A Wining Cost Estimate
That Helps You To Win Framing More Construction Projects
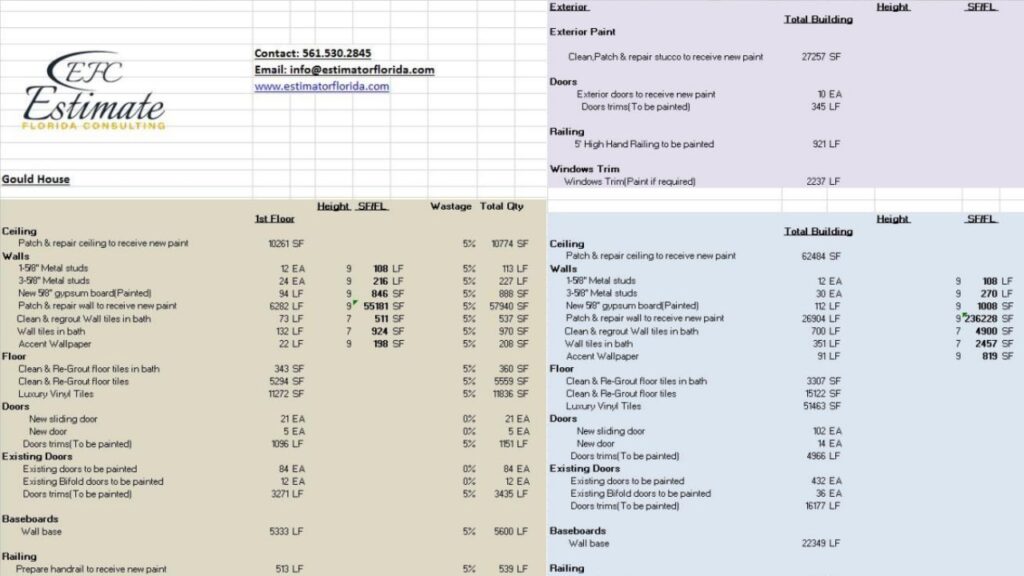
Framing estimation is the process of calculating the cost and supplies needed for constructing a frame in a building.
To understand it, create a table with the components involved, such as wood type, studs, headers, plates, and nails. Plus, list the price per unit or bundle of these items to figure out the total cost.
Besides, take into account labor costs, transport expenses, and permit fees when reckoning framing costs accurately. Planning well helps complete projects on time and within budget.
Don’t forget vital information when estimating framing. Understand all aspects to make a wise decision.
Be alert to potential waste or missed opportunities. Following the right guidance prevents issues later and raises profits.
If you’re missing any of these materials, forget about building a house of cards.
To ensure your framing project goes smoothly, you need the right tools and materials. With the necessary tools and materials, you can take accurate measurements, hammer in nails effectively, saw correctly, and work with high-quality lumber. Measuring tape, hammer, saw, nails, and lumber are the essential components of your framing toolkit.
The distance-measuring instrument is an important tool for carpenters and builders. It’s used for more than just measuring lengths or widths.
It can also be used to measure body proportions for clothing alterations. Knowing how to read it accurately is key. Pro Tip: Make sure there’s no slack in the tape, as it may lead to sizing errors. If you want your DIY project to turn out perfectly, don’t forget the hammer – it can work wonders!
A striking device is an absolute must-have for your kit! It’s known as a ‘hammer’ because it pounds nails into any sturdy surfaces with ease. This time-tested tool makes intensive projects stress-free and provides a helping hand.
Choose hammers that suit different tasks – lightweight for delicate applications and heavier for geological operations or demolition. Check the grip for comfort and precision. But remember – misuse can cause bodily harm. So, wear protective clothing for safety. Don’t miss out on opportunities or work under unfavorable conditions – having multiple types of hammers is key. Their versatility ensures proficiency in various situations. Feeling saw-ry for those without this tool!
A hand-held saw: the perfect tool for woodworking! It’s versatile and can make both straight and curved cuts. To choose the right blade, consider the type of cut, as well as the material’s hardness and thickness.
The perfect saw for a project can make or break the final result. Circular saws are ideal for quick, long cuts. Jigsaws can handle intricate angles and curves. Meanwhile, band saws are great for massive workloads, like resawing lumber or cutting awkward shapes with accuracy.
