A Wining Cost Estimate
That Helps You To Win More Flooring Construction Projects
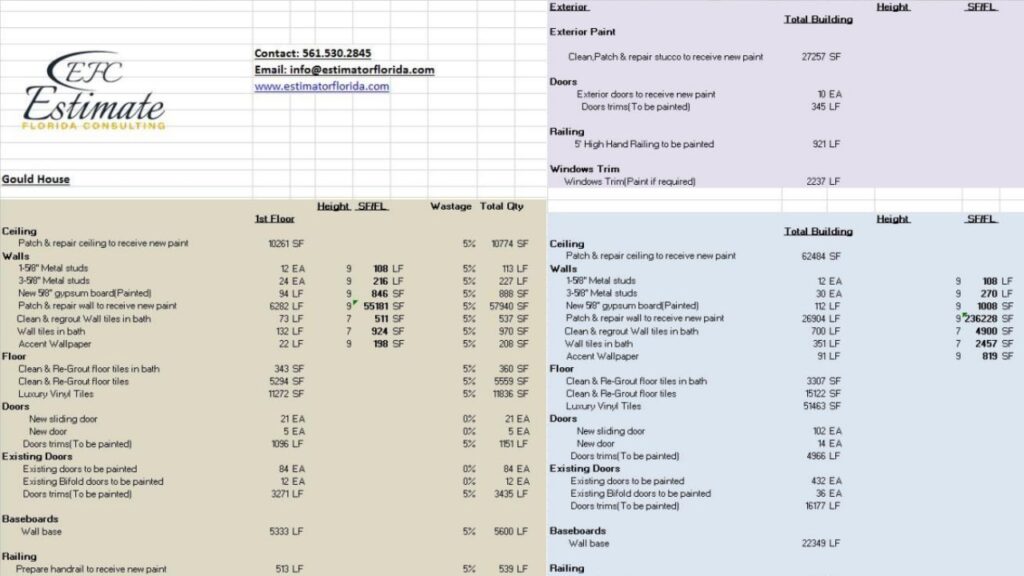
To estimate the price of self-leveling epoxy flooring for industrial spaces with material cost, labor cost, square footage, and installation complexity as determining factors, dive into the section of “Factors Affecting the Price of Self-Leveling Epoxy Flooring.” Here, we’ll explore the sub-sections containing the potential costs and their impact on the overall price of installing self-leveling epoxy flooring in your industrial space.
Material Costs for self-leveling epoxy flooring installation can greatly affect the total job cost. It’s wise to create a table for all materials, showing names, supplier names, unit cost and quantity required.
For example, epoxy resin is around $75-$150 per gallon, whilst MEK and acetone solvents cost about $9 per gallon.
High-quality premium materials may be more expensive upfront, but they require less maintenance and last longer, making them cheaper in the long run.
Pro Tip: Research suppliers/producers offering field-tested materials at competitive rates to reduce material costs. To save even more, don’t try to DIY – it’s cheaper to hire a pro!
Skilled workers are an important part of the cost of self-leveling epoxy flooring installation. The price you pay may depend on the availability of highly trained professionals. Wage rates can also vary in different locations. Skilled labor includes surface preparation, mixing, pouring, troweling, and finishing. Bigger areas require more time, which can affect labor costs. Unexpected issues can lead to more fees. It’s essential to hire a licensed, insured contractor for safety. HomeAdvisor.com recommends making sure they are bonded, licensed, and insured.
Who needs a penthouse when you can have a self-leveling epoxy floor that makes every square foot feel like a luxury suite?
Square Footage: Square footage matters when it comes to self-leveling epoxy flooring prices. The bigger the area, the more materials and labour time it requires, which increases cost. Complicated floorplans or intricate designs also add to the installation cost.
Surface Type: The type of surface on which the epoxy will be installed affects pricing too. If the floor has damage, repairs may be necessary before applying the epoxy, resulting in additional labour costs.
Unique Pricing Factors: Other factors that can raise the price are custom stencils or logos, and using translucent flakes in the design.
