Boost Your Warehouse Construction Bids – Request a Precision Estimate!
- Accurancy
- Efficiency
- Transparency
- Customization
- Time Saving
- Professionalism
- Cost Control
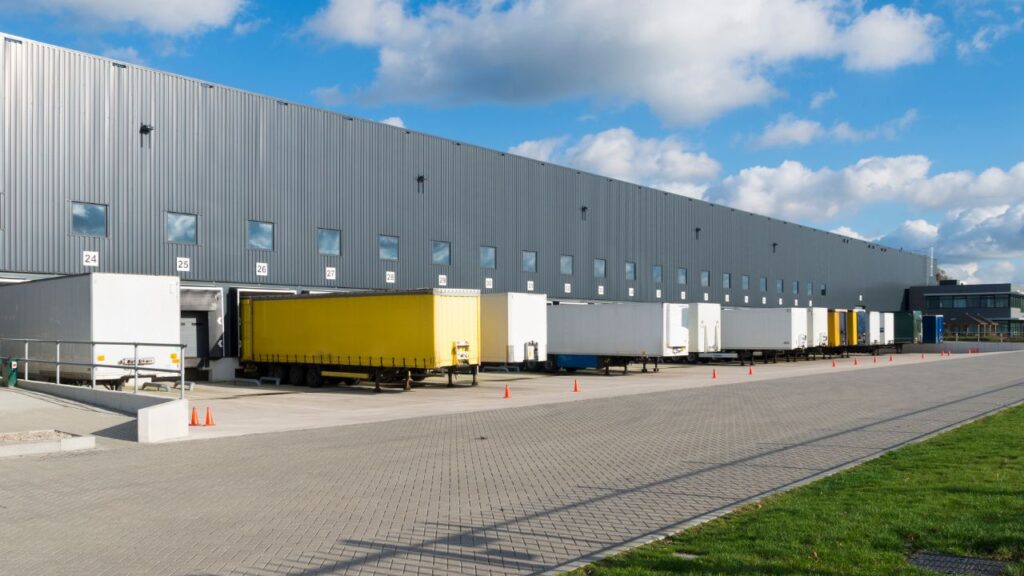
The construction cost of a metal warehouse in Florida varies significantly, primarily determined by its size and the selected options. Generally, the expenses can range from $5,000 to well over $100,000. It’s important to note that the quoted figures do not include the cost of a concrete slab, an essential element in warehouse construction.
The additional expense for a concrete slab is noteworthy, with prices spanning from $4 to $10 per square foot.
These cost considerations underscore the importance of thorough planning and budgeting when embarking on metal warehouse construction projects in the dynamic and diverse environment of Florida. At Estimate Florida Consulting, we understand the significance of accurate estimates for your projects.
Fully Insured Licensed
Hire Contractor For Warehouse Construction
Make Informed Design Decisions Showcase Your Design Ideas
Get RenderingThe size and square footage of a metal warehouse wield a profound influence on construction costs. Larger buildings, characterized by expansive square footage, invariably translate to higher expenses. This is primarily due to the augmented material requirements necessary for construction and the additional labor needed to complete the project. The dimensions, height, and layout of the warehouse contribute significantly to the overall square footage. Beyond impacting initial construction costs, these dimensions play a crucial role in determining operational efficiency and the potential for future scalability. Businesses undertaking the construction of a metal warehouse must meticulously assess their storage needs and operational requirements, striking a delicate balance between the desired warehouse size and the associated construction costs.
The architectural design and intricacy of a metal building constitute pivotal factors that profoundly affect construction costs. Opting for intricate designs with specialized features can escalate project expenses, necessitating additional materials and skilled labor. Whether it involves unique roofing styles, distinctive façade treatments, or the integration of specific architectural elements, design complexity invariably leads to increased costs. While such designs may enhance the aesthetic appeal of the warehouse, stakeholders must judiciously weigh these additional costs against the functional benefits and the overall budget. Collaborating closely with architects and engineers during the design phase becomes imperative to ensure that the chosen design not only aligns with aesthetic preferences but also adheres to stringent budgetary considerations.
The geographical location of the construction site emerges as a critical determinant in assessing overall costs for metal warehouse construction. Local building codes, climate considerations, and accessibility factors contribute to variations in construction expenses. Different regions come with distinct regulatory requirements and environmental conditions that invariably impact the construction process. For example, areas with stringent building codes might demand additional investments to meet compliance standards.
Moreover, exposure to extreme weather conditions due to geographical location may necessitate specific construction features, adding to costs. The accessibility of the construction site also influences transportation costs for materials and labor. Recognizing the significance of these location-specific factors, a thorough site analysis becomes paramount for anticipating and budgeting for region-specific construction challenges.