The number of teeth on a saw affects the finish. More teeth = finer cut, less sanding required. Fewer teeth = rougher finish, but faster cut through thicker materials. Safety first! Always wear protective gloves and goggles when working with any saw.
Frank, a carpenter from Texas, remembers his first day on the job. His boss had given him all the power tools, but this was his first time using a band saw. He was so nervous! But, thankfully, his boss showed him how to use it safely – and everything went perfectly.
Why settle for a hammer when you can pretend you’re Thor and use a nail gun instead?
When it comes to joining materials, ‘nails’ are a must. Selecting the right type of nail is important. It should suit the thickness, length and type of material you’re working with. Common nails are good for general framing, but roofing nails are best for shingles and other roofing materials.
Ensure the nail is the correct size – too short or thin and it could cause instability or damage the materials. Consider the surface quality of the materials too. Some may need specific types of nails or coatings to avoid corrosion and keep them stable.
Adhesives and joint compounds can be added too, to secure the nails and stop any wobbling. Have a variety of sizes and types of nails on hand for all projects. Before you go shopping, make sure you have the right tools!
Structural materials are a must for construction. This includes wooden planks. It’s important to check the grade of the wood, from A to F, with A being best. Buying all the lumber upfront is wise, to avoid delays and added costs.
A contractor friend was working late one night to frame a two-story building with scrap lumber. When they came back, almost all their materials were gone! This caused further delays and expenses to get more materials. If framing had a personality type, it would surely be Type A – all straight lines and perfect details.
To understand the different types of framing in your building project, turn to the section on Types of Framing in the complete guide on How to Estimate Framing. This section breaks down the three main components: Wall Framing, Roof Framing, and Foundation Framing. By analyzing each sub-section, you can determine the specific framing needs for your project and make a more informed estimate.
Wall Framing requires expertise! To make a structure that’ll stand for decades, follow these 5 steps:
Each step is important. Walls can be strong if framed correctly. Wall Framing is essential for structural integrity. Otherwise, projects may fail.
I saw this firsthand on vacation in Utah. A hotel building collapsed after just 3 months due to incorrect Framing. Even small projects need experts. Roof Framing is no exception – it’s the only time you’ll want to be above the ceiling!
We help contractors find new customers with high-converting websites and locally targeted niche-specific lead-generation programs. You’ll never need to worry about running out of work again! We focus on quality over quantity with our leads for contractors.
Creating the structural frame that supports a building’s roof is known as roof framing.
Here’s a 5-step guide for it:
A key part of roof framing is selecting materials, such as wood or steel, that will be durable and stable in bad weather.
Pro Tip: Installing insulation properly can boost energy efficiency and reduce heat loss from the roof structure. This makes it a must in any roofing project.
Remember, if your foundation framing is weak, your house may not stand!
Foundation Framing is vital for strength and stability. Here are 5 steps that will help guide you through the process:
Bear in mind that different types of structures may require different methods or materials. Also, accuracy in measurements is key at all stages above Foundation Framing. Lastly, check your tape measure before you begin!
To measure for wall framing with accuracy, you need to know the correct dimensions. In order to frame your wall, you’ll need to measure its width, height and the total available stud spacing. This guide will walk you through each of these sub-sections, helping you to accurately estimate framing and ensuring that your wall is built to the correct specifications.
Estimating Wall Width:
To estimate wall width, calculate the horizontal distance between the two walls that contain the opening.
The table below shows different wall thicknesses and the related property values. These figures can provide essential info to select the right framing for a particular structure.
Wall Thickness | Property Value |
---|---|
2 Inches | Standard Studs |
3 Inches | Double Studs |
4 Inches | Boxed Headers |
Remember, external walls need thicker framing than internal walls as they experience extra weight and load from weather risks such as wind, rain, or snow.
To get the best result while constructing your wall assembly system, make the task simpler to reduce waste and mistakes by using pencil drawings on graph paper. Also, plan where outlets will go so that you avoid making holes after mounting drywall. No need for a tape measure when you can just lean against the wall and be done with it!
Accurately framing a wall is critical. To do this, measure the height of the wall. Vertical measurements are necessary to determine the length of studs and the location of headers and plates.