FOMO: Square footage is an essential element when calculating the flooring’s final price. It’s important to measure the property as soon as possible to avoid higher expenses due to extensive repairs or delay in installation. Self-leveling epoxy flooring must be done correctly – one wrong step and the floor could end up full of cracks and unevenness.
The cost of laying self-leveling epoxy flooring depends on its complexity. Factors that make up this complexity include:
Every job site may have its own unique complexities. This could affect the total service cost.
Self-leveling epoxy flooring was first used in Germany during WWII. It was created to meet military demands for durable, chemical-resistant floors. Technology has come a long way since then, leading to more sophisticated epoxy formulations used around the world today. So, why do math when you can just epoxy and go?
To calculate the material cost for self-leveling epoxy flooring for industrial spaces, you need to know the cost of each component. This section on calculating material cost for self-leveling epoxy flooring with sub-sections including base resin cost, hardener cost, additive cost, pigment cost, and surface preparation cost, helps you estimate the total cost of your self-leveling epoxy flooring project.
For self-leveling epoxy flooring, the cost of the base resin is a must-know. You need to establish how much material your project needs.
Below is a table with Brand, Type, Unit Cost, and Quantity columns. It shows base resin cost. However, where you live and the supplier may affect this data.
Brand | Type | Unit Cost | Quantity |
---|---|---|---|
ABC Coating | Epoxy Resin | $20 per kg | 100 kg |
XYZ Paint | Floor Sealer | $10 per L | 50 L |
You should also think about curing time and pot life when figuring out the base resin cost. Curing time is how long it takes for the resin to reach max hardness. Pot life is how long the mixed resin can be used before it hardens.
To keep your budget on track, we suggest talking to experts. They can help you accurately estimate what you need.
Get ready. Your wallet may need to be leveled just like your floor – the base resin cost isn’t going to be easy on it!
We help contractors find new customers with high-converting websites and locally targeted niche-specific lead-generation programs. You’ll never need to worry about running out of work again! We focus on quality over quantity with our leads for contractors.
The cost of hardener, a crucial component of the flooring system, should be taken into account when calculating the cost of self-leveling epoxy flooring.
Create a table with columns such as brand, quantity, unit price, and total. Popular brands like Sikadur or Flexbon range from $50-$200 per gallon.
For example:
Brand | Quantity | Unit Price | Total |
---|---|---|---|
X | 2 Gallons | $70 | $140 |
Y | 1 Gallon | $150 | $150 |
Z | 5 Gallons | $55 | $275 |
Remember, different brands may require different amounts of hardener per gallon. Check manufacturer specifications for accurate calculations.
Bulk purchases and special promotions can affect final costs.
Pro Tip: Ensure compatibility between your chosen resin and hardener. Consult with a professional or supplier if unsure.
The cost of extra material to give properties to self-leveling epoxy flooring is called Enhancer Expenses. To figure out the Enhancer Expenses, think about the type and amount of additives needed to get the wanted flooring features.
For example, Micro-flake additive (3 lbs.) at $50 per pound is needed for a special design. Metallic pigment (8 oz.) at $40 per package is required for a reflective surface or if adding color to the formula. Polyaspartic topcoat additive (1 gallon) at $100 helps with added protection against UV light, fading, and clear finish.
Additive Type | Package Quantity | Cost Per Quantity |
---|---|---|
Micro-Flake Flake | 3lbs | $50/lbs |
Metallic Pigment | 8oz | $40/pkg |
Polyaspartic Topcoat Additive | 1 Gallon | $100/gal |
Adding more coats or applications can also change the Enhancer Expenses in terms of types and amounts of additives used.
Pro Tip: An excel sheet can help you keep track of the different types and quantity of additives used. It comes in handy during documentation or reapplication of similar projects, reducing wastage during calculations.
Instead of going to a therapist, why not just add some pigments to your self-leveling epoxy and express yourself through your flooring?
