Boost Your Warehouse Construction Bids – Request a Precision Estimate!
- Accurancy
- Efficiency
- Transparency
- Customization
- Time Saving
- Professionalism
- Cost Control
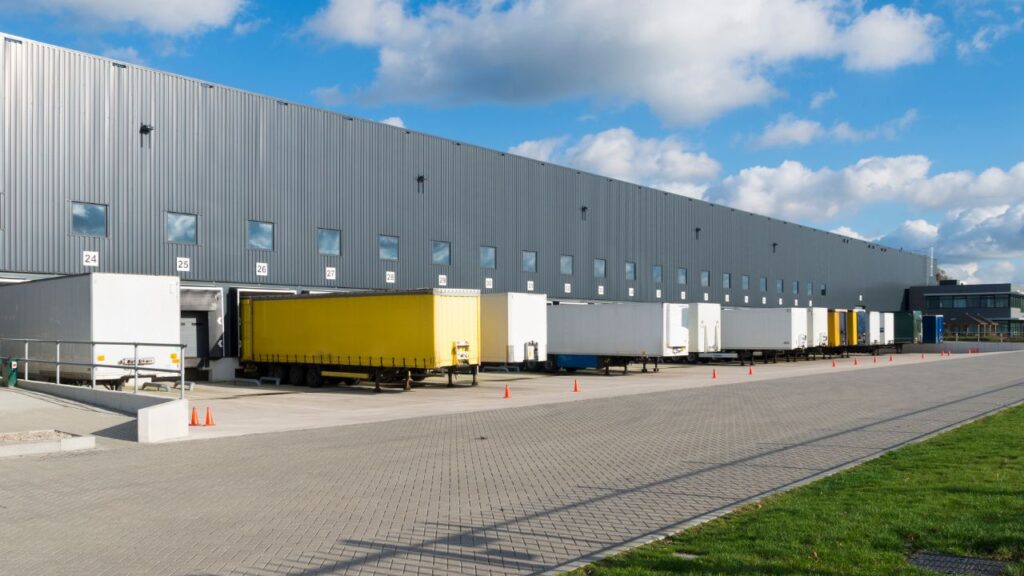
The overall gross cost for metal warehouse siding, taking into account materials, labor, and potential additional features, typically ranges from $50,000 to $200,000 or more for a standard-sized warehouse. This wide range reflects the various factors influencing costs, including the type of metal siding selected, its quality, the complexity of the installation, and any customization or architectural elements incorporated into the design. Basic metal siding options may result in lower overall costs, while premium materials with advanced features or finishes can contribute to higher expenses.
As costs can vary significantly depending on regional labor rates, market conditions, and project intricacies.
This comprehensive guide aims to unravel the intricacies of metal warehouse siding costs, examining various types, materials, and the multitude of factors influencing overall expenses.
Fully Insured Licensed
Hire Contractor For Warehouse Construction
Make Informed Design Decisions Showcase Your Design Ideas
Get RenderingMetal siding has gained widespread popularity in both residential and commercial construction, with steel and aluminum emerging as the top choices for their durability and versatility. Notably, galvanized steel siding, while pricier, boasts enhanced longevity compared to aluminum.
When delving into the realm of metal siding prices, it’s essential to understand the varying costs associated with different types of metals and styles. Here’s a detailed breakdown of metal siding prices per square foot, shedding light on the diverse options available in the market:
Copper siding, known for its premium aesthetic and exceptional durability, is priced in the higher bracket, ranging from $30 to $45 or more per square foot when installed.
A classic and budget-friendly option, tin siding is available at an affordable range of $2 to $5 or more per square foot when installed.
Understanding the factors influencing metal siding costs is crucial for making informed decisions in construction projects. Material preferences, installation intricacies, and regional pricing variations can all contribute to the overall budget. Additionally, the choice between steel and aluminum, the two most popular options, often hinges on the balance between initial costs and long-term durability.
