Boost Your Warehouse Bids – Request a Precision Estimate!
- Accurancy
- Efficiency
- Transparency
- Customization
- Time Saving
- Professionalism
- Cost Control
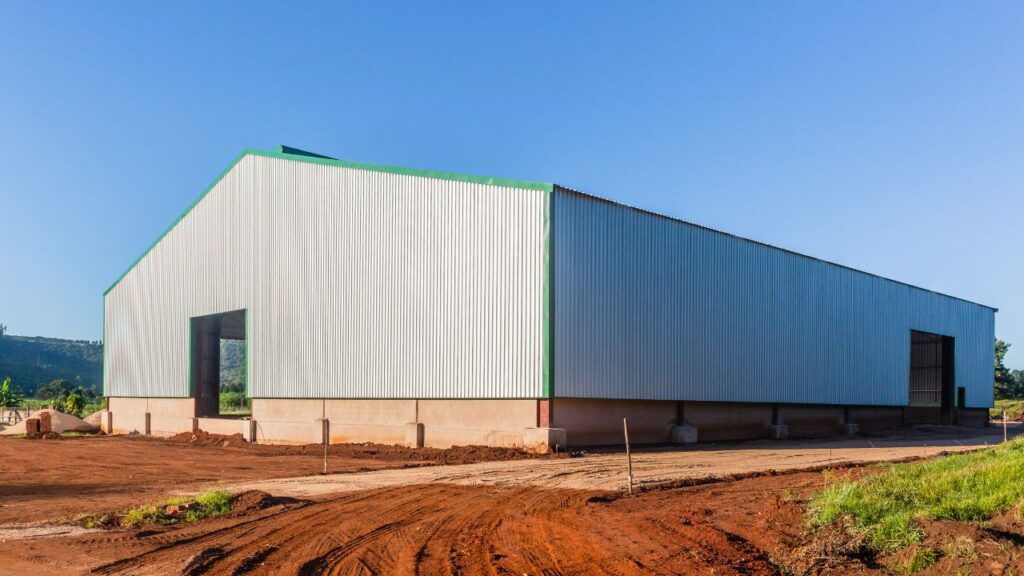
Warehouse construction plays a pivotal role in the logistics and supply chain industry, and one method gaining popularity is pre-cast concrete construction. The use of pre-cast components offers numerous advantages, including speed of construction, durability, and design flexibility. However, determining the cost of a pre-cast warehouse involves considering various factors. In this guide, we’ll delve into the key elements to help you estimate the cost of constructing a pre-cast warehouse building.
The foundation serves as the backbone of any building, and for pre-cast warehouses, its significance cannot be overstated. The choice between a simple slab-on-grade or a more intricate foundation system plays a pivotal role in determining overall costs. Factors such as soil conditions, adherence to local building codes, and the incorporation of features like drainage systems all contribute to the comprehensive expenses associated with the foundation. Assessing these aspects meticulously ensures a solid and stable base for the pre-cast warehouse, setting the stage for the structural integrity of the entire building.
Make Informed Design Decisions Showcase Your Design Ideas
Get RenderingAt the heart of pre-cast construction lies the utilization of pre-manufactured concrete components, offering efficiency and precision. Estimating costs in this realm involves a detailed consideration of the quantity and specifications of these components, encompassing pre-cast panels, beams, columns, and slabs. The size, finish, and detailing of each element have direct implications on both material and labor costs. The advantages of customization and controlled manufacturing processes must be weighed against the associated expenses to optimize the cost-efficiency of the pre-cast concrete components.1
While pre-cast construction is renowned for its expedited timeline, skilled labor remains a critical component for ensuring the proper installation of components. Labor costs are subject to variations based on the complexity of the project, the requirement for specialized skills, and the prevailing local wage rates. Efficient installation procedures are paramount not only for meeting project deadlines but also for upholding the structural integrity and overall quality of the pre-cast warehouse.
Before the first pre-cast element is put in place, the site must undergo thorough preparation, involving processes such as clearing, grading, and utilities installation. The costs associated with site preparation are contingent on factors including site accessibility, soil conditions, and the extent of utility connections needed. A well-prepared site lays the foundation for a streamlined and effective construction process, minimizing disruptions and ensuring optimal conditions for subsequent phases.
Investing in a robust structural design is indispensable for pre-cast warehouses. Professional structural engineering services encompass the design and analysis of pre-cast components, incurring additional costs that are justified by the assurance of safety, compliance with building codes, and the long-term durability of the structure. The meticulous engineering of these components ensures that the pre-cast warehouse not only meets but exceeds industry standards, providing a reliable and resilient facility.
Navigating the intricate regulatory landscape is integral to the construction process. Acquiring the necessary permits and ensuring strict compliance with local building codes are essential steps that contribute to overall costs. Budgeting for fees associated with permitting and engaging with regulatory authorities early in the planning process is crucial to prevent delays and complications during the construction of the pre-cast warehouse.
