Boost Your Warehouse Construction Bids – Request a Precision Estimate!
- Accurancy
- Efficiency
- Transparency
- Customization
- Time Saving
- Professionalism
- Cost Control
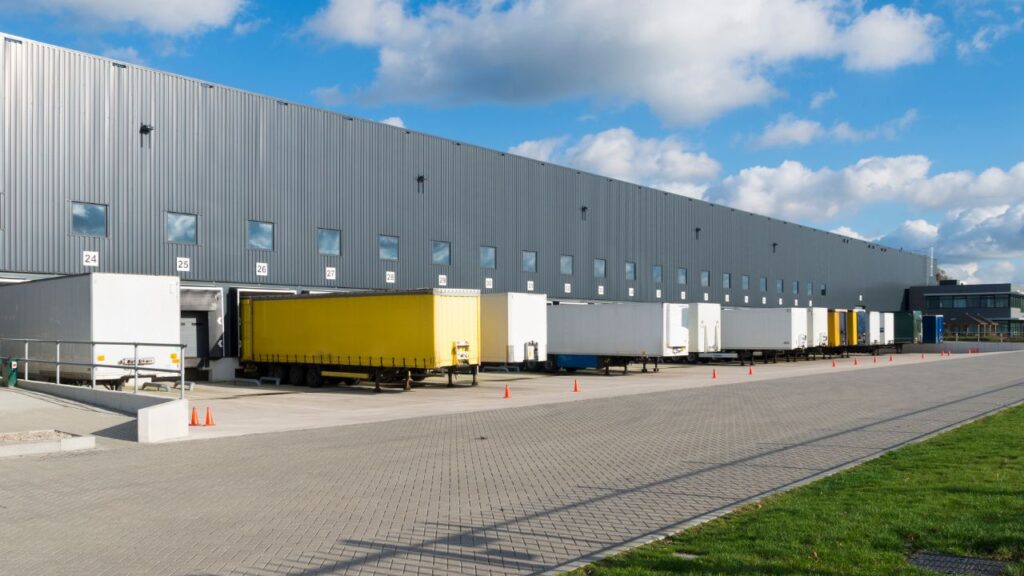
The construction of a metal warehouse involves various elements, with framing being a critical component that influences both the structural integrity and overall cost of the project. Metal framing offers several advantages, including durability, sustainability, and cost-effectiveness.the total average cost for a complete metal warehouse framing project typically ranges from $500,000 to $2 million or more, depending on the aforementioned factors.
This estimate encompasses all aspects of the project, including the metal framing, foundation work, site preparation, insulation, doors, windows, and any additional features or customization.
The wide range in cost reflects the variability in project requirements and local construction costs.
It’s crucial to note that these are general averages, and actual costs can vary significantly based on project specifics and any changes in market conditions or construction trends since my last update.
Fully Insured Licensed
Hire Contractor For Warehouse Construction
Make Informed Design Decisions Showcase Your Design Ideas
Get RenderingThe cost of steel is a critical determinant in the overall expense of metal warehouse framing. Steel prices are subject to constant fluctuations due to dynamic market conditions, supply and demand dynamics, and global economic factors. As of the latest data available, the average cost of structural steel in the United States is approximately $900 to $1,500 per ton. The type and grade of steel chosen for warehouse framing significantly influence costs. High-strength steel, while more expensive at around $1,200 to $2,000 per ton, often translates to a reduced quantity of material required, contributing to potential savings. Market conditions play a crucial role, as increases in demand or disruptions in the supply chain can lead to spikes in steel prices. Additionally, the availability of alternative materials or innovations in steel production techniques can impact the overall cost structure. It is imperative for project managers to closely monitor steel prices, engage with reputable suppliers, and consider long-term trends when budgeting for
Protective coatings and finishes are essential considerations in metal warehouse framing, playing a vital role in enhancing the longevity and resilience of the steel structure. The choice of coating can have implications for both upfront costs and long-term maintenance expenses. As of the latest information, the cost of galvanized coatings, a common choice for corrosion resistance, ranges from $1.50 to $3.50 per square foot. While such coatings contribute to the durability of the steel framing, they also add to the overall material costs. The selection of coatings should be guided by the environmental conditions at the construction site, with factors such as exposure to harsh weather, industrial pollutants, or proximity to saltwater influencing the decision-making process. Investing in high-quality coatings can yield substantial benefits over the life cycle of the warehouse, reducing the need for frequent maintenance and repairs. Therefore, while coatings contribute to initial costs, they are a crucial element in ensuring the structural integrity and longevity of the metal warehouse framing.