The condition of the construction site and the extent of site preparation required play a pivotal role in determining overall costs for metal warehouse construction. Fundamental steps such as clearing, grading, and addressing soil conditions are essential aspects of site preparation, each contributing significantly to the budget. Sites with uneven terrain or poor soil quality may require additional grading and foundation work, leading to increased expenses. Furthermore, addressing environmental factors, including potential water runoff or drainage issues, is crucial for ensuring the long-term stability of the warehouse. Investing in thorough site preparation not only establishes a solid foundation for construction but also mitigates complications that may arise during and after the building process, contributing to overall cost-effectiveness.
The selection of materials, particularly the type and quality of metal, stands out as a critical determinant in shaping construction costs for metal warehouses. Opting for high-quality steel and metal alloys may entail higher upfront costs, but these choices offer enhanced durability and longevity, ultimately leading to reduced long-term maintenance expenses. The cost of metal can fluctuate based on market conditions, and decisions regarding different metal grades and coatings can significantly impact overall expenses. Additionally, the choice of supplementary materials, such as insulation and roofing materials, adds to the overall cost. Striking a judicious balance between upfront material costs and long-term durability is paramount for informed decision-making during the material selection process.
The functionality of a warehouse often necessitates specific features and accessories, each contributing to construction and operational costs. Loading docks, insulation, ventilation systems, and fire suppression systems are integral elements enhancing warehouse efficiency and usability. While these features undoubtedly add to the overall cost of construction, they play a crucial role in ensuring that the warehouse meets industry standards and operational requirements. Businesses must meticulously assess their operational needs and regulatory obligations to determine the necessary accessories and features. This involves considering both their upfront costs and the long-term benefits they bring to the functionality and safety of the warehouse, striking a balance between initial expenses and enduring advantages.
Meeting local building codes and adhering to regulatory requirements are non-negotiable aspects of any construction project, integral to budget considerations. Costs associated with obtaining permits, conforming to zoning regulations, and ensuring compliance with safety standards must be factored into the overall budget from the project’s outset. Failure to account for these regulatory costs can lead to delays, fines, and potential legal complications. Engaging with local authorities early in the planning process and collaborating with professionals possessing expertise in navigating regulatory requirements become essential steps. This ensures that the warehouse construction adheres to all applicable codes and standards, mitigating the risk of unforeseen financial and legal challenges.
The cost of skilled labor represents a substantial component of the overall budget for metal building construction. Skilled labor costs can vary based on factors such as location, prevailing labor market conditions, and the complexity of the project. Various tasks, including framing, roofing, welding, and assembly, require skilled workers. The availability of skilled labor in a given region, along with considerations such as union requirements and prevailing wages, significantly influences labor costs. Efficient project management and workforce optimization strategies become imperative for controlling labor cost escalations. Ensuring that the construction process remains within budget constraints requires careful planning, coordination, and adaptability to labor market conditions.
Establishing a realistic budget serves as the bedrock for the successful execution of any warehouse construction project. A meticulous and comprehensive assessment of financial resources is paramount, encompassing a detailed understanding of construction costs, permitting expenses, labor fees, and potential unforeseen expenditures. The process involves a nuanced examination of each facet of the project’s financial landscape, ensuring that stakeholders are well-informed about the financial commitments involved.
This proactive approach not only provides a clear roadmap for the allocation of resources but also acts as a safeguard against budget overruns. By acknowledging and addressing budgetary constraints from the project’s inception, stakeholders can make informed decisions, prevent financial setbacks, and maintain fiscal responsibility throughout the planning and construction phases, contributing to the overall success of the warehouse construction endeavor.
Anticipating future needs and strategically designing the warehouse with scalability in mind is a foresighted approach that can yield substantial long-term cost savings. Incorporating features that allow for seamless future expansions is an investment in the adaptability and longevity of the facility. This proactive design strategy minimizes the need for extensive modifications or the undertaking of additional construction projects when business growth demands an expanded warehouse space. The dynamic nature of business landscapes, where growth and changes in operational needs are inevitable, underscores the importance of an adaptable and scalable warehouse design. This strategic foresight not only aligns the facility with evolving business requirements but also mitigates the risk of costly retrofits or new construction projects to accommodate future expansion, contributing to both operational efficiency and financial prudence.
