Boost Your Warehouse Construction Bids – Request a Precision Estimate!
- Accurancy
- Efficiency
- Transparency
- Customization
- Time Saving
- Professionalism
- Cost Control
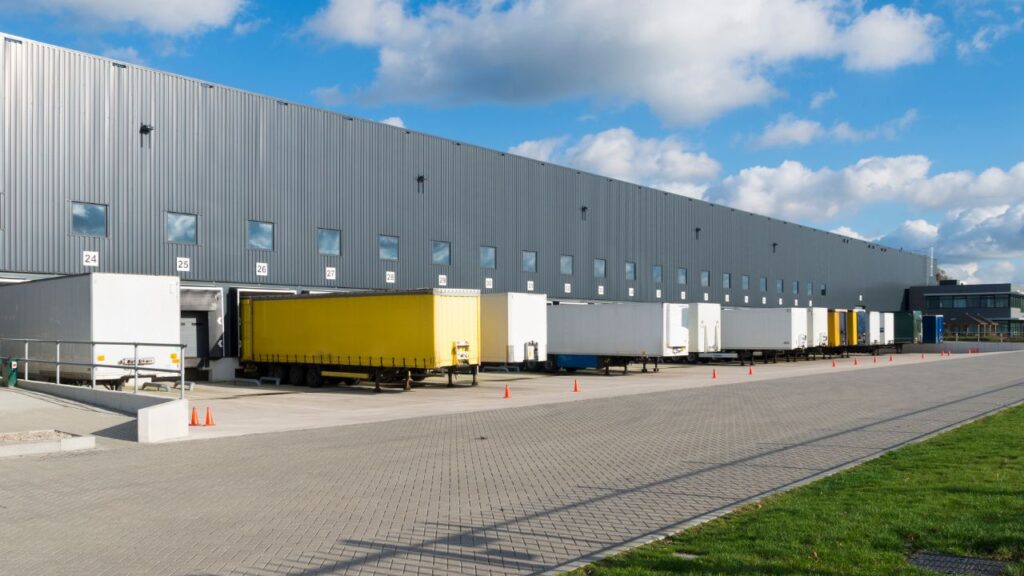
Maintaining a metal warehouse is a crucial aspect of ensuring its longevity, operational efficiency, and compliance with industry standards. From routine upkeep to addressing structural concerns, understanding the various aspects of metal warehouse maintenance costs is essential for businesses looking to optimize their operational space. In this guide, we’ll explore the key considerations, common maintenance areas, and strategies to manage costs effectively.
Regular maintenance forms the bedrock of minimizing long-term costs in metal warehouse management. Conducting routine inspections, typically estimated at an annual range of $1,000 to $5,000 or more, allows businesses to proactively identify potential issues. This preventive approach is instrumental in averting minor problems before they escalate into major repairs. Consistent attention to routine maintenance not only ensures the smooth functioning of warehouse systems but also contributes to prolonged equipment lifespan and cost savings over time.
Fully Insured Licensed
Hire Contractor For Warehouse Construction
Make Informed Design Decisions Showcase Your Design Ideas
Get RenderingMaintaining the structural integrity of a metal warehouse is paramount for both safety and compliance with building codes. Addressing structural repairs promptly is crucial to prevent safety hazards and avoid potential legal ramifications. The costs associated with structural repairs can vary significantly, ranging from $5,000 to $50,000 or more, depending on the extent of the damage. By proactively identifying and rectifying structural issues, businesses not only ensure a secure working environment but also mitigate the risk of more extensive and costly repairs in the future.
The roof serves as a critical component of any warehouse, shielding goods and equipment from the elements. Regular roof maintenance involves thorough inspections for leaks, rust, and overall damage. The budget for roof maintenance may range from $2,000 to $20,000 or can be exceeded, encompassing costs associated with repairs, recoating, or, in some cases, complete roof replacements. Investing in regular roof maintenance is an essential preventive measure, safeguarding assets and preventing potential water damage that could lead to more extensive and expensive repairs down the line.
