Rebar, or reinforcing bar, is a critical component of modern construction, providing strength and stability to concrete structures. Estimating rebar costs accurately is crucial for contractors, subcontractors, developers, and homeowners to ensure budget-friendly and efficient project execution. This blog will provide a detailed guide on rebar cost estimation, including essential factors, cost breakdowns, and practical tips tailored for construction projects in Florida.
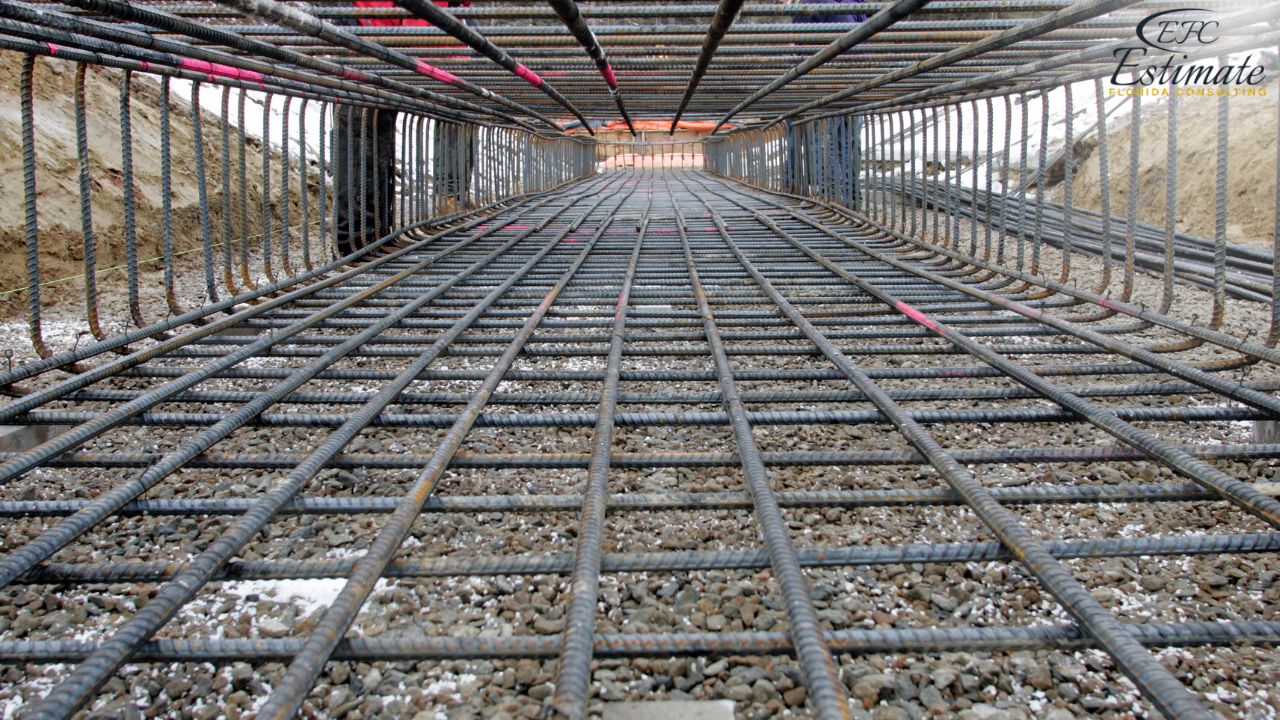
Rebar Cost per Unit and by Size
Rebar is typically priced per ton or by individual length. Prices vary depending on the diameter and material type.