The architectural complexity of a warehouse significantly influences the framing cost, with more intricate designs translating to higher expenses. Warehouses featuring unconventional shapes, additional architectural features, or unique design elements may necessitate more specialized framing solutions.
The complexity of these designs often requires custom engineering and fabrication, contributing to increased material and labor costs. Moreover, intricate designs may result in more time-intensive construction processes, further impacting overall project expenses. As a result, projects with higher architectural complexity typically incur a framing cost that ranges from 15% to 30% above the cost of more standard warehouse designs. It is essential for project planners and stakeholders to carefully assess the balance between architectural aspirations and budget constraints to ensure a cost-effective yet aesthetically pleasing metal warehouse frame.
The role of structural engineering is paramount in designing a robust and safe metal warehouse frame. The complexity of the engineering services required can have a direct impact on overall project costs. Structural engineers are crucial for addressing factors such as seismic considerations or special load-bearing requirements. Their expertise ensures that the metal framing system is not only structurally sound but also compliant with safety standards and local building codes. The cost of structural engineering services for metal warehouse framing typically ranges from 5% to 10% of the total construction cost. Projects in areas prone to seismic activity or with unique structural challenges may incur higher engineering costs due to the additional analysis and design considerations. While the cost of structural engineering represents a relatively small percentage of the overall project cost, its influence on the safety and integrity of the metal warehouse frame underscores its significance in the construction process.
The assembly of metal warehouse frames heavily relies on skilled labor, including welders, steel erectors, and other experienced workers. The cost of skilled labor is a significant factor influencing the overall expense of constructing a metal warehouse frame. Labor costs can vary widely, skilled labor rates for welding and steel erection typically range from $25 to $50 or more per hour. The overall cost depends on the number of hours worked, the complexity of the project, and the region’s labor market conditions. In areas with high demand and a scarcity of skilled labor, wages may be on the higher end, impacting the project’s labor cost. It’s crucial for project planners to conduct a thorough assessment of local labor rates to accurately estimate the skilled labor cost for the metal warehouse frame assembly.
The efficiency of the construction process, particularly the installation time, directly affects labor costs associated with metal warehouse frame assembly. As hourly wages for skilled construction laborers range from $20 to $40 or more. Faster assembly times may necessitate a larger workforce but can lead to a reduction in the overall project duration. While having more workers on-site may increase labor costs, the potential time savings can offset other associated expenses. The overall labor cost for installation time is typically calculated based on the number of hours worked by the skilled laborers. Striking the right balance between workforce size, project duration, and associated costs is critical for optimizing efficiency without compromising the quality of the metal warehouse frame construction.
The condition of the construction site plays a crucial role in determining project costs, particularly when it comes to metal warehouse frame assembly. Sites with challenging terrain, poor soil conditions, or pre-existing structures may require extensive site preparation efforts. This can include land grading, clearing, and soil stabilization, adding to the overall project expenses. In instances where specialized foundation work is necessary due to uneven terrain or problematic soil conditions, costs can increase significantly. As the cost of site preparation for a metal warehouse construction project typically ranges from $5,000 to $20,000 or more, depending on the complexity of the site conditions and required groundwork.