While upfront costs are a significant consideration, evaluating long-term operational costs is equally crucial in warehouse construction. Energy efficiency emerges as a key component in this regard. Investing in energy-efficient features, such as advanced insulation and reflective roofing materials, can yield substantial savings over the lifespan of the warehouse. Beyond the immediate financial benefits, energy-efficient practices align with environmental responsibility, meeting the growing demand for sustainable and eco-friendly business practices. Although the initial investment in these technologies may be higher, the long-term operational savings make them a financially sound decision. This approach not only contributes to cost-effectiveness but also positions the warehouse as a sustainable and responsible facility, meeting both economic and environmental objectives.
The selection of materials in warehouse construction involves a delicate balancing act between upfront costs and the long-term benefits derived from high-quality materials. Opting for materials that prioritize durability and structural integrity may result in a slightly higher initial investment. However, this choice pays dividends in the reduction of long-term maintenance costs. Quality materials, including premium steel grades, robust roofing materials, and efficient insulation, contribute significantly to the overall longevity and cost-effectiveness of the facility. Careful consideration of materials becomes an integral part of the decision-making process, ensuring that the warehouse is constructed to withstand the rigors of its operational environment. This strategic approach not only safeguards against premature wear and tear but also minimizes the risk of structural issues, translating into sustained cost savings over the life of the warehouse.
Efficient project management stands as a linchpin in controlling construction costs and ensuring the successful completion of a warehouse project. Delays in construction not only lead to increased labor expenses but can also result in potential disruptions to business operations. Establishing a realistic timeline and adhering to a well-defined project schedule are integral components of effective cost control. Efficient project management involves the seamless coordination of various tasks, adept resource management, and the prompt resolution of potential challenges. Collaboration among stakeholders, including architects, contractors, and suppliers, becomes crucial to ensure that the construction process progresses according to plan. By avoiding delays and adhering to the established timeline, businesses can minimize labor costs, prevent potential financial penalties, and ensure that the warehouse is operational within the projected timeframe. This disciplined approach to project scheduling contributes significantly to cost-effectiveness and overall project success.
Metal warehouses are gaining popularity across diverse applications due to their cost-effectiveness.A metal building with an area of 20,000 square feet typically carries a price range of $288,000 to $456,000. The actual cost is influenced by various factors including the building’s location, prevailing steel prices, design specifications, and the type of inventory it is intended to house.
Employing standardized or pre-engineered designs in warehouse construction can be a strategic decision that significantly streamlines the entire construction process, resulting in substantial cost reductions. These designs are meticulously crafted to be optimized for both efficiency and cost-effectiveness. By adopting standardized designs, construction projects benefit from the elimination of much of the customization process, allowing for quicker planning and implementation phases. This not only accelerates the overall construction timeline but also minimizes the likelihood of errors or inconsistencies. The efficiency gained from standardized designs not only expedites the construction process but also contributes to notable cost savings, making this approach an advantageous choice for those prioritizing efficiency and economy in warehouse construction projects.
One of the key strategies for optimizing costs in large-scale warehouse projects is negotiating bulk purchasing agreements for construction materials. This approach proves to be particularly beneficial when substantial quantities of materials, such as steel and other building essentials, are required. By securing materials in bulk, construction projects can capitalize on economies of scale, obtaining more favorable pricing and, consequently, achieving enhanced cost efficiency. The advantages extend beyond mere cost reduction, as bulk material purchasing also contributes to better budget predictability.
This strategic approach allows for improved financial planning and resource allocation throughout the entire construction process, providing a dual advantage of cost savings and budget control.
Value engineering constitutes a meticulous process within the construction industry, involving a comprehensive evaluation of the design to identify areas for cost reduction without compromising structural integrity. This process requires close collaboration with architects and engineers during the design phase to ensure that every element, from material selection to construction methodologies, is scrutinized for cost-effectiveness. The objective is to strike an optimized balance between quality and affordability, ensuring that the final design meets high standards while remaining within budget constraints. Value engineering is a proactive approach that contributes to a cost-effective yet efficient warehouse construction plan, providing stakeholders with the means to make informed decisions that align with both financial considerations and construction requirements.
The integration of technology, particularly through methodologies like Building Information Modeling (BIM), stands as a transformative force in warehouse construction. This technology allows for a detailed virtual representation of the warehouse, facilitating construction teams in identifying and addressing potential issues before they manifest on the construction site. The integration of technology enhances communication, collaboration, and precision throughout the project, leading to streamlined processes, reduced construction time, and optimized costs. By leveraging technology, construction projects can significantly minimize errors, reduce the need for rework, and ultimately realize substantial cost savings. Technology integration becomes a cornerstone for efficient, precise, and cost-effective warehouse construction.
