- Homepage
- Blogs
Prefabricated Wall Panel Cost
Leading provider of prefabricated wall panel cost estimating.
Prefabricated wall panels are factory-made wall sections that are transported to a construction site for quick and efficient assembly. Unlike traditional wall construction methods, prefabricated panels are created in controlled environments, reducing the impact of weather, labor delays, and material waste. In recent years, prefabricated wall panels have gained popularity across Florida due to their cost-effectiveness and ability to accelerate project timelines.
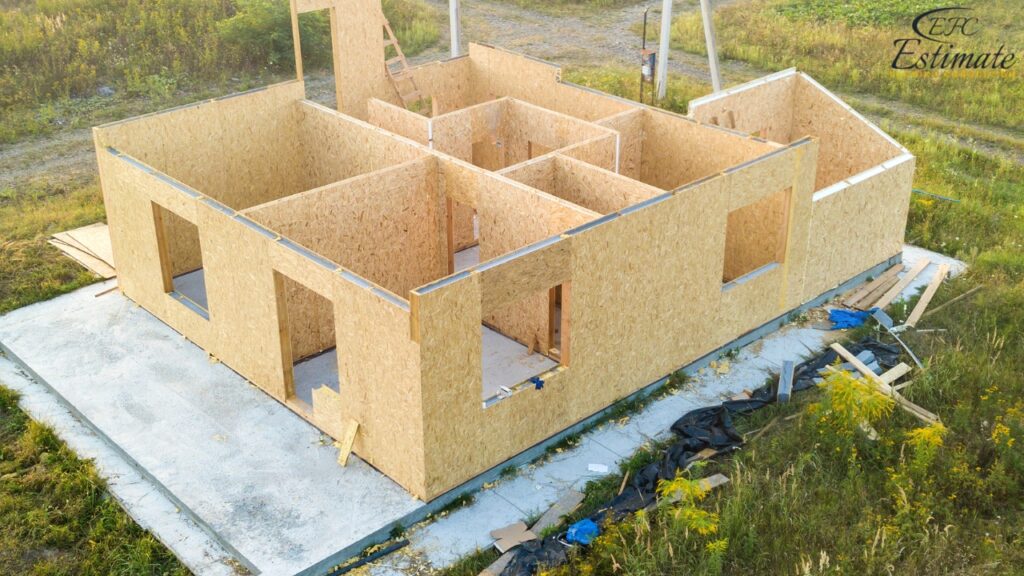
Average Cost of Prefabricated Wall Panels in Florida
The cost of prefabricated wall panels in Florida ranges from $12 to $30 per square foot. This estimate includes basic material costs, transportation, and standard installation. Factors such as panel type, thickness, and customization can drive these costs up or down. Here’s a cost table for prefabricated wall panels based on average pricing in Florida:
Panel Type | Average Cost per Square Foot |
Standard Wall Panel | $12 – $18 |
Insulated Wall Panel | $18 – $25 |
Custom Design Wall Panel | $22 – $30 |
Prefabricated Wall Panel Cost by Size and Thickness
The size and thickness of wall panels also affect the overall cost. Larger and thicker panels generally cost more due to the additional materials required. Here’s an example of pricing based on panel size and thickness:
Panel Size | Thickness | Cost per Panel |
4′ x 8′ | 4 inches | $180 – $300 |
4′ x 10′ | 6 inches | $220 – $360 |
4′ x 12′ | 8 inches | $260 – $420 |
Average Cost of Prefabricated Wall Panels by Material
The cost of prefabricated wall panels varies depending on the material used. Each material has unique benefits and is suited to different types of projects.
Material Type | Average Cost per Square Foot |
Structural Insulated Panels (SIPs) | $8 – $15 |
Concrete Panels | $15 – $30 |
Wood Panels | $10 – $20 |
Metal Panels | $12 – $25 |
Win More Projects With Us
Prefabricated Wall Panel Installation Costs
Installation costs for prefabricated wall panels vary based on labor rates, site conditions, and panel complexity. On average, installation can range from $5 to $15 per square foot. Installation costs may be higher for projects requiring cranes, scaffolding, or additional safety measures, which are often necessary for multi-story buildings or large commercial projects.
Installation Cost Factor | Average Cost per Square Foot |
Standard Installation | $5 – $10 |
Complex Installation (Multi-Story) | $10 – $15 |
Additional Equipment (e.g., Crane) | Varies by project |
Get Acquainted
12 Construction marketing strategies
Prefabricated Wall Panel Costs by Building Type
Different building types require varying levels of structural support, insulation, and customization, which influence panel costs.
