Metal is a vital material in construction, manufacturing, and various industrial applications due to its durability, versatility, and strength. Its applications range from structural frameworks to decorative elements, making it an indispensable choice in a variety of projects. Accurately estimating metal costs is crucial for project budgeting and resource allocation to avoid unexpected expenses and delays. In Sarasota, FL, metal costs can vary significantly based on factors such as type, quantity, processing requirements, and market conditions. This comprehensive guide provides an in-depth analysis of metal cost estimation to help you plan your projects effectively and efficiently.
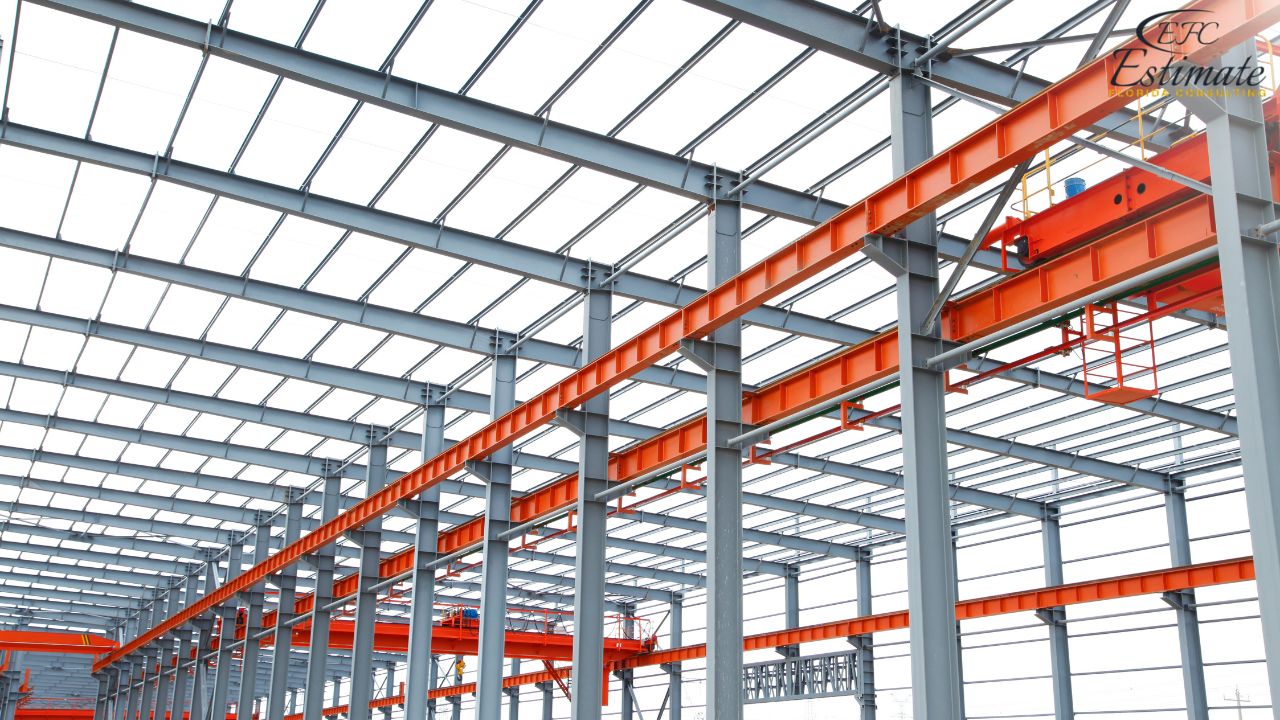
Average Metal Costs in Sarasota
Metal Type | Estimated Cost Range (per pound) |
Steel | $0.50 – $1.50 |
Aluminum | $1.00 – $3.00 |
Copper | $4.00 – $8.00 |
Stainless Steel | $2.00 – $4.50 |
Brass | $1.50 – $3.50 |
The final costs depend on the type of metal chosen, the quantity required, and any additional processing or fabrication needs. For instance, raw steel is more affordable but may require coatings or welding, which can increase the overall cost. Knowing the specific application and volume can help streamline cost estimations.
