A Wining Cost Estimate That Helps You To Win More Construction Projects
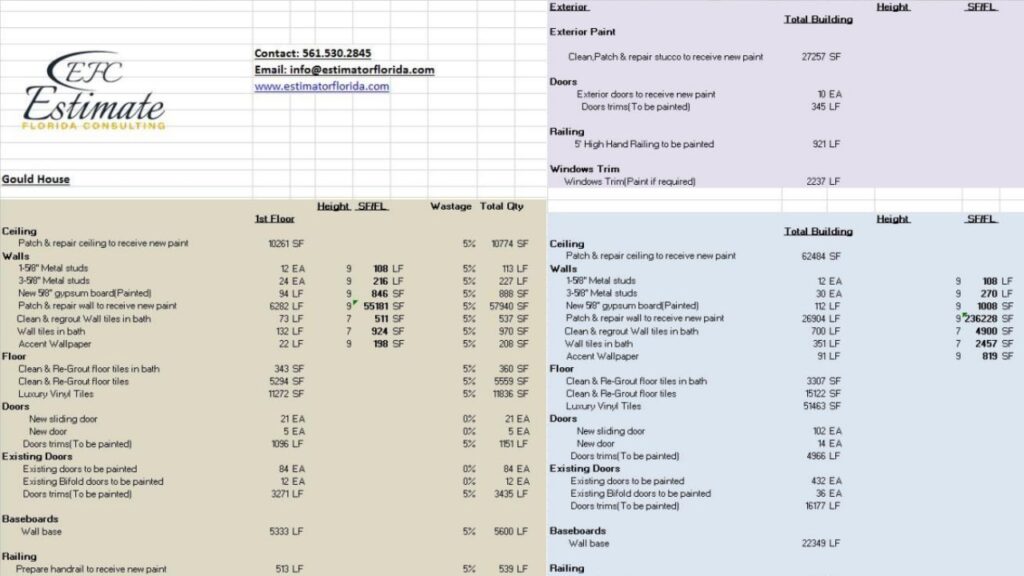
$20 to $100 Per Square Foot
$15 to $70 Per Square Foot
$25 to $50 Per Square Foot
Masonry work is an old craft that has been used for thousands of years. The interlocking units of masonry were typically made from stone and mortar, but over time it has evolved to include other materials like concrete, wood, or clay.
Masonry cost estimating must take into consideration wall reinforcement, mortar, cement and lintels, and flashing.
The most direct means of determining the number of concrete masonry units needed for any project is to simply determine the total square footage of each wall and divide by the surface area provided by a single unit specified for the project.
Call Now: +1(561)530-2845
It’s easy to figure out – simply take the total amount of square feet that were measured for the project, then divide the total amount of square feet by the coverage rate of the material.
Call Now: +1(561)530-2845
Call Now: +1(561)530-2845
Brick Siding average Installation Costs for a 2,500-square-foot home is $13,000 to $26000, including labor and materials.
Call Now: +1(561)530-2845
When allowing for an allowance during the estimating process, it is very important to build in a 10-percent cushion. It may surprise you that this amount is applicable to over 90 percent of all estimates. By including this extra ten percent, ensure given ample room within estimate to cover any last-minute add-ons or any problems that can arise during the job.
Prepare for estimating brick wall masonry by measuring the length and height of the proposed wall. Multiply the quantity of materials needed per square foot by the net wall areas.
For example, if anyone needs 1.5 bags of cement to finish 3 feet off the ground and 4 feet high, multiply 1.5 (materials needed) x 20 (20 bags are required for a 20 x 20-foot wall) = 30 total bags of cement.
Take measurements and make a drawing of the job to estimate what is required for brick work. Estimating brick work is done by measuring the surface in square feet and dividing that figure by 27 Bricks per cubic foot of brick.
Considerations include the amount of straight walls, pilasters, or other items that may be necessary to complete the project. Estimates will also include the number of bricks needed. We have an on-site showroom where we will help decide which material is best suited to needs.
The cost of materials for brick masonry work can be calculated by adding the costs of mortar, cement, sand and what it would take for a bricklayer to lay a wall. will need to make an allowance for tools such as a cement mixer and trowels. Adding 5 percent to each type of material will give a cushion against unforeseen accidents.
Building a brick fence costs $65 to $250 per linear foot for 3’ to 6’ tall walls or $24 to $44 per square foot of wall face. Brick wall fencing costs depend on the design when adding posts, wrought iron, gates, or stone caps.