Metal warehouse siding cost is influenced by various factors that play a crucial role in determining the overall expenses associated with the selection, installation, and maintenance of the siding. Understanding these factors is essential for effective budget planning and decision-making in construction projects. Here are key elements that influence the cost of metal warehouse siding:
The selection of the metal material for warehouse siding is a critical decision with far-reaching implications for both the aesthetic appeal and financial aspects of the project. Among the commonly used materials are steel, aluminum, copper, tin, and zinc, each bringing its distinct characteristics and price considerations. Steel, known for its durability and affordability, often undergoes protective coatings like aluminum or zinc to enhance resistance against corrosion. Aluminum, although more expensive, offers a lightweight and corrosion-resistant alternative, ideal for regions with extreme weather conditions. Copper, tin, and zinc provide unique properties such as corrosion resistance and historical reliability, but they come with a higher price tag. Thus, the careful consideration of material type is paramount in achieving a balance between functionality and cost-effectiveness.
The choice of siding style and profile introduces an element of design versatility but also contributes to project costs. Corrugated panels, smooth boards, and specialized profiles like exposed or concealed fastener panels offer different aesthetics and functional characteristics. The selection of a specific style can impact costs due to variations in manufacturing and installation requirements. More intricate profiles may necessitate custom fabrication, leading to higher expenses. The decision-making process should involve weighing the desired visual appeal against the potential additional costs associated with the chosen siding style. Striking the right balance is crucial for achieving both the intended design vision and budgetary considerations.
The thickness of the metal panels used for siding is a fundamental factor influencing both the durability and the overall cost of the project. Thicker panels typically come at a higher price but offer advantages in terms of increased resilience against environmental factors. The choice of thickness should align with the specific needs of the warehouse, considering factors such as weather conditions, potential impact, and the desired lifespan of the siding. A careful assessment of the trade-offs between upfront costs and long-term durability is essential in determining the optimal metal thickness for the project.
The finish and coating applied to the metal panels play a dual role in influencing the aesthetic appeal and protective qualities of the siding. Options such as galvanized coatings, painted finishes, or specialized coatings for enhanced weather resistance introduce variability in costs. Galvanized coatings provide corrosion resistance, while painted finishes contribute to the visual appeal of the siding. The choice of coating should align with the specific environmental conditions of the warehouse location, and the budget should account for the additional costs associated with premium finishes that offer both protection and aesthetic enhancement.
The size of the warehouse and the total coverage area requiring siding directly impact material quantities and, consequently, project costs. Larger warehouses necessitate more material, contributing to higher expenses. Accurate measurements and calculations are crucial to determining the exact amount of siding required, and this information becomes a key input in the budgeting process. Balancing the desired coverage with budget constraints is essential to avoid unnecessary material waste and associated costs.
The complexity of the installation process is a critical factor influencing labor costs in metal warehouse siding projects. Factors such as the need for custom cuts, intricate designs, or challenging access can contribute to higher installation expenses. Custom fabrication requirements, especially for unique architectural features, may demand specialized skills and additional labor hours. Project planners should carefully assess the installation complexity to ensure that the budget adequately accounts for the expertise and time required to execute the project successfully.
Regional variations in material costs, labor rates, and building regulations introduce a layer of complexity to budget planning for metal warehouse siding. Different locations may have distinct pricing structures, and adherence to local building codes can influence costs. Considering these regional factors is essential for accurate budget estimates. Collaboration with local suppliers and contractors familiar with regional nuances becomes crucial to navigating these variations and optimizing costs effectively.
While upfront costs are a significant consideration, the long-term maintenance requirements of the chosen metal siding material should not be overlooked. Some materials may demand more frequent maintenance activities, impacting overall costs over time. Evaluating the anticipated maintenance needs and associated costs is essential for a comprehensive understanding of the project’s lifecycle expenses. Investing in materials with lower long-term maintenance requirements may result in significant cost savings over the operational life of the warehouse.