Rebar Size (Diameter) | Average Cost per Ton | Cost per 20-Foot Length |
#3 (3/8 inch) | $800 – $1,000 | $5 – $10 |
#4 (1/2 inch) | $850 – $1,100 | $6 – $12 |
#5 (5/8 inch) | $900 – $1,200 | $8 – $15 |
#6 (3/4 inch) | $950 – $1,300 | $10 – $18 |
Rebar Cost Per Ton and Per Linear Foot
Rebar, or reinforcing bar, is a critical component in construction projects, providing strength and stability to concrete structures. The cost of rebar varies based on the type, material, and coating, which impact its durability, corrosion resistance, and suitability for specific applications. Here’s a breakdown of rebar costs per ton and per linear foot:
Rebar Type | Cost Per Ton | Cost Per Linear Foot |
Carbon Steel Rebar | $1,080 – $1,440 | $0.60 – $0.90 |
Epoxy-Coated Rebar | $2,160 – $3,000 | $1.20 – $1.80 |
Stainless Steel Rebar | $3,000 – $4,200 | $1.80 – $3.00 |
Fiberglass Rebar | $2,400 – $3,600 | $1.44 – $2.40 |
Carbon Steel Rebar
Carbon steel rebar is the most commonly used type due to its affordability and versatility. It is ideal for general-purpose construction projects where corrosion resistance isn’t a primary concern. Costs range from $1,080 to $1,440 per ton or $0.60 to $0.90 per linear foot, making it a cost-effective choice for large-scale projects like foundations and highways.
Get Acquainted with Estimation
Mastering Bids: 12 Pro-Level Bidding Tips for Construction Managers
Top 10 Tips to Running a Successful Construction Business
Epoxy-Coated Rebar
Epoxy-coated rebar is designed for environments where corrosion resistance is crucial, such as coastal areas or projects exposed to de-icing salts. The epoxy coating adds a protective layer, increasing durability and lifespan. This rebar costs between $2,160 and $3,000 per ton or $1.20 to $1.80 per linear foot, making it more expensive than standard carbon steel but invaluable for long-term performance in harsh conditions.
Fiberglass Rebar
Fiberglass rebar is a lightweight, corrosion-resistant alternative to traditional steel rebar. It is non-conductive and often used in projects requiring electromagnetic neutrality, such as hospitals or power plants. Fiberglass rebar costs between $2,400 and $3,600 per ton or $1.44 to $2.40 per linear foot, offering a balance of durability and cost-effectiveness for niche applications.
Factors Affecting Rebar Costs
Material Type and Grade
The type and grade of rebar play a significant role in determining its cost. Standard carbon steel rebar is the most affordable option, but specialty types such as epoxy-coated or stainless steel come at a premium due to their enhanced durability and corrosion resistance.
Fiberglass rebar, though lightweight and rust-resistant, is the most expensive option. Below is a breakdown of average rebar costs by type:
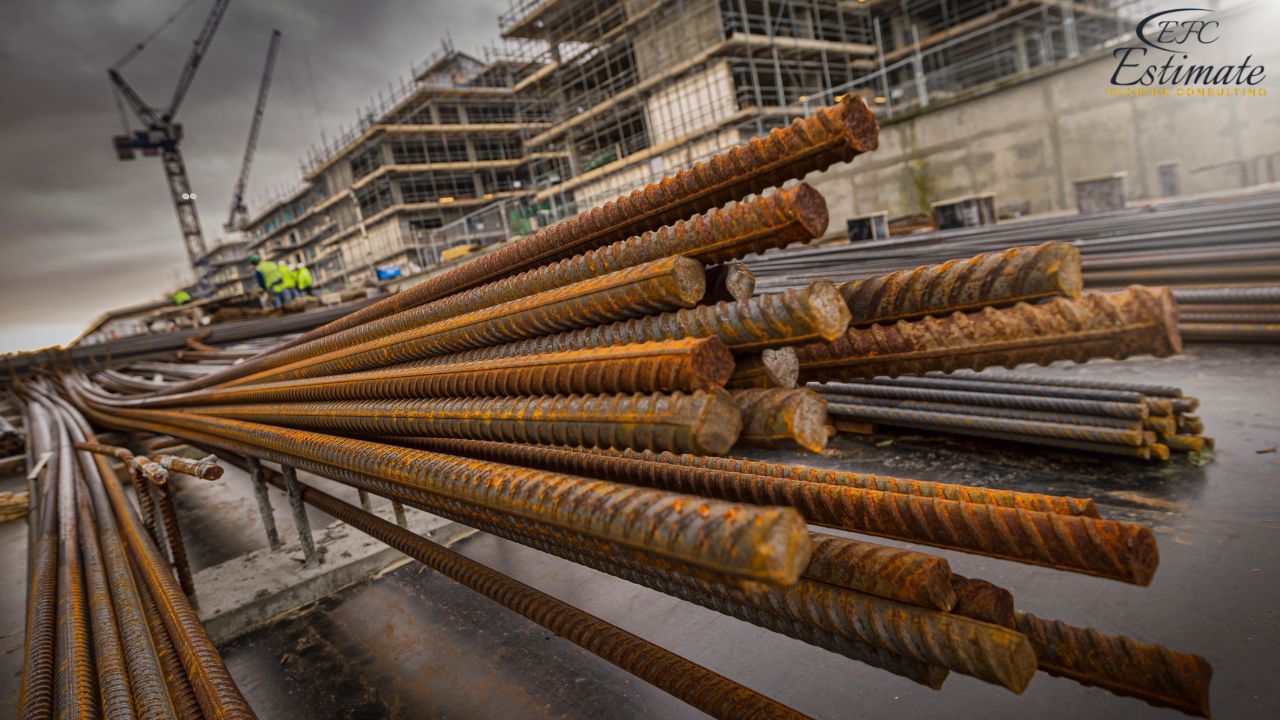
Rebar Type | Average Cost per Ton |
Carbon Steel | $840 – $1,200 |
Epoxy-Coated | $1,320 – $1,680 |
Stainless Steel | $2,400 – $3,600 |
