A Wining Cost Estimate That Helps You To Win More Construction Projects
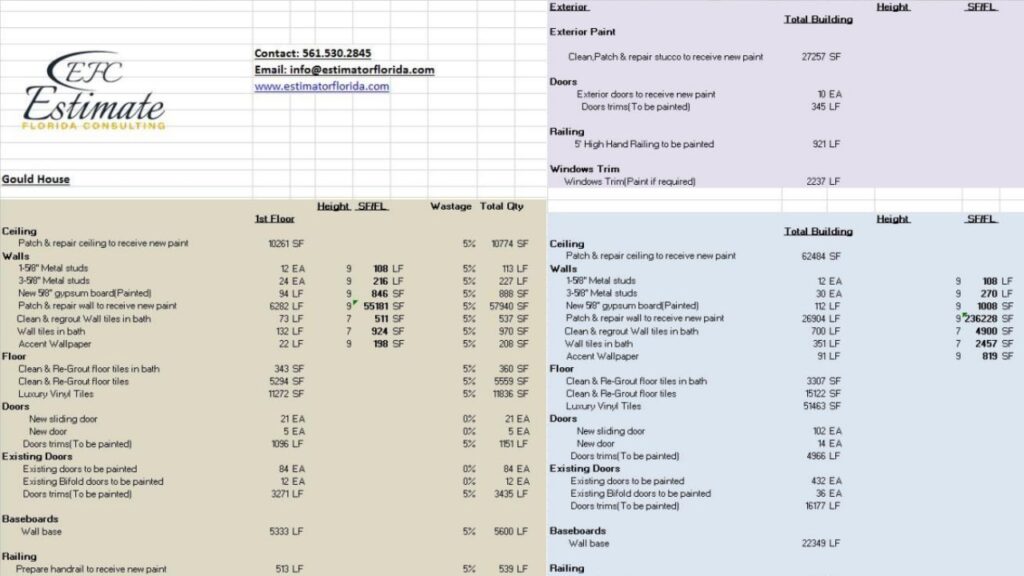
Identifying the Different Materials used in Construction
Construction materials are essential components needed for every building project. The use of proper materials is critical to ensure the safety, durability and quality of the structure.
Classification of Construction Materials
Below is a table indicating the various types of construction materials used in building projects, including the materials’ characteristics and applications.
Construction Material | Characteristics | Applications |
---|---|---|
Concrete | Strong, durable | Foundations, walls, floors |
Steel | Lightweight, rigid | Beams, frames, roof trusses |
Wood | Easy to shape | Doors, windows, framing |
Glass | Transparent, rigid | Windows, skylights |
Brick | Fire-resistant | Walls, partitions |
Stone | Durable, aesthetic | Walls, flooring, facades |
Construction materials have unique qualities that influence their usability and effectiveness in each building project. These factors, such as strength, durability, aesthetic appeal, and cost-effectiveness, are crucial considerations that must be weighed carefully when selecting materials for specific structures.
According to the National Association of Home Builders, the cost of construction materials increased by 19% from April 2020 to April 2021, impacting the overall cost of construction projects.
Looking for a sturdy natural material to build with? Wood, because sometimes you just need to get back to basics and hug a tree.
The material made from the fibrous organic matter of trees is a popular choice for construction, thanks to its versatility and availability. It can be used in various forms such as lumber, plywood, particleboard, and more. With its natural beauty and strength, wood is durable and sustainable when harvested responsibly.
In addition to being renewable and eco-friendly, wood also boasts of excellent insulation properties which make it a great choice for walls, roofs and floors.
Wood can be treated with chemicals to improve its resistance to fire, insects and decay. Different types of timber like softwood, hardwoods and engineered woods offer varying benefits depending on their intended use.
It’s worth noting that while wood has numerous advantages over other materials like concrete or steel (such as lower environmental impact), it’s important to consider the specific uses when choosing between options. For example, using wooden planks in an area that receives frequent water exposure may not be the wisest idea.