Brick fences are a popular choice for homeowners who want to add both security and aesthetic value to their property. The cost of a brick fence can vary depending on several factors including the height, length, and design of the fence.
The height of the fence is one of the biggest factors that affects the cost per square foot. The taller the fence, the more bricks and labor are required to build it, which increases the cost. Additionally, the length of the fence also plays a role in the cost as more materials are required to build a longer fence.
Masons can mix and match brick with other fence materials:
Interior brick wall installation costs $1,200 to $2,800 on average or $10 to $22 per square foot, depending on the brick type and installation method. Contractors typically adhere thin-brick veneer to existing walls or install a single layer of non-loadbearing face bricks.
Type | Cost per square foot |
---|---|
Thin-brick veneer | $10 – $22 |
Face brick wall | $15 – $22 |
We help contractors to win more bids with accurate estimate reports.
Upload Your PlanThe labor cost to build a brick wall is $50 to $130 per hour. Brick masonry labor rates are $9 to $22 per square foot on average. The total labor charge for brickwork depends on the wall thickness, location, wall design, supplies needed, and the mason’s skill level.
Labor rates | Average cost |
---|---|
Per hour | $50 – $130 |
Per square foot | $9 – $22 |
Per 1,000 bricks | $400 – $1200 |
Building a brick garden wall costs $18 to $44 per linear foot for 1’ to 2’ tall walls or $18 to $24 per square foot of wall surface. A 10′ to 25′ brick garden wall costs $160 to $1,200 to install. Most garden walls are one brick thick without a foundation.
Length (linear feet) | Average cost |
---|---|
10’ | $160 – $450 |
25’ | $395 – $1,200 |
50’ | $780 – $2,300 |
Rock walls are a great addition to any property. They provide a natural and rustic look while also serving as a practical retaining wall. The cost of a rock wall per square foot can vary based on a number of factors including the type of rock, size of the wall, and location.
On average, the cost of a rock wall per square foot can range from $30 to $85. This cost includes the materials and labor required to build the wall. The cost can be higher or lower depending on the factors mentioned above.
One of the biggest factors that affects the cost of a rock wall is the type of rock being used. There are a variety of options to choose from including natural stone, boulders, and manufactured stone. Natural stone is the most expensive option as it requires a lot of labor to quarry and cut to size. Boulders are the least expensive option as they are typically sourced from nearby areas and require minimal cutting.
Masonry type | Cost per square foot |
---|---|
Natural stone wall | $40 – $95 |
Manufactured stone wall | $30 – $75 |
Understanding Concrete Block Masonry is essential for anyone involved in construction or building projects. Concrete block masonry refers to the construction method using concrete blocks as the primary building material, known for its durability and versatility. To grasp this concept fully, one must delve into the characteristics and properties of concrete blocks, including their composition, strength, and various sizes available in the market.
Additionally, a comprehensive understanding involves recognizing the different types of concrete block masonry, such as load-bearing and non-load-bearing walls. Familiarity with these fundamentals lays the groundwork for accurate estimations, enabling professionals to assess material and labor requirements effectively. Ultimately, a solid grasp of Concrete Block Masonry is pivotal for successful project planning, execution, and cost estimation in the construction industry.
Long-term savings through quality masonry work: Recognizing the financial benefits of investing in quality construction.
Quantity estimation for brick masonry is done by estimating the number of bricks and mortar to make 1m3 of brick masonry. Cement, sand, and water are required in proportion to the number of bricks used to make brick masonry.
For example, assume that 1m3 of brick masonry has 480 bricks and 0.25m3 of cement mortar. Quantity Estimation Calculation Example: Let us calculate the quantity estimation for brick masonry. Determine the quantity of bricks and mortar to make 1m3 of brick masonry: We have already discussed how to calculate the quantity of cement and sand for mortar. Then, for 480 bricks, we will need 494 bricks.
Building a home is one of the most important stages in your life, therefore deciding on which material to be used is crucial in obtaining your dream home. Preference plays a major role in this choice but many other factors should be taken into consideration also. Stone masonry is one of the many options available and it comes with both its advantages and disadvantages during construction.
To ensure you get the strongest outcome for building is to choose the stone as a construction material. Stone has an average compressive strength of about 104.9 MPa meaning it can withstand a larger amount of weight within its structure. This makes it a popular choice over other masonry materials while still maintaining a high aesthetic appearance.
