Metal Building Estimator
Estimate Florida Consulting, your go-to source for metal building estimates, offers FL metal buildings engineered and certified to withstand wind loads ranging from 170 to 200 mph. Our steel components are of the highest quality, all proudly made in the USA. We understand the unique needs of Floridians, which is why we provide a vast array of customization options for Florida-certified buildings. Plus, to make your experience even more convenient, we offer free delivery and installation services across the Sunshine State.
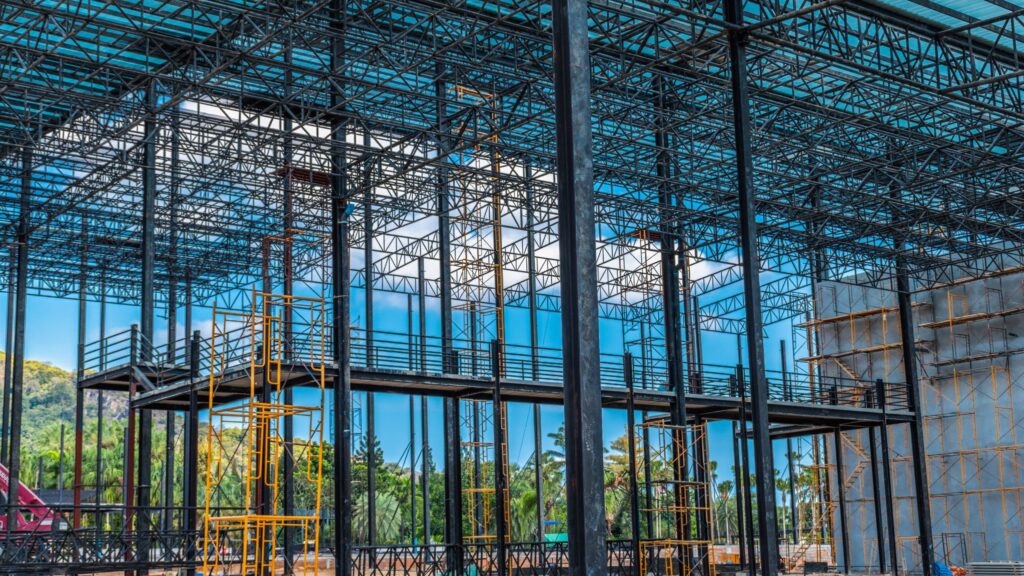
When it comes to durable, high-quality metal structures in Florida, we’ve got you covered. Visit our website at https://estimatorflorida.com/ for more information
Are You Looking For?
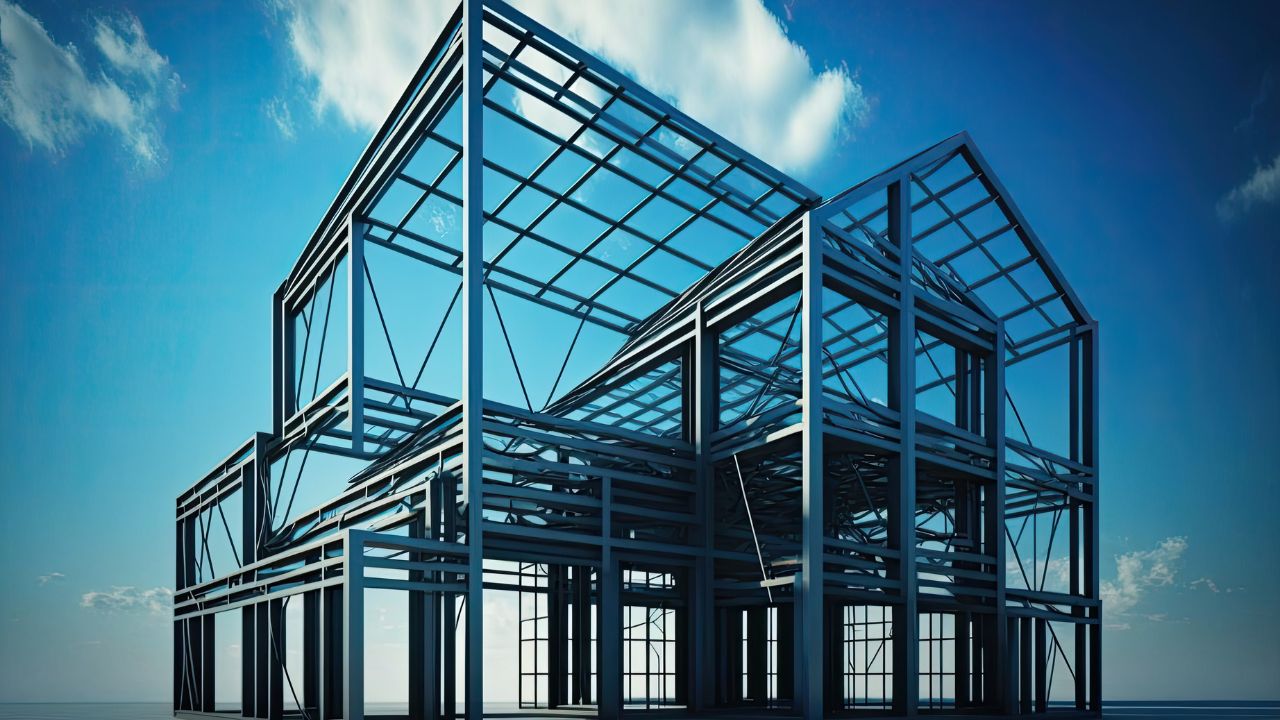
Make Informed Design Decisions Showcase Your Design Ideas
Get RenderingCall Us To Discuss More at 561-530-2845
Key Responsibilities of a Metal Building Estimator
Evaluating Project Requirements
Metal Building Estimators are responsible for thoroughly examining project specifications. They need to comprehend the scope of work, the materials required, and the labor involved. This initial assessment sets the foundation for a precise cost estimate.
Material Cost Estimations
Estimators must determine the quantity and cost of materials needed for the project. This includes steel, concrete, insulation, and any other materials that will be used in construction.
Labor Cost Estimations
Estimators also assess the labor costs, considering the required skills, workforce size, and time needed to complete the project. Accurate labor cost estimations are essential for budgeting.
Analyzing Blueprints and Plans
To provide an accurate estimate, Metal Building Estimators need to thoroughly analyze blueprints and construction plans. This involves identifying specific details and specifications to avoid overlooking essential elements.
Material | Average Cost per Square Foot |
Steel Frame | $13 – $18 |
Exterior Panels | $8 – $16 |
Roofing | $6 – $12 |
Insulation | $5 – $10 |
Doors and Windows | $30 – $50 |
Concrete Slab | $10 – $14 |
Electrical Wiring | $6 – $12 (per sq ft) |
Plumbing | $10 – $14 (per sq ft) |
HVAC System | $22 – $38 |
These figures are still approximations, and it’s crucial to get detailed quotes from local suppliers and contractors for your specific project to obtain more precise and up-to-date cost estimates.
WHAT IS A PRE-ENGINEERED METAL BUILDING?
A pre-engineered metal building, often referred to as a PEMB, is a structure in which key components, such as wall and roof panels, are fabricated in a factory and later transported to the construction site for assembly. This pre-engineering approach involves constructing the entire building off-site before final assembly.