Stories abound about homes that have lasted generations because they were built with the right type of wood materials – which just goes to show how reliable this building resource is when correctly chosen by experts in the field.
You can trust steel to hold up better than your ex’s promises.
One of the most popular types of construction materials is an alloy made of iron and other elements, widely known as the ‘metal for kings’. This material is stronger and more durable than many others, making it ideal for use in buildings that require stability and longevity. Steel can be shaped into various forms and sizes to meet the design needs of any construction project, including sheets, bars, beams, pipes, and more. Not only does steel provide structural integrity to commercial and residential structures alike, but it also offers numerous environmental benefits. For instance, steel is 100% recyclable as well as energy-efficient to produce.
An interesting characteristic of this construction material is its flexibility; it can be modified to create unique designs that fulfill different architectural purposes while maintaining their durability. Furthermore, the quality control measures during manufacturing ensure a homogenous material composition with consistent properties throughout.
In terms of history, steel has played a significant role in shaping modern infrastructure worldwide. The Brooklyn Bridge in New York City was one of the earliest examples of large-scale steel construction that set new standards for bridge building using this material.
As demand for sustainable and eco-friendly materials continues to increase globally, steel will remain a strong contender due to its recyclability and low carbon footprint compared to traditional construction materials like concrete or wood. As such, it will continue playing a crucial role in future building projects and creating reliable infrastructure for generations to come.
Concrete might be tough and durable, but after staring at it for hours on end, even the material itself begins to look bored.
A mixture of aggregates, water and cement forms a composite construction material that is known for its durability and strength. This versatile material is commonly referred to as the grey gold and is widely used in construction projects worldwide. Concrete possesses exceptional compressive strength, making it viable for myriad projects ranging from walls, sidewalks, bridges, dams and more. Moreover, with time and technological advancements, concrete has undergone numerous modifications based on project specifications.
Incorporating different additives into concrete offers unique characteristics such as resistance to frost and fire, increased density among others. The addition of reinforcing steel bars (rebars) enhances the tensile strength of concrete resulting in reinforced concrete; another widely used version of concrete in constructions.
Pro Tip: Proper measures must be taken while handling wet or fresh concrete since it can cause skin irritation if it makes contact with the skin.
Bricks – the building blocks of society, and also the easiest thing to throw at your ex’s car.
Among the various types of construction materials, a popular choice is the rectangular building blocks made of clay and shale. These units are informally called ‘Bricks‘ and serve various purposes in masonry construction. They offer natural insulation, soundproofing capabilities and are energy efficient. Bricks can be further classified into different categories based on their composition, size, strength, texture and color. Each type has its unique features that make it suitable for specific applications.
For instance, fire bricks are engineered to withstand high temperatures and can resist thermal shock without cracking or breaking apart. On the other hand, lightweight bricks are used in situations where load-bearing capacity is not needed or when a structure needs to reduce overall weight. Another example is facing bricks that have a smooth surface finish and can be used for aesthetic appeal or for decorative purposes.
Interestingly, modern brick manufacturing methods have resulted in eco-friendly solutions where alternative materials like recycled glass or plastic waste can be added to the mix. This results in higher performance standards, reduced environmental impact, cost savings as well as social benefits.
When selecting brick as a construction material, it is essential to consider factors such as climate conditions, project location as well as budget constraints. Generally speaking, comparing different types of bricks based on their technical specifications and durability ratings will help achieve long-lasting results while keeping cost-effectiveness in mind.
If you’re looking for tiles that can withstand the apocalypse, you’ve come to the right place.
Maximize your construction business’s potential with our competitive financing options
The following are various types of tiles for flooring, roofing or decorative purposes:
Metal Tiles: Use this type of material for your roofs with corrugated galvanized iron sheets or sheet aluminum panels. It is strong and lasts many years if installed correctly because it repels water or snow effectively.
To add to the above, each type of tile has specific features that set it apart from the others making choosing the ideal tile crucial towards creating your perfect space.
Considering the range of options available means there is always something to suit every taste; factors such as durability should also be noted when selecting a tile material. Remember to avoid by making choices based on fashion trends only as these change frequently, resulting in costly renovations.