Key Factors Affecting Metal Costs
1. Type of Metal
The type of metal plays a significant role in determining costs, as each metal has distinct properties that make it suitable for specific applications. For example, steel is widely used for its affordability and tensile strength, making it ideal for structural applications like beams and columns. On the other hand, copper’s high conductivity and corrosion resistance make it essential but more expensive for electrical wiring and plumbing systems. Aluminum’s lightweight and non-corrosive nature make it a preferred choice for roofing and HVAC systems, though it costs more than steel.
Get Acquainted with Estimation
Construction Projects Going Over Budget? Here's How to RECOVER!
Secrets of Successful Bids: Advanced Tips for Construction Managers
2. Quantity Needed
The amount of metal required directly impacts the total cost. Bulk purchases often reduce the per-pound cost due to economies of scale, making them more cost-effective for large projects. However, smaller projects requiring specialized materials may incur higher costs due to limited quantities and additional handling fees. Proper planning and accurate measurements ensure you procure the right amount without over-ordering or underestimating.
3. Processing and Fabrication
Metals often require additional processing to meet project specifications, such as cutting, welding, shaping, or coating. Custom fabrication for intricate designs or high-precision requirements increases labor and material costs. For example, a prefabricated metal framework may save time but could be more expensive upfront due to manufacturing complexity. Understanding these costs helps align project expectations with budget constraints.
4. Market Conditions
Global market trends, including supply chain disruptions, geopolitical events, and demand fluctuations, significantly influence metal prices. For instance, a surge in demand for construction materials can drive up prices, while economic slowdowns may result in cost reductions. Monitoring market conditions allows you to plan purchases during periods of stable or declining prices, minimizing overall expenses.
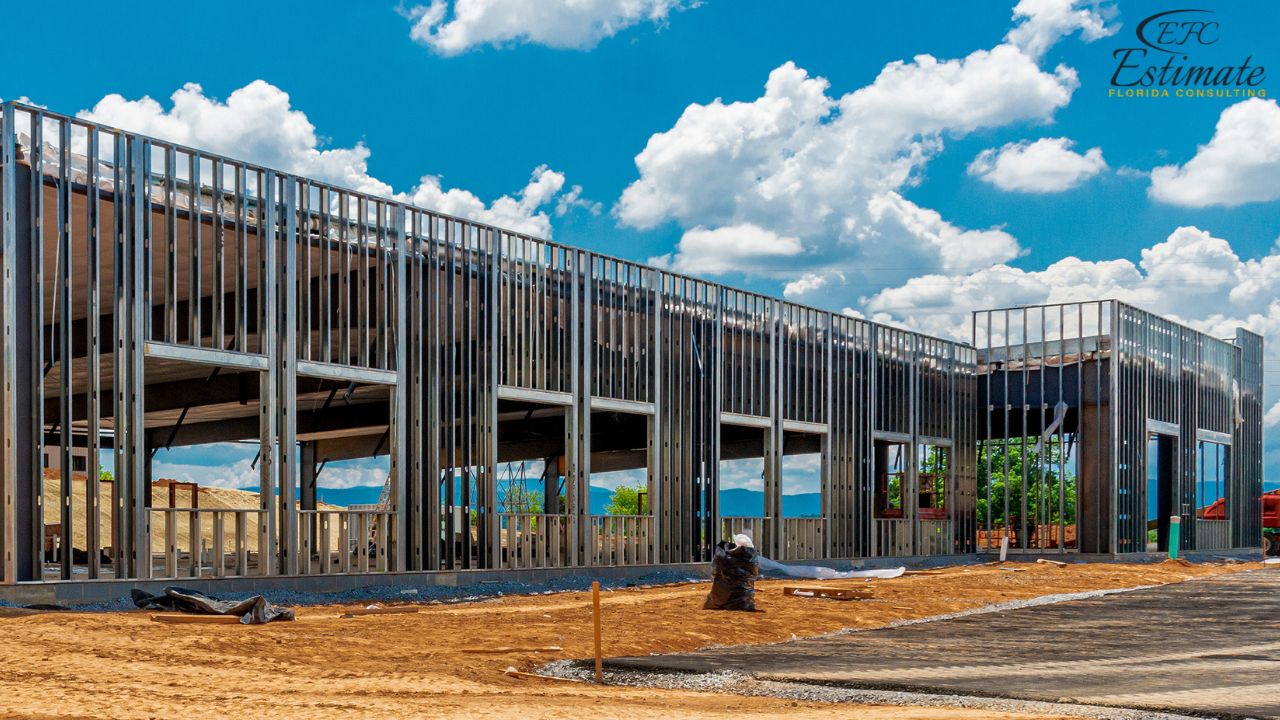
5. Delivery and Logistics
Transportation costs for heavy materials like metal can significantly impact overall project expenses. Local sourcing can help reduce delivery fees and lead times, while imported materials may incur additional tariffs or customs charges. Coordinating with local suppliers ensures timely delivery and cost efficiency, especially for large-scale projects.