Building Type | Average Cost per Square Foot |
Residential (Single-Family) | $10 – $20 |
Multi-Family (Apartments) | $15 – $25 |
Commercial Buildings | $18 – $30 |
Industrial Buildings | $20 – $30 |
Types of Prefabricated Wall Panels
Structural Insulated Panels (SIPs)
Structural Insulated Panels, or SIPs, are widely used in residential and commercial construction due to their excellent energy efficiency and structural strength. These panels consist of a core layer of insulating foam sandwiched between two structural facings, typically oriented strand board (OSB) or plywood. SIPs are durable, versatile, and easy to install, making them a popular choice for energy-conscious builders. The cost of SIPs ranges from $8 to $15 per square foot, depending on panel thickness, insulation type, and specific project requirements.
Concrete Panels
Concrete panels are known for their durability, strength, and high fire resistance, making them ideal for multi-story buildings, industrial facilities, and other projects requiring robust structural support. These panels are pre-cast and can be customized for thickness and structural needs. Concrete panels are designed to withstand harsh conditions, and their fire-resistant properties make them suitable for high-occupancy structures. Costs for concrete panels range from $15 to $30 per square foot, influenced by factors like panel thickness, design, and structural reinforcements.
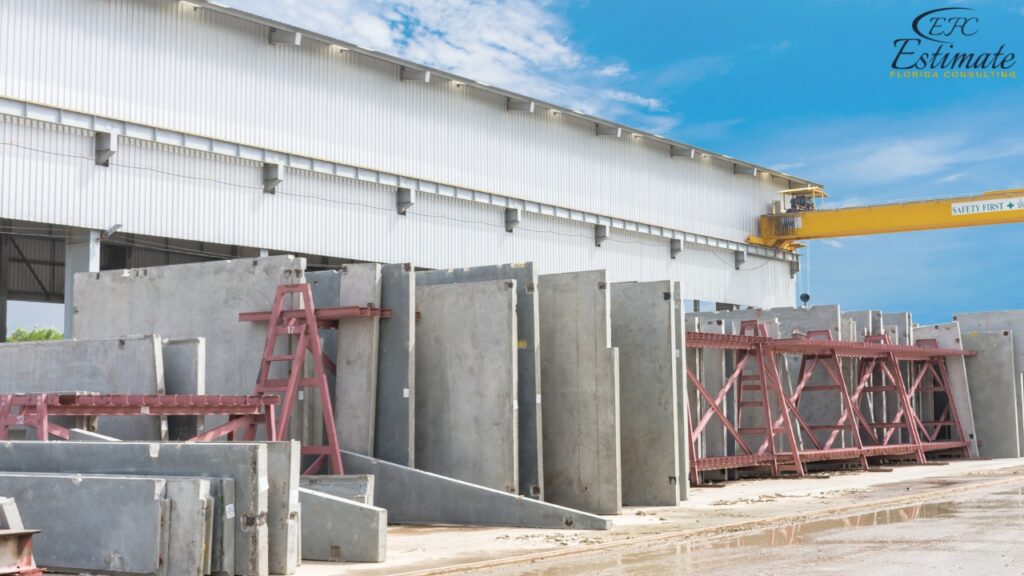
Wood Panels
Wood prefabricated wall panels are commonly used in residential projects for their natural aesthetic appeal and affordability. These panels are easy to install and can be customized with various wood types and finishes. While wood panels are generally more affordable, they may require more maintenance, especially in humid or termite-prone regions. Average costs for wood panels range from $10 to $20 per square foot, though premium woods or additional treatments can increase this cost.
Metal Panels
Metal wall panels, typically made from steel or aluminum, are known for their durability and are often used in commercial and industrial settings. Metal panels are resistant to fire, pests, and moisture, providing long-term durability with minimal maintenance. These panels are also popular for their sleek, modern look, often used in contemporary architectural designs. The cost for metal panels generally ranges from $12 to $25 per square foot, with variations based on metal type, thickness, and any additional protective coatings.
Factors Affecting Prefabricated Wall Panel Costs
Material Selection
The choice of material has a major impact on the overall cost of prefabricated wall panels. Concrete and metal panels tend to be more expensive upfront due to their durability and structural properties, while wood panels are generally more affordable but may require more maintenance over time. Material selection depends on the project’s requirements, with cost considerations balanced against factors like durability, aesthetics, and environmental conditions.