Why break the bank on construction materials when you can just use bubble wrap and duct tape?
Construction material cost is affected by several factors that include transportation costs, market demand, processing fees, taxes, and quantity of material ordered. In this article, we will discuss the factors that affect construction material costs and how estimating them can help in planning and budgeting for construction projects.
Factor Name | Description |
Transportation Costs | Cost of transporting material from supplier to construction site |
Market Demand | Price fluctuations due to supply and demand |
Processing Fees | Cost of processing raw material into construction material |
Taxes | Applicable taxes on construction material |
Quantity Ordered | Larger orders receiving discounts and price reductions |
Other factors that can affect construction material costs include supplier location, material quality, and availability, which can change from project to project. It is essential to research and estimate these factors accurately to create a precise construction budget and estimate for material costs.
Pro Tip: When estimating construction material costs, always review multiple suppliers and compare their prices and offers to ensure the best deal for your project. Quality is like a good joke – if you have to explain it, it’s probably not there.
The characteristics of the construction materials that determine their usefulness and durability are a significant factor in their cost. Various attributes, such as strength, resilience, and sustainability, contribute to the quality of these materials. The higher the quality of the material, the more expensive it will be.
Besides quality, other factors may impact the cost of construction materials. For example, sourcing raw materials from distant locations may increase transportation charges and affect pricing. Additionally, high labor costs can also raise the overall cost of producing such materials.
It is crucial to understand that quality is not limited to just one aspect but encompasses different parameters like safety standards, environmental factors, certifications adherence and efficiency. The use of low-quality materials can lead to frequent repairs and replacements increasing costs in construction projects.
Pro Tip: Research well on the quality standards adhered by different suppliers before purchasing any building material to ensure long-term efficiency and reduced retrospective costs due to replacements or damages.
Apparently, too much of a good thing isn’t always a good thing when it comes to construction material quantity and cost.
The abundance of construction materials is a critical component affecting its cost. Different factors, including but not limited to the availability and demand for resources, influence the quantity of materials required to complete a project. Additional suppliers and production facilities can affect the amount of material available in a specific area, leading to fluctuations in price.
To provide an overview, we have constructed a table showcasing how the Quantity of materials impacts their cost. The table includes columns detailing Material Type, Availability and Demand Factors as well as Average Price Range Per Unit.
Material Type | Availability/Demand Factors | Avg. Price Range Per Unit |
---|---|---|
Lumber | Decreasing supply due to environmental regulations | $300 – $400 |
Steel | High demand from China, increasing transportation costs | $800 – $900 |
Concrete | Increased competition among producers | $220 – $250 |
Aside from supply and demand factors, there are unique impacts on different types of construction materials. For instance, lumber production faces increased scrutiny from environmental regulations causing less allocation to supply chains resulting in slower projects due to scarcity.
It is worth noting that Quantity also influences indirect costs associated with construction projects such as transportation and storage costs.
According to industry experts at BuildZoom, “Inflation has led to an increase of building material prices by an average of 17 percent.” As evident from our discussion above, Quantity plays a vital role in determining construction material prices as it affects both the direct cost of materials used as well as indirect expenses related to their transportation and storage. Unfortunately, construction materials can’t just Uber themselves to the job site, so transportation costs are a cruel reality of the industry.
The Logistics Expense Contribution to the Construction Materials Cost
Transportation Costs are a crucial factor that adds up to the overall expense of construction materials. The cost of transportation is not limited to fuel expenses but also includes truck/trailer rentals, salaries, toll taxes, insurance, and maintenance expenses.
To comprehend better, let’s look at an example table below that elucidates how transportation costs can affect the price of materials in different regions across the USA.
