Modular Construction Cost Estimator
Modular construction has gained popularity as an efficient, cost-effective, and sustainable building method. By constructing sections of a building in a controlled factory environment, modular construction reduces on-site labor, minimizes waste, and accelerates the construction timeline. Understanding the costs associated with modular construction is crucial for budgeting and planning. This guide provides a comprehensive overview of the factors influencing modular construction costs and a detailed cost estimator to help you plan your modular construction project. Knowing these costs upfront allows for better financial planning and helps ensure that your project stays on track and within budget.

Factors Influencing Modular Construction Costs
Several factors influence the overall cost of modular construction. These include the size and complexity of the design, the location, the quality of materials, and any additional features or customization. Each factor plays a crucial role in determining the final price, and careful consideration of these aspects can help you plan your budget more effectively. Understanding these factors can also help you prioritize your needs and make choices that balance cost, efficiency, and aesthetics. By analyzing these elements in detail, you can develop a realistic budget and timeline for your project.
Size of the Building
The size of the building is a significant factor in determining the cost of modular construction. Larger buildings require more materials and labor, which increases the overall cost. The size of the modules and the number of modules required can also affect transportation and installation costs. Additionally, larger buildings often involve more complex systems, such as HVAC and electrical, which can add to the overall expenses.
Small Buildings (1,000 - 2,000 sq ft): $140,000 - $280,000
- Small modular buildings, such as single-family homes or small offices, typically cost less due to their smaller footprint and simpler design. These projects can be completed more quickly, reducing labor and on-site costs. Smaller buildings often involve less complex systems, making them easier and faster to construct.
- Example: A small single-family home or a compact office space. These types of buildings are ideal for individuals or small businesses looking for an efficient and affordable construction option.
Medium Buildings (2,000 - 4,000 sq ft): $280,000 - $560,000
- Medium-sized modular buildings, such as larger homes or small commercial buildings, require more materials and labor. These projects may also involve more complex designs and additional features, increasing the overall cost. Medium-sized buildings often include multiple rooms, larger common areas, and enhanced amenities.
- Example: A mid-sized home with multiple bedrooms and bathrooms or a small commercial building. These buildings provide ample space for families or businesses while maintaining cost efficiency.
Large Buildings (4,000+ sq ft): $560,000 - $1,400,000+
- Large modular buildings, such as multi-family homes, schools, or large commercial spaces, take the longest and cost the most due to their extensive size and complexity. These projects often involve multiple modules and advanced customization. Large buildings typically include advanced systems and amenities, such as elevators, large HVAC systems, and extensive electrical networks.
- Example: A multi-family apartment building or a large office complex. These buildings are suitable for large families, organizations, or institutions that require significant space and advanced features.
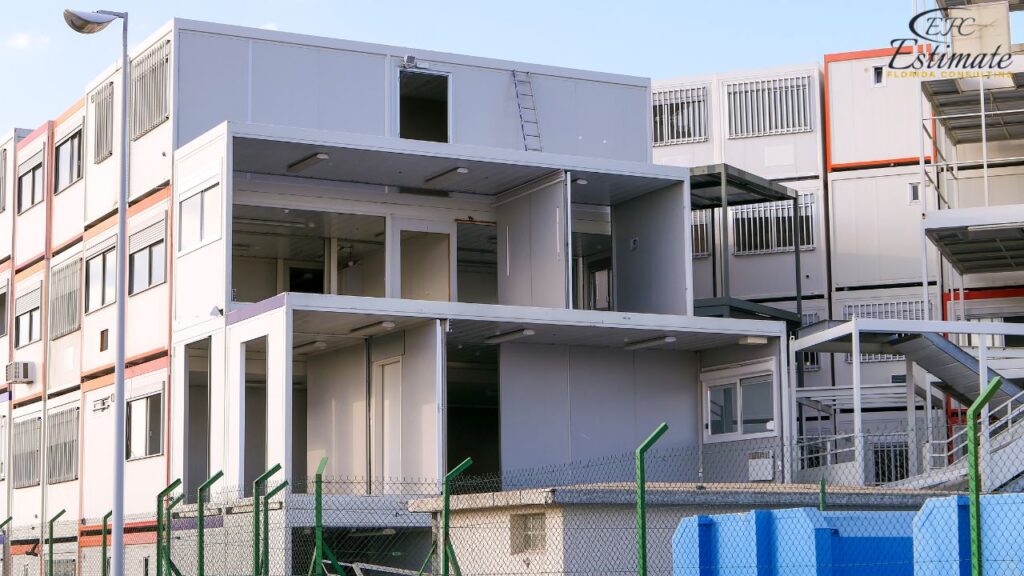
Complexity of the Design
The complexity of the design also impacts the cost. Modular buildings with intricate architectural features, unique layouts, or high-end finishes will be more expensive to construct than simpler designs. Complex designs may require more detailed planning, specialized labor, and custom materials, adding to the overall cost. The complexity of the design can also influence the construction timeline, as more intricate projects typically take longer to complete.