Get a measuring tape and level. Start in one corner and measure straight up to the ceiling. Measure several points along the wall, as walls can be uneven due to floor or ceiling irregularities. Record the measurements at each point.
For sloping ceilings, measure both the high and low ends of each stud’s intended location. Then, adjust the measurements accordingly.
Double-check your measurements for proper stability. Confirm the finished heights according to building codes. Enjoy spacing out the studs – unless you’re a horse!
Stud Placement is essential for wall framing. Studs are vertical pieces of framing that hold up the weight of a structure and transfer it to the foundation. The gap between two studs is known as stud spacing. For a secure structure, you need proper stud spacing. Commonly, it’s either 16 or 24 inches from the center of one stud to the center of the next.
The chart below outlines the spacing for different building types:
Building Type | Stud Spacing (OC) |
---|---|
Residential | 16 inches |
Commercial | 24 inches |
Industrial | 48 inches |
Other factors to consider when determining stud spacing include wall height, load-bearing capacity, wind resistance, insulation thickness, and drywall sheet sizes. Plus, you never know who invented this technique or when it was first used in construction!
Roof framing is even more difficult. It’s like trying to measure a jigsaw puzzle made of triangles.
To measure for roof framing correctly, you need to assess the roof width, roof pitch, and rafter spacing. Each of these variables plays a crucial role in determining the overall stability and durability of the roof. This section in “How to estimate framing complete guide step by step” with the title “How to measure for Roof Framing” will provide you with a step-by-step guide to measure your roof framing efficiently.
Determining the horizontal span of a roof is key in roof framing. You need to have the right width to make sure you choose the right materials, support the structure, and have stability. To measure it, figure out the distance between the two opposite ends of the house where you plan to install the roof.
You must consider overhangs, gutters, and other protrusions that can change the measurements. Use a laser range finder or tape measure to get accurate readings of the width. Don’t mix up this measurement with the length or depth, which is the extension from front-to-back.
It’s a good idea to measure twice before making any decisions about the installation. Get advice from roofing professionals for more help. Home Advisor states that “the average cost to install a new roof ranges between $5,353-$11,012,” so it’s important to measure correctly before buying roofing construction materials.
When it comes to roof pitch, steep is good, but not too steep that you need a ladder.
Roof Angle is the degree of slope on a roof. It’s important for choosing and placing roof frames. To calculate Roof Angle, measure the horizontal distance for every 12 inches of vertical rise. A 6-inch rise is called a 6:12 pitch and an 18-inch rise is an 18:12 pitch.
Using a table can help with accurate framing dimensions. In the Roof Slope table, list the pitch size horizontally and vertically, plus the ridge board length, hip/valley rafter length, common rafter length and angle cuts. For example, an 8:12 pitch with a 10-foot two-inch cantilever common rafter run needs wings that are four-foot-one-and-seven-eighths long.
Be aware that changes in pitch affect calculations differently. A transition from low to high sloping areas requires alternate measurements like “rise over run.”
Before cutting materials, always double-check measurements and calculate twice. Tradespeople often prepare framing designs and show layout prints to lumber yard carpenters or manufacturer company executives. This helps avoid mistakes during construction and leads to better craftsmanship. Spacing rafters correctly gives you room to breathe and your roof room to shine.
Maximize your framing construction business’s potential with our competitive financing options
Calculating the distance between roof rafters is key for a strong and safe roof. It works out how much weight your roof can hold and how many roofing panels or shingles you’ll need.
To get the spacing right, measure from the outside of one rafter to the outside of another. Generally, rafters are 16 or 24 inches apart. But the spacing can vary on different roof areas due to pitch and snow load. Refer to this table for usual rafter spacing ranges:
Pitch (in degrees) | Snow Load (in pounds per square foot) | Rafter Spacing (in inches) |
---|---|---|
Less than 3/12 | Up to 20 | 16-24 |
3/12 – Less than 5/12 | Up to 30 | 16-24 |
5/12 – Less than 7/12 | Up to 40 | 16-24 |
7/12 – Less than 9/12 | Up to 50 | 16-20 |
9/12 – Greater | Up to 70 | 16 |
Obey local building codes and regulations when constructing your roof. Even if your materials can take more weight, too much weight in certain areas could cause a collapse. Get help from an expert if you’re not sure your plans are safe.