The choice of roofing and cladding materials is a significant cost factor with implications for both aesthetics and functionality. Factors such as insulation, weatherproofing, and design considerations play a crucial role in selecting roofing and cladding systems. While pre-cast construction offers design flexibility, the decision on materials directly influences both initial construction costs and long-term maintenance expenses. Striking a balance between functionality, durability, and budget considerations is vital for an efficient and cost-effective roofing and cladding solution.
Recognizing the inherent uncertainties in construction projects, a contingency budget is a prudent inclusion in the overall project plan. This budget, typically calculated as a percentage of the total project cost, acts as a financial safety net to address unforeseen challenges or additional requirements that may arise during the construction of the pre-cast warehouse. The contingency budget enhances the project’s resilience to unexpected circumstances, allowing for adaptive and informed decision-making.
Effective project management is indispensable for orchestrating the various facets of construction seamlessly. General conditions, which include on-site supervision, safety measures, and the provision of temporary facilities, contribute to project management costs. These elements are fundamental to maintaining a well-organized, safe, and productive construction environment throughout the duration of the pre-cast warehouse project. A well-managed project ensures timely completion, adherence to quality standards, and the overall success of the construction endeavor.
Warehouse construction entails a range of costs, classified into various categories, including hard costs, soft costs, financing costs, and long-term operational costs.
Estimating soft costs proves challenging due to their indirect connection to physical construction but crucial contribution to project operations. Soft costs encompass permits, taxes, insurance, engineering and architectural design, and movable equipment. Uniqueness in each project makes soft costs difficult to predict, and if overlooked, they have the potential to disrupt project continuity.
Directly tied to physical construction, hard costs constitute predictable expenses, including labor, materials, site development, grading, and landscaping. Although seemingly foreseeable, market conditions influence these costs, introducing fluctuations. Understanding and managing hard costs are vital for accurate project budgeting.
A critical aspect of construction expenses, financing costs are essential for projects funded through loans. Clients assess anticipated costs to ensure value for money from lenders. Warehouse construction involves short-term construction loans, bridge financing to settle standing construction loans, and permanent takeout financing for long-term project funding.
Ongoing expenses such as maintenance, utility bills, and upkeep fall under long-term costs. These costs vary significantly over a project’s lifetime. Investments in upgrades, insulation, and other enhancements can lead to reduced monthly bills in the long run. Long-term expenses also encompass property management, taxes, and insurance.
Central to every warehouse, concrete foundations differ from standard slabs found in typical houses. Reinforced with rebar to withstand wind and seismic forces, these foundations play a crucial role in supporting the entire structure. Concrete slab foundation costs are estimated at around $9 per square foot. Understanding these diverse cost categories is essential for effective planning and management throughout the warehouse construction process.
Effectively managing and limiting costs in warehouse construction is crucial for a successful project. Here are key strategies to control costs throughout the construction process:
Thorough planning stands as the cornerstone of a successful warehouse construction project. Extensive investment in time and resources during the planning phase is essential to create a roadmap that anticipates challenges, mitigates risks, and streamlines the construction process. This involves a meticulous consideration of design aspects, material selection, and logistical intricacies. A well-thought-out plan not only provides clarity to all stakeholders but also minimizes the likelihood of costly changes and delays that may arise later in the construction process.
Engaging in competitive bidding is a strategic approach that empowers project owners to make well-informed decisions while managing costs effectively. By soliciting detailed bids from multiple reputable contractors, property owners gain insight into the range of pricing and services offered in the market. This transparency fosters healthy competition among contractors, potentially leading to more competitive pricing and better value for the investment. Comparative bidding establishes a foundation for transparency and collaboration throughout the construction project.
The implementation of value engineering principles is pivotal for optimizing project costs without compromising quality. This process involves a meticulous evaluation of design and construction elements to identify opportunities for cost savings while maintaining the functionality and structural integrity of the warehouse. Value engineering ensures that each component of the project contributes efficiently to the overall goals, providing a cost-effective solution without compromising on the essential aspects of the construction.
Considering energy-efficient solutions is a forward-thinking strategy that extends beyond immediate costs to focus on long-term operational savings. This involves exploring options for roofing, insulation, and other building components that prioritize energy efficiency. While the upfront costs for energy-efficient alternatives might be slightly higher, the potential for reduced operational expenses over time makes them a prudent investment. These solutions not only contribute to cost management but also align with sustainability goals, positioning the warehouse as an environmentally responsible facility.
Seeking professional consultation from experienced architects, engineers, and project managers is an indispensable step in effective cost management. The expertise of these professionals guides project owners in making informed decisions, avoiding costly mistakes, and optimizing the overall construction process. Professional consultation ensures accurate cost estimation, effective project planning, and optimal decision-making tailored to the specific needs and goals of the warehouse construction project.