Fiberglass | $3,000 – $4,200 |
Choosing the right type depends on the specific needs of the project. For example, epoxy-coated or stainless steel is often used in coastal areas like Florida to withstand high humidity and salt exposure.
Project Size and Complexity
The size and complexity of the project have a direct impact on rebar costs. Larger projects require more material, increasing overall expenses, while intricate designs or heavy reinforcement demands drive up both material and labor costs. For example, constructing multi-story buildings or bridges often involves complex rebar arrangements that require skilled labor and precise installation techniques, leading to higher costs.
Labor Costs
Labor costs for rebar installation vary based on factors like location, project complexity, and the expertise of the workforce. In Florida, labor rates typically range from $48 to $120 per hour, with highly skilled workers commanding higher wages. For smaller, straightforward projects, labor costs are lower, but larger, intricate projects require more time and expertise, significantly increasing expenses.
Market Fluctuations in Steel Prices
Steel prices are subject to fluctuations due to global demand, tariffs, and supply chain challenges. These variations can have a significant impact on rebar costs, especially for large-scale projects. For instance, an increase in global demand or disruptions in the supply chain can lead to price spikes, affecting both material costs and project budgets. Contractors should monitor market trends and consider adding a contingency budget to account for potential price changes during the project timeline.
Win More Projects With Us
Rebar Installation Cost Breakdown
Labor Costs for Rebar Installation
Labor represents a substantial portion of rebar installation costs. The process requires experienced crews skilled in handling and placing rebar to ensure structural integrity. Labor costs typically range from $1,800 to $5,400 per ton, depending on the complexity of the project. Factors such as intricate designs, tight deadlines, or challenging site conditions can drive labor costs higher. Hiring a professional team is essential for safety and precision, especially for large-scale projects like high-rise buildings or reinforced foundations.
Equipment and Tools Costs
Rebar installation involves the use of specialized tools and equipment to cut, bend, and secure the steel bars effectively. Common tools include rebar benders, cutters, and tying machines, which can be rented for $240 to $600 per day. Larger projects may also require additional machinery like cranes or hoists to position and secure heavy rebar sections. Equipment costs can vary based on the duration of the project and the specific tools required. While renting equipment can be cost-effective for short-term needs, larger or ongoing projects may benefit from purchasing essential tools outright.
