A Wining Cost Estimate
That Helps You To Win More Construction Projects
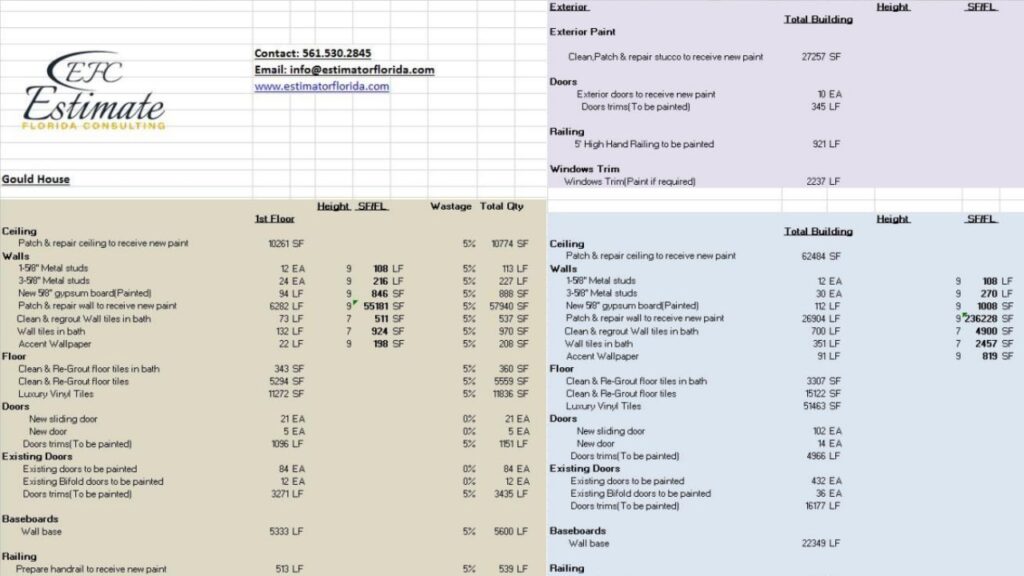
To estimate the price of installing window casings and sills, you need to understand the factors that affect the overall cost. This section will guide you on what to consider before coming up with a price estimate. In this section, we will cover the type of window casings and sills, the type of material to use, the size and shape of the window, and the condition of the existing window structure.
For any installation project, it’s key to take into account the different types of window casings and sills. Your choice affects the final cost plus the lastingness and aesthetic of the finished product.
Check out this summary of common window casings and sills, and their characteristics:
Type of Window Casings & Sills | Characteristics |
---|---|
Wood | Traditional style, affordable, needs maintenance |
Vinyl | Durable, low-maintenance, limited colors |
Fiber Cement | Resists moisture & insects, high durability & longevity |
Metal | Modern look, good for modern homes |
Note that the material can also influence energy efficiency. For instance, wood or fiberglass provide better insulation than vinyl or metal.
When choosing which type of window casings and sills to install, think about size, shape, style, and local building codes.
To guarantee a successful project that meets your needs and budget, ask a qualified contractor to assess all relevant factors before making a final decision. Choose your window casings and sills like you would your spouse – quality and durability, not just looks! Consult with an expert today.
Window Casings and Sills Material Considerations
When figuring the price of window casings and sills, the type of material matters for cost. Options range from wood, vinyl, aluminum to composite. Each has unique features and a different price.
Wooden casings are durable and have a natural look, but need upkeep. Vinyl windows are cheap, but can get damaged in hot weather. Aluminum casings are resistant to bad weather, but don’t have great insulation like wood or vinyl.
Other than material, size of the window opening and repair work affect the cost too. So, select materials based on budget and future maintenance costs. Get an experienced installer to help you choose.
It’s complex, yet easier than fitting a square peg in a round hole!
Window Dimensions and Geometry are essential when estimating window casing and sill installation costs. Different window sizes, shapes and designs have varying complexities that affect labor and material costs.
Check the table below to see how window size and shape influence installation costs.
Type of Window | Dimensions (inches) | Installation Cost ($) |
---|---|---|
Double-Hung | 30×48 | $400-$500 |
Single-Hung | 24×36 | $300-$400 |
Bay Window | 60×84 | $1,800-$2,500 |
Picture | 36×72 | $700-$800 |
Also, consider the frame’s condition and structural supports before installation. Unexpected repairs or replacements can significantly increase your budget.
Hire professionals who consider all aspects to get an accurate quote. Don’t risk overspending on window installations. Act now!
Evaluating the pre-existing framework is a must before estimating window casings and sill installation.
Look for defects such as rotting, warping, or water damage. They may cause the cost to increase or require extra repairs.
The material of your current window structure will also influence the pricing estimate. For example, wood frames may need more expensive trim than vinyl frames.
