- Homepage
- Precast Concrete Wall Cost Estimator
Precast Concrete Wall Cost Estimator
Leading provider of precast concrete wall estimating.
Estimating the cost of precast concrete walls is a critical step in any construction project, and it requires a comprehensive understanding of various factors that influence the final budget. Precast concrete walls offer numerous advantages, including durability, customization options, and faster installation, but their cost can vary significantly based on factors such as wall dimensions, design complexity, material quality, labor, transportation, and finishing choices. To accurately estimate the cost, it’s essential to consider these variables carefully. Additionally, you can choose from different cost estimation methods, such as obtaining detailed quotes from contractors, using online calculators, or conducting a DIY estimation.
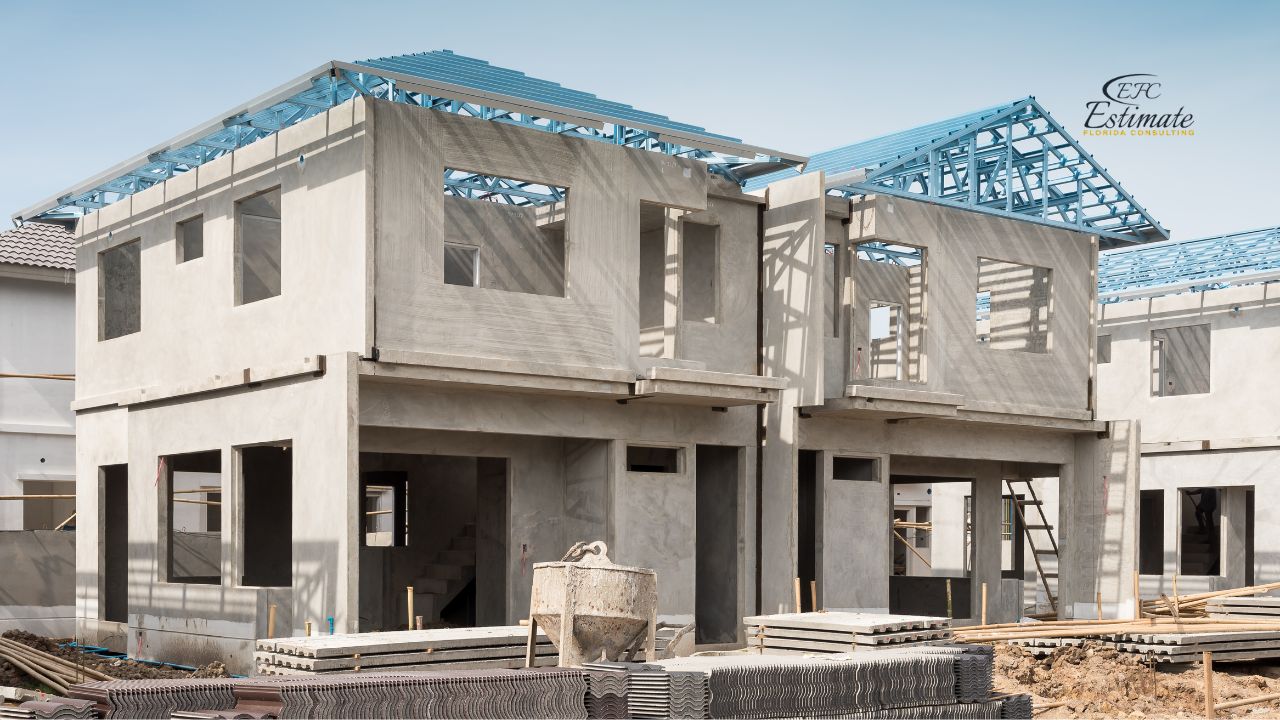
By taking these steps and factoring in potential contingencies, you can ensure that your project stays within budget while enjoying the benefits of precast concrete walls in terms of both cost-efficiency and longevity.
Understanding Precast Concrete Walls
What are Precast Concrete Walls?
