- Homepage
- How To Estimate Concrete Work?
How To Estimate Concrete Work?
Leading provider of concrete estimating.
Estimating the cost of new concrete involves much more than the price of concrete per yard (or meter). There are many variables to consider, such as surface prep, formwork, reinforcing materials, and finish work, plus the cost of the ready-mix concrete, that will add up to the total price of the job. Costs for specific items will vary from location to location or from site to site, but you can get a rough estimate using some averaged amounts.
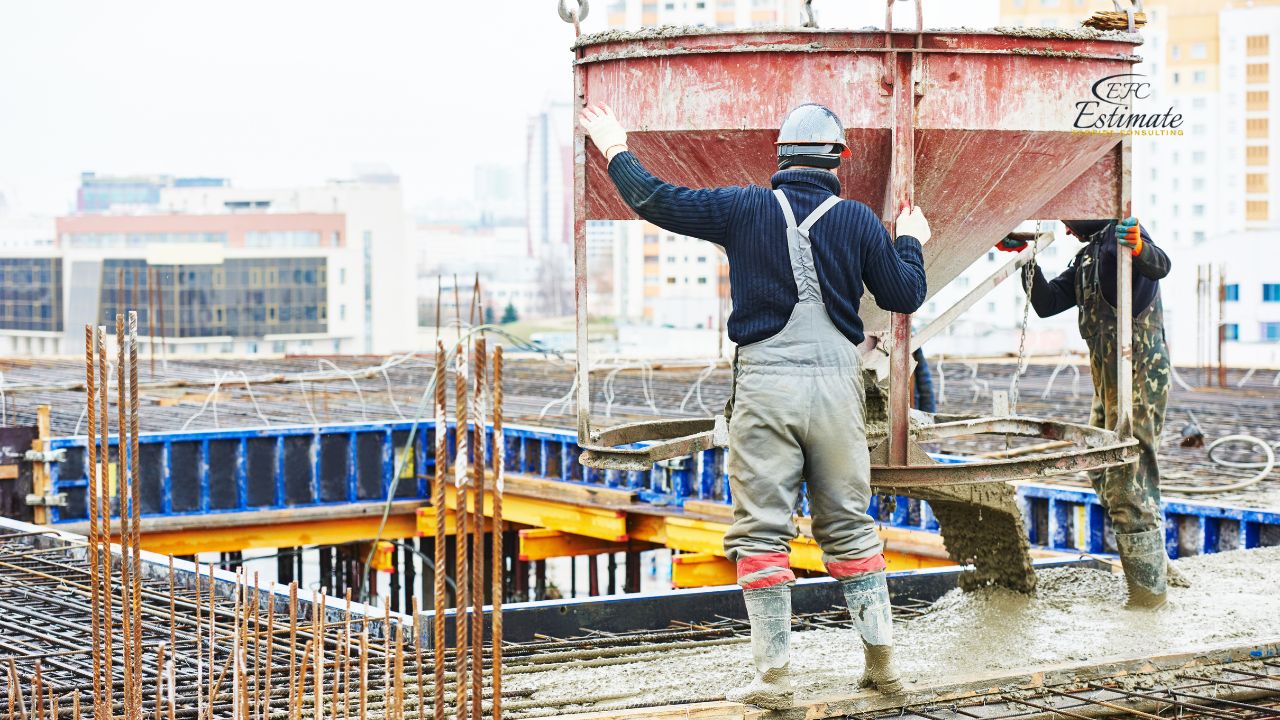
Question Answer
Frequently Asked Question
Call Now: +1(561)530-2845
Call Now: +1(561)530-2845
Standard concrete floor slab thickness in residential construction is 4 inches. Five to six inches is recommended if the concrete will receive occasional heavy loads, such as motor homes or garbage trucks. To prepare the base, cut the ground level to the proper depth to allow for the slab thickness.