Pre-engineered metal buildings typically feature a steel framework that supports metal wall and roof panels. These structures are designed in advance to precisely fit specific requirements, which include:
- The preferences of the building owner
- Compliance with local building codes
- Addressing potential load considerations
- Environmental factors and considerations
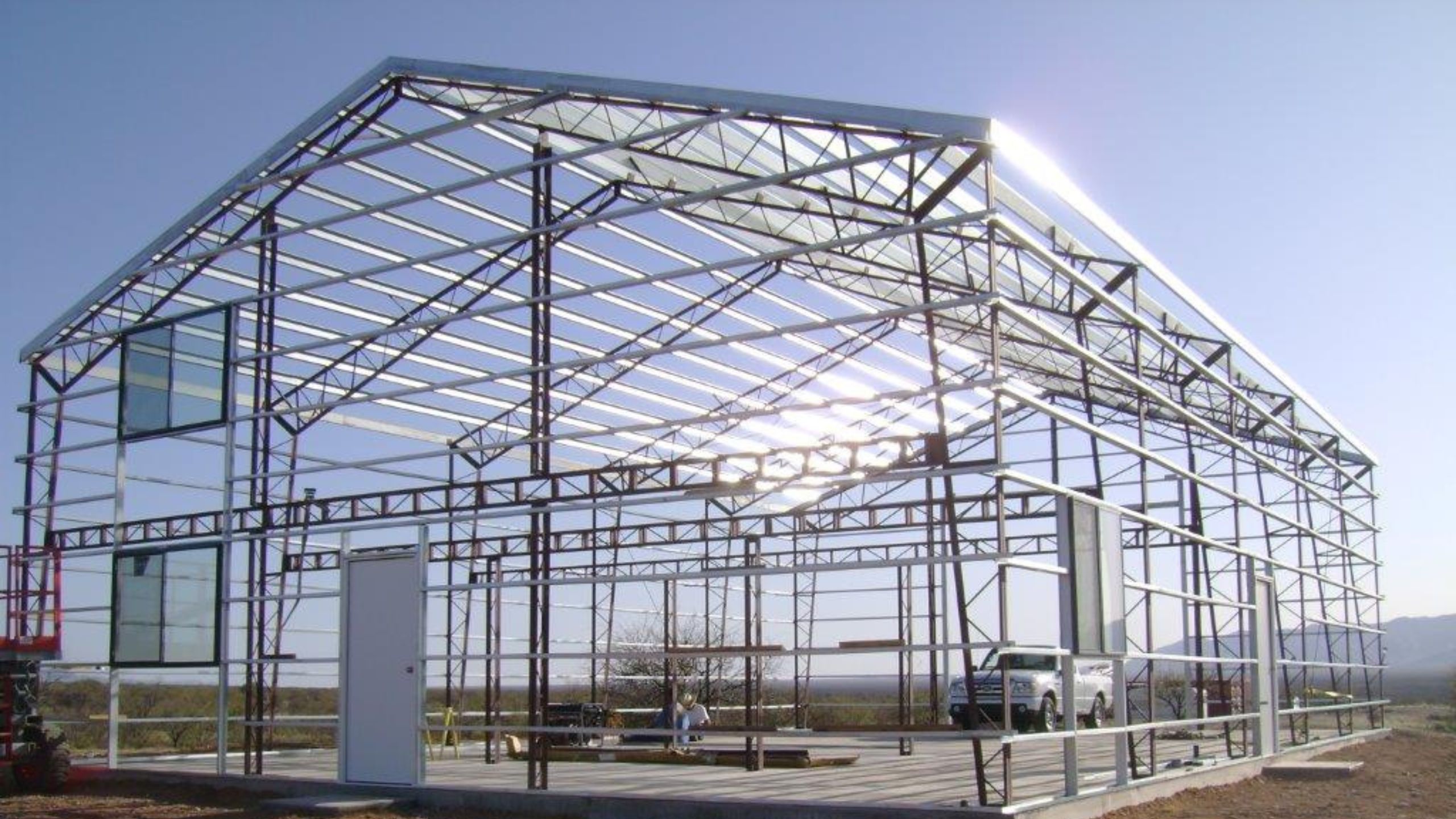
Steel buildings predominantly employ “I-beams,” aptly named for their resemblance to the letter “I.” These I-beams are produced by welding together steel plates and then assembled to create the primary framework of the building.
COMMON USES FOR PRE-ENGINEERED METAL BUILDINGS
Thanks to their cost-effective and time-efficient attributes, Pre-Engineered Metal Buildings (PEMBs) find wide-ranging applications across various building types. Metal buildings are commonly utilized for small retail and commercial office structures, storage units, industrial facilities, warehouses, and more.
Commercial: Steel structures are a fantastic and affordable investment for commercial buildings of all sizes. PEMB frames offer versatility, allowing for the design of attractive steel buildings, whether they’re intended to be large-scale retailers or compact storage units.
Agricultural: Metal buildings present an economical solution for sheltering agricultural equipment and safeguarding livestock.
Warehouses: The robust durability of steel buildings makes them an excellent choice for warehouses. Owners can securely store their goods within a metal building, assured that they will remain protected from adverse weather conditions and pests.
