Boost Your Warehouse Construction Bids – Request a Precision Estimate!
- Accurancy
- Efficiency
- Transparency
- Customization
- Time Saving
- Professionalism
- Cost Control
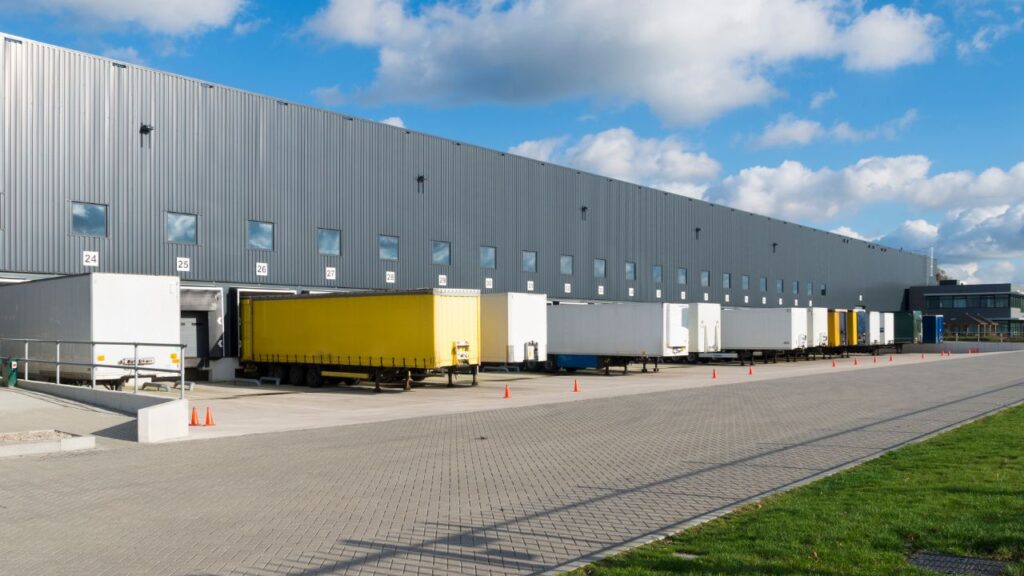
Expanding a metal warehouse involves careful consideration of construction costs, which can vary significantly based on the size and scope of the project. On average, the cost to build a warehouse falls within the range of $20 to $60 per square foot. For a compact 30×40 ft warehouse, the estimated cost hovers around $25,000, while a more expansive distribution center spanning 50,000 to 60,000 sq ft can incur expenses ranging from $750,000 to $1 million. Breaking down the expenses further, the shell building alone averages at $20 per square foot.
Smaller warehouses, such as those measuring 40×60 ft, can be erected for as little as $150,000, while larger counterparts encompassing 50,000 sq ft may demand investments reaching up to $3,125,000. At Estimate Florida Consulting, we understand the importance of accurate project estimates.
Fully Insured Licensed
Hire Contractor For Warehouse Construction
Make Informed Design Decisions Showcase Your Design Ideas
Get RenderingHard costs constitute tangible, physical expenses directly tied to the construction and physical development of the metal warehouse. These are straightforward expenditures with clear quantifiable values.
The fundamental building blocks of the warehouse, materials include steel, concrete, insulation, roofing, doors, and fixtures. Estimating costs:
Direct expenses for skilled and unskilled labor, encompassing wages, benefits, and payroll taxes for construction workers, project managers, and subcontractors.
Costs associated with clearing the land, grading, excavation, and any necessary groundwork to ready the site for construction.
Total Hard Costs: $620,000 or can be exceeded
Soft costs are indirect expenses crucial for planning, design, and management, often not immediately visible but integral to a successful warehouse expansion.
Professional services costs for designing the expansion, covering architectural plans, engineering studies, and other design-related expenses.
Fees for obtaining necessary permits, compliance with building codes, environmental assessments, and legal consulting.
Additional insurance premiums to cover the expanded facility during construction and after completion.
Costs related to hiring a project manager or project management team to oversee the entire construction process and ensure it stays on schedule and within budget.
Expenses related to incorporating technology and automation solutions into the warehouse design.
Total Soft Costs: $190,000 or can be exceeded
Financial costs involve expenses associated with securing funding and managing the financial aspects of the expansion project, which may vary based on financing options.
If the expansion is funded through loans, interest payments will be incurred.
Fees associated with obtaining loans or financing, including application fees, origination fees, and other financial service charges.
The potential loss of income or revenue that could have been generated during the construction period.