Materials | East Coast | West Coast | Mid-West |
---|---|---|---|
Lumber (per 1000 board ft.) | $800-$900 | $900-$1000 | $700-$800 |
Cement (per ton) | $130-$150 | $120-$140 | $100-$110 |
Steel Reinforcement (per ton) | $700-$800 | $750-$850 | $650-$700 |
Additionally, several external factors like traffic conditions or natural calamities like floods or landslides can severely disrupt the supply chain and result in inflated hauling expenses. In such cases, suppliers have to compensate for these additional expenditures by increasing their material’s selling price. It is essential to note that transportation costs may differ based on various other substantial factors such as distance between source and location of delivery, accessibility of the supplier, and fuel price fluctuations.
Therefore, to minimize logistics expense and overall materials cost, construction firms must collaborate with local vendors and opt for bulk purchases.
Don’t let transportation costs impact adversely; collaborate with accessible vendors for advantageous discounts and competitive prices.
Looks like Mother Nature was a union worker – she only delivers construction materials on her schedule.
Seasonal fluctuations in the availability of construction materials can add to their cost. The supply chain is impacted by natural disasters, changes in demand, and festive seasons. Here are some factors that influence seasonal availability:
Factors | Description |
Weather Conditions | Harsh weather like heavy rainfall and snow may hamper transportation and manufacturing processes. |
Production Schedules | The timing of production runs varies from factory to factory which can result in inconsistent stock levels. |
Demand Fluctuations | Fluctuations in demand during peak seasons like summer or winter can put pressure on supply levels. |
Apart from these factors above, labor challenges or equipment failures could also affect seasonal availability. It is essential to be aware of these variables when planning construction projects.
One way to overcome material shortages caused by seasonal issues is to source from different suppliers who operate all year round. Another method is preordering materials before their specific periods of scarcity. By understanding the seasonal patterns affecting construction material costs, we can plan our projects better and cut back on unnecessary expenses.
The high demand for construction materials is a reminder that even in the apocalypse, people still want to build their dream bunker.
The popularity of a particular construction material within the industry is one of the significant factors that can influence its cost. The higher the market demand for a particular material, the more expensive it will be due to increased competition and limited supplies. Materials like concrete, steel, and timber are known to be in constant high demand, making them on the pricier side.
In addition, fluctuations in market demands can also affect construction materials’ prices. For instance, if there’s a surge in building projects within an area or a region leading to an increase in demand for construction supplies, vendors may take advantage of that situation and raise their prices. Similarly, when there’s low market demand for some materials during a specific period, their costs might reduce since vendors would want to clear stagnant inventories.
Moreover, macroeconomic factors have been said to impact market demands for building materials – such as GDP growth rate and inflation rate levels. These social economy indicators cause changes in consumer tastes and spending habits resulting in a decline or an increase of vacant land rates.
Pro Tip: It’s essential to understand how market demand varies before you start any building project and purchase your required materials at competitive rates.
When it comes to estimating the cost of construction materials, it’s either you’re a wizard with numbers or you’re just winging it and hoping for the best.
To estimate the expenses of construction materials, various methods can be used. One such approach is to determine the cost of each material per unit and then calculate the total cost required for the project. Another is to consider the market prices of construction materials and estimate the cost accordingly.
In the following table, methods to estimate the cost of construction materials, along with their key features and considerations, have been presented with real-world examples.
Method | Key Features | Examples |
---|---|---|
Unit Cost | Cost of each material per unit is calculated | $2 per square foot for flooring tile |
Market Rate | Cost is estimated based on current market prices | $50 per bag of cement |
It is crucial to note that the type and quality of materials used can significantly impact the cost estimate. It is advisable to consult with industry experts or suppliers to get accurate estimates and compare prices from several sources before making any purchase decisions.
Pro Tip: Consider purchasing materials in bulk, as it can often lead to cost savings in the long run. Want to know the cost per unit of construction materials? Just remember, it’s like buying snacks in bulk – always check the expiration date before committing.
One way to estimate the expense of construction materials is through determining the ‘Price Per Item.’ This refers to the cost of a single unit of an item, such as a bag of cement or a box of tiles. By calculating the price per item, one can better understand how much they need and how much it will cost them.
