Mechanical Cost Estimator in Palm Beach Gardens, FL
At Estimate Florida Consulting in Palm Beach Gardens, we specialize in providing detailed mechanical cost estimations, tailored to both residential and commercial projects. For residential HVAC systems, installation costs typically range from $5,000 to $10,000, influenced by system type, size, and installation complexity. Commercial mechanical systems, including HVAC and specialized components like elevators, start at around $15,000 and can exceed $30,000, reflecting the greater scale and complexity. Maintenance costs for these systems also vary, with residential HVAC maintenance averaging between $100 and $500 annually, and commercial systems incurring higher due to their intricate nature.
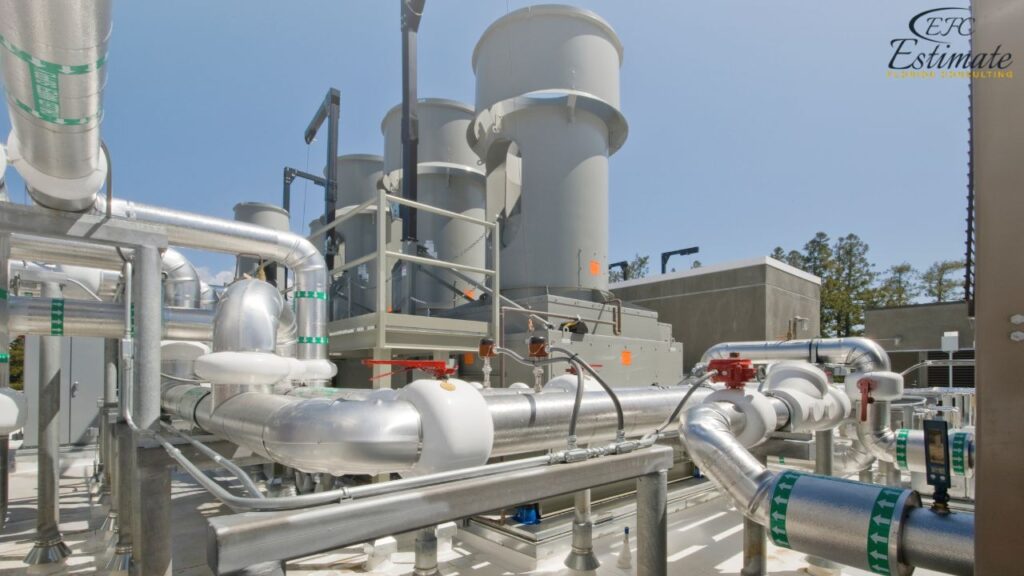
Additionally, we factor in the potential long-term savings from energy-efficient systems, which, despite higher upfront costs, can offer operational savings and may qualify for rebates or tax incentives, providing a comprehensive financial perspective for our clients.
We Work for All Construction Trades
Construction trades encompass a variety of specialized roles, each critical to the successful completion of a project. Skilled tradespeople not only ensure the work is done right but also enhance safety, efficiency, and compliance with local building codes. From the initial groundwork to the final touches, every step requires expertise from dedicated professionals.
Cost to Repair Ductwork by Material
There exist various types of ductwork, ranging from economical, flexible, non-metallic options to premium sheet metal variants. Each type features distinct designs and materials, with repair costs varying accordingly. Hence, the type of duct you have can significantly impact the expenses of repairs. Below outlines the primary duct types alongside their average repair costs for a standard 30 linear feet section of ductwork.
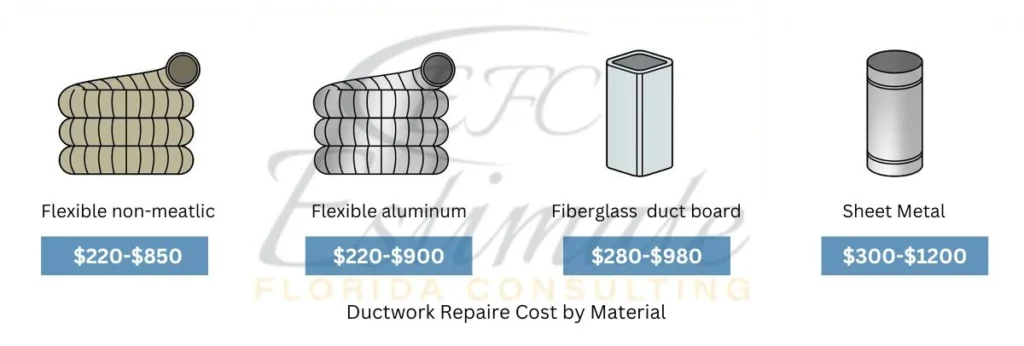
Duct Material | Repair Cost |
Flexible Non-Metallic | $220 – $850 |
Flexible Aluminum | $220 – $900 |
Fiberglass Duct Board | $280 – $980 |
Sheet Metal | $300 – $1200 |
90% More Chances to Win Projects With Our Estimate!
- Multi-Family Building
- Hotel Building
- Hospital Building
- Warehouse Building
- School & University Building
- High-Rise Building
- Shopping Complex
- Data Center Building
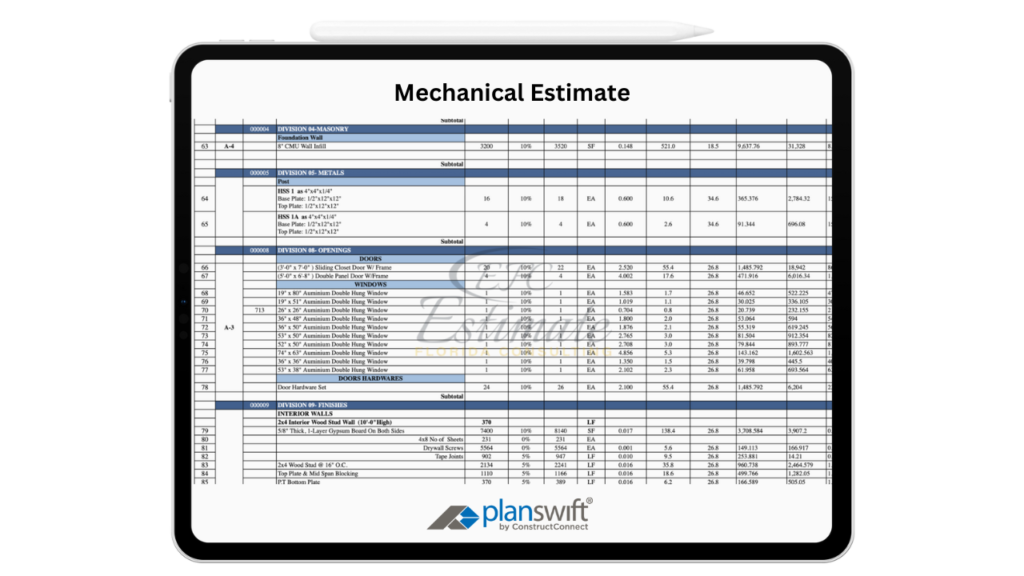
Mechanical Cost Breakdown
At Estimate Florida Consulting, we pride ourselves on delivering precise mechanical cost estimations tailored to the unique requirements of both residential and commercial projects. Our comprehensive approach covers a wide range of cost factors, ensuring that our clients in Palm Beach Gardens can make well-informed financial decisions.