Panel Size and Thickness
The dimensions of the wall panels play a significant role in determining the cost. Larger or thicker panels require more materials, increasing production costs. Projects that need enhanced insulation or extra structural strength may also demand thicker panels, contributing to higher overall expenses. Consulting with structural engineers can help determine the optimal size and thickness for specific applications, ensuring safety and performance without unnecessary cost.
Insulation and R-Value
The insulation quality of prefabricated wall panels, measured in R-value, affects both their cost and energy efficiency. Higher-R-value panels provide better insulation, making them ideal for projects focused on energy savings. However, these panels typically cost more upfront. While higher R-values increase initial expenses, they can lead to long-term savings on heating and cooling bills, making them a valuable investment in energy-efficient construction.
Customization and Design
Customization options, such as specific finishes, colors, or unique design elements, can increase the cost of prefabricated wall panels. Architectural panels, for example, often feature decorative elements or special textures that require additional manufacturing steps. Panels tailored to unique design specifications or with intricate details may require specialized molds or coatings, leading to added expenses. For projects where aesthetics are a high priority, customization is an important consideration in the overall budget.
Prefabricated vs. Traditional Wall Construction
Comparing prefabricated wall panels to traditional wall construction can provide insights into the potential cost savings.
Construction Method | Average Cost per Square Foot | Labor Requirement | Installation Time |
Prefabricated Wall Panels | $8 – $30 | Lower | Faster (1-2 days per floor) |
Traditional Wall Construction | $10 – $35 | Higher | Slower (1 week per floor) |
Long-Term Savings and Benefits of Prefabricated Wall Panels
While prefabricated wall panels may involve higher upfront costs compared to traditional construction methods, they offer substantial long-term savings:
- Reduced Labor Costs: Quicker installation reduces labor expenses, particularly beneficial in areas with high labor costs.
- Lower Utility Bills: Insulated panels improve energy efficiency, leading to reduced heating and cooling costs over the building’s lifespan.
- Minimal Maintenance: Many prefabricated panels, especially metal and concrete types, require less maintenance than traditional materials, contributing to long-term cost savings.
Cost Estimation for a Project Using Prefabricated Wall Panels
Creating an accurate cost estimate for a project using prefabricated wall panels involves several steps:
- Determine Panel Type and Specifications: Select the appropriate panel material, thickness, and insulation based on project requirements.
- Calculate Square Footage: Measure the total area that will be covered by the prefabricated panels.
- Add Manufacturing, Transportation, and Installation Costs: Factor in costs for manufacturing, delivery to the site, and on-site installation based on local labor rates.
- Account for Contingencies: It’s advisable to set aside an additional 10-15% of the budget for unexpected expenses or adjustments.
Example Cost Estimate for a Residential Project
Cost Component | Cost Estimate |
Wall Panels (5000 sq ft) | $75,000 – $150,000 |
Manufacturing | $10,000 – $20,000 |
Transportation | $5,000 – $10,000 |
Installation | $20,000 – $40,000 |
Total Estimate | $110,000 – $220,000 |
Benefits of Prefabricated Wall Panels
Prefabricated wall panels offer various advantages, including:
- Cost Savings: Reduced labor costs and minimized construction time help lower overall expenses.
- Time Efficiency: With prefabricated panels, construction timelines are significantly shortened, as on-site labor requirements decrease.
- Precision and Quality Control: Manufactured in a controlled environment, prefabricated panels offer high-quality, uniform components.
- Waste Reduction: Prefabrication reduces material waste, making it an eco-friendly construction choice.

Additional Costs in Prefabricated Wall Panel Installation
When planning for prefabricated wall panel installation, it’s essential to consider potential additional costs:
Transportation
Transporting prefabricated wall panels from the manufacturing facility to the job site is a key cost factor, particularly for projects located far from the production site. Transportation costs can vary depending on the distance, the weight and size of the panels, and any special handling requirements. Typically, transportation expenses add around $1 to $3 per square foot to the project budget. For remote or large-scale projects, planning for these logistics early can help optimize shipping costs.
On-Site Adjustments
Even with precise manufacturing, on-site adjustments may be necessary to ensure panels fit perfectly within the structure. Adjustments could include cutting, resizing, or accommodating specific design details that were not accounted for initially. These adjustments often require specialized tools and skilled labor, adding $2 to $5 per square foot to the overall cost. Proper planning and site measurements can help minimize these adjustments, but it’s wise to budget for potential modifications.