Metal Cost Estimation by Project Type
Residential Projects
Residential metal projects typically range from $2,000 to $15,000, depending on the application and materials used. Common uses include:
- Roofing: Metal roofs, known for their durability and energy efficiency, cost between $7 and $15 per square foot. They provide excellent longevity and require minimal maintenance, making them a valuable investment.
- Fencing and Gates: Aluminum or steel fences cost $15 to $30 per linear foot, offering both security and aesthetic appeal. Custom designs and additional features, such as automation, can increase costs.
- Decorative Elements: Metal railings or ornamental features cost $50 to $200 per piece, depending on the complexity of the design. These elements enhance the visual appeal of residential spaces and add unique character to homes.
Commercial Projects
Commercial metal applications range from $20,000 to $200,000 due to the larger scale and complexity involved. Examples include:
- Structural Frameworks: Steel frameworks for buildings cost $0.50 to $1.50 per pound, with additional expenses for assembly and welding. These frameworks provide the backbone for multi-story buildings and large warehouses.
- HVAC Systems: Ductwork and metal components cost $10 to $25 per linear foot, depending on the material and size. Proper installation ensures energy efficiency and long-term durability.
- Facade Panels: Aluminum or stainless steel panels cost $15 to $50 per square foot for modern architectural designs. These panels offer both functional and aesthetic benefits, such as weather resistance and sleek appearances.
Your trusted Metal experts, Get started Now!
Industrial Projects
Industrial metal projects often exceed $50,000 due to specialized requirements and heavy-duty applications. Examples include:
- Piping Systems: Stainless steel or copper pipes for chemical or food-grade applications cost $3 to $10 per linear foot. These materials meet stringent health and safety standards while providing exceptional durability.
- Heavy Machinery Components: Custom-fabricated metal parts range from $100 to $5,000 per piece, depending on size, precision, and material requirements. These components ensure machinery operates efficiently and safely.
- Storage Tanks: Steel or aluminum tanks for liquids or gases cost $10,000 to $100,000 based on capacity and specifications. Proper tank fabrication and installation are crucial for industrial safety and compliance.
Cost Breakdown of Metal Components
Component | Cost Range |
Raw Material | $0.50 – $8.00 per pound |
Fabrication and Welding | $50 – $150 per hour |
Coating and Finishing | $2 – $10 per square foot |
Delivery and Logistics | $100 – $1,000+ |
Tips for Reducing Metal Costs
1. Choose Cost-Effective Materials
Select metals like steel or aluminum for general applications to balance cost and performance. While copper and stainless steel offer superior properties, they should only be used where necessary to control expenses.
2. Plan Efficiently
Accurate measurements and detailed project plans reduce material waste and minimize over-ordering. Collaborating with experienced contractors or estimators ensures precise calculations and avoids unnecessary costs.
3. Buy in Bulk
Purchasing larger quantities of metal can lower per-unit costs through bulk discounts. Coordinate with suppliers to align purchases with project schedules to avoid excess storage fees or delays in material availability.