Precast concrete walls represent a construction innovation wherein panels are meticulously fabricated in a controlled manufacturing environment before being transported to the construction site for installation. These panels are incredibly versatile and can be seamlessly integrated into a wide spectrum of applications, including residential, commercial, and industrial structures. Precast concrete panels offer several distinct advantages that contribute to their popularity and widespread use in the construction industry.
Advantages of Precast Concrete Walls
- Cost-Effective: One of the primary advantages of opting for precast concrete walls is their inherent cost-effectiveness. They require significantly less labor and time for installation compared to traditional construction methods, resulting in lower overall project costs.
- Durability: Precast concrete walls are renowned for their exceptional durability. These robust panels are engineered to withstand the harshest weather conditions, ensuring that they maintain their structural integrity and appearance over an extended period.
- Customization: Precast concrete walls offer a remarkable degree of customization. Builders and architects can tailor these panels to meet specific project requirements, adjusting variables such as size, texture, and color to achieve the desired aesthetic and functional outcomes.
- Speed of Construction: The rapid installation process associated with precast concrete walls significantly accelerates construction timelines. This efficiency can be especially advantageous in projects where time constraints are a critical factor, reducing overall project duration and associated costs.
Skilled Precast Concrete
Wall Expert?
How Much Does Precast Concrete Cost?
Determining the precise cost of precast concrete walls can be challenging due to various factors at play.
In general, you can anticipate that precast concrete walls will fall within the range of $25 to $50 per square foot. For a segment measuring 6 to 8 feet in height, budgeting should typically range from $150 to $350 per linear foot. The cost per cubic yard of precast concrete spans from $400 to $1250.
Precast concrete suppliers possess the capability to fashion structures in nearly any conceivable shape. Nevertheless, certain shapes are more prevalent than others. Let’s examine the expenses associated with some of the most popular concrete projects.
Type of precast concrete product
Average price you can expect to pay
Precast Concrete Product | Average Price Range |
Fence | Installed cost: $15 – $40 per square foot, depending on block type |
Light Pole Base | Installed cost: $500 – $900 per base |
Panel | Price varies by panel type, typically $150 – $500 per panel (excluding installation) |
Precast Concrete Retaining Wall Block | Installed cost: $15 – $30 per square foot |
Splash Concrete Blocks | Price per block: $10 – $40 |
Steps | 4-foot wide step cost (excluding installation): $200 |
Wall Caps | Cost per linear foot: $12 – $15 |
Cost of Architectural Precast Concrete