A table can be created to showcase the ‘Unit Price’ for different construction materials. The table can consist of columns such as the material name, quantity needed, unit type (e.g., meter, square feet), unit price per item or amount (depending on the category), and total price. For example, concrete may have a unit type of cubic meter with a unit price per item/amount ranging from $80-$100. This information can be beneficial when estimating overall expenses for a construction project.
It’s essential to note that some suppliers may provide different pricing structures based on bulk purchasing, location or specific levels of quality. In these cases, an estimator needs to consider those variables carefully before adding those factors into any calculations.
Pro Tip: Before purchasing or making any decisions about particular materials, make sure to double-check with multiple suppliers for pricing fluctuations in your area as this could affect your final costs significantly.
If you’re ever feeling light on cash, just remember that construction materials are priced by weight, so you can always sell yourself on a scale and make some extra dough.
Calculating the expenses of construction materials based on their weight is an effective way to determine the cost. This approach, which can be referred to as “Weight-Based Cost Estimation,” involves evaluating the price of construction materials per unit of mass.
To exemplify, let’s consider some common building materials such as steel, concrete, and asphalt. Assuming that the cost per unit mass for steel is $1.20, concrete is $0.09, and asphalt is $0.35 per pound; we can establish estimates for the costs by multiplying the weight of each material required by its respective unit rate.
The Table below represents a sample calculation of Weight-Based Cost Estimation:
Construction Material | Weight (lbs) | Unit Rate ($/lb) | Estimated Cost ($) |
---|---|---|---|
Steel | 500 | 1.20 | 600 |
Concrete | 8000 | 0.09 | 720 |
Asphalt | 12000 | 0.35 | 4200 |
It’s important to note that this method should only be used in combination with other cost estimation methods to get more precise estimations.
While this technique provides a reasonable estimate of construction material costs, it does have limitations related to various variables that could affect project timelines and product availability. To overcome these limitations, using additional methods such as Quantity-based, Assembly-based or Location-based costing methodologies would provide more precise estimations.
For example: breaking down projects into phases or assemblies may allow you the opportunity to achieve more accurate cost estimates using assembly-based costing strategies while maintaining control over overall budget allocation for a project by appearing more detailed in nature – thus perhaps allowing for better cost-saving decisions on a micro-level within individual aspects of construction.
If you think buying construction materials by volume is expensive, just wait until you see the cost of buying them by weight.
The pricing of construction materials based on their volume is a valuable method to estimate costs. This approach calculates the total cost of a material needed for construction by determining how much volume is necessary and multiplying it by the unit price.
To illustrate this, let’s delve into the ‘Cost by Volume’ variation of semantic NLP. Consider a scenario where concrete is required for building a foundation. The table below presents the average cost of one cubic meter (m3) of concrete in different regions.
Region | Cost of 1 m3 of Concrete |
---|---|
North | $200 |
South | $210 |
West | $220 |
It is essential to note that these costs are subject to change based on factors such as inflation, transportation, and market demand.
When planning a build project, conducting research and comparing cost estimates will provide insight into which materials are economically feasible.
As an example, a contractor had initially sourced her concrete from a supplier located in the South region at $210 per cubic meter. They managed to find a new supplier located in the North region who charged only $200 per cubic meter, resulting in significant savings for the contractor over time.
Overall, calculating construction material costs using the volume method can assist in creating accurate budgets and uncovering cost-saving opportunities. Who knew that calculating the cost of construction materials by surface area would require more math skills than my high school geometry class?
One way to estimate the cost of construction materials is by calculating it based on the surface area of the project. This method can provide a rough estimate but may not account for other factors such as labor and transportation costs.
For example, suppose we want to calculate the cost of building a driveway with an area of 1000 square feet using concrete. Based on national averages, the cost would be around $4 to $8 per square foot. Therefore, the estimated cost for our project would be between $4000 to $8000.
To further break down the cost by surface area, we can create a table to showcase different costs for various sizes of projects. For instance:
Surface Area Range | Cost per Square Foot |
---|---|
Less than 500 sq ft | $5 – $10 |
501 – 1000 sq ft | $4 – $8 |
1001 – 1500 sq ft | $3 – $6 |
More than 1500 sq ft | $2 – $5 |
It’s essential to note that these prices are specific only to concrete; each material has its own price range.