Call Now: +1(561)530-2845
To prepare a concrete estimate properly for bidding purposes the estimator must consider two facets of an estimate. The first is the quantity takeoff; the second is the pricing schedule. The quantity takeoff must be done by the same man who is to price the job or at least by someone who uses the same system of takeoff as the one who prices it. This is especially true in formwork quantities. Without this understanding between the “takeoff estimator” and the “pricing estimator” error are introduced that can make the bid either too high or too low. A quantity takeoff of all items of concrete is the first step in preparing an estimate. All items of concrete material are listed on the quantity takeoff sheets.
We Quantify in our Concrete Estimating Service
- Sidewalks
- Driveways
- Patios
- Paving
- Parking Lots
- Retaining Walls
- Wire Mesh
- Foundations Concrete
- Structural Rebar
- Dowels
- Curbs
- Basements
- Cast in Place
- Concrete Repairs
- Tie Beams
- Knockouts
- Shear Walls
- Decks
- Square Pilasters
- Lintel Block
- Backyard
- Stirrups
Costs To Install Concrete Slab
Concrete slab installation costs a minimum of $6.25 per square foot for a 4″ thickness, and as high as $11.72 per sq. ft. for a 6″ slab with thicker edges, styrofoam beneath the slab, and wire mesh. Adding radiant heat, extra dirt work, or grading to the sub-base costs extra.
If you want to add additional reinforcement due to poor soil conditions, or if you’re worried about big cracks, put some structural reinforcing metal in the concrete foundation with either wire mesh or rebar. Also, if your going to go with 4″ thick slab, reinforcing metal is highly recommended to make your slab structurally sound.
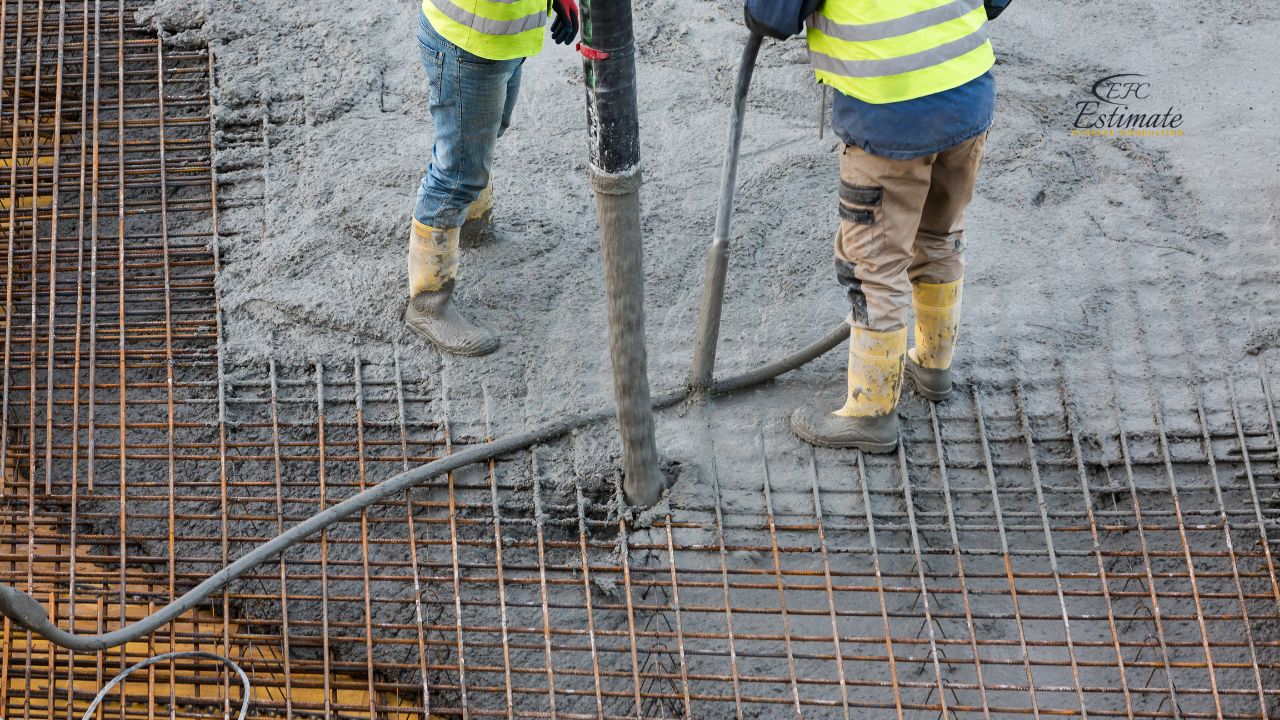
Concrete Slab Cost Per Square Foot
On average, to pour a concrete slab costs $6.25 to $7.37 per square foot for both labor and materials. Your total price depends on the thickness of the slab, and if you chose to reinforce your slab with wire mesh or rebar.
