Concrete Cost Estimator
Consult our experts for a concrete cost estimate tailored to your project. Make informed decisions and budget effectively with our assistance.
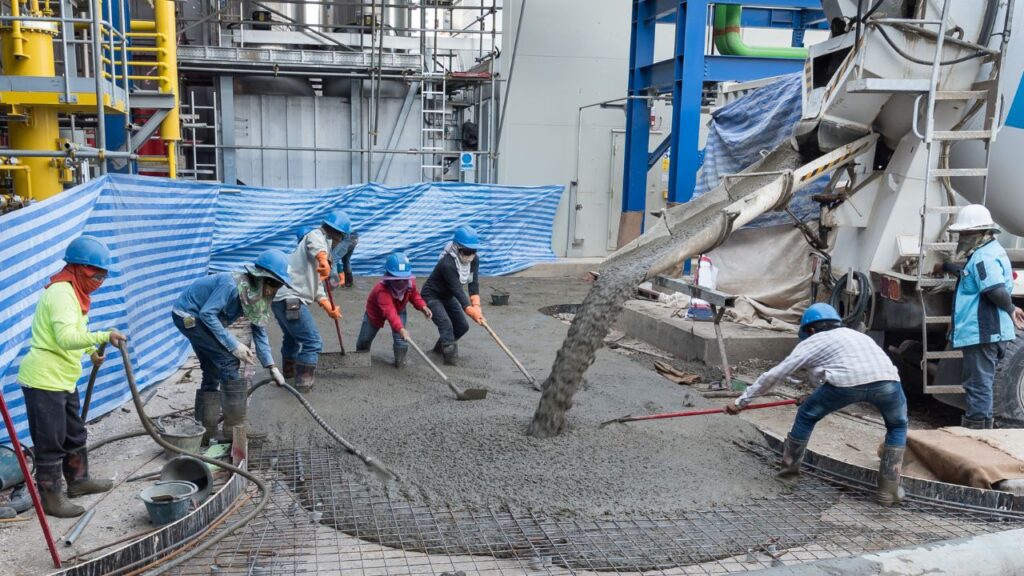
The role of a precast concrete building cost estimator cannot be overstated when embarking on a construction project involving this innovative building material. Precast concrete has gained immense popularity due to its numerous advantages, including cost-efficiency, quality control, and environmental benefits. Accurately estimating the costs associated with precast concrete is essential to ensure a project’s success. A skilled cost estimator takes into account various factors such as design complexity, size and quantity of precast elements, transportation, labor, equipment, overhead, and profit margins.
They collaborate closely with architects, engineers, and contractors to create a comprehensive estimate that aligns with the project’s budget and objectives. A precise cost estimate not only prevents financial surprises but also facilitates efficient resource allocation and project planning, ultimately contributing to the seamless execution of precast concrete construction projects.
Precast concrete is a construction method that involves the fabrication of concrete components in a controlled environment, typically a specialized factory, far from the actual construction site. These components encompass a wide range of building elements, such as walls, beams, columns, slabs, and architectural details. Unlike traditional cast-in-place concrete, which is poured and cured on-site, precast concrete elements are cast, cured, and quality-checked in a factory setting before being transported to the construction location. This controlled production environment allows for precise customization, quality assurance, and the integration of various architectural and structural features.
Concrete Cost Estimator
Consult our experts for a concrete cost estimate tailored to your project. Make informed decisions and budget effectively with our assistance.
Precast concrete construction offers a plethora of advantages, yet comprehending the intricacies of cost estimation is imperative for a successful project. The process of estimating the cost of precast concrete buildings necessitates a meticulous evaluation of various factors that exert influence on project expenses. By delving into these critical aspects, you can acquire a more profound insight into the methodologies for strategic planning and budgeting in the realm of precast concrete construction.