Embracing energy-efficient systems is a strategic move that aligns both with environmental responsibility and long-term cost-effectiveness. Though the upfront costs of upgrading lighting, HVAC systems, and insulation may range from $10,000 to $50,000 or can be exceeded, the subsequent reduction in ongoing operational costs makes it a judicious investment. Beyond immediate financial benefits, energy-efficient systems contribute to a more sustainable operation, fostering a positive corporate image and meeting the growing demand for eco-conscious business practices.
Incorporating technology into maintenance processes brings about operational efficiencies and cost reduction. Computerized Maintenance Management Systems (CMMS) play a pivotal role in scheduling routine tasks, tracking equipment condition, and managing work orders efficiently. While the initial investment in technology integration may fall within the range of $5,000 to $20,000 or more, the long-term benefits, including reduced downtime and lower maintenance costs, make it a worthwhile and strategic expense. The seamless integration of technology streamlines workflows, enhances overall efficiency, and contributes to a proactive maintenance approach.
Embracing sustainable maintenance practices not only benefits the environment but also contributes to long-term cost savings. Utilizing eco-friendly materials, implementing waste reduction strategies, and adhering to environmental standards can lead to operational efficiencies and positive public perception. Many sustainable practices, while aligning with environmental responsibility, also coincide with cost-effective measures. The estimated annual cost for integrating sustainable practices may range from $2,000 to $10,000 or more, offering businesses an opportunity to reduce their ecological footprint while optimizing operational costs.
While routine maintenance is essential, preparing for emergencies is equally crucial in minimizing unforeseen costs. Having a well-thought-out contingency plan for unexpected events, such as natural disasters or sudden equipment failures, is vital. Businesses should allocate funds for emergency repairs, with potential costs ranging from $10,000 to $50,000 or more, depending on the severity of the situation. A proactive approach to emergency preparedness not only minimizes downtime but also reduces the financial impact of unexpected events, ensuring the resilience of the warehouse operation.
Regular maintenance plays a pivotal role in extending the lifespan of a metal warehouse’s equipment. By conducting routine inspections and addressing potential issues early on, businesses ensure that storage systems, conveyor belts, and machinery operate at optimal efficiency. This proactive approach not only reduces the frequency of replacements but also mitigates the need for major repairs, resulting in significant long-term cost savings. The sustained functionality of equipment enhances the overall operational efficiency of the warehouse.
Safety is a paramount consideration in any warehouse environment. Regular maintenance activities contribute to the enhancement of safety standards by identifying and addressing potential hazards promptly. This commitment to safety goes beyond mere compliance with regulations; it creates a secure working environment for employees. Preventing accidents and injuries not only safeguards personnel but also shields the business from potential legal and financial repercussions, fostering a workplace culture of responsibility.
Proactive maintenance is inherently cost-effective, focusing on preventing issues before they escalate into costly repairs. Routine inspections, structural repairs, and preventive measures contribute to a reduction in overall maintenance costs. By identifying and addressing issues in their early stages, businesses avoid the need for emergency repairs, minimizing the associated higher expenses. This approach not only protects the bottom line but also establishes a foundation for long-term cost savings.
Maintenance efforts aimed at energy-efficient systems contribute to reduced operational costs for a metal warehouse. Upgrading lighting, HVAC systems, and insulation not only enhances energy efficiency but also leads to long-term savings in utility expenses. This dual benefit of sustainability and cost-effectiveness aligns with modern business practices, positioning the warehouse as an environmentally responsible operation. Energy-efficient systems not only reduce costs but also contribute to a positive corporate image.
The optimal performance of a metal warehouse is contingent on the seamless operation of its various systems. Regular maintenance ensures that everything, from conveyor belts to automated storage systems, works efficiently. This, in turn, contributes to streamlined workflows, efficient material handling, and overall operational excellence. An efficiently operating warehouse enhances productivity, reduces downtime, and positively impacts customer satisfaction, reinforcing the warehouse’s role as a reliable and high-performing facility.
Metal warehouses are exposed to environmental elements, making regular roof maintenance and inspections crucial. These efforts safeguard the warehouse and its contents from potential water damage, leaks, or structural issues caused by weather-related factors. Investing in protective measures ensures that the warehouse remains a secure and reliable space for storing goods. This protection not only preserves the integrity of the facility but also safeguards valuable inventory and assets.
