Boost Your Apartment Building Bids – Request a Precision Estimate!
- Accurancy
- Efficiency
- Transparency
- Customization
- Time Saving
- Professionalism
- Cost Control
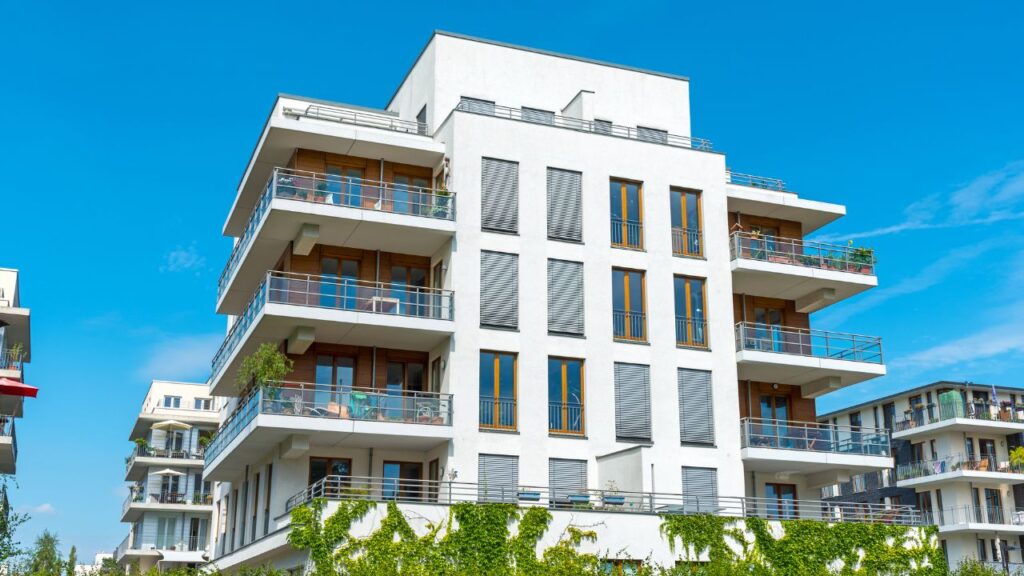
In the realm of modern construction, the choice of building materials plays a pivotal role in determining both the efficiency and cost-effectiveness of a project. One material that has gained significant traction in the construction of apartment buildings is precast concrete. The cost of incorporating precast concrete elements in apartment construction can vary, with general estimates ranging widely based on the specific precast components used. For precast concrete wall panels, costs may fall within the range of $60 to $150 or more per square foot, while precast concrete floors could range from $40 to $120 or more per square foot.
The cost for precast concrete beams and columns may vary from $80 to $200 or can be exceeded per linear foot. These figures are approximate and are subject to change based on factors such as project complexity, customization requirements, specialty finishes, and transportation costs.
Fully Insured Licensed
Hire Builder For Apartment Building
Make Informed Design Decisions Showcase Your Design Ideas
Get RenderingThe complexity of precast elements is intricately tied to the architectural design, with highly customized and detailed designs presenting unique challenges. In instances where architects envision intricate details or unconventional shapes, the production of precast elements demands advanced molds and specialized production processes. These sophisticated requirements inherently contribute to an increase in overall costs. The need for precision and attention to detail in crafting molds tailored to complex designs amplifies the intricacy of the manufacturing process. Consequently, the expenses incurred in producing precast elements for projects characterized by high design complexity can escalate notably. Architects and project stakeholders must carefully weigh the aesthetic benefits of intricate designs against the associated cost implications to achieve a harmonious balance between architectural vision and budgetary considerations.
The logistics surrounding the transportation and installation of precast elements are pivotal aspects that significantly influence overall project costs. The expenses incurred in transporting these elements from manufacturing facilities to the construction site are contingent on factors such as transportation distance, size, and weight of the components. Larger or heavier precast elements may require specialized transportation arrangements, further adding to the logistical complexities and associated costs. Additionally, the process of lifting and precisely placing these elements into their designated positions demands sophisticated equipment, skilled labor, and careful coordination. The cost of transportation and installation should be meticulously factored into the project budget, and strategies for optimizing these processes, such as on-site assembly or strategic delivery scheduling, should be explored to mitigate potential cost overruns.
The scale of a construction project, in terms of the overall volume of precast elements required, plays a pivotal role in determining costs. Larger projects often benefit from economies of scale, where the per-unit cost of precast elements decreases as the volume increases. This cost-effectiveness in larger-scale projects is attributed to streamlined production processes, bulk material purchasing, and optimized manufacturing efficiencies. Conversely, smaller projects with limited precast element requirements may experience relatively higher per-unit costs.
