Lumber Cost Estimator in Boca Raton
Estimate Florida Consulting, based in Boca Raton, provides detailed and thorough lumber cost estimation services for a wide range of residential and commercial projects. Our estimates carefully consider a variety of factors that affect lumber prices, including market trends, the complexities of your project, and the quantity of lumber needed. Generally, in Boca Raton, lumber prices tend to fall between $400 and $1,500 per thousand board feet. However, these costs can fluctuate considerably depending on the type, grade, species, moisture content, and size of the lumber.
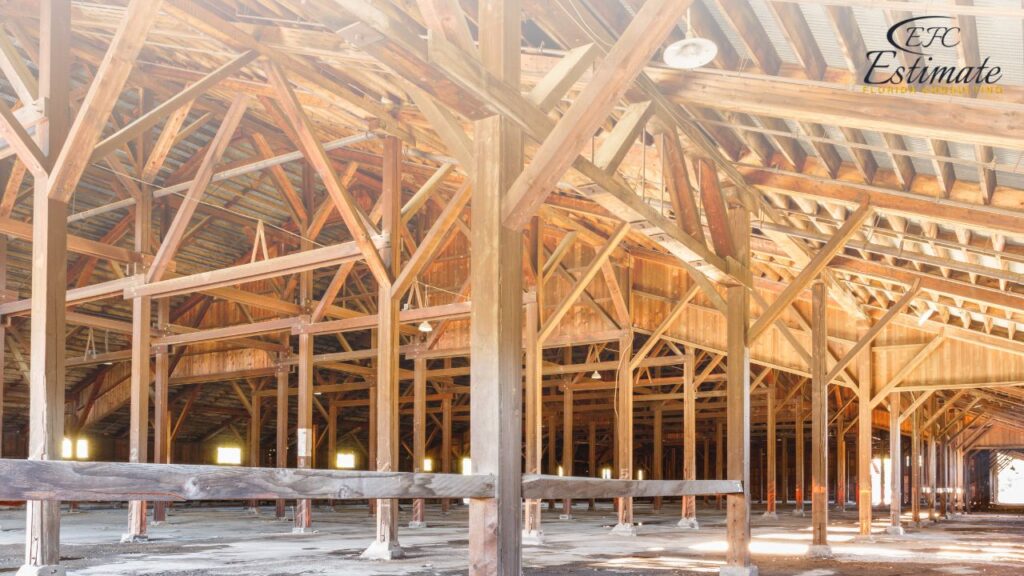
Additionally, the final cost may be influenced by transportation and delivery fees. For accurate and customized lumber cost estimates that meet the specific requirements of your project, get in touch with Estimate Florida Consulting today.
We Work for All Construction Trades
Construction trades encompass a variety of specialized roles, each critical to the successful completion of a project. Skilled tradespeople not only ensure the work is done right but also enhance safety, efficiency, and compliance with local building codes. From the initial groundwork to the final touches, every step requires expertise from dedicated professionals.
Cost to Install Wood Siding Over Existing Siding
As a Lumber Cost Estimator, it’s essential to consider the various factors involved in installing wood siding over existing siding materials rather than starting from scratch. While this approach can save time and resources, it’s crucial for contractors to assess the integrity of the current siding closely. Rotted or damaged siding pieces cannot be covered up with new ones as it may lead to structural issues. Certain materials, like vinyl siding, must be removed before new installations due to their softness and susceptibility to damage if covered over. Understanding which sidings can support wood siding installations helps ensure a smooth and structurally sound transition, ultimately impacting cost estimations for lumber-related projects.
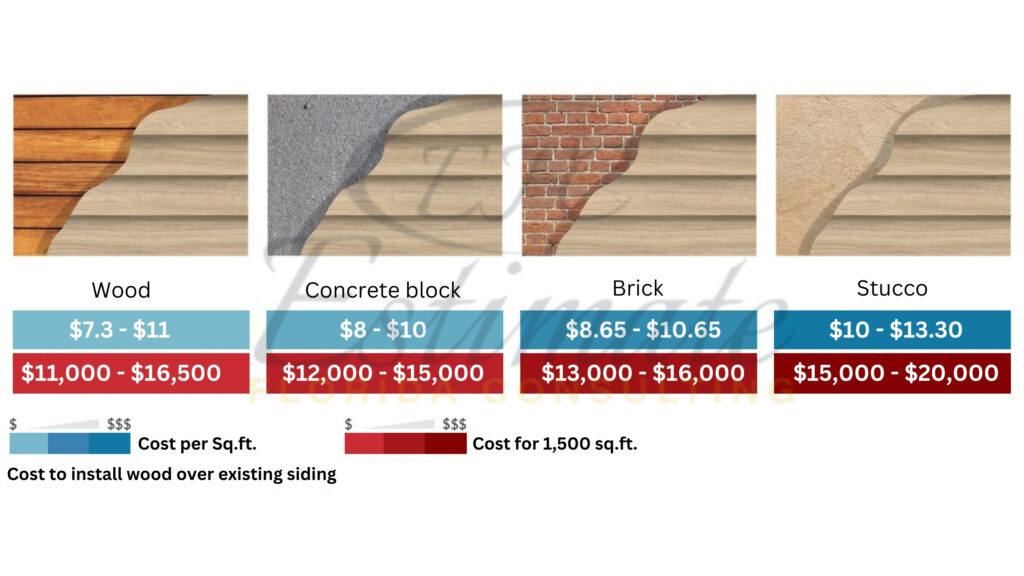
Existing Siding | Cost per Sq.Ft. (Installed) | Cost for 1,500 Sq.Ft. (Installed) |
---|---|---|
Wood | $7.30 – $11 | $11,000 – $16,500 |
Concrete Block | $8 – $10 | $12,000 – $15,000 |
Brick | $8.65 – $10.65 | $13,000 – $16,000 |
Stucco | $10 – $13.30 | $15,000 – $20,000 |
90% More Chances to Win Projects With Our Estimate!