Government: Publicly funded buildings often contend with tight budgets. Steel buildings provide an ideal solution for government facilities like fire stations and libraries, effectively managing costs while maintaining an appealing aesthetic. Additionally, steel buildings align with environmentally friendly practices.
Recreational Sports Facilities: PEMBs maximize space utility, rendering them a popular choice for recreational sports centers. Furthermore, their flexibility allows for potential expansion in the future as needs evolve.
PRE-ENGINEERED METAL BUILDINGS AVERAGE COST PER SQUARE FOOT
Alright, we’ve delved into the essence of pre-engineered metal buildings and their exceptional features. Now, let’s talk about the cost.
Metal buildings are priced based on square footage, and on average, you can anticipate an expenditure of $13 to $32.50 per square foot for a PEMB. However, this cost range can fluctuate, spanning from $7.80 to as high as $156 per square foot, contingent on specific considerations.
When you juxtapose this pricing with the average cost of wooden structures at $46.80 per square foot, the economic advantage of PEMBs becomes evident. Remember those I-beams we discussed earlier? On average, I-beam steel buildings cost around $22.10 per square foot.
For instance, if you were planning to construct a 2,400-square-foot warehouse (40 x 60 ft.) with I-beams, you might budget approximately $52,000.
Are You Looking For?
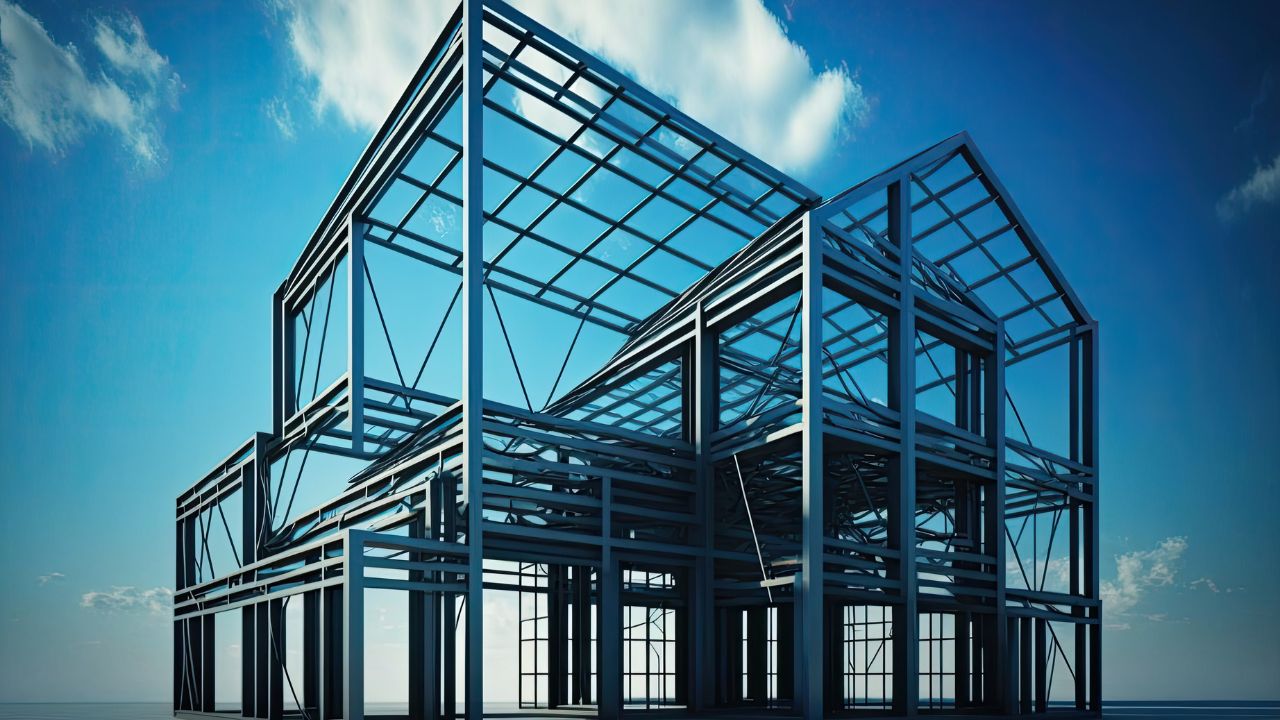
Make Informed Design Decisions Showcase Your Design Ideas
Get RenderingCall Us To Discuss More at 561-530-2845
7 FACTORS THAT INFLUENCE COST
The cost of a pre-engineered metal building is a dynamic variable, subject to a multitude of factors that can impact the final project expense. Seven key factors that play a pivotal role in determining the cost include:
- BUILDING SIZE: The size of the structure can significantly impact costs. Larger metal buildings tend to offer a lower cost of steel per square foot due to potential bulk discounts from suppliers. Conversely, smaller buildings might incur higher costs per square foot but lower overall costs, particularly for simpler designs.