Transportation Costs
The cost of transporting rebar to the construction site is another important factor. Transportation costs depend on the project’s location, the amount of rebar needed, and the distance from the supplier. On average, transportation costs range from $120 to $1,200, with longer distances and larger loads incurring higher fees. For remote sites or projects requiring frequent deliveries, transportation can significantly impact the overall budget. To minimize costs, coordinating bulk deliveries and sourcing rebar locally when possible is recommended.
Rebar Cost Estimation by Project Type
Residential Construction Rebar Costs
For residential projects, such as single-family homes or small apartment buildings, rebar costs typically range from $3,600 to $18,000. The final expense depends on the size of the structure, the level of reinforcement needed, and local material prices. Foundations, driveways, and retaining walls are common areas requiring rebar in residential construction. Homes in areas prone to seismic activity or heavy storms may incur higher costs due to stricter reinforcement requirements.
Commercial Building Rebar Costs
Commercial projects, including office buildings, retail spaces, and industrial facilities, demand a higher volume of rebar due to their size and complexity. Rebar expenses for commercial buildings generally range from $60,000 to $240,000, influenced by factors such as building height, load-bearing requirements, and zoning codes. Projects involving multi-story structures or complex designs often require specialized rebar arrangements, which can further increase costs.
Infrastructure and Large-Scale Projects
Infrastructure projects like highways, bridges, and tunnels involve extensive use of rebar to ensure durability and safety. These large-scale undertakings require significant quantities of high-grade rebar, leading to costs exceeding $600,000 in some cases. Factors such as project length, design specifications, and environmental considerations—like resistance to corrosion in marine environments—can add to the overall expense. These projects also require highly skilled labor and detailed planning, which contribute to the higher costs.