- Multi-Family Building
- Hotel Building
- Hospital Building
- Warehouse Building
- School & University Building
- High-Rise Building
- Shopping Complex
- Data Center Building
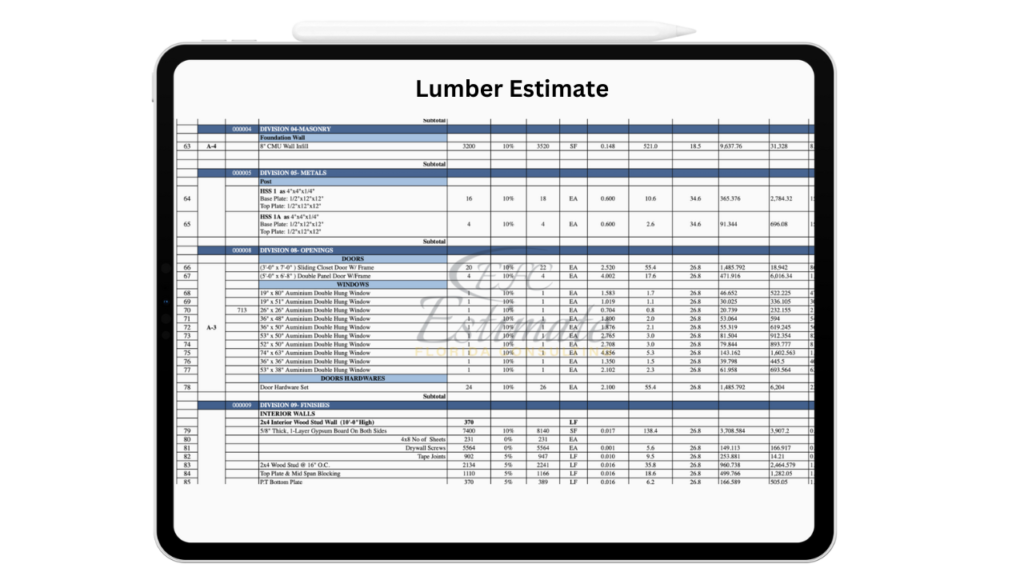
Influences on Lumber Pricing
The cost of lumber is impacted by several dynamic factors that shape pricing and acquisition strategies:
1. Market Dynamics
Lumber prices are highly sensitive to worldwide economic trends, trade policies, and environmental factors. Shifts in supply and demand, along with evolving regulations, can result in significant price volatility. Keeping up-to-date with market conditions and industry predictions is crucial for predicting price movements and reducing the risk of cost fluctuations.
2. Project Specifics
Every construction project has its unique challenges and needs that affect lumber choice and cost. Elements such as the project’s location, building codes, design requirements, and environmental factors determine the type and quantity of lumber required. Projects demanding specialized wood for architectural features, structural elements, or sustainability objectives might face increased material costs.
3. Volume Requirements:
The size of the project plays a key role in lumber procurement tactics and pricing models. Larger projects often enjoy cost benefits due to bulk purchasing and discounted rates for large orders. On the other hand, smaller projects might encounter higher per-unit costs due to limited buying power and greater transactional expenses. Effective design and planning that optimize material use and minimize waste can help control costs for projects of any scale.
Get 5 New Leads in the Next 7 Days With Our System
- Multi-Family Building
- Hotel Building
- Hospital Building
- Warehouse Building
- High-Rise Building
- Shopping Complex
4. Supply Chain Dynamics
The effectiveness and stability of the lumber supply chain also affect cost and availability. Elements like transportation expenses, logistical challenges, and inventory management can impact the overall pricing of lumber. Moreover, regional variations in lumber production, processing capabilities, and distribution networks can lead to price differences in different areas. Implementing proactive supply chain strategies, forming strategic sourcing partnerships, and diversifying suppliers can reduce risks and uncertainties in lumber procurement.
Wood Trim Cost by Style
it’s essential to recognize the diverse array of styles available in wood trim, catering to various architectural preferences and home styles. From simple and modern to historical and intricate designs, there’s a trim style to accentuate any home’s unique architecture. These styles are offered in both paint-grade and stain-grade options, available in a range of sizes and materials. Homeowners have the flexibility to choose from dark or light wood tones or opt for trim that can be painted to match the color scheme of their choice. By understanding the versatility of trim styles and materials, accurate cost estimations can be provided to meet the needs and preferences of homeowners for their lumber-related projects.