Here is the mechanical cost breakdown presented in a table format:
Cost Category | Residential Costs | Commercial Costs |
Installation Costs – Basic Systems | $6,000 – $8,500 | $18,000 – $24,000 |
Installation Costs – Mid-Range Systems | $8,500 – $10,000 | $24,000 – $30,000 |
Installation Costs – High-Efficiency Systems | $10,000 – $12,000 | $30,000 – $36,000 |
Installation Costs – Elevators (Basic Models) | $15,000 – $20,000 | $24,000 – $48,000 |
Installation Costs – Elevators (Advanced Models) | $20,000 – $30,000 | $48,000 – $84,000 |
Maintenance Costs (Annual) – Standard HVAC | $120 – $240 | $600 – $1,200 |
Maintenance Costs (Annual) – Comprehensive HVAC | $240 – $600 | $1,200 – $3,600 |
Maintenance Costs (Annual) – Elevator | $500 – $1,500 | $1,200 – $4,800 |
Residential Projects
Installation Costs
- Basic Systems: Homeowners can expect to pay between $6,000 and $8,500 for the installation of basic HVAC systems. These systems are ideal for standard-sized homes and provide essential heating and cooling functions.
- Mid-Range Systems: For those seeking a balance between cost and efficiency, mid-range systems are priced between $8,500 and $10,000. These systems often include additional features or higher efficiency ratings.
- High-Efficiency Systems: High-end systems, which offer the best in efficiency and performance, range from $10,000 to $12,000. While they have higher upfront costs, they can lead to significant long-term energy savings.
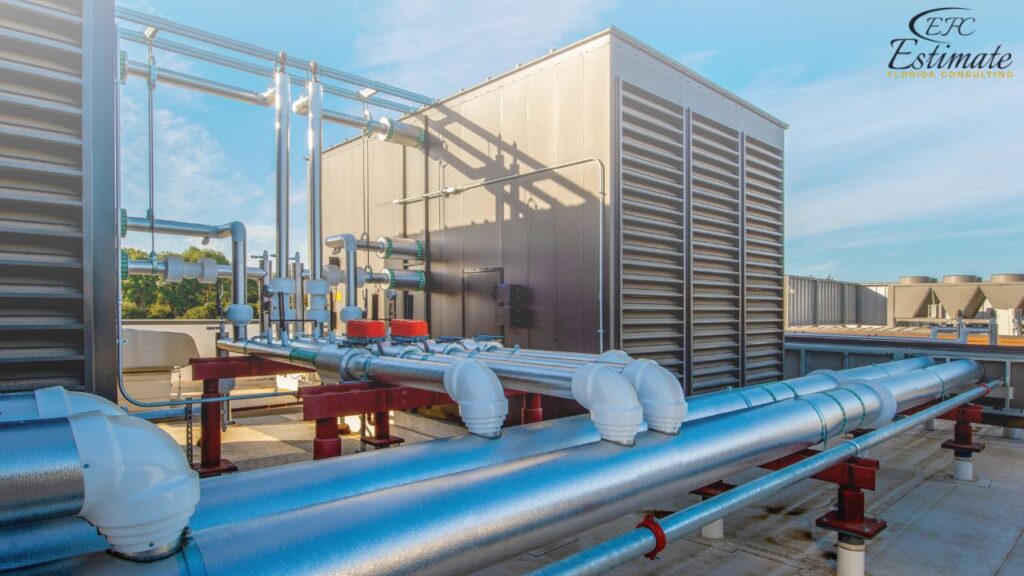
Annual Maintenance Costs
- Standard HVAC Maintenance: On average, annual maintenance for standard HVAC systems will cost between $120 and $240. Regular maintenance is crucial for optimal performance and longevity.
- Comprehensive HVAC Maintenance: For more comprehensive service plans, homeowners should budget between $240 and $600 annually. These plans often include more extensive checks and preventive measures.
Get 5 New Leads in the Next 7 Days With Our System
- Multi-Family Building
- Hotel Building
- Hospital Building
- Warehouse Building
- High-Rise Building
- Shopping Complex
Cost to Run a Gas Line by Project
Numerous factors contribute to the varied expenses associated with plumbing your home for gas installation. These costs are contingent on variables like geographic location, the specific appliance, line length, and the installation process. While plumbers are responsible for extending a gas pipe from your meter to your appliances, the utility company handles the installation of the gas line from the street to your residence. As these two entities entail distinct charges, effective coordination between them is imperative to ensure optimal gas pipe installation. Furthermore, even within the confines of your house, diverse types of gas pipe installations exist, each exerting an influence on the overall project.
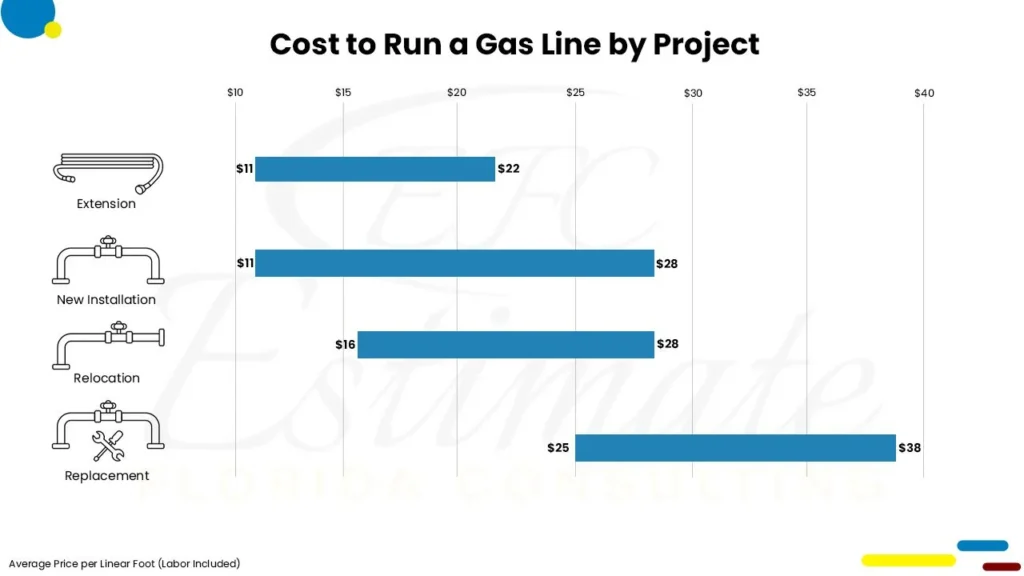
Project | Average Price per Linear Foot (Labor Included) |
---|---|
Extension | $11 – $22 |
New Installation | $11 – $28 |
Relocation | $16 – $28 |
Replacement | $25 – $38 |
Commercial Projects:
Installation Costs
- HVAC Systems: The installation costs for commercial HVAC systems start at $18,000 and can go up to $36,000, depending on the system type and complexity. Commercial systems are designed to handle larger spaces and higher demands.
- Elevators: Basic elevator models start around $24,000, with more advanced models costing between $48,000 and $84,000. These costs vary significantly based on the elevator’s capacity and technology.
