Metal Framing Cost Per Square Foot
Metal stud framing prices typically range from $17 to $32 per square foot when professionally installed. The cost can vary based on several factors, including the complexity of the project, geographical location, and specific materials used. Metal stud framing is a popular choice for commercial buildings and interior wall construction due to its durability and fire resistance. While the initial investment might seem relatively high, the long-term benefits of reduced maintenance and enhanced safety make it a cost-effective option for many construction projects. It’s essential to obtain accurate quotes from contractors and suppliers to determine the exact pricing for your specific needs.
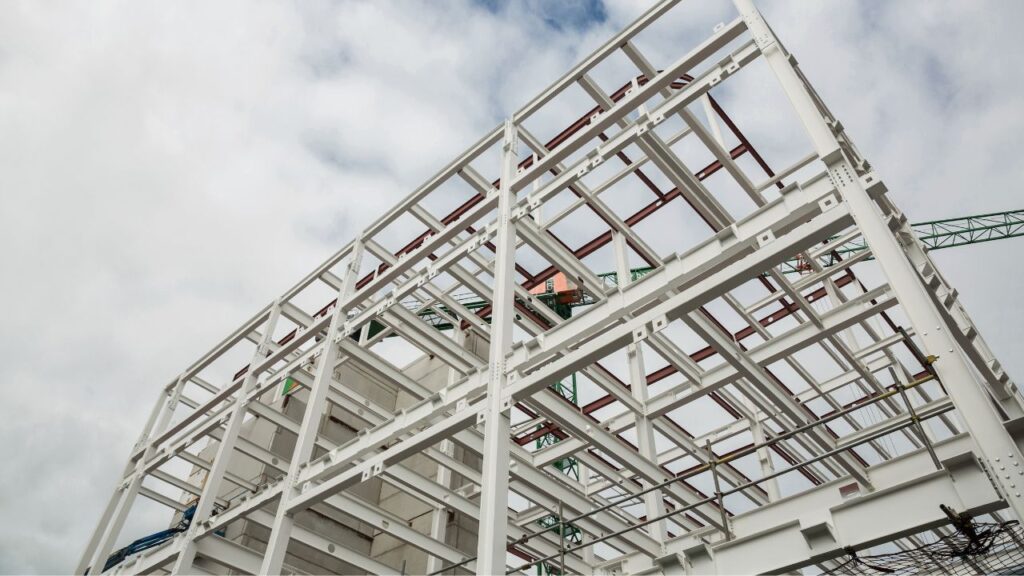
When it comes to constructing interior walls in commercial and residential buildings, metal stud framing has become a popular choice due to its durability and versatility. Understanding the cost of metal framing per square foot is essential for anyone planning a construction project. In this article, we will break down the factors that affect metal framing costs and provide you with insights on how to manage your budget effectively.
Metal stud framing is the use of steel studs to create the framework for walls, partitions, and ceilings. These studs have gained popularity for several reasons, including their resistance to common issues like warping, rot, and pests. This method offers longevity and stability, making it a preferred choice for many construction projects.
Are You Looking For?
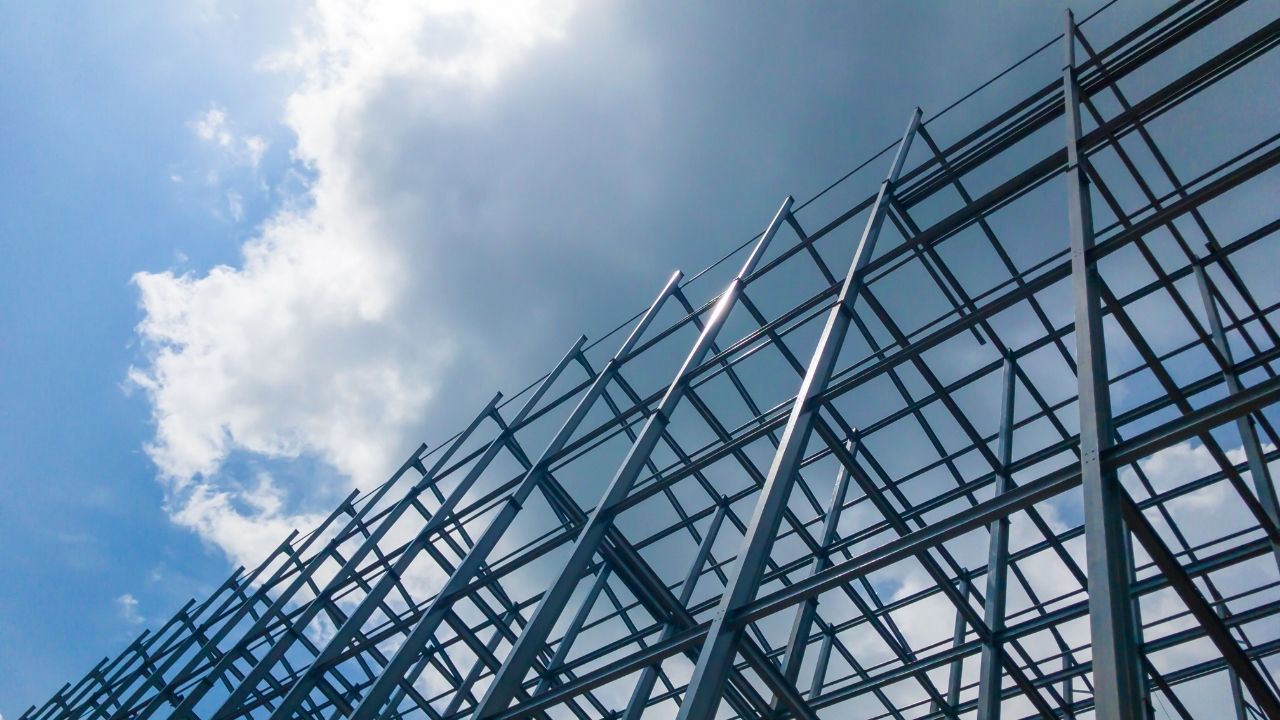