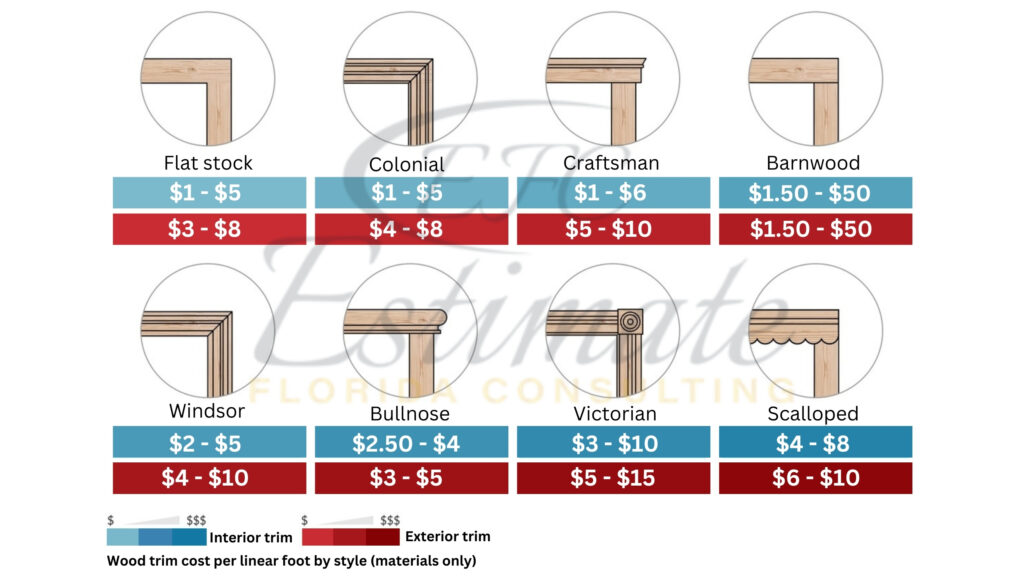
Style | Interior Trim Cost per Linear Foot (Materials Only) | Exterior Trim Cost per Linear Foot (Materials Only) |
---|---|---|
Flat Stock | $1 – $5 | $3 – $8 |
Colonial | $1 – $5 | $4 – $8 |
Craftsman | $1 – $6 | $5 – $10 |
Barnwood | $1.50 – $50 | $1.50 – $50 |
Windsor | $2 – $5 | $4 – $10 |
Bullnose | $2.50 – $4 | $3 – $5 |
Victorian | $3 – $10 | $5 – $15 |
Scalloped | $4 – $8 | $6 – $10 |
Download Template For Lumber Project Breakdown
- Materials list updated to the zip code
- Fast delivery
- Data base of general contractors and sub-contractors
- Local estimators
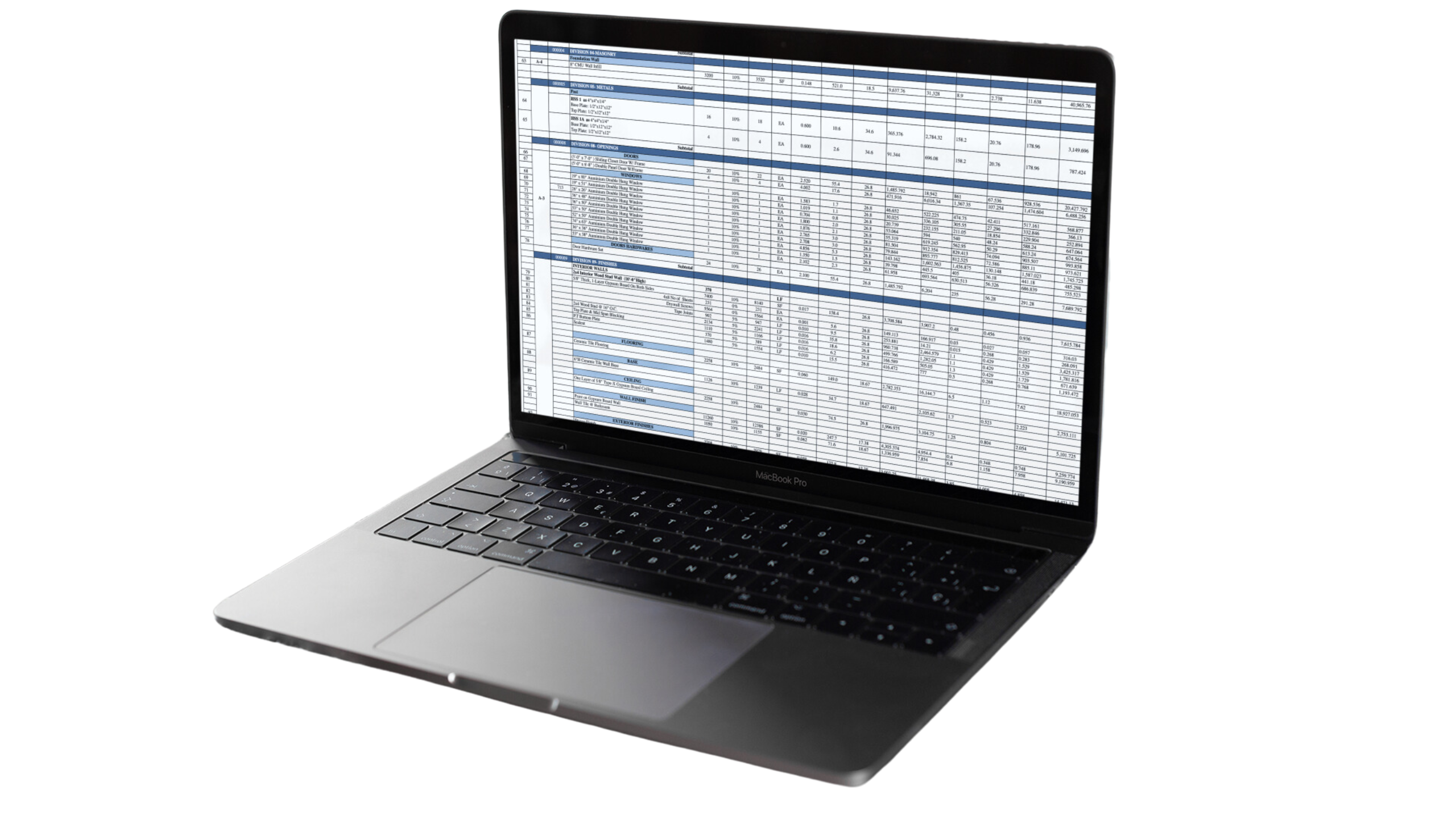
Lumber Videos
Pole Barn Construction
House Building
Building a bARNDOOR
In-Depth Lumber Price Breakdown in Boca Raton
Here’s a revised table presenting a more detailed breakdown of lumber costs in Boca Raton, listed per thousand board feet. This table includes various lumber types, their grades, price ranges, and common applications:
Lumber Type | Grade | Price Range (per Thousand Board Feet) | Common Uses |
Softwood | Low | $400 – $600 | Framing, sheathing |
Softwood | High | $700 – $900 | Fine carpentry, visible surfaces |
Hardwood | Low | $800 – $1,000 | Flooring, furniture |
Hardwood | High | $1,100 – $1,200 | Specialty projects, high-end finishes |
Types of Wood Commonly Used in Home Framing
Framing lumber, often referred to as structural wood, is a specific grade of wood utilized in the construction of homes for elements such as studs, Larsen Trusses for Double-Stud walls, headers, roof trusses, and floor joists, as well as in timber frame buildings. This type of lumber is selected for its ability to support large spans, a critical aspect in construction. Below is a list of the most commonly used wood types for framing lumber, popular in house construction and increasingly employed in timber frames for low to mid-rise multi-family buildings across in Boca Raton.