- MATERIAL: The choice of steel material can have a pronounced effect on the cost per square foot of your Pre-Engineered Metal Building (PEMB). Options for steel materials encompass varieties such as Galvanized, Stainless, Structural, Rebar, Alloy, Mild, Tool, and Light Gauge. Galvanized and stainless steel are preferred for their quality, albeit with higher upfront costs offset by long-term structural integrity.
- LOCATION AND CLIMATE: Regional variances in building codes and climate conditions play a substantial role in determining cost. Diverse local building codes necessitate additional components that can raise expenses. Climate conditions, such as seismic risks or extreme weather demands, can lead to specific design features that translate into higher costs.
- STEEL PRICES: Steel prices are influenced by the fluctuating nature of the commodity market. Factors like weather, global economic shifts, and supply-demand dynamics can lead to price fluctuations. Tariffs on steel trade have also impacted costs, with recent developments expected to mitigate price escalation.
- LABOR COSTS: Labor costs are another significant consideration. The materials chosen and the complexity of the design influence the skilled labor required. Simple structures typically result in lower labor costs, whereas intricate and larger buildings necessitate higher labor expenditures.
- CUSTOMIZATIONS: Customizing your building design can affect the final cost. Complex features like second floors, basements, hangar doors, windows, and insulation packages can lead to higher expenses. Customization is encouraged for those seeking tailored solutions, recognizing the investment’s long-term nature.
- STRUCTURE OPTIONS: The choice of building structure is an important factor. Various suppliers offer multiple options, and the structure chosen can influence the overall price. Options include Arch, Open Web, Tube Steel, Hybrid Open Web Truss, Rigid Frame, and C-Channel, each with its unique attributes impacting cost differently.
These seven factors collectively determine the cost of a pre-engineered metal building, and careful consideration of each element is essential when estimating project expenses.
ASSEMBLE YOUR DREAM TEAM FOR YOUR UPCOMING CONSTRUCTION VENTURE
The allure of pre-engineered metal buildings, with their cost-efficiency, versatility, and eco-friendliness, is indeed captivating. Eager to embark on your new project, it’s vital to consider turning your vision into a lasting, prideful investment.
You deserve nothing less than excellence in construction. With Our Construction Group at your side, you can rest assured that our team will surpass your expectations, beginning with that initial phone call and extending all the way to the ribbon-cutting ceremony.
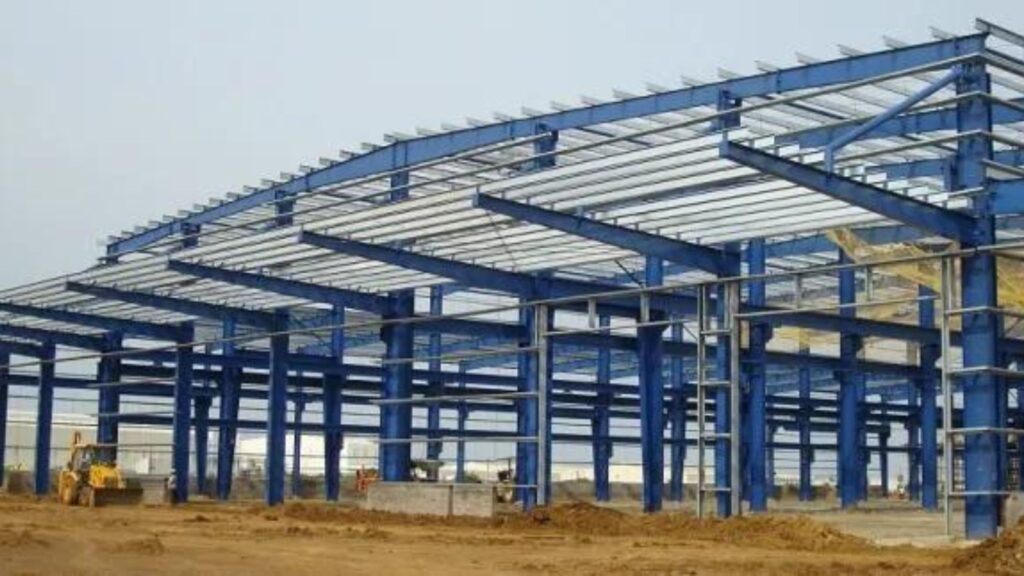
Let be the catalyst for bringing your vision to life. Get in touch with us today and kickstart your journey towards construction excellence!