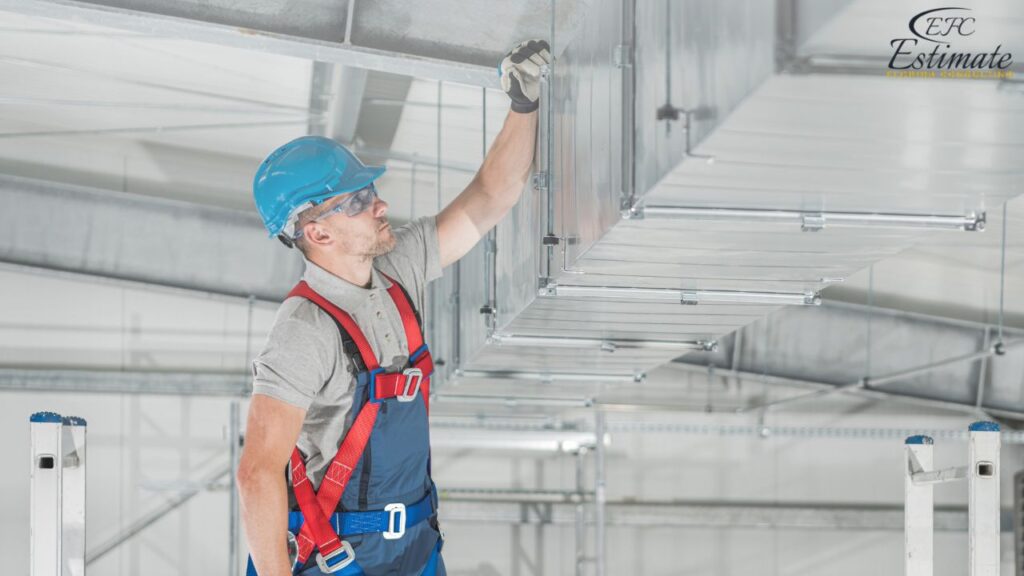
Annual Maintenance Costs
- HVAC Maintenance: Commercial properties should expect to spend between $600 and $3,600 annually for HVAC maintenance. The higher costs reflect the complexity and scale of commercial systems.
- Elevator Maintenance: Elevator maintenance is crucial for safety and efficiency, with annual costs ranging from $1,200 to $4,800. These costs can vary based on the type and usage of the elevator.
Commercial Heating System Installation Cost
The cost of installing a commercial heating system is significantly affected by the system’s size and capacity to produce heat. Larger spaces in commercial settings require more powerful heating systems, leading to higher initial costs due to the equipment’s size, complexity, and installation requirements. The design and layout of the building also play a crucial role in determining the installation costs. Factors such as the building’s square footage, number of floors, room configurations, and ease of access can all add complexity to the installation process, thereby impacting the cost.
Download Template For Mechanical Project Breakdown
- Materials list updated to the zip code
- Fast delivery
- Data base of general contractors and sub-contractors
- Local estimators
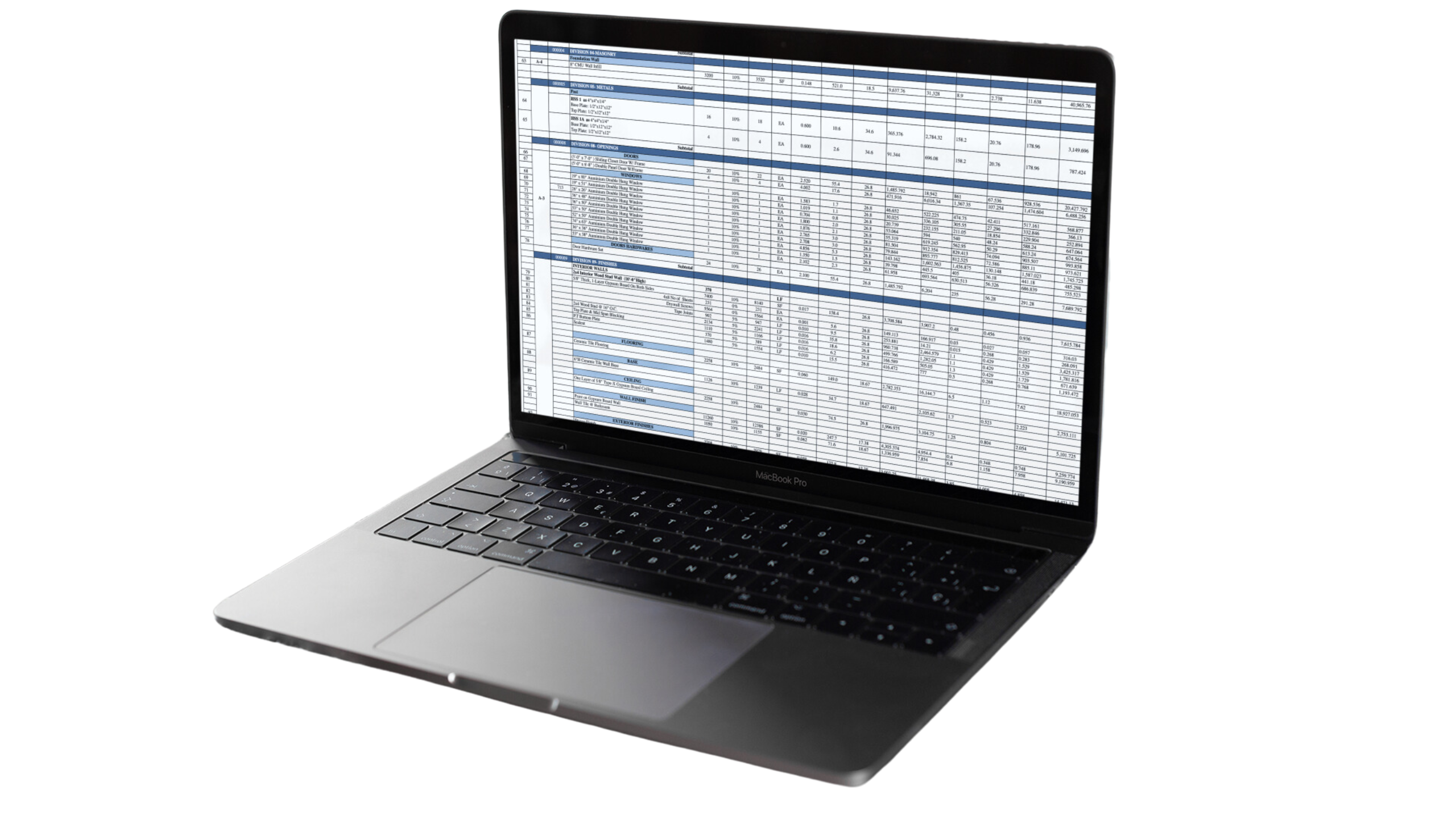
When selecting a heating system for commercial use, the type of system chosen also influences the installation costs. Common options include rooftop HVAC units, boilers, heat pumps, and radiant heating systems. The choice depends on various factors, including the building’s heating needs, local climate conditions, and energy efficiency goals.
Heating System Type | Cost Range |
Rooftop HVAC Units | $20,000 – $60,000+ |
Boilers | $10,000 – $50,000+ |
Heat Pumps | $10,000 – $30,000+ |
Radiant Heating Systems | $15,000 – $40,000+ |
Cost of Mechanical Ventilation by Type
Mechanical air exchange systems typically cost between $520 and $10,000. These systems utilize fans installed in windows, walls, or air ducts to either remove or add air to the home. Condensation, formed when warm air meets cold surfaces, can be prevented by these fans, which either extract or introduce air to maintain balanced air quality within the room. A balanced mechanical ventilation system ensures that the air quality meets specific design specifications.