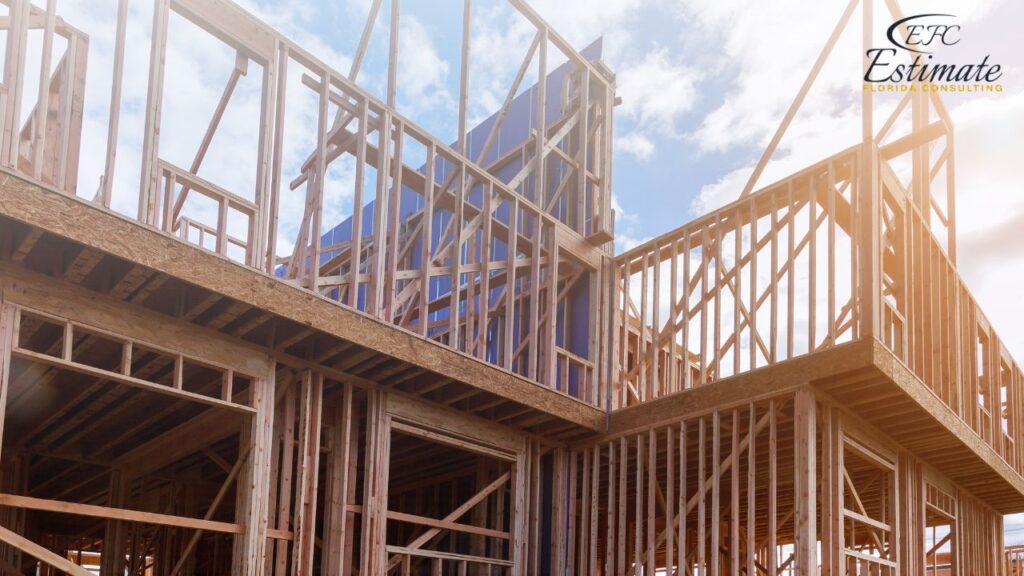
Light Structural Lumber
Primarily utilized in building single-family homes, light structural lumber is crafted from softwood trees such as spruce, fir, and pine. These trees are milled and machine-planed into standard sizes like 2×4″, 2×6″, 2×8″, and more. Wood serves as an ideal framing material due to its minimal processing, low embodied energy, renewable nature, and carbon storage capability.
Heavy Timber
Heavy timber comprises dimensional lumber over 4.5 inches thick and is frequently used in post-and-beam construction or for timber frame houses. Its large dimensions allow it to support substantial loads and span greater distances, with the added benefit of significant fire resistance.
Business Finance Loan
Find out if you're pre-qualified in seconds
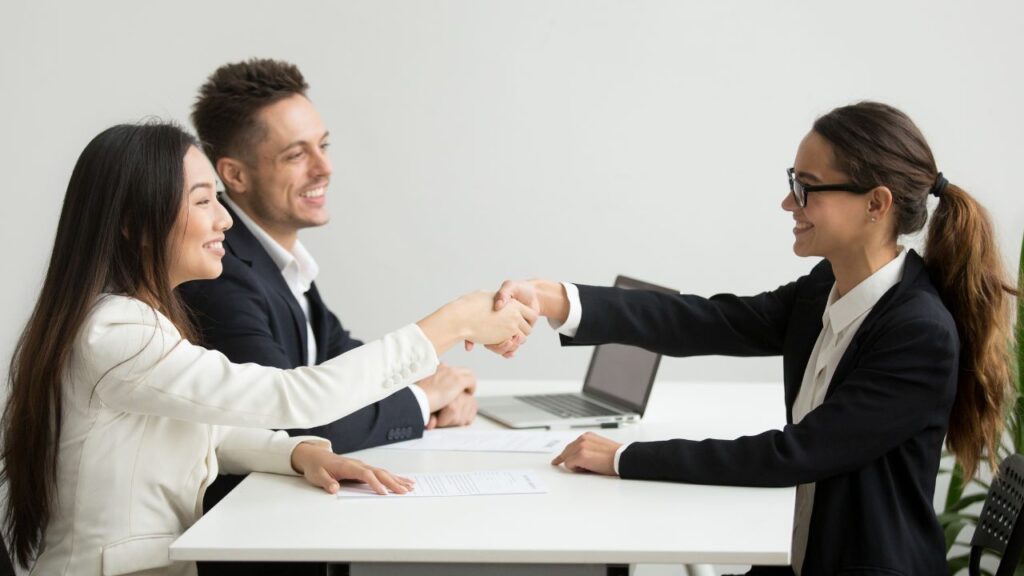
Get Prequalified Now
IMPORTANT: Make sure the email and phone number you enter are correct. We will email and text you a link to get started.
Finger-Jointed Lumber
Finger-jointed lumber, also known as end-jointed or end-glued, is produced by joining short, dry wood pieces that have been machined at each end with a water repellent structural adhesive. This environmentally friendly method maximizes the use of short wood pieces to create larger, more stable, and easier-to-align finished products. Often used in conjunction with Glulam and CLT products, finger-jointed lumber is key in constructing substantial timber structural elements for modern structures like “Plyscrapers.”