Don’t gamble with your home’s stability. Get your measurements right by following industry standards and consulting code officials and professionals. Get it wrong and your foundation won’t stand.
To measure for foundation framing with Sill Plate Length, Stud Placement, and Anchor Bolt Placement as a solution, you need accurate estimates. Knowing the right measurements will ensure your construction project is stable and durable. Here’s a guide on the steps you need to follow to get precise measurements of the foundation framing for your construction project.
Calculating the base for a building’s framework is essential. The ‘length of the sill plate’ depends on the measurements of the foundation. It is firmly fixed parallel to the ground to form a stable base.
Let’s take an example of a 30ft x 20ft wooden frame building. Here, two 20ft lengths and two 32ft lengths from cinder-blocks or bricks are needed as support. This adds up to 104ft. That means two sections of 52ft each must be used.
Not all structures are square. Angled corners and varying dimensions are also possible. Therefore, custom measuring is necessary. Measure each side and then add up the total length with additional safety length.
For secure construction from anchors to frames to roofs, detailed attention is needed when measuring. Double-checking is recommended even after calculating multiple variations. By following these steps, a reliable foundation framework is created for safe house development. Goldilocks got it right – the studs must be neither too far apart nor too close, but just right.
Stud Positioning is super important for any building. A proper layout means more structural stability and longevity. Examining the site before construction will lead to ideal placement.
Here’s an example of Stud Orientation with two measurements (16-inch and 24-inch centers). The 16-inch measurement is the distance between each stud’s center; the 24-inch measurement is one in every three studs from the previous.
True and Actual Data is in this Table.
Stud Spacing (16in) | Stud Spacing (24in) | |
---|---|---|
Wall top | 14 | 20 |
Wall bottom | 15 | 22 |
Different factors affect Stud Orientation, like local building codes or wall covering materials. Get expert advice on regulatory specifications and building practices. Aim for a sturdy foundation, but make sure your anchor bolt placement is on point.
Anchor Bolts must be placed strategically to secure a foundation. This placement prevents movement or sliding in severe weather or everyday use.
A table must be created for accurate bolt placement. This table should have columns for bolt diameter, spacing, edge distance and more. This helps measure where the bolts should go quickly and precisely.
When placing Anchor Bolts, you must consider the type of foundation. Concrete and wood require different anchors. Also, the project may call for special diameter and spacing measurements.
It is wise to be careful when constructing walls near existing structures. It can be hard to get the right bolt placement.
Be sure to take into account weather conditions during preparation. This ensures accurate measurements and a secure foundation.
To calculate the amount of lumber and nails needed for framing, use the solutions provided in ‘How to Calculate Lumber and Nails’ section of ‘How to estimate framing complete guide step by step.’ The sub-section ‘Board Feet Calculation’ provides guidance on estimating lumber according to its size, while ‘Nails Count Calculation’ suggests techniques for determining the required number of nails.
Calculate the lumber and nails needed for success. To start, measure the length of the lumber in feet. Then, measure the width in inches and the thickness in quarter inches. Multiply these numbers and divide by 144 to get Board Feet. Add 5-10% to this number to account for any mistakes.
Be sure to know your nail requirements for specific projects. For instance, decks need 3 nails per joist and trim on walls need 2-inch finish nails every 16 inches. Make sure you use the right nails – otherwise they’ll break or bend easily ruining the project. Nail those calculations like a pro – or else your project won’t float!
To calculate the nails needed for a project, here’s what to do:
For example, for a standard 2×4 board with a 6-inch space between each nail and 10 boards for the project, the calculation is as follows:
Total nails needed:
– Length of board / spacing = (96/6)*10 = 160 nails
Table for Nails Count Calculation:
Item | Measurement |
---|---|
Length of Board | 8 feet |
Width of Board | 4 inches |
Spacing Between Nails | Every 6 inches |
Total Boards | 10 |
Number of nails per Linear Foot | (12/6) = 2 |
Total Nails Required | (96/6)*10 = 160 |
If the project is more complex, multiple measurements may be needed to determine the exact amount of nails.