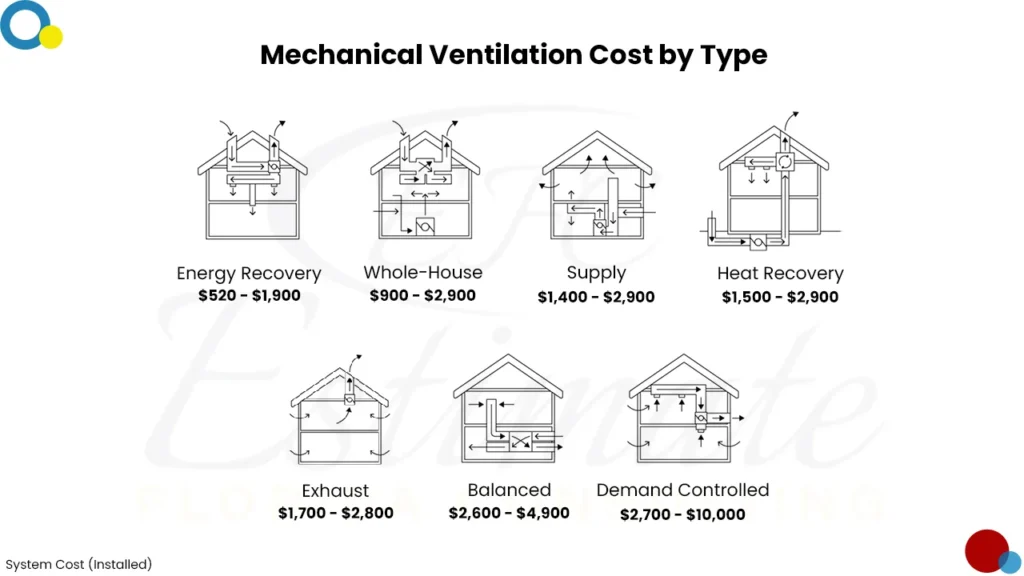
Mechanical Ventilation Type | System Cost (Installed) |
Energy Recovery | $520 – $1,900 |
Whole-House | $900 – $2,900 |
Supply | $1,400 – $2,900 |
Heat Recovery | $1,500 – $2,900 |
Exhaust | $1,700 – $2,800 |
Balanced | $2,600 – $4,900 |
Demand Controlled | $2,700 – $10,000 |
Business Finance Loan
Find out if you're pre-qualified in seconds
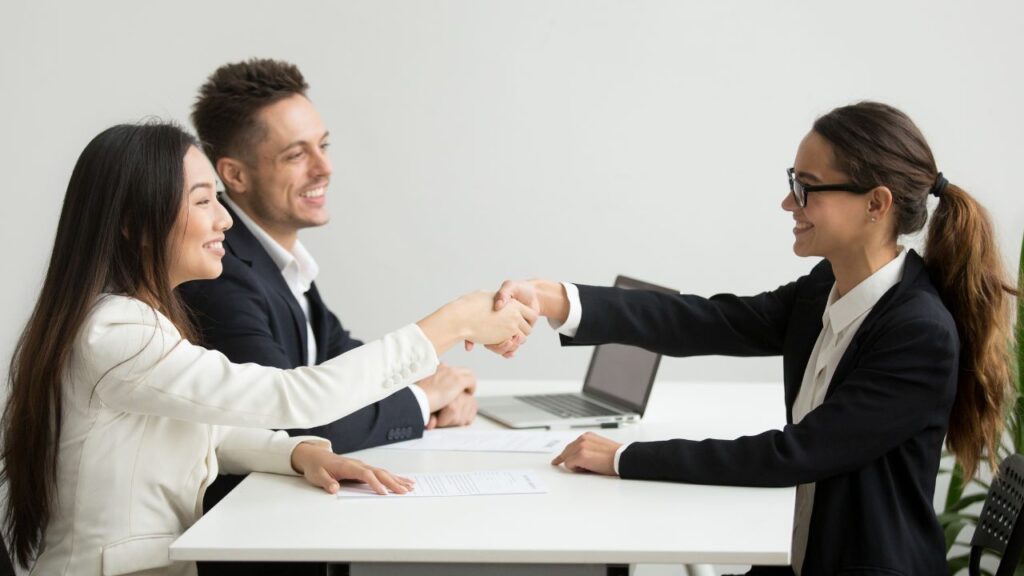
Get Prequalified Now
IMPORTANT: Make sure the email and phone number you enter are correct. We will email and text you a link to get started.
Factors Affecting Cost Estimates
Factors affecting cost estimates for the Mechanical Cost Estimator project in Palm Beach Gardens include labor availability, material prices, equipment procurement, overhead expenses, economic conditions, regulatory requirements, and environmental considerations, all influencing the accuracy and reliability of project budgeting.
Labors Cost
Estimate Florida Consulting specializes in providing accurate cost estimations for projects like the Mechanical Cost Estimator in Palm Beach Gardens. Our comprehensive approach considers various factors such as labor availability, material prices, and overhead expenses. For this project, estimated at $100,000, labor costs in Palm Beach Gardens are influenced by the local workforce’s skill level and prevailing wage rates. By meticulously analyzing these factors and leveraging industry expertise, we ensure our clients receive reliable estimates crucial for effective project planning and budgeting. With our commitment to precision and transparency, Estimate Florida Consulting enables clients to make informed decisions and achieve successful outcomes in their mechanical projects.
Labors Breakdown Cost
Labor Category | Cost |
Skilled Worker | $50,000 |
Supervisor | $30,000 |
Miscellaneous | $10,000 |
Contingency | $10,000 |
Materials Cost
At Estimate Florida Consulting, our expertise extends to estimating the material costs for projects like the Mechanical Cost Estimator in Palm Beach Gardens. With a budget estimate of $80,000, we meticulously assess various factors influencing material expenses, such as market prices, transportation costs, and the specific requirements of the project. In Palm Beach Gardens, sourcing materials may entail considerations like availability and shipping logistics, which impact overall costs. Our comprehensive approach ensures that clients receive accurate and detailed estimates, facilitating informed decision-making and efficient resource allocation.
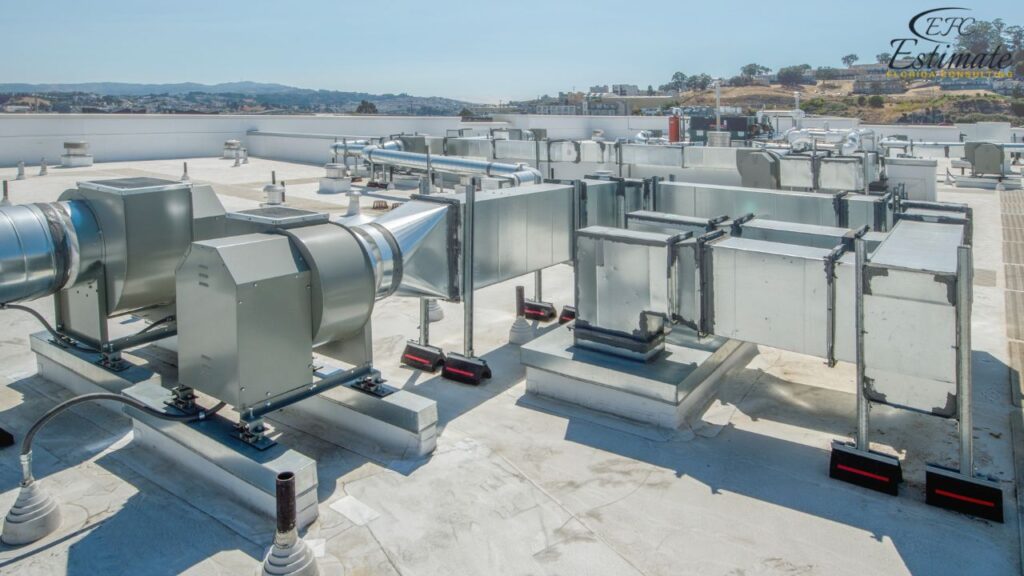
By leveraging our experience and industry insights, Estimate Florida Consulting empowers clients to plan and execute their mechanical projects with confidence, knowing they have reliable cost projections tailored to their needs and circumstances.