Enhancing Color Appearance
Pigments are essential for creating an attractive self-leveling epoxy floor. They add color and tone to the final look. The following table shows the type of pigment, cost (per pound/kg), and amount (per square foot/meter).
Type of Pigment | Cost (per pound/kg) | Amount (per square foot/meter) |
---|---|---|
Iron Oxide | $2.50/$5.50 | 0.05 lb/sqft |
Titanium Dioxide | $4/$8 | 0.03 lb/sqft |
Phthalocyanine Blue | $6/$12 | 0.02 lb/sqft |
High-quality pigments add aesthetic value to the design. But, installation expertise is also necessary to ensure success. Without proper preparation and a skilled team, even the best pigments may give disappointing results.
Pigment has been used for centuries to provide color for painting and printing textiles. Now, it’s even more important for self-leveling epoxy flooring systems. It pays to be OCD when prepping the surface and buying the right pigment – it’s expensive!
Elevate your space with the help of a professional flooring contractor. Experience expert installation services and unlock the beauty and durability your floors deserve. Contact us today for a flawless flooring transformation.
Calculating the cost of a smooth surface for self-leveling epoxy flooring requires considering Surface Preparation expenses. This includes removing existing floor coatings, grinding or shot blasting the concrete beneath, and repairing any cracks.
To get an idea of the cost, it’s helpful to create a table with Item, Unit of Measurement (UoM), Quantity, Rate per UoM and Total Cost columns. Items can be things like Concrete Repair, Grinding/Shot Blasting, Cleaning/Degreasing, etc. UoM could include Square Feet (sq.ft), Hours/Day, etc.
Note: Surface Preparation costs vary depending on substrate condition, preparation method, size of the area, and accessibility. So, it’s essential to assess these factors before estimating material costs for epoxy flooring projects.
Pro Tip: Always set aside a budget for unexpected expenses. Even slight variations from estimates can significantly impact the total project cost.
To estimate the labor cost for self-leveling epoxy flooring for industrial spaces, focusing on installation time, installer’s experience and skill level, and type of equipment used can help achieve accurate cost estimation. In this section, we will introduce the sub-sections that play a crucial role in determining the cost. The sub-sections are installation time, installer’s experience and skill level, and type of equipment used.
Estimating the time for self-leveling epoxy flooring installation requires consideration of several factors. These include surface preparation, area size, number of coats, and curing time.
Here is a 5-step guide:
Time required varies based on different factors. Temperature and humidity can also affect curing times.
Pro Tip: Allow enough time for each layer to dry before adding more coats. This ensures top-notch adhesion and long-term performance. Installing self-leveling epoxy flooring takes skill and patience – like watching a mesmerizing dance with power tools and chemicals!
To calculate labor cost accurately for self-leveling epoxy flooring installation, the experience and skillset of installers plays a crucial role. The table below shows the different levels of experience and skillset a professional installer must have.
Level | Description |
---|---|
Beginner | No prior experience with Self-Leveling Epoxy Flooring but knows flooring basics |
Intermediate | Some experience with Self-Leveling Epoxy Flooring but needs supervision |
Expert | Highly trained with extensive knowledge and experience in Self-Leveling Epoxy Flooring, without supervision |
Expert-level installers may charge higher labor costs than beginners or intermediates. Thus, assessing the requirement of your project beforehand can help minimize costs.
Inexperienced installers may make costly mistakes, like incorrect mixing ratios or uneven application techniques, so hiring professionals with the right skills is vital.
According to Grand View Research report, the global self-leveling epoxy flooring market size was valued at USD 1.4 billion in 2018 and is estimated to rise at a CAGR of 5.5% over the forecast period.
To get maximum return on investment and avoid extra expenses, it’s best to choose an installer experienced in epoxy flooring installation. Trying to estimate labor cost for self-leveling epoxy flooring? It ain’t easy – just like leveling your ex’s accusations!