4. Consider Recycled Metals
Recycled metals are environmentally friendly and often cost less than virgin materials. These metals meet quality standards for various applications, making them a sustainable and cost-effective choice.
5. Source Locally
Working with local suppliers reduces transportation costs and lead times. Local sourcing also supports regional economies and simplifies logistics, ensuring timely project execution.
Advanced Metal Solutions
1. Prefabricated Components
Using prefabricated metal components speeds up installation and reduces labor costs. Prefabrication is particularly beneficial for structural frameworks, HVAC systems, and modular constructions, ensuring precision and consistency.
2. Eco-Friendly Coatings
Opt for environmentally friendly coatings that protect metals from corrosion while reducing environmental impact. These coatings, costing $2 to $5 per square foot, extend the lifespan of metal structures and reduce maintenance costs.
3. Custom Metal Fabrication
Custom fabrication allows for tailored designs that meet specific project requirements. While it increases upfront costs, it ensures precision, durability, and long-term performance, particularly for industrial applications.
Download Template For Metal Project Breakdown
- Materials list updated to the zip code
- Fast delivery
- Data base of general contractors and sub-contractors
- Local estimators
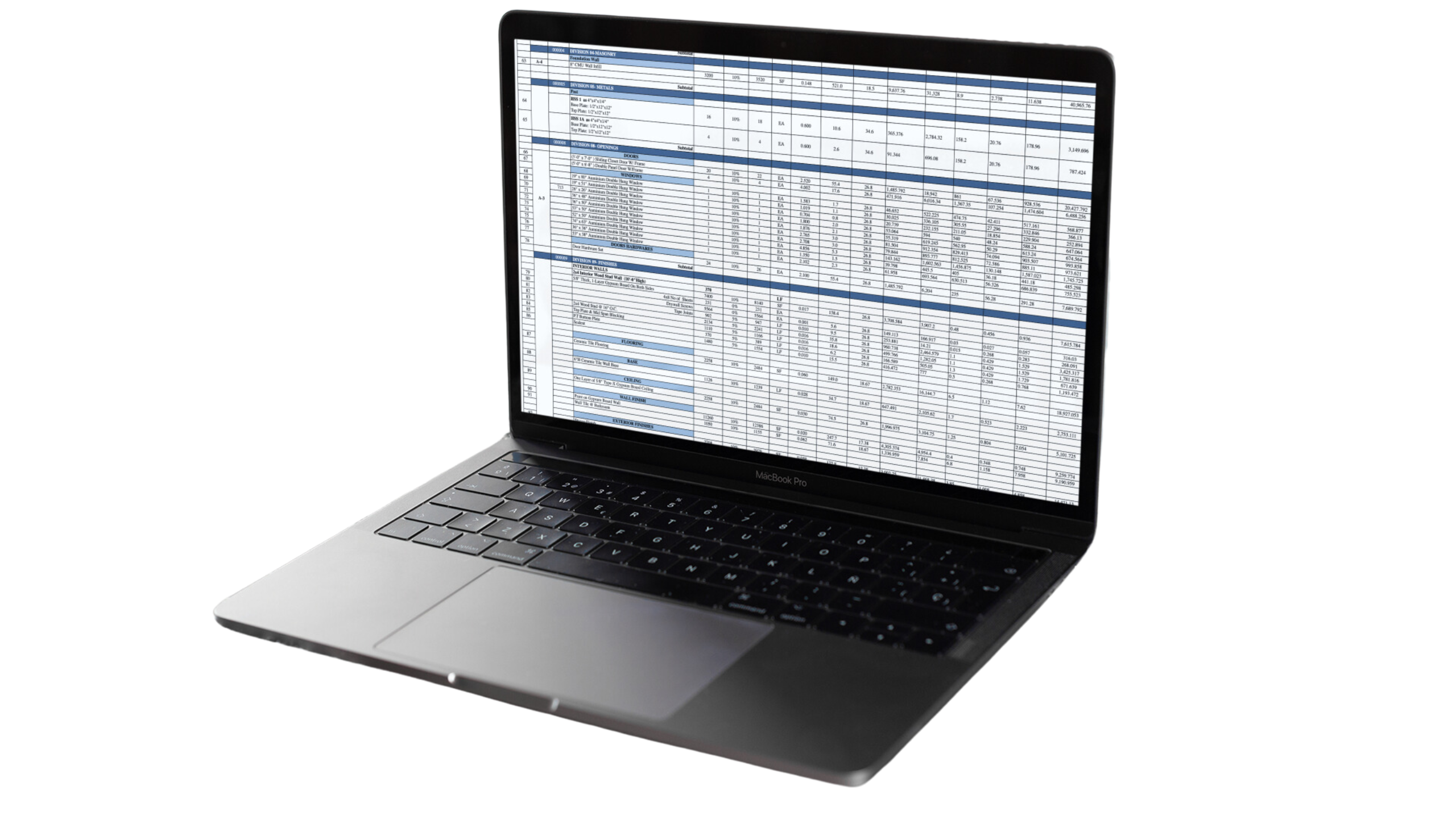
Conclusion
Estimating metal costs accurately is critical for the success of any construction or industrial project in Sarasota, FL. By understanding the factors that influence metal prices and implementing cost-saving strategies, you can optimize your budget while ensuring high-quality results. At Estimate Florida Consulting, we specialize in providing detailed metal cost estimates tailored to your project’s needs. Contact us today for expert advice and customized solutions.