The logistics and transportation aspect of a metal warehouse construction project involves considerations such as the distance between the steel fabrication facility and the construction site, as well as the methods of transportation. The transportation costs for delivering steel components to the construction site can vary based on factors like fuel prices, the size of the shipment, and the chosen shipping methods. As transportation costs for steel components typically range from $2,000 to $10,000 or more, depending on the distance and logistics involved. Additionally, considerations for offloading and handling materials at the construction site should be factored into the budget. Accurate estimation of logistics and transportation costs is essential for project planners to ensure that the overall budget accounts for the seamless and cost-effective delivery of materials to the construction site.
Ensuring compliance with local building codes and regulations is an indispensable aspect of any construction project, including metal warehouse framing. Local building codes are established to safeguard public safety, health, and welfare, providing a set of standards that structures must meet.
Failure to comply with these codes can result in costly legal consequences and, more importantly, compromise the structural integrity and safety of the warehouse. The cost associated with adhering to building codes varies depending on the specific requirements of the jurisdiction. For instance, certain areas might necessitate additional engineering assessments or design modifications to meet seismic or environmental considerations, adding an estimated $5,000 to $15,000 to the overall project costs.
Additionally, the use of specific materials or construction methods mandated by local codes may impact material and labor expenses. It is crucial for project managers to engage with local building authorities early in the planning phase to accurately estimate the costs associated with code compliance and ensure a smooth approval process.
The cost of inspections and approvals from relevant authorities is a significant consideration in the budgeting of metal warehouse framing projects. Local building departments often require inspections at various stages of construction to verify compliance with approved plans and building codes. The cost of inspections can vary widely, with fees ranging from $500 to $2,500 or more depending on the complexity of the project and the number of required inspections. Delays in the approval process can have cascading effects on the construction timeline, impacting labor costs, equipment rentals, and overall project scheduling. Additionally, unforeseen issues identified during inspections may necessitate costly modifications or remediation efforts, potentially adding an extra $2,000 to $5,000 or more to the overall project budget. To mitigate these risks, it is essential for project managers to allocate sufficient funds for inspection and approval costs, engage proactively with building authorities, and adhere closely to project timelines to avoid potential financial and scheduling setbacks.
Investing time and resources in the meticulous design of a metal warehouse frame is a strategic move that can yield substantial cost savings. Collaborate closely with architects and structural engineers to craft designs that not only meet structural requirements but also minimize material waste and reduce the need for complex structural elements. By maximizing the use of standardized components, an optimized design can result in lower material costs and streamline the construction process. The careful consideration of design efficiency can lead to a more economical project overall, providing a foundation for cost-effective construction practices and long-term operational efficiency.
The choice of steel for warehouse framing is a pivotal decision that directly impacts both structural integrity and project costs. To achieve a balance between strength requirements and cost considerations, conduct a thorough analysis of market prices and engage in negotiations with steel suppliers to secure competitive rates. Additionally, exploring the option of bulk material procurement can provide opportunities for significant cost savings through volume discounts. The careful selection and procurement of materials are integral components of cost-effective metal warehouse framing, with strategic decisions influencing the overall project budget.
Meticulous project planning is a cornerstone of cost-saving strategies in metal warehouse framing. Establishing a realistic construction schedule and identifying potential bottlenecks in the process are key elements of advanced planning. Close coordination with suppliers and contractors facilitates optimized resource allocation, minimizing delays and preventing costly overruns. Early identification of challenges allows for proactive solutions, contributing to a streamlined construction process and ensuring that the project remains within budgetary constraints.
Efficient labor management is a critical factor in achieving cost savings in metal warehouse framing. While hiring skilled and experienced labor is essential, it is equally important to ensure that the workforce is appropriately sized for the project’s scope. Implementing effective project management and communication strategies helps minimize downtime, optimize workflow, and prevent unnecessary labor costs associated with delays or rework. A well-managed labor force not only contributes to cost efficiency but also ensures the timely completion of the project.
The adoption of prefabrication and modular construction techniques presents an innovative avenue for cost savings in metal warehouse framing. Prefabricating steel components offsite can reduce labor requirements, accelerate construction times, and enhance quality control. Modular construction, with standardized components assembled on-site, minimizes material waste and overall construction time. Exploring these advanced construction approaches offers the potential for significant cost reductions while maintaining the structural integrity of the warehouse frame.