Fully Insured Licensed Hire a Contractor For Metal Framing
Hire Contractor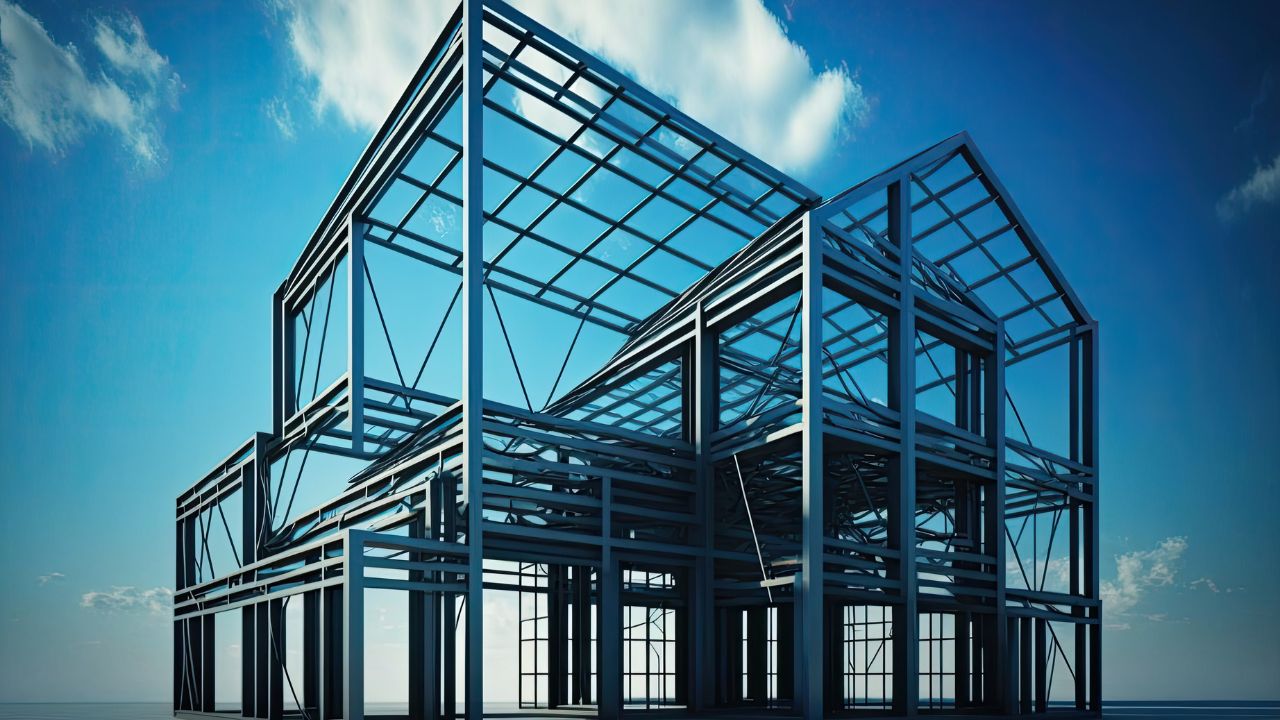
Make Informed Design Decisions Showcase Your Design Ideas
Get RenderingCall Us To Discuss More at 561-530-2845
Understanding Metal Stud Framing
Metal stud framing involves using steel studs to create the framework for walls, partitions, and ceilings. These steel studs are known for their strength and resistance to common issues like warping, rot, and pests. This construction method offers longevity and stability, making it a preferred choice for many.
One of the primary advantages of metal stud framing is its durability. Steel studs are not susceptible to issues like warping or rot, which can be common problems with wood framing. Additionally, metal framing is resistant to pests, making it an excellent choice for areas prone to termite infestations. This durability ensures that your walls and ceilings maintain their structural integrity over time, reducing the need for repairs and maintenance.
Factors Affecting Metal Framing Costs
Several factors influence the cost of metal stud framing:
Material Costs
Steel Studs
Steel studs are the primary component of metal framing. The cost of steel studs can vary depending on the gauge, length, and manufacturer. Thicker gauges and longer lengths are typically more expensive. For example, using 25-gauge steel studs can be more cost-effective for interior non-load-bearing walls, while 20-gauge or 18-gauge studs are preferred for load-bearing walls. Some manufacturers offer pre-cut studs, which can save time and reduce labor costs.