Frequently Asked Question
Multiply the weight of the required metal by the cost per pound. Add expenses for processing, fabrication, delivery, and any additional features like coatings to get an accurate estimate.
Metal prices depend on type, quantity, processing needs, market trends, and logistics. Global market conditions and local availability also significantly affect prices.
Yes, recycled metals can meet structural requirements as long as they are processed and certified for quality. Discuss these options with your supplier to ensure they align with project needs.
Opt for cost-effective materials, plan efficiently, buy in bulk, and source locally. Consider using prefabricated or recycled components to further reduce costs while maintaining quality.
Metal offers unparalleled durability, versatility, and strength, making it ideal for structural, decorative, and functional applications. It is also recyclable, resistant to pests, fire, and weather, ensuring long-term value.
Comprehensive Trade-Specific Estimates
At Estimate Florida Consulting, we offer detailed cost estimates across all major trades, ensuring no part of your project is overlooked. From the foundation to the finishing touches, our trade-specific estimates provide you with a complete and accurate breakdown of costs for any type of construction project.
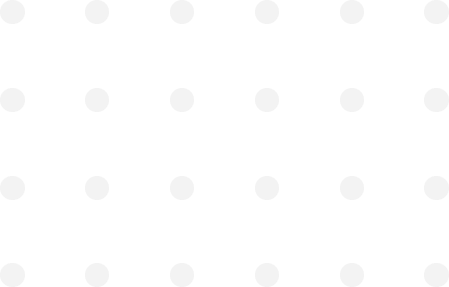
Testimonials
What Our Clients Say
We take pride in delivering accurate, timely, and reliable estimates that help contractors and builders win more projects. Our clients consistently praise our attention to detail, fast turnaround times, and the positive impact our estimates have on their businesses.
Estimate Florida Consulting has helped us win more bids with their fast and accurate estimates. We trust them for every project!