Permit Fees
Depending on local building codes and regulations, permits may be required for prefabricated wall panel installation. Permit fees vary by jurisdiction and project type but typically range from $100 to $500 for residential projects. For commercial or industrial applications, permit costs may be higher. Checking with local authorities in advance ensures compliance and prevents delays, allowing for a smooth installation process.
Weather Protection
If prefabricated wall panels will be exposed to the elements during transportation or before installation, weatherproofing measures may be necessary. Temporary waterproofing treatments, such as tarps, sealants, or protective coatings, protect the panels from moisture damage. Weather protection costs can vary depending on the type of protection used, but it’s typically an additional $1 to $2 per square foot. For projects in rainy or humid climates, these measures are particularly important to maintain the quality and longevity of the panels.
Conclusion
Prefabricated wall panels offer a cost-effective, efficient, and environmentally friendly solution for construction in Florida. Ranging from $12 to $30 per square foot, these panels reduce material waste, minimize weather-related delays, and streamline project timelines. They come in various materials, including concrete, wood, and metal, catering to diverse building needs. Installation costs, ranging from $5 to $15 per square foot, and factors like customization and insulation quality further influence pricing. With advantages like lower labor costs, energy savings, and reduced maintenance, prefabricated panels present a durable, high-quality alternative to traditional construction methods.
Download Template For Prefabricated Wall Panel Project Breakdown
- Materials list updated to the zip code
- Fast delivery
- Data base of general contractors and sub-contractors
- Local estimators
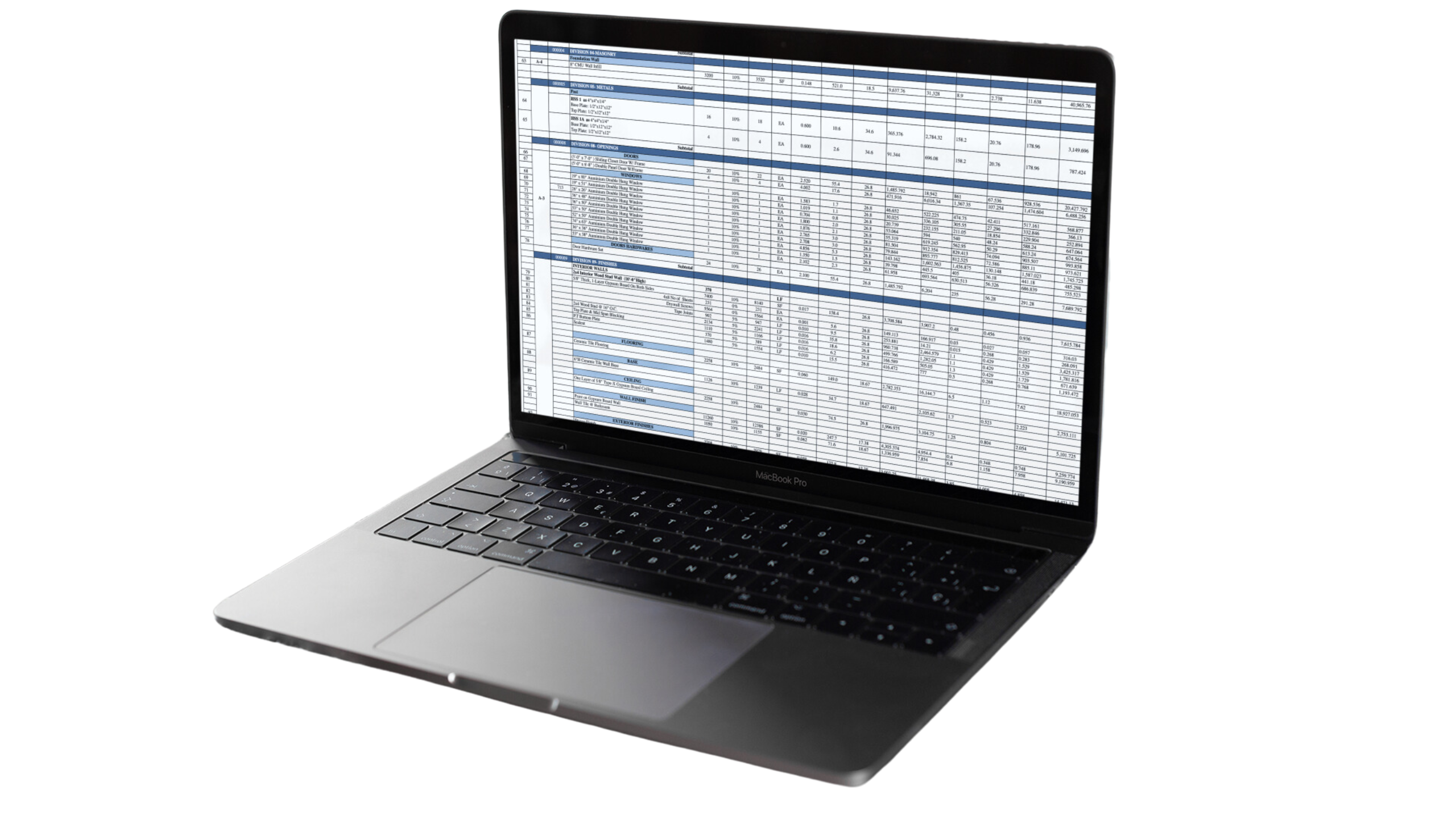
Question Answer
Frequently Asked Question
Prefabricated wall panels are factory-made wall sections designed for quick and efficient on-site assembly. Unlike traditional methods, they are built in controlled environments, reducing weather delays and minimizing material waste, making them faster to install and often more cost-effective.