Interior Wood Trim Prices by Type
As a Lumber Cost Estimator, it’s essential to understand the diverse range of trim types used in homes, each serving slightly different purposes. While some trim pieces are purely ornamental, enhancing the aesthetic appeal of a space, others are utilized to cover gaps and provide a cohesive, finished look. Trim plays a crucial role in adding a polished touch to a home’s interior or exterior and can be customized through staining or painting to seamlessly blend with any decor scheme. By recognizing the various functions and decorative possibilities of trim, accurate cost estimations can be provided to meet the unique needs of homeowners for their lumber-related projects.
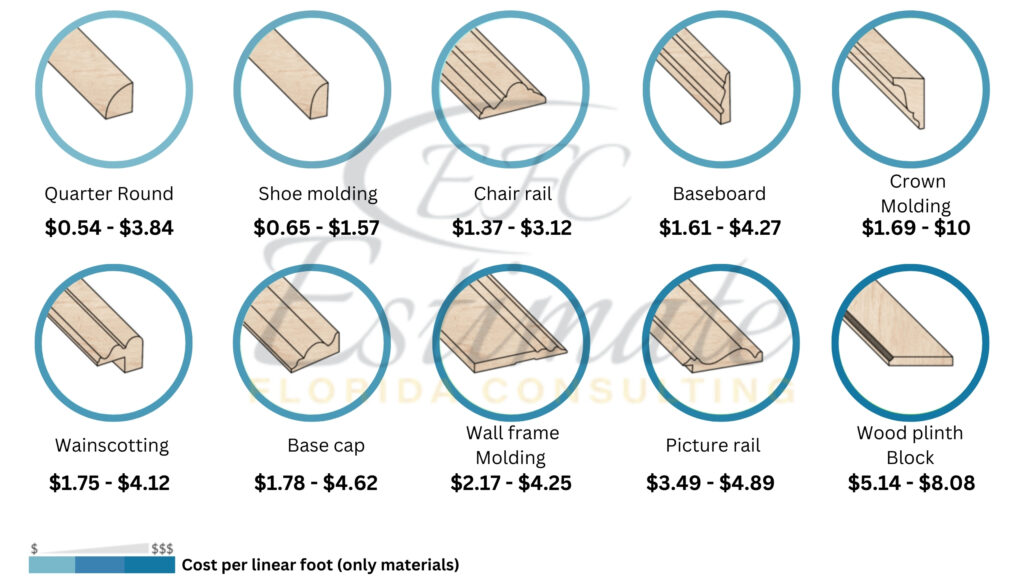
Type | Cost Per Linear Foot (Only Materials) |
---|---|
Quarter Round | $0.54 – $3.84 |
Shoe Molding | $0.65 – $1.57 |
Chair Rail | $1.37 – $3.12 |
Baseboard | $1.61 – $4.27 |
Crown Molding | $1.69 – $10 |
Wainscotting | $1.75 – $4.12 |
Base Cap | $1.78 – $4.62 |
Wall Frame Molding | $2.17 – $4.25 |
Picture Rail | $3.49 – $4.89 |
Wood Plinth Block | $5.14 – $8.08 |
Estimate Your Project With Us
Impact of Rising Lumber Prices on Housing Affordability
This decade has seen a significant surge in lumber prices, directly affecting the affordability of new homes. In the 1980s, the average cost was around $200 per 1,000 board feet, but this figure rose to over $300 during the 1990s. This increase is largely attributed to environmental regulations that restrict timber harvesting in the Pacific Northwest forests. Lumber and wood products constitute about one-third of the material costs in home construction. For a standard 2,000 square-foot home, which typically requires about 16,000 board feet of lumber and 6,000 square feet of structural panels like plywood, the cost of lumber alone at $400 per 1,000 board feet can reach nearly $10,000.
Other Expenses Related to Lumber Costs
Beyond the basic cost of lumber, various additional factors play a role in the overall expense, including transportation and delivery costs:
Local Delivery Charges
In Alachua, delivery fees typically vary from $50 to $100. These charges are influenced by factors like the distance to the construction site, road conditions, and how accessible the site is. Opting for faster, expedited delivery services can also lead to increased costs.
Long-Distance Transportation
When lumber is obtained from far-off locations, transportation costs escalate due to the longer distances involved, which increase fuel and mileage expenses. These long-distance shipping fees can range from $150 to $300, depending on how far the lumber needs to travel and the transportation method, with trucking being the most common. However, rail and ocean freight are also viable options for some shipments.
Need Template For Your Lumber Business
We provide services for Brochure, Banner, Business Card, Envelope, Invoice, etc.
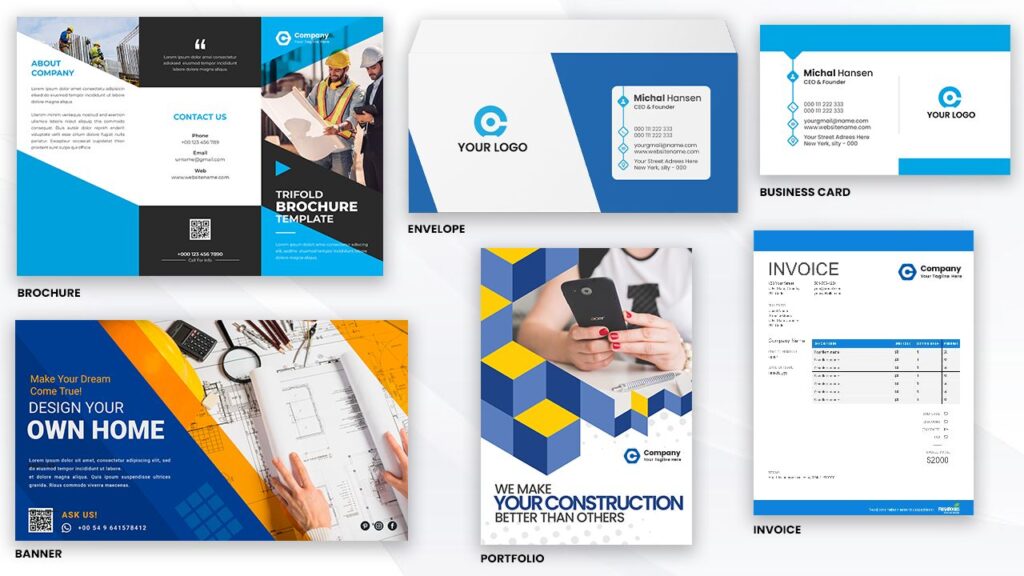
Special Handling Requirements
Certain projects necessitate lumber that has undergone specific treatments or requires special handling, such as lumber that is pressure-treated for outdoor use or treated to be fire-retardant for compliance with building codes. These specialized treatments can add fees ranging from $75 to $150, based on the treatment type and level. Moreover, lumber that is oversized or overweight may attract additional handling charges during both transportation and delivery.