Slab Thickness | Materials | Labor | Average Cost (SF) |
---|---|---|---|
4” | $3.33 | $3.32 | $6.25 |
5” | $3.60 | $3.16 | $6.46 |
6” | $3.97 | $3.30 | $7.37 |
Skilled Concrete Work
Experts?
Poured concrete retaining wall cost
A poured concrete retaining wall costs $70 to $280 per linear foot for 3’ to 6’ tall walls or $30 to $55 per square foot of wall surface. Total costs depend on the wall-finish type, drainage, excavation depth, and backfill options. Retaining walls often have French drains at the base.
How to Estimate a Concrete Takeoff?
Regularly securing projects for your business involves estimating projects that often include a concrete estimate as part of the bid. This means that you’ll need to review the plans carefully so that you can calculate the labor and materials needed to complete the project.
Because the takeoff is essential to your estimating process, it’s critical that the several steps required to complete a concrete takeoff be handled carefully and methodically. Below we provide the 4 essential steps to completing an accurate concrete takeoff.
1. Estimating Materials
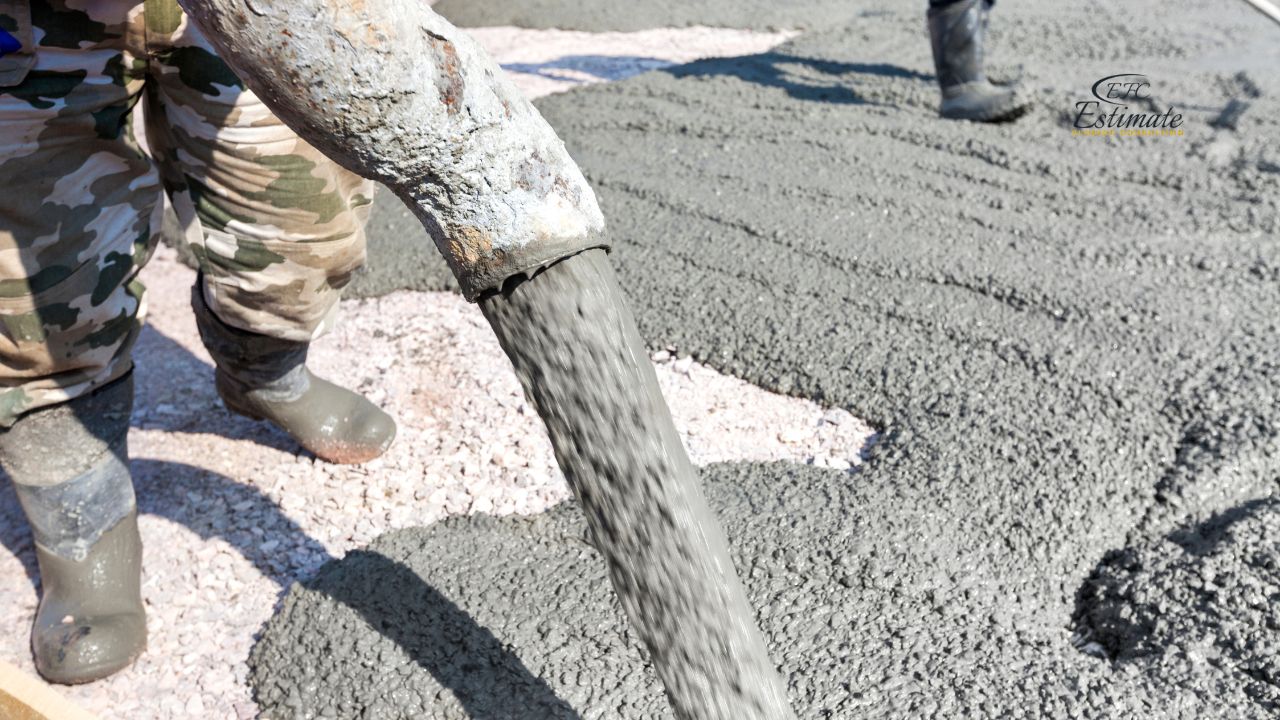
To calculate the cost of materials, you’ll need to use a careful, methodical approach to determine measurements, quantities, and similar information. To start, you’ll work on your materials takeoff using the list above. Reviewing the plans, you can start from the bottom of one corner, work across that level, and then move up to the next level, taking care to note every piece of rebar, square-foot of reinforcing mesh, or similar materials.