Project planners and developers should carefully evaluate the project’s scale to explore opportunities for cost savings associated with economies of scale while considering the specific requirements and constraints of the construction endeavor.
The aesthetic considerations and desired finishes of precast elements introduce another dimension of cost variability. Basic finishes, such as exposed aggregate or smooth surfaces, generally incur lower costs due to their standard nature. However, when projects call for specialized finishes, intricate textures, or decorative features, the costs can escalate considerably. Achieving unique aesthetics may involve additional labor, specialized materials, and meticulous craftsmanship, all of which contribute to an augmentation of expenses. Project stakeholders should engage in a comprehensive discussion during the design phase to align aesthetic aspirations with budgetary considerations. Collaborating with precast concrete manufacturers and design professionals can provide valuable insights into the cost implications of specific finishes, enabling informed decisions that balance aesthetic objectives with financial feasibility.
Here’s the information presented in a table format:
Factor | Cost Implication | Cost Range/Rate |
Design Complexity | For simple designs: 5% to 15% additional cost | For intricate designs: 20% to 30% additional cost |
Transportation | Average transportation cost: $5 to $15+ per mile per ton | |
Installation | Average installation cost: $500 to $1,500 or more per ton | |
Volume and Scale | Smaller projects: $150 to $200 or more per square foot | Larger projects: $100 to $150+ per square foot |
Finishes and Aesthetics | Basic finishes: $5 to $10 + per square foot | Specialized finishes: $15 to $30+ per square foot or more |
Note: The costs provided are approximate and can vary based on project-specific details, location, and market conditions. These figures are meant to serve as general guidelines.
From small to large projects, residential to commercial, we’re here to help you win. Fast results guaranteed.
Here’s the information presented in a table format:
Precast Concrete Element | Cost Range per Unit | Description |
Precast Concrete Panels | $60 to $150 or more per square foot | Manufacturing, transportation, and installation of panels for walls or facades. |
Precast Concrete Beams and Columns | $80 to $200 or more per linear foot | Production and installation of beams and columns providing structural support. |
Precast Concrete Slabs | $80 to $120+ per square foot | Manufacturing, transportation, and installation of slabs for flooring systems. |
Stairs and Landings | $150 to $300+ per linear foot | Fabrication and installation of precast concrete stairs and landings. |
Custom Precast Elements | Varies widely based on design | Customized elements like decorative panels, facades, or unique architectural features, with costs depending on complexity. |
Note: The costs provided are general estimates and can vary based on specific project requirements, location, and market conditions.
Precast concrete is a construction product produced by casting concrete in a reusable mold or form, which is then cured in a controlled environment, transported to the construction site, and lifted into place for assembly. The precasting process allows for the creation of a variety of structural components, such as columns, beams, panels, and slabs, with high precision and quality.
The speed of construction represents a paramount advantage of utilizing precast concrete components in building projects. Unlike traditional construction methods where components are cast in place on-site, precast elements are manufactured off-site concurrently with on-site activities like foundation preparation. This simultaneous process drastically reduces construction timelines. Once transported to the construction site, precast elements can be swiftly assembled, contributing to the expeditious completion of the overall building process.
This efficiency not only accelerates project delivery but also minimizes disruptions to neighboring environments, making precast concrete an attractive choice for projects with time-sensitive requirements.
Precast concrete construction offers a superior level of quality assurance, a critical factor in ensuring the longevity and durability of structures. The controlled environment of precasting facilities provides optimal conditions for the curing of concrete components. This controlled setting minimizes the impact of external factors, such as adverse weather conditions, which can compromise the curing process in traditional cast-in-place methods. As a result, precast concrete components exhibit higher quality and consistency, with fewer defects. The rigorous quality control measures inherent in precasting contribute to a final product that surpasses the standards achievable through traditional on-site casting, providing builders and developers with confidence in the durability and performance of the constructed environment.
One of the significant advantages of precast concrete construction is the higher degree of cost predictability compared to traditional methods. The manufacturing process allows for precise cost estimation, enabling accurate budgeting from the project’s inception. This predictability minimizes the likelihood of budget overruns due to unexpected on-site challenges or delays. Project stakeholders can benefit from a comprehensive understanding of costs, facilitating more informed decision-making and financial planning. The transparency in cost estimation is a key factor in the growing preference for precast concrete, particularly in projects where adherence to a predetermined budget is of utmost importance.