Accounting for these extra costs is crucial for stakeholders to form more precise budget forecasts and efficiently handle expenses throughout the lumber acquisition process.
Effective Budgeting Strategies for Lumber Costs
Managing lumber expenses effectively requires smart budgeting practices for both homeowners and contractors. Here are some strategic tips to help control lumber costs:
- Monitor Market Trends: Stay updated on lumber market shifts to make well-informed budget decisions. Keep track of factors like supply chain issues, global economic changes, and demand variations, as these can significantly affect lumber prices. Being proactive in understanding market trends enables you to foresee potential price changes and adjust your budget as needed.
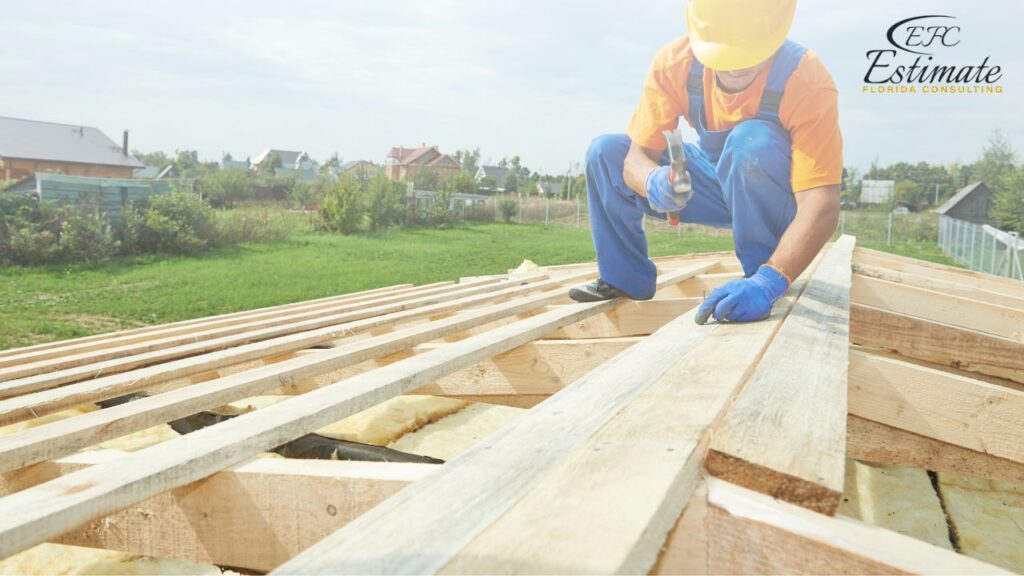
- Consider Alternative Wood Types: Popular wood species can be expensive. Exploring other wood species or engineered wood products like laminated veneer lumber (LVL) or oriented strand board (OSB) could provide cost-effective alternatives. These options often mimic the properties of traditional lumber at a reduced cost. Additionally, using sustainably sourced lumber not only benefits the environment but may also lead to cost savings.
- Optimize Purchase Timing: The timing of lumber purchases can impact costs. Look out for seasonal price variations and aim to buy during off-peak times when demand is lower. Bulk buying and seeking supplier discounts can also lead to significant savings. Plan purchases ahead and coordinate with suppliers to avoid rush orders that typically carry higher prices.
- Maximize Material Efficiency: Reducing waste and using materials efficiently can stretch your budget. Collaborate with builders to plan construction in a way that uses lumber effectively, with minimal scrap. Advanced framing methods and the use of prefabricated components can reduce lumber needs while also speeding up construction.
- Include Transportation and Handling in Budget: Transport and handling costs can be substantial, especially for distant or complex deliveries. Incorporate these costs into your overall budget. Seek local delivery options or combined shipping to cut down on transport expenses. Additionally, account for any special handling needs, like crane services or special delivery methods, in your financial planning.
Adhering to these budgeting strategies can help homeowners and contractors manage lumber expenses more effectively, ensuring that construction projects remain within budget.
Are You Looking For?