Once you’ve taken note of every material needed for the project, it’s now time to start estimating how much concrete will be needed and what type.
2. Estimating Labor
Now that you’ve determined how much material is needed and its cost, you’ll need to think about how long it will take to complete the project in terms of hours of labor and factor in the cost of that labor to your concrete takeoff. While calculating the labor involved, make sure to take into account shift differentials, union or non-union wages, overtime, time spent traveling up or down multi-story structures and similar aspects of the project that can impact labor costs.
It’s also wise to base your figures on how many square feet of work an average worker can do in a day rather than base it on your most productive worker because once you know that, you can estimate labor costs no matter the season or year. A good rule of thumb is to assume an average worker can complete about 300 to 350 square feet of concrete work a day.
3. Determining Overhead
The next step is to add in overhead costs. Overhead costs are any costs incurred that are not related to labor, direct materials, or production, such as running your back office, vehicles, upkeep, advertising, and other expenses. And don’t forget your time meeting with the client and preparing the estimate! That’s all part of what has to be billed.
Calculating overhead can be intimidating at first, but it’s not too difficult. First, you have to know what your overhead expenses are for a year. Include all salaries for anyone who works on the business’s back end, like the bookkeeper or secretary.
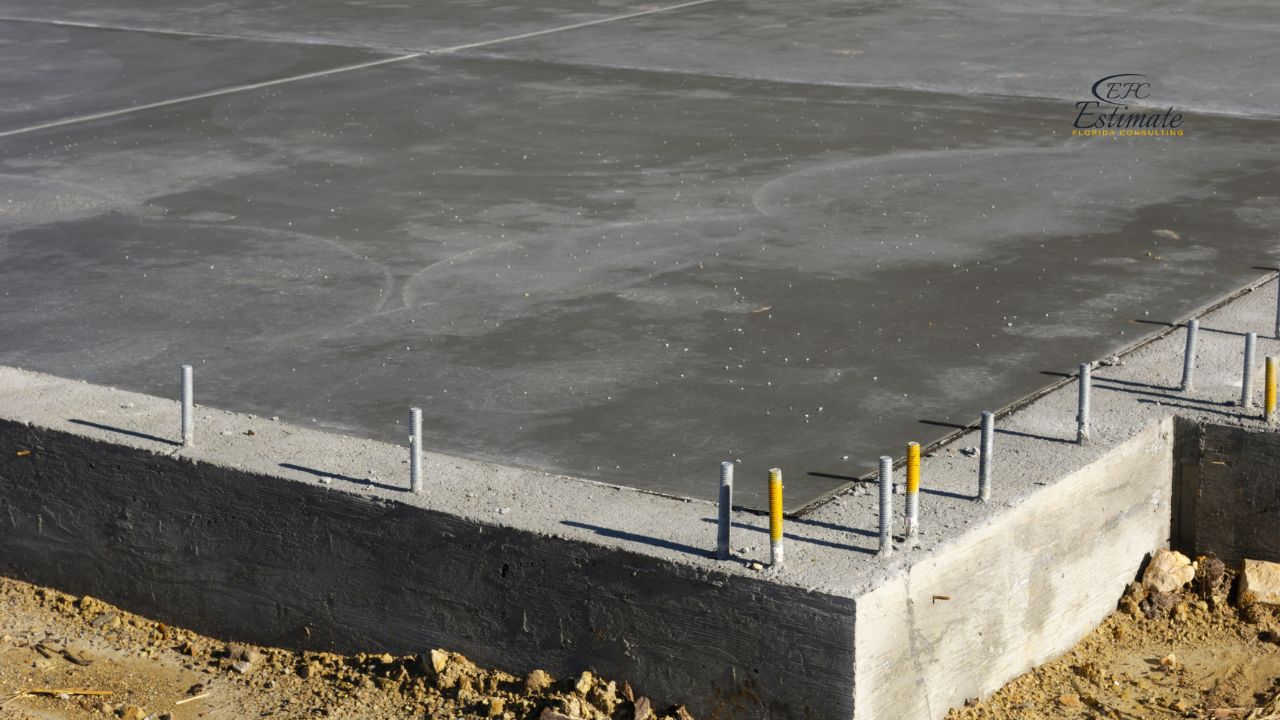