In Florida, prefabricated wall panels typically cost between $12 and $30 per square foot. The price varies based on factors like panel type, thickness, and design complexity.
Different panel types have varying costs due to their specific characteristics:
Standard Wall Panels: $12 - $18 per square foot
Insulated Wall Panels: $18 - $25 per square foot
Custom Design Wall Panels: $22 - $30 per square foot
Panel sizes and thicknesses vary, with larger and thicker panels costing more. Common examples include:
4' x 8', 4 inches thick: $180 - $300 per panel
4' x 10', 6 inches thick: $220 - $360 per panel
4' x 12', 8 inches thick: $260 - $420 per panel
Materials significantly impact cost, with options like:
Structural Insulated Panels (SIPs): $8 - $15 per sq. ft.
Concrete Panels: $15 - $30 per sq. ft.
Wood Panels: $10 - $20 per sq. ft.
Metal Panels: $12 - $25 per sq. ft.
Installation costs range from $5 to $15 per square foot, depending on project complexity and whether additional equipment like cranes is needed. Standard installations typically cost between $5 and $10 per square foot.
Different building types have varying panel costs:
Residential (Single-Family): $10 - $20 per sq. ft.
Multi-Family (Apartments): $15 - $25 per sq. ft.
Commercial Buildings: $18 - $30 per sq. ft.
Industrial Buildings: $20 - $30 per sq. ft.
Popular types include:
Structural Insulated Panels (SIPs): Known for energy efficiency and strength.
Concrete Panels: Ideal for durability and fire resistance.
Wood Panels: Common for residential use, valued for aesthetics.
Metal Panels: Durable and moisture-resistant, used in commercial and industrial buildings.
Comprehensive Trade-Specific Estimates
At Estimate Florida Consulting, we offer detailed cost estimates across all major trades, ensuring no part of your project is overlooked. From the foundation to the finishing touches, our trade-specific estimates provide you with a complete and accurate breakdown of costs for any type of construction project.
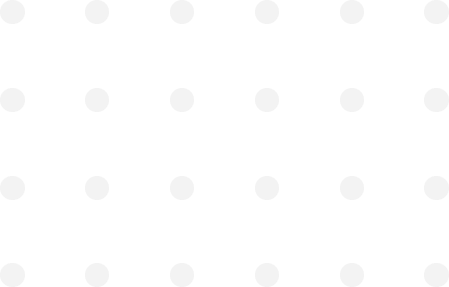
Testimonials
What Our Clients Say
We take pride in delivering accurate, timely, and reliable estimates that help contractors and builders win more projects. Our clients consistently praise our attention to detail, fast turnaround times, and the positive impact our estimates have on their businesses.
Estimate Florida Consulting has helped us win more bids with their fast and accurate estimates. We trust them for every project!