Fasteners
The foundation is a critical component of your building’s stability. In the case of a steel frame building, the foundation cost typically ranges from $5 to $9 per square foot of poured concrete. The choice of foundation type, such as slab, pier and beam, or crawl space, can significantly influence this cost. The foundation is the literal bedrock upon which your project rests, so its importance cannot be overstated.
Insulation
Insulation is essential for temperature control and soundproofing. The type and quality of insulation you choose will impact your overall costs. Fiberglass insulation is a cost-effective option, while mineral wool provides excellent soundproofing but may be slightly more expensive.
Drywall
The installation of drywall sheets over the metal studs is a significant cost factor. The thickness and quality of the drywall material also affect the overall expenses. Standard 1/2-inch drywall is suitable for most interior applications, but you can opt for thicker drywall for enhanced soundproofing.
Labor Costs
Labor costs for metal stud framing include the wages of skilled workers who will assemble the metal framework, attach insulation, and install drywall. The level of expertise required for the project can influence labor costs.
The expertise of the laborers is crucial when it comes to metal framing. Skilled workers will ensure that the metal studs are precisely aligned, reducing the chances of errors and the need for costly corrections. They will also be proficient in attaching insulation effectively, which is critical for maintaining temperature control and soundproofing.
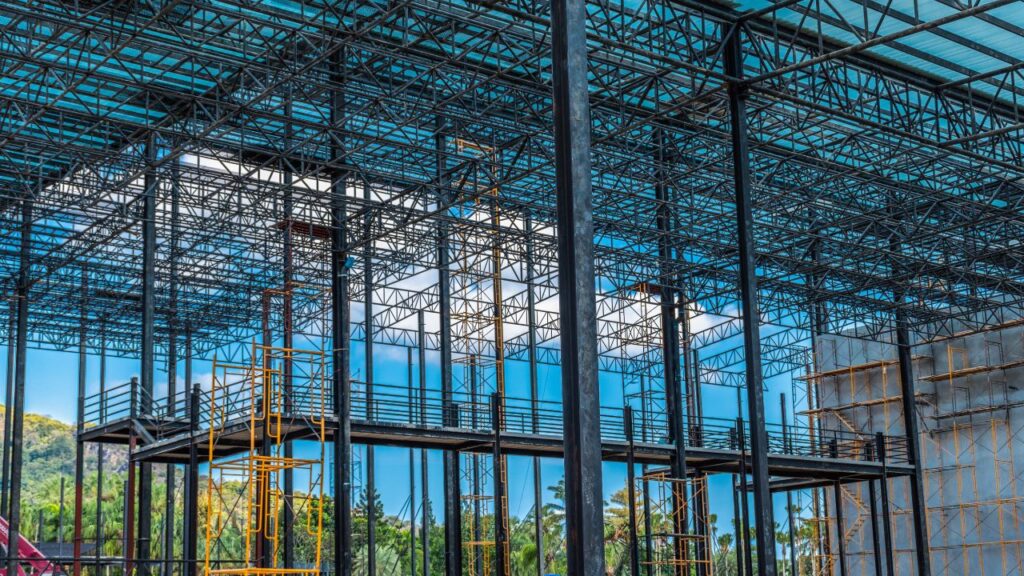
Their experience in drywall installation will result in a smooth and professional finish.
Tools and Equipment
Specialized tools and equipment are necessary for metal stud framing. This includes cutting tools, drills, and safety gear. Investing in quality tools can affect your initial expenses but can lead to efficiency during construction.
To ensure the quality and precision of the framing, it’s essential to invest in high-quality tools. Cutting tools, such as compound snips and aviation shears, should be sharp and well-maintained to ensure clean cuts in the steel studs. A drill with the appropriate bits for steel is essential for securing the studs and attaching drywall. Safety gear, including safety glasses, gloves, and hearing protection, should be provided to the workers to maintain a safe working environment.
Project Size and Complexity
Larger projects with intricate designs and multiple rooms will naturally have higher metal framing costs. The complexity of the project can also affect labor hours and material requirements.
The size and complexity of the project have a direct impact on the overall cost. Larger projects, such as commercial spaces or multi-unit residential buildings, will require more materials and labor, leading to higher expenses. Additionally, projects with intricate designs, curved walls, or multiple rooms may require more time and effort, further increasing the cost. It’s essential to plan and budget accordingly for such projects.
Hire a Commercial Metal Contractor
We provide commercial metal estimating services for small and big construction projects. We analyze the costs of commercial metal projects. A growing trend in commercial metal building construction is the use of prefabricated steel buildings.