Simple Designs: $140 - $210 per sq ft
- Simple modular designs with standard features and minimal customization typically cost less. These projects involve fewer custom elements and are easier to plan and execute. Simple designs often prioritize functionality and efficiency, making them a cost-effective choice for many projects.
- Example: A basic single-story home with standard finishes. These homes are ideal for those looking for a straightforward, functional living space without the need for extensive customization.
Moderate Complexity: $210 - $350 per sq ft
- Modular buildings with moderate complexity may include additional features such as multiple stories, custom finishes, or unique architectural elements. These projects require more detailed planning and coordination. Moderately complex designs strike a balance between aesthetics and functionality, offering more personalized features while remaining cost-effective.
- Example: A two-story home with custom cabinetry and upgraded flooring. These homes provide a blend of luxury and practicality, catering to homeowners who desire a more refined living space.
High Complexity: $350 - $560+ per sq ft
- Highly complex modular buildings with elaborate designs, high-end finishes, and unique features will take the longest to complete and be the most expensive. These projects often require specialized labor and materials, adding to the timeline and cost. High-complexity designs typically incorporate luxury features and advanced technology, resulting in a premium living or working environment.
- Example: A luxury home with intricate architectural details, high-end appliances, and custom-built features. These homes are perfect for those who seek a unique and luxurious living experience.
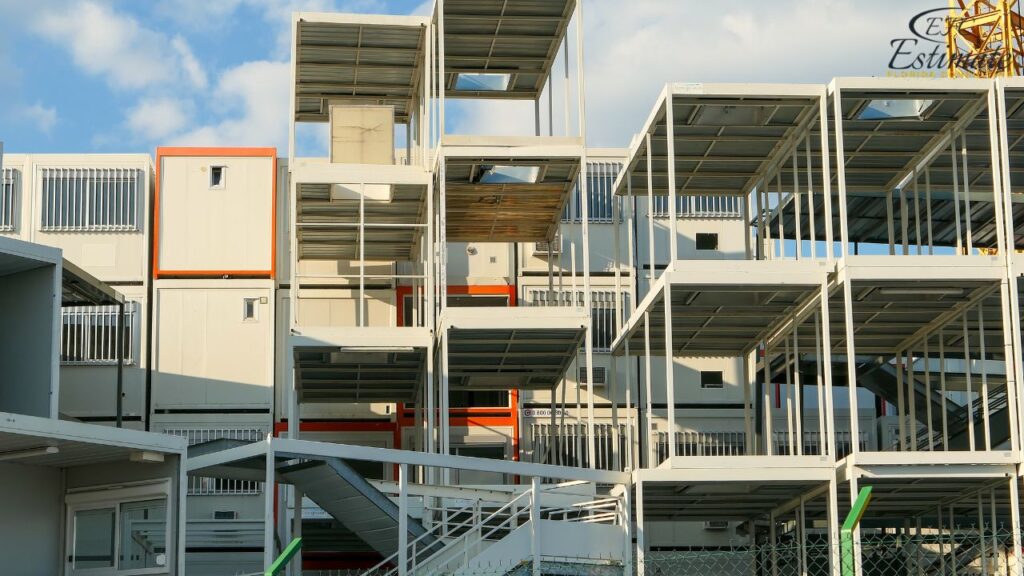
Location and Site Preparation
The location of the build site and the amount of preparation required can significantly impact the cost. Factors such as the condition of the land, access to utilities, and local permitting processes can all affect how long it takes to start and complete construction. Additionally, transportation costs for delivering the modules to the site can vary based on the distance and accessibility of the location. Proper site preparation is crucial for ensuring the stability and longevity of the building.
Urban Areas: $140,000 - $420,000
- Building in urban areas may involve quicker access to utilities and materials, but it can also mean navigating stricter zoning laws and permitting processes. These factors can both expedite and delay the construction timeline. Urban construction often requires careful planning to comply with local regulations and minimize disruption to surrounding areas.