Opting for the local sourcing of construction materials is not only a sustainable practice but also a cost-effective strategy. Local suppliers often provide materials at competitive prices, and the proximity of these materials significantly reduces transportation costs. This dual advantage not only supports the local economy but also contributes to environmental sustainability by minimizing the carbon footprint associated with long-distance transportation. Choosing local sourcing fosters positive relationships within the community, creating a symbiotic dynamic where construction teams benefit from cost efficiency, timely material supply, and community support. Embracing local sourcing aligns with both economic prudence and environmental responsibility, making it a strategic and ethical choice in warehouse construction.
Incorporating energy-efficient systems into warehouse construction, such as LED lighting, solar panels, and advanced HVAC (Heating, Ventilation, and Air Conditioning) systems, represents a forward-thinking approach that leads to ongoing operational cost savings. While there may be an initial investment involved in implementing these technologies, the long-term benefits significantly outweigh the upfront expenses. For instance, LED lighting consumes less energy and has a longer lifespan, reducing both energy consumption and maintenance costs. Solar panels provide a renewable energy source, potentially leading to energy independence and reduced utility expenses. Advanced HVAC systems optimize energy usage, contributing to a more sustainable and cost-effective operation over time. By embracing energy-efficient systems, warehouse owners not only align financial prudence with environmental responsibility but also position their facilities for long-term operational efficiency and cost savings.
Fully Insured Licensed
Hire Contractor For Warehouse Construction
Make Informed Design Decisions Showcase Your Design Ideas
Get RenderingMetal warehouse construction represents a significant investment for businesses seeking durable, versatile, and cost-effective storage solutions. The cost of building a metal warehouse is influenced by various factors, including size, design complexity, location, site preparation, materials used, and regulatory compliance. To make informed decisions and optimize costs, businesses must carefully consider budgetary constraints, plan for future expansion, prioritize energy efficiency, and select high-quality materials. Efficient project management, adherence to timelines, and strategic cost-saving measures, such as standardized designs, bulk material purchasing, value engineering, technology integration, local material sourcing, and energy-efficient systems, play crucial roles in achieving a cost-effective metal warehouse construction. With proper planning and consideration of these factors, businesses can not only control costs but also ensure the long-term functionality, scalability, and sustainability of their metal warehouses.
The cost of constructing a metal warehouse is influenced by various factors, including the size and square footage, design complexity, geographical location, site preparation requirements, materials used, inclusion of specific features and accessories, regulatory compliance, and skilled labor costs.
Larger buildings with expansive square footage generally result in higher construction costs due to increased material requirements and additional labor needed for the project. The dimensions, height, and layout of the warehouse play a crucial role in determining both initial costs and future operational efficiency.
Geographical location affects construction costs by influencing local building codes, climate considerations, and accessibility factors. Different regions have distinct regulatory requirements and environmental conditions that impact construction expenses. Additionally, the accessibility of the construction site influences transportation costs for materials and labor.
Businesses can optimize costs through careful budgetary planning, considering future expansion needs, prioritizing energy efficiency, selecting high-quality materials, and implementing efficient project management strategies. Cost-saving measures, such as employing standardized designs, negotiating bulk material purchases, value engineering, technology integration, local material sourcing, and adopting energy-efficient systems, also contribute to overall cost-effectiveness.
A metal warehouse with an area of 20,000 square feet typically carries a price range of $288,000 to $456,000. However, the actual cost is influenced by factors such as the building’s location, prevailing steel prices, design specifications, and the type of inventory it is intended to house.
Technology integration, such as Building Information Modeling (BIM), facilitates a detailed virtual representation of the warehouse, allowing construction teams to identify and address potential issues before construction begins. This minimizes errors, reduces the need for rework, and ultimately leads to substantial cost savings by enhancing communication, collaboration, and precision throughout the construction project.
Here I am going to share some steps to get a metal warehouse construction cost estimate report.
You can send us your plan on info@estimatorflorida.com
Before starting your project, we send you a quote for your service. That quote will have detailed information about your project. Here you will get information about the size, difficulty, complexity and bid date when determining pricing.
Our team will takeoff and estimate your project. When we deliver you’ll receive a PDF and an Excel file of your estimate. We can also offer construction lead generation services for the jobs you’d like to pursue further.
561-530-2845
info@estimatorflorida.com
Address
5245 Wiles Rd Apt 3-102 St. Pete Beach, FL 33073 United States
561-530-2845
info@estimatorflorida.com
Address
5245 Wiles Rd Apt 3-102 St. Pete Beach, FL 33073 United States
All copyright © Reserved | Designed By V Marketing Media | Disclaimer