The complexity of your project’s design stands as a cornerstone in the determination of precast concrete costs. This encompasses a broad spectrum, including architectural intricacies, the configuration of shapes, and the selection of surface finishes. Precast concrete undoubtedly provides unparalleled design versatility, enabling the realization of diverse creative visions. However, it’s pivotal to recognize that intricate designs can amplify costs due to the heightened precision and expertise demanded during the manufacturing process. Elaborate architectural features, ornate facades, decorative elements, and distinctive geometries often necessitate specialized molds and intricate casting techniques. Consequently, these factors contribute to an elevation in overall expenses. When venturing into precast concrete construction, maintaining a delicate equilibrium between aesthetic aspirations and budgetary constraints is paramount.
The dimensions and quantity of precast elements requisite for your project wield substantial influence over the overarching cost structure. Larger precast components inherently entail a more significant consumption of materials and resources, inherently leading to heightened expenditures. Additionally, the quantity of precast elements, such as panels, beams, columns, or other architectural and structural components, holds a direct correlation with the cumulative project cost. A judicious approach to cost management involves close collaboration with architects and engineers, fostering a synergy that allows for the optimization of precast element design and dimensions. This collaborative endeavor ensures that precast elements meet rigorous structural criteria while simultaneously adhering to predetermined budgetary boundaries.
The intricacies of transporting and installing precast elements from the manufacturing facility to the construction site wield considerable influence over cost considerations. The geographical distance between the manufacturing facility and the construction site plays a pivotal role in determining transportation expenses.
Extended transportation distances translate into heightened costs, encompassing increased fuel consumption, transportation fees, and potential logistical challenges, such as traffic-related delays.
Furthermore, the complexity of the installation process exerts a tangible impact on cost estimation. Precast elements endowed with intricate connections, unique assembly requisites, or specialized load-bearing attributes may necessitate the utilization of specialized equipment and the engagement of highly skilled labor, consequently impinging on the overall project budget. To mitigate these cost-inflating factors, astute project planning should include the assessment of the manufacturing facility’s proximity to the construction site and the meticulous orchestration of installation processes.
The first and foremost component in the estimation process is the calculation of building construction material costs. This involves a meticulous assessment of the raw materials required for the production of precast elements. Central to this calculation is the concrete mix, which serves as the fundamental building block of precast components. The estimation takes into account the type and quality of concrete mix needed, considering factors such as strength requirements, durability, and any specific additives or admixtures required to meet project specifications. Additionally, reinforcement materials, such as steel bars or mesh, are factored in to ensure structural integrity. The judicious selection of materials while adhering to quality standards is pivotal in controlling costs while maintaining the desired level of performance and durability.
Estimating labor costs is a multifaceted endeavor that encompasses various stages of the precast concrete project. It commences with the manufacturing phase, where skilled labor is engaged in the casting, curing, and quality assurance processes. The transportation phase necessitates labor for loading, securing, and unloading precast elements, with a keen focus on ensuring safe and damage-free transport. Finally, during the on-site installation phase, labor costs extend to the assembly of precast elements, which demands precision and expertise. Estimating labor costs entails not only quantifying the workforce required but also considering factors such as wage rates, labor productivity, and potential overtime expenses. Proper workforce management is essential to optimize labor costs while adhering to project timelines and quality standards.
Precast concrete manufacturing and installation often require specialized equipment to ensure efficiency, precision, and safety. Estimating equipment costs involves factoring in expenses related to the acquisition, maintenance, and operation of machinery and tools specific to precast concrete construction. This encompasses a wide range of equipment, including concrete mixers, molds, curing chambers, cranes, lifting devices, and transportation vehicles. The selection of appropriate equipment, along with meticulous planning for its utilization, is instrumental in minimizing equipment-related costs while maximizing productivity and safety on the construction site.
In any construction project, overhead costs are an integral component of cost estimation. For precast concrete construction, this includes expenses related to the operation of the manufacturing facility, such as rent, utilities, insurance, and administrative costs. Overhead costs also encompass expenses associated with quality control, testing, and compliance with safety regulations. Additionally, a reasonable profit margin is factored into the estimation process to ensure that the project remains financially viable for the contractor or manufacturer. Striking the right balance between covering overhead costs and achieving a reasonable profit margin is a critical aspect of successful cost estimation in precast concrete construction.