For larger overhead expenses such as a work vehicle or truck lease, you can also prorate the expense and include it as a cost on your concrete takeoff. For example, if you have a truck that you use regularly for your business and expect it to last 10 years, your yearly cost is 10% of the total cost (1 out of 10).
4. Calculating Profitability
To factor in profit, start by determining the overall margin for your business, usually somewhere between 2 and 10% in the construction industry, and then include a percentage of this total annual number just like you did for overhead costs.
Of course, when you write up your final takeoff, estimate, or quote, you won’t include sections for “overhead” and “profit”. Instead, you’ll fold these costs into labor costs on your final concrete takeoff.
90% More Changes to Win Bids With Our Estimate
Take the First Step to Your Bid Win – Upload Plans!
Concrete Pool Costs by Concrete Type
Average concrete pools cost range between $79.3 to $185 per sq.ft. for prefab models and $120.50 to $312.50 per sq.ft. for custom models. The exact cost depends on whether your design is built in place or off-site and then shipped to your home. After deciding to build one, the next question is what type of concrete. Depending on the style and type of concrete pool you want, contractors can often recommend which will be the best. The chart below describes the cost per sq. ft. of the main types.
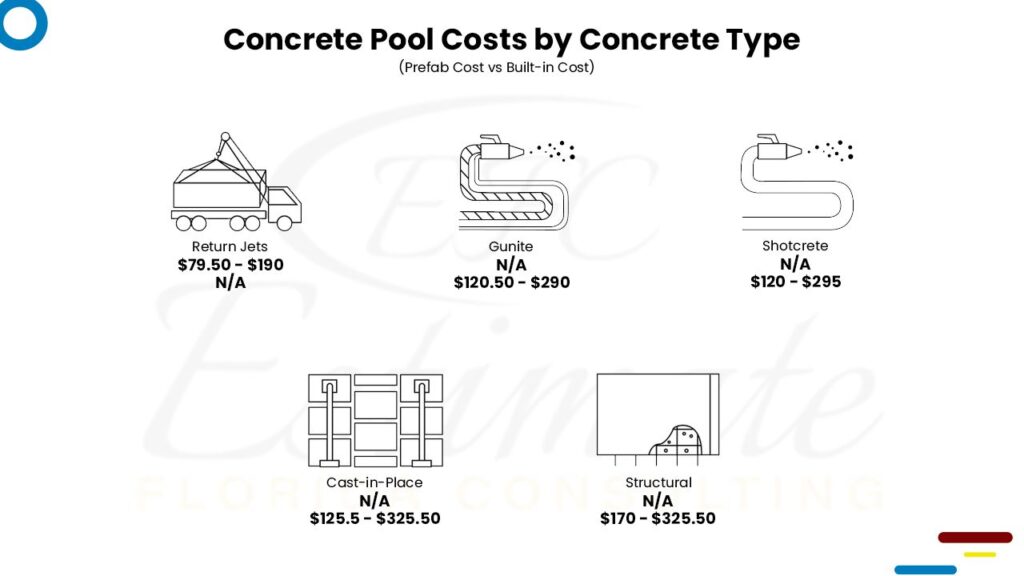
Concrete Stair Installation Costs
Expect to pay between $550 and $1,700 to install precast cement stairs. The total precast cost of $850 to $3,700 compares favorably to the cost of a custom-poured staircase, which ranges from $950 to $5,500, including materials and labor.