When it comes to architectural precast concrete, which combines structural integrity with decorative aesthetics, the production process involves additional intricacies. Architectural elements such as cornices and relief designs fall under this category.
So, what is the price range for precast concrete panels? Due to the complexity of crafting these panels, which require intricate casting molds and numerous design possibilities, the cost per square foot can vary significantly.
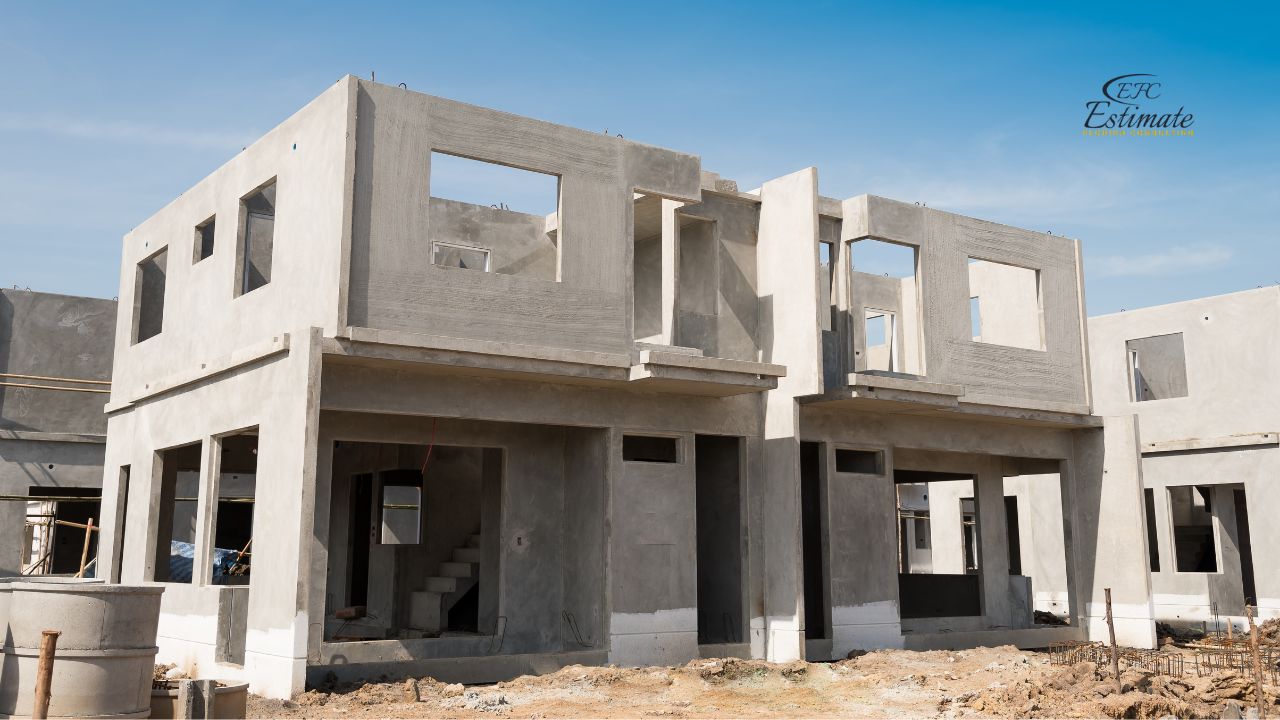
Precast Concrete Panels Pricing
Producing precast concrete panels is a more intricate process compared to precast blocks. These panels often demand a greater volume of concrete, as they are frequently employed for load-bearing purposes such as flooring. Additionally, they typically incorporate a higher level of steel reinforcement, necessitating surface treatments.
The expected cost for precast concrete panels falls within the range of $450 to $750 per cubic yard.
We Provide 3D Rendering Services!
For Precast Concrete Wall and Other Projects
Turnaround time is 1-2 days.
Win More Projects With Us
Precast Concrete Stairs Pricing
Precast concrete stairs are an excellent choice for building entrances, offering safety and aesthetic appeal while being relatively straightforward and speedy to install.
The starting price for precast concrete stairs begins at approximately $200 for each 4-foot-wide step. Please note that this price does not cover installation expenses.
Precast Concrete Pole Bases
Another popular application of precast concrete is for pole bases, often used for lighting fixtures. When factoring in installation costs, a lightweight precast concrete pole base typically falls within the price range of $500 to $900. The cost per square foot increases with the weight of the pole base.
Factors Affecting the Pricing of Precast Concrete Products
Shape
The shape of precast concrete is adaptable to meet customer specifications. Standard molds are available for common shapes. However, when customizing molds for more intricate shapes, the price per square foot tends to rise.
Dimensions
The length, height, and depth of a precast concrete product directly impact its overall cost. Taller concrete walls, for instance, require multiple formwork adjustments during shaping, resulting in extended processing time, increased labor, and a higher price per square foot.
Weight
The weight of a precast concrete product influences the equipment needed for installation and affects production costs, as heavier products require more materials during casting.
Delivery
Delivery costs are influenced by previous factors. Smaller and simpler precast concrete structures are easier to transport, whereas larger and more complex products incur higher delivery expenses.
Excavation
For projects involving precast concrete as basement or foundation walls, excavation may be necessary, adding an extra cost. This service typically costs up to $200 per cubic yard.
Concrete Cost Estimator
Consult our experts for a concrete cost estimate tailored to your project. Make informed decisions and budget effectively with our assistance.