Achieving precise cost estimation in precast concrete construction is a pivotal aspect of project planning and management. To enhance the accuracy of your cost estimates and ensure the financial success of your project, consider the following tips:
Engaging with experienced precast concrete contractors and engineers is an invaluable step in achieving accurate cost estimates. These professionals possess a wealth of knowledge and practical insights into the intricacies of precast concrete construction. Collaborating with experts allows for a thorough evaluation of project-specific factors, such as design complexities, material selection, and construction methodologies. Their input can help you anticipate potential challenges, identify cost-saving opportunities, and tailor your cost estimate to the unique requirements of your project.
Furthermore, expert guidance ensures that your estimate aligns with industry standards and best practices, enhancing the overall reliability of your financial planning.
Incorporating specialized software designed for precast concrete cost estimation is a modern and efficient approach to streamline the estimation process. Estimation software offers a range of tools and features that facilitate precise calculations and reduce the risk of errors. These software solutions typically encompass databases of precast concrete materials, labor costs, equipment rates, and regional pricing data, allowing for real-time cost analysis and adjustments. Additionally, they provide templates and standardized formats for creating detailed cost estimates, ensuring consistency and clarity in your documentation. By harnessing the power of estimation software, you not only expedite the estimation process but also enhance its accuracy, providing a solid foundation for financial planning and decision-making throughout your precast concrete construction project.
Developing a precise cost estimate for precast concrete construction is a pivotal phase in project planning. To ensure that your estimate is both comprehensive and accurate, it’s essential to follow a structured approach that encompasses a range of critical factors. Here, we outline the step-by-step process for creating an accurate cost estimate for your precast concrete building project:
Begin by conducting a meticulous assessment of your project. This foundational step involves a comprehensive understanding of the project’s intricacies, including the architectural and structural design, required materials, and the overall scope of work. Additionally, consider any unique requirements or challenges specific to your project that may have a significant impact on costs. This initial assessment sets the stage for the subsequent estimation process by providing a holistic view of the project’s key parameters.
Material costs constitute a substantial portion of the overall project budget. Calculate these costs with precision by considering the specific materials required for your precast concrete elements. This includes the cost of the concrete mix, reinforcing materials (such as steel bars or mesh), and any additional materials specified in the project design. Be vigilant in accounting for variations in material costs based on design specifications, as different concrete mixes and reinforcement types can have varying price points.
Labor and equipment expenses are integral components of any construction project, and precast concrete construction is no exception. Estimate labor costs based on the project’s complexity and the number of workers required for tasks ranging from manufacturing to transportation and on-site installation. Additionally, consider the equipment needed for manufacturing and installation and factor in associated costs, including equipment rental if applicable. It’s crucial to assess the skill levels required for various labor tasks, as specialized skills may command higher wages, impacting your labor cost estimation.
Transportation logistics play a pivotal role in precast concrete construction, particularly when conveying components from the manufacturing facility to the construction site. When estimating transportation costs, account for the distance between these locations, fuel expenses, logistical considerations, and any permits or escorts required for oversized or overweight components. Ensuring a thorough understanding of transportation-related expenses is essential for an accurate cost estimate.
The unpredictable nature of construction projects necessitates the inclusion of a contingency allowance in your cost estimate. Allocate a percentage of the total cost as a contingency to account for unforeseen expenses, adjustments, or challenges that may arise during construction. Additionally, consider overhead costs related to project management and administration, including items such as rent, insurance, utilities, and quality control measures.
With all cost components meticulously assessed, combine them to arrive at the final cost estimate. In this final calculation, be sure to incorporate a margin for profit. This profit margin not only ensures the financial viability of your business but also serves as a buffer to cover unexpected expenses or market fluctuations that may impact project costs.