Diverse Materials for Mechanical Projects
Steel: Widely used for structural components, piping, and machinery due to its strength and durability.
Aluminum: Lightweight and corrosion-resistant, ideal for applications requiring both strength and low weight.
Copper: Commonly used in plumbing systems and electrical wiring due to its excellent conductivity and corrosion resistance.
Plastic/PVC: Versatile material used for piping, insulation, and components requiring corrosion resistance and cost-effectiveness.
Composite Materials: Combining two or more materials to create a material with specific properties, often used in aerospace and automotive industries.
Titanium: Known for its high strength-to-weight ratio and corrosion resistance, used in aerospace, medical implants, and high-performance applications.
Brass: Alloy of copper and zinc, valued for its corrosion resistance and aesthetic appeal, used in plumbing fixtures and decorative applications.
Ceramics: Heat-resistant and wear-resistant materials used in high-temperature applications such as engine components and cutting tools.
Glass: Used in mechanical projects for windows, lenses, and specialized components requiring transparency and optical properties.
Rubber: Elastic and flexible material used in seals, gaskets, and vibration isolation components in mechanical systems.
Estimate Your Project With Us
Materials of Mechanical Project and Breakdown Cost
Item | Cost |
Steel | $5 – $20 per square foot |
Aluminum | $10 – $30 per square foot |
Copper | $20 – $40 per square foot |
Plastic/PVC | $2 – $8 per square foot |
Composite Materials | $30 – $50 per square foot |
Titanium | $30 – $60 per square foot |
Brass | $15 – $35 per square foot |
Ceramics | $20 – $50 per square foot |
Glass | $40 – $50 per square foot |
Rubber | $5 – $15 per square foot |
Project Complexity
The Mechanical Cost Estimator project in Palm Beach Gardens encounters varying levels of complexity influenced by several factors. Factors include the scale of the project, intricacy of mechanical systems, site conditions, and regulatory requirements. For instance, estimating the cost for a small-scale HVAC system installation in a commercial building may be less complex compared to retrofitting a large-scale industrial facility with advanced mechanical ventilation systems. Moreover, the presence of unique challenges such as tight deadlines, limited access to the site, or the need for specialized equipment further adds to the project’s complexity.
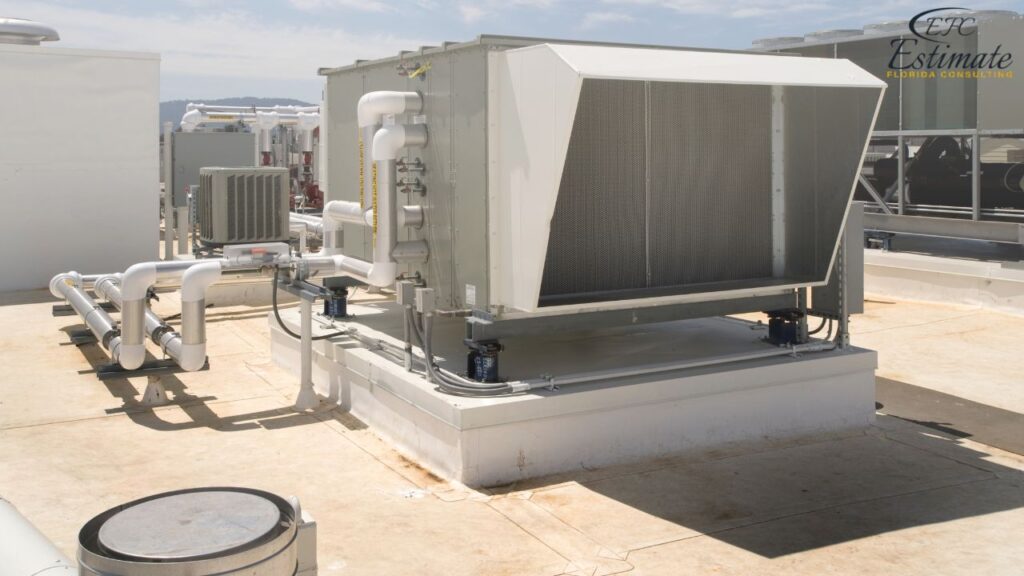
Successfully navigating these complexities demands a thorough understanding of mechanical systems, effective communication with stakeholders, and adept project management skills to ensure accurate cost estimation and timely completion of projects in Palm Beach Gardens.
Location-specific Factors
Location-specific factors significantly influence the Mechanical Cost Estimator project in Palm Beach Gardens. Situated in a coastal area, Palm Beach Gardens’s unique environmental conditions, such as humidity and salt exposure, impact material selection and system design to ensure durability and corrosion resistance. Moreover, the availability of skilled labor and local subcontractors, as well as transportation logistics for materials, affect project timelines and costs. Regulatory requirements specific to Florida, including building codes and environmental regulations, must also be carefully considered during cost estimation. Additionally, Palm Beach Gardens’s economic landscape and market dynamics can influence material prices and labor rates, necessitating ongoing monitoring and adaptation to ensure accurate budgeting. By addressing these location-specific factors, the Mechanical Cost Estimator project can effectively tailor cost estimates to the realities of the Palm Beach Gardens area, facilitating successful project execution.
We Provide Manual Estimate!
We provide accurate pricing for the ZIP code of your project.
Turnaround time is 1-2 days.
Win More Projects With Us
Common Challenges and Solutions
Common challenges for the Mechanical Cost Estimator project in Palm Beach Gardens include fluctuating material prices and labor shortages. Solutions involve regularly updating cost databases, fostering relationships with local suppliers, and exploring alternative materials and technologies to mitigate cost uncertainties.
Data Accuracy
Ensuring the accuracy of input data such as material costs, labor rates, and project specifications can be challenging, leading to inaccurate cost estimates.
Solution: Implement rigorous data validation processes and regularly update databases with current market rates. Utilize software tools to cross-check and validate inputs, minimizing errors in estimates.
Variability in Material Costs
Fluctuations in material prices can significantly impact project cost estimates, especially for long-term projects where prices may change over time.
Solution: Maintain close relationships with suppliers to stay informed about price fluctuations. Incorporate contingency plans and buffers in estimates to accommodate unexpected price changes. Utilize historical data and trend analysis to predict future price trends more accurately.
Complexity of Project Specifications
Interpreting and incorporating complex project specifications accurately into cost estimates can be daunting and prone to errors.