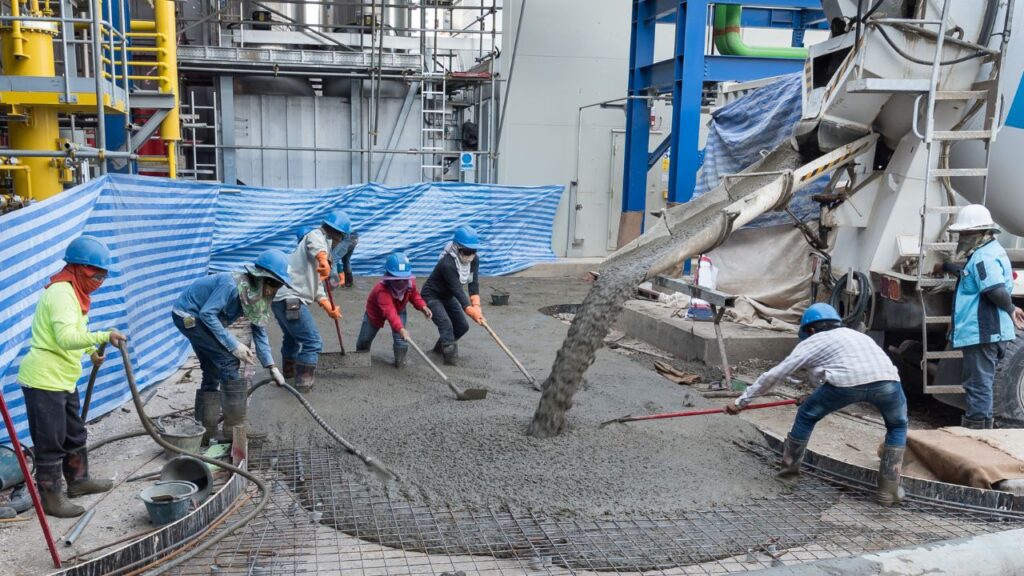
Engineering Fees
Structural precast concrete walls require approval from a structural engineer, incurring a fee ranging from $350 to $720.
Installation
Professional installation of precast concrete products comes at a higher cost but ensures proper setup. While self-installation may save money initially, it could lead to future repairs or adjustments.
Factors impacting installation costs include:
- Required building materials, including framing equipment.
- Delivery expenses.
- Drainage considerations for concrete wall installation.
- Involvement of a structural engineer.
- Potential excavation for basement, retaining, or foundation walls.
- Finishing
- Concrete walls can feature various finishes, such as plastering, paneling, or stamping, adding aesthetic appeal. The cost of concrete finishing ranges from $4 to $18 per square foot, depending on complexity.
Design
Precast concrete can be tailored to individual preferences. Standard pieces are more budget-friendly, while intricate and unique designs command higher costs.
Additional Costs
If using precast panels for wall construction, obtaining a building permit may be necessary, ensuring compliance with local building codes. Building permit costs vary by location and can reach up to $2,230.
Labor Costs
Installation Crew
The labor costs associated with precast concrete wall installation hinge on the size and complexity of the project. The number of workers required for installation is a pivotal factor. Smaller projects may only require a few skilled laborers, while larger and more intricate installations necessitate a larger crew. The skill level of the installation team is also a critical consideration. Skilled workers, though potentially commanding higher wages, bring a level of expertise and efficiency that can translate into cost savings in the long run. Their ability to ensure precise alignment, proper connection, and efficient handling of the precast panels can contribute significantly to the overall quality of the project.