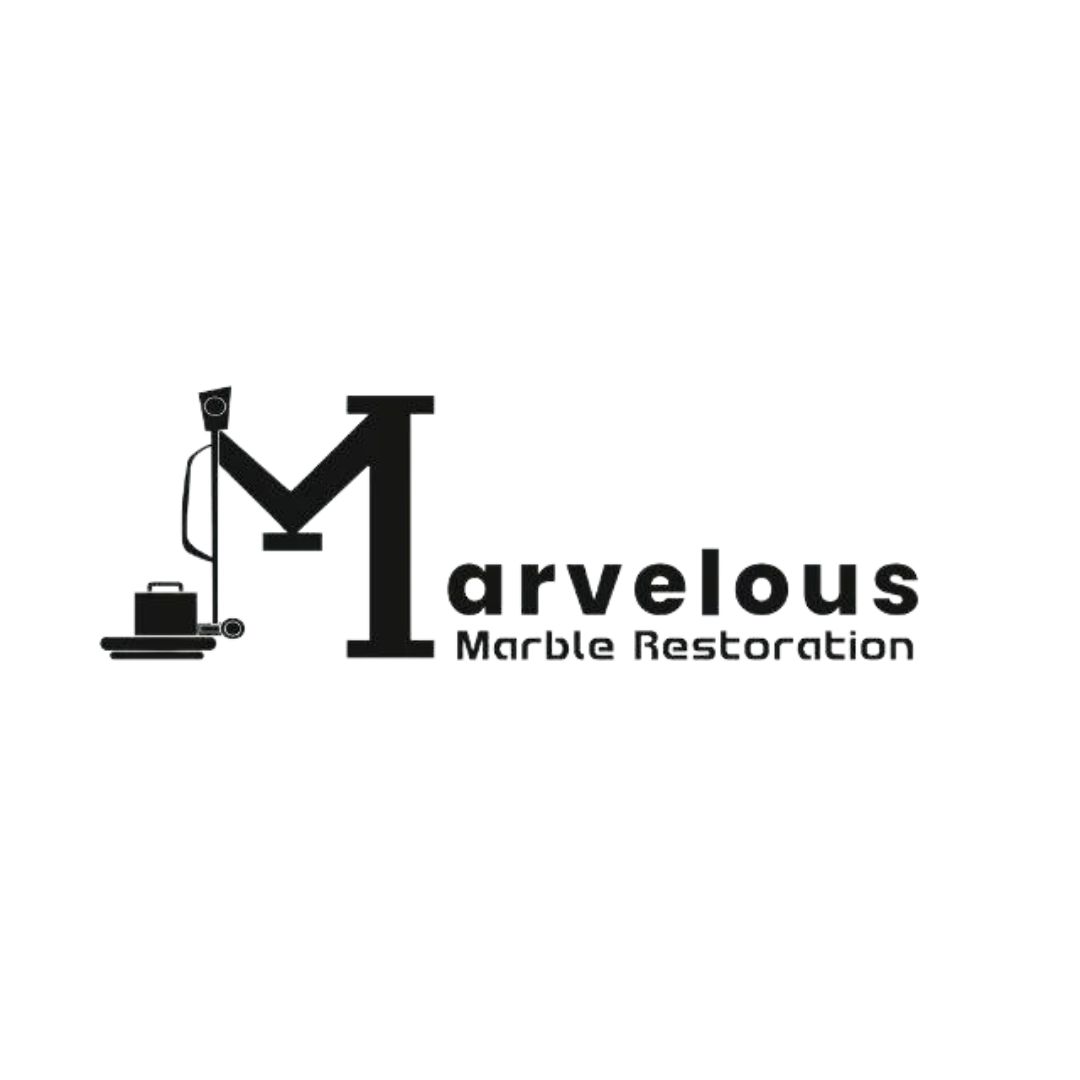
Steps to Follow
Our Simple Process to Get Your Estimate
01
Upload Plans
Submit your project plans, blueprints, or relevant documents through our online form or via email.
02
Receive Quotation
We’ll review your project details and send you a quote based on your scope and requirements.
03
Confirmation
Confirm the details and finalize any adjustments to ensure the estimate meets your project needs.
04
Get Estimate
Receive your detailed, trade-specific estimate within 1-2 business days, ready for your project execution.
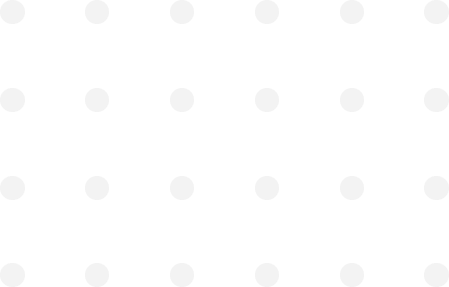