It’s also crucial to understand that hidden or extra costs exist that would not appear in this table, leading to a higher overall expense.
A construction worker shared his experience when estimating costs by surface areas for outdoor kitchen installations. The client requested an outdoor kitchen with approximately 200 square feet of surface area. After preparing different estimates and proposals based on different construction materials and finishes, he found that calculating the cost based on surface area alone is one element that affects his proposal’s accuracy since he had discovered additional costs after he began working on the project.
Get ready to channel your inner Bob the Builder with these helpful tools and resources for estimating construction material costs.
The method used for estimating construction material costs varies between different construction projects and depends on the size, location, and specifications of the project. To make it easy, there are some tools and resources available that can help us to estimate construction material costs. This article examines some of the popular methods and tools that can be used for estimating construction material costs.
Tools and Resources for Estimating Commencement Material Costs
Method | Description | Advantages | Disadvantages |
---|---|---|---|
Historical Data | Using previous data from similar construction projects | Quick and easy | Data may not be up-to-date |
Online Calculator | Software that calculates estimates based on entered information | Saves time, accurate | Calculations may not be completely accurate |
Takeoff Software | Digitized drawings used for material quantity takeoff | Accurate, saves time | May be expensive |
Vendor Quotes | Requesting quotes from vendors or suppliers | Provides accurate pricing | Time-consuming, quotes may not include all materials |
When estimating construction material costs, it is important to consider unique project specifications that may impact pricing, such as time constraints, materials availability, location, and market trends. These factors can affect the cost of materials and should be included in estimations.
Historically, construction material cost estimation was a manual process that required extensive research and analysis. With the rapid development of technology, several software tools and online resources have been introduced to simplify the process. These tools allow for quick and accurate cost estimations, which help to save time and increase construction project efficiency.
“Who needs a math degree when you have online calculators to estimate construction costs? #EasyPeasyBuildingSqueezy”
Assisting with the computation of construction materials, digital calculators are practical tools accessible on the internet.
Calculator Name | Purpose | Source/Website Link |
Concrete Calculator | Helps in determining how much concrete is needed for a project. | |
Painting Calculator | Determines the amount of paint required any painting project. | |
Spray Foam Insulation Calculator | Calculates the amount of foam needed for specific spray form insulation tasks. | |
Flooring Calculator | Aids in estimating the cost of tiles and grout necessary to cover a particular area. |
Ensuring accuracy is crucial when using online calculators; thus, double-checking inputs narrows chances of inaccuracies.
To explore other options for obtaining an estimated cost, there are various mobile applications available to aid in pricing construction materials.
Cost guides: because nothing says ‘fun weekend reading’ like a list of construction material prices.
When it comes to determining the cost of construction materials, having access to reliable and up-to-date information is key. With that in mind, we turn to resources that provide insight into pricing opportunities for a variety of materials needed to complete your project.
One such resource is the ‘Estimating Cost Guides’ or commonly known as the ‘Pricing Manuals’. These guides present a comprehensive list of costs for various building materials applicable to different regions based on your requirements. They consist of tables containing price estimates for materials and may come with installation costs.
We have created a sample table below, outlining estimated prices of some common building materials:
Material | Average Cost per Unit |
---|---|
Concrete | $100 – $200 / cubic yard |
Roofing | $120 – $300 / square |
Lumber | $3 – $12 / foot |
Flooring | $3 – $10 / square foot |
It’s important to note that material prices can vary depending on the region you’re in, so be sure to use guides specific to your area. Many of these resources are updated annually or bi-annually, so keep an eye out for updated versions.
In addition to estimating cost guides, manufacturers’ data sheets are also helpful when creating budget outlines. This information provides details about specific products and their pricing. By knowing exactly what you need, you’ll be able to get more accurate quotes from suppliers.