Grand Total Cost (Hard + Soft + Financial): $980,000 or can be exceeded
Breaking down costs into these categories and providing detailed estimates allows for a comprehensive understanding of the financial implications of a metal warehouse expansion. This breakdown facilitates precise budgeting, financial planning, and risk management throughout the entire expansion process. Actual costs may vary based on specific project requirements and market conditions.
Cost optimization is a critical aspect of any warehouse expansion project, helping businesses achieve their goals while maintaining financial prudence. Here are key strategies to optimize costs for a metal warehouse expansion:
A successful metal warehouse expansion begins with comprehensive planning and meticulous budgeting. A detailed project scope, including specific size, features, and specifications, should be established upfront. This clarity helps prevent unnecessary changes during construction, reducing the risk of additional costs. Simultaneously, developing an accurate budget that encompasses all anticipated expenses is crucial. This includes materials, labor, site preparation, and soft costs. A well-thought-out plan and budget provide a roadmap for the project, enabling better financial planning and resource allocation throughout the expansion process.
Value engineering involves the exploration of cost-effective alternatives without compromising the structural integrity and functionality of the metal warehouse. This strategy seeks to optimize the use of materials and design, minimizing waste and maximizing efficiency. It involves critically assessing each component of the project, from the choice of construction materials to the design elements. The goal is to deliver the desired outcomes at the most economical cost. By embracing value engineering, businesses can make informed decisions that contribute to both cost savings and the overall success of the warehouse expansion.
Efficiency in energy usage is a key factor in long-term cost optimization for a metal warehouse expansion. Investing in high-quality insulation and roofing materials is paramount to regulating temperature effectively, thereby reducing ongoing energy expenses. Additionally, incorporating green technologies such as solar panels and energy-efficient lighting can lead to substantial operational cost savings over the warehouse’s lifespan. By prioritizing energy-efficient solutions, businesses not only reduce their environmental footprint but also enhance the sustainability and cost-effectiveness of their expanded warehouse.
Strategic integration of technology is a cornerstone of cost optimization in warehouse expansion projects. Implementing Warehouse Management Systems (WMS) enhances inventory management, order processing, and overall operational efficiency. Automation solutions, such as conveyor systems and robotics, can optimize workflows, reduce labor requirements, and enhance overall productivity. The upfront investment in technology integration pays off in the long run, leading to streamlined operations, reduced operational costs, and increased competitiveness in the market.
Effective negotiation and vendor management play a crucial role in controlling costs during a metal warehouse expansion. Negotiating bulk purchases with suppliers can yield substantial discounts on construction materials. Seeking competitive bids from multiple contractors and subcontractors ensures that the project benefits from the most cost-effective options available. A strategic approach to negotiation and vendor management allows businesses to maximize their purchasing power, resulting in cost savings without compromising the quality of materials and services.
Lean construction practices focus on eliminating waste and improving overall project efficiency. By streamlining processes and adopting a just-in-time delivery approach, businesses can reduce costs associated with excess materials and unnecessary delays. Lean construction emphasizes collaboration, continuous improvement, and the elimination of non-value-added activities. Through the adoption of lean principles, construction projects can achieve higher levels of efficiency, delivering the desired outcomes while minimizing costs and optimizing resource utilization.
Robust risk management is a fundamental strategy for cost optimization in warehouse expansion. Developing a contingency plan that addresses unforeseen challenges and potential risks is essential. A well-defined contingency budget provides a financial buffer to handle unexpected circumstances, preventing budget overruns. Regular insurance reviews and a proactive approach to compliance with safety and regulatory standards contribute to risk mitigation. By anticipating and addressing potential risks, businesses can safeguard their budgets and ensure the successful and cost-effective completion of the warehouse expansion project.
Efficient project management is a cornerstone of cost optimization in warehouse expansion. Developing a realistic construction schedule that accounts for potential challenges and dependencies helps minimize project delays and associated costs. Hiring an experienced project manager to oversee the entire construction process is crucial for effective coordination, problem resolution, and adherence to the established timeline. By optimizing project management practices, businesses can ensure that resources are utilized efficiently, and the project progresses in a timely and cost-effective manner.
A deep understanding of local building codes and regulations is indispensable for cost optimization in warehouse expansion. Businesses need to proactively address regulatory requirements to prevent costly revisions and modifications during construction. Engaging with local authorities early in the planning phase helps ensure compliance with all applicable standards. By staying informed and proactive in navigating regulatory landscapes, businesses can avoid fines, delays, and unexpected expenses, contributing to a smoother and more cost-effective expansion process.
Investing in employee training and safety measures is not just about compliance but is a proactive cost optimization strategy. Proper training reduces the likelihood of accidents, which can result in costly delays, medical expenses, and legal repercussions. A safety-focused culture contributes to a more efficient and productive work environment, minimizing the risk of injuries and associated costs. Retaining skilled workers through ongoing training programs can also reduce turnover, preventing the need for additional recruitment and training expenses.