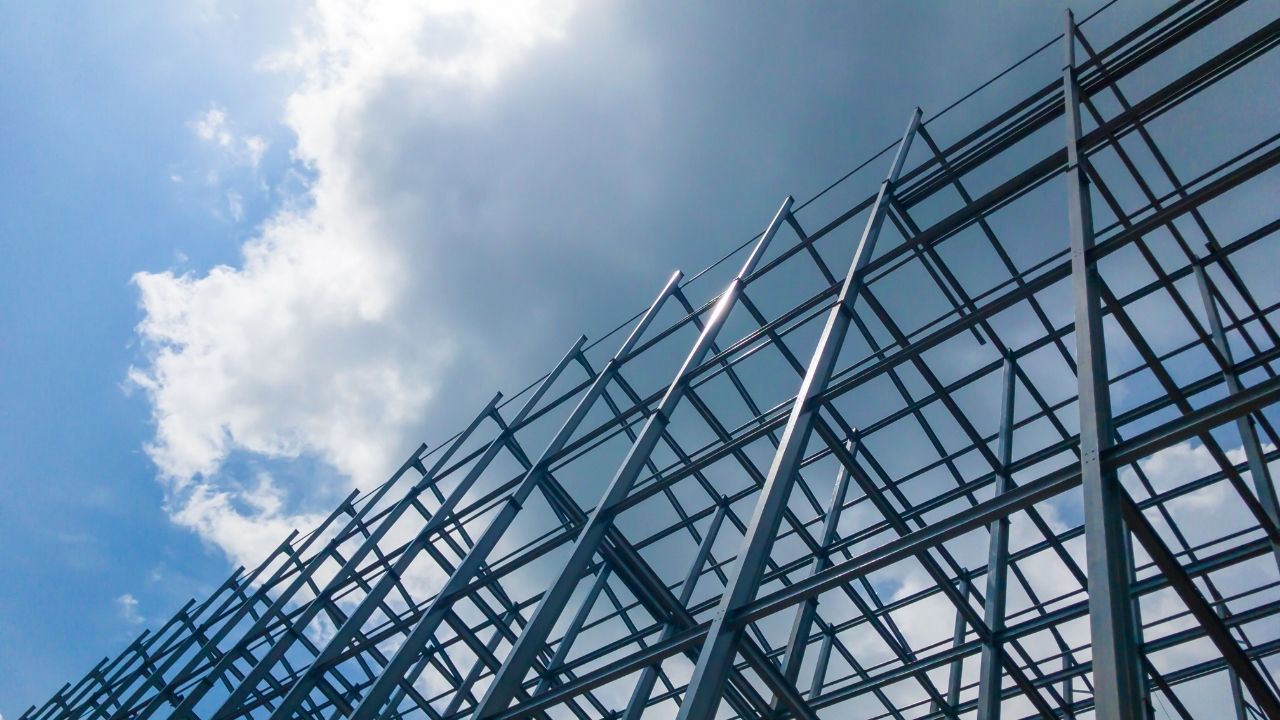
Geographic Location
The cost of living and construction materials can vary significantly by geographic location. Therefore, where your project is located will play a role in determining your overall costs.
The geographic location of your construction project is a critical factor in determining costs. In areas with a high cost of living, such as major cities, labor costs tend to be higher. Additionally, the availability and cost of construction materials can vary by region. It’s important to obtain local quotes and estimates to accurately budget for your project based on the specific conditions of your location.
Cost Range for Metal Framing
On average, metal stud framing costs range from $19 to $38 per square foot installed. However, this range is flexible, depending on the factors mentioned earlier. Keep in mind that this cost range covers the complete metal framing system, including studs, fasteners, insulation, and drywall installation.
The cost of metal framing can vary widely based on the factors we’ve discussed. For instance, a project that requires thicker gauge steel studs and high-quality insulation will fall toward the higher end of the cost range. Conversely, a smaller project with standard materials may be more cost-effective. It’s crucial to obtain detailed quotes from contractors that specify the materials and labor included to get an accurate estimate for your project.
Cost Savings and Benefits
Metal stud framing offers long-term benefits, such as durability and reduced maintenance costs. While the initial expenses may be higher than wood framing, the long-term savings can outweigh the upfront investment.
Investing in metal stud framing can result in long-term cost savings. The durability of steel studs means that you won’t need to worry about issues like rot or termite damage, which can be costly to repair with wood framing. Additionally, metal framing provides excellent fire resistance, making it a preferred choice for buildings with stringent safety requirements.
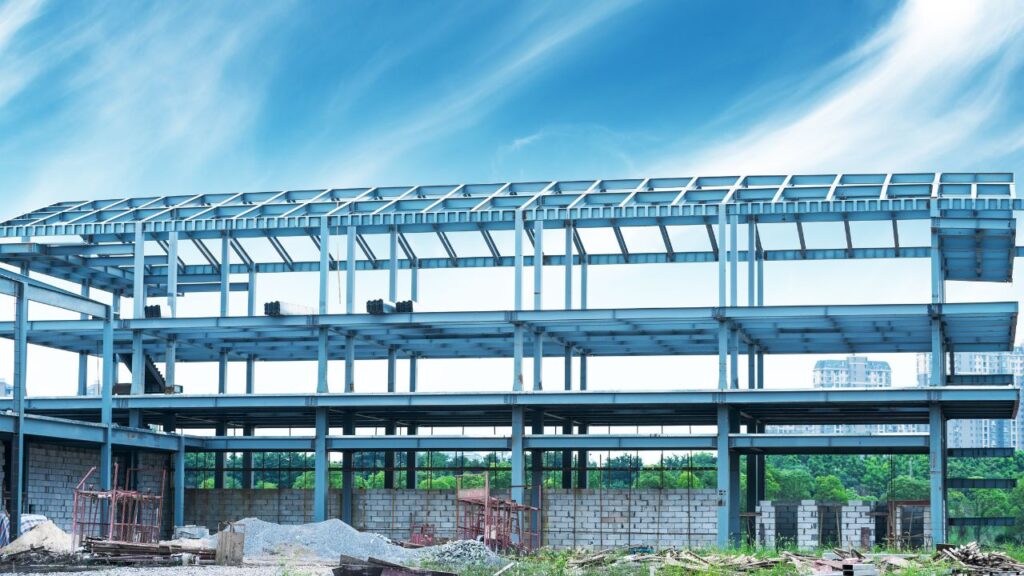
The reduced maintenance and repair costs over the years can make metal framing a cost-effective choice in the long run.