The Estimation Process
Initial Assessment
Before diving into detailed estimations, Metal Building Estimators conduct an initial assessment of project requirements, allowing them to get a broad sense of the project’s scope and needs.
Cost Breakdown
Estimators break down the costs into material, labor, and additional expenses. This thorough breakdown helps in creating a comprehensive budget.
Final Estimate
The final estimate is a culmination of all calculations and assessments. It provides clients with a detailed overview of expected costs.
Conclusion
When it comes to obtaining precise and reliable metal building estimates in Florida, Estimate Florida Consulting stands as the go-to source. With metal buildings engineered and certified to withstand the state’s unique wind loads and a wide array of customization options, we’re dedicated to meeting the diverse needs of Floridians. Our commitment to quality is unwavering, with steel components proudly made in the USA. What’s more, we offer the added convenience of free delivery and installation services across the Sunshine State. When you choose Estimate Florida Consulting, you’re choosing durability, high quality, and peace of mind for your metal structure needs. Visit our website at https://estimatorflorida.com/ for more information on how we can help you realize your construction vision in the state of Florida.
Frequently Asked Questions (FAQs) for Metal Building Estimator
Estimate Florida Consulting offers metal buildings engineered and certified to withstand wind loads ranging from 170 to 200 mph. They provide steel components made in the USA and offer a wide array of customization options for Florida-certified buildings. They also offer free delivery and installation services across Florida.
Metal Building Estimators evaluate project requirements, estimate material and labor costs, and analyze blueprints and plans to provide precise cost estimates. Their responsibilities include ensuring accurate cost estimations for projects.
Material costs for metal buildings are estimated based on the quantity and cost of materials required for the project. This includes steel, concrete, insulation, and other construction materials.
Labor costs are estimated by considering factors such as the required skills, workforce size, and time needed to complete the project. Accurate labor cost estimations are crucial for budgeting.
Common materials and their average costs per square foot include:
Steel Frame: $13 – $18
Exterior Panels: $8 – $16
Roofing: $6 – $12
Insulation: $5 – $10
Doors and Windows: $30 – $50
Concrete Slab: $10 – $14
Electrical Wiring: $6 – $12 (per sq ft)
Plumbing: $10 – $14 (per sq ft)
HVAC System: $22 – $38
These are approximations; specific project costs may vary.
A pre-engineered metal building, or PEMB, is a structure where key components like wall and roof panels are fabricated in a factory and later assembled on-site. These buildings often feature a steel framework and are designed to fit specific requirements, such as local building codes and environmental considerations.
PEMBs are used for various building types, including commercial structures, agricultural buildings, warehouses, government facilities, and recreational sports facilities. They are valued for their cost-effectiveness and flexibility.
On average, the cost for a pre-engineered metal building ranges from $13 to $32.50 per square foot. The cost may vary based on specific project requirements and considerations.
Several factors impact the cost, including building size, choice of steel material, location and climate, steel prices, labor costs, customizations, and structure options. Careful consideration of these factors is essential when estimating project expenses.
The estimation process includes:
Initial Assessment: A broad assessment of project requirements.
Cost Breakdown: Breaking down costs into material, labor, and additional expenses.