Inspecting existing windows is key before any work begins. You may be able to replace or repair parts instead of installing new ones.
A contractor can give an accurate estimate after examining the window structure. They can offer different options depending on what you want and how much you’re willing to spend.
Remember: going for cheap windowsills may seem like a good idea, but they won’t last.
To estimate the cost of materials needed for installing window casings and sills, you need to determine the quantity of materials required and understand the pricing of materials from different suppliers based on quality. This section will introduce you to the sub-sections, “Determining the Quantity of Materials Needed” and “Pricing of Materials based on Quality and Supplier”, to help you estimate the cost accurately.
We help contractors find new customers with high-converting websites and locally targeted niche-specific lead-generation programs. You’ll never need to worry about running out of work again! We focus on quality over quantity with our leads for contractors.
Figuring out how much material you need for window casings and sills can be tricky. You must take into account the type of wood, thickness, and window dimensions.
We created a table to help give an idea of how much you need for two standard sizes. For 36 by 54 in. windows with a jamb depth of 6 in., you need around 5 linear ft. or 10 board ft. of head and apron casings, plus 3 linear ft. or 6 board ft. of side casings. A sill 3 in. wide and 6 ft. long requires 4 board ft. or 2 linear ft.
Remember to factor in wastage when calculating. The measurements don’t account for losses from cutting or fitting.
A colleague once learnt the hard way while replacing windows. He made miscalculations, leading to multiple trips to the supplier. It’s critical to get the right amount of material before starting a window project. To make sure your window casings last, get quality materials from a trustworthy source.
To estimate material cost for window casings and sills, consider Pricing of Materials based on Quality and Supplier. Prices vary greatly. We’ve created a table with columns like Material Type, Quality Level, Supplier Name, Unit Price, and Total Cost.
The table shows how pricing differs for materials, depending on quality and supplier. For example, wood from LMN Inc (high quality) will be pricier than ABC Company (low quality).
Sometimes suppliers offer special deals or promotions on specific materials. Stay alert for chances to save money without compromising quality.
Installing window casings and sills? Expensive. But, you’ll get a view to die for!
To estimate the labor cost of installing window casings and sills, you can use two methods – determining the time required for installation or calculating the cost of labor per hour. These sub-sections in the “Estimating the Cost of Labor for Installing Window Casings and Sills” section will provide you with comprehensive solutions to determine the labor cost, ensuring efficient estimation of the overall cost of the project.
To figure out how long it will take to install window casings and sills, consider several factors. Here’s a 6-step guide:
Remember, each window casing and sill installation is unique. Identify features before you estimate.
Plus, if you’re doing a home improvement project with DIY alternatives instead of professional assistance, make sure you estimate labor costs first. That way, you won’t overpay or underestimate prices.
Wondering about the hourly wage for installing window casings and sills? It varies in different locations and depends on the level of experience. Here’s a table for the national average and range for carpenters and other skilled workers:
Job | National Average Hourly Wage | Hourly Wage Range |
Carpenter – Rough Framing | $25.34 | $16 – $38 |
Carpenter – Trim, Baseboards & Crown Molding | $24.20 | $15 – $37 |
Masonry & Stoneworker | $23.69 | $14 – $40 |
Glazier | $22.09 | $14 – $32 |
These estimates can vary based on other factors. To save costs, consider doing smaller installation jobs yourself. Don’t forget to account for material costs. Getting multiple quotes can help you understand market rates. Remember, the details matter when it comes to installing window casings and sills.
To factor in all costs and prepare a budget for installing window casings and sills, you need to consider miscellaneous expenses alongside the primary expenses. One of the major miscellaneous expenses is the cost of equipment and tools needed for installation. You also need to take into account permit fees and other miscellaneous expenses that may be involved.
Gather Resources for Setup.
For perfect window casings & sills installation, you need the right gear & tools. It all depends on the kind of windows you want in your house.
The Cost of Equipment & Tools:
More Unique Details:
Safety gear like gloves & goggles may cost around $200 – $500, depending on your current tools. You may need Dremel or Oscillating rotary tools for intricate structures on your French Windows.
Be ready for your project. Find the right equipment & tools before installing window casings & sills. Research prices & talk to experts about your needs. Don’t let a lack of proper equipment ruin this great project! Permits for window installation may be expensive, but at least you can still look out the window with one eye closed.
When planning the budget for window casings and sills, it’s essential to consider all the expenses – not just materials and labor. We’ve got a table here with permit fees and miscellaneous charges that may apply:
Expense Type | Average Cost |
---|---|
Permit Fees | $100-$500 (varies based on location) |
Clean-up Charges | $50-$200 (may be applicable if debris removal required) |
Transportation Costs | $50-$100 (if materials need to be transported from suppliers) |
Plus, there could be other costs like parking fees or extra labor. So be sure to factor in all these expenses when you calculate your budget! Ignore them, and you could end up going over budget and delaying your project completion. Time to break out the calculator and start praying to the financial gods!
