Boost Your Warehouse Construction Bids – Request a Precision Estimate!
- Accurancy
- Efficiency
- Transparency
- Customization
- Time Saving
- Professionalism
- Cost Control
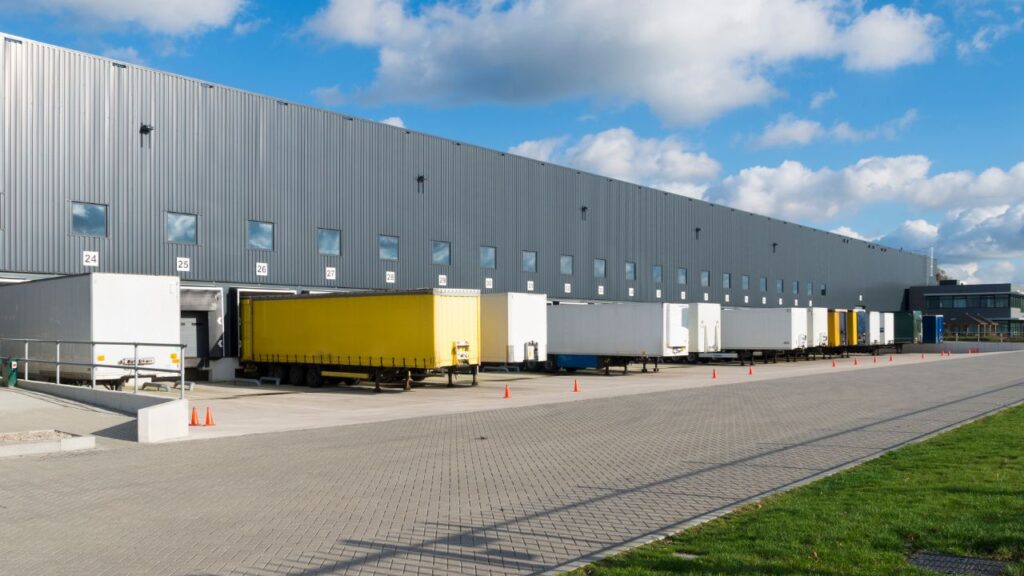
The cost of retrofitting a metal warehouse is a crucial consideration for businesses seeking to update older structures and enhance functionality. Estimate Florida Consulting, indicates that the expenses for such retrofit projects typically range from $6 to $15 per square foot. However, in the case of more intricate installations, such as those in multi-floor buildings, the costs can escalate to $5–$7 per square foot or even higher. Comparatively, the average cost to construct a new warehouse falls within the range of $20 to $60 per square foot.
It’s important to note that the total expense varies significantly, from a modest 30×40 warehouse costing $35,000 to a large 50,000-square-foot distribution center demanding an investment exceeding $1 million. As businesses weigh the pros and cons of retrofitting versus constructing anew, understanding these cost dynamics becomes paramount in making informed decisions regarding warehouse upgrades. If you’re planning such a project, Estimate Florida Consulting provides estimates tailored to your needs.
Fully Insured Licensed
Hire Contractor For Warehouse Construction
Make Informed Design Decisions Showcase Your Design Ideas
Get RenderingRetrofitting Aspect | Estimated Cost Range |
Structural Upgrades | $10,000 – $100,000 or more |
Technology Integration | $20,000 – $200,000 or more |
Energy-Efficient Solutions | $15,000 – $50,000 or more |
Environmental Compliance | $5,000 – $30,000 or more |
Safety and Security Measures | $10,000 – $50,000 or more |
Space Optimization | $20,000 – $100,000 or more |
Return on Investment (ROI) | Evaluated based on long-term benefits |
It’s important to note that these are estimated costs, and actual expenses may vary based on factors such as warehouse size, location, and specific retrofitting requirements.
Retrofitting stands as more than a mere upgrade; it’s a proactive response to the dynamic demands of the modern industry. Beyond routine maintenance, it represents a strategic initiative aimed at aligning warehouses with current technological advancements, meeting evolving business requirements, and ensuring compliance with regulatory standards. The overarching objective of retrofitting is to future-proof these structures, ensuring they remain agile and efficient in the face of continually evolving industrial needs. It’s a commitment to resilience and adaptability, acknowledging that the warehouse must evolve to stay relevant in an ever-changing landscape.
The structural integrity of a metal warehouse is paramount for its longevity and functionality. Retrofitting addresses this by focusing on structural upgrades to ensure stability and compliance with contemporary building codes. This involves a comprehensive assessment of the existing framework, reinforcing support systems, and adapting structures to accommodate modern storage and handling systems. Beyond its financial implications, structural upgrading is a commitment to the very foundation of the warehouse, ensuring it can withstand the demands of the future and support the technological advancements it will house.
It’s important to note that the total expense varies significantly, from a modest 30×40 warehouse costing $35,000 to a large 50,000-square-foot distribution center demanding an investment exceeding $1 million. As businesses weigh the pros and cons of retrofitting versus constructing anew, understanding these cost dynamics becomes paramount in making informed decisions regarding warehouse upgrades. If you’re planning such a project, Estimate Florida Consulting provides estimates tailored to your needs.
At the forefront of warehouse retrofitting is the integration of advanced technologies. This includes the implementation of automation systems, smart sensors, and data analytics to optimize various facets of warehouse operations. The objective extends beyond monetary considerations. It’s about embracing a paradigm shift in how warehouses operate. Automating inventory management, enhancing logistics through data-driven insights, and streamlining workflows are not just objectives but a commitment to operational excellence. The associated costs represent an investment in the intelligence and efficiency that will define the warehouse’s future.