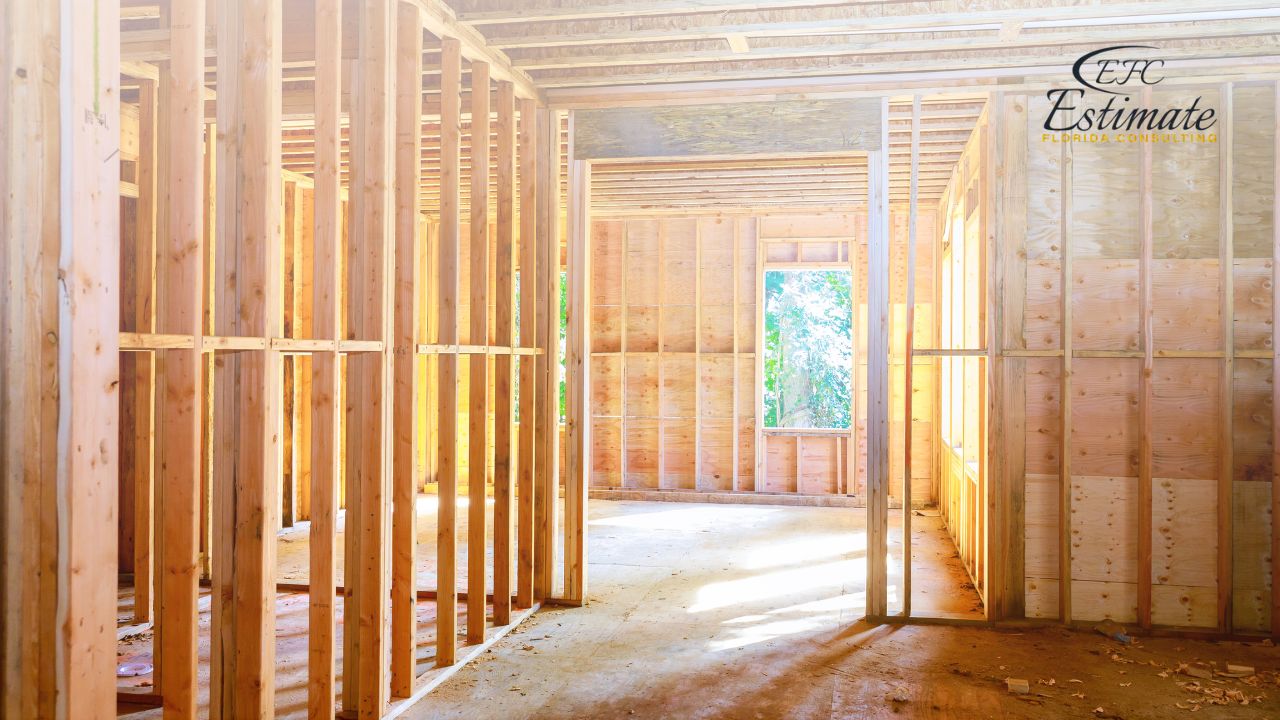
Fully Insured License Hire Contractor For Lumber
Hire ContractorCall Us To Discuss More at 561-530-2845
Conclusion
The lumber cost estimation services provided by Estimate Florida Consulting in Boca Raton are essential for both residential and commercial construction projects. Understanding the various factors that influence lumber costs, such as market trends, project specifics, and supply chain dynamics, is crucial for accurate budgeting and cost control. With the rising prices of lumber significantly impacting housing affordability, exploring cost-effective alternatives and adopting efficient budgeting strategies becomes imperative. Whether it’s selecting the right type of lumber, optimizing purchase timing, or considering transportation costs, effective planning and understanding of the lumber market can lead to substantial savings and successful project outcomes. Estimate Florida Consulting stands as a valuable resource in navigating these complexities, ensuring tailored and precise lumber cost estimates for diverse construction needs.
Choose Your Trade & Get a Sample Project
FAQs
Estimate Florida Consulting, located in Boca Raton, specializes in detailed and thorough lumber cost estimation for both residential and commercial construction projects.
Lumber prices in Boca Raton typically range between $400 and $1,500 per thousand board feet. Factors influencing these prices include the type, grade, species, moisture content, and size of the lumber, along with transportation and delivery fees.
The cost of lumber is influenced by market dynamics, project specifics, volume requirements, and supply chain dynamics, including global economic trends, trade policies, environmental regulations, logistical challenges, and regional variations in lumber production.
Common types of lumber used in home framing include light structural lumber (from softwood trees like spruce, fir, and pine), heavy timber, and finger-jointed lumber. These are used for different aspects of construction, such as studs, trusses, and joists.
The surge in lumber prices over the decades has significantly impacted the affordability of new homes. Lumber and wood products constitute a substantial portion of the material costs in home construction.
Beyond the basic cost of lumber, additional factors include local delivery charges, long-distance transportation costs, and special handling requirements, which vary depending on distance, transportation method, and specific lumber treatment or handling needs.
Effective budgeting strategies include monitoring market trends, considering alternative wood types, optimizing purchase timing, maximizing material efficiency, and including transportation and handling costs in the overall budget.
Process To Get Lumber Cost Estimate Report
Here I am going to share some steps to get your lumber cost estimate report.
-
You need to send your plan to us.
You can send us your plan on info@estimatorflorida.com
-
You receive a quote for your project.
Before starting your project, we send you a quote for your service. That quote will have detailed information about your project. Here you will get information about the size, difficulty, complexity and bid date when determining pricing.
-
Get Estimate Report
Our team will takeoff and estimate your project. When we deliver you’ll receive a PDF and an Excel file of your estimate. We can also offer construction lead generation services for the jobs you’d like to pursue further.