Component | Price |
---|---|
Cement | $230 – $650 |
Labor | $350 – $850 |
Additional Materials | $70 – $230 |
Delivery | $230 – $450 |
Extra Features | $180 – $1,500 |
Building Permit | $130 – $1,700 |
Total | $1,190 – $5,380 |
Concrete Pool Costs by Type
Above-ground concrete pools cost between $18,000 and $84,000, while in-ground ones are $27,000 to $94,000. Choosing between the two is primarily a matter of style choice for the homeowner. However, one significant benefit of an above-ground model is that it costs less than an in-ground model to install and maintain. They are also easier to install than in-ground options as they don’t require excavation or lengthy installation. Unfortunately, above-ground models don’t add as much value to your home as in-ground ones.

Type | Cost Prefab (Installed) | Cost Custom (Installed) |
---|---|---|
Above-Ground | $18,000 – $32,000 | $30,000 – $84,000 |
In-Ground | $27,000 – $54,000 | $52,000 – $94,000 |
We Provide 3D Rendering Services!
For Commercial & Residential, and Other Projects
Turnaround time is 1-2 days.
Win More Projects With Us
Concrete Floor Slab Construction Process
-
Prepare formwork
The formwork is the frame for the concrete slab. For measurements, consult the approved building plans to ensure the formwork is setup correctly. Following the process of laying the formwork correctly, reduces the likelihood that the concrete slab is compromised. Preparation of formwork must also follow established building standards and guidelines.
-
Excavate earth
The site is cut to near level with excavation machinery. Once the excavation is complete, the surveyor sets pins in the ground to mark out floor area and give tradesmen points to measure from. Electricians and Plumbers trench and run access for services. Footings and piers are dug to the Engineers specifications and the site is made level using laser level. Formwork is constructed around the perimeter of the slab to be poured. This will form the shape of the slab and hold the concrete while it sets hard.
-
Prepare slab bedding
It is important to prepare the slab bedding correctly. This will ensure that the concrete slab rests on a firm base and that the concrete slab does not start cracking. To prepare the slab bedding, use road base or crusher dust of a reasonable thickness based on building codes. Ensure that the surface is level and flat and compacted firmly. A well-drained base and compacted bed prevents the concrete slab cracking.
-
Install reinforcement
Reinforcement prevents the concrete from cracking, buckling and caving in when a load is placed on it by improving the tensile strength of the concrete and making it more durable. Ensure the reinforcement bars, spacers and ties are installed in accordance with the approved building plans.
-
Pour, compact and finish concrete
A professional should be engaged to pour the concrete from a reputable pre-mix company. This will ensure that the concrete is at the specified strength. Prior to pouring, soak the slab bed with water to prevent moisture loss. Once the concrete is poured, add control joints where required. As the concrete dries, it will shrink. To avoid cracks forming randomly, control / expansion joints ensure cracks to not develop.
-
Cure concrete and remove formwork
Curing a concrete slab involves the application of water over an approximate 7 day period. Applying moisture to the concrete helps it to seal. Spraying twice daily is ideal – use light mist sprays with complete coverage. After 24 hours of the concrete being poured, the formwork can be removed. Take care removing the formwork to avoid any damage to the concrete slab. The slab can be walked on after 3 days, but avoid heavy loads for at least 7 days
Precast Concrete Steps Pricing Factors
Precast concrete is about 20 percent less expensive than poured concrete, which needs to be mixed first. For an estimated $2,500 project, you might save up to $450 by using precast concrete over poured.