Rebar in Construction
Rebar is used to enhance the structural integrity of concrete in various construction applications:
- Foundations: Ensures stability and load-bearing capacity.
- Beams and Columns: Provides tensile strength to vertical and horizontal structures.
- Slabs and Driveways: Reinforces concrete surfaces against cracking and shifting.
- Retaining Walls: Adds durability to walls resisting lateral pressures.
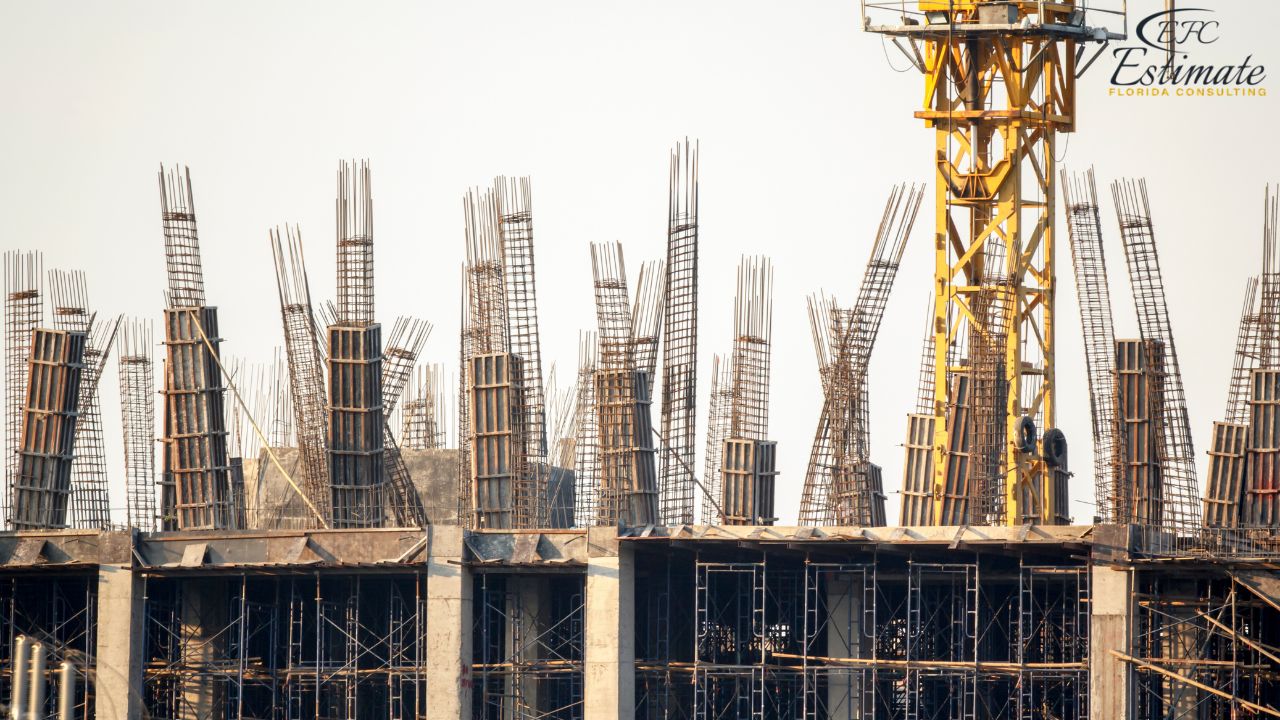
Rebar Installation Costs
Labor Costs
Labor costs for rebar installation depend on the project’s complexity, the type of structure being reinforced, and the expertise of the workers. Basic installations in straightforward designs may cost less, while intricate or large-scale projects require more skilled labor, increasing expenses. On average, labor costs range from $0.96 to $2.40 per square foot, with more complex projects on the higher end of the spectrum. Hiring experienced professionals ensures accurate placement, which is crucial for the structure’s durability and safety.
Equipment Costs
Rebar installation often requires specialized tools like rebar benders and cutters, which add to the overall project cost. Renting this equipment typically costs between $60 and $180 per day, making it a practical choice for smaller projects. For larger or long-term projects, purchasing the machinery may be more cost-effective, with prices ranging from $1,200 to $6,000 depending on the equipment’s size and capabilities. Proper tools not only improve efficiency but also ensure precision during installation.
Additional Costs to Consider
Waste and Overruns
During rebar installation, extra materials are often needed to account for cutting waste, unexpected errors, or design modifications. Contractors typically include a contingency of 5% to 12% of the total material cost to cover these overruns. This helps prevent delays and ensures the project remains on schedule.
Transportation Costs