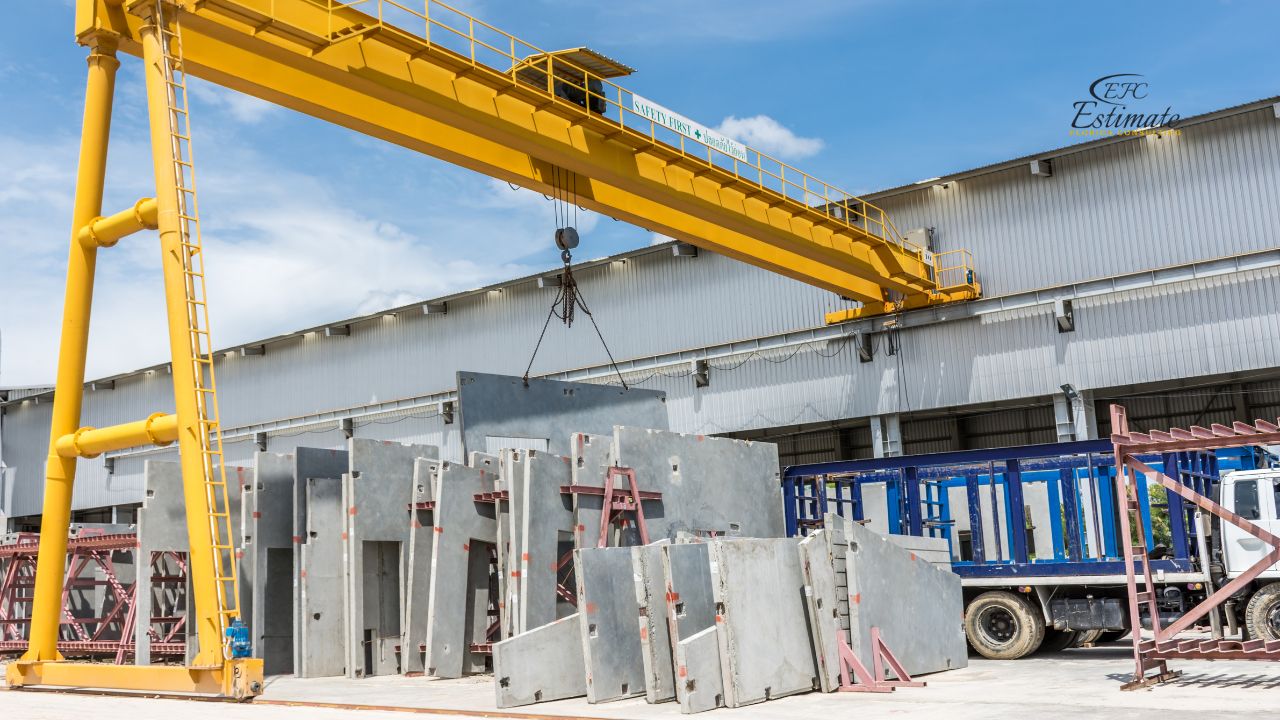
Equipment and Tools
The tools and equipment required for the installation of precast concrete walls can vary based on the project’s scope and complexity. Specialized tools are often necessary to handle the heavy and bulky precast panels efficiently. These tools may include lifting devices, scaffolding, concrete saws, and anchoring systems. The cost of acquiring or renting such equipment should be factored into the labor costs. Moreover, the skill and experience of the installation crew in using these tools can impact both the efficiency and safety of the installation process. While equipment costs can add to the overall project expense, they are essential for ensuring the successful and timely completion of the precast concrete wall installation.
Get 5 New Projects in the Next 7 Days With Our System
Budgeting Tips
Budgeting for a precast concrete wall project requires careful planning and consideration of potential variables that may impact the overall cost. To safeguard your project against unforeseen expenses, it’s highly recommended to allocate a contingency fund within your budget. This fund serves as a financial cushion to address unexpected costs that can arise during construction, such as minor design changes, material adjustments, or unforeseen site conditions. Additionally, to make informed financial decisions, it’s prudent to seek multiple quotes from reputable contractors. Comparing quotes not only helps in determining a reasonable and competitive price for the project but also allows you to evaluate the expertise and reliability of potential contractors. By incorporating these budgeting tips into your project planning, you can enhance your financial preparedness and ensure that your precast concrete wall project proceeds smoothly within the confines of your budget.