Naturally resistant to moisture, stone masonry can be used for constructions that will be subjected to the elements of weather throughout the year. And unlike most other materials, the stone is not susceptible to water absorption which means any problems related to dampness are one less thing the construction team has to worry about.
Stone masonry is a type of construction that has proven to be the most durable. This construction is excellent for home foundations, veneers, and stone substrates. It provides great strength to the structure which makes it last over years without showing signs of damage. One benefit of this construction is that it does not require regular maintenance, unlike most other structures and surfaces. Through normal wear and tear its beautiful feature will still be in place.
Stone is a versatile material that can be used for a whole host of construction applications. It comes in a wide variety of textures, colors, and sizes. This makes it possible to create almost any imaginable design. Stone is durable and easy to maintain, which means it will not require much upkeep.
Using stone masonry as the primary method of construction is something that has been referred to as a “durable building material” because of its great resistance to the destructive forces of natural elements such as wind, rain, and extreme temperatures. You will not have to worry about maintenance on buildings if they are built using stone masonry because the houses made using this method require little attention in order for them to remain in good condition.
We help contractors to win more bids with accurate estimate reports.
Upload Your PlanStone is heavy and thick walls produce. This makes it difficult to reduce the floor spacing advantages, such as high load-bearing capacity, thermal insulation and fire retardancy. Also bulkiness makes handling quite difficult.
Required Skilled Workers is used when the construction of a residential building must take place and the homeowner is to remain in the property. This method requires the entire structure to be raised off the ground, either by stilts, platforms or concrete columns. It is often used for homes that are located in areas prone to flooding.
The biggest advantage to this kind of construction is its ability to create living conditions in places that would otherwise be uninhabitable. It can also increase the potential of land that may have been previously considered unsuitable for building purposes. However, this technique can prove dangerous to both workers and homeowners alike when not properly executed or maintained.
Handling stones of this nature can be challenging. Accidents can easily occur due to the thickness and weight. More care is needed to ensure the safety of people, materials, and equipment.
Handling construction costs for stone masonry is a bit on the higher side because of the skilled labour required, expensive equipment to be used and many other costs incurred. At the same time, when handled efficiently with proper workers and without error, the costs can work out to be quite economical.
Though the construction is slow, it has the advantage of withstanding erosion for a long time. The stones are also easier to be taken and fit in their desired location as compared to other construction methods. These stones are also decorative and attractive enough to be used as landmarks.
Contractors can win more bids with the right strategies of bidding. We have shared secrets for residential and commercial bids.
A dry-stack stone wall costs $30 to $80 per square foot installed for freestanding structures, depending on the stone type, size, and local availability. Contractors typically stack these natural and irregular-shaped stones on a compacted base without using mortar.
Additional finishing options include:
Masonry labor rates are $50 to $120 per hour and vary according to the location and skill level of the mason.
Pressure washing costs $0.45 to $0.87 per square foot. Some masonry walls need cleaning before repair work starts.
Detailed or patterned brickwork increases labor time.
Testing costs $170 to $347 to match the rest of the existing mortar in the brick structure.
Mortar ingredient analysis costs $340 to $540 for historic building repairs to avoid further damages.
Detailed or patterned brickwork increases labor time.
Waterproofing new brickwork costs $2 to $10 per square foot for blocking exterior moisture.
Flashing repair costs $200 to $500 on average. Masons fix or replace flashing to stop future damages from water leaks.
Labor costs increase by 20% to 40% for scaffolding and working in hard-to-reach places.
A permit costs $120 to $280 for masonry repair or replacement work, depending on the location and extent of the damages.
Here I am going to share some steps to get your masonry estimate report.
You can send us your plan on info@estimatorflorida.com
Before starting your project, we send you a quote for your service. That quote will have detailed information about your project. Here you will get information about the size, difficulty, complexity and bid date when determining pricing.
We do masonry estimating and prepare a detailed report for your project. At last you finalize the report and finish the project.
561-530-2845
info@estimatorflorida.com
Address
5245 Wiles Rd Apt 3-102 St. Pete Beach, FL 33073 United States
561-530-2845
info@estimatorflorida.com
Address
5245 Wiles Rd Apt 3-102 St. Pete Beach, FL 33073 United States
All copyright © Reserved | Designed By V Marketing Media | Disclaimer