Transporting rebar to the project site can significantly affect costs, especially for remote locations or large orders. Delivery fees range from $120 to $600 per trip, depending on the distance and size of the order. For bulk purchases, some suppliers may offer discounts or waive delivery fees if the order exceeds a certain threshold.
Rebar Couplers and Accessories
Accessories like couplers, spacers, and chairs are essential for securing rebar in place and maintaining proper alignment. These small components enhance stability and durability but come at an additional cost. Expect to pay $0.06 to $0.18 per foot of rebar for these accessories, which can add up significantly for larger projects.
Download Template For Rebar Project Breakdown
- Materials list updated to the zip code
- Fast delivery
- Data base of general contractors and sub-contractors
- Local estimators
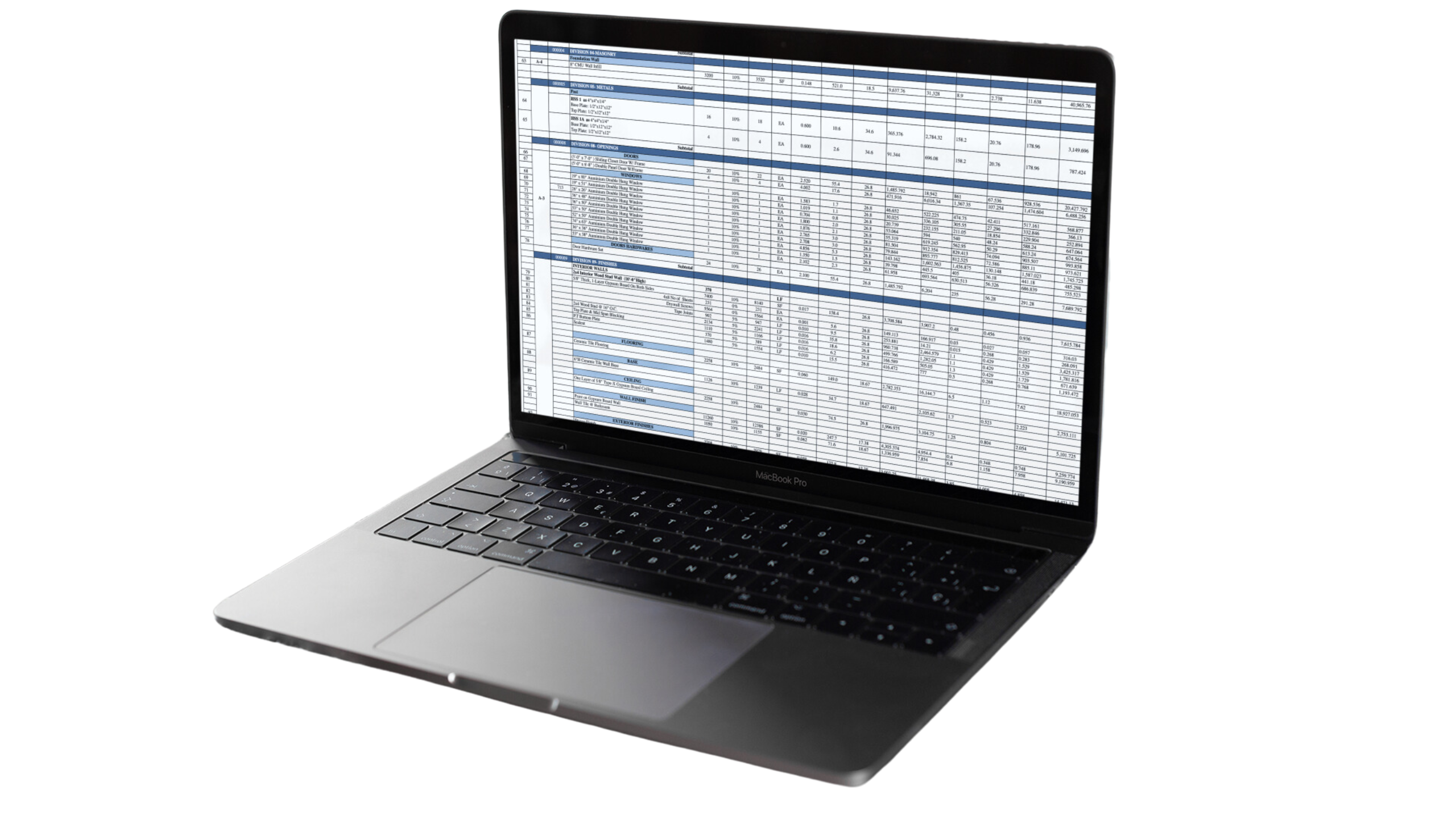
Tips to Reduce Rebar Costs
- Bulk Purchasing: Buying rebar in bulk can help reduce per-unit costs.
- Optimize Design: Work with engineers to minimize unnecessary reinforcement while maintaining safety.
- Local Suppliers: Source rebar from local vendors to reduce transportation expenses.
- Regular Market Monitoring: Keep an eye on steel price trends to purchase at the best rates.
Conclusion
Rebar is a crucial element in construction projects, providing the reinforcement necessary for durable and long-lasting structures. By understanding the factors influencing rebar costs and using precise estimation methods, contractors can budget effectively and avoid unnecessary expenses. At Estimate Florida Consulting, we specialize in providing detailed cost estimates and expert advice to help you manage your construction projects efficiently. Contact us today for professional rebar cost estimation services tailored to your project needs!
Frequently Asked Question
Rebar, short for reinforcing bar, is a steel component used to strengthen and stabilize concrete structures. It enhances the tensile strength of concrete, making it essential for building foundations, columns, beams, and more. Accurate cost estimation of rebar is crucial for contractors and developers to ensure project efficiency and budget control.
