Mechanical Cost Estimator in Destin, FL
At Estimate Florida Consulting offers comprehensive mechanical cost estimation services in Destin. Our estimates range from $65,000 to $200,000, with a cost per square foot falling between $40 and $60. Whether you’re planning a large-scale project or a smaller renovation, our team ensures accurate and reliable estimates to guide your budgeting decisions. With years of experience and expertise in the industry, we take into account various factors to provide precise cost assessments tailored to your specific needs. From initial consultation to project completion, we prioritize transparency and efficiency, striving to deliver unparalleled value to our clients.
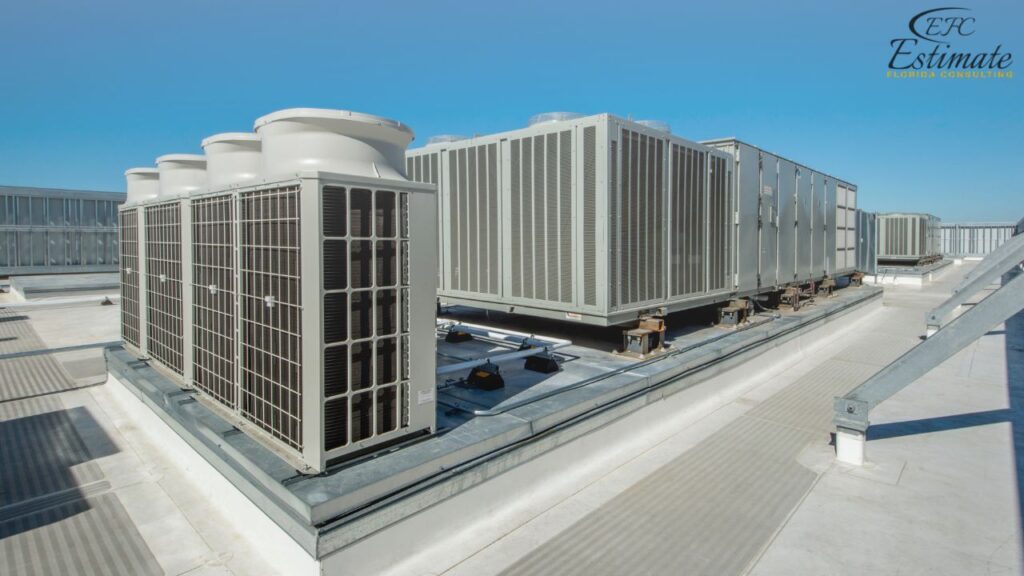
Trust Estimate Florida Consulting for your mechanical cost estimation needs, and let us help you navigate your project with confidence and clarity.
Types of HVAC Units and Their Maintenance Costs
Keeping HVAC systems well-maintained is essential to preserve their efficiency and lifespan. Various types of units require regular upkeep to ensure smooth operation. Air conditioners, heat pumps, furnaces, split systems, hybrid split systems, duct-free mini-splits, and packaged heating and air conditioning units all come with their own set of maintenance needs. Typical servicing may include activities like coil cleaning, refrigerant level checks, electrical component inspections, and filter replacements.
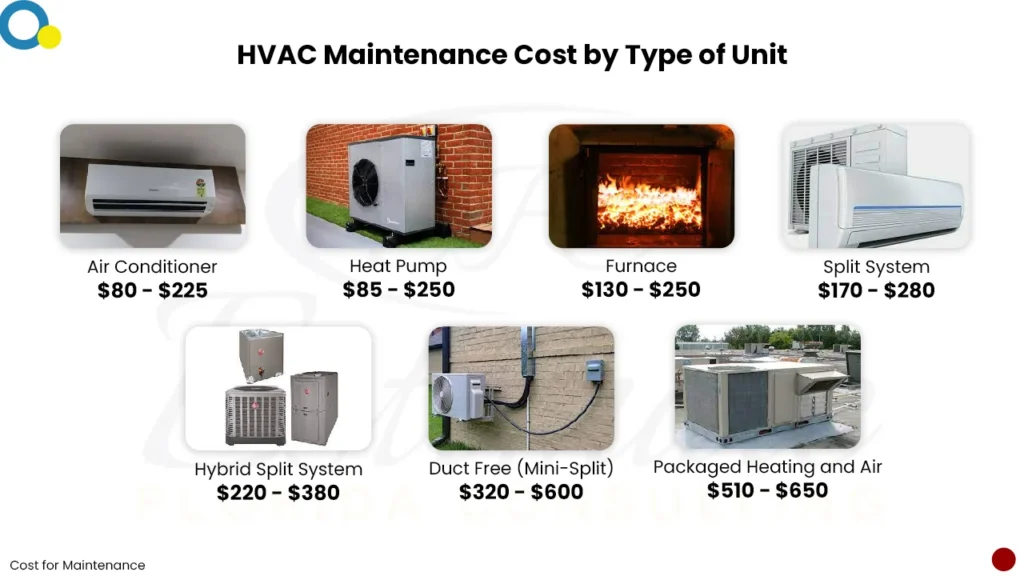
Type of Unit | Cost Range |
Air Conditioner | $80 – $225 |
Heat Pump | $85 – $250 |
Furnace | $130 – $250 |
Split System | $170 – $280 |
Hybrid Split System | $220 – $380 |
Duct-Free (Mini-Split) | $320 – $600 |
Packaged Heat and Air | $510 – $650 |
90% More Chances to Win Projects With Our Estimate!
- Multi-Family Building
- Hotel Building
- Hospital Building
- Warehouse Building
- School & University Building
- High-Rise Building
- Shopping Complex
- Data Center Building
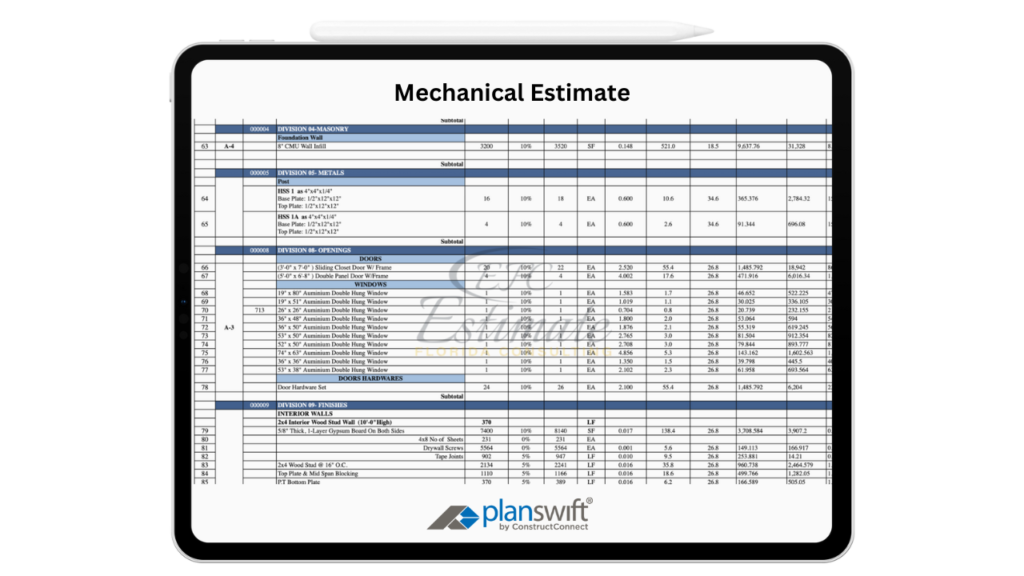
Mechanical Breakdown Cost
Item | Total |
Labor | $120,000 |
Materials | $50,000 |
Equipment | $20,000 |
Contingency | $20,000 |
Cost by Size of Project
The Mechanical Cost Estimator project in Destin this sum is determined by various factors such as labor, materials, equipment, and a contingency budget, reflecting the project’s scale and complexity.
Size of Project | Estimated Cost Range |
Small-scale | $65,000 – $110,000 |
Large-scale | $150,000 – $200,000 |
Get 5 New Leads in the Next 7 Days With Our System
- Multi-Family Building
- Hotel Building
- Hospital Building
- Warehouse Building
- High-Rise Building
- Shopping Complex
Different Types of Mechanical
Mechanical systems are the backbone of modern engineering, facilitating the conversion of energy into useful work across various applications. Among the plethora of mechanical systems, we delve into seven distinct types, each with its unique principles and functionalities. From the intricate workings of gears to the powerful thrust of jet engines, let’s embark on a journey through the fascinating realm of mechanical engineering.