Cement Quality
A low-grade cement step costs $250, while the highest-quality step averages about $450.
What sets cement apart is the quality of the ingredients mixed into it. High-grade concrete often contains more minerals, such as fly ash, which increases tensile strength.
Size of Staircase
You can expect to pay between $80 and $180 per standard-size step. The number of steps you need will affect the size of your staircase and your budget. Standard units are around 2 feet wide, but your project may differ. Wider or curved concrete steps may increase your budget.
Coatings and Treads
Treads help to distinguish your concrete staircase and make it more visually appealing. You can find precast staircases with existing treads, which adds $130 to $550 to your stairs project.
On exterior steps, the most common treads are made of natural stone. You can also pay for a cement coating for about $230 to $450. A coating will make your steps more durable and can improve slip resistance.
Get 5 New Projects in the Next 7 Days With Our System
How many concrete blocks per cubic foot (CFT)
- Calculate block wall cubic footage (10 ft × 10 ft × 0.66 ft = 66 cubic footage) :- measures length, height and thickness of block wall, suppose a block wall is 10 feet long by 10 feet high by 8 inch wide, volume of wall in CF = length × height × thickness = 10 ft × 10 ft × 0.66 ft = 66 cubic feet.
2. Calculate volume of block (16″× 8″ × 8″ = 1024 sq in ÷ 1728 = 0.59 cubic feet):- most commonly used, a standard size of concrete block is 8″×8″×16″, volume of one block in CF = length × height × thickness = 16″ × 8″ × 8″ = 1024 cubic inch, divide by 1728 to get 1024 ÷ 1728 = 0.59 cubic feet
3. determining the number of blocks you need (66 CF÷ 0.59 CF = 112 nos blocks):- determining the number of blocks you need by dividing the volume of block wall by cubic feet of one concrete block, such as number of blocks = volume of wall CF/ volume of block CF, 66/0.59 = 112 nos blocks
4. Add 5% – 10% additional blocks (5% of 112 = 6 nos, 112 + 6 = 118 nos blocks
Comprehensive Trade-Specific Estimates
At Estimate Florida Consulting, we offer detailed cost estimates across all major trades, ensuring no part of your project is overlooked. From the foundation to the finishing touches, our trade-specific estimates provide you with a complete and accurate breakdown of costs for any type of construction project.
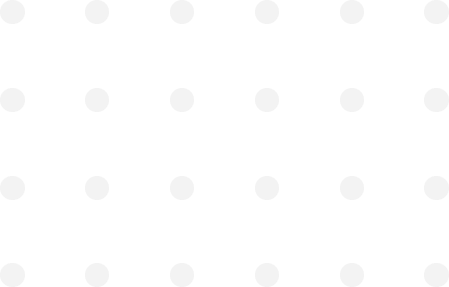
Testimonials
What Our Clients Say?
We take pride in delivering accurate, timely, and reliable estimates that help contractors and builders win more projects. Our clients consistently praise our attention to detail, fast turnaround times, and the positive impact our estimates have on their businesses.
Estimate Florida Consulting has helped us win more bids with their fast and accurate estimates. We trust them for every project!