- Example: A city lot with existing utility connections. Urban projects benefit from the proximity to suppliers and labor, potentially reducing transportation costs.
Suburban Areas: $210,000 - $490,000
- Suburban areas often provide a balance between accessibility and regulatory processes. However, depending on the location, there may still be specific requirements that affect the timeline and cost. Suburban projects often involve moderate site preparation and easier access to utilities compared to rural areas.
- Example: A suburban neighborhood with established infrastructure. Suburban construction typically offers a good balance of cost and convenience, making it a popular choice for residential and commercial projects.
Rural Areas: $280,000 - $700,000+
- Building in rural areas can involve more extensive site preparation, such as clearing land and installing utilities. These projects may also face delays due to weather conditions and access to materials and labor. Rural construction often requires additional planning for transportation and logistics to ensure that materials and modules arrive on site as scheduled.
- Example: A rural property requiring significant land clearing and utility installation. Rural projects may offer more space and flexibility but can come with higher costs and longer timelines due to the additional preparation required.
Quality of Materials
The quality of materials used in modular construction can significantly impact the overall cost. Higher-quality materials often come with a higher price tag but can result in a more durable and aesthetically pleasing final product. Choosing the right materials for your project involves balancing cost, durability, and aesthetic appeal. High-quality materials can also improve the energy efficiency and environmental impact of the building, providing long-term benefits.
Standard Materials: $140 - $280 per sq ft
- Using standard materials can help keep costs down while still providing a durable and functional building. Standard materials are typically more readily available and easier to work with, reducing both material and labor costs. These materials provide a good balance of cost and performance for most projects.
- Example: Basic wood framing, standard insulation, and conventional roofing materials. These materials are suitable for a wide range of applications, offering reliability and affordability.
Download Template For Modular Construction Project Breakdown
- Materials list updated to the zip code
- Fast delivery
- Data base of general contractors and sub-contractors
- Local estimators
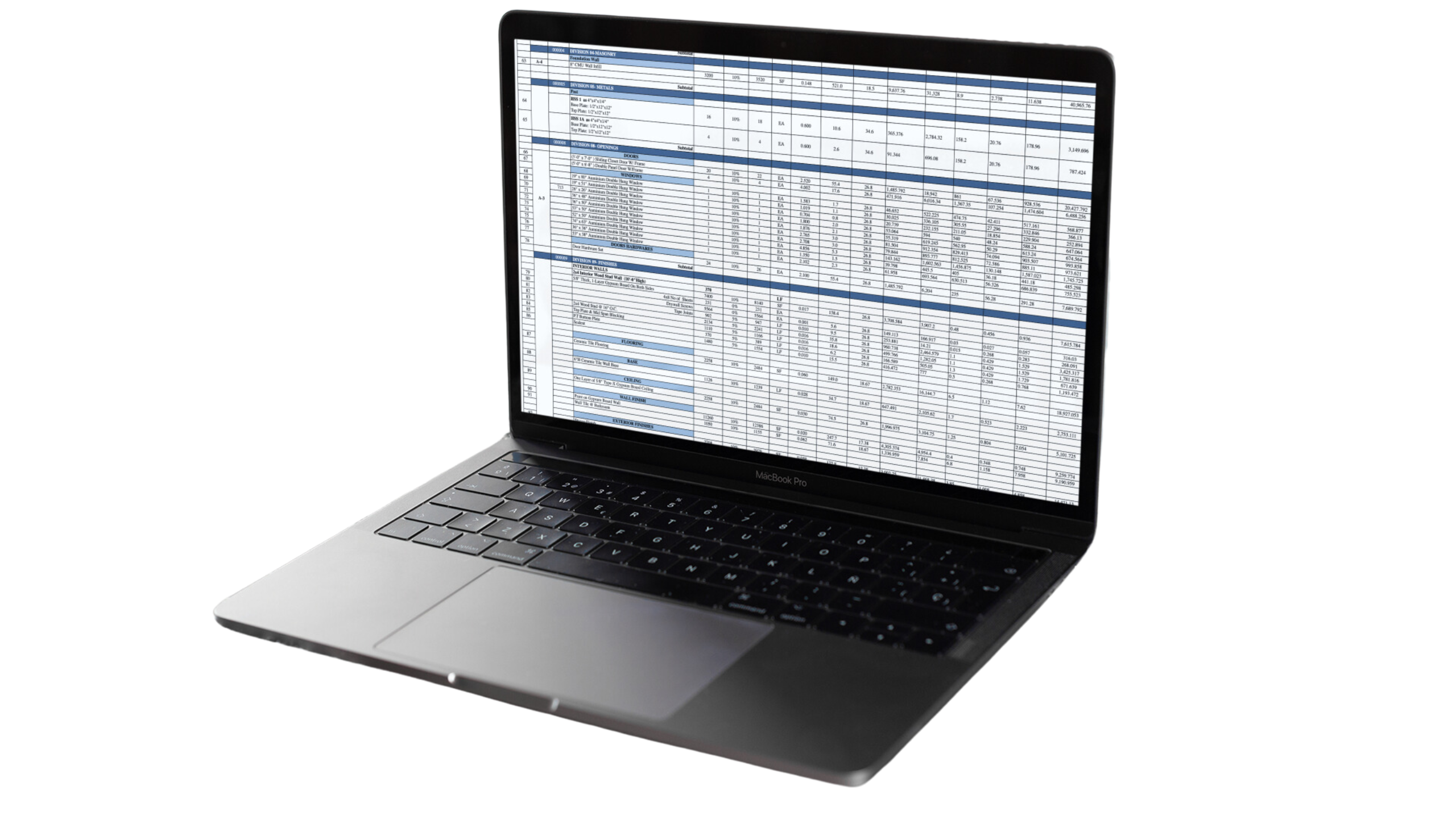
Mid-Range Materials: $280 - $420 per sq ft
- Mid-range materials offer a balance between cost and quality. These materials provide better durability and aesthetics without significantly increasing the overall cost. Mid-range materials often include upgraded finishes and improved performance characteristics.