Solution: Invest in training for estimators to enhance their understanding of project specifications. Utilize standardized templates and checklists to ensure all relevant details are captured. Collaborate closely with project managers and engineers to clarify ambiguities and refine estimates.
Need Template For Your Mechanical Business
We provide services for Brochure, Banner, Business Card, Envelope, Invoice, etc.
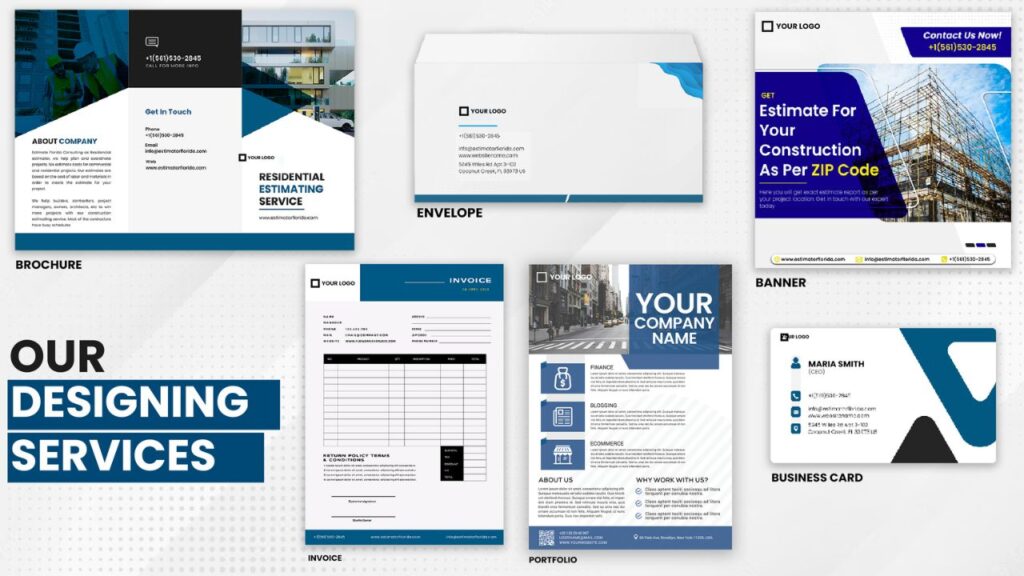
Labor Productivity and Availability
Predicting labor productivity and availability accurately can be challenging due to factors such as skill shortages, seasonal fluctuations, and unforeseen delays.
Solution: Conduct thorough workforce analysis to understand labor availability and skill levels in the Palm Beach Gardens region. Incorporate buffer times in estimates to account for potential delays. Utilize subcontractors and temporary labor to supplement in-house resources during peak demand periods.
Stakeholder Communication and Alignment
Ensuring clear communication and alignment between stakeholders regarding project scope, budget constraints, and expectations can be difficult, leading to misunderstandings and disputes.
Solution: Establish transparent communication channels and hold regular meetings to keep stakeholders informed about cost estimates and any changes. Use visual aids such as charts and graphs to illustrate cost breakdowns and potential impacts. Foster a collaborative environment where stakeholders can provide feedback and raise concerns openly.
Steps in the Mechanical Cost Estimator in Palm Beach Gardens
The Mechanical Cost Estimator in Palm Beach Gardens follows a structured process: gathering project specifications, sourcing material and labor costs, calculating estimates using specialized software, reviewing for accuracy, and presenting findings to stakeholders for approval and adjustments as needed.
Project Scope Definition
- Gather detailed project specifications including size, materials, and any special requirements from the client or project manager.
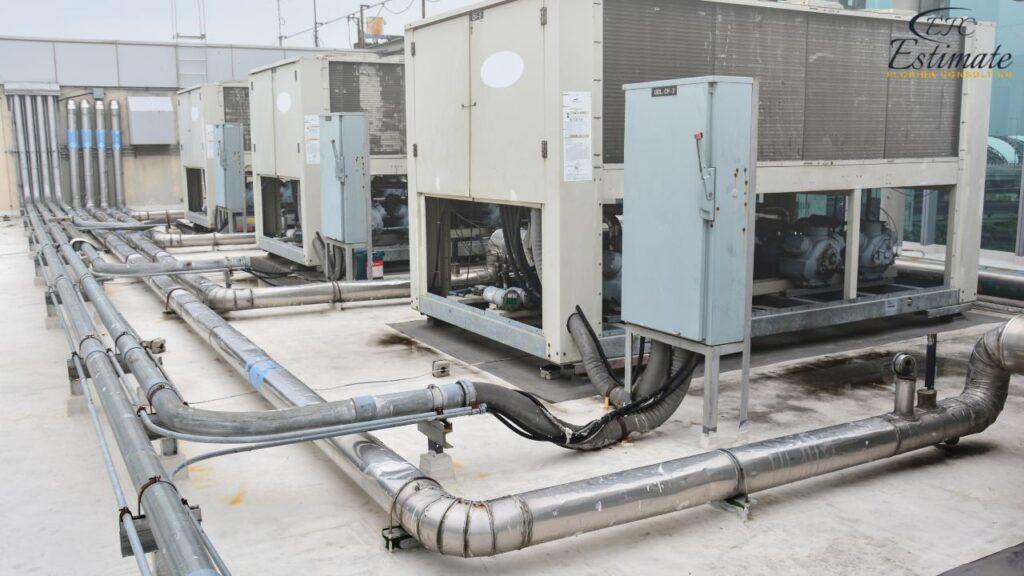
- Clarify any ambiguities or uncertainties in the scope to ensure accurate estimation.
Resource Identification
- Source material costs from local suppliers in Palm Beach Gardens, considering factors like quality, availability, and delivery times.
- Determine labor rates based on prevailing wages in the region, factoring in skill levels and experience.
Cost Calculation
- Utilize specialized software tools to calculate costs based on gathered data, incorporating factors such as material quantities, labor hours, and overhead expenses.
- Apply industry-standard formulas and methodologies to ensure accuracy in cost estimation.
Review and Validation
- Conduct a thorough review of the cost estimates to identify any discrepancies or errors.
- Validate the estimates against historical data, industry benchmarks, and comparable projects to ensure reliability.
Are You Looking For?