Cost optimization extends beyond the construction phase to post-expansion operational efficiency. Designing the warehouse for optimal space utilization minimizes the need for future expansions, saving on additional construction costs. Developing a proactive maintenance plan ensures that the facility remains in optimal condition, preventing costly repairs and prolonging the lifespan of the infrastructure. By considering the long-term operational implications, businesses can optimize costs throughout the entire lifecycle of the expanded metal warehouse.
From small to large projects, residential to commercial, we’re here to help you win. Fast results guaranteed.
The initial phase in establishing a warehouse construction project involves crucial decisions about its size and design. The size is influenced by business needs, inventory volume, and the workforce size. Warehouse design considerations include whether a simple rectangular building suffices or if a more intricate multistory structure is necessary. Additionally, the type of inventory to be stored plays a role in determining the design. Metal construction, renowned for its durability and cost-effectiveness, is often a preferred choice. When opting for metal buildings, businesses need to assess factors like warehouse size, design complexity, and the nature of the inventory to ensure compliance with building codes and regulations in the area.
Metal buildings offer flexibility in terms of:
Before embarking on construction, businesses should thoroughly evaluate their warehouse size and design requirements. This proactive approach ensures that the final structure meets operational needs efficiently while staying within budgetary constraints.
Selecting an appropriate location for the warehouse is paramount to its success. The chosen location directly impacts transportation costs, labor expenses, and overall operational efficiency.
Factors to consider when choosing a warehouse location include:
Choosing the right warehouse location requires a careful evaluation of factors like accessibility, labor availability, and site suitability. Industrial parks, in particular, offer a structured setting with existing amenities, enhancing overall operational efficiency and success.
The expansion of a metal warehouse demands a thorough understanding of the associated costs and effective strategies for optimization. Warehouse construction costs, encompassing hard, soft, and financial elements, necessitate meticulous planning and budgeting. Breaking down these costs provides a comprehensive view, aiding in precise financial planning and risk management throughout the expansion process. Cost optimization strategies, ranging from comprehensive planning and value engineering to energy-efficient solutions and advanced technology integration, further contribute to the overall success of the project. Additionally, setting up a warehouse construction project involves key steps, including determining size and design, choosing an optimal location, and considering the long-term implications of post-expansion operational efficiency. By adopting these approaches, businesses can ensure not only the efficient expansion of their metal warehouse but also long-term cost-effectiveness and operational success.
The cost of expanding a metal warehouse is influenced by various factors, including materials, labor, site preparation, architectural and engineering fees, permitting, insurance, project management, technology integration, financing, and potential opportunity costs.
Hard costs refer to tangible, physical expenses directly tied to construction, such as materials, labor, and site preparation. Soft costs, on the other hand, are indirect expenses related to planning, design, and management, including architectural and engineering fees, permitting, insurance, project management, and technology integration.
Cost optimization strategies include comprehensive planning and budgeting, value engineering, energy-efficient solutions, technology integration, negotiation and vendor management, lean construction practices, robust risk management, optimized project management, and considering local and regulatory knowledge.
Estimating material costs involves considering fundamental building blocks such as steel, concrete, insulation, roofing, doors, and fixtures. Businesses can use detailed estimates for each material type, factoring in quantities and market prices to arrive at an accurate projection.
Efficient project management is crucial for cost optimization. A well-defined construction schedule, experienced project manager, and proactive problem resolution help minimize delays and associated costs. It ensures that resources are utilized efficiently, and the project progresses within the established timeline and budget.
To minimize additional costs, businesses should engage in comprehensive planning, conduct thorough budgeting, embrace value engineering, prioritize energy-efficient solutions, integrate technology strategically, negotiate effectively with vendors, adopt lean construction practices, and proactively manage risks and compliance with local regulations.
Here I am going to share some steps to get your metal warehouse expansion cost estimate report.
You can send us your plan on info@estimatorflorida.com
Before starting your project, we send you a quote for your service. That quote will have detailed information about your project. Here you will get information about the size, difficulty, complexity and bid date when determining pricing.
Our team will takeoff and estimate your project. When we deliver you’ll receive a PDF and an Excel file of your estimate. We can also offer construction lead generation services for the jobs you’d like to pursue further.
561-530-2845
info@estimatorflorida.com
Address
5245 Wiles Rd Apt 3-102 St. Pete Beach, FL 33073 United States
561-530-2845
info@estimatorflorida.com
Address
5245 Wiles Rd Apt 3-102 St. Pete Beach, FL 33073 United States
All copyright © Reserved | Designed By V Marketing Media | Disclaimer