Conclusion
Estimating the cost of precast concrete walls is a complex but crucial aspect of any construction project. These walls offer a multitude of benefits, including cost-effectiveness, durability, customization, and rapid installation. However, the final budget can vary significantly due to factors such as wall dimensions, design intricacies, material choices, labor, transportation, and finishing options. To achieve an accurate cost estimation, it’s imperative to meticulously consider these variables. You have several methods at your disposal, from obtaining detailed contractor quotes to utilizing online calculators or conducting your own estimations. Incorporating a contingency fund into your budget can shield your project from unexpected expenses. Seeking multiple quotes from contractors ensures competitive pricing and allows you to assess their expertise. By integrating these strategies, you can confidently embark on your precast concrete wall project, maintaining financial control while reaping the rewards of cost-efficiency and long-lasting structural integrity.
Question Answer
Frequently Asked Question
Determining the precise cost of precast concrete walls can be challenging due to various factors at play. In general, you can anticipate that precast concrete walls will fall within the range of $25 to $50 per square foot. For a segment measuring 6 to 8 feet in height, budgeting should typically range from $150 to $350 per linear foot. The cost per cubic yard of precast concrete spans from $400 to $1250.
Several factors impact the pricing of precast concrete products, including the shape, dimensions, weight, delivery, excavation, engineering fees, installation, finishing, design, and additional costs such as permits. Each of these factors can influence the overall cost of your precast concrete project.
Precast concrete offers several advantages, including consistency, quick installation, compact footprint, weather resistance, durability, versatility, time and cost savings, and environmental sustainability. These benefits can contribute to both cost savings and a more efficient construction process.
To protect your budget, consider allocating a contingency fund to address unexpected costs that may arise during construction. Additionally, obtaining multiple quotes from reputable contractors can help you make informed financial decisions and ensure competitive pricing for your project.
Labor costs for precast concrete wall installation depend on the project's size and complexity. The number of workers required and their skill level play a crucial role. Smaller projects may require fewer laborers, while larger ones may need a more extensive crew. Skilled laborers, although potentially more expensive, can ensure quality work and cost savings in the long run.
The tools and equipment required for installation can vary based on the project's scope and complexity. Specialized tools such as lifting devices, scaffolding, concrete saws, and anchoring systems may be necessary. These equipment costs should be factored into the labor costs. The expertise of the installation crew in using these tools is also essential for an efficient and safe installation process.
Comprehensive Trade-Specific Estimates
At Estimate Florida Consulting, we offer detailed cost estimates across all major trades, ensuring no part of your project is overlooked. From the foundation to the finishing touches, our trade-specific estimates provide you with a complete and accurate breakdown of costs for any type of construction project.
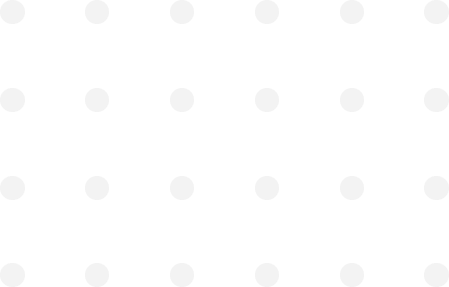
Testimonials
What Our Clients Say
We take pride in delivering accurate, timely, and reliable estimates that help contractors and builders win more projects. Our clients consistently praise our attention to detail, fast turnaround times, and the positive impact our estimates have on their businesses.
Estimate Florida Consulting has helped us win more bids with their fast and accurate estimates. We trust them for every project!