Key factors influencing rebar costs include:
- Material Type and Grade: Carbon steel is the most affordable, while stainless steel and fiberglass rebar cost more due to corrosion resistance and specialized applications.
- Project Size and Complexity: Larger or intricate projects require more material and skilled labor, increasing costs.
- Labor Rates: In Florida, labor costs range from $48 to $120 per hour, depending on project complexity.
- Market Fluctuations: Steel prices vary due to demand, tariffs, and supply chain issues, impacting rebar costs significantly.
Costs vary by material and application. Here’s a breakdown:
Rebar Type | Cost Per Ton | Cost Per Linear Foot |
Carbon Steel Rebar | $1,080 - $1,440 | $0.60 - $0.90 |
Epoxy-Coated Rebar | $2,160 - $3,000 | $1.20 - $1.80 |
Stainless Steel Rebar | $3,000 - $4,200 | $1.80 - $3.00 |
Fiberglass Rebar | $2,400 - $3,600 | $1.44 - $2.40 |
Labor costs depend on project size and complexity:
- Small Projects: $1,800 to $3,600 per ton.
- Large/Complex Projects: $3,600 to $5,400 per ton.
In Florida, hourly labor rates range from $48 to $120, depending on workforce expertise.
Rebar accessories like couplers, spacers, and chairs are used to secure alignment and maintain structural integrity.
- Cost per Foot of Rebar: $0.06 to $0.18.
While these items are inexpensive individually, their costs can add up for larger projects.
Project Type | Estimated Cost Range |
Residential Construction | $3,600 - $18,000 |
Commercial Buildings | $60,000 - $240,000 |
Infrastructure Projects | $600,000+ |
To minimize costs:
- Buy in Bulk: Purchase larger quantities to secure discounts.
- Optimize Design: Collaborate with engineers to avoid over-reinforcement.
- Source Locally: Reduce transportation expenses by buying from local vendors.
Monitor Market Trends: Watch steel price fluctuations to make cost-effective purchases.
Transportation costs vary based on distance, load size, and location:
- Average Range: $120 to $1,200 per trip.
- For remote or large projects, transportation can form a significant portion of the budget. Bulk ordering and sourcing from local suppliers help minimize costs.
Comprehensive Trade-Specific Estimates
At Estimate Florida Consulting, we offer detailed cost estimates across all major trades, ensuring no part of your project is overlooked. From the foundation to the finishing touches, our trade-specific estimates provide you with a complete and accurate breakdown of costs for any type of construction project.
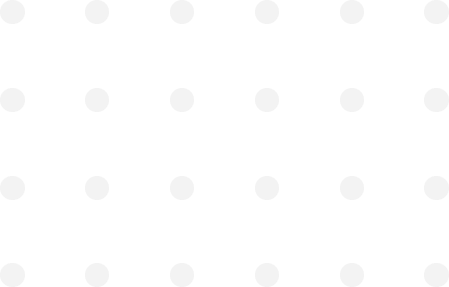
Testimonials
What Our Clients Say
We take pride in delivering accurate, timely, and reliable estimates that help contractors and builders win more projects. Our clients consistently praise our attention to detail, fast turnaround times, and the positive impact our estimates have on their businesses.
Estimate Florida Consulting has helped us win more bids with their fast and accurate estimates. We trust them for every project!