Implementing regular maintenance plans during and after construction is a proactive strategy that pays dividends in long-term cost savings. A well-maintained facility not only extends its lifespan but also helps identify and address potential issues early on, preventing costly repairs or replacements in the future. Routine inspections, timely repairs, and proactive maintenance contribute to the overall health of the warehouse, reducing the likelihood of major issues that could escalate costs over time.
Strategic timing of the construction schedule is a cost management strategy that takes into account seasonal variations and weather conditions. Performing construction activities during favorable weather conditions can streamline the process, reduce potential delays, and minimize associated costs. Additionally, scheduling the project during periods of lower demand for construction services may provide an opportunity to negotiate better pricing with contractors, optimizing overall project costs.
Carefully choosing construction materials based on durability, cost-effectiveness, and suitability for the project is a crucial consideration for effective cost management. Balancing quality with cost considerations ensures that the selected materials meet the necessary standards without exceeding budget constraints. Avoiding over-specification of materials prevents unnecessary expenses and contributes to a cost-effective yet resilient warehouse construction solution.
Incorporating a contingency budget into the overall project plan is a prudent measure to account for unforeseen challenges or additional requirements. Unanticipated issues may arise during the construction process, and having a contingency budget provides the flexibility to address these challenges without compromising the overall project quality or timeline. This strategy adds a layer of financial preparedness, enhancing the project’s resilience to unexpected circumstances.
Make Informed Design Decisions Showcase Your Design Ideas
Get RenderingExploring and leveraging technological innovations in construction is essential for enhancing efficiency, reducing errors, and contributing to cost savings. Automation, advanced project management tools, and building information modeling (BIM) are among the technological advancements that can streamline construction processes. Embracing these innovations ensures that the warehouse construction project benefits from the latest tools and methodologies, optimizing efficiency and contributing to overall cost-effectiveness.
Estimating and managing costs in pre-cast warehouse construction involve a comprehensive analysis of various factors, from foundation and pre-cast components to labor, site preparation, and regulatory compliance. The diverse cost categories, including soft costs, hard costs, financing costs, and long-term operational costs, highlight the multifaceted nature of warehouse construction expenses. Limiting costs requires strategic planning, competitive bidding, value engineering, consideration of energy-efficient solutions, professional consultation, regular maintenance plans, strategic timing, careful material selection, a contingency budget, and the integration of technological innovations. Successfully navigating these considerations ensures not only cost-effectiveness but also the overall success and longevity of the pre-cast warehouse construction project.
Pre-cast warehouse construction involves the use of pre-manufactured concrete components, offering advantages such as speed of construction, durability, and design flexibility. The popularity stems from its efficiency and precision in utilizing customized, factory-made elements.
The choice between a simple slab-on-grade and a more complex foundation system significantly influences overall costs. Factors like soil conditions, adherence to local building codes, and features like drainage systems contribute to comprehensive foundation expenses.
Estimating costs for pre-cast components involves considering the quantity and specifications of elements like panels, beams, columns, and slabs. The size, finish, and detailing of each component directly impact both material and labor costs.
While pre-cast construction is known for its speed, skilled labor remains crucial for proper component installation. Labor costs vary based on project complexity, specialized skills, and local wage rates, emphasizing the importance of efficient installation for structural integrity.
Thorough site preparation, including clearing, grading, and utilities installation, is crucial. Costs depend on factors like site accessibility, soil conditions, and utility connections. Well-prepared sites streamline construction, minimize disruptions, and ensure optimal conditions for subsequent phases.
Navigating regulatory requirements, obtaining permits, and ensuring compliance with local building codes contribute to overall costs. Early engagement with regulatory authorities and budgeting for associated fees are essential to prevent delays and complications during construction.
Roofing and cladding material choices significantly impact costs and aesthetics. Factors such as insulation, weatherproofing, and design considerations play a crucial role. Balancing functionality, durability, and budget considerations is vital for an efficient and cost-effective solution.
Here I am going to share some steps to get your pre cast warehouse building cost estimate report.
You can send us your plan on info@estimatorflorida.com
Before starting your project, we send you a quote for your service. That quote will have detailed information about your project. Here you will get information about the size, difficulty, complexity and bid date when determining pricing.
Our team will takeoff and estimate your project. When we deliver you’ll receive a PDF and an Excel file of your estimate. We can also offer construction lead generation services for the jobs you’d like to pursue further.
561-530-2845
info@estimatorflorida.com
Address
5245 Wiles Rd Apt 3-102 St. Pete Beach, FL 33073 United States
561-530-2845
info@estimatorflorida.com
Address
5245 Wiles Rd Apt 3-102 St. Pete Beach, FL 33073 United States
All copyright © Reserved | Designed By V Marketing Media | Disclaimer