At Estimate Florida Consulting provides meticulous labor cost estimation services for the Mechanical Cost Estimator project in Neples, with estimates averaging at $90,000. Our experienced team factors in various elements influencing labor costs, such as prevailing wages, project duration, skill requirements, and local labor market conditions. We prioritize accuracy and transparency in our estimates, ensuring clients have a clear understanding of the labor expenses involved in their projects. By leveraging our expertise and industry knowledge, we aim to deliver reliable estimations that enable clients to effectively plan and budget for their mechanical construction endeavors. Trust Estimate Florida Consulting for precise labor cost estimates tailored to the unique requirements of your project in Neples.
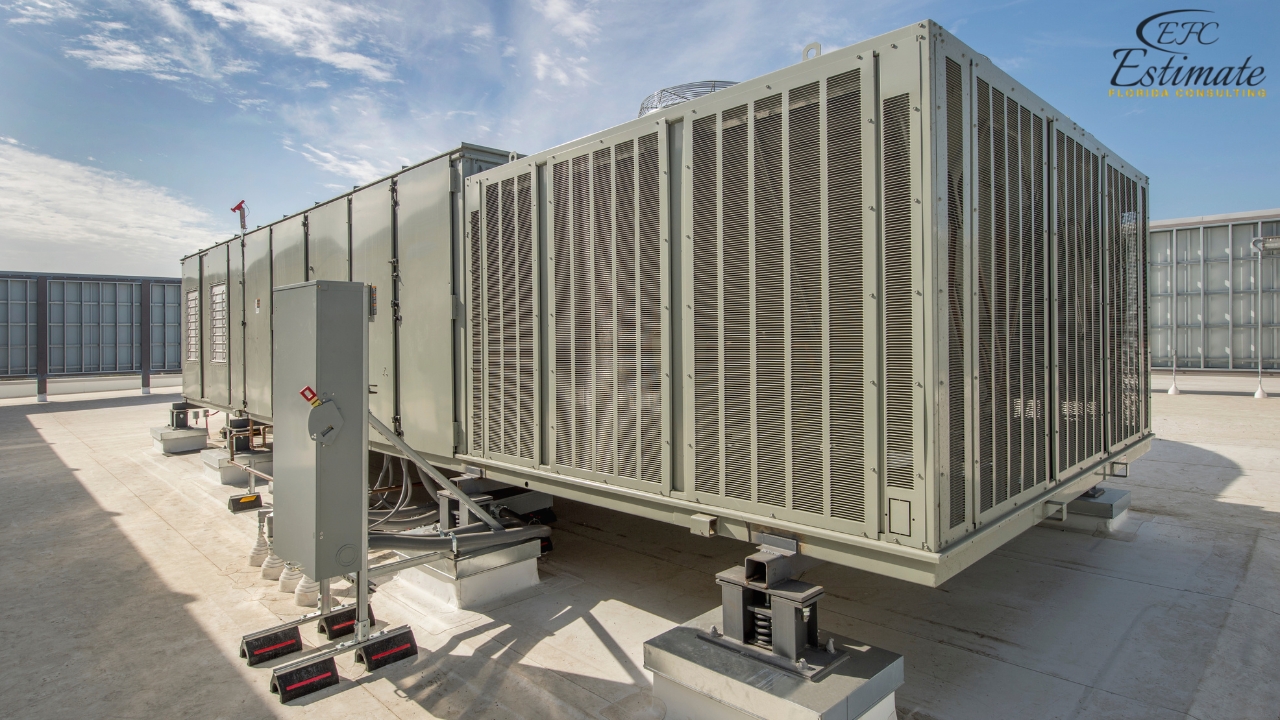