Maximize your plumbing construction business’s potential with our competitive financing options
Various equipment is used for self-leveling epoxy flooring, tailored to the needs of each project. Mixers to mix and distribute, rollers to evenly spread, and squeegees to quickly cover large areas. Advanced equipment like shot blasters and vacuum cleaners can also be used to prepare and clean surfaces before application. Remember, it’s important to check that all equipment is in good condition. That way, labor costs can be minimized and the job completed smoothly.
Calculating the cost of self-leveling epoxy isn’t easy, so be prepared to do some serious number crunching!
To calculate the total cost of self-leveling epoxy flooring for industrial spaces, you need to understand the material and labor costs involved in the process. Approach the task by breaking down the costs into two sub-sections: material cost and labor cost. When you have clarity on both, you can easily estimate the total cost and make an informed decision.
Self-leveling epoxy flooring cost is calculated by adding materials and labor. The total cost varies, depending on size, type of epoxy, and the complexity of application.
The table below shows the material cost and labor cost of installing self-leveling epoxy:
Cost | Materials | Labor |
---|---|---|
Examples | Epoxy Resin | Surface Preparation |
Hardener | Mixing & Application | |
Pigments or Dye | Roll & Trowel Coat | |
Total per Sq/Foot | $3 to $12 | $2 to $5 |
Materials make up a big part of the cost, but hiring an expert or doing it yourself can reduce labor costs.
Remember, extra costs may arise. For this reason, seek advice from an experienced installer to get accurate quotes.
Don’t wait any longer! Get in touch today to arrange a consultation or research your DIY project. Enjoy a durable finish that boosts your home’s function and look!
To compare the cost of self-leveling epoxy flooring with other industrial flooring options like concrete, vinyl, and tile, here’s a section you should read. Knowing the differences in price can help you make an informed decision about the best flooring option for your project. We will discuss the cost-effective benefits of each option in the following sub-sections.
Concrete flooring is a popular pick for industrial spaces, thanks to its strength and durability. But, with technology advancements, self-leveling epoxy flooring has gained popularity as an alternative. It provides better resistance against chemicals, abrasion, and impact–plus customizable design options.
Self-leveling epoxy flooring can be cost-effective when compared to other industrial flooring options, like vinyl or ceramic tiles. Its quick and easy installation process requires less labor time, reducing costs. Plus, minimal maintenance leads to long-term savings.
Unique qualities of this flooring include: seamless finish with no joints or cracks, ideal for sanitary environments (like food processing facilities and healthcare institutions), and anti-slip properties for high traffic areas.
To get the most out of self-leveling epoxy flooring, preparation is key. Clean the surface and fill any cracks or pits. Proper prep allows for better adhesion of the epoxy coating, thus a longer-lasting finish.
In conclusion, self-leveling epoxy flooring is a great option for industrial spaces–durable, easy maintenance, design customizability, and cost-effective. Prep the surface and enjoy the maximum benefits of this innovative flooring solution.
Vinyl flooring is a popular industrial flooring choice, offering durability and versatility. It comes in a variety of colors and textures, so you can customize its look. Here’s a cost comparison table to help you decide:
Flooring Option | Cost per square foot |
---|---|
Vinyl | $3 – $7 |
Epoxy | $3 – $12 |
Polished Concrete | $2 – $10 |
Ceramic Tiles | $4 – $8 |
Remember that these costs are only approximations. Your location and installer rates can affect the final price.
Vinyl has another advantage: it’s easy to install. DIYers can save on labor fees, and contractors can finish the job quickly. Luxury vinyl tiles (LVT) are a great choice. They have a high-quality printing technology that looks like natural wood or stone – a less expensive alternative to materials that require regular upkeep.
Looking for something as durable and inexpensive as self-leveling epoxy? Good luck! It’s like finding a needle in a porcelain haystack.
Tile flooring is a great choice for industrial applications. It’s durable, low-maintenance, and can be made from ceramic, porcelain, natural stone, or glass. It comes in different shapes, sizes, colors, patterns, and textures. It offers excellent resistance against heavy traffic, abrasions, stains, chemicals, and moisture. Plus, if a tile gets damaged, it can easily be replaced without disrupting the whole floor.