Implementing energy-efficient design principles is a forward-thinking strategy that can lead to both short-term and long-term cost savings. Consider incorporating features such as proper insulation, energy-efficient lighting, and natural ventilation. Although initial costs may be slightly higher, the long-term energy savings contribute to a more economical warehouse operation, reducing overall operational costs over time. Energy-efficient design not only aligns with sustainability goals but also adds a layer of financial prudence to the overall project.
Adopting a value engineering approach is a proactive strategy for identifying opportunities to reduce costs without compromising structural integrity. Engage with the project team, including architects, engineers, and contractors, to evaluate alternatives for materials, construction methods, and design elements. Through collaborative brainstorming, innovative and cost-effective solutions can be implemented throughout the project lifecycle. Value engineering is a dynamic process that encourages continuous improvement, allowing for the optimization of costs while maintaining the highest standards of construction.
The construction of a metal warehouse frame involves various factors influencing costs, ranging from steel prices to labor efficiency and regulatory compliance. The estimated project cost falls between $500,000 to $2 million, considering elements like framing, foundation work, and site preparation.
To optimize cost-effectiveness, key strategies include designing efficiently to minimize waste, carefully selecting and procuring materials, meticulous project planning, efficient labor management, exploring prefabrication, prioritizing energy-efficient design, and adopting value engineering. These strategies ensure a balance between cost savings and a durable, sustainable metal warehouse frame.
Collaborative efforts among project stakeholders, continuous market monitoring, and strategic decision-making are essential for successfully navigating the complexities of metal warehouse framing projects, ultimately achieving both budgetary and structural goals.
The total average cost for a complete metal warehouse framing project typically ranges from $500,000 to $2 million or more. This estimate includes various elements such as metal framing, foundation work, site preparation, insulation, doors, windows, and additional features. The actual cost may vary based on project specifics and local construction costs.
Steel prices are a critical determinant in the overall expense of metal warehouse framing. The cost of structural steel in the United States, on average, ranges from $900 to $1,500 per ton. Factors such as market conditions, supply and demand dynamics, and global economic factors contribute to constant fluctuations in steel prices. The type and grade of steel selected also significantly influence costs.
Protective coatings, such as galvanized coatings for corrosion resistance, are essential in enhancing the longevity and resilience of the steel structure. The cost of galvanized coatings typically ranges from $1.50 to $3.50 per square foot. While these coatings contribute to durability, they add to the overall material costs. High-quality coatings can, however, reduce the need for frequent maintenance and repairs, offering long-term benefits.
Architectural complexity, including unconventional shapes or unique design elements, can significantly influence framing costs. More intricate designs may require custom engineering and fabrication, contributing to increased material and labor costs. Projects with higher architectural complexity may incur framing costs ranging from 15% to 30% above the cost of standard warehouse designs.
Logistics and transportation costs involve factors such as the distance between the steel fabrication facility and the construction site, fuel prices, shipment size, and chosen shipping methods. Transportation costs for delivering steel components typically range from $2,000 to $10,000 or more. Accurate estimation of logistics costs is crucial to ensure seamless and cost-effective material delivery to the construction site.
Here I am going to share some steps to get your metal warehouse framing cost estimate report.
You can send us your plan on info@estimatorflorida.com
Before starting your project, we send you a quote for your service. That quote will have detailed information about your project. Here you will get information about the size, difficulty, complexity and bid date when determining pricing.
Our team will takeoff and estimate your project. When we deliver you’ll receive a PDF and an Excel file of your estimate. We can also offer construction lead generation services for the jobs you’d like to pursue further.
561-530-2845
info@estimatorflorida.com
Address
5245 Wiles Rd Apt 3-102 St. Pete Beach, FL 33073 United States
561-530-2845
info@estimatorflorida.com
Address
5245 Wiles Rd Apt 3-102 St. Pete Beach, FL 33073 United States
All copyright © Reserved | Designed By V Marketing Media | Disclaimer