Pro Tip: Better to have extra nails on hand than run out mid-project. Estimating framing materials is like solving a jigsaw puzzle with half the pieces missing!
To enhance your understanding of estimating framing materials, this section provides you with additional tips on how to ensure your estimate takes into account all necessary factors. By following the advice in this section, which includes adding extra materials and consulting with professionals, you can feel confident that your framing projects will be well-planned and successful.
To get the right amount of framing materials for your construction project, think about any factors that may need extra material. This’ll stop delays in building.
Here’s what to consider:
Consulting with professionals is key. They know how much extra material should be added. Although it may seem costly, having extra material can save time and cash if anything unexpected happens during construction. The National Association of Home Builders (NAHB) even suggests adding an extra 10-15%.
By keeping these tips in mind and consulting, you can make sure the construction process is smooth, with no setbacks.
Seeking expert advice on optimizing framing material estimation can be a smart move. Architects, engineers and carpenters – industry specialists – offer the guidance needed to help regulate material projections. Communicating project plans and designs well with pros gives accurate info for estimating framing materials.
Professionals suggest calculating timber lengths and surface area. Also factor in doors, windows and wall space for precise material requirements before starting a project.
Consulting industry professionals helps with planning and execution guidelines. Keep an eye on updates about regulations by visiting official construction websites. This prevents costly remedies later due to inaccurate estimations.
Timely consultations can save time and resources. Partnering with professional expertise streamlines planning from start to finish while keeping resources economical. Consulting experts is a prudent investment to avoid setbacks and have access to meticulous resources throughout the building or remodeling process.
It’s clear that framing is key in construction. To estimate it, the first step is to understand the blueprint and project needs. Next, measuring dimensions accurately is crucial for understanding material quantities. Plus, extra costs like labor and wastage should be factored in for a precise framing cost.
Not all constructions require the same estimations. For example, office building framing will differ from residential apartments. So, it’s essential to know the project’s nature before doing cost estimations.
A challenge with framing estimation is miscalculating, leading to over or underestimation. Modern technology can help with this problem by providing precise measurements and better accuracy.
Framing refers to the process of building the structure of a building, such as the walls, floors, and roof. It involves creating a skeleton-like framework that provides support and stability to the building.
Estimating framing materials requires taking accurate measurements of the building’s dimensions, including wall lengths, ceiling heights, and roof pitches. From there, you can calculate the amount of lumber, sheathing, and other materials needed for the framing.
Some of the tools you’ll need for framing include a circular saw, hammer, nail gun, level, tape measure, and framing square. You may also need a chop saw, drill, and other power tools depending on the scope of the project.
To frame a wall, you’ll need to measure and mark the wall layout, cut the lumber to size, and then assemble the framing using nails or screws. You’ll also need to ensure that the wall is plumb and square before installing any sheathing or drywall.
The cost of framing a house depends on many factors, including the size of the house, the complexity of the design, and the cost of materials in your area. Generally, you can expect to pay anywhere from $10 to $20 per square foot for framing work.
The time it takes to frame a house depends on the size and complexity of the project. A small, simple home may take only a few weeks to frame, while a large, intricate home may take several months. It’s best to discuss the timeline with your contractor before starting the project.
Here I am going to share some steps to get your framing construction cost estimate report.
You can send us your plan on info@estimatorflorida.com
Before starting your project, we send you a quote for your service. That quote will have detailed information about your project. Here you will get information about the size, difficulty, complexity and bid date when determining pricing.
We do framing construction cost estimating and prepare a detailed report for your project. At last, you finalize the report and finish the project.
561-530-2845
info@estimatorflorida.com
Address
5245 Wiles Rd Apt 3-102 St. Pete Beach, FL 33073 United States
561-530-2845
info@estimatorflorida.com
Address
5245 Wiles Rd Apt 3-102 St. Pete Beach, FL 33073 United States
All copyright © Reserved | Designed By V Marketing Media | Disclaimer
IMPORTANT: Make sure the email and cell phone number you enter are correct. We will email and text you a link to get started.
By clicking “I Agree” above you give Estimate Florida Consultin express written consent to deliver or cause to be delivered calls and messages to you by email, telephone, pre-recorded message, autodialer, and text. Message and data rates may apply. You are able to opt-out at any time. You can text STOP to cancel future text messages.