Google Reviews
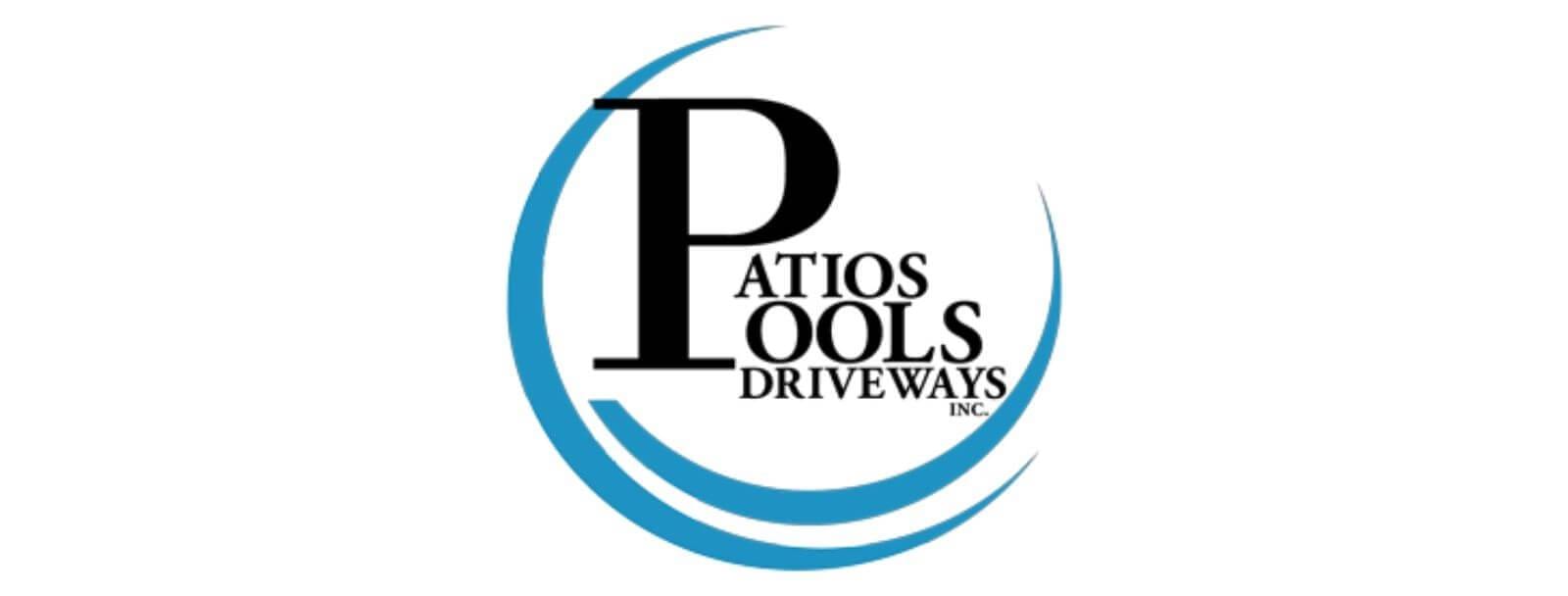
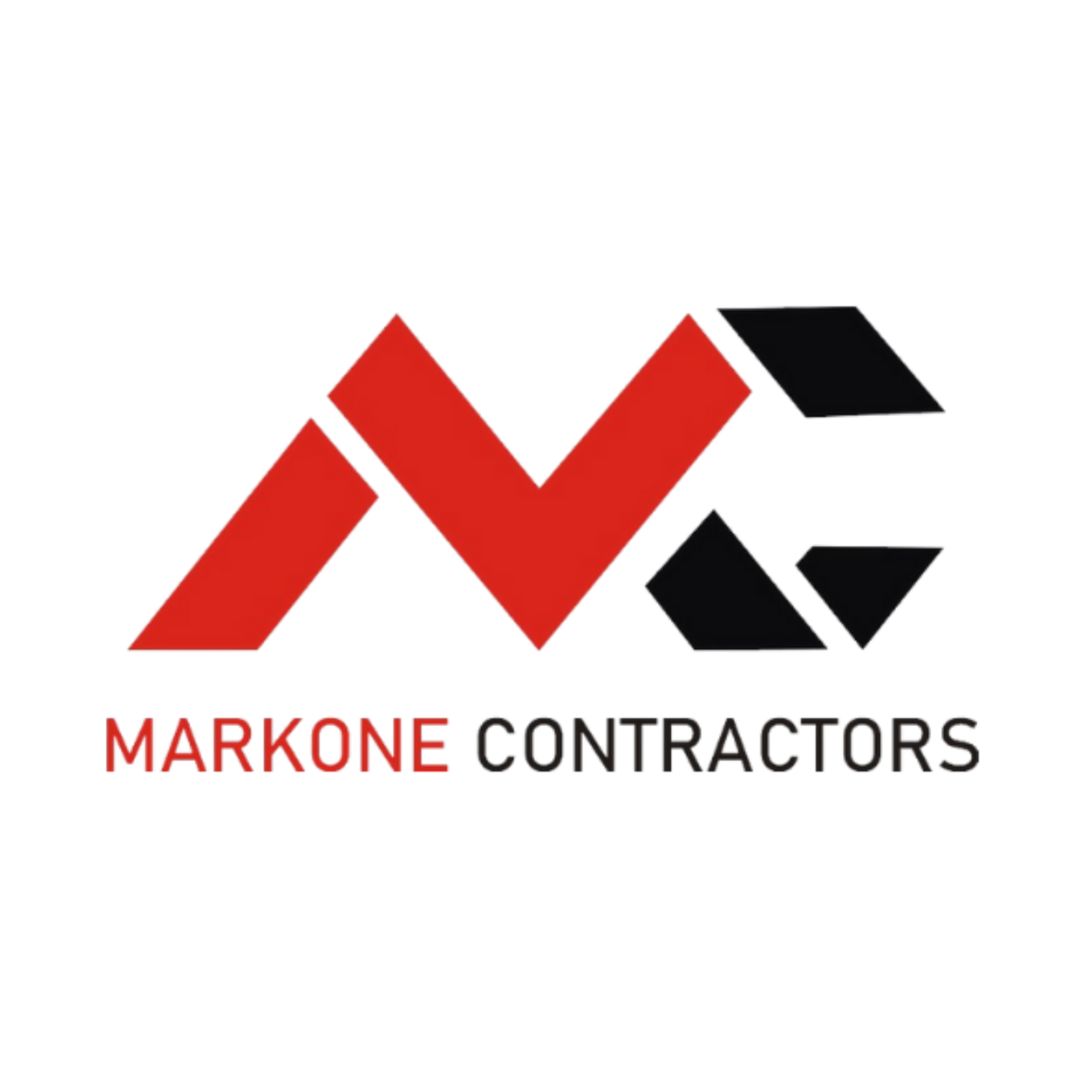