Final Estimate: Providing clients with a detailed overview of expected costs based on calculations and assessments.
Process To Get Metal Building Cost Estimate Report
Here I am going to share some steps to get your metal building cost estimate report.
-
You need to send your plan to us.
You can send us your plan on info@estimatorflorida.com
-
You receive a quote for your project.
Before starting your project, we send you a quote for your service. That quote will have detailed information about your project. Here you will get information about the size, difficulty, complexity and bid date when determining pricing.
-
Get Estimate Report
Our team will takeoff and estimate your project. When we deliver you’ll receive a PDF and an Excel file of your estimate. We can also offer construction lead generation services for the jobs you’d like to pursue further.
Google Reviews
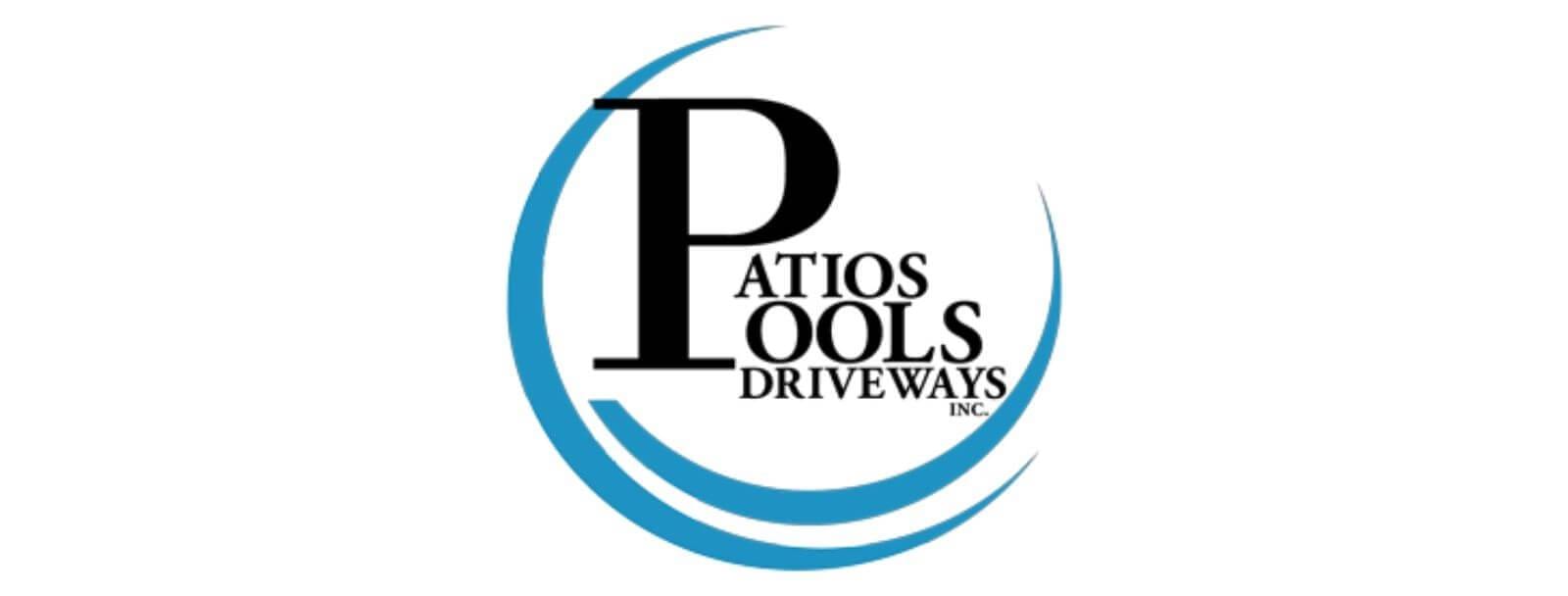
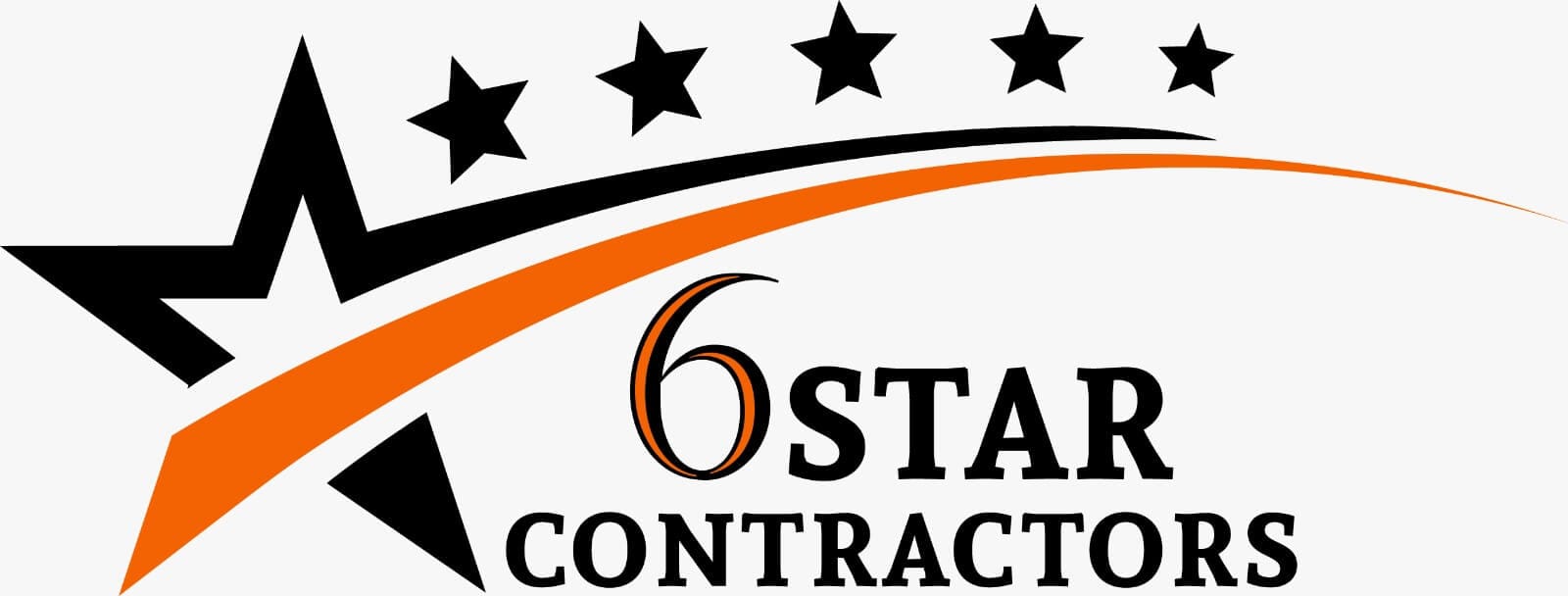
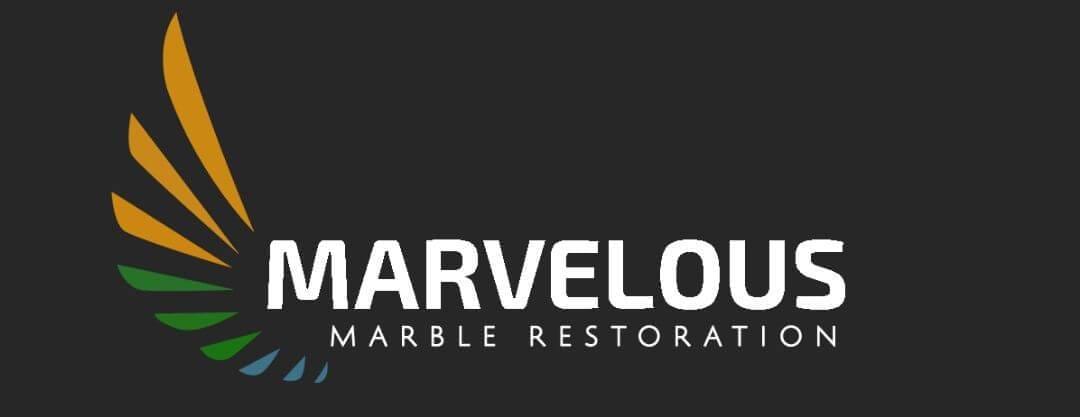