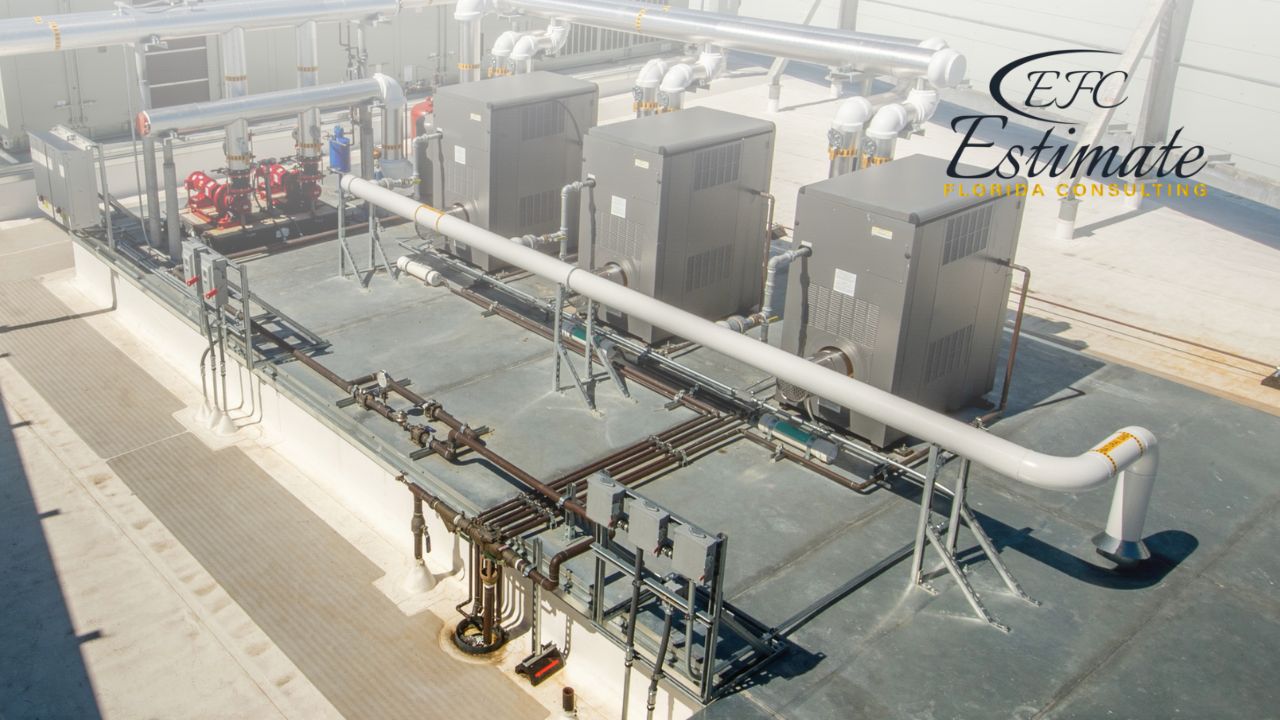
Fully Insured License Hire Subcontractor For Mechanical Work
Hire Contractor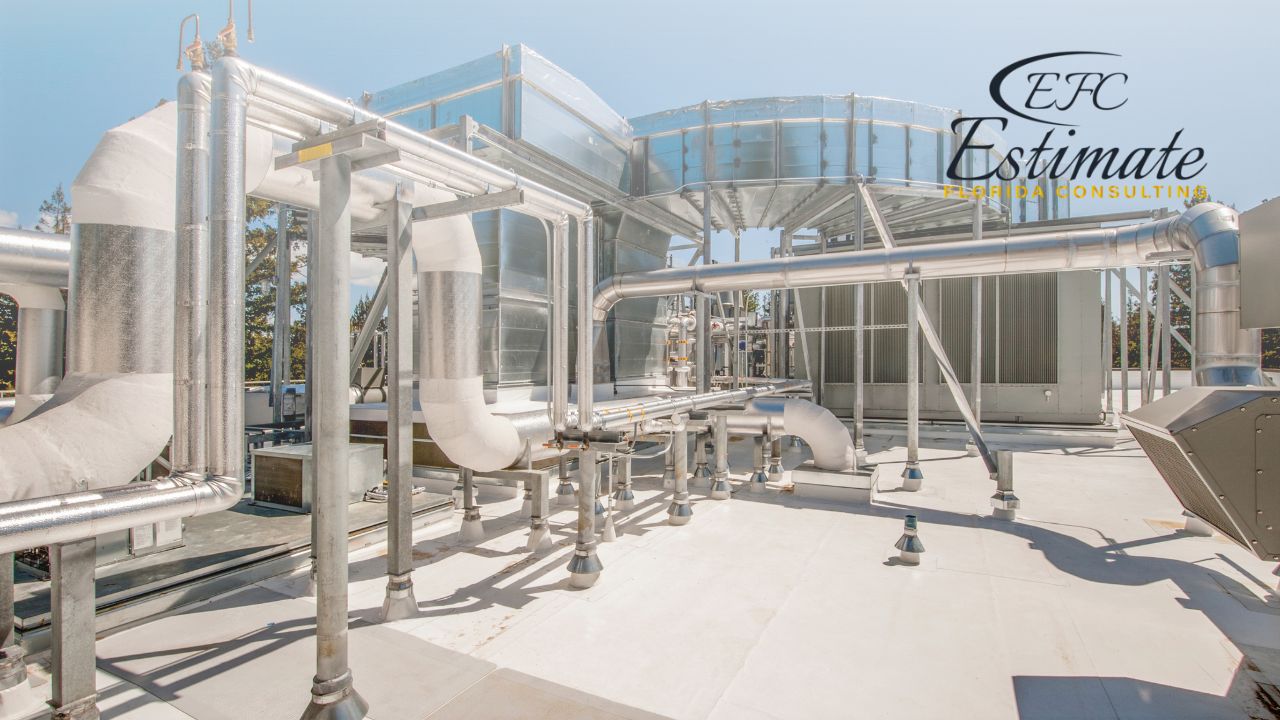
Make Informed Design Decisions Showcase Your Design Ideas
Get RenderingCall Us To Discuss More at 561-530-2845
Presentation and Approval
- Present the finalized cost estimates to stakeholders, including clients, project managers, and decision-makers.
- Clearly communicate the assumptions, methodologies, and potential risks associated with the estimates.
- Address any questions or concerns raised by stakeholders and obtain approval for the estimated costs before proceeding with the project.
Conclusion
The Mechanical Cost Estimator project in Palm Beach Gardens has demonstrated the crucial role of accurate cost estimation in the successful execution of mechanical projects. Through meticulous gathering of project specifications, diligent identification of resources, and utilization of specialized software tools, the estimation process has been streamlined and optimized. By ensuring the accuracy and reliability of cost calculations, this project contributes to better decision-making, budget planning, and risk management for stakeholders involved. Moreover, the emphasis on thorough review and validation underscores the commitment to delivering high-quality estimates that align with industry standards and best practices. Moving forward, the lessons learned from this project will continue to inform and enhance future cost estimation endeavors, driving efficiency, transparency, and ultimately, project success in the Palm Beach Gardens region.
Choose Your Trade & Get a Sample Project
FAQs
A Mechanical Cost Estimator is a professional responsible for calculating the anticipated costs of mechanical projects in Apalachicola. This includes estimating material, labor, and overhead expenses to provide accurate budget projections.
Cost estimation is crucial for effective project planning, budgeting, and resource allocation. It helps stakeholders make informed decisions, mitigate financial risks, and ensure projects are completed within budget constraints in Apalachicola.
Costs are estimated by gathering detailed project specifications, sourcing material and labor rates from local suppliers, and utilizing specialized software tools for calculation. The estimates are then reviewed and validated to ensure accuracy and reliability.
Yes, estimates can change based on factors such as fluctuations in material prices, unforeseen circumstances, and changes in project scope. Regular updates and communication with stakeholders help to adjust estimates as needed to reflect the current project status in Apalachicola.
To ensure accurate cost estimates, provide detailed project specifications, collaborate closely with the estimator to clarify any ambiguities, and regularly review and validate the estimates. Additionally, stay informed about market trends and changes in material and labor costs specific to Palm Beach Gardens.
Process To Get Mechanical Cost Estimate Report
Here I am going to share some steps to get your mechanical cost estimate report.
-
You need to send your plan to us.