Energy efficiency is a cornerstone of sustainable retrofitting. Upgrading lighting systems, HVAC (Heating, Ventilation, and Air Conditioning) systems, and insulation contributes not only to ecological responsibility but also results in long-term cost savings. Beyond the initial financial investment, this aspect of retrofitting symbolizes a commitment to balancing ecological concerns with economic considerations. It’s about creating a warehouse that not only functions efficiently but does so with a minimal environmental footprint, aligning economic progress with environmental responsibility.
The evolving landscape of environmental regulations necessitates retrofitting for compliance. This involves adopting eco-friendly materials, implementing waste reduction strategies, and ensuring adherence to environmental standards. Beyond the financial costs, retrofitting for environmental compliance represents a commitment to corporate responsibility. It positions the warehouse as an entity mindful of its ecological impact, aligning with broader sustainability goals. The associated expenses are not just financial; they are an investment in being a responsible steward of the environment.
Enhancing safety and security measures is a critical facet of warehouse retrofitting. This involves upgrading surveillance systems, installing advanced access control mechanisms, and implementing robust fire safety measures. The financial investment in safety and security retrofits goes beyond numbers; it represents a commitment to the well-being of personnel, the protection of valuable assets, and the mitigation of potential risks. It transforms the warehouse into a secure and resilient operational hub, prioritizing the safety of individuals and the preservation of assets.
Efficient space utilization is a key consideration in warehouse retrofitting. This involves reconfiguring layouts, implementing mezzanine systems, and adopting automated storage solutions. Beyond financial considerations, optimizing space represents a strategic investment in maximizing efficiency and storage capacity. It’s about creating a warehouse layout that not only accommodates current needs but anticipates future requirements. The associated costs are not just expenses; they are investments in operational excellence and the adaptability of the warehouse.
While retrofitting incurs upfront costs, assessing the long-term benefits and return on investment is paramount. Enhanced operational efficiency, reduced energy expenses, compliance with modern standards, and increased competitiveness are key factors contributing to the overall value of the warehouse. Evaluating the ROI is not just about numbers; it’s about ensuring that retrofitting projects are not only strategic but also economically viable in the evolving industrial landscape. It represents a forward-looking approach, where each investment contributes to the warehouse’s resilience and relevance in the years to come.
Warehouse retrofitting offers several advantages, providing an economical, sustainable, reliable, and future-proof solution. Some key benefits include:
Warehouse retrofitting is a strategic and forward-thinking approach, offering a balance between cost-effectiveness, sustainability, reliability, and future readiness.
Warehouse retrofitting is a multifaceted endeavor that demands careful planning, strategic decision-making, and seamless execution. Follow these seven steps to ensure a successful warehouse retrofitting project:
By following these steps, your warehouse retrofitting project is poised for success, creating a modern, efficient, and sustainable operational space that aligns with contemporary industry standards.
From small to large projects, residential to commercial, we’re here to help you win. Fast results guaranteed.
In the face of evolving industrial demands, metal warehouses are undergoing a transformative journey through strategic retrofitting. This guide has intricately explored the facets of this process, shedding light on key considerations and estimated costs associated with structural upgrades, technology integration, energy efficiency, environmental compliance, safety measures, and space optimization. Recognizing these estimates as variable, contingent on factors like size and location, is crucial. Beyond a mere upgrade, retrofitting signifies a proactive response to modern industry dynamics, a commitment to longevity through resilience and adaptability. The advantages are manifold, offering an economical, sustainable, and reliable solution. As businesses contemplate these investments, the guide concludes with a practical roadmap for success, emphasizing comprehensive assessment, detailed planning, and ongoing monitoring. Ultimately, metal warehouse retrofitting emerges as a strategic and forward-thinking approach, revitalizing these structures for a future marked by efficiency, sustainability, and continued relevance.
Warehouse retrofitting is a strategic modification process aimed at enhancing the efficiency, sustainability, and compliance of metal warehouses with evolving industry standards. It becomes necessary to adapt these structures to contemporary needs, ensuring they remain agile and efficient in an ever-changing business environment.
Estimated costs for retrofitting aspects such as structural upgrades, technology integration, energy-efficient solutions, and others are influenced by factors such as warehouse size, location, and specific retrofitting requirements. These figures provide a range, and actual expenses may vary based on individual circumstances.
Structural upgrades are foundational for the longevity and functionality of metal warehouses. Retrofitting addresses this by reinforcing support systems, adapting structures to accommodate modern storage systems, and ensuring compliance with contemporary building codes.
Advanced technology integration involves implementing automation systems, smart sensors, and data analytics to optimize warehouse operations. This not only enhances operational efficiency but signifies a commitment to embracing technological advancements for future-proofing the warehouse.
Metal warehouse retrofitting offers an economical, sustainable, reliable, and future-proof solution. Advantages include cost-effective investment, operational cost reduction, energy efficiency, continuous operation during retrofitting, state-of-the-art components, enhanced cybersecurity, extended support, and the use of original spare parts, contributing to the warehouse’s resilience and relevance in the long term.
Here I am going to share some steps to get your metal warehouse retrofitting cost estimate report.
You can send us your plan on info@estimatorflorida.com
Before starting your project, we send you a quote for your service. That quote will have detailed information about your project. Here you will get information about the size, difficulty, complexity and bid date when determining pricing.
Our team will takeoff and estimate your project. When we deliver you’ll receive a PDF and an Excel file of your estimate. We can also offer construction lead generation services for the jobs you’d like to pursue further.
561-530-2845
info@estimatorflorida.com
Address
5245 Wiles Rd Apt 3-102 St. Pete Beach, FL 33073 United States
561-530-2845
info@estimatorflorida.com
Address
5245 Wiles Rd Apt 3-102 St. Pete Beach, FL 33073 United States
All copyright © Reserved | Designed By V Marketing Media | Disclaimer