Hiring Professionals vs. DIY
Deciding whether to hire professionals or undertake a DIY metal framing project is a critical choice. While DIY can save on labor costs, it requires knowledge, skill, and access to the necessary tools.
Choosing between hiring professionals and taking a do-it-yourself (DIY) approach depends on the scope and complexity of your project. For smaller projects or simple wall partitions, DIY may be a cost-effective option, as it can save on labor costs. However, it’s essential to have the necessary knowledge and skills for metal framing, including understanding how to properly secure the studs, install insulation, and attach drywall. Additionally, having access to the right tools, such as a steel-cutting tool, drill, and safety gear, is crucial for a successful DIY project.
For larger or more complex projects, it’s highly recommended to hire experienced professionals who have the expertise and tools needed to ensure a structurally sound and efficient outcome. Professional installers can work more quickly and efficiently, reducing the project’s overall timeline and ensuring that all safety and quality standards are met.
Are You Looking For?
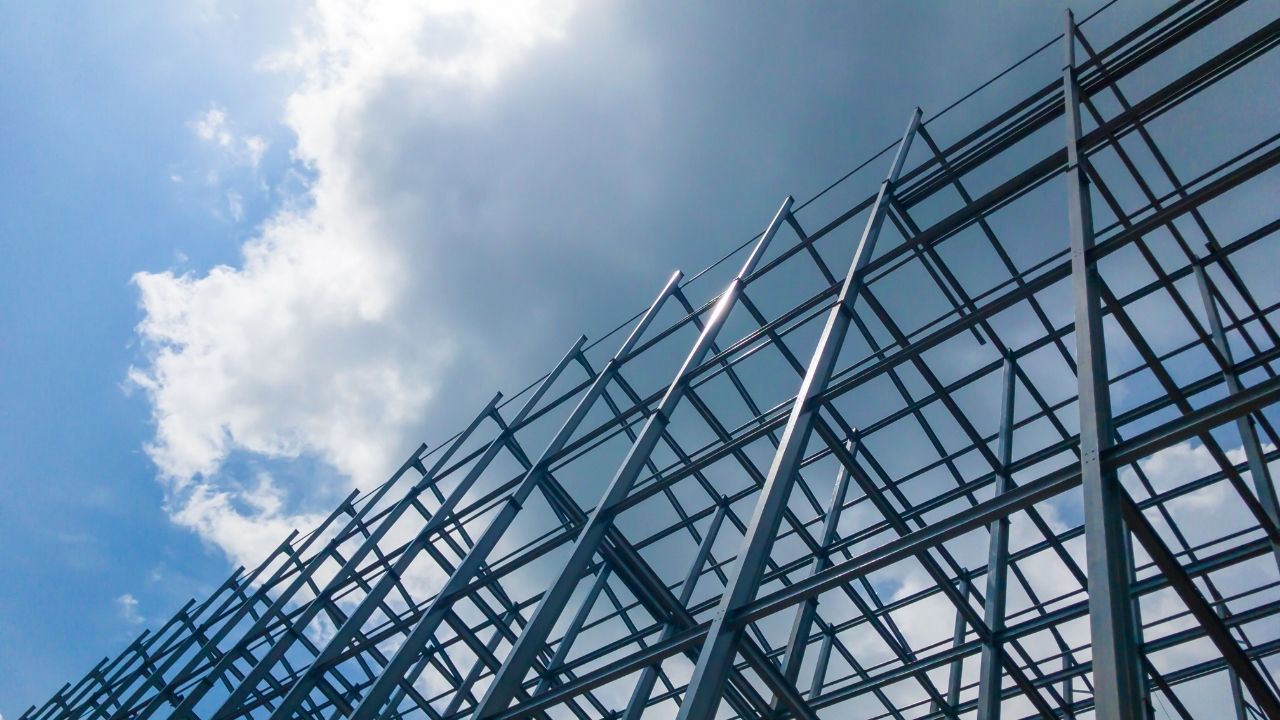
Fully Insured Licensed Hire a Contractor For Metal Framing
Hire Contractor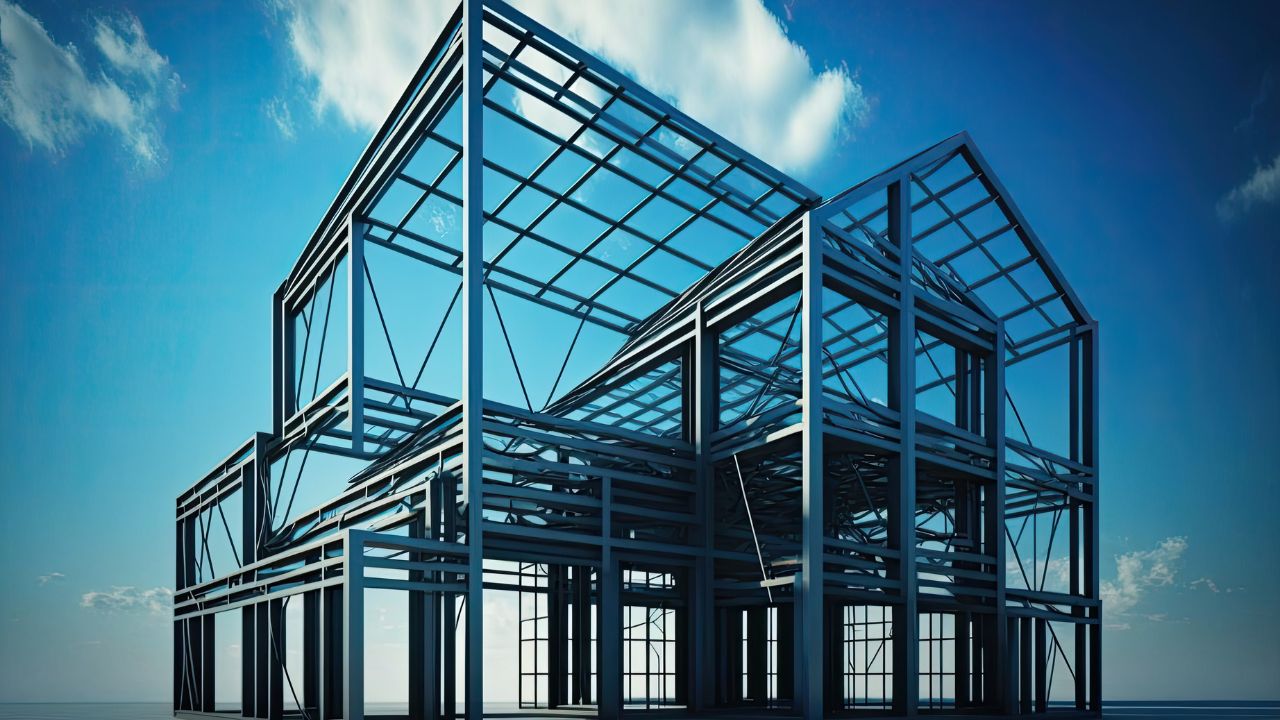
Make Informed Design Decisions Showcase Your Design Ideas
Get RenderingCall Us To Discuss More at 561-530-2845
Tips for Reducing Metal Framing Costs
If you’re looking to reduce metal framing costs, consider options like bulk purchasing of materials, using cost-effective insulation, and negotiating with contractors for competitive pricing. Additionally, plan your project efficiently to minimize wasted materials and labor time.
Here are some practical tips to help reduce metal framing costs:
- Bulk Purchasing: Consider purchasing materials in bulk, as this can often result in discounts from suppliers. It’s essential to plan your project carefully to estimate the required quantities accurately.
- Cost-Effective Insulation: Choose insulation materials that offer a good balance between cost and performance. Fiberglass insulation is a popular and cost-effective option, providing both thermal and soundproofing benefits.
- Competitive Pricing: When hiring professionals, don’t hesitate to obtain multiple quotes from different contractors. This allows you to compare pricing and negotiate for competitive rates.
- Efficient Project Planning: Plan your project efficiently to minimize waste. Ensure that you accurately measure and cut materials to avoid unnecessary scrap. Wasted materials and additional labor time can drive up costs.
Comparing Metal Framing with Wood Framing
It’s essential to compare the cost of metal framing with traditional wood framing to make an informed decision for your project. Both methods have their pros and cons, and cost is a significant factor.
When choosing between metal framing and wood framing, it’s crucial to consider the specific needs and goals of your project. Here’s a brief comparison of the two methods:
- Metal Framing:
- Pros:
- Durability
- Fire resistance
- Reduced maintenance
- Resistance to pests
- Cons:
- Higher initial cost
- Pros:
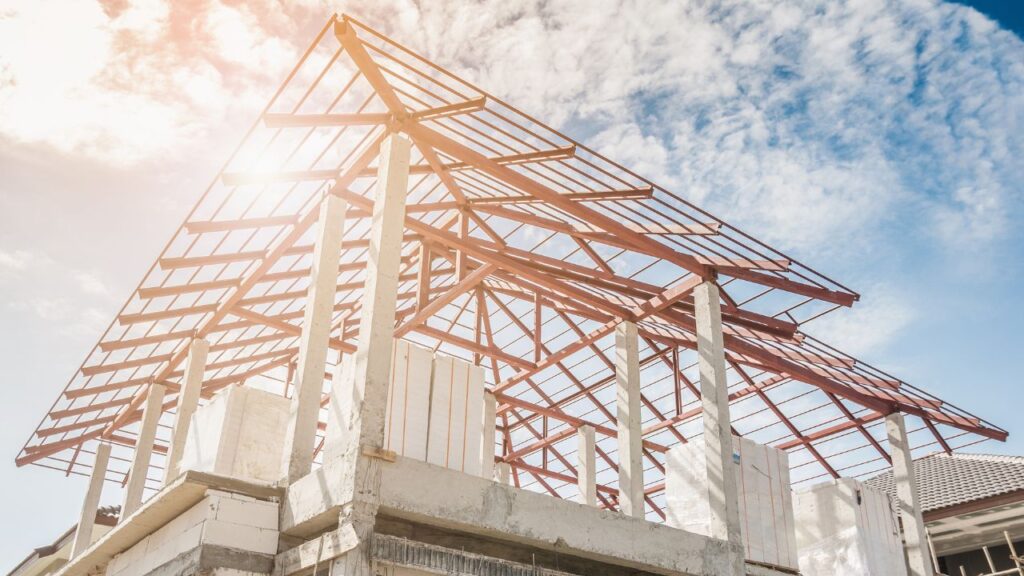
- Wood Framing:
- Pros:
- Lower initial cost
- Widespread availability
- Ease of installation
- Cons:
- Susceptible to rot and pests
- Limited fire resistance
- Pros:
For projects where durability, fire resistance, and long-term cost savings are a priority, metal framing is often the preferred choice. However, for smaller residential projects or areas with a limited budget, wood framing can be a cost-effective option.