You can send us your plan on info@estimatorflorida.com
-
You receive a quote for your project.
Before starting your project, we send you a quote for your service. That quote will have detailed information about your project. Here you will get information about the size, difficulty, complexity and bid date when determining pricing.
-
Get Estimate Report
Our team will takeoff and estimate your project. When we deliver you’ll receive a PDF and an Excel file of your estimate. We can also offer construction lead generation services for the jobs you’d like to pursue further.
Google Reviews
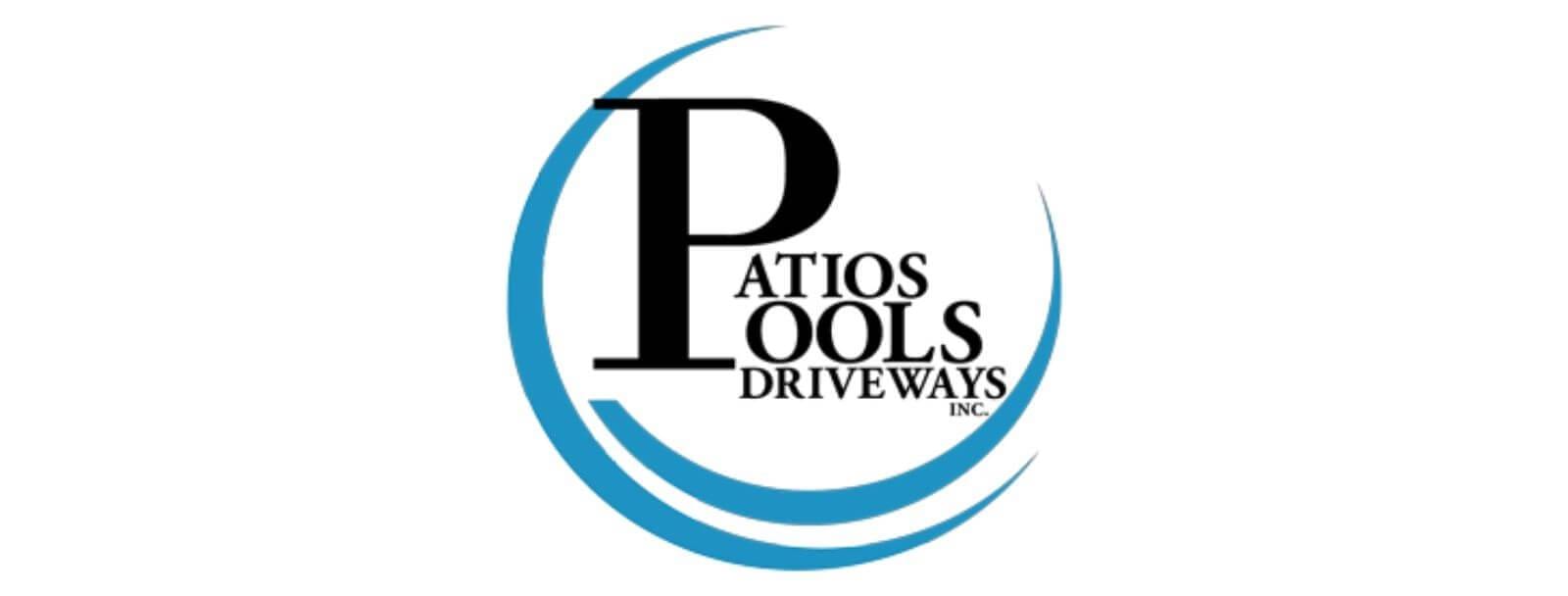
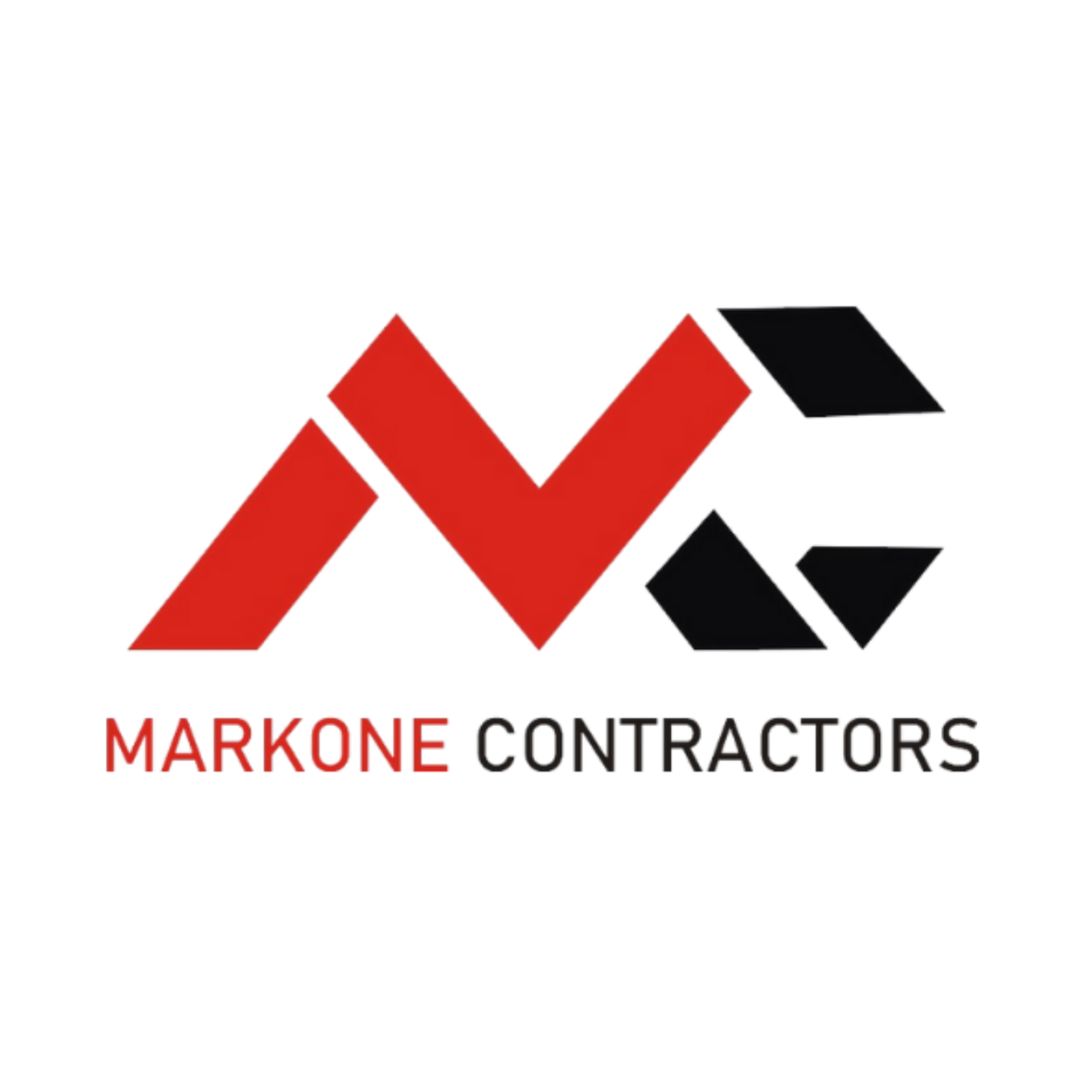
