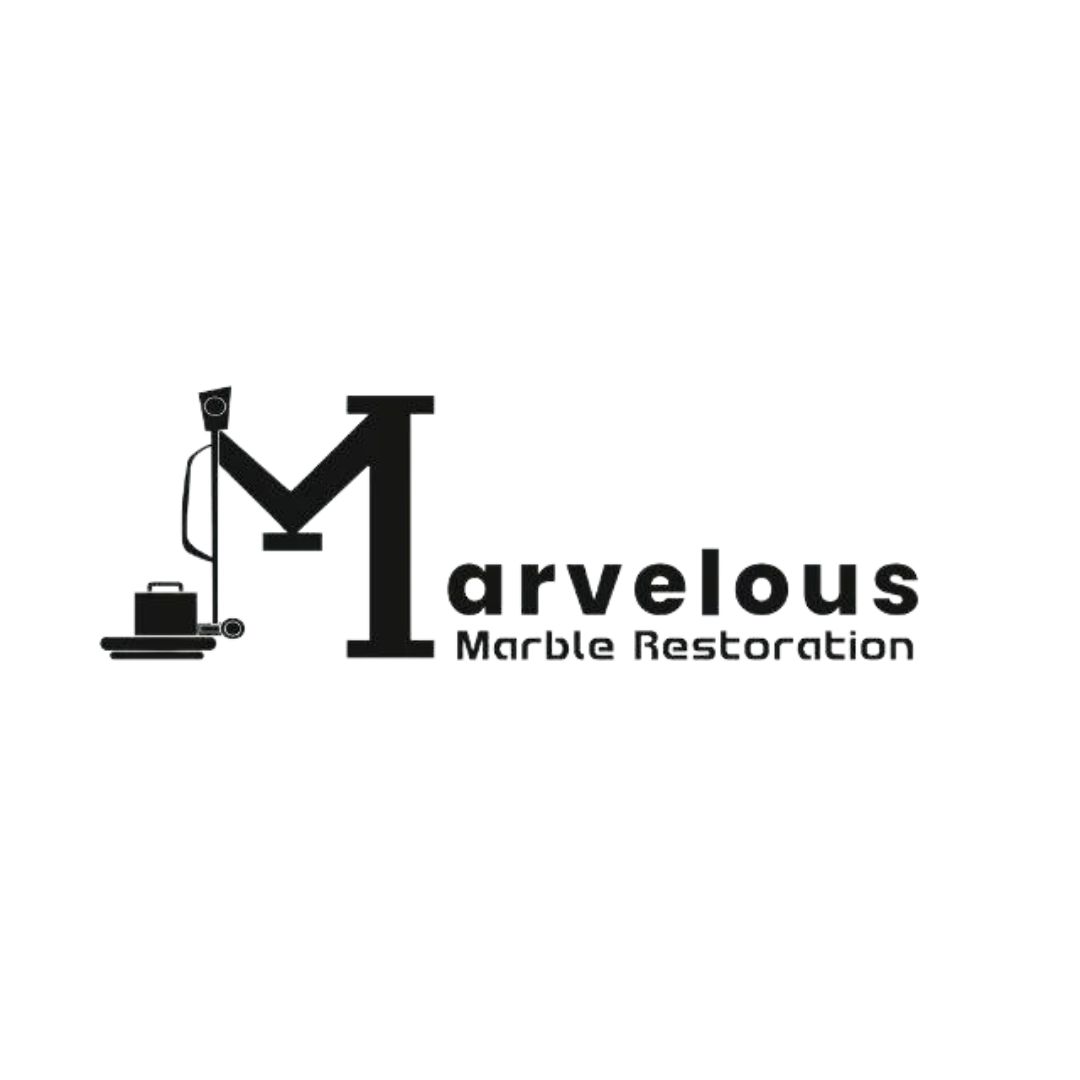
Steps to Follow
Our Simple Process to Get Your Estimate
01
Upload Plans
Submit your project plans, blueprints, or relevant documents through our online form or via email.
02
Receive Quotation
We’ll review your project details and send you a quote based on your scope and requirements.
03
Confirmation
Confirm the details and finalize any adjustments to ensure the estimate meets your project needs.
04
Get Estimate
Receive your detailed, trade-specific estimate within 1-2 business days, ready for your project execution.
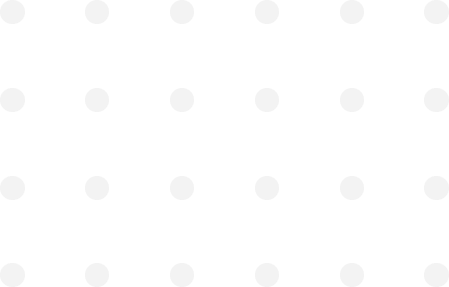