- Example: Upgraded wood or steel framing, improved insulation, and higher-quality roofing materials. These materials enhance the appearance and functionality of the building while remaining cost-effective.
High-End Materials: $420 - $700+ per sq ft
- High-end materials can significantly increase the cost but offer superior durability, energy efficiency, and aesthetic appeal. These materials are often custom-ordered and may require specialized installation techniques. High-end materials can also add value to the property and improve its marketability.
- Example: Premium hardwood flooring, high-efficiency windows, and custom cabinetry. These materials provide a luxurious finish and exceptional performance, making them ideal for high-end residential and commercial projects.
Additional Features and Customization
Additional features and customization can also impact the cost of modular construction. These can include upgraded appliances, advanced HVAC systems, smart home technology, and custom finishes. The more features and customization you choose, the higher the overall cost will be. Customization allows for greater personalization and functionality, but it requires careful planning and coordination to ensure that all elements are seamlessly integrated.
Basic Features: $140 - $280 per sq ft
- Basic modular buildings with standard features and minimal customization typically cost less. These projects involve fewer custom elements and are easier to plan and execute. Basic features provide essential functionality and comfort without adding significant costs.
- Example: Standard kitchen and bathroom fixtures, basic lighting, and conventional HVAC systems. These features are sufficient for most residential and commercial applications, offering practicality and reliability.
Moderate Customization: $280 - $420 per sq ft
- Modular buildings with moderate customization may include upgraded appliances, advanced HVAC systems, or smart home technology. These projects require more detailed planning and coordination. Moderately customized features enhance the building’s functionality and aesthetics without overwhelming the budget.
- Example: Energy-efficient appliances, enhanced lighting systems, and integrated smart home technology. These features improve the building’s efficiency and convenience, making it more attractive to potential buyers or tenants.
High Customization: $420 - $700+ per sq ft
- Highly customized modular buildings with elaborate designs, high-end finishes, and unique features will be the most expensive. These projects often require specialized labor and materials, adding to the timeline and cost. High customization allows for the creation of unique and highly personalized spaces that meet specific needs and preferences.
- Example: Custom kitchen cabinetry, luxury bathroom fixtures, and advanced home automation systems. These features provide a high level of comfort and luxury, making the building stand out in the market.