Conclusion
The cost of metal framing per square foot can vary widely, depending on factors like materials, labor, tools, project size, and location. Understanding these variables is crucial for planning your construction project effectively. Whether you’re working on a commercial space or a residential property, metal framing offers long-term benefits that make it a worthwhile investment. Consider all the factors discussed in this article to make an informed decision that aligns with your project’s goals and budget.
FAQs
The initial cost of metal framing is usually higher, but it offers long-term cost savings due to its durability, fire resistance, and reduced maintenance needs.
Efficient project management, using local labor resources, and optimizing labor product
While it’s possible, professional installation is recommended for complex projects. Ensure you have the necessary tools and knowledge to complete the job effectively.
ivity can help reduce labor costs. Hiring experienced contractors and addressing labor shortages promptly can also be beneficial.
The choice of insulation depends on your project’s specific needs, but common options include fiberglass and mineral wool. Consult with a construction professional for guidance.
Steel studs are coated to resist rust, making them a durable choice. Proper maintenance and moisture control are essential to prevent corrosion.
You can search online, ask for recommendations from others in your area, or consult with a construction professional for referrals. Make sure to obtain multiple quotes and check references to find a reliable contractor.
Process To Get Metal Framing Cost Estimate Report
Here I am going to share some steps to get your metal framing cost estimate report.
-
You need to send your plan to us.
You can send us your plan on info@estimatorflorida.com
-
You receive a quote for your project.
Before starting your project, we send you a quote for your service. That quote will have detailed information about your project. Here you will get information about the size, difficulty, complexity and bid date when determining pricing.
-
Get Estimate Report
Our team will takeoff and estimate your project. When we deliver you’ll receive a PDF and an Excel file of your estimate. We can also offer construction lead generation services for the jobs you’d like to pursue further.
Google Reviews
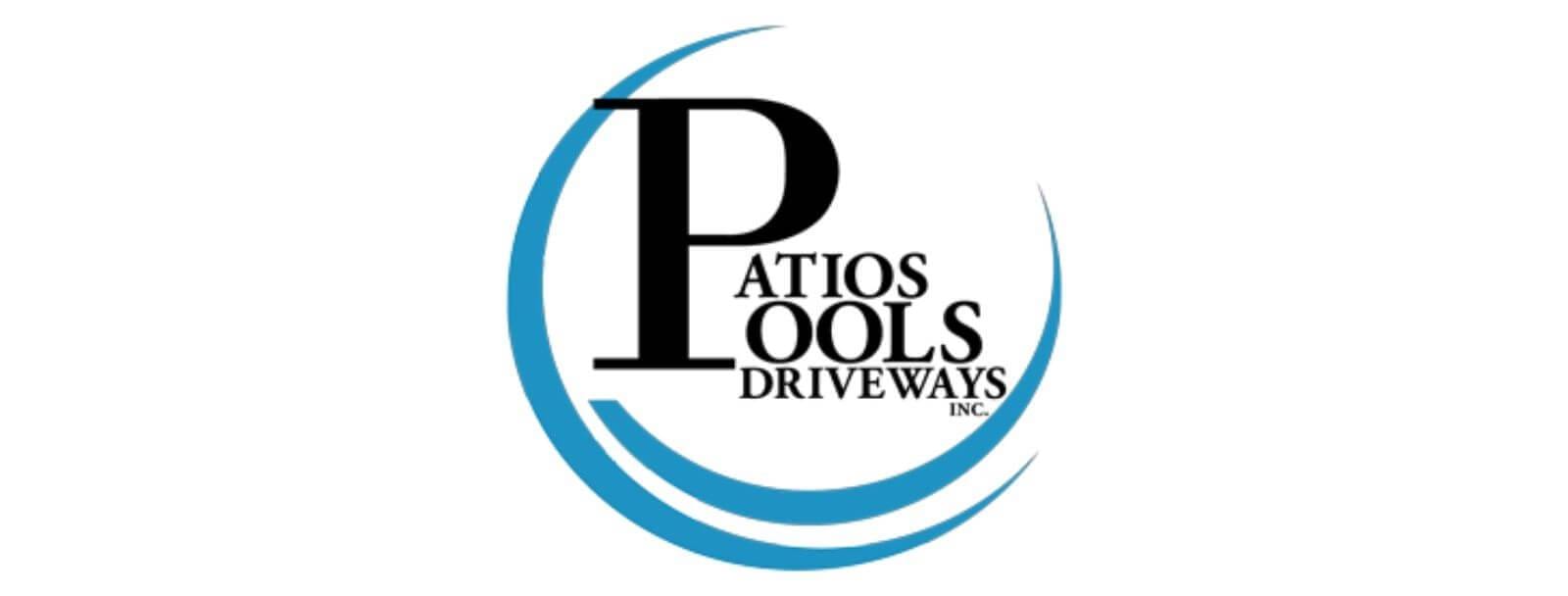
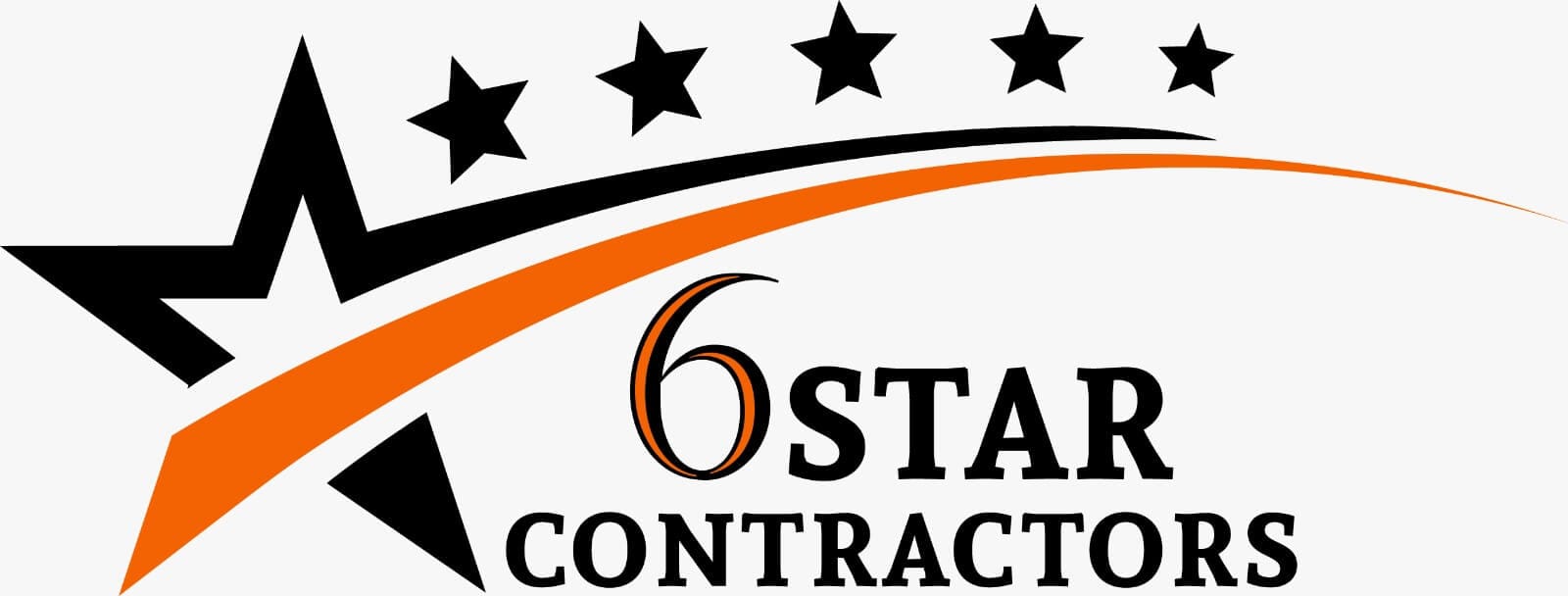
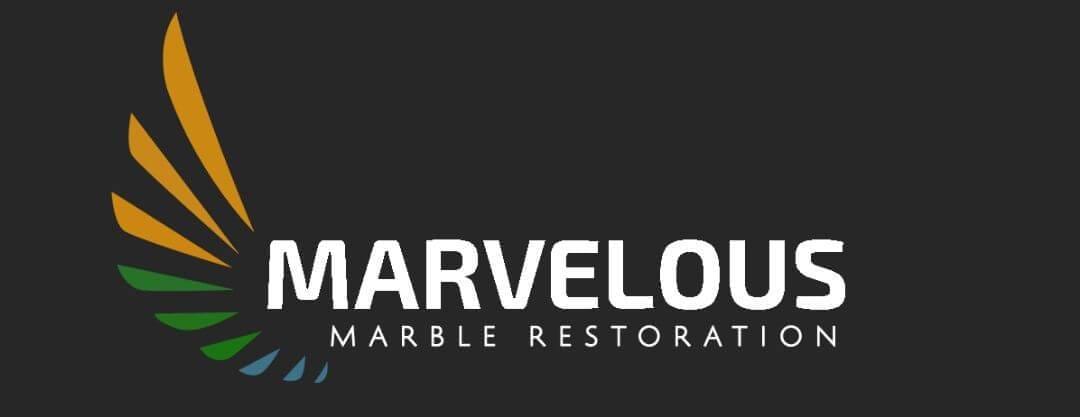