Adhering to industry regulations is a critical aspect of maintaining a metal warehouse. Regular maintenance helps ensure that the warehouse meets all safety and environmental standards set by regulatory bodies. This commitment to compliance not only safeguards against potential fines but also fosters a positive public image. Businesses that prioritize regulatory adherence showcase responsibility and integrity, establishing themselves as trustworthy entities in the industry.
Well-maintained warehouses are better equipped to handle emergency situations. Whether facing a sudden equipment failure or unexpected environmental events, having a robust maintenance plan in place allows for swift responses. Emergency preparedness reduces downtime, minimizing the impact on operations and ensuring a quicker return to normalcy. This resilience enhances the warehouse’s overall operational reliability and continuity, mitigating potential disruptions caused by unforeseen circumstances.
Investing in a robust preventive maintenance strategy is an indispensable aspect of cost savings for metal warehouse upkeep. Regular inspections, systematic equipment checks, and timely repairs constitute a proactive approach to identifying and addressing potential issues before they evolve into costly emergencies. By mitigating minor problems in their early stages, businesses can circumvent the need for extensive and expensive repairs, consequently extending the operational lifespan of equipment and diminishing overall maintenance expenditures.
The adage “prevention is better than cure” holds particularly true in the context of warehouse maintenance, where a vigilant approach pays off in terms of both cost-effectiveness and sustained operational efficiency.
The adoption of energy-efficient systems emerges not only as a boon for environmental sustainability but also as a strategic maneuver for long-term cost reduction in metal warehouse maintenance. Embracing technologies such as energy-efficient lighting, HVAC systems, and insulation proves to be an investment that pays dividends over time by curbing utility expenses. While the initial financial commitment might be substantial, the ongoing operational savings render it a prudent and forward-thinking strategy for warehouse maintenance, aligning economic considerations with environmental responsibility.
The integration of technology into maintenance processes marks a paradigm shift in efficiency and cost reduction for metal warehouses. Implementing advanced solutions like Computerized Maintenance Management Systems (CMMS) allows for the automation of scheduling, tracking equipment conditions, and optimizing work orders. The upfront investment in technology integration is offset by the tangible and sustainable benefits of reduced downtime and lower maintenance costs. Embracing technology not only streamlines day-to-day operations but also positions the warehouse for enhanced productivity and cost-efficiency in the dynamic landscape of modern industrial maintenance practices.
From small to large projects, residential to commercial, we’re here to help you win. Fast results guaranteed.
The roof, a critical component of any warehouse, demands consistent attention to ensure long-term cost savings. Regular roof maintenance, involving vigilant inspections for leaks, rust, and damage, acts as a preventive measure against more extensive and expensive repairs or replacements. Proactive measures in roof maintenance guarantee that the structural integrity of the warehouse remains intact, shielding it from the costly consequences of water damage and reinforcing the roof as a protective barrier against external elements.
Incorporating sustainable maintenance practices not only showcases environmental responsibility but also serves as a cornerstone for long-term cost savings in metal warehouse management. The utilization of eco-friendly materials and the implementation of waste reduction strategies contribute to operational efficiencies. Beyond the immediate financial gains, sustainable practices position the warehouse as a responsible and cost-conscious operation, resonating positively with stakeholders who prioritize environmental stewardship in the business landscape.
Empowering warehouse staff with fundamental maintenance skills emerges as a cost-saving initiative. Training employees to conduct routine tasks, such as equipment checks and minor repairs, reduces reliance on external contractors for every maintenance issue. This approach minimizes labor costs and ensures quicker responses to immediate maintenance needs, fostering a culture of self-sufficiency within the warehouse workforce. By leveraging internal capabilities, businesses can achieve cost-effective maintenance solutions and enhance overall operational resilience.