A precast concrete building cost estimator plays a crucial role in construction projects involving precast concrete. Their primary responsibility is to accurately estimate the costs associated with utilizing precast concrete. This includes assessing various factors such as material costs, labor, transportation, equipment, overhead, and profit margins. Their expertise ensures that project budgets align with objectives and that resources are efficiently allocated.
Precast concrete offers several advantages, including cost-efficiency, quality control, and environmental benefits. It can reduce labor costs and construction timelines, maintain strict quality standards, and minimize waste. Precast concrete also reduces environmental impact by generating less on-site waste and emissions compared to traditional construction methods.
Several factors influence the cost of precast concrete construction, including design complexity, the size and quantity of precast elements, and transportation and installation logistics. Design intricacies, larger components, and longer transportation distances can lead to increased costs. Specialized labor and equipment may also impact expenses.
To create an accurate cost estimate, follow a structured approach. Begin with a detailed project assessment, calculate material costs, estimate labor and equipment expenses, factor in transportation costs, include a contingency for unforeseen expenses, consider overhead, and add a profit margin. Combining these elements will result in a comprehensive cost estimate.
Collaborating with experienced precast concrete contractors and engineers is essential to achieving accurate cost estimates. These experts provide valuable insights into design complexities, material selection, and construction methodologies. Their guidance ensures that estimates align with industry standards and best practices, contributing to reliable financial planning.
Yes, specialized software is available for precast concrete cost estimation. These software solutions include databases of precast concrete materials, labor costs, equipment rates, and regional pricing data. They streamline calculations, reduce errors, and offer templates for creating detailed cost estimates, enhancing accuracy and efficiency in the estimation process.
A contingency allowance is essential because construction projects are subject to unforeseen challenges and changes. Allocating a percentage of the total cost as a contingency ensures that funds are available to address unexpected expenses, adjustments, or issues that may arise during the project. It serves as a financial safety net.
To optimize costs while maintaining quality, collaborate closely with architects and engineers to optimize precast element design and sizing. Consider value engineering to identify cost-saving opportunities. Additionally, efficient project management, careful equipment selection, and skilled labor management are essential for cost control.
Precast concrete aligns with sustainable building practices by reducing construction waste and minimizing environmental impact. It generates less waste material on-site since most fabrication and assembly processes occur in a controlled environment. The reduction in on-site construction time also contributes to fewer emissions, noise pollution, and disruption to local ecosystems.
To ensure your project stays within budget, create a comprehensive and accurate cost estimate, monitor expenses throughout the project, and adapt to any changes or challenges promptly. Effective project management, regular financial assessments, and prudent decision-making are essential for maintaining budgetary control.
The role of a precast concrete building cost estimator is paramount in the realm of construction projects involving this innovative building material. Precast concrete has rightfully earned its popularity due to its cost-efficiency, stringent quality control, and commendable environmental benefits. Accurate cost estimation is the cornerstone of a successful project, and a skilled estimator considers an array of factors, from design complexity to transportation logistics, in order to create a comprehensive and precise estimate. Collaborative efforts with architects, engineers, and contractors ensure that the estimate aligns with the project’s objectives and budget, paving the way for efficient resource allocation and project planning. A meticulous cost estimate not only shields against financial surprises but also facilitates the seamless execution of precast concrete construction projects, harnessing the full potential of this remarkable building material.
Here I am going to share some steps to get your concrete cost estimate report.
You can send us your plan on info@estimatorflorida.com
Before starting your project, we send you a quote for your service. That quote will have detailed information about your project. Here you will get information about the size, difficulty, complexity and bid date when determining pricing.
We do concrete estimating and prepare a detailed report for your project. At last, you finalize the report and finish the project.
561-530-2845
info@estimatorflorida.com
Address
5245 Wiles Rd Apt 3-102 St. Pete Beach, FL 33073 United States
561-530-2845
info@estimatorflorida.com
Address
5245 Wiles Rd Apt 3-102 St. Pete Beach, FL 33073 United States
All copyright © Reserved | Designed By V Marketing Media | Disclaimer