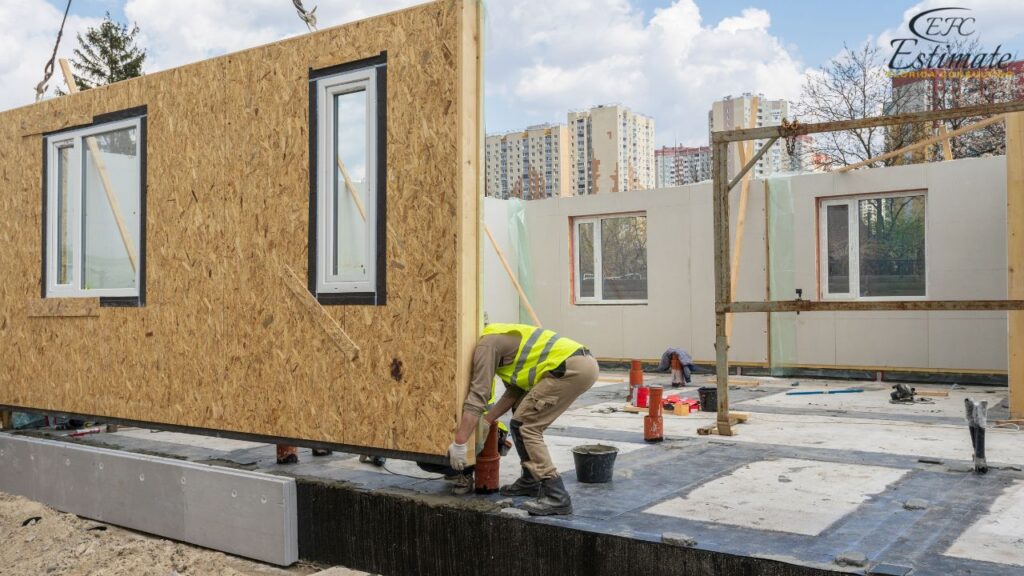
Detailed Cost Breakdown
Here’s a detailed cost breakdown for modular construction, including materials, labor, and additional costs.
Small Buildings (1,000 - 2,000 sq ft)
Small buildings are ideal for individuals or small families looking for affordable and efficient living spaces. They typically require less time to construct and can be built with standard materials and features, keeping costs relatively low.
Item | Cost per Unit | Total Cost (1,500 sq ft) |
Standard Materials | $140 – $280 per sq ft | $210,000 – $420,000 |
Labor | $70 – $140 per sq ft | $105,000 – $210,000 |
Site Preparation | $28,000 – $70,000 | $28,000 – $70,000 |
Additional Features | $28,000 – $56,000 | $28,000 – $56,000 |
Total Cost | $371,000 – $756,000 |
Medium Buildings (2,000 - 4,000 sq ft)
Medium-sized buildings offer a balance of space and cost, making them suitable for larger families or small businesses. These projects often include additional features and customization, enhancing both functionality and aesthetics.
Item | Cost per Unit | Total Cost (3,000 sq ft) |
Mid-Range Materials | $280 – $420 per sq ft | $840,000 – $1,260,000 |
Labor | $105 – $210 per sq ft | $315,000 – $630,000 |
Site Preparation | $42,000 – $98,000 | $42,000 – $98,000 |
Additional Features | $56,000 – $112,000 | $56,000 – $112,000 |
Total Cost | $1,253,000 – $2,100,000 |
Large Buildings (4,000+ sq ft)
Large buildings are suitable for multi-family residences, commercial spaces, or institutional buildings. These projects involve extensive planning, advanced systems, and high-end materials, resulting in higher costs and longer construction timelines.
Item | Cost per Unit | Total Cost (5,000 sq ft) |
High-End Materials | $420 – $700 per sq ft | $2,100,000 – $3,500,000 |
Labor | $140 – $280 per sq ft | $700,000 – $1,400,000 |
Site Preparation | $70,000 – $140,000 | $70,000 – $140,000 |
Additional Features | $140,000 – $280,000 | $140,000 – $280,000 |
Total Cost | $3,010,000 – $5,320,000 |
Additional Considerations
When planning a modular construction project, several additional considerations can impact the overall cost and timeline. Understanding these factors can help you better prepare and manage your project effectively.
Permits and Approvals
Obtaining the necessary permits and approvals is a crucial step in the modular construction process. These requirements vary by location and can add to the overall cost of the project. Permits ensure that the work complies with local building codes and safety standards, while inspections verify that the work is completed correctly.
Permit Costs: $1,400 - $14,000
- Depending on the complexity and location of the project, permit costs can vary. Ensuring all necessary permits are obtained can prevent delays and additional costs later in the project.
- Example: Building permits, zoning approvals, and environmental assessments.