The utilization of precast concrete components results in a substantial reduction in on-site labor requirements, offering both economic and safety benefits. Many precast elements arrive on-site preassembled, minimizing the need for extensive on-site labor for intricate construction tasks. This reduction in labor demands not only lowers overall construction costs but also contributes to a safer and more organized construction site. The decreased reliance on on-site labor also aligns with contemporary construction trends focused on efficiency and enhanced safety protocols. As a result, precast concrete construction becomes an attractive option for projects seeking to optimize costs while ensuring a streamlined and secure work environment.
The production of precast concrete is inherently more energy-efficient compared to traditional on-site casting methods. The controlled environment of precasting facilities allows for better management of resources, leading to reduced waste and energy consumption. The optimized use of materials and energy in precast concrete production contributes to a more sustainable and environmentally friendly construction process. As the construction industry increasingly emphasizes eco-conscious practices, the energy efficiency inherent in precast concrete aligns with broader sustainability goals, making it a choice that not only accelerates construction but also minimizes the environmental impact associated with traditional building methods.
Optimizing the design phase to balance aesthetics and functionality can significantly impact costs. Prioritize designs that are visually appealing yet feasible for precast production. Simplifying intricate details, while maintaining the overall aesthetic, can lead to cost savings in mold creation and production processes. Engage architects, engineers, and precast manufacturers early in the design process to ensure a harmonious blend of creativity and cost-effectiveness.
Careful planning of transportation logistics can mitigate costs associated with moving precast elements from manufacturing facilities to the construction site. Consideration of transportation distance, size, and weight of components is crucial. Exploring options such as on-site assembly or strategic delivery scheduling can optimize transportation, reducing expenses related to specialized transportation arrangements and potential delays.
Leverage the benefits of economies of scale, especially in larger construction projects. The per-unit cost of precast elements tends to decrease as the overall volume increases. By accurately estimating the required precast elements based on project scale, developers can capitalize on cost-effectiveness in production processes, bulk material purchasing, and manufacturing efficiencies. Strategic planning to align project scale with economies of scale is essential for optimizing costs.
Collaboration during the design phase to align aesthetic aspirations with budgetary constraints is crucial. While specialized finishes and decorative features enhance visual appeal, they often incur higher costs. Balancing the desired aesthetics with cost considerations is essential. Engage in thorough discussions with design professionals and precast concrete manufacturers to make informed decisions that meet aesthetic objectives without compromising financial feasibility.
Leveraging technology for monitoring and optimizing processes can contribute to cost savings. Implementing sensors, imaging technologies, and data analytics during the manufacturing and transportation phases can provide real-time insights, enhancing efficiency and reducing the likelihood of errors. Embracing technology-driven solutions can lead to streamlined operations, minimized waste, and improved overall cost-effectiveness in precast concrete construction.
The cost of precast concrete wall panels can vary, but a general estimate falls within the range of $60 to $150 or more per square foot. Actual costs depend on factors such as design complexity, customization, and finishes.
Design complexity, especially with intricate and customized designs, can significantly increase costs. For simple designs, the additional cost may range from 5% to 15%, while intricate designs may incur an additional cost of 20% to 30%.
Strategic transportation management is crucial for cost mitigation. Careful planning, considering factors like transportation distance, size, and weight of components, can help optimize costs. Exploring options such as on-site assembly or strategic delivery scheduling is recommended.
Larger construction projects often benefit from economies of scale, leading to a decrease in the per-unit cost of precast elements. The cost-effectiveness in larger-scale projects is attributed to streamlined production processes, bulk material purchasing, and optimized manufacturing efficiencies.
Technology integration can contribute to cost savings by monitoring and optimizing processes. Implementing sensors, imaging technologies, and data analytics during the manufacturing and transportation phases provides real-time insights, enhancing efficiency and reducing the likelihood of errors. Embracing technology-driven solutions leads to streamlined operations and improved overall cost-effectiveness.
Here I am going to share some steps to get your precast concrete cost for apartment construction estimate report.
You can send us your plan on info@estimatorflorida.com
Before starting your project, we send you a quote for your service. That quote will have detailed information about your project. Here you will get information about the size, difficulty, complexity and bid date when determining pricing.
Our team will takeoff and estimate your project. When we deliver you’ll receive a PDF and an Excel file of your estimate. We can also offer construction lead generation services for the jobs you’d like to pursue further.
561-530-2845
info@estimatorflorida.com
Address
5245 Wiles Rd Apt 3-102 St. Pete Beach, FL 33073 United States
561-530-2845
info@estimatorflorida.com
Address
5245 Wiles Rd Apt 3-102 St. Pete Beach, FL 33073 United States
All copyright © Reserved | Designed By V Marketing Media | Disclaimer