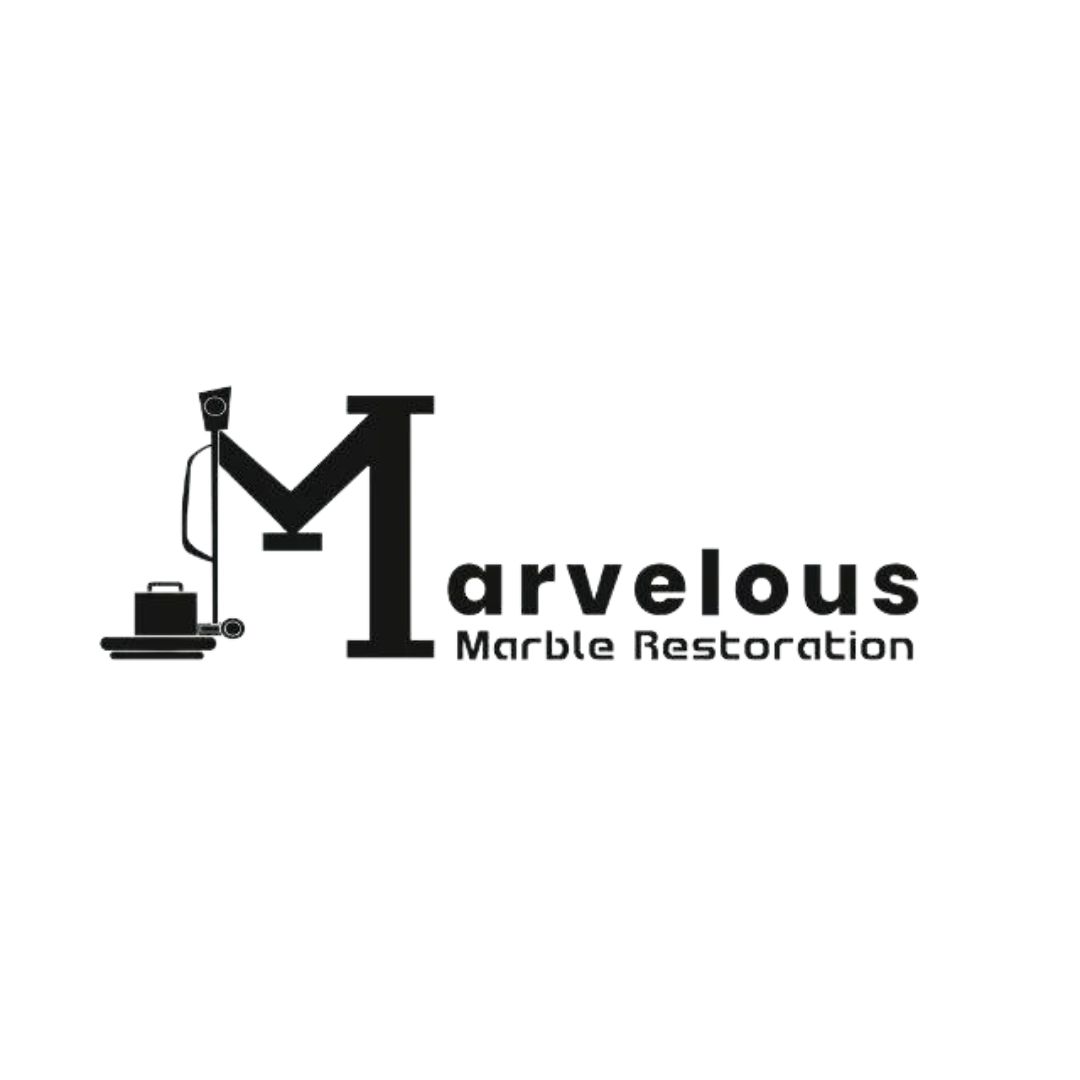
Steps to Follow
Our Simple Process to Get Your Estimate
01
Upload Plans
Submit your project plans, blueprints, or relevant documents through our online form or via email.
02
Receive Quotation
We’ll review your project details and send you a quote based on your scope and requirements.
03
Confirmation
Confirm the details and finalize any adjustments to ensure the estimate meets your project needs.
04
Get Estimate
Receive your detailed, trade-specific estimate within 1-2 business days, ready for your project execution.
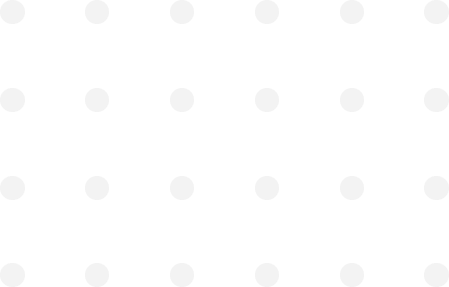