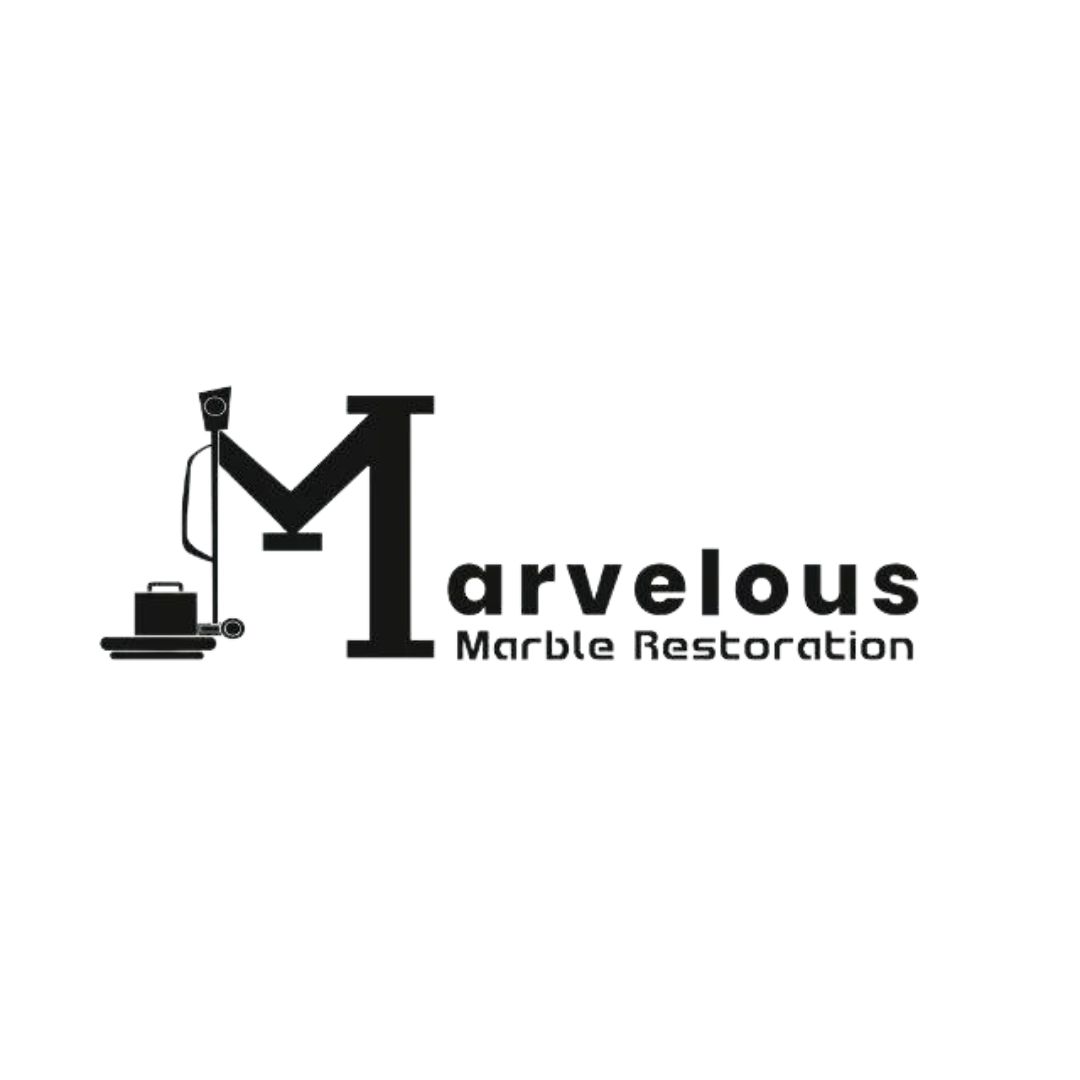
Steps to Follow
Our Simple Process to Get Your Estimate
01
Upload Plans
Submit your project plans, blueprints, or relevant documents through our online form or via email.
02
Receive Quotation
We’ll review your project details and send you a quote based on your scope and requirements.
03
Confirmation
Confirm the details and finalize any adjustments to ensure the estimate meets your project needs.
04
Get Estimate
Receive your detailed, trade-specific estimate within 1-2 business days, ready for your project execution.
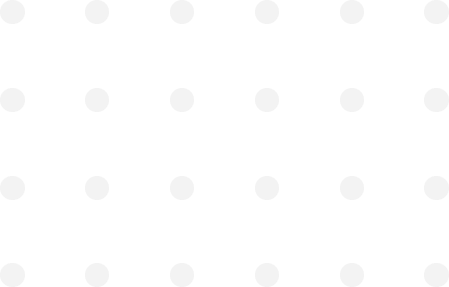