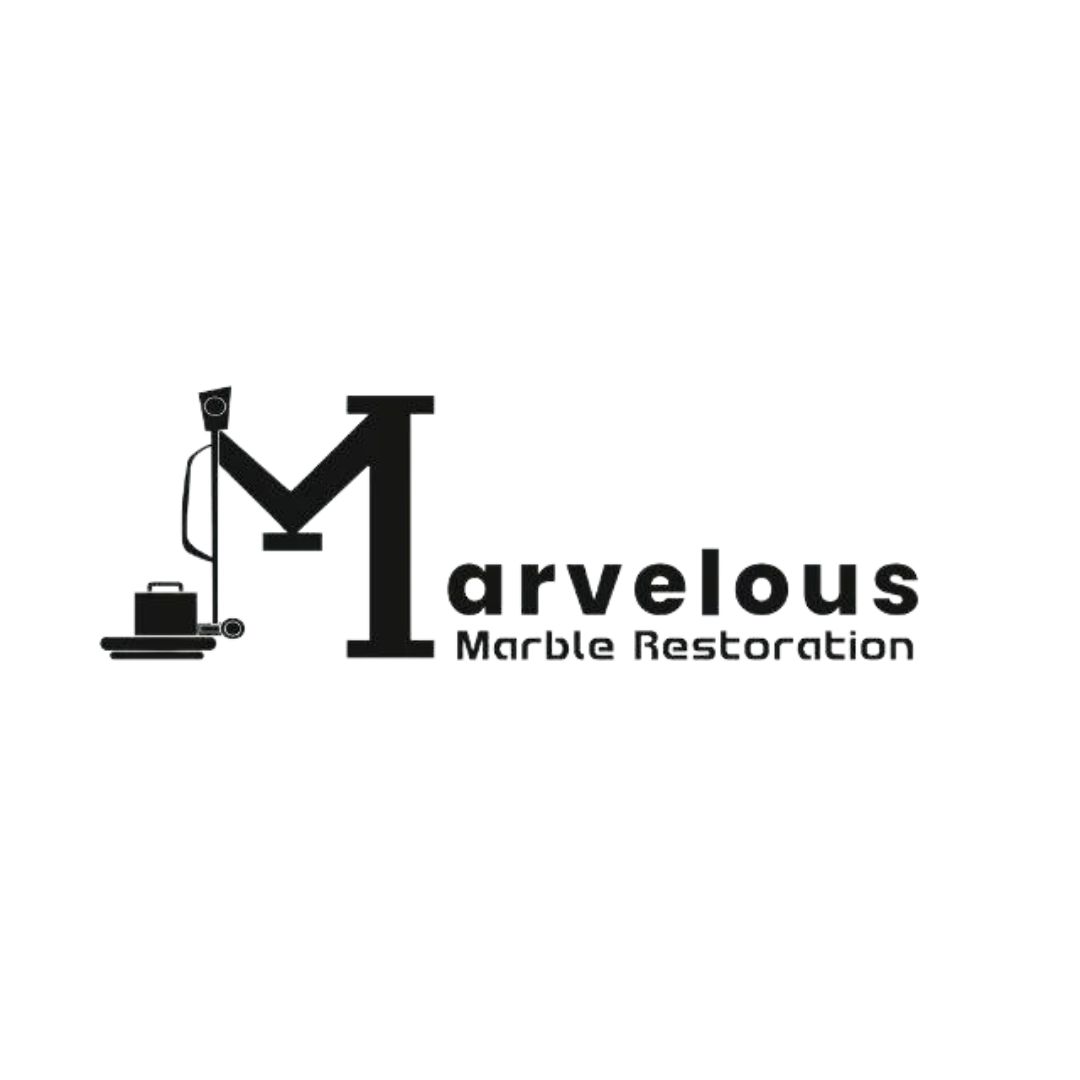
Steps to Follow
Our Simple Process to Get Your Estimate
01
Upload Plans
Submit your project plans, blueprints, or relevant documents through our online form or via email.
02
Receive Quotation
We’ll review your project details and send you a quote based on your scope and requirements.
03
Confirmation
Confirm the details and finalize any adjustments to ensure the estimate meets your project needs.
04
Get Estimate
Receive your detailed, trade-specific estimate within 1-2 business days, ready for your project execution.
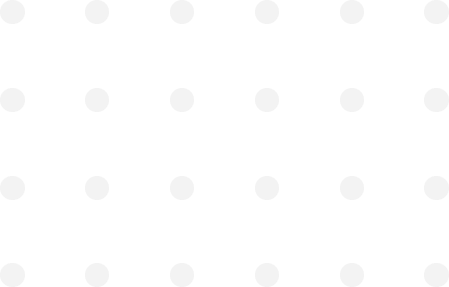