Inspection Fees: $700 - $7,000
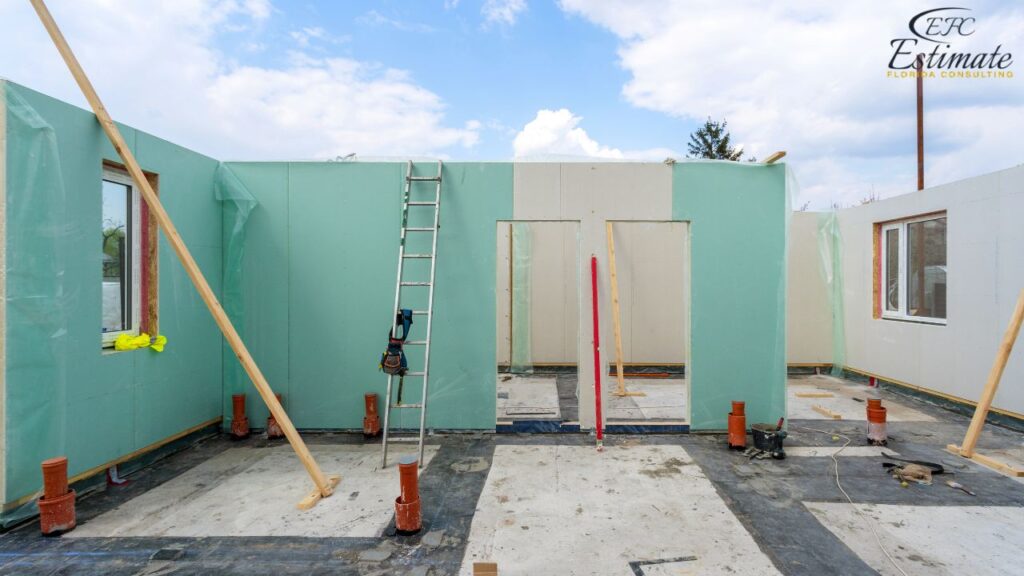
- Inspections are required at various stages of construction to ensure compliance with local building codes and safety standards. These fees should be included in the overall budget.
- Example: Electrical, plumbing, and structural inspections.
Transportation and Logistics
Transporting modular units from the factory to the build site is another critical consideration. The cost of transportation can vary based on the distance and complexity of the delivery route. Proper planning and coordination are essential to ensure timely delivery and minimize delays.
Local Transportation: $7,000 - $21,000
- Transporting modules within a local area is generally less expensive and involves fewer logistical challenges.
- Example: Delivery of modular units within a 50-mile radius of the factory.
Long-Distance Transportation: $21,000 - $70,000+
- Long-distance transportation involves higher costs due to the distance and potential obstacles along the route. Planning for secure and efficient delivery is crucial to avoid damage and delays.
- Example: Delivery of modular units across state lines or to remote locations.
Get 5 New Leads Next 7Days With Our System
- Multi-Family Building
- Hotel Building
- Hospital Building
- Warehouse Building
- High-Rise Building
- Shopping Complex
Site Preparation and Utility Installation
Proper site preparation and utility installation are essential for the successful completion of a modular construction project. These tasks ensure that the build site is ready to receive the modular units and that all necessary infrastructure is in place.
Site Clearing and Grading: $14,000 - $70,000
- Preparing the site involves clearing vegetation, leveling the ground, and ensuring a stable foundation for the modular units. Proper site preparation is crucial for the stability and longevity of the building.
- Example: Removing trees, grading the land, and setting up temporary facilities.
Utility Installation: $28,000 - $84,000
- Installing utilities such as water, electricity, and sewage systems is a vital part of site preparation. Ensuring these systems are in place before the modules arrive can prevent delays and additional costs.
- Example: Connecting the building to municipal water and sewage systems, installing electrical and gas lines.
Conclusion
The cost of modular construction varies significantly based on several factors, including the size of the building, the complexity of the design, the location, the quality of materials, and any additional features or customization. By understanding these factors and using the detailed cost breakdowns provided, you can plan your budget effectively and ensure your project stays within budget. Whether you’re building a small home, a mid-sized commercial space, or a large luxury residence, careful planning and coordination are essential to ensure a smooth and successful construction process.
Investing time in the pre-construction phase, working with experienced professionals, and planning for potential delays can help you achieve your modular construction project within your desired timeframe and budget. Properly managing each stage of the construction process will ensure that your modular building is constructed to the highest standards and meets all your expectations. Ensuring that all elements are well-coordinated and integrated will result in a functional and aesthetically pleasing final product.
FAQs
Several factors influence the cost, including the size and complexity of the design, the location, the quality of materials, and any additional features or customization. Each factor plays a crucial role in determining the final price.
The size of the building significantly impacts the cost. Larger buildings require more materials and labor, increasing the overall cost. The size also affects transportation and installation costs.