The inclusion of insulation materials or energy-efficient features in the siding introduces an upfront cost consideration that aligns with long-term operational savings. While these investments may contribute to increased initial expenses, they can lead to energy savings and reduced operational costs in the long run. Insulated metal panels, for example, offer enhanced energy efficiency and climate control, contributing to potential cost savings through reduced heating and cooling expenses. Balancing the upfront costs with the expected long-term energy savings is essential for making informed decisions regarding insulation and energy efficiency features.
Customization options, such as unique color choices, architectural detailing, or specific design requirements, can add a layer of uniqueness to metal warehouse siding. However, customization often comes with additional costs, especially when it involves custom fabrication to meet specific aesthetic or structural needs. Balancing the desire for architectural distinctiveness with budget constraints is crucial. Project planners should carefully evaluate the cost implications of customization, ensuring that the chosen features align with the overall project vision while maintaining financial feasibility.
Optimizing costs in metal warehouse siding projects requires a strategic approach that balances functionality, aesthetics, and financial considerations. Implementing the following cost optimization strategies can contribute to a successful siding project that meets budgetary constraints without compromising on quality.
Fully Insured Licensed
Hire Contractor For Warehouse Construction
Make Informed Design Decisions Showcase Your Design Ideas
Get RenderingIn the dynamic landscape of metal warehouse siding costs, thorough consideration of material nuances, installation intricacies, and long-term implications is paramount. The explored factors, from material types to customization and location-specific considerations, provide a holistic view for decision-makers.
Embracing strategic approaches like local sourcing, bulk purchasing, and investing in energy-efficient systems positions projects for success. Proactive maintenance, technological integration, and collaborative partnerships with experienced contractors emerge as key pillars in optimizing costs and ensuring the longevity of metal warehouse siding systems.
As industries strive for a balance between functionality and aesthetics, these insights serve as a roadmap, guiding businesses toward cost-effective and sustainable solutions. Through meticulous planning and a keen eye on emerging technologies, businesses can embark on metal siding projects that stand the test of time while remaining economically prudent.
The cost of metal warehouse siding is influenced by various factors, including the type of metal chosen, the siding style and profile, metal thickness, finish and coating options, the size and coverage area of the warehouse, installation complexity, location-specific pricing, long-term maintenance requirements, energy efficiency features, and customization needs.
Commonly used metal materials for warehouse siding include steel, aluminum, copper, tin, and zinc. Steel is known for durability and affordability, while aluminum offers corrosion resistance. Copper, tin, and zinc provide unique properties but come at a higher cost. The choice depends on factors such as budget, aesthetics, and environmental conditions.
The thickness of metal panels affects both durability and cost. Thicker panels generally come at a higher price but offer increased resilience against environmental factors. Choosing the optimal thickness involves considering factors such as weather conditions, potential impact, and the desired lifespan of the siding.
Cost optimization strategies include strategic material selection, local sourcing, bulk purchasing, investing in energy-efficient siding systems, proactive maintenance planning, technology integration, weather-adaptive design, collaboration with experienced contractors, and waste reduction and recycling. These strategies aim to balance functionality, aesthetics, and financial considerations.
Balancing customization desires with budget constraints involves careful evaluation of the cost implications of specific features. Customization, such as unique color choices or architectural detailing, often comes with additional costs, especially if it requires custom fabrication. Project planners should prioritize features that align with the overall vision while ensuring financial feasibility.
Here I am going to share some steps to get your metal warehouse siding cost estimate report.
You can send us your plan on info@estimatorflorida.com
Before starting your project, we send you a quote for your service. That quote will have detailed information about your project. Here you will get information about the size, difficulty, complexity and bid date when determining pricing.
Our team will takeoff and estimate your project. When we deliver you’ll receive a PDF and an Excel file of your estimate. We can also offer construction lead generation services for the jobs you’d like to pursue further.
561-530-2845
info@estimatorflorida.com
Address
5245 Wiles Rd Apt 3-102 St. Pete Beach, FL 33073 United States
561-530-2845
info@estimatorflorida.com
Address
5245 Wiles Rd Apt 3-102 St. Pete Beach, FL 33073 United States
All copyright © Reserved | Designed By V Marketing Media | Disclaimer