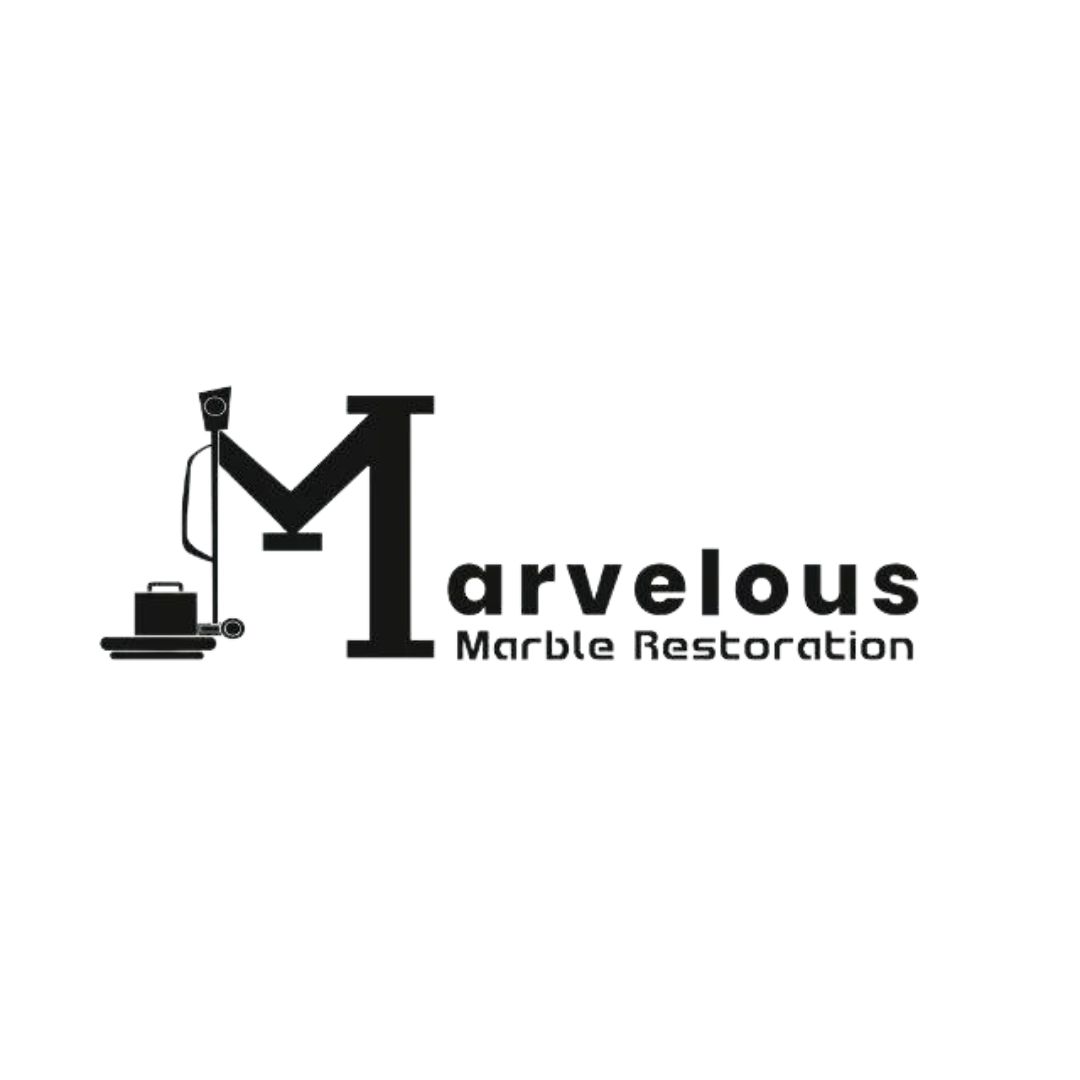
Steps to Follow
Our Simple Process to Get Your Estimate
01
Upload Plans
Submit your project plans, blueprints, or relevant documents through our online form or via email.
02
Receive Quotation
We’ll review your project details and send you a quote based on your scope and requirements.
03
Confirmation
Confirm the details and finalize any adjustments to ensure the estimate meets your project needs.
04
Get Estimate
Receive your detailed, trade-specific estimate within 1-2 business days, ready for your project execution.
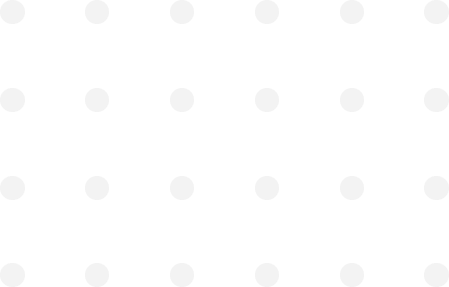