Proactivity in addressing structural issues is a strategic approach to achieving cost savings in metal warehouse maintenance. Regular inspections serve as a vigilant mechanism for identifying potential areas of concern, allowing for prompt and targeted interventions. Addressing structural problems in their early stages prevents safety hazards and mitigates the risk of more extensive, and consequently more expensive, repairs down the line. While the initial investment in structural repairs may vary based on the scope, the long-term savings contribute significantly to the overall cost-effectiveness and sustainability of the warehouse.
Being prepared for emergency situations is pivotal in minimizing costs associated with unforeseen events. Establishing comprehensive contingency plans for potential natural disasters or sudden equipment failures provides the framework for swift and effective responses. Allocating specific funds for emergency repairs ensures that unforeseen costs are managed without disrupting the overall maintenance budgets. This proactive approach not only safeguards the warehouse against unexpected disruptions but also underscores the importance of strategic planning in maintaining cost-effectiveness and operational continuity.
We trust that this comprehensive information has provided you with a deeper understanding of the factors to anticipate and contemplate when embarking on warehouse maintenance. It aims to offer a clearer perspective on the intricacies involved in such endeavors. As you plan your project comprehensively, we encourage you to delve further into the specifics of each maintenance aspect.
Should you have inquiries about metal warehouses, feel free to reach out to Estimate Florida Consulting. We are here to assist you in navigating the intricacies of your project and providing valuable insights.
Prioritizing the maintenance of a metal warehouse is not only essential for its longevity and operational efficiency but also a strategic investment in cost-effectiveness. By adopting preventive measures, embracing energy-efficient systems, integrating technology, and considering sustainable practices, businesses can achieve long-term savings while ensuring a secure and optimized operational environment. The key lies in proactive structural repairs, routine maintenance, and effective contingency planning. As you embark on your warehouse maintenance journey, delve into the specifics of each area and consider reaching out to professionals for guidance. For inquiries about metal warehouses, Estimate Florida Consulting is here to assist, providing valuable insights for your project’s success.
Routine maintenance is essential for a metal warehouse as it helps identify and address potential issues early on, preventing minor problems from escalating into major repairs. This proactive approach ensures the smooth functioning of warehouse systems and contributes to prolonged equipment lifespan, ultimately leading to cost savings over time.
The costs for structural repairs in a metal warehouse can vary significantly, ranging from $5,000 to $50,000 or more, depending on the extent of the damage. Proactively addressing structural issues is crucial for ensuring a secure working environment, preventing safety hazards, and avoiding potential legal ramifications.
Roof maintenance is critical for a metal warehouse as the roof serves as a protective barrier against environmental elements. Regular inspections for leaks, rust, and damage are essential. The budget for roof maintenance may range from $2,000 to $20,000 or more, encompassing costs associated with repairs, recoating, or complete roof replacements.
Embracing energy-efficient systems, while involving upfront costs ranging from $10,000 to $50,000, contributes to long-term cost-effectiveness and environmental responsibility. These systems reduce ongoing operational costs, enhance sustainability, and foster a positive corporate image aligned with eco-conscious business practices.
Incorporating technology, such as Computerized Maintenance Management Systems (CMMS), streamlines maintenance processes, schedules routine tasks, tracks equipment condition, and manages work orders efficiently. While the initial investment may be $5,000 to $20,000 or more, the long-term benefits include reduced downtime and lower maintenance costs, making it a worthwhile and strategic expense.
Here I am going to share some steps to get your metal warehouse maintenance cost estimate report.
You can send us your plan on info@estimatorflorida.com
Before starting your project, we send you a quote for your service. That quote will have detailed information about your project. Here you will get information about the size, difficulty, complexity and bid date when determining pricing.
Our team will takeoff and estimate your project. When we deliver you’ll receive a PDF and an Excel file of your estimate. We can also offer construction lead generation services for the jobs you’d like to pursue further.
561-530-2845
info@estimatorflorida.com
Address
5245 Wiles Rd Apt 3-102 St. Pete Beach, FL 33073 United States
561-530-2845
info@estimatorflorida.com
Address
5245 Wiles Rd Apt 3-102 St. Pete Beach, FL 33073 United States
All copyright © Reserved | Designed By V Marketing Media | Disclaimer