Gears
Gears are omnipresent in machinery, serving as the quintessential components for transmitting motion and power. Whether in a clock, a car transmission, or industrial machinery, gears play a pivotal role. The meshing of toothed wheels allows for the transformation of rotational motion, altering speed, torque, and direction. With various types such as spur gears, bevel gears, and helical gears, engineers can tailor designs to meet specific requirements, ensuring optimal performance and efficiency.
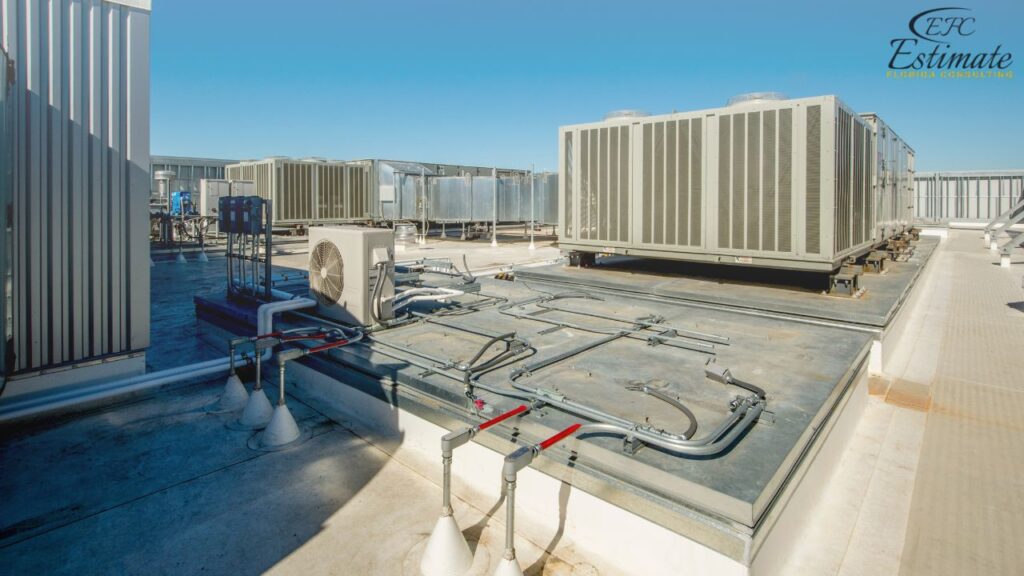
CAMs (Cam Mechanisms)
CAMs are ingenious devices used to impart controlled motion to other components. They consist of specially shaped profiles mounted on shafts, which interact with followers to produce desired movements. CAM systems find applications in engines, automation, and manufacturing processes, enabling precise timing, intermittent motion, and complex sequences. From the straightforward operation of a piston engine’s valve train to the intricate motions of automated machinery, CAMs showcase the elegance of mechanical design.
Levers
Levers epitomize simplicity and effectiveness in mechanical design. Operating on the principle of torque and balance, levers amplify force or distance, making tasks easier to accomplish. From the basic seesaw to sophisticated industrial machines, levers find myriad applications. They are instrumental in lifting heavy loads, exerting controlled pressure, and achieving mechanical advantage. Understanding the interplay between effort, load, and fulcrum positions allows engineers to harness the power of levers across diverse fields.
Download Template For Mechanical Project Breakdown
- Materials list updated to the zip code
- Fast delivery
- Data base of general contractors and sub-contractors
- Local estimators
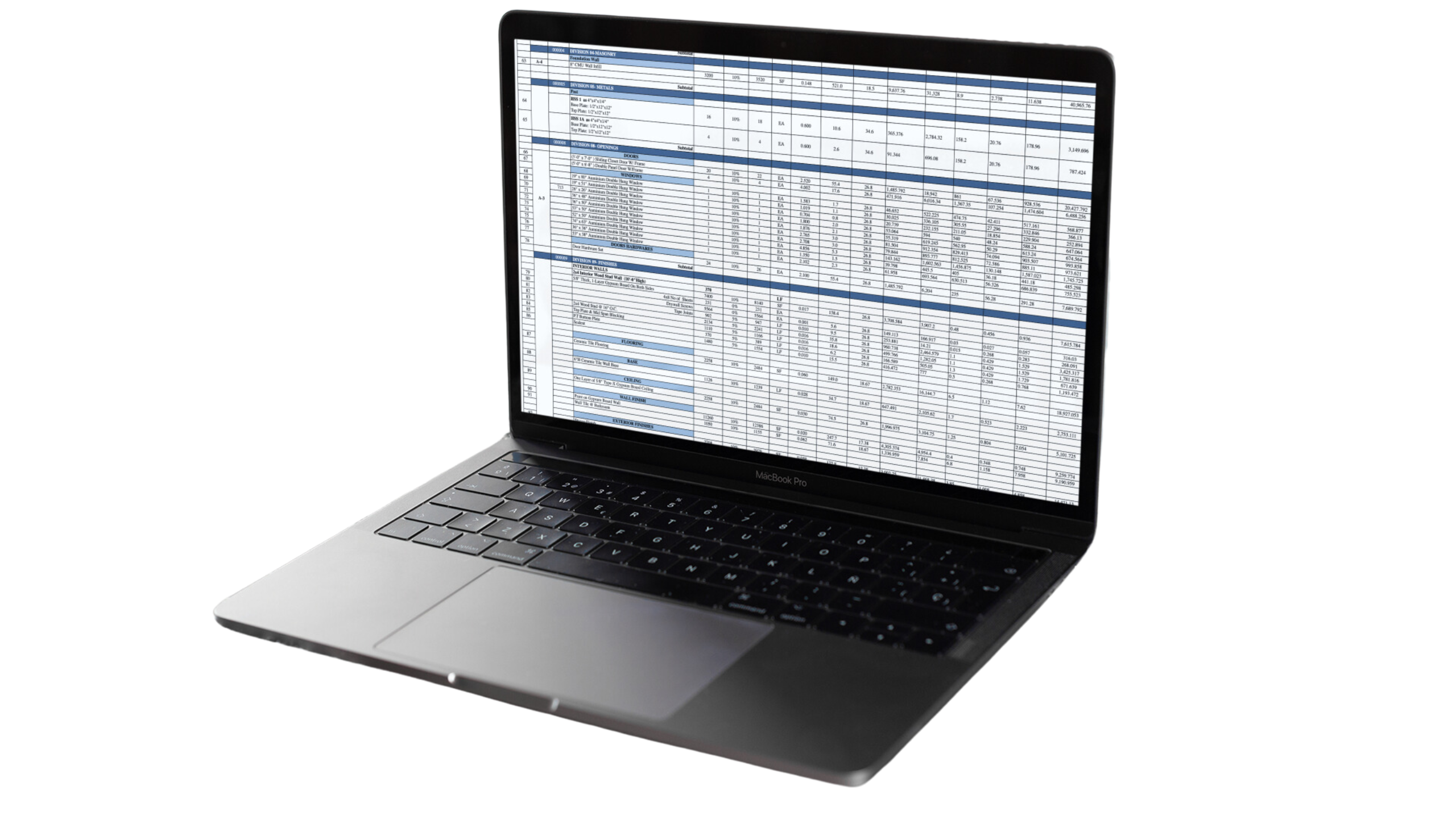
V-Belts
V-Belts are flexible power transmission elements commonly used in machinery to transfer rotational motion between shafts. Their V-shaped cross-section ensures efficient grip and reduced slipping, enabling reliable power transfer in various applications such as industrial equipment, automobiles, and HVAC systems. V-belts offer advantages including quiet operation, shock absorption, and ease of installation, making them indispensable components in mechanical systems requiring smooth and reliable power transmission.
Friction Wheels
Friction wheels harness the force of friction to transmit motion and control speed in mechanical systems. Consisting of a driven wheel pressed against a surface, they provide traction and stability, particularly in applications such as conveyor systems, escalators, and automotive transmissions. By adjusting the pressure between the wheel and the surface, engineers can modulate speed and torque, ensuring optimal performance and safety in diverse operating conditions.
Hydraulic Excavators
Hydraulic excavators epitomize the synergy between mechanical and fluid power systems. These versatile machines utilize hydraulic principles to perform a myriad of tasks, from digging trenches to lifting heavy loads. Hydraulic excavators leverage the incompressibility of hydraulic fluids to transmit force efficiently, enabling precise control and high power-to-weight ratios. With their ability to adapt to various attachments and terrain conditions, hydraulic excavators are indispensable in construction, mining, and earthmoving operations worldwide.