A little piece of history about estimating cost guides; earlier versions were printed every two years as books that would cover all building costs in one guide. Over the years they evolved into comprehensive online databases with detailed search functions allowing users to find specific types of material quickly and efficiently.
By utilizing these resources, you’ll have the ability to determine accurate material costs early on in your project planning process without any surprises in store down the road.
Prepare your wallets, folks! Here’s a sneak peek of the materials that will drain your bank account.
When planning a construction project, it’s important to have a clear idea of the materials needed and how much they will cost. Here are some useful resources for creating lists of materials required for your particular project:
Finally, when preparing a material list, it may be helpful to keep in mind any unique features or design elements desired for your project. This additional consideration will ensure that you purchase everything you need while avoiding costly mistakes or omissions.
Pro Tip: When creating material estimates, it’s important to consider both immediate needs and long-term maintenance requirements to make informed decisions about which products best fit your budgetary constraints.
Finding local suppliers and contractors: because sometimes it’s easier to outsource than to operate heavy machinery while blindfolded.
In the construction industry, it is essential to have access to reliable sources for materials and labor. The regional supply chain plays a vital role in this regard. Here are a few factors to consider regarding the local suppliers and contractors that you should keep in mind while estimating costs:
It is crucial to have stable supplier networks due to several advantages such as accurate cost estimation, better project management, and timely completion of projects. Building healthy relationships with regional contacts can also help obtain discounts on purchases and receive tips on where to find rare supplies.
One unique detail is that contacting or visiting the regional supply chain first before finalizing any estimates can save you vast amounts of money because you will be aware of real-time prices prevailing in the market. The establishment of a strong rapport can also allow you room for negotiation when making large orders or obtaining quotes from competitors.
In the past, many contractors have undergone severe time constraints and budget constraints when they failed to procure raw material at reasonable lead times or did not explore a comprehensive range of suppliers.
Therefore, establish good communication with your regional suppliers since it can save you substantial amounts while being assured of quality deliveries.
Saving money on construction materials is easy, just hire a magician to magically make them appear out of thin air.
Managing Construction Material Costs: As a project owner or contractor, controlling the budget is crucial. Here are effective ways to manage construction material costs.
Tips to Manage Costs of Construction Materials:
Unique Details: By negotiating with suppliers and building strong relationships, you can often secure better prices and more favorable terms. Additionally, investing in technology can reduce material waste and lower overall construction costs.
Story: A construction firm was hired to build a new school, with a strict budget and timeline. The project manager researched various materials and found that using precast concrete would save time and money while providing durable results. By incorporating this material in the building design and working with a trusted supplier, the project was completed efficiently and below budget.
Remember, failing to plan ahead is planning to spend more on construction materials than you’d like to admit.
In order to effectively manage construction materials costs, one should engage in Strategic Planning. This involves more than just determining a budget but encompasses an entire methodology. Follow these six steps for effective planning and cost management:
It’s essential to stay proactive when managing costs in construction projects by implementing efficient strategic planning methods throughout each stage of the process continually. By staying vigilant with communication between all stakeholders can further make significant cost-effectiveness while increasing efficiency overall.
Buying in bulk may not guarantee success, but it does guarantee that your construction site will look like a hoarder’s paradise.
Bulk Purchasing for Construction Materials
Maximizing your savings on construction materials can start by bulk buying. Here are 5 ways how ‘Bulk purchasing’ can drastically cut down your costs:
Furthermore, it is a wise move to source your material from one supplier or manufacturer so that you won’t have to waste time and money dealing with multiple entities.
On top of these benefits, buying in bulk also mitigates the possibility of running out of essential resources mid-construction, which may lead to costly delays and complications.
If you want to avoid missing out on the massive cost-saving potential of purchasing construction materials in bulk, make sure to scout for reliable suppliers and plan ahead.
Buy as many items as possible within your budget constraints in order to minimize overall project expenditures.
So what are you waiting for? Start talking to suppliers now!
If you don’t negotiate with suppliers, you might as well build your house out of gold instead of bricks.