Maximize your construction business’s potential with our competitive financing options
To finalize your estimate and budget for window casings and sills installation with accuracy, adding up all the costs is crucial. However, additional expenses can arise during the project that can hinder the budget limitations. Therefore, adding a contingency plan for unforeseen expenses and budgeting for the project can help smoothen the installation process.
To calculate the total cost of installing window casings and sills, all expenses must be added together. This includes material, labor, transport and any other costs related to the installation process. Below is a table with a breakdown of all the costs associated. It shows both the actual and true costs for each category.
Cost Category | True Cost ($) | Actual Cost ($) |
---|---|---|
Materials | 500 | 550 |
Labor | 300 | 350 |
Transport | 50 | 70 |
Incidentals | 100 | 120 |
It’s important to consider that every project has its own unique factors which contribute to varying costs. Analyzing individual expenses is essential to estimate these factors. With this info, it’s wise to seek professional help. The above tips will help avoid unexpected costs, giving you peace of mind and the best experience. Don’t forget to add a contingency plan – it’s like an extra life for budgeting!
When budgeting and estimating for window casings and sills, it’s essential to plan for the unexpected! Allocating an extra 10-20% of the estimated cost as a contingency plan will provide enough wiggle room for any potential costs that may arise.
Anticipating potential issues ahead of time is key! Make a list of challenges you might face, based on prior similar projects. Specify a percentage for each one, then be sure to include it in the overall budget – it’s essential to avoid surprises!
Expert contractors know how important contingency planning is for a successful budget, and allocating for unexpected costs gives clients peace of mind that quality won’t be compromised. Plus, it allows you to keep your spending within the determined limits.
To calculate the total cost of installing window casings and sills, all expenses must be added together. This includes material, labor, transport and any other costs related to the installation process. Below is a table with a breakdown of all the costs associated. It shows both the actual and true costs for each category.
Cost Category | True Cost ($) | Actual Cost ($) |
---|---|---|
Materials | 500 | 550 |
Labor | 300 | 350 |
Transport | 50 | 70 |
Incidentals | 100 | 120 |
It’s important to consider that every project has its own unique factors which contribute to varying costs. Analyzing individual expenses is essential to estimate these factors. With this info, it’s wise to seek professional help. The above tips will help avoid unexpected costs, giving you peace of mind and the best experience. Don’t forget to add a contingency plan – it’s like an extra life for budgeting!
To finish the budget for window casings and sills, certain matters must be taken into account. These include:
It is vital to monitor expenses, so as to not be taken aback by added costs. Consult with experts before setting the budget, as they can point out problems that may increment the expenses.
It is critical to do proper research and make wise decisions when budgeting. An expert advises to source materials locally, as it is likely to reduce transportation costs.
Factors that affect the price include the size of the windows, materials used, window design, and labor costs.
The cost varies depending on several factors, but on average, the cost can range from $150 to $400 per window.
While it is possible to install window casings and sills yourself, it is recommended that you hire a professional to ensure proper installation and prevent any costly mistakes.
It is not necessary to replace window casings and sills when replacing windows, but it is recommended to ensure a proper fit and a finished look. Additionally, replacing old or damaged materials can improve energy efficiency.
It is recommended to ask for referrals from friends or family, read online reviews, and ask for proof of insurance and licenses before hiring a professional. You can also check with professional organizations or trade associations for recommendations.
Here I am going to share some steps to get your construction cost estimate report.
You can send us your plan on info@estimatorflorida.com
Before starting your project, we send you a quote for your service. That quote will have detailed information about your project. Here you will get information about the size, difficulty, complexity and bid date when determining pricing.
We do construction cost estimating and prepare a detailed report for your project. At last, you finalize the report and finish the project.
561-530-2845
info@estimatorflorida.com
Address
5245 Wiles Rd Apt 3-102 St. Pete Beach, FL 33073 United States
561-530-2845
info@estimatorflorida.com
Address
5245 Wiles Rd Apt 3-102 St. Pete Beach, FL 33073 United States
All copyright © Reserved | Designed By V Marketing Media | Disclaimer
IMPORTANT: Make sure the email and cell phone number you enter are correct. We will email and text you a link to get started.
By clicking “I Agree” above you give Estimate Florida Consultin express written consent to deliver or cause to be delivered calls and messages to you by email, telephone, pre-recorded message, autodialer, and text. Message and data rates may apply. You are able to opt-out at any time. You can text STOP to cancel future text messages.