Tile flooring is also ideal for food processing and cleanroom environments, since its smooth surface makes it hygienic. It can even help you earn LEED certification, as it’s durable and recyclable. Furthermore, tile flooring has a shorter installation time compared to other flooring options, meaning less business disruption during renovation or replacement projects.
A 2020 study by Grand View Research shows that ceramic tiles dominate the global industrial flooring market, due to their affordability and versatility. So, if you want to optimize your industrial space, consider tile flooring – it’s a win-win!
Understanding the cost of self-leveling epoxy flooring for industrial spaces can be confusing. Here are some helpful tips to estimate it. First, consider the square footage and type of epoxy needed. Next, find out if repairs or preparations are required prior to installation. Lastly, check the complexity and accessibility of the site. These factors are key for estimating the cost accurately.
To get a more accurate estimate, consider all expenses related to installation. This includes labor costs from third-party contractors and materials like sealants or coatings. Moreover, remember that self-leveling epoxy flooring can vary in quality and price based on the manufacturer and supplier. Doing research before investing can save you money.
It’s also important to evaluate the long-term benefits of investing upfront in quality epoxy flooring. This could improve durability and reduce maintenance costs at your industrial facility, contributing positively to your bottom line.
Self-leveling epoxy flooring is a type of resinous floor coating that is applied in liquid form and then levels itself out to create a smooth, seamless surface. It is a popular choice for industrial spaces due to its durability and resistance to chemicals, abrasion, and impact.
The price of self-leveling epoxy flooring is determined by several factors, including the size of the area to be covered, the condition of the existing substrate, the type and grade of epoxy being used, and any additional customization or design features. It is important to obtain an accurate measurement and assessment of the space before receiving a quote.
Self-leveling epoxy flooring provides numerous benefits for industrial spaces, including seamless and easy-to-clean surfaces, excellent durability and resistance to wear and tear, and customizable aesthetic options. It can also increase safety by providing slip-resistant surfaces and reducing the risk of accidents.
Self-leveling epoxy flooring is a versatile and customizable option for many different types of industrial spaces, including warehouses, manufacturing facilities, and clean rooms. However, it may not be suitable for spaces with high moisture levels or extreme temperature fluctuations, as these factors can affect the product’s performance.
The installation process for self-leveling epoxy flooring typically involves several steps. First, the substrate is prepared by cleaning and repairing any damage or imperfections. Next, an epoxy primer is applied to the surface. Then, the self-leveling epoxy is mixed and poured onto the substrate, where it will spread and self-level over the entire area. Finally, a topcoat is applied to protect the surface and provide additional durability.
The lifespan of self-leveling epoxy flooring depends on several factors, including the quality of the product, the conditions of the space, and the level of maintenance provided. However, properly installed and maintained self-leveling epoxy flooring can last anywhere from 10-20 years or more.
Here I am going to share some steps to get your flooring construction cost estimate report.
You can send us your plan on info@estimatorflorida.com
Before starting your project, we send you a quote for your service. That quote will have detailed information about your project. Here you will get information about the size, difficulty, complexity and bid date when determining pricing.
We do flooring construction cost estimating and prepare a detailed report for your project. At last, you finalize the report and finish the project.
561-530-2845
info@estimatorflorida.com
Address
5245 Wiles Rd Apt 3-102 St. Pete Beach, FL 33073 United States
561-530-2845
info@estimatorflorida.com
Address
5245 Wiles Rd Apt 3-102 St. Pete Beach, FL 33073 United States
All copyright © Reserved | Designed By V Marketing Media | Disclaimer
IMPORTANT: Make sure the email and cell phone number you enter are correct. We will email and text you a link to get started.
By clicking “I Agree” above you give Estimate Florida Consultin express written consent to deliver or cause to be delivered calls and messages to you by email, telephone, pre-recorded message, autodialer, and text. Message and data rates may apply. You are able to opt-out at any time. You can text STOP to cancel future text messages.