To manage the costs of construction materials, it is important to find ways to negotiate with suppliers in an effective manner. This can help you secure better deals and save on expenses.
Here is a five-step guide for negotiating with suppliers:
Suppliers are always willing to hear from contractors who want better deals while maintaining quality services. An extra tip: Never fail to value the time of suppliers during negotiations because they generally have limited profit margin per unit sold but gain resources through repeat business deals!
Who needs traditional bricks and mortar when you can build your house out of recycled plastic bottles? Reduce, reuse, and build to amaze.
Buy as many items as possible within your budget constraints in order to minimize overall project expenditures.
So what are you waiting for? Start talking to suppliers now!
If you don’t negotiate with suppliers, you might as well build your house out of gold instead of bricks.
If you want to cut down construction costs, there are many ways in which you can save money on the materials used for construction. Consider exploring alternative materials that can offer similar, if not better, performance at a reasonable cost.
Here are six points to help you take full advantage of using alternative materials:
Choosing alternative materials would not only make your construction project eco-friendly but also prove financially beneficial in the long run.
Remember that quality should never be compromised over quantity while cost-cutting during construction. Don’t compromise on essential features of your building just to save money. Therefore, it is crucial to evaluate all alternatives carefully and choose the appropriate one that meets your needs without breaking the budget.
Therefore, don’t miss out on exploring new ideas while choosing building materials. Seize an opportunity to build efficiently with proper planning and research.
Tracking costs is like monitoring your ex’s social media – it’s time-consuming but you’ll feel more in control when you know where the money is going.
To effectively handle the financial viability of a construction project, it is important to stay vigilant and keep track of expenses. This involves closely monitoring and scrutinizing the costs incurred for purchasing construction materials, and developing strategies to optimize spending.
In order to ensure that your construction project stays within budget, be sure to implement these measures at every stage of the project.
In order to ensure that your construction project stays within budget, be sure to implement these measures at every stage of the project. Analyzing costs continuously can prevent unexpected expenditure and improve overall efficiency in managing your budget.
Don’t let financial mismanagement impede your construction projects’ success. Employing these techniques can save you time and money in addition to increasing profit margins. Don’t wait, start now!
Several factors can affect the cost of construction materials, including supply and demand, availability, location, and the current state of the economy.
To estimate the cost of construction materials for a project, you will need to assess the required quantity of each material and multiply it by its price per unit. You can obtain the price of each material by contacting local suppliers or sourcing it online.
Common mistakes to avoid when estimating the cost of construction materials include not considering all required materials, failing to account for waste or loss, not factoring in delivery costs, and failing to update your cost estimates as prices change.
Both options have their advantages and disadvantages. Buying locally allows you to inspect materials and avoid shipping costs, while buying online can often provide a wider selection and lower prices. Assess your needs and budget to determine which option is best for you.
No, you do not need to be an expert to estimate the cost of construction materials. However, it is important to have a basic understanding of the materials required for your project and to obtain accurate prices from reliable sources.
Here I am going to share some steps to get your construction cost estimate report.
You can send us your plan on info@estimatorflorida.com
Before starting your project, we send you a quote for your service. That quote will have detailed information about your project. Here you will get information about the size, difficulty, complexity and bid date when determining pricing.
We do construction cost estimating and prepare a detailed report for your project. At last you finalize the report and finish the project.
561-530-2845
info@estimatorflorida.com
Address
5245 Wiles Rd Apt 3-102 St. Pete Beach, FL 33073 United States
561-530-2845
info@estimatorflorida.com
Address
5245 Wiles Rd Apt 3-102 St. Pete Beach, FL 33073 United States
All copyright © Reserved | Designed By V Marketing Media | Disclaimer
IMPORTANT: Make sure the email and cell phone number you enter are correct. We will email and text you a link to get started.
By clicking “I Agree” above you give Estimate Florida Consultin express written consent to deliver or cause to be delivered calls and messages to you by email, telephone, pre-recorded message, autodialer, and text. Message and data rates may apply. You are able to opt-out at any time. You can text STOP to cancel future text messages.