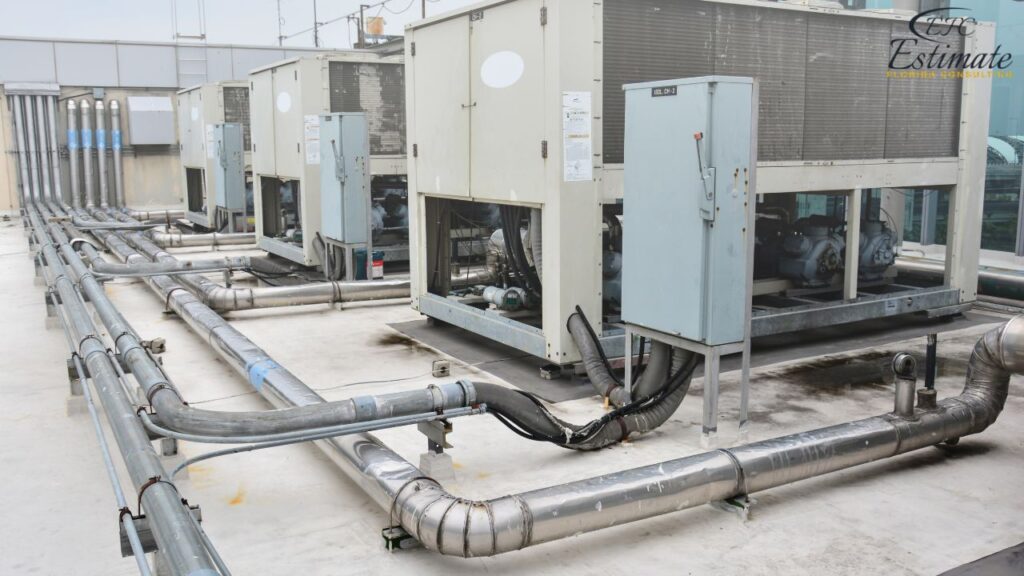
Jet Engines
Jet engines represent the pinnacle of aerospace engineering, propelling aircraft with extraordinary speed and efficiency. These marvels of engineering operate on the principles of thermodynamics and fluid dynamics, compressing incoming air, mixing it with fuel, and igniting the mixture to produce thrust. From turbojets to turbofans, jet engines come in various configurations, each optimized for specific performance characteristics such as speed, altitude, and fuel efficiency. Their relentless pursuit of higher performance and reliability continues to drive advancements in aerospace technology, shaping the future of air travel and exploration.
Mechanical Types | Installation Cost (Per Installation) |
Gears | $400 – $700 |
CAMs (Cam Mechanisms) | $550 – $850 |
Levers | $100 – $205 |
V-Belts | $52 – $126 |
Friction Wheels | $250 – $300 |
Hydraulic Excavators | $100 – $300 |
Jet Engines | $380 – $747 |
Business Finance Loan
Find out if you're pre-qualified in seconds
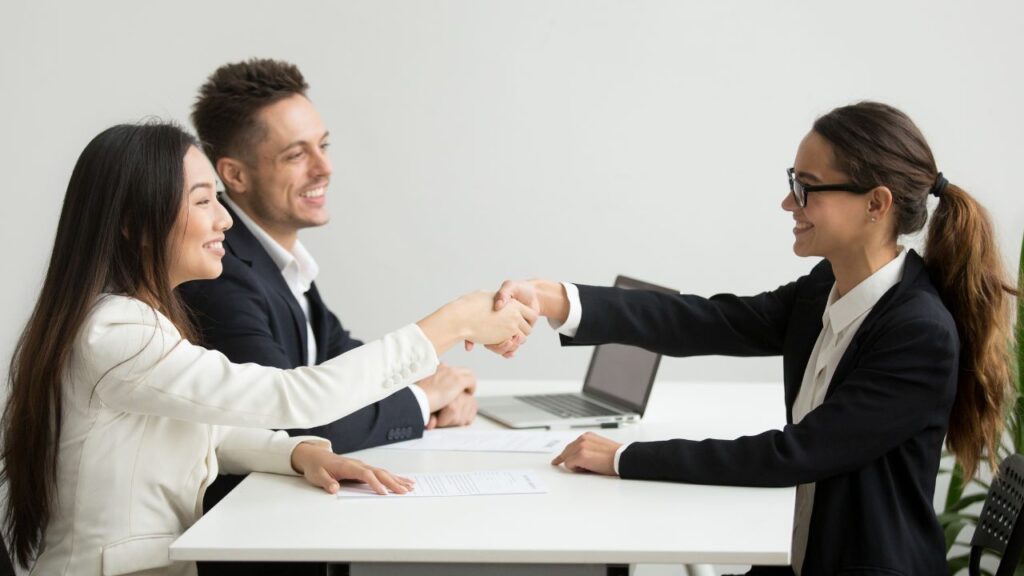
Get Prequalified Now
IMPORTANT: Make sure the email and phone number you enter are correct. We will email and text you a link to get started.
Cost to Repair Ductwork by Material
There exist various types of ductwork, ranging from economical, flexible, non-metallic options to premium sheet metal variants. Each type features distinct designs and materials, with repair costs varying accordingly. Hence, the type of duct you have can significantly impact the expenses of repairs. Below outlines the primary duct types alongside their average repair costs for a standard 30 linear feet section of ductwork.
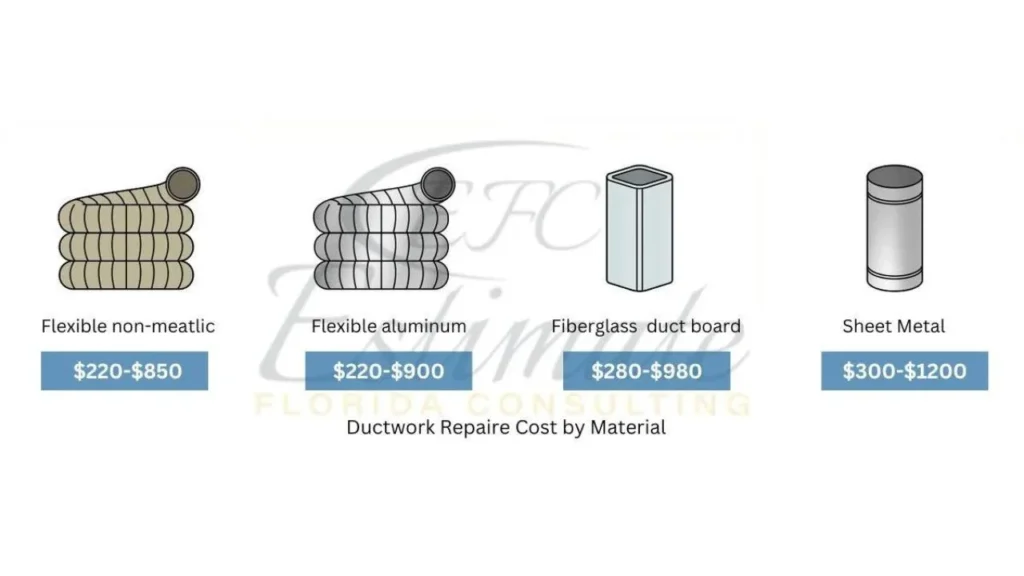
Duct Material | Repair Cost |
Flexible Non-Metallic | $220 – $850 |
Flexible Aluminum | $220 – $900 |
Fiberglass Duct Board | $280 – $980 |
Sheet Metal | $300 – $1200 |
Estimate Your Project With Us
Factors Influencing Mechanical
In developing a Mechanical Cost Estimator project in Destin, several factors uniquely influence its success. Firstly, understanding the local market dynamics and labor costs in Destin is paramount, as they directly impact project budgets. Additionally, considering the specific regulatory requirements and building codes prevalent in Destin ensures compliance and mitigates potential delays and penalties. Moreover, the availability and cost of materials, as well as subcontractor rates in the region, must be thoroughly assessed to provide accurate estimates. Furthermore, incorporating factors such as project scope, complexity, and timeline constraints is essential for precise cost projections. By meticulously analyzing these factors within the context of Destin mechanical construction landscape, the Mechanical Cost Estimator project can effectively deliver reliable estimates, fostering client trust and project success.
Project Objective
The primary objective of the Mechanical Cost Estimator project in Destin is to streamline and enhance the process of estimating costs for mechanical construction projects in the region. By developing a comprehensive and accurate cost estimation tool tailored specifically to Destin unique market conditions, the project aims to provide stakeholders with reliable and transparent estimates. The tool will incorporate factors such as local labor rates, material costs, regulatory requirements, and project specifications to generate precise projections. Additionally, the project seeks to improve efficiency by automating repetitive tasks and integrating data analytics capabilities to analyze historical project data. Ultimately, the Mechanical Cost Estimator project aims to empower decision-makers with the information they need to make informed choices, optimize project budgets, and ensure successful outcomes for mechanical construction endeavors in Destin.
Key Components and Methodology
The Mechanical Cost Estimator project in Destin encompasses several key components and a methodological approach to ensure its effectiveness. Firstly, it involves gathering comprehensive data on local market conditions, including labor rates, material costs, and regulatory requirements specific to Destin. This data serves as the foundation for the development of the cost estimation tool. Secondly, the project focuses on designing an intuitive user interface that allows stakeholders to input project parameters easily and obtain accurate estimates promptly.
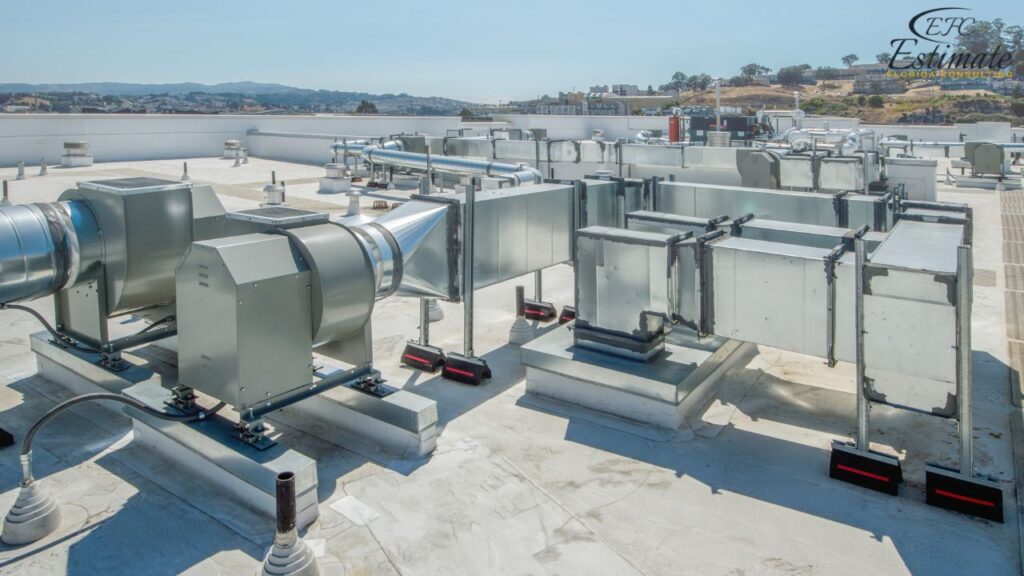
Additionally, the methodology involves incorporating advanced algorithms and data analytics techniques to analyze historical project data and identify trends, helping to refine the accuracy of cost projections over time. Furthermore, rigorous testing and validation procedures are implemented to ensure the reliability and robustness of the estimator tool before its deployment. By integrating these key components and methodologies, the Mechanical Cost Estimator project aims to deliver a comprehensive and dependable solution to meet the needs of mechanical construction projects in Destin.
Factors Affecting Cost Estimates
Factors affecting cost estimates for the Mechanical Cost Estimator project in Destin include local labor rates, material costs, regulatory requirements, project scope, complexity, and timeline constraints, all of which influence the accuracy and reliability of cost projections.
Labor Cost
Estimate Florida Consulting, specializing in estimating services, offers a meticulous evaluation of the labor cost for the Mechanical Cost Estimator project in Destin. Taking into account local labor rates, regulatory demands, and project intricacies, our estimate reflects a comprehensive understanding of the region’s mechanical construction landscape. With a projected cost of $120,000, our assessment ensures transparency and accuracy, facilitating informed decision-making for stakeholders. By leveraging our expertise and methodology, we aim to provide invaluable insights that optimize project budgets and promote successful outcomes in Destin mechanical construction endeavors.
We Provide Manual Estimate!
We provide accurate pricing for the ZIP code of your project.
Turnaround time is 1-2 days.
Win More Projects With Us
Technology and Innovation
Labor Category | Cost |
Skilled Worker | $60,000 |
Supervisor | $40,000 |
Miscellaneous | $10,000 |
Contigency | $10,000 |
Materials Cost
At Estimate Florida Consulting provides comprehensive services for the Mechanical Cost Estimator project in Destin, with a meticulous breakdown of expenses. The materials cost, estimated at $50,000, encompasses various components crucial for the project’s execution. Our thorough assessment ensures accuracy in budget allocation, allowing for seamless planning and execution. By meticulously evaluating material requirements and associated costs, we optimize resource utilization while adhering to quality standards. With our expertise, clients can confidently navigate the intricacies of project management, ensuring cost-effectiveness and timely completion. Estimate Florida Consulting prioritizes transparency and precision in cost estimation, fostering trust and reliability in every project undertaken.
Mechanical Components | Cost |
HVAC System | $15,000 |
Piping | $8,000 |
Ductwork | $7,000 |
Plumbing Fixtures | $5,000 |
Ventilation System | $6,000 |
Other Mechanical | $9,000 |
Overview of Mechanical Components in Construction Projects
Mechanical systems are integral parts of construction projects, ensuring functionality, comfort, and safety within buildings. Among these systems, HVAC (Heating, Ventilation, and Air Conditioning), piping, ductwork, plumbing fixtures, ventilation systems, and various other mechanical components play crucial roles. Let’s delve into each of these components:
HVAC System
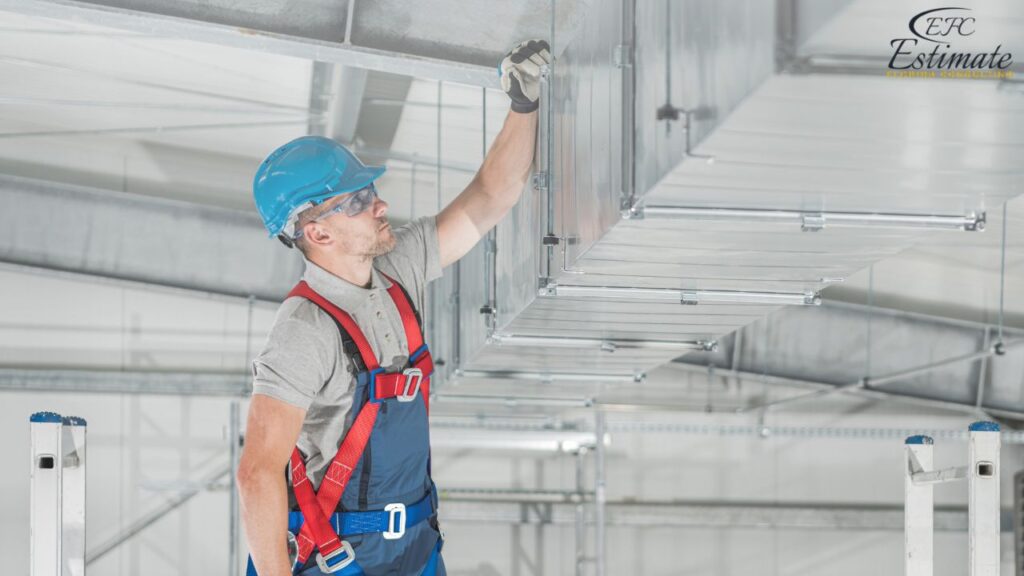
HVAC systems regulate indoor environmental conditions, including temperature, humidity, and air quality. They encompass heating, cooling, and ventilation systems. Heating is typically achieved through furnaces, boilers, or heat pumps, while cooling is facilitated by air conditioners or refrigeration systems. Ventilation ensures adequate air circulation, preventing the buildup of pollutants and maintaining freshness indoors.
Piping
Piping systems transport fluids, such as water, gas, or chemicals, within buildings or across sites. These systems comprise pipes, fittings, valves, and other accessories. Piping networks are designed to withstand varying pressures and temperatures, ensuring efficient and safe conveyance of fluids for heating, cooling, sanitation, or industrial processes.
- Multi-Family Building
- School & University
- Hospital Building
- Warehouse Building
- Hotel Building
- High-Rise Building
Ductwork
Ductwork refers to a network of channels used for conveying air throughout a building. These channels distribute conditioned air from HVAC systems to different spaces and return air to be reheated or cooled. Ductwork systems may include supply ducts, return ducts, and exhaust ducts, along with dampers, grilles, and diffusers to regulate airflow and distribute air evenly.
Plumbing Fixtures
Plumbing fixtures encompass a variety of devices and appliances used for the distribution and disposal of water within buildings. This includes sinks, faucets, toilets, showers, bathtubs, and water heaters. Plumbing fixtures are essential for maintaining hygiene, sanitation, and convenience in residential, commercial, and industrial settings.
Ventilation System
Ventilation systems provide fresh air and remove stale air from enclosed spaces, promoting indoor air quality and occupant comfort. These systems may incorporate mechanical ventilation, natural ventilation, or a combination of both. Components of ventilation systems include fans, ductwork, air filters, and control systems to regulate airflow and pollutant levels.
Other Mechanical Components
Besides the aforementioned systems, various other mechanical components contribute to the functionality and efficiency of buildings. These may include fire suppression systems, elevator systems, escalators, conveyors, generators, and hydraulic systems, among others. Each of these components serves specific purposes, ranging from safety and accessibility to power generation and material handling.
The Price Tag on Mechanical
In Destin, the mechanical cost estimator for a project serves as a vital tool in determining the financial implications of various mechanical components. With every element meticulously priced, from HVAC systems to piping, ductwork, plumbing fixtures, ventilation systems, and other mechanical components, the price tag on mechanical aspects reflects the intricate balance between functionality, efficiency, and budget constraints. Each dollar allocated to these mechanical systems in Destin represents not just a monetary value, but an investment in the comfort, safety, and functionality of the project.
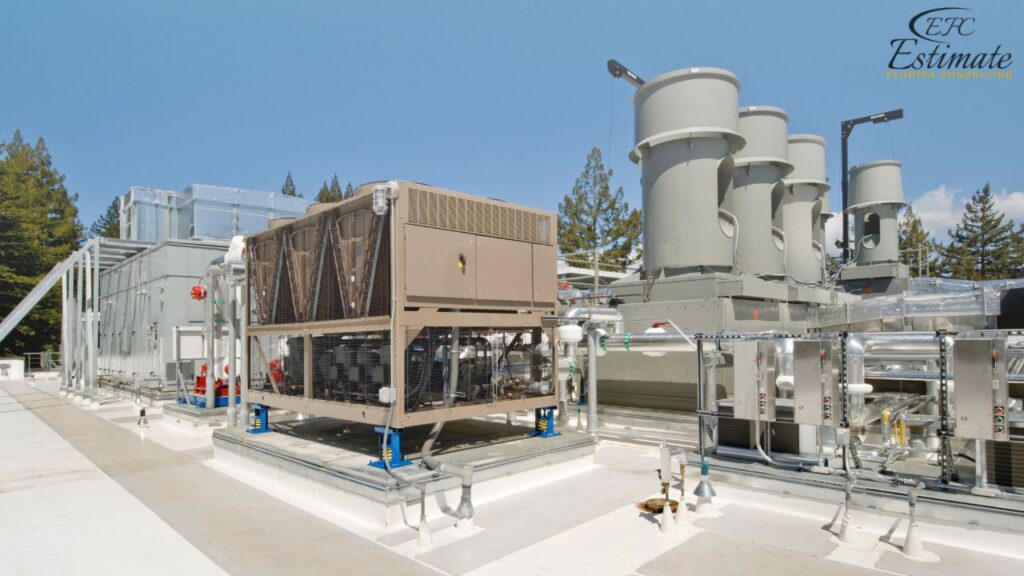
The cost estimator’s role is paramount in ensuring that the project stays within budgetary limits while meeting the necessary standards and requirements, thereby contributing to the overall success and sustainability of the construction endeavor in Destin.
Item | Description | Cost per Sq. Foot |
HVAC System | Heating, Ventilation, & Air Conditioning | $8 – $12 |
Piping | Transporting fluids within buildings | $4 – $7 |
Ductwork | Distribution of conditioned air | $3 – $5 |
Plumbing Fixtures | Water distribution & disposal | $6 – $10 |
Ventilation System | Indoor air quality management | $5 – $8 |
Let us take your project to the next level! Send us your plans, and we’ll provide a detailed estimate with competitive pricing. Our ZIP Code-based approach means better accuracy and a 90% higher chance of winning bids. Get personalized, no-shortcut service every time.
Project Complexity
In Destin, the mechanical cost estimator for a project faces the challenge of navigating through varying degrees of project complexity. Factors such as building size, design intricacy, structural requirements, and technological specifications contribute to the complexity of estimating mechanical costs. Large-scale projects with sophisticated HVAC systems, extensive piping networks, intricate ductwork layouts, and advanced plumbing fixtures demand meticulous assessment and precise costing. Moreover, the integration of energy-efficient solutions, compliance with building codes, and adherence to environmental standards further amplify the complexity. The mechanical cost estimator in Destin must possess a comprehensive understanding of mechanical systems, construction methodologies, and market dynamics to accurately forecast expenses amidst the intricacies of the project. Successfully navigating these complexities ensures that the project’s mechanical components are not only functional and efficient but also economically viable within the context of Destin construction landscape.
Location-specific Factors
In Destin, location-specific factors significantly influence the work of a project’s mechanical cost estimator. Destin geographical location, climate, and local regulations play pivotal roles in determining the cost of mechanical systems. Factors such as extreme weather conditions, humidity levels, and seismic considerations impact the selection and sizing of HVAC systems, ductwork layouts, and plumbing designs. Additionally, Destin market dynamics, including material availability, labor costs, and subcontractor rates, directly influence project budgets. Local building codes and zoning ordinances further shape mechanical cost estimates, requiring compliance with specific standards and guidelines unique to Destin. Thus, the mechanical cost estimator must meticulously analyze these location-specific factors to accurately forecast expenses and ensure the project’s mechanical components are tailored to Destin environmental and regulatory context.
Common Challenges and Solutions
In Destin, common challenges for mechanical cost estimators include fluctuating material prices and labor shortages. Solutions involve conducting thorough market research, establishing strong vendor relationships, and implementing value engineering techniques to optimize costs and mitigate risks.
Fluctuating Material Prices
Rapid changes in material costs can disrupt budget projections.
Solution: Regularly monitor market trends, establish flexible contracts, and consider alternative materials to mitigate price fluctuations.
Labor Shortages
Limited availability of skilled laborers can lead to project delays and increased labor costs.
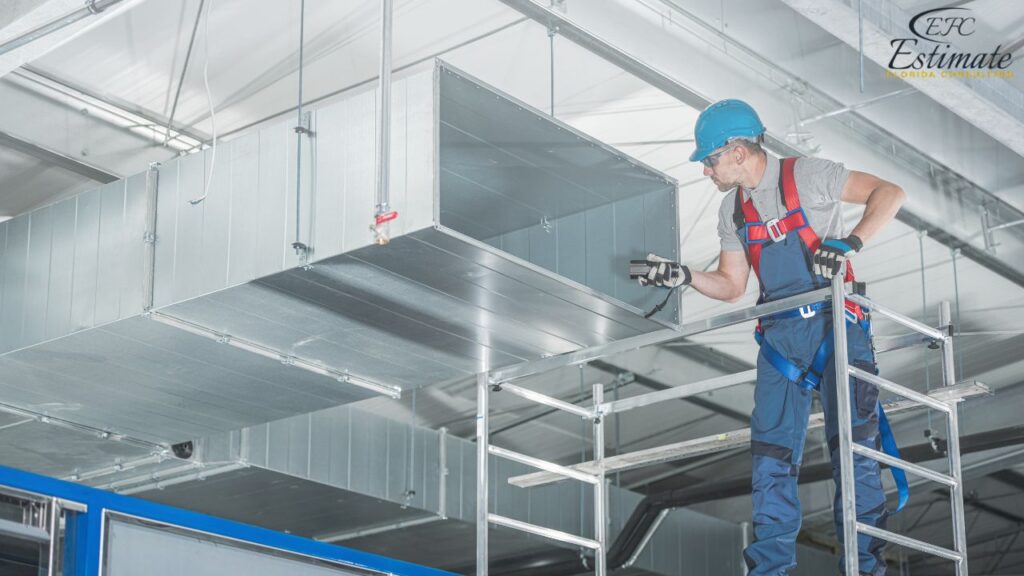
Solution: Collaborate with local trade organizations, invest in workforce development programs, and implement efficient scheduling to optimize labor resources.
Complex Project Specifications
Detailed project requirements may pose challenges in accurately estimating mechanical costs.
Solution: Engage with architects and engineers early in the design phase, conduct thorough cost breakdowns, and utilize specialized software for precise estimations.
Stringent Building Codes
Strict adherence to building codes increases project complexity and costs.
Solution: Stay updated on local regulations, work closely with regulatory authorities, and incorporate compliance measures into the initial project planning stages.
Stringent Building Codes
Strict adherence to building codes increases project complexity and costs.
Solution: Stay updated on local regulations, work closely with regulatory authorities, and incorporate compliance measures into the initial project planning stages.
Need Template For Your Mechanical Business
We provide services for Brochure, Banner, Business Card, Envelope, Invoice, etc.
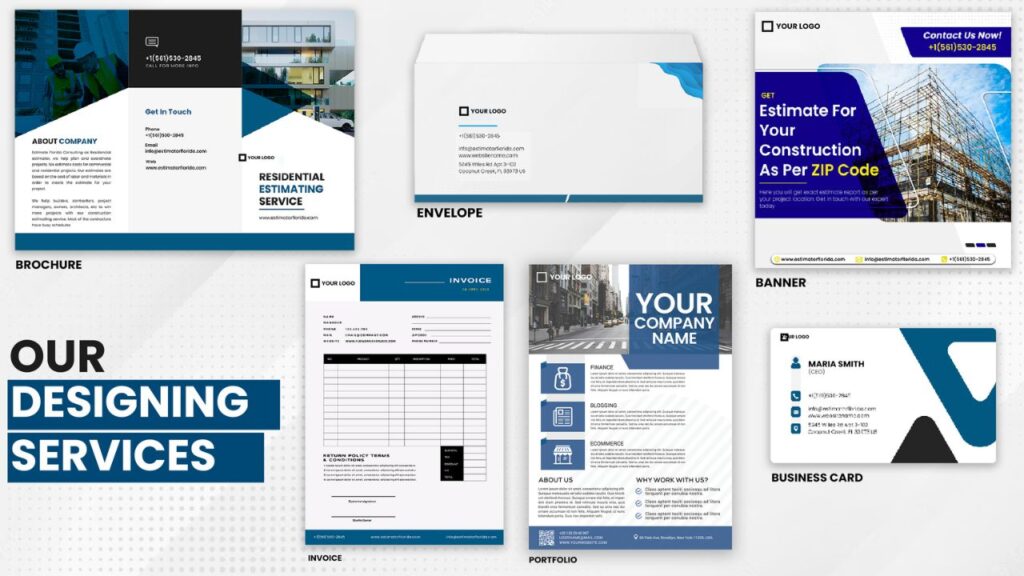
Environmental Regulations
Compliance with environmental standards adds complexity and expense to mechanical systems.
Solution: Incorporate sustainable design practices, utilize energy-efficient technologies, and explore available incentives for green building initiatives.
Supply Chain Disruptions
Disruptions in the supply chain can cause delays and impact project timelines.
Solution: Diversify suppliers, maintain buffer stocks of critical materials, and establish contingency plans to mitigate supply chain risks.
Cost Overruns
Exceeding budget allocations due to unforeseen expenses or misestimations.
Solution: Implement rigorous cost tracking mechanisms, conduct regular budget reviews, and employ value engineering techniques to identify cost-saving opportunities.
Technology Integration Challenges
Integrating complex technological systems within mechanical designs can present technical hurdles.
Solution: Collaborate with technology specialists, conduct thorough system testing, and provide comprehensive training to project teams to ensure seamless integration.
Community Engagement
Addressing community concerns and expectations regarding project impacts and costs.
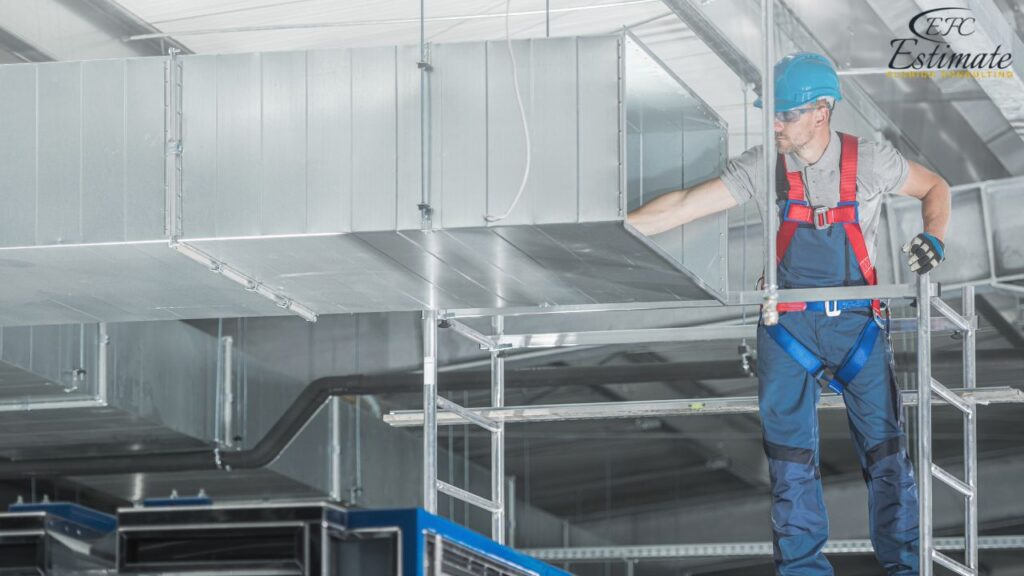
Solution: Foster open communication channels, actively engage with stakeholders, and incorporate community feedback into project planning and execution processes.
Steps in the Mechanical Cost Estimator in Destin
In Destin, mechanical cost estimation involves analyzing project specifications, conducting market research, and collaborating with architects and engineers to develop accurate cost projections. Thorough cost breakdowns and continuous monitoring ensure alignment with budgetary constraints and project objectives.
Project Assessment
The process begins with a comprehensive assessment of project requirements, including scope, design specifications, and regulatory constraints, to establish a clear understanding of the project’s mechanical needs.
Project Assessment
The process begins with a comprehensive assessment of project requirements, including scope, design specifications, and regulatory constraints, to establish a clear understanding of the project’s mechanical needs.
Are You Looking For?
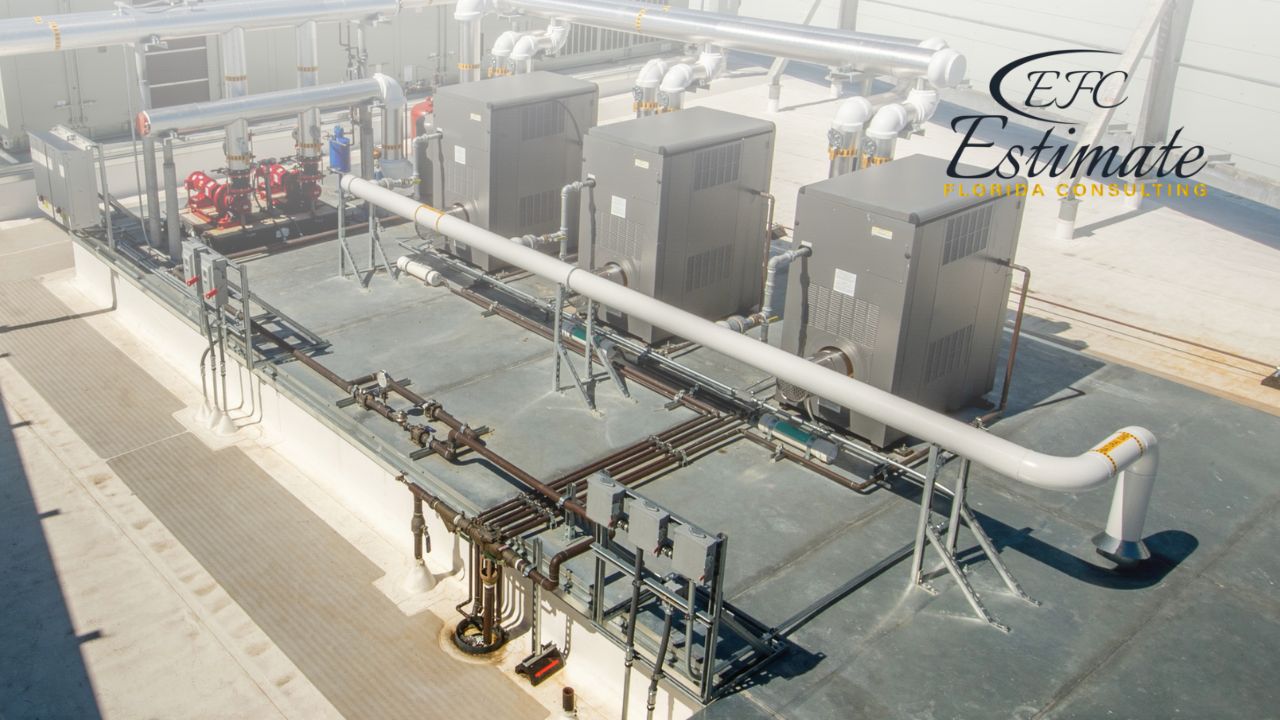
Fully Insured License Hire Sub-Contractor For Mechanical Work
Hire Contractor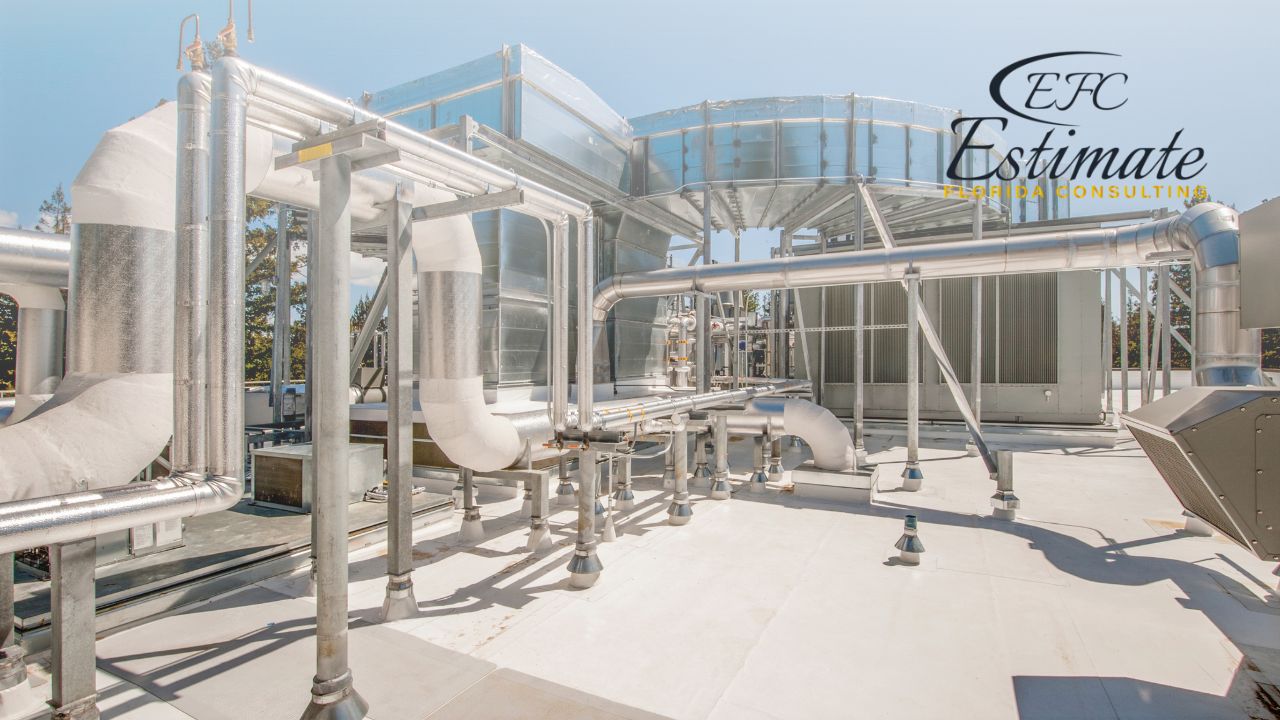
Make Informed Design Decisions Showcase Your Design Ideas
Get RenderingCall Us To Discuss More at 561-530-2845
Cost Breakdown
Breaking down the project into individual components, such as HVAC systems, piping, ductwork, and plumbing fixtures, allows for a detailed analysis of costs associated with each element.
Market Analysis
Conducting a thorough analysis of the local market dynamics, including material availability, labor trends, and subcontractor capabilities, helps in understanding cost trends and potential fluctuations.
Collaboration with Stakeholders
Collaborating with architects, engineers, project managers, and other stakeholders ensures alignment of cost estimates with project goals, design requirements, and quality standards.
Risk Assessment
Identifying potential risks and uncertainties, such as changes in regulations, supply chain disruptions, or unforeseen project delays, allows for proactive risk mitigation strategies to be implemented.
Cost Estimation Software Utilization
Leveraging specialized software tools and platforms for cost estimation streamlines the process, improves accuracy, and facilitates efficient data analysis and reporting.
Value Engineering
Employing value engineering techniques to optimize costs without compromising quality or performance helps in identifying cost-saving opportunities and maximizing project value.
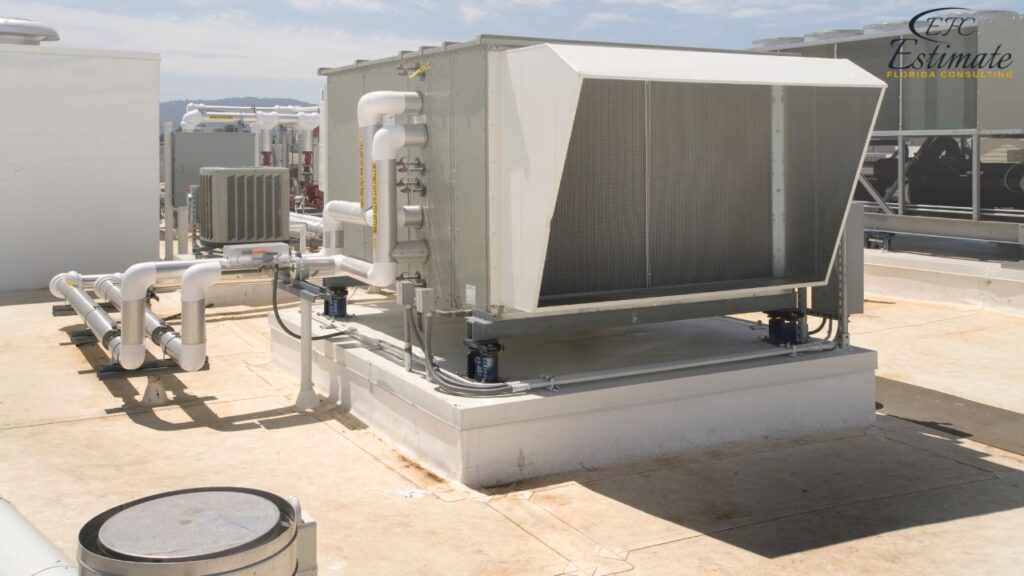
Continuous Monitoring and Adjustment
Continuously monitoring project progress, market conditions, and budgetary constraints enables timely adjustments to cost estimates, ensuring alignment with evolving project requirements.
Documentation and Reporting
Maintaining detailed documentation of cost estimates, assumptions, and methodologies employed, and providing clear, concise reports facilitates transparency, accountability, and effective decision-making throughout the project lifecycle.
Conclusion
The role of the Mechanical Cost Estimator in Destin is indispensable in ensuring the success and efficiency of construction projects. Through meticulous analysis, collaboration with stakeholders, and utilization of advanced tools and methodologies, Mechanical Cost Estimators play a critical role in accurately forecasting and managing project costs. By navigating through challenges such as fluctuating material prices, labor shortages, and complex project specifications, they facilitate informed decision-making and risk mitigation strategies. Moreover, their ability to adapt to location-specific factors, regulatory requirements, and market dynamics ensures that projects in Destin are executed within budgetary constraints while meeting quality standards and achieving desired outcomes. Ultimately, the expertise and dedication of Mechanical Cost Estimators contribute significantly to the sustainable growth and development of the construction industry in Destin.
Choose Your Trade & Get a Sample Project
FAQs
A Mechanical Cost Estimator in Destin assesses project requirements, gathers data on material and labor costs, analyzes market trends, collaborates with stakeholders, and uses specialized software to provide accurate cost estimates for mechanical components of construction projects.
Mechanical Cost Estimators in Bartow determine costs by breaking down projects into individual components, researching material prices, obtaining labor rates, factoring in equipment expenses, subcontractor quotes, and accounting for overhead and profit margins.
Mechanical Cost Estimators in Destin may face challenges such as fluctuating material prices, labor shortages, complex project specifications, stringent building codes, and environmental regulations. However, they employ various strategies such as market analysis, value engineering, and risk assessment to overcome these challenges.
Mechanical Cost Estimators strive to provide accurate cost estimates based on thorough data analysis, market research, and collaboration with industry professionals. While estimates may vary depending on project complexities and unforeseen factors, efforts are made to ensure alignment with project goals and budgetary constraints.
To excel as a Mechanical Cost Estimator in Destin, individuals typically possess a degree in engineering, construction management, or a related field, along with strong analytical skills, attention to detail, proficiency in cost estimation software, and a thorough understanding of mechanical systems and construction practices. Additionally, ongoing professional development and staying updated on industry trends are essential for success in this role.
Process To Get Mechanical Cost Estimate Report
Here I am going to share some steps to get your mechanical cost estimate report.
-
You need to send your plan to us.
You can send us your plan on info@estimatorflorida.com
-
You receive a quote for your project.
Before starting your project, we send you a quote for your service. That quote will have detailed information about your project. Here you will get information about the size, difficulty, complexity and bid date when determining pricing.
-
Get Estimate Report
Our team will takeoff and estimate your project. When we deliver you’ll receive a PDF and an Excel file of your estimate. We can also offer construction lead generation services for the jobs you’d like to pursue further.
Google Reviews
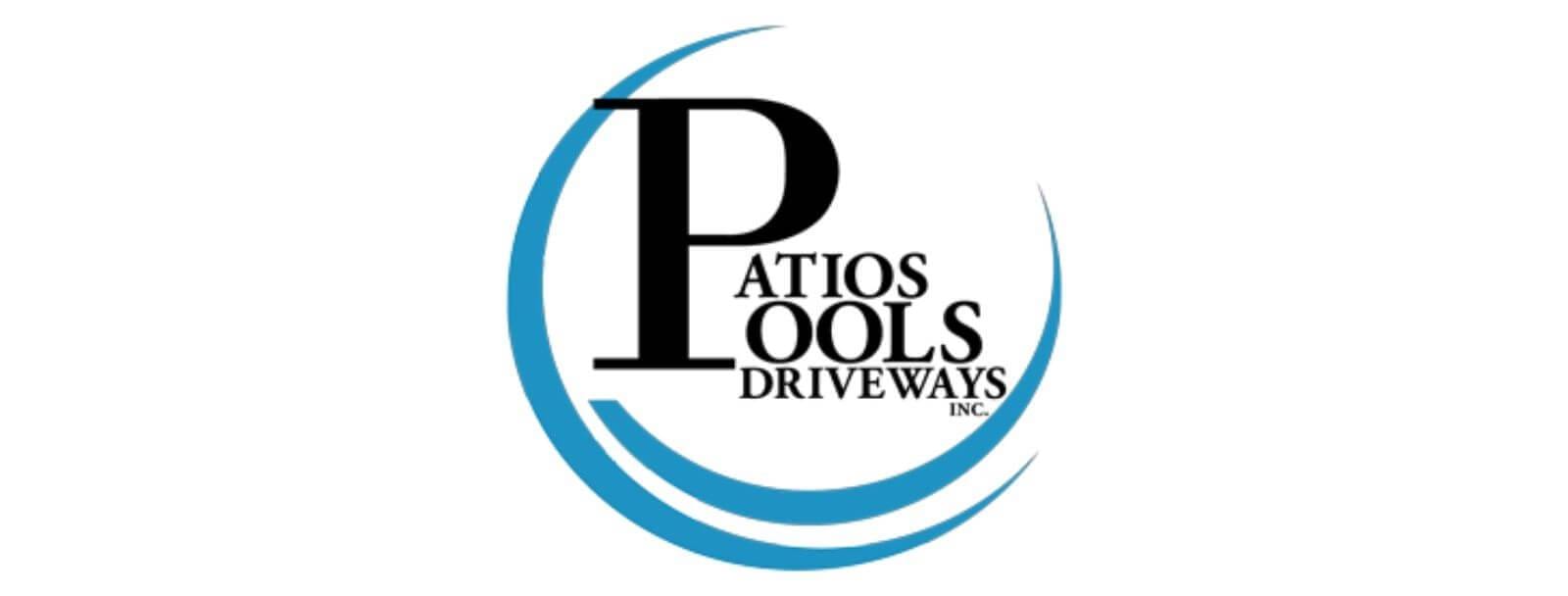
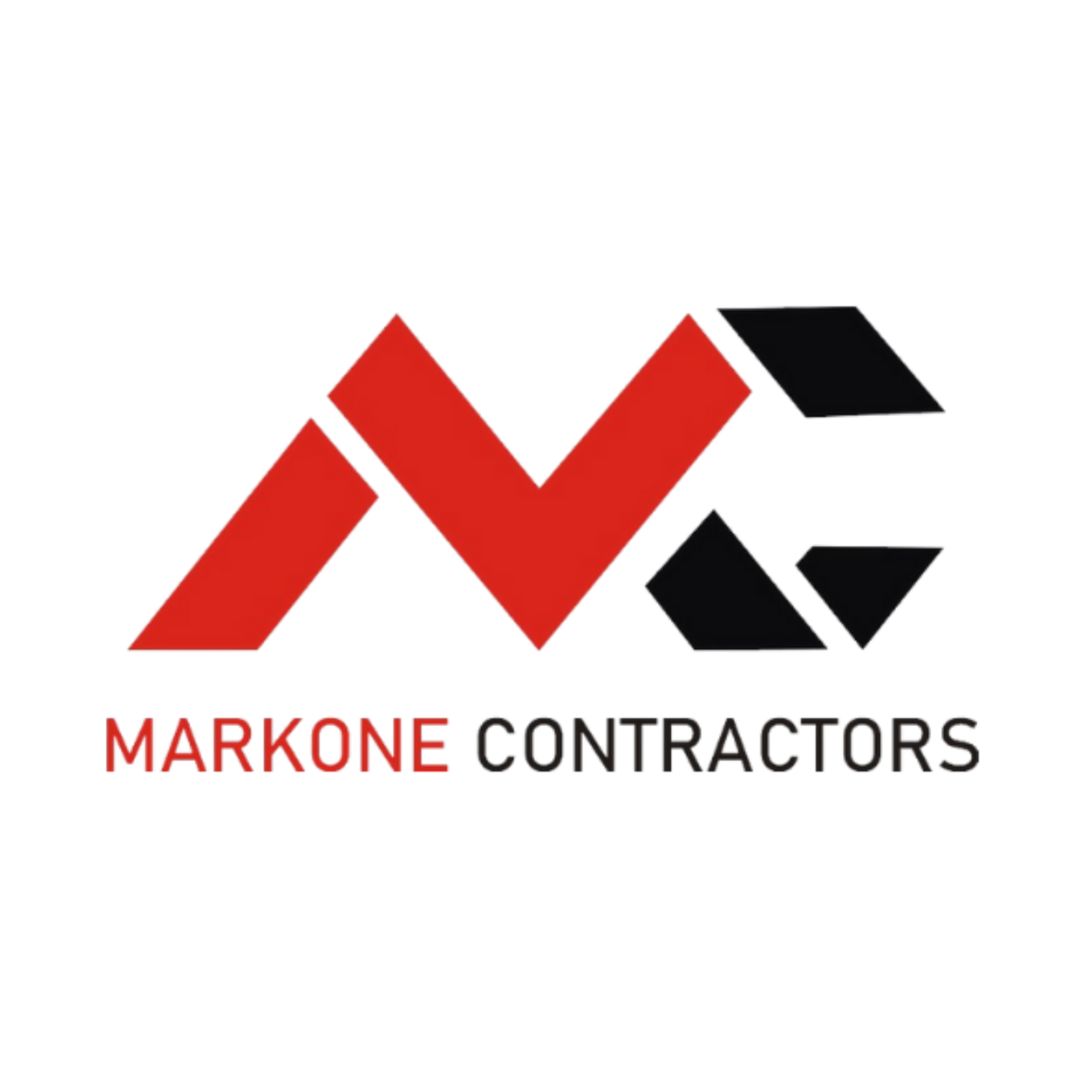