- Small Buildings (1,000 – 2,000 sq ft): $140,000 – $280,000
- Medium Buildings (2,000 – 4,000 sq ft): $280,000 – $560,000
- Large Buildings (4,000+ sq ft): $560,000 – $1,400,000+
More complex designs with intricate architectural features, unique layouts, or high-end finishes increase costs due to the need for detailed planning, specialized labor, and custom materials.
- Simple Designs: $140 – $210 per sq ft
- Moderate Complexity: $210 – $350 per sq ft
- High Complexity: $350 – $560+ per sq ft
- Urban Areas: $140,000 – $420,000
- Suburban Areas: $210,000 – $490,000
- Rural Areas: $280,000 – $700,000+
Higher-quality materials are more expensive but offer better durability and aesthetic appeal. The choice of materials affects both the initial cost and the long-term value of the building.
- Standard Materials: $140 – $280 per sq ft
- Mid-Range Materials: $280 – $420 per sq ft
- High-End Materials: $420 – $700+ per sq ft
Additional features and customization, such as upgraded appliances, advanced HVAC systems, and custom finishes, increase the overall cost. The more features and customization, the higher the cost.
- Basic Features: $140 – $280 per sq ft
- Moderate Customization: $280 – $420 per sq ft
- High Customization: $420 – $700+ per sq ft
Additional considerations include permits and approvals, transportation and logistics, and site preparation and utility installation.
- Permit Costs: $1,400 – $14,000
- Inspection Fees: $700 – $7,000
- Local Transportation: $7,000 – $21,000
- Long-Distance Transportation: $21,000 – $70,000+
Google Reviews
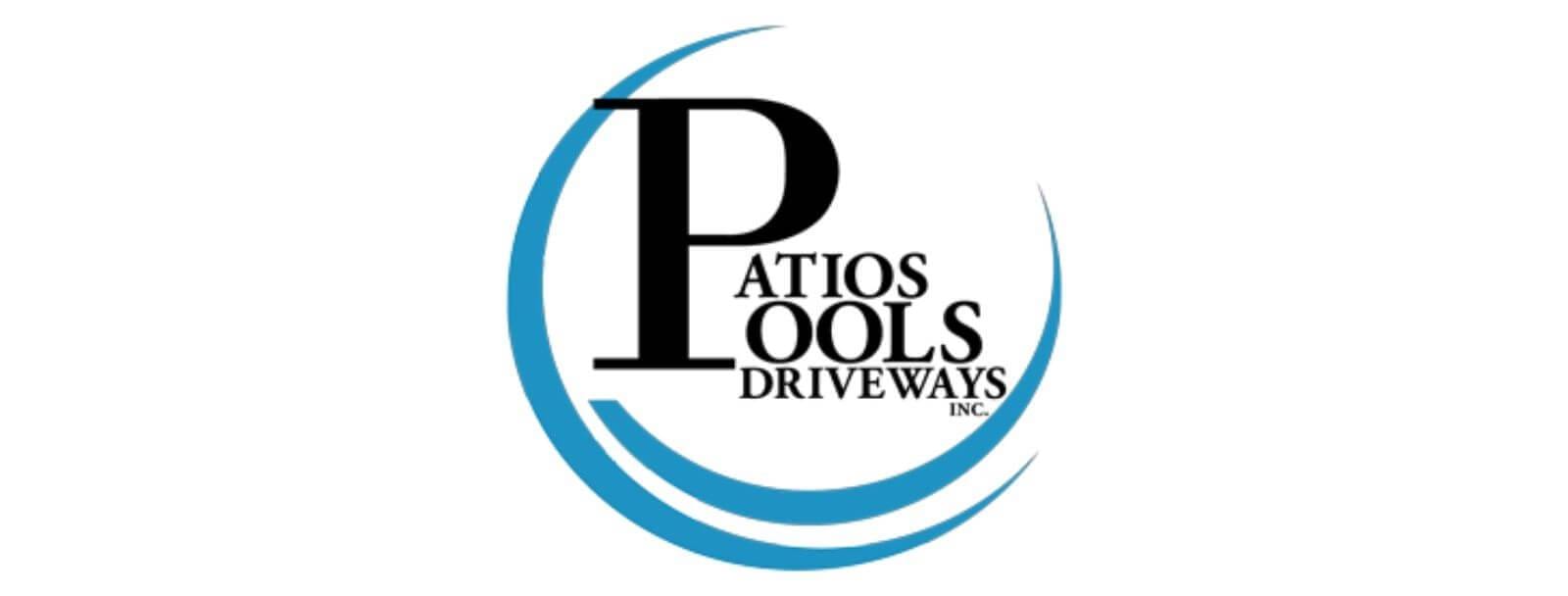
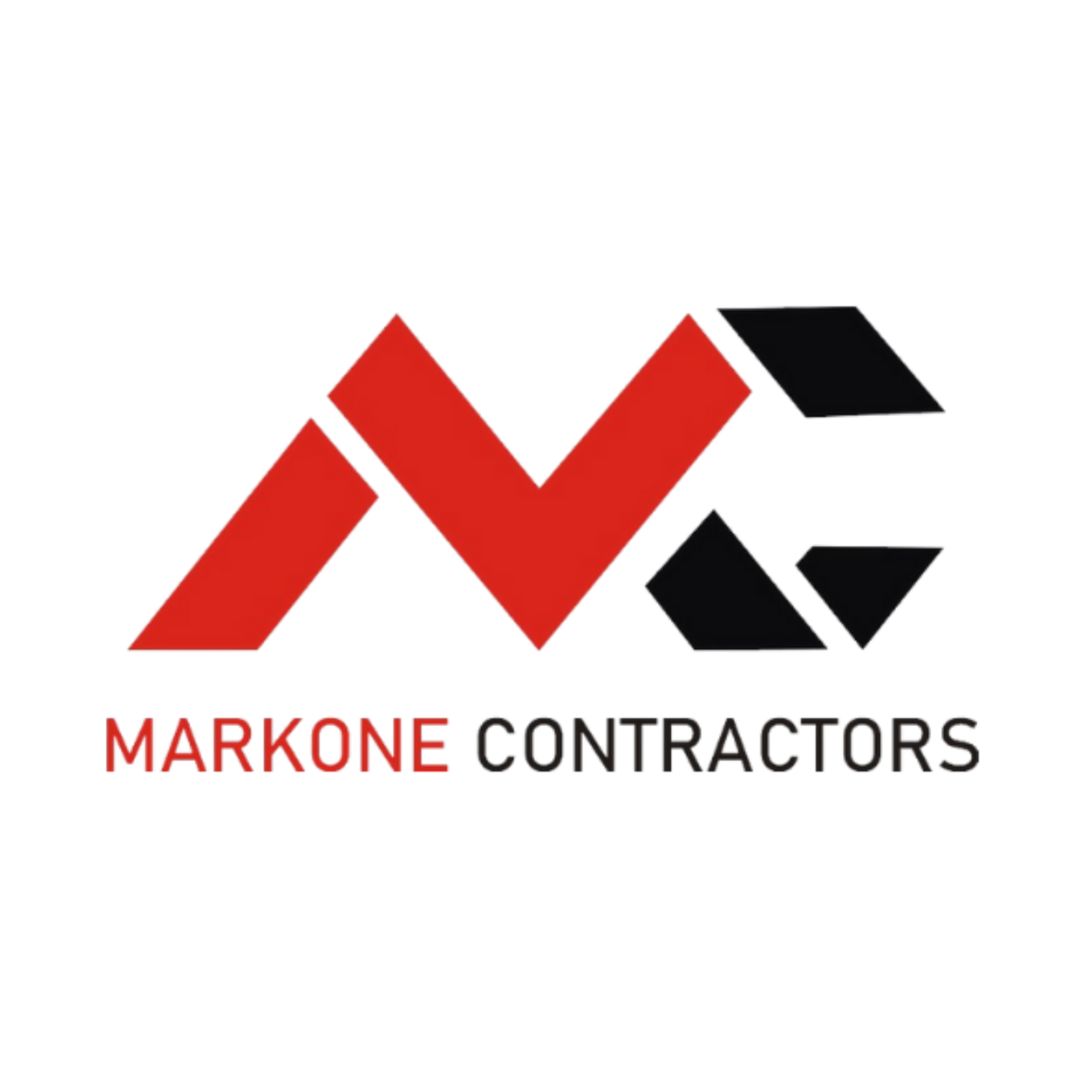

Process To Get Modular Construction Estimate Report
Here I am going to share some steps to get modular construction estimate report.
-
You need to send your plan to us.
You can send us your plan on info@estimatorflorida.com
-
You receive a quote for your project.
Before starting your project, we send you a quote for your service. That quote will have detailed information about your project. Here you will get information about the size, difficulty, complexity and bid date when determining pricing.
-
Get Estimate Report
Our team will takeoff and estimate your project. When we deliver you’ll receive a PDF and an Excel file of your estimate. We can also offer